его изготовка в домашних условиях, пропорции на на 1 м3
Главная » Бетон » Пенобетон
Пенобетон
Автор Георгий Русиев На чтение 3 мин Просмотров 2к. Опубликовано
Задавшись идеей создания собственного дома, владелец участка использует любую возможность удешевить процесс строительства. Лучшим способом этому послужит самостоятельная работа, в том числе при получении материалов для возведения объекта. Действительно, зная состав пеноблока, изготовка нужного количества единиц, труда не представляет. А ячеистый бетон, сегодня популярен, как никогда.
Компоненты и пропорции
Все участвующие материалы при изготовлении в фабричных условиях проходят строгий контроль и стандартизацию. Нельзя допустить отхождения от нормы и в самодельном производстве.
- Портландцемент. ГОСТ 10178. Его основа – силикатный кальций содержанием не менее 80 %.
- Песок. ГОСТ 8736. С наличием кварца не менее 75 % и допустимым количеством примесей не более 3 %.
- Пенообразователь. В его состав входят многие элементы – канифоль, едкий натр, клеи.
- Вода техническая. ГОСТ 23732.
- Отвердитель – кальций хлористый. Используется как скорейшее достижение результата в промышленных условиях.
Пропорции для производства различного назначения пеноблоков – от возведения фундамента, до кровли, отличаются, и продукт имеет отличную друг от друга рецептуру.
Для изготовления пенобетона плотностью до 1800 кг/м3, потребуется:
- кварцевый песок 1330 кг;
- цемент 420 кг;
- вода 185 л;
- концентрированный пенообразователь 0.44 кг;
На выходе, получится пластичная масса весом в 1935 кг.
Для менее тяжелого продукта, параметром 440 кг/м³, песок не требуется вовсе.
- цемент 350 кг;
- вода 110 170 л;
- пеноконцентрат 1.5 кг.
Окончательный вес будущего материала перед заливкой в формы равен почти половине тонны в сыром виде.
Варианты рецептов производства пеноблоков могут разниться и по составу пенообразователей. Используя дешевые синтетические, можно получить хорошее качество изделия для подсобных одноэтажных помещений. На жилом объекте экономить в натуральном сырье нельзя – от этого зависит прочность конструкции.
Важно приобрести все нужные агрегаты автоматического процесса, если производство планируется вести в домашних условиях и позаботиться о темном сухом помещении для сушки и хранения единиц стройматериала.
Сравнительные характеристики пеноблока и газобетона
Оба представляют собой ячеистые образования в результате добавления присадок. Состав пенобетона, в отличие от газобетона содержит пенообразователи. В то время как второй вариант создается с помощью алюминиевой пудры, которая выделяет водород. От разницы в составе, технические характеристики обоих материалов существенно отличаются:
- Прочность и нагрузка. Пенобетон выдерживает не более 9 кг/см², а газовый блок до 35 при одинаковой плотности – 500 кг/м³.
- Уровень энергосбережения. Стена из материала с добавлением алюминия почти в 1.5 раза тоньше, нежели с присадками пенообразователя. На этом примере станет ясно, каким образом однородность ячеек влияет на сохранение тепла – пенобетон одинаковыми «пузырьками» похвастать не может. Отчего возникает риск промерзания в разных местах объекта.
- Микроклимат дома из газоблоков лучше, так как поры сквозные. Однако менее подвержен сырости и не потребует отделки сразу же после строительства, здание из пенобетона – ячейки в нем имеют твердые перегородки, это, естественно, влаге препятствует.
- Внешний вид.
Сказать, что оба материала красивы нельзя – цвет от белого, до темно-серого, шероховатая структура, швы, требующие профессионализма. Поэтому такие дома все-таки подлежат отделке – сайдинг, блок хаус. К тому же если производство велось вне зоны промышленных предприятий, то геометрию с погрешностями так или иначе, придется закрывать. Сравнить материалы в таком ключе можно, когда для отделки используется штукатурка – на газовый блок она ляжет ровнее, именно из-за его однородной пористости.
Что касается цены. Разница существенна, если принимать в расчет высококачественный газобетон и автоклавный раствор с добавлением пены почти на треть стоимости. Но из-за популярности и спроса на второй вариант, вполне возможно, приобрести достойный продукт, мало уступающий блоку, в составе которого есть алюминиевая пудра.
видео-инструкция по изготовлению своими руками, что входит в раствор, фото
Пеноблок является пористым камнем, разновидностью ячеистого бетона. Нужно отметить, что иногда объединяют понятия пенобетона с газобетоном, почему-то считая их идентичными. Различие между этими материалами заключено, во-первых, в их названиях, а во-вторых, в способе их изготовления.
Пенобетон производится механическим перемешиванием специальной смеси и в состав раствора для пеноблоков входит песок, вода, цемент и приготовленная пена. Газобетон получают с помощью газа, а именно водорода, который образуется во время протекания химических реакций.
В результате в газобетоне образуется множество сквозных пор, в то время как в пенобетоне – много закрытых. И его изготовка приводит к тому, что гидроизоляционные свойства обладают более высокими характеристиками.
Фото пенобетонного блока
Содержание
- 1 Что же представляет собой пенобетон
- 1.1 Состав пенобетона
- 1.2 Виды, характеристики пенобетонных блоков
- 2 Преимущества и недостатки пенобетона
- 2.1 Преимущества
- 2.2 Недостатки
- 3 Вопросы кладки пенобетона
- 4 Вывод
Что же представляет собой пенобетон
Состав пенобетона
Рецептура производства пенобетона
Пенобетонные блоки являются своеобразным, дышащим материалом, способным помочь в создании такого же микроклимата в доме, как и натуральное дерево. Что входит в состав пеноблоков, что дает возможность получить такие комфортные параметры?
Смесь для приготовления пенобетонной смеси состоит из следующих компонентов, согласно документу ГОСТ 25485-89 «Бетоны ячеистые»:
- Вяжущий элемент – портландцемент, произведенный согласно ГОСТ 10178-85, в котором содержание силиката кальция должно содержат до 80%.
- Песок, отвечающий требованиям ГОСТ 8736-93, в котором содержание кварца должно составлять порядка 75%, глинистые и илистые включения не превышать 3%.
- Вода, технические требования к которой должны соответствовать ГОСТ 23732-79.
- Пенообразователь, в состав которого входит костный клей, сосновая канифоль, мездровый клей и едкий технический натр.
Пенообразователи, в зависимости от применяемой основы подразделяются на два вида:
- Синтетические, позволяющие получить довольно дешевые изделия, но материал из них получается не очень качественный и прочный.
- Натуральные, на экологически чистой основе, не имеющей класса опасности.
Такие блоки получаются довольно прочными, потому что у них более толстая перегородка между порами.
Совет: Покупая пенобетонные блоки, поинтересуйтесь, что послужило основой, пошедшей на производство пенообразователя. И на основании полученной информации принимайте решение о покупке блоков.
Некоторыми заводами изготовителями применяются другие компоненты при производстве пенобетона, в частности:
- Полипропиленовое микроармирующее строительное волокно или иначе фиброволокно ВСМ. Его использование придает блокам точные, неразрушающиеся грани, повышает его прочность на четверть.
- Зола, образующаяся после сгорания твердого топлива на теплоэлектростанциях. Это мелкодисперсный материал, в котором самые маленькие размеры частичек составляют доли микрона самые большие – 0,14 мм. В результате также создаются более плотные и твердые межпоровые перегородки и кроме того на 30% экономится цемент.
Виды, характеристики пенобетонных блоков
Разделение блоков по типам
Если изменять процентное соотношение составляющих пенобетонную смесь ингредиентов, получается пенобетон, имеющий различные характеристики.
Давайте рассмотрим основные свойства пенобетона и существующие градации.
- Разделение пенобетонных блоков по плотности:
- Конструкционный материал, марка которого D1000, D1100, D1200. Из таких блоков возводят фундаменты, цокольные этажи зданий, несущие стены
- Конструкционно-теплоизоляционный материал: под маркой от D500, до D900. Он используется при устройстве перегородок, а также несущих стен.
- Теплоизоляционный материал, под маркой от D300, до D500. Из него выполняется теплоизоляционный контур стен.
Делаем из пенобетона фундамент
- Разделение по показателю теплопроводности:
- У конструкционных марок пенобетона показатели теплопроводности лежат в пределах 0,29 – 0,38 Вт/м*град, что меньше чем теплопроводность глиняного кирпича.
- У конструкционно-теплоизоляционных – 0,15 – 0,29 Вт/м*град.
- У теплоизоляционных – 0,09 – 0,12 Вт/м*град. Говоря о теплопроводности дерева, то она лежит в пределах 0,11 – 0,19 Вт/м*град.
- Морозостойкость пенобетона составляет от 15 до 75 циклов. Это качество находится на очень высоком уровне, потому что, находясь в микропорах, состояние воды является связанным.
Что позволяет воде не переходить в лед даже при очень низкой уличной температуре. Всегда может быть подобран материал, имеющий нужную прочность и морозостойкость.
- Различие в методах изготовления:
- Резаный материал: принцип изготовления заключается в разрезании большого массива пенобетона, с использованием специального резательного комплекса. У таких изделий лучшая геометрия и более прочные кромки, но в свою очередь качество определяется добросовестностью завода-изготовителя.
- Формовой материал: пенобетонный раствор заливают в специальную форму, имеющую перегородку.
Цена его меньше, чем у резаного.
Форма для заливки раствора
Преимущества и недостатки пенобетона
Преимущества
- Крепость и долговечность. Этот материал является практически вечным, потому что с течение времени его прочность увеличивается. Так его марочная крепость за десять лет эксплуатации увеличивается в два раза.
- Пеноблок имеет низкую плотность, что значительно снижает транспортные расходы, упрощает работу с ними, сокращаются строительные сроки и уменьшается давление на фундамент здания.
- Низкая теплопроводность. Пеноблочная стена толщиной 20 см равнозначна по теплоизоляции кирпичной стене толщиной в 60 см.
- По экологичности пенобетон уступает только натуральному дереву.
- Очень высокая звукоизоляция.
- Относительно небольшая стоимость.
Недостатки
Растворные швы не должны быть толще 2 мм, иначе ухудшаются звукоизоляционные и теплопроводные показатели (см.также статью Калькулятор расчета количества пеноблоков – простой вариант подсчета).
Совет: В качестве раствора для пеноблоков лучше всего использовать специальный клей. В этом случае не изменятся характеристики кладки, только стоит обращать внимание на то, чтобы геометрия материала была близка к идеальной.
Чтобы здание из пенобетона имело привлекательный и эстетичный вид, возникает необходимость во внешней отделке. Как самый лучший вариант – навесной вентилируемый фасад.
Вопросы кладки пенобетона
Инструкция по кладке пеноблоков своими руками:
- Поверхность фундамента, на которую будут укладываться пенобетонные блоки должна быть выровнена под «ноль», иначе это скажется на качестве кладки.
- Так же по этой поверхности должна быть проложена гидроизоляция, для недопущения попадания излишней влаги.
- Первый ряд блоков укладывается на цементно-песчаный раствор, который поможет убрать возможные небольшие неровности фундамента.
Укладка первого ряда на гидроизоляцию и раствор
- Каждый последующий ряд укладывается со сдвигом относительно нижнего ряда и в качестве раствора используется специальный клей.
Перевязка блоков в кладке
- Через каждые три-четыре ряда, по верхней поверхности прокладывается арматура. Для чего с помощью циркулярной пилы вырезаются специальные пазы.
- Используя строительный уровень и отвес, осуществляется постоянный контроль горизонтальности и вертикальности кладки.
Вывод
Пенобетон относится к очень популярным и, конечно же, перспективным материалам (узнайте здесь, что выбрать: пеноблок или газоблок). В представленном видео в этой статье Вы найдете дополнительную информацию по этой теме.
Состав и материалы для производства пенобетона
В зависимости от технологии производства применяются разные цементы, заполнители, пенообразователи и добавки. Далее мы подробно рассмотрим каждый компонент и приведем список всех пенообразователей и добавок.
Перечень добавок и пенообразователей:
- Пенообразователь ПБ-2000
- Протеиновый пенообразователь Laston
- Белковый пенообразователь GreenFroth
- Ускоритель твердения пенобетона бетона и пенобетона Асилин-12
- Смазка форм Компил
- Немецкое фиброволокно (фибра – полипропиленовое волокно)
- Микрокремнезем
- Суперпластификатор С-3
Для производства пенобетона используется цемент, заполнитель, вода, пенообразователь и добавки (если требуются). В зависимости от технологии производства применяются разные цементы, заполнители, пенообразователи и добавки. Далее мы подробно рассмотрим каждый компонент и приведем список всех пенообразователей и добавок.
1. Цемент
Для производства пенобетона используется обычный портландцемент. При использовании баротехнологии (ее иногда называют кавитационной или без пеногенераторной) обязательно использовать цемент марки М500Д0. Это цемент дорогой и дефицитный. Причем даже при его использовании получение пенобетона удовлетворяющего ГОСТ по баротехнологии сопряжено с большими затратами и технологическими трудностями. Если пенобетон производится по классической технологии, то возможно использовать цемент М500Д20, М400Д0, М400Д20.
2. Заполнитель
В качестве заполнителя в большинстве случаев используется песок. Он должен удовлетворять ГОСТ 8736-93 ПЕСОК ДЛЯ СТРОИТЕЛЬНЫХ РАБОТ. Также в качестве заполнителя могут использоваться различные отходы производств – зола уноса ТЭЦ, известняковая мука, доломитовая мука и т. п. Зачастую использование подобных отходов позволяет значительно снизить себестоимость и при этом увеличить качество продукции. При покупке оборудования завода Строй-Бетон, покупатели получают полную информацию о возможных заполнителям и помощь в их подборе.
3. Вода
Для производства пенобетона используется обычная питьевая или техническая вода. Вода должна удовлетворять требованиям ГОСТ 23732-79 ВОДА ДЛЯ БЕТОНОВ И РАСТВОРОВ. Температура воды подбирается исходя из технологии.
4. Пенообразователи
Пенообразователи бывают 2 видов – синтетические и белковые. Синтетические используются в баротехнологии (установки Санни), белковые в классической технологии (установки Фомм-Проф). Белковые пенообразователи считаются более совершенными и позволяют получать пенобетон удовлетворяющий ГОСТ 25485-89 БЕТОНЫ ЯЧЕИСТЫЕ без особых затрат. Подробнее можно прочитать в статье Причины использования белкового (протеинового) пенообразователя.
5. Добавки
В зависимости от технологии и используемых материалов периодически требуется использование специальных добавок. Добавки применяются для того, чтобы получить продукцию удовлетворяющую ГОСТ. Подбор добавок сложен и требует экспериментов. Для клиентов завода Строй-Бетон добавки подбираются бесплатно.
Рецепт пенобетона при использовании белкового пенообразователя
Плотность пенобетона в сухом состоянии. |
400 |
600 |
800 |
1000 |
1200 |
1400 |
1600 |
Песок (до 2мм, содержание глина не более 2%). |
– |
210 |
400 |
560 |
750 |
950 |
1100 |
Цемент марки М500Д0. |
300 |
310 |
320 |
350 |
360 |
380 |
400 |
Вода для приготовления раствора. |
110 |
130 |
150 |
180 |
210 |
240 |
300 |
Вода для приготовления пены литров. |
64 |
57 |
50 |
45 |
37 |
30 |
23 |
Количество пены (литров). |
800 |
715 |
630 |
560 |
460 |
370 |
290 |
Количество пенообразователя кг (не литров!). |
1,2 |
1,1 |
1 |
0,95 |
0,9 |
0,7 |
0,6 |
Вес сырой пенобетонной массы кг. |
474 |
707 |
920 |
1135 |
1357 |
1600 |
1823 |
Рецепт пенобетона при использовании синтетического пенообразователя
Плотность кг/куб.м. |
Песок |
Цемент |
Пенообразователь Ареком-4 |
|
1200 |
900 |
250 |
0,80 |
|
1100 |
740 |
360 |
0,88 |
|
1000 |
667 |
333 |
0,96 |
|
900 |
375 |
450 |
1,03 |
|
800 |
330 |
400 |
1,12 |
|
700 |
290 |
350 |
1,14 |
|
650 |
270 |
325 |
1,15 |
|
600 |
250 |
300 |
1,16 |
|
550 |
458 |
1,17 |
||
500 |
417 |
1,18 |
Состав пеноблока – пропорции для 1 м3 пенобетона!
Автор: Pavel Markovich
Быстрая навигация по статье (содержание)
- Раствор для пеноблоков — состав.
- Пропорции смеси пеноблока на 1 куб для разных марок.
- Изготовления разных видов пеноблоков.
- Оборудование для производства пеноблоков.
При производстве пеноблоков в промышленных условиях технология требует строгого соблюдения всех норм для используемых материалов и компонентов смеси. Так и при самостоятельном изготовлении ячеистого бетона вам будет необходимо строго придерживаться всех необходимых требований и стандартов. Рассмотрим более подробно какой состав и из чего делают пеноблоки в домашних условиях.
Состав пеноблока всех марок.Пенобетонные блоки являются своеобразным, дышащим материалом, способным помочь в создании такого же микроклимата в доме, как и натуральное дерево. Что входит в состав пеноблоков, что дает возможность получить такие комфортные параметры?
Смесь для приготовления пенобетонной смеси состоит из следующих компонентов, согласно документу ГОСТ 25485-89 «Бетоны ячеистые»:
- Вяжущий элемент – портландцемент, произведенный согласно ГОСТ 10178-85, в котором содержание силиката кальция должно содержат до 80%.
- Песок, отвечающий требованиям ГОСТ 8736-93, в котором содержание кварца должно составлять порядка 75%, глинистые и илистые включения не превышать 3%.
- Вода, технические требования к которой должны соответствовать ГОСТ 23732-79.
- Пенообразователь, в состав которого входит костный клей, сосновая канифоль, мездровый клей и едкий технический натр.
В зависимости от назначения готового изделия варьируется требуемая плотность, различная плотность достигается определенными особенностями в пропорции состава пеноблока.
Если на выходе нам необходимо получить пеноблок плотностью менее 1800 кг на кубометр, то для смеси потребуются элементы в следующем соотношении:
- 1320 кг песка кварцевого;
- 410 кг портландцемента;
- 184 л технической воды;
- 430 г пеноконцентрата.
В результате такого замеса получаем 1930 кг пенобетона.
В качестве примера приведена таблица, где указан состав смеси для получения 1 м3 пенобетона определенной марки и процентное содержание воздуха в нем:
Марка / состав раствора для пеноблоков | D400 | D800 | D1200 | D1600 |
Песок, кг | — | 420 | 780 | 1130 |
Портландцемент, кг | 300 | 320 | 360 | 400 |
Вода в растворе, кг | 110 | 120 | 140 | 160 |
Вода в пене, л | 60 | 46 | 35 | 21 |
Пенообразователь, кг | 1,5 | 1,2 | 0,9 | 0,6 |
Содержание воздуха,% | 80 | 63 | 46 | 29 |
Сырой пенобетонный состав, кг | 471 | 907 | 1316 | 1712 |
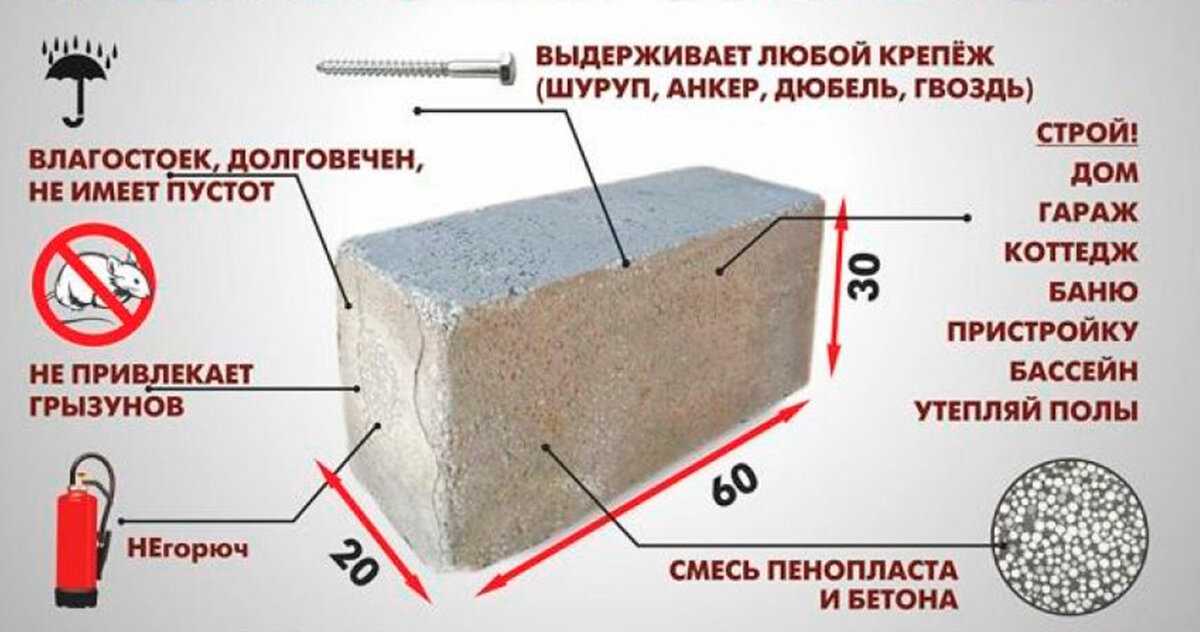
Блоки из пенобетона изготавливают из смеси, в состав которой входит песок, цемент, вода и пенообразователь. При перемешивании ингредиентов в нем образуются закрытые поры, обусловливающие теплосберегающие и гидроизоляционные свойства материала.
При производстве пенобетона необходимо точно соблюдать пропорции взятых компонентов. Их процентное соотношение определяет физико-химические характеристики материала.
В зависимости от этого пеноблоки подразделяют на следующие виды:
Виды пеноблоков | Марка | Область применения | Вес блоков, кг | Коэффициент теплопроводности, Вт/м*°C |
Теплоизоляционный | D400, D500 | для утепления внутренних помещений | 11– 19 кг | 0,12 |
Конструктивно-теплоизоляционный | D600 – D900 | для возведения стен в малоэтажных домах | 23– 35 | 0,14 – 0,29 |
Конструктивный | D1000, D1100 | для устройства перекрытий и как кладочный материал для несущих стен | 39 –47 | 0,36 |
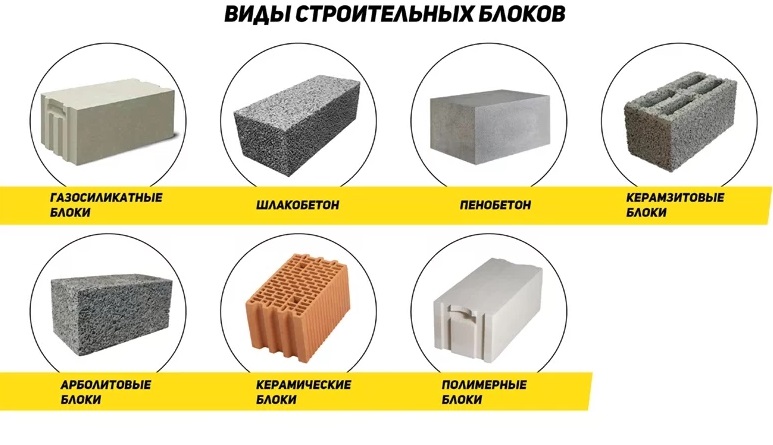
В процессе создания пеноблока, его твердение должно происходить в автоклавных условиях (в среде, насыщенной паром, и при давлении, которое должно быть выше атмосферного), что требует наличия специального дорогостоящего оборудования. Словом, его целесообразней производить в заводских условиях.
Оборудование для создания пеноблоков в домашнем условии.Но, его производство настолько простое, что, если зная пропорции для пеноблока, данный материал можно сделать даже в домашних условиях.
Для этого понадобится приобрести или самостоятельно смастерить такое оборудование, как:
- формы для отливки блоков;
- растворомешалку;
- компрессор, который должен быть рассчитан на переменное напряжение 220 Вт, иметь мощность 0,3 – 0,5 м3 и давление 6 Атм;
- пеногенератор.
Заключения.
Пенобетон — качественный строительный материал, пользуется большим спросом. Имеет простой состав, обеспечивающий его положительные особенности, экологическую безопасность.
его обязательные составляющие и возможные добавки
Дом, построенный из качественных пеноблоков, по комфорту, близок к деревянному. Ведь пеноблок, как и дерево, способен пропускать воздух!
1 Полный состав пеноблока
2 Коротко о составе пеноблока
3 Описание составляющих пеноблока
3.1 Цемент
3.2 Песок
3.3 Вода
3.4 Воздух
3.5 Пенообразователи
3.6 Добавки
3.7 По теме:
Полный состав пеноблока
Ниже таблица, наиболее точно отражающая состав пеноблоков и пропорции пенобетонных смесей в зависимости от плотности пенобетонных изделий.
Состав пеноблока | Объёмная плотность пенобетона, кг/метр куб. |
400 | 600 | 800 | 1000 | 1200 | 1400 | 1600 | 1800 | |
Песок, кг | — | 210 | 420 | 590 | 780 | 950 | 1130 | 1330 |
Цемент, кг | 300 | 310 | 320 | 350 | 360 | 380 | 400 | 420 |
Вода в растворе, кг | 110 | 110 | 120 | 120 | 140 | 150 | 160 | 170 |
Вода в пене, литр | 60 | 54 | 46 | 42 | 35 | 28 | 21 | 15 |
Пенный концентрат, кг | 1,5 | 1,3 | 1,2 | 1,0 | 0,9 | 0,7 | 0,6 | 0,4 |
Пена, литр | 800 | 715 | 630 | 560 | 460 | 370 | 290 | 200 |
Соотношение воды к цементу | 0,57 | 0,53 | 0,49 | 0,46 | 0,48 | 0,47 | 0,45 | 0,44 |
Содержание воздуха, % | 80 | 71 | 63 | 54 | 46 | 37 | 29 | 20 |
Сырая пенобетонная смесь, кг | 471 | 685 | 907 | 1103 | 1316 | 1509 | 1712 | 1935 |
Коротко о составе пеноблока
Вот основные компоненты, из которых делают пеноблоки:
- цемент;
- песок;
- вода;
- воздух;
- пенообразователь;
- улучшающие добавки.
Описание составляющих пеноблока
Теперь о каждой составляющей более подробно.
Цемент
Если ориентироваться на ГОСТ (ГОСТ 25485-89 Бетоны ячеистые), то вяжущим элементом пенобетонного блока может быть только портландцемент (ПЦ) с содержанием силиката кальция порядка 80%. Однако, если особая прочность не нужна, вполне возможно заменить его на шлакопортландцемент (ШПЦ). На объёме, получится неплохая экономия.
Когда есть желание окрасить пеноблок в процессе производства, тогда, для более точного соответствия цвету, цемент лучше выбрать белый (БЦ).
На что, абсолютно точно, следует обратить внимание, так это на дату производства цемента. Как правило, срок годности его — шесть месяцев. Не закупайтесь впрок, на будущее! Использование просроченного цемента может привести к тому, что готовый пеноблок будет обладать прочностью ниже расчётной!
Песок
По ГОСТу, песок должен быть кварцевым не менее, чем на 75%. Посторонние примеси, такие как глина и ил, например, не более 3%.
На практике, используется обычный просеянный строительный песок.
В идеале, его, всё же, лучше промыть и отфильтровать до размера песчинок не более 1,5 мм. Более крупные фракции будут разрушать пенные пузыри в процессе производства.
Вода
ГОСТ «говорит», что воду можно применять только ту, что прошла проверку на соответствие соляного состава.
По факту, вода идёт обыкновенная, очищенная до состояния технической. Примеси нежелательны. Жёсткость, по возможности, минимальная. Во время производства, при применении определённых пенообразователей воду подогревают.
Воздух
Имеются в виду, воздушные пузыри, образовавшиеся в процессе производства. Очевидно, чем их меньше и меньше сами они по размеру, тем тяжелее пенобетонный блок и выше его плотность.
Пенообразователи
Разделяются на натуральные и синтетические.
Натуральные пенообразователи, в основе своей, белковые, протеиновые, известны давно. Производятся из натуральных компонентов, экологически чисты и безопасны.
Синтетические пенообразователи появились относительно недавно. Но используются всё чаще. Расход их значительно меньше, пену образуют более устойчивую, с пенобетонными добавками практически не контактируют. И, в итоге, значительно уменьшают себестоимость готового пеноблока. Правда, не вся синтетика экологически безопасна. Будьте внимательны!
В целом, роль пенообразователя чрезвычайно важна. Критично важно, чтобы сырая пенобетонная масса не оседала, не выделяла влагу. В итоге, от стойкости пены и её несущей способности во время производства пенобетонного блока напрямую зависят плотность и прочность будущего изделия.
Добавки
Из основного стоит перечислить.
- Зола. Используется часто. Особенно, если рядом с производством работает теплоэлектростанция. Зола является отходом после выработки твёрдого топлива. Выгодно экономически. Кроме того, частицы золы небольшие, что позволяет получать более плотные пенобетонные блоки. Обратная сторона повышенной плотности- снижение энергосберегающих характеристик.
Чтобы прочность не пострадала, золы используют не более 30% от общей массы наполнителя.
- Фиброволокно. Повышает прочность готового изделия на 15-25%. Получается усиленный пенобетонный блок, способный выдержать повышенные нагрузки.
- Хлористый кальций. Ускоряет затвердевание пеноблока.
- Известняк. Частично заменяет цемент, не более 30%. Повышает морозостойкость и прочность.
- Микрокремнезем. Увеличивает сопротивление пенобетонного блока к высокой температуре и повышенной кислотности среды.
- Гидрофобизаторы. Даже незначительная их добавка в пенобетонную смесь повышает прочность готовых пеноблоков. Так же улучшается водонепроницаемость и морозостойкость.
Зная теперь, из чего состоит пенобетонный блок, можно попробовать сделать его самому.
Состав пеноблока, пропорции на 1 м3, изготовление в домашних условиях
Подбор пропорций при изготовлении ячеистых марок бетона имеет первостепенное значение, для получения качественных кладочных изделий важно понимать, из чего делают пеноблоки, выполнять все требования технологии при подготовке ингредиентов и соединять их в правильной последовательности. Стандартные соотношения зависят от ожидаемой марки прочности и целевого назначения, при отсутствии точной рецептуры состав подбирается и подтверждается опытным путем.
Оглавление:
- Соотношение компонентов
- Технология изготовления
- Разновидности блоков
Состав и пропорции
В качестве сырьевой массы используется смесь портландцемента с высокой долей силикатов (70-80%), кварцевый песок, синтетический или белковый пенообразователь, чистая вода и затвердитель (хлористый кальций, относящийся к вспомогательным ингредиентам). Требования к компонентам регламентированы ГОСТ 10178, 8736 и 23732, доля посторонних примесей в них сведена к минимуму. Для улучшения прочностных характеристик в состав вводится небольшое количество фибры (полипропиленового волокна в пропорции 0,5 кг на 1 куб) или зола уноса, позволяющая сократить расход вяжущего до 30%.
Плотность смеси для пеноблоков, кг/м3 | Требуемое количество на 1 м3 | |||
Портландцемент не ниже М400, кг | Кварцевый песок, кг | Концентрированный пенообразователь, л | Вода, л | |
400 | 361 | — | 1,2 | 165 |
600 | 155 | 1 | 155 | |
800 | 481 | 205 | 0,95 | 185 |
1000 | 581 | 281 | 0,9 | 215-220 |
1200 | 651 | 381 | 0,85 | 235 |
Ввод хлористого кальция (затвердителя) обусловлен потребностью в ускорении оборачиваемости форм: чем меньше в них находится раствор, тем большее количество изделий можно получить. Выемка блоков без наличия ускорителей схватывания чревата их усадкой и снижением прочности. При необходимости получения составов со средней плотностью оптимальными пропорциями цемента и песка признаны 1:1. При этом рекомендуемое соотношение В/Ц не превышает 0,5, а доля пенообразователя — 4 кг на 1 куб.
В роли образующего поры вещества используются костный или мездровый клей, канифоль, едкий натр и аналогичные составы органического или синтетического происхождения. Применение последних при изготовлении блоков из пенобетона позволяет исключить из линии парогенератор, но их расход и влияние на качество изделий оставляют желать лучшего.
Белковые пенообразователи нуждаются в предварительном подогреве перед активацией, но элементы на их основе имеют минимальную усадку и более прочные стенки ячеек.
Технология производства
Процесс начинается с подбора рецептуры, подготовки ингредиентов, форм и оборудования. В отличие от автоклавного газосиликата в растворе отсутствует алюминиевая пудра, процесс образования пены обеспечивается заливкой воды густого концентрата в отдельном активаторе или чаще баросмесителя. Соединение всех компонентов происходит под избыточным давлением, способствующим получению однородной массы. В последствие она направляется в смазанные специальной эмульсией формы (кассетные по размеру или крупные с разборной опалубкой, позволяющие получить монолит, разрезаемый на отдельные изделия струнами).
К важным требованиям технологии изготовления блоков из пенобетона относят непрерывный контроль за составом смеси и процессом протекания реакций. Процесс соединения ингредиентов длится не более 5 минут, время выдержки в формах зависят от наличия и доли затвердителя и других параметров схватывания. По аналогии с обычными цементосодержащими растворами нуждается в хорошей сушке в нормальных условиях не менее 1 месяца. Исключение делается лишь для элементов, подвергающихся автоклавной обработке с алюминиевой пудрой, но ввод такого оборудования целесообразен только при условии производства в промышленных масштабах.
Виды пеноблоков
В зависимости от технологии изготовления все изделия разделяются на резанные и формовочные, первые ценятся за точность размеров и форм в пределах ±1 мм, вторые – за возможность заливки в домашних условиях, без задействования дорогостоящего оборудования.
Выделяют три основных группы:
- Теплоизоляционные, с удельным весом пенобетона в пределах 300-500 кг/м3 и коэффициентом теплопроводности в сухом состоянии не выше 0,12 Вт/м·°С. При производстве этой подгруппы в состав входит максимальное количество пенообразователя при минимальном В/Ц соотношении и низкой доле инертного наполнителя.
- Конструкционно-теплоизоляционные – от 500 до 900 кг/м3 и от 0,15 до 0,29 Вт/ м·°С. Эта разновидность является самой востребованной в частном строительстве, ее характеристики оптимальны при необходимости возведения домов в пределах 3 этажей.
- Конструкционные – с плотностью в пределах 1000-1200 кг/м3 при коэффициенте теплопроводности от 0,29 до 0,38 Вт/ м·°С. В состав входит максимальное количество песка и цемента, основным назначением является возведение нагружаемых элементов постройки.
Foam Различия: EPS, XPS и EPU
Village Suites, крупнейший проект LEED-Platinum в Канаде, строится с использованием ICF Neopor.
По меньшей мере пять различных типов пены в настоящее время используются для создания изолированных бетонных форм. Вспененный полистирол (EPS) на сегодняшний день является самым популярным выбором, но экструдированный полистирол (XPS) и вспененный полиуретан (EPU) также имеют свое место благодаря уникальным характеристикам этих пен. Смеси Cement-EPS существуют с самого начала индустрии ICF и обладают уникальными характеристиками, которым полностью пенопластовые ICF не могут соответствовать. Новейшая пена ICF, тип пенополистирола с графитовым усилением под названием Neopor, существует на рынке менее двух лет, но она также представляет некоторые интригующие варианты. Как владелец здания, установщик на месте или архитектор, каждая из этих пен имеет свои особенности, которые необходимо учитывать. Полиуретаны Пенополиуретан — единственный из пяти типов пенопластов, обсуждаемых в этой статье, который не основан на шариках полистирола. Жесткий пенополиуретан, пожалуй, наиболее известен как «распыляемая пена», производимая и применяемая такими компаниями, как Icynene и Fomo. Но несколько компаний используют его для производства блоков ICF. Пенополиуретан получается при смешивании двух отдельных ингредиентов, изоцианурата и полиола. Химические вещества бурно реагируют друг с другом, вспениваются и быстро расширяются. Когда реакция подходит к концу, полученное соединение затвердевает, задерживая миллионы крошечных пузырьков газа. На самом деле около 97% полиуретана задерживают газы. Полученный продукт легкий, прочный и предлагает впечатляющие показатели изоляции. Жесткий пенополиуретан имеет один из самых низких показателей теплопроводности среди всех утеплителей. Тип полиуретана, используемый для ICF, имеет R-значение 5,9 на дюйм, что на 50% больше, чем у обычного пенополистирола.
Полиуретан также прочнее и плотнее, чем пенополистирол, а это означает, что формы могут выдерживать небрежное обращение на стройплощадке. Их также легче наливать, практически без риска деформаций или разрывов. Две ведущие марки полиуретановых ICF — ThermoBlock и InsuLock — очень похожи. Оба имеют размеры 8x8x32 дюйма, с вертикальными колоннами диаметром 5,5 дюйма, которые образуют структуру типа стоек и балок. В то время как кубический ярд бетона заполнит почти 80 квадратных футов стены, а полиуретан обеспечивает протестированное значение R-значения R-38, у блоков есть недостатки. Стоечно-балочная система требует специальной инженерии для соответствия местным строительным нормам, и, поскольку ни одна из систем не имеет встроенных полос обрешетки, прикрепление отделки может быть проблематичным. EPS Композиты Композитные ICF изготавливаются из смеси пенополистирола и портландцемента. Эта технология имеет проверенную репутацию, насчитывающую более 40 лет.
Карл Холик запатентовал первый такой блок, Rastra, еще в 1972 году. Вариации производятся и продаются компаниями Apex, Tech Block, Perform Wall и Cempo. По сути, необработанные гранулы пенополистирола покрывают порошкообразным портландцементом и запатентованным агентом, а затем расширяют с помощью пара в форме. Влага частично расширяет шарики и связывает их с цементом, что делает шарик пожаробезопасным. Из-за цемента композитные ICF непроницаемы для плесени, термитов и других вредителей, без каких-либо пестицидов или специальной обработки, которая может просочиться в почву. Кроме того, они полностью пожаробезопасны, поэтому для соответствия нормам пожарной безопасности не требуется дополнительная обшивка. Композитные ICF принимают гипсокартон, штукатурку и акриловые полимеры (иногда называемые текстурированными акриловыми покрытиями), наносимые непосредственно на блок. Они также значительно плотнее и тяжелее, чем их полностью пенопластовые аналоги. Блоки Rastra длиной 10 футов весят от 150 до 250 фунтов каждый.
Обычный блок размером 48 x 16 дюймов весит от 25 до 40 фунтов, в зависимости от толщины стенки. Все композитные ICF, представленные в настоящее время на рынке, представляют собой системы экранных решеток, что означает, что бетон образует ряд колонн и балок, обычно через каждые 16 дюймов по вертикали и горизонтали. Это означает, что кубический ярд бетона заполнит почти 100 кв. футов стены, что сэкономит 50% затрат на бетон. Из-за их плотности и веса стены высотой до 10 футов можно заливать без крепления. Они также выдерживают бетон с высокой посадкой или SCC, поэтому попадание смеси в горизонтальные балки не является проблемой. Наконец, блоки достаточно плотные, чтобы гвозди и шурупы держались, где бы они ни были забиты, что значительно упрощает нанесение внутренней и внешней отделки. Их можно резать и формовать стандартными столярными инструментами. Вспомогательные канавки можно резать пилой или фрезером, но не горячим ножом. EPS Пенополистирол и экструдированный полистирол изготавливаются из одного и того же пластика, но используют разные технологии производства.
Для изготовления блоков из пенополистирола рыхлые гранулы нерасширенного полистирола, содержащие жидкий пентан, смешивают с вспенивающим агентом. Затем смесь нагревают, в результате чего шарики увеличиваются во много раз по сравнению с их первоначальным размером. Частично расширенные шарики помещают в форму ICF.
Новые ICF выкатываются из формовочной машины.
Затем формовщик впрыскивает пар высокой температуры и высокого давления, который еще больше расширяет шарики и полностью заполняет форму. Конечным результатом являются пеноблоки или панели. Антипирены, инсектициды и другие химические вещества почти всегда добавляются в процессе формования для создания лучшего продукта. Некоторые производители используют гранулы пенополистирола с красителем. Quad-Lock и Nudura используют зеленый цвет; Fold-Form от Owen-Corning предпочитает розовый цвет. Этот краситель не меняет характеристик пены, это просто маркетинговый инструмент для дифференциации бренда.
Эта iForm от Reward является типичным примером стандартного блока ICF, сделанного из EPS.
Физические свойства пенополистирола варьируются в зависимости от типа используемого шарика и могут формоваться с различной плотностью для удовлетворения конкретных требований ICF. Увеличение плотности пены также обеспечивает более высокое значение R на дюйм и повышенную прочность, но это дорого и требует больше материала. Вот почему, несмотря на то, что значения R могут варьироваться от 3,8 до 4,3 на дюйм толщины, почти все EPS, используемые в ICF, находятся в нижней части шкалы. Хорошо больше 95% всех проданных ICF используют формованный пенополистирол. Хотя это не самая прочная, самая изолирующая или термостойкая альтернатива, она предлагает исключительную ценность. Он популярен, потому что обеспечивает достаточную прочность, плотность, звукоизоляцию и R-значение по самой разумной цене. ЭПС XPS, или экструдированный полистирол, представляет собой пенопласт с закрытыми порами, в котором вместо формования используется процесс экструзии. На самом базовом уровне процесс похож на продавливание детской глины через маленькое отверстие. Конечно, реальный процесс XPS намного сложнее. Он начинается с тех же гранул, которые используются для производства пенополистирола, но гранулы смешиваются с различными химическими веществами для их разжижения. Затем в смесь вводят вспенивающий агент, образуя пузырьки газа. Затем густая вспенивающаяся жидкость пропускается через формовочную головку, создавая непрерывный «лист» пены, который можно производить с различной плотностью и толщиной. Вместо того, чтобы формовать окончательную форму, XPS разрезается на окончательные размеры.
Эта формовочная матрица используется для формирования панелей XPS. Вспенивающаяся жидкость вытесняется через прямоугольное отверстие справа от машины.
XPS дороже, чем EPS — в некоторых случаях на 50% дороже — и поэтому встречается не так часто. Тем не менее, он более чем в два раза прочнее и обеспечивает примерно на 25% большую изоляцию при той же толщине (около R-5 на дюйм). Он также гораздо более постоянен по плотности и имеет более высокую прочность на сжатие, чем пенополистирол. Nudura, TF System, Lite-Form и ArmoPanel предлагают панели XPS в качестве опции. Неопор Новейшей пеной, используемой для ICF, является Neopor, тип пенополистирола, в котором используются запатентованные черные шарики от BASF. В настоящее время единственным ICF на рынке, изготовленным из Neopor, является серия Logix Platinum. В отличие от обычного пенополистирола, Неопор содержит порошкообразный графит, придающий пене неповторимый серый цвет. В отличие от красителей, о которых говорилось ранее, графит значительно влияет на характеристики пены. Neopor примерно на 33% лучше изолирует, чем обычный пенополистирол, а также отражает больше тепла. ICF, изготовленные из Neopor, появились на рынке Северной Америки совсем недавно, но они уже вызывают ажиотаж. Комплекс Village Suites, один из крупнейших зарегистрированных проектов ICF и крупнейший на сегодняшний день проект с платиновым сертификатом LEED в Канаде, строится с помощью Logix Platinum.
Установщики утверждают, что серый цвет снижает нагрузку на глаза и уменьшает блики. Производители надеются, что это улучшит продажи. «Существует мнение, что Neopor более совершенен, — говорит Тобиас Холд, менеджер по маркетингу пеноматериалов в BASF. «Я думаю, что люди принимают его легче, потому что он не похож на обычный пенопласт». Хоулд говорит, что Neopor стоит примерно на 5% дороже, чем обычные белые шарики. Выбор Согласно техническому описанию PCA по этому вопросу: «Все типы жесткой пеноизоляции обеспечивают надежную работу при использовании в ICF… Каждый пеноматериал обладает уникальными эксплуатационными свойствами, зависящими от плотности материала, размеров и других факторов». Все пять систем, описанных в этой статье, имеют общие преимущества перед изоляцией из стекловолокна или целлюлозы. Жесткий пенополистирол и пенополиуретан не содержат формальдегида и не вызывают проблем с дыханием или раздражения кожи, в отличие от некоторых изоляционных материалов на основе волокон.
При тестировании качества воздуха в помещении вредных выбросов обнаружено не было. Они водонепроницаемы, и в случае затопления их легче восстановить. Композитный пенополистирол полностью пожаробезопасен, а другие системы имеют антипирен, предназначенный для минимизации распространения пламени. Испытания на сжигание пенополистирола показывают, что выбросы не более токсичны, чем выбросы от сжигания древесины. Принимая окончательное решение, PCA кратко предупреждает: «При сравнении эффективности одной системы ICF с другой может оказаться полезным базовое понимание различных вспененных материалов. Однако наиболее важно выбрать наилучшую систему ICF для ваших конкретных нужд, а не для конкретного типа пены. Не существует какого-то одного «лучшего» материала, но пены предлагают переменные характеристики, которые могут помочь объяснить различия между продуктами ICF».
Состав пеноблока. Проекты одноэтажных домов из пеноблоков. Производство пеноблоков
Пеноблок представляет собой пористый ячеистый материал, который имеет такую структуру за счет воздушных пузырьков, распределенных по всему объему. Эти изделия являются наиболее доступными и легкими среди тех, что сегодня предлагает рынок и предназначены для строительства зданий и сооружений. Используется пеноблок также для тепло-, а также звукоизоляции стен.
Если вы тоже решили использовать этот материал, то должны знать, из чего состоит пеноблок, и по какой технологии он изготовлен.
Ингредиентный состав
Для получения прочного и качественного пеноблока необходимо придерживаться ГОСТов и технологии производства. В состав пеноблока входят следующие ингредиенты:
- Портландцемент;
- песок;
- Пенообразователи;
- Добавки.
Что касается портландцемента, то он действует как вяжущее средство. Марка, используемая для баротехнологии, – М-500. Если в основу производства положена классическая технология, то допускается использование следующих марок портландцемента:
- М500 Д20.
- М400 Д0.
- М400 Д20.
В роли заполнителя выступает песок, может содержать глинистые примеси в объеме до 3% и кварц – от 75% и выше. Одним из компонентов является вода. Также используются пенообразователи. Они могут быть синтетическими или белковыми. Первые используются в баротехнологии, а вторые – в классическом способе производства. Белковые пенообразователи, которые еще называют белковыми, являются лучшими, поскольку позволяют получить качественную пену, не способную нанести вред здоровью человека.
Дополнительные ингредиенты
Для того, чтобы материал затвердел как можно быстрее, используются специальные добавки. В зависимости от технологии могут использоваться различные смазки форм. Знакомясь с составом пеноблока, вы узнаете, что пенообразователи изготавливаются на основе костного клея, сосновой канифоли, мездевского клея, едкого натра, чистящей пасты и других компонентов.
Пример пеноблока
Потребителям будет интересно узнать, каков примерный состав пенобетона для получения одного кубометра материала. Основой послужит портландцемент марки ПЦ 500 Д0. Для получения пеноблока М400 необходимо использовать 300 кг цемента, 160 литров воды и 0,85 кг пенообразователя. Песок в данном случае не применяется.
Для производства пенобетона М-600 необходимо взять песка 210 кг, цемента 330 кг, воды 180 литров и пенообразователя 1,1 кг. Важно изучить состав пеноблока, если вы планируете получать материал М-800. При этом используется 340 кг песка, 400 кг цемента, 230 л воды и пенообразователь в количестве 1,1 кг.
Производство пеноблоков
Производство пеноблоков требует соблюдения технологии. Он включает в себя приготовление раствора из песка и цемента, затворение пенного состава и формирование блоков. Для работы понадобятся следующие инструменты и материалы:
- бетономешалка;
- Пеногенератор;
- Форма или емкость;
- цемент;
- Отвердитель или песок;
- Вспениватель.
На первом этапе готовят воду, цемент и песок. Необходимо следовать классической схеме замешивания традиционного раствора. На следующем этапе постепенно добавляют пенообразователь. Некоторые специалисты рекомендуют использовать его синтетическую разновидность или аналог, который готовят из столярного клея, канифоли и гидроксида натрия.
Для добавления ингредиенты смешивают и нагревают. Такую смесь можно приготовить только при наличии пеногенератора. Состав соединяется с бетоном, после чего формируются пеноблоки. Производство пеноблока предполагает использование мелкого песка, не имеющего глинистых примесей. Воду можно использовать водопроводную, она не должна содержать кислот и солей.
Особенности раствора для пеноблока
Для производства пеноблоков следует использовать заводскую бетономешалку, так как самодельные устройства не всегда способны помочь добиться желаемого результата. Для изготовления форм подойдет фанера, при этом важно соблюдать размеры. Для ускорения затвердевания препарата следует использовать соответствующие вещества. Среди них особой популярностью пользуется хлорид кальция. Добавляется в смесь пенобетона и пенобетона. Объем этого вещества составляет примерно 2% от общей массы.
Состав распределяется по формам, а готовая продукция раскладывается на поддоны для отправки на стройплощадку. Техника замешивания раствора предусматривает засыпку речного песка и цемента в бетономешалку, постепенно добавляя в состав воду и пенообразователь. Смесь хорошо перемешивается, в нее добавляется отвердитель. Через 2 минуты раствор будет готов для лепки. Прежде чем приступить к формированию изделий, следует подготовить тару. Формы очищают от мусора или смеси, а затем внутренние стенки обрабатывают специальным составом без масел. Если нанести смазку, готовый блок можно будет легко извлечь из формы. Для этих целей контейнеры изнутри покрыты полиэтиленом. Изделия также могут быть изготовлены методом резки.
Размеры и плотность пеноблока
Что такое пеноблоки, вы уже знаете. Однако важно знать больше о других параметрах, например, о плотности. Последняя характеристика влияет на назначение. Если материал относится к плотности в пределах М1000-М1200, то он является конструкционным. Конструкционно-теплоизоляционные блоки имеют плотность от М500 до М900. Что касается теплоизоляционных изделий, то их плотность равна М300-М500.
По способу изготовления описываемые блоки можно разделить на литые и резные. Последние позволяют получать отдельные изделия из единого массива пенобетона. Формоблоки из пеноблоков заливают в формы с перегородками. Пеноблок 600х400х300 мм является стандартным, а его вес варьируется от 11 до 19 г.кг, что справедливо для теплоизоляционных изделий. Для конструкционных пеноблоков масса колеблется от 39 до 47 кг.
Проекты домов
Пеноблоки, размеры и цены которых указаны в статье и должны быть известны потребителю, довольно часто составляют основу одноэтажных домов. Перед составлением проекта потребуется определить только несущие стены. Обычно это центральные и внешние стены, что актуально для случая, когда дом не более 6 м. Все остальные разделы можно настроить по своему желанию.
Если ширина дома довольно внушительная и превышает 12 м, стоит подумать о расположении несущих конструкций, т.к. при такой ширине крыша будет иметь значительную массу, что вызовет повышенное давление на наружную несущие стены. Специалисты в этом случае рекомендуют рассматривать проекты с мансардой или делать дома менее широкими.
При разработке проектов одноэтажных домов из пеноблоков необходимо помнить, что несущие стены должны располагаться на фундаменте. Как раз на полу обычно устанавливают перегородки, потому что особой нагрузки они не несут. В этом случае вы обеспечите устойчивость стен. В качестве примера можно рассмотреть дом, в котором будет три жилых комнаты, один общий коридор и санузел. Одна из небольших комнат имеет площадь 8 м 2 , большая спальня площадью 9,1 м 2 . Что касается гостиной, то ее площадь может быть 11,1 м 2 . Общий коридор расположен на площади 5,2 м 2 . Санузел можно расположить в угловой части дома, он будет иметь площадь 7 м 2 .
Составляя проекты одноэтажных домов из пеноблоков, специалисты нередко делают жилые помещения большими. Одним из примеров является вариант дома с холлом на 26,3 м 2 . Санузел раздельный по проекту, санузел площадью 2,7 м 2 , санузел 4 м 2 . Последняя находится рядом с кухней по адресу 7 м 2 . Общий коридор расположен на площади 4,6 м 2 , он переходит в небольшой коридор, который соединяет гостиную и спальню. Последняя комната имеет площадь 12,1 м 2 .
Вместо заключения: стоимость пеноблоков
Размеры и цены пеноблоков – характеристики, которые больше других интересуют потребителей. Купить изделие размерами 600 х 250 х 375 мм можно по цене 3600 рублей за кубометр. За блок весом 120 кг, размеры которого 600 х 250 х 200 мм, придется заплатить 120 рублей. Когда вы собираетесь строить дом из пеноблоков, вы можете купить следующие изделия: 600 х 250 х 150 мм и 600 х 250 х 125 мм. Цена таких стройматериалов будет равна 90 и 80 рублей за штуку соответственно.
Клей для пеноблоков – обзор производителей, инструкция
Содержимое:
- Какой клей лучше цементного раствора?
- Состав и характеристики клея
- Расход клея на 1 м3
- Производители и цены
- Как класть пеноблок на клей?
На протяжении последних десятилетий пеноблоки занимают лидирующие позиции среди строительных материалов. Их используют при строительстве жилых домов и подсобных помещений, возведении межкомнатных перегородок, для утепления и улучшения звукоизоляции. Для соединения пенобетонных кирпичей между собой используется клей для пеноблоков, который не только обеспечивает прочное и долговечное сцепление, но и позволяет полностью сохранить все положительные качества газобетона.
Какой клей лучше цементного раствора?
Пеноблоки изготавливаются из пенобетона, представляющего собой смесь цемента, песка и воды с добавлением пенообразователя. В результате такого соединения получается легкий ячеистый материал, который используется для строительства различных зданий и сооружений. Пеноблок отличается от кирпича структурой, размерами, весом. Технология укладки этого материала также отличается от возведения кирпичной стены, поэтому к составу, используемому для соединения отдельных элементов, предъявляются определенные требования.
Дело в том, что теплоизоляционные свойства пенобетона намного выше, чем эти показатели у цементного раствора. Слои цемента толщиной 1-1,5 см делают конструкцию легко продуваемой. В результате приходится устраивать дополнительную теплоизоляцию. Специальный клеевой состав с добавками, повышающими эластичность и водостойкость, образует тонкий (3 мм) герметичный слой и успешно решает эту проблему.
Клей для пеноблоков имеет ряд преимуществ, отличающих его от цементного раствора.
- Высокая прочность сцепления.
- Быстрое отверждение клея сокращает время строительства.
- Невозможность образования грибка и плесени.
- При резком перепаде температур клеевой слой не трескается и не разрушается.
- Удобство и простота использования клея.
- Экономичность – клей дороже цемента, но его потребуется в разы меньше, в результате чего стоимость кладки будет ниже.
Важно!
В состав цемента входит большое количество воды, которая при установке узла начинает впитываться в пористую структуру. Чтобы этого избежать, приходится каждый ряд обрабатывать специальной водоотталкивающей грунтовкой, на что уходит дополнительное время и деньги.
Состав и технические характеристики клея
Любой клей, используемый для склеивания пеноблоков, содержит цемент, песок и различные добавки, улучшающие характеристики изделия и усиливающие те или иные свойства клея.
В состав сухой смеси входят следующие компоненты:
- песок кварцевый мелкоизмельченный – позволяет выполнить шов шириной не более двух миллиметров;
- Портландцемент – обеспечивает высочайшую прочность сцепления и быстрое затвердевание клея;
- добавки из полимеров – делают состав более гибким и податливым, способным проникать в самые труднодоступные щели и полости, всегда присутствующие на поверхности пеноблока; пластичный шов предотвращает образование трещин при резком перепаде температур;
- добавки, улучшающие водоотталкивающие свойства клея и препятствующие образованию плесени.
На рынке строительных материалов можно найти клей летний и зимний. Первый вид клея содержит белый цемент и используется при температуре воздуха не ниже +5°С. Зимний клей за счет антифризных добавок способен работать даже при температуре -30°С.
Клей для пеноблоков в продается в виде сухой смеси, расфасованной в мешки по 25 кг.
Расход клея на 1 м
3Многие производители указывают на упаковке, сколько клея необходимо на 1 м 2 кладки. Прежде чем купить клей, нужно изучить этикетку и рассчитать, сколько мешков понадобится для сборки того или иного объекта.
При этом не следует забывать, что нормы расхода, указанные производителем, являются усредненными, а фактические цифры складываются в зависимости от многих обстоятельств, таких как:
- уровень квалификации строителя;
- температура воздуха при кладочных работах;
- ровность поверхности пеноблока;
- количество и толщина швов.
Обычно нормативный расход клея при толщине слоя 1 мм составляет 1,3–1,5 кг на 1 м 2 площади кладки. Чтобы соединение было прочным и надежным, клеевой слой должен иметь толщину 3-5 мм. Так вот, если взять максимум, то на 1 м 2 уйдет 6,5-7,5 кг смеси.
Исходя из того, что высота стандартного пеноблока около 20 см, можно рассчитать количество слоев в кубометре. Их будет пять. Максимальное количество клея, необходимое для кладки 1 м 3 стены, составит 32,5-37,5 кг, то есть полтора мешка сухой смеси.
Наконечник
После завершения кладки рекомендуется повторно проклеить наружные швы клеем. Необходимо предусмотреть это и купить клей с запасом.
Производители и цены
Все клеи, используемые для соединения блоков, имеют примерно одинаковый состав. Отличие только в пропорции между наполнителем и полимерными добавками. Поэтому при выборе клея для пеноблоков особое внимание следует обращать на температуру, при которой используется состав и подходит ли он для строительства в конкретных условиях.
Специалисты советуют при покупке клея соблюдать правила:
- Не покупайте подозрительно дешевый товар;
- отдавайте предпочтение проверенным производителям;
- учитывать сезон работы;
- смесь берем с запасом.
Здесь представлены одни из самых популярных клеевых составов, изготовленные известными производителями и заслужившие положительные отзывы специалистов. Цены указаны за упаковку (25 кг).
- Практик бергауф (зимний) – 274 рубля;
- Aeroc – 179 руб.;
- Ceresit CT 21 -265 руб.;
- Founces Selfform T 112 – 167 руб.;
- Практик бергауф – 165 руб.;
- Волма – 190 руб.
Многие специалисты признали клей «Основанный Селфформ» лучшим клеевым составом для работы в летний период. Среди морозостойких лучшими характеристиками обладает зимний клей Aeroc. Соединение, образованное с этим продуктом, устойчиво к температурным изменениям. Работать с составом просто и удобно, так как клей схватывается не сразу и есть время подкорректировать расположение блока.
Как ставить пеноблок на клей?
Перед началом возведения стены из пеноблоков необходимо правильно приготовить клеевой состав. На упаковке с клеем имеется подробная инструкция, которой следует руководствоваться при смешивании клеевого порошка с водой.
Для приготовления качественного раствора без комков и сгустков лучше использовать строительный миксер со специальной насадкой в виде бабочки. В качестве емкости для перемешивания можно взять обычное ведро.
Через два часа с момента приготовления клей постепенно загустеет и затвердеет, поэтому за один раз желательно приготовить столько смеси, сколько вам потребуется для двухчасовой работы. Конечно, можно разбавить загустевший клей небольшим количеством воды, но качество продукта заметно снизится, так как будут нарушены пропорции между компонентами.
Важно!
Приготовление клея из сухой смеси требует точного соблюдения соотношения количества воды и порошка, указанного в инструкции.
Перед началом кладки необходимо провести необходимую разметку. Для этого по углам будущей постройки укладывают пеноблоки и между ними натягивают леску. Верхняя часть блока должна располагаться строго по уровню.
Первый ряд блоков укладывают на фундамент на цементно-песчаный раствор и только начиная со второго ряда используют клеевую смесь. Если есть такая возможность, лучше выбирать блоки с ровной поверхностью, без глубоких впадин и выпуклостей. Это сделает шов более тонким. Слишком грубую поверхность можно отшлифовать. Перед укладкой сдуйте пыль с агрегата и удалите мелкий мусор.
Клей лучше наносить зубчатым шпателем. Равномерными плавными движениями проклеивают верхнюю и боковые стороны пеноблока клеем, удаляя остатки в ведро. Толщина слоя должна быть 2-3 мм. Чтобы блок плавно встал на место, его можно аккуратно подправить резиновой киянкой.
Важно!
Необходимо проверять вертикальность стены и ровность кладки после приклеивания каждых 3-4 пеноблоков.
Клей начинает затвердевать через 15 минут после нанесения. Если что-то пошло не так, вы все равно можете исправить проблему в течение четверти часа.
Если вы решили строить дом из пеноблоков, необходимо уделить особое внимание выбору клея. Ведь от герметичности, прочности и водонепроницаемости соединительного шва будет зависеть качество и долговечность постройки.
Исследование механических характеристик и долговечности пенобетона с летучей золой
- Список журналов
- Материалы (Базель)
- PMC9457397
Материалы (Базель). 2022 сен; 15(17): 6077.
Опубликовано в Интернете 1 сентября 2022 г. doi: 10.3390/ma15176077
, 1 , 1, 2, 3, * , 1 , 1 , 1 и 1
Angelo Marcello Tarantino, Academic Editor
Информация о статье Angelo и лицензии Disclainter
- 9999999999999.
(1)
Метод определения плотности в сухом состоянии осуществляется по «Пенобетон» JG/T266-2011 [34], формула расчета:
ρ = М / В × 10 3
(1)
где ρ – сухая плотность образца ТИТЭ, кг/м 3 ; M – масса при высыхании навески ЭТТ, г; V – объем образца ТКЭ, мм 3 .
(2)
Испытание на прочность при сжатии
(4)
Ультразвуковой контроль
(5)
Исследование пористой структуры
(1)
Результаты испытаний различных дозировок пероксида водорода на параметры прочности на сжатие, теплопроводности и пористой структуры ВАТЭ показали, что прочность на сжатие и теплопроводность ВИТЭ снижались с увеличением дозировки пероксида водорода, и пиковая прочность на сжатие составила 0,670 МПа при дозировке перекиси водорода 4%. Теплопроводность составила 0,0580 Вт/(м·К) при дозировке перекиси водорода 5%. Пористость и средний размер пор FAFC положительно коррелируют с дозировкой перекиси водорода, а распределение пор по размерам мигрирует в сторону больших пор. Поэтому рекомендуется, чтобы доза перекиси водорода составляла 5%.
(2)
При изучении влияния различных дозировок микрокремнезема на прочность при сжатии, теплопроводность и параметры пористой структуры FAFC при 5% пероксида водорода плотность сухой FAFC продемонстрировала тенденцию к снижению с увеличением увеличение дозировки диоксида кремния, а все остальные показатели достигли максимума.
Пиковая прочность на сжатие составила 0,625 МПа, а пиковая теплопроводность составила 0,0596 Вт/(м·К) при дозировке микрокремнезема 4%. Пористость, средний размер пор и коэффициент формы пор FAFC показали тенденцию к снижению с увеличением дозировки микрокремнезема. Распределение пор по размерам мигрирует сначала в направлении мелких пор, а затем в направлении крупных пор. Учитывая все свойства, рекомендуемая доза микрокремнезема составляет 4%.
(3)
Мы также исследовали влияние дозировки полипропиленового волокна на параметры прочности при сжатии, теплопроводности и пористой структуры FAFC с 5% перекиси водорода и 4% микрокремнезема. Прочность на сжатие FAFC, легированных полипропиленовыми волокнами, была лучше, чем без легирования. Пиковая прочность на сжатие составила 0,679 МПа, а пиковая теплопроводность – 0,0610 Вт/(м·К) при дозировке полипропиленового волокна 0,1%. При дозировке полипропиленовых волокон 0,1 % пористость, средний размер пор и коэффициент формы пор FAFC были самыми низкими — 83,24 %, 5290,05 мкм и 1,218 соответственно, и распределение пор по размерам сначала мигрировало в направлении малых пор, а затем в направлении крупных пор.
Поэтому рекомендуется дозировка полипропиленового волокна 0,1%.
(4)
С ростом числа циклов замораживания-оттаивания индекс поврежденности () ТЖК увеличивался. Тем не менее, с увеличением добавки полипропиленового волокна его показатель поврежденности () постепенно снижался, а скорость потери массы, скорость потери прочности на сжатие и показатель поврежденности тестовых блоков FAFC были наименьшими при добавке полипропиленовых волокон 0,4 %. Таким образом, полипропиленовые волокна могут улучшить морозостойкость FAFC.
- Полиуретан
- Пена с закрытыми порами
- Пена с эффектом памяти
- Латексная пена
- Batch Foam Machines:
- Batch foam machines make PU пена в небольших количествах небольшими партиями.
- Эти машины для производства пенопласта очень эффективны. И они производят 30-40 высококачественных блоков пенополиуретана за один цикл.
- Эта машина также доступна по цене из-за меньшего объема производства.
- Несмотря на производство в небольших количествах, он может производить пеноблоки высокой плотности.
- Машина состоит из двигателя, который обеспечивает равномерное перемешивание, в результате чего получается однородная смесь.
- Использует инновационные методы, которые являются эффективными и высокоэффективными.
- Пеногенераторы непрерывного действия:
- При значительных затратах на настройку, которые поначалу кажутся сложными, Пеногенератор непрерывного действия также предлагает привлекательные преимущества.
- Эта машина в основном нацелена на максимальное увеличение производства
- В отличие от машин периодического действия, она постоянно производит пену, пока она не закончится.
- Поскольку эта машина производит пену в больших количествах, она очень экономична.
- Постоянные поставки качественной пены помогают завоевать хорошую репутацию на потребительском рынке.
- Поскольку установка этих машин стоит дорого, у них очень мало конкурентов, и как только вы прочно закрепитесь на рынке, им будет сложно догнать вас.
- Станки для контурной резки пенопласта
- Станки для резки пенопласта известны своим опытом и высокой скоростью.
- Они делают разрезы любой геометрической формы, используя в качестве режущих инструментов различные материалы, такие как ленточные ножи или проволоку.
- Существуют вертикальные и горизонтальные машины контурной резки пенопласта. В зависимости от типа машины различают качающийся нож или гладкий вращающийся нож.
- Эта машина также может резать пенополиуретан очень высокой плотности.
- Машина проста в эксплуатации и поэтому удобна в использовании.
- Машина имеет двойную операционную систему, т. е. помимо автоматического управления ею также можно управлять вручную без специального обучения.
- Вертикальная машина для резки пенопласта:
- Эти машины являются одним из основных видов оборудования в индустрии обработки пенопласта.
- Гладкий или зубчатый ленточный нож или ленточная пила на этом станке перемещаются вертикально.
- Этот станок особенно необходим для окантовки полиуретановых блоков или изготовления прямоугольных плит из пенопласта.
- Горизонтальная машина для резки пенопласта:
- Горизонтальные машины для резки пенопласта могут нарезать пенополиуретан на тонкие или толстые пластины без ущерба для качества.
- Для сравнения, эти машины имеют более прочную конструкцию.
- В большинстве машин разделительные пластины необходимо вынимать вручную.
- Они считаются идеальными для матрасов.
Блок заклинания купола
Ограждение
SPA Grotto
0002 Тротуарная брусчатка
Приподнятая садовая грядка
Стеновые панели
. Информация о статье. Примечания Capyright и лицензия Disclainter
9035 9035Химический состав (%) | Physical Indicators | ||
---|---|---|---|
SiO 2 | 22.36 | Fineness (%) | 1.![]() |
SO 3 | 2.86 | Loss on ignition (%) | 1.4 |
CaO | 57,25 | Время коагуляции (мин) | |
K 2 O | 0.76 | Initial condensation | 200 |
MgO | 1.![]() | Final condensation | 245 |
Al 2 O 3 | 7.70 | Compressive strength (MPa) | |
Na 2 O | 0.41 | 3 d | 25.47 |
Fe 2 O 3 | 5.10 | 28 д | 42.![]() |
Открыть в отдельном окне
Таблица 2
Химический состав и физические показатели золы-уноса.
Химический состав (%) | Физические индикаторы | ||
---|---|---|---|
SiO 2 | 28.56 | Fineness (%) | 17.8 |
SO 3 | 6.![]() | ||
TiO 2 | 1.07 | Loss on ignition (%) | 2.07 |
CaO | 12.28 | ||
K 2 O | 1.69 | Water content (%) | 0.33 |
MgO | 2.10 | ||
Al 2 O 3 | 37.![]() | Water demand ratio (%) | 97 |
Fe 2 O 3 | 12.80 |
Открыть в отдельном окне
Таблица 3
Химический состав и физический показатель микрокремнезема.
Chemical Composition (%) | Fineness (m 2 /kg) | 28 d Activity Index (%) | ||||||
---|---|---|---|---|---|---|---|---|
SiO 2 | Al 2 O 3 | Fe 2 O 3 | Na 2 O | CaO | MgO | K 2 O | 18,000 | 95 |
97.![]() | 2.87 | 4.91 | 4.12 | 1.11 | 2.87 | 5.64 |
Открыть в отдельном окне
2.2. Соотношение соответствия
Соответствующее количество микрокремнезема и дозировка полипропиленового волокна могут значительно улучшить прочность на сжатие и прочность на растяжение при раскалывании FAFC, а также улучшить хрупкость FAFC. Таким образом, это испытание было разработано для проведения исследования физико-механических свойств и пористой структуры FAFC с тремя переменными: дозировка перекиси водорода, дозировка микрокремнезема и дозировка полипропиленового волокна. Конкретный коэффициент соответствия показан на .
Таблица 4
Соотношение испытательной смеси пенобетона с летучей золой.
Сериал Номер | Мюмовая зола (%) | Силикарный флам (%/кг · м −3 ) | ГВУРД ПЕРЕЙСИД 9067 (%/KG/KG/KG/KG/KG/KG/KG/KG/KG/KG/KG/KG/KG/KG/KG). Fiber (%/kg·m −3 ) | |
---|---|---|---|---|
1 | 40/83.3 | 6/12.5 | 4/8.3 | 0/0 |
2 | 40/83.![]() | 6/12.5 | 4.5/9.3 | 0/0 |
3 | 40/83.3 | 6/12.5 | 5/10.4 | 0/0 |
4 | 40/83.3 | 6/12.5 | 5.5/11.4 | 0/0 |
5 | 40/83.![]() | 6/12.5 | 6/12.5 | 0/0 |
6 | 40/83.3 | 0/0 | 5/10,4 | 0/0 |
7 | 40/83.3 | 2/4.1 | 5/10.4 | 0/0 |
8 | 40/83.![]() | 4/8.3 | 5/10.4 | 0/0 |
9 | 40/83.3 | 8/16.6 | 5/10.4 | 0/0 |
10 | 40/83.3 | 4/8.3 | 5/10.4 | 0.1/0.2 |
11 | 40/83,3 | 4/8,3 | 5/10,4 | 0,2/0,4 |
12 | 40/83.![]() | 4/8.3 | 5/10.4 | 0.3/0.6 |
13 | 40/83.3 | 4/8.3 | 5/10.4 | 0.4/0.8 |
Открыть в отдельном окне
2.3. Подготовка образцов
Физическое вспенивание: водный раствор пенообразователя преобразуется в пену методом механического перемешивания, а затем пена добавляется в состав суспензии. Принцип физического вспенивания заключается в формировании структуры двойного электронного слоя в растворителе с помощью поверхностно-активного вещества или поверхностно-активного вещества и обертывании воздуха для образования пузырьков. Судя по молекулярной микроструктуре, поверхностно-активные вещества состоят из двух отдельных частей: одна представляет собой олеофильную группу (также известную как гидрофобная группа), а другая представляет собой гидрофильную группу (также известную как олеофобная группа). Исходя из структурных характеристик поверхностно-активных веществ, когда поверхностно-активные вещества растворяются в растворителе, гидрофильная группа притягивается к молекулам воды, а гидрофильная группа отталкивается от молекул воды. Для достижения стабильного состояния ПАВ занимает только поверхность раствора, олеофильная основа переходит в газовую фазу, гидрофильная основа погружается вглубь воды, а пенообразователь растворяется в воде. Механическое перемешивание вводит пузырьки воздуха, что приводит к однопузырьковой пене. Ключом к образованию химически пенобетона является то, что скорость вспенивания пенообразователя соответствует скорости схватывания и затвердевания раствора, и достигается динамическое равновесие.
Во-первых, к суспензии добавляют пенообразователь и тщательно перемешивают, чтобы обеспечить равномерное распределение пенообразователя. Под действием инициатора пенообразователь продолжает вступать в химические реакции с образованием газов, образуя многочисленные, равномерно распределенные независимые источники газа. Затем в некоторых местах вокруг источника газа постепенно создается давление воздуха. Когда давление газа превышает предельное напряжение сдвига пульпы (сумма сопротивления вязкости и гидростатического давления), источник газа начинает быстро расширяться, образуя самостоятельный пузырек, и пульпа начинает расширяться. В процессе надувания воздухом из-за гидратационных гелевых материалов консистенция пульпы увеличивается, поэтому расширение для преодоления сопротивления также увеличивается; в то же время, по мере расходования реакционного материала расширение потенциальной мощности меньше, поэтому процесс надувания смещается с ускорения на плавный, медленный темп, и процесс постепенно становится застойным.
Наконец, расширение завершено и получен пенобетон. Метод химического вспенивания отличается от метода физического вспенивания тем, что вещества вступают в реакцию и образуют новую газовую пену. Основной характеристикой химического вспенивания являются пузырьки без стенки пузыря и низкая стабильность. Продукты гидратации цемента и других материалов должны быть основным материалом и могут быть стабильными, а разница в давлении размера диаметра газового пузыря зависит от количества вспененного материала, что трудно контролировать. Однако метод химического вспенивания имеет большие преимущества по прочности, водопоглощению и другим свойствам пенобетона низкой плотности [33].
В этом исследовании FAFC получали методом химического вспенивания. Сначала цемент, зольная пыль, микрокремнезем, восстановитель воды, коагулянт, стабилизатор пены, полипропиленовое волокно, вода и перекись водорода были взвешены на электронных весах в соответствии с заранее рассчитанным соотношением и упакованы в заранее подготовленную коробку для подготовка испытательных блоков FAFC. Затем началось испытание путем смешивания цемента, золы-уноса, микрокремнезема, стабилизатора пены (стеарат кальция), коагулянта (карбонат лития) и полипропиленового волокна в высокоскоростном диспергаторе в течение 1 мин. Вновь к предварительно перемешанному цементному раствору добавляли навеску воды и реагента для снижения содержания воды и продолжали перемешивание в течение 1 мин; перемешивание останавливали, перемешивая цементную смесь, прикрепленную к стенке цилиндра, с водой при помощи шпателя, после чего продолжали перемешивание в течение 1 мин. Затем добавляли предварительно взвешенную перекись водорода и перемешивали в течение 1 мин. Затем мы добавили предварительно отмеренное количество перекиси водорода, перемешивали в течение примерно 6-7 с, пока перекись водорода не была равномерно диспергирована в цементном растворе, прекратили перемешивание и быстро поместили перемешанные FAFC в предварительно смазанные 100 мм × 100 мм × 100 мм и 30 см × 30 см × 3 см, а сверху накрыли полиэтиленовой пленкой, чтобы избежать рассеивания влаги.
Наконец, его немедленно поместили в стандартную камеру для отверждения и извлекли из формы через 48 часов. Его помещали в стандартный сушильный шкаф со стандартной температурой 20 ± 2 °С и относительной влажностью более 95% для отверждения перед последующими испытаниями.
Испытательные блоки FAFC, показанные на рисунках a, b, представляют собой испытательные блоки FAFC с размерами 10 см × 10 см × 10 см. c, d показаны тестовые блоки FAFC с размерами 30 см × 30 см × 3 см. Образец для испытаний, показанный на рисунке а, разрезают на плоской поверхности и извлекают из формы, чтобы он стал образцом для испытаний, показанным на рисунке b. Испытательный образец, показанный на c, необходимо разрезать после извлечения из формы, чтобы он стал испытательным образцом, показанным на d, где a — стандартный испытательный образец, а c — самодельный инструмент из пленки с теплопроводностью.
Открыть в отдельном окне
Блок для испытаний пенобетона с летучей золой. ( a ) Подготовка испытательного образца. ( b ) Обработка тестовых блоков. ( c ) Подготовка испытательного блока. ( d ) Работа с тестовым блоком.
2.4. Методы испытаний
Для проверки характеристик подготовленных образцов проводятся испытания на плотность в сухом состоянии, прочность на сжатие и теплопроводность, ультразвуковое испытание, испытание на структуру пор и испытание на цикл замораживания-оттаивания.
Машина для испытания на прочность при сжатии использовалась для испытания на прочность при сжатии образцов размером 100 мм × 100 мм × 100 мм, см. (JG/T266-2011 ) [31]. На каждое отношение испытывали по три образца, и, наконец, за окончательную испытательную прочность принимали среднее значение трех образцов.
Использовался тестер теплопроводности CD-DR3030. Испытательный метод определения теплопроводности проводился на GB/T1029.5-2008 [35] спецификация. Размер образцов составлял 30 см × 30 см × 30 см, по три экземпляра в каждой группе. Согласно спецификации, тестер теплопроводности должен быть откалиброван с использованием профессиональных эталонных образцов теплопроводности перед использованием, чтобы обеспечить точность измеренных данных теплопроводности FAFC. Для калибровки использовались стандартные модели Центра технического надзора и исследований промышленности строительных материалов. (1) Стандартная модель представляет собой композитную пластину из стекловолокна желтого цвета средней щелочности с техническими характеристиками 30 см × 30 см × (25–27) мм и диапазоном плотности 110–130 кг/м 9 .0113 3 . (2) Эталонная пластина сначала была высушена в сушильном шкафу при 100 °C в течение 8 часов. После того, как качество было постоянным, эталонная пластина была удалена, и была измерена средняя теплопроводность в соответствии со спецификацией GB/T10294-2008 [36], измеренная при средней температуре 298 К, чтобы получить стандартное значение теплопроводности 0,0328 Вт. /(м·К).
В этом тесте используется ультразвуковой анализатор неметаллических материалов производства Beijing Kangkorui Company; после установки параметров размера тестового блока к поверхностям обеих сторон тестового блока прикрепляются передающий и приемный зонды; затем нажимаем кнопку отбора проб и сохраняем результаты ультразвукового контроля. Каждый тестовый блок тестировался по 5 точкам.
Изображения структуры пор поверхности FAFC были получены с помощью электронного микроскопа, а изображения поверхности FAFC были бинаризированы с использованием программного обеспечения Photoshop. Бинаризованные изображения были обработаны программой обработки изображений Image-Pro-Plus, и характеристические параметры пористой структуры были получены путем анализа. Изучено влияние различных дозировок перекиси водорода, микрокремнезема и полипропиленового волокна на обычные параметры пористой структуры ТВС.
Ссылаясь на спецификацию JGJ/T341-2014 [37], исследовали морозостойкость тестовых блоков ТВС путем проведения 25 циклов замораживания-оттаивания и измерения плотности в сухом состоянии, прочности на сжатие и скорости ультразвуковой волны тестовых блоков ТВС после сушки. в конце каждых 5 циклов для изучения влияния дозировки полипропиленового волокна и количества циклов замораживания-оттаивания на морозостойкость FAFC, а также для оценки скорости потери качества, скорости потери прочности на сжатие и скорости ультразвуковой волны. Взаимосвязь между пористой структурой и морозостойкостью была проанализирована, чтобы обеспечить ориентир для улучшения морозостойкости FAFC.
3.1. Влияние внешней добавки на плотность в сухом состоянии
3.1.1. Анализ дозировки кремнеземного дыма и перекиси водорода на плотность в сухом состоянии
Как видно из рисунка, взаимосвязь между плотностью в сухом состоянии FAFC и количеством дозировки перекиси водорода имеет отрицательную корреляцию. Сухая плотность FAFC составляла 241, 225, 205, 191, 180 кг/м 3 , а степень восстановления составляла 6,64%, 8,89%, 6,83%, 5,76% при дозировке перекиси водорода 4%, 4,5%, 5%, 5,5% и 6% соответственно. С увеличением содержания пенообразователя сухая плотность FAFC уменьшалась, что согласуется с результатами исследований Su et al. [38]. Результаты показали, что количество дозируемого перекиси водорода значительно влияет на сухую плотность FAFC, поскольку по мере увеличения количества дозируемого перекиси водорода количество пузырьков на единицу объема FAFC увеличивалось, масса цемента уменьшалась, а сухая плотность уменьшалась.
Открыть в отдельном окне
Взаимосвязь между сухой плотностью, микрокремнеземом и дозировкой перекиси водорода.
Зависимость между сухой плотностью FAFC и дозировкой микрокремнезема имеет отрицательную корреляцию в . Сухая плотность уменьшилась с 218 кг/м 3 до 202 кг/м 3 при увеличении дозировки кремнезема с 0 до 8%, что уменьшилось на 7,34%; таким образом, можно видеть, что дозировка микрокремнезема мало влияет на плотность в сухом состоянии. Это связано с тем, что, хотя с увеличением дозировки микрокремнезема частицы микрокремнезема заполнили поры суспензии ВКЖК, увеличивая плотность стенки пор ВВСЖ, активность вулканического пепла кремнеземной пыли способствовала вторичной гидратации. реакция цемента, повышающая стабильность пузырьков испытательного блока. Сухая плотность испытательного блока снижается, но количество кремнеземной пыли, замещающей цемент, невелико, поэтому влияние дозы кремнеземной пыли на сухую плотность FAFC незначительно. Содержание пенообразователя может существенно повлиять на плотность, а влияние микрокремнезема незначительно. Однако Лю и соавт. [39] установлено, что сухая плотность пенобетона увеличивается с увеличением содержания микрокремнезема, что может быть связано с сырьем, используемым для приготовления пенобетона.
3.1.2. Анализ влияния дозировки полипропиленового волокна на плотность в сухом состоянии
Как показано на рисунке, взаимосвязь между сухой плотностью FAFC и дозировкой полипропиленового волокна имеет отрицательную корреляцию. Сухая плотность образца уменьшилась с 212 кг/м 3 до 202 кг/м 3 с небольшим изменением на 4,72 % при увеличении дозировки волокна ПП от 0 до 0,4 %.
Открыть в отдельном окне
Взаимосвязь между сухой плотностью и дозировкой клетчатки.
Эти результаты приписываются примеси полипропиленового волокна, поскольку трехмерная пространственная сетчатая структура, встроенная в FAFC, может улучшить стабильность пены в суспензии. Сухая плотность уменьшалась с увеличением примеси полипропиленового волокна. Часть полипропиленового волокна присутствовала в агломерате цементного раствора. В растворе FAFC основным материалом был цемент. Поэтому раствор FAFC называют цементным раствором. При введении дополнительного газа окружающие мельчайшие пузырьки разрываются и сливаются в крупные [40], а сухая плотность уменьшается.
3.2. Результаты испытаний на прочность при сжатии
3.2.1. Анализ влияния добавки пенообразователя на прочность на сжатие
показывает, что прочность на сжатие FAFC в том же возрасте значительно снижалась по мере увеличения количества перекиси водорода. С одной стороны, с увеличением примеси перекиси водорода уменьшается масса цемента в единице объема. Вяжущие вещества, такие как гидратированный силикат кальция и гидратированный алюминат кальция, образующиеся в результате реакции гидратации, уменьшаются. Таким образом, уменьшается плотность продуктов гидратации, уменьшается толщина стенки поры и снижается прочность на сжатие тестового блока FAFC. С другой стороны, с увеличением количества перекиси водорода скорость образования пузырьков в испытательном блоке увеличивается; увеличивается количество пор в единице объема; стенка пор становится тоньше; поры легко разрушаются и сплавляются, увеличивается образование совместных пор, а (вредное) увеличение пор приводит к большему количеству дефектов пористой структуры и снижению прочности на сжатие [41].
Открыть в отдельном окне
Влияние перекиси водорода на прочность на сжатие в разном возрасте.
Прочность на сжатие FAFC с различными добавками перекиси водорода увеличивалась с увеличением срока отверждения. Это связано с тем, что летучая зола представляет собой крошечные сферические частицы, и ее опрокидывающий эффект может улучшить текучесть и однородность раствора FAFC, заполняя промежутки между пустотами пенобетонного раствора и улучшая плотность FAFC. Летучая зола обладает активностью вулканического пепла, а содержащийся в ней аморфный кремнезем может реагировать с цементом и водой с образованием гидратированного силиката кальция с низкой щелочностью и других вяжущих веществ; с увеличением возраста отверждения продукты гидратации растут, микроструктура постепенно становится более плотной, а макроскопические характеристики показывают, что прочность на сжатие FAFC постепенно увеличивается. Однако скорость роста в течение 7–28 дней была относительно выше, чем в другие периоды, что связано с реакцией гидратации цемента с образованием Ca(OH) 2 , летучей золы в SiO 2 , Al 2 O 3 и других реакционноспособных оксидов, образующихся во вторичной реакции гидратации с образованием C-S-H, Aft и других продуктов гидратации. С увеличением срока эксплуатации уменьшается активный материал, замедляется скорость вторичной реакции гидратации и снижается скорость роста прочности [42].
3.2.2. Анализ влияния добавки микрокремнезема на прочность на сжатие
Как видно из графика, прочность на сжатие ВТК после добавления в ВВС микрокремнезема сначала увеличивается, а затем уменьшается с увеличением добавки микрокремнезема, указывая на то, что добавка с соответствующей количество микрокремнезема полезно для увеличения прочности на сжатие FAFC. Это можно объяснить тем, что микрокремнезем содержит большое количество активного SiO 2 , который может реагировать с Ca(OH) 2 с образованием вяжущего вещества гидратированного силиката кальция, который улучшает плотность и прочность стенки пор, но с увеличением количества примеси микрокремнезема текучесть пульпы снижается , испытательный блок FAFC сталкивается с трудностями, и внутренние дефекты увеличиваются. Кроме того, увеличение примеси микрокремнезема привело к относительному снижению содержания цемента. Содержание Ca(OH) 2 , образующихся в результате реакции гидратации цемента, снижается. Содержание вяжущих веществ, таких как гидратированный силикат кальция и гидратированный алюминат кальция, уменьшается, а прочность на сжатие FAFC снижается.
Открыть в отдельном окне
Влияние микрокремнезема на прочность на сжатие в разном возрасте.
С увеличением срока эксплуатации прочность на сжатие образцов FAFC с различным количеством примеси микрокремнезема демонстрировала тенденцию к увеличению. Эти результаты приписываются влиянию микрокремнезема на FAFC, которое в основном включало эффект микрофильмирования микрокремнезема и эффект вулканического пепла [43]. Частицы микрокремнезема с малым размером частиц и большой удельной поверхностью могут заполнять поры FAFC и улучшать плотность FAFC. Между тем, в FAFC в результате реакции гидратации цемента образуется большое количество Ca(OH) 2 и активный SiO 2 и Al 2 O 3 в микрокремнеземе для получения вяжущих веществ, таких как гидратированный силикат кальция и гидратированный алюминат кальция. Достаточно щелочная среда внутри шлама ускоряет эффект вулканического пепла кремнеземной пыли и улучшает прочность на сжатие FAFC.
3.2.3. Анализ влияния дозировки полипропиленового волокна на прочность на сжатие
Как показано на , прочность на сжатие FAFC того же возраста имеет тенденцию сначала увеличиваться, а затем уменьшаться с увеличением примеси волокна. Подобным же образом Geng Ling [44] обнаружил аналогичные закономерности при изучении влияния содержания полипропиленового волокна и стекловолокна на прочность на сжатие сверхлегкого пенобетона. Причина в том, что, когда примесь полипропиленового волокна увеличилась с 0 до 0,1%, волокно построило трехмерную пространственную сетчатую структуру в FAFC, которая сыграла роль перекрытия скелета, защиты пены от разрыва и улучшения стабильности пены. ; волокна и продукты гидратации были тесно связаны в единое целое, уменьшая развитие трещин, играя роль режущей пены, так что распределение пор по размерам было равномерным, улучшая прочность на сжатие FAFC. Кроме того, от 0,1 до 0,4% примеси волокон было слишком много и они не могли быть равномерно диспергированы в суспензии. Возникло явление локальной агрегации, которое привело к разрыву пены и повреждению пористой структуры. Гидратация была неравномерной, что привело к снижению прочности на сжатие FAFC.
Открыть в отдельном окне
Влияние дозировки полипропиленового волокна на прочность на сжатие в зависимости от возраста.
С возрастом прочность на сжатие ВКВС с различным количеством полипропиленового волокна постепенно увеличивается, потому что в ВВС суспензия обернута полипропиленовыми волокнами. Активные вещества в растворе вступают в реакцию гидратации с образованием гидратированного силиката кальция и других вяжущих веществ, тесно связанных с полипропиленовыми волокнами. После схватывания и затвердевания испытательного блока соединение между полипропиленовыми волокнами и стенкой пор становится более плотным, что снижает образование трещин и дополнительно повышает компактность FAFC. Прочность на растяжение полипропиленового волокна значительна. В испытании на прочность на сжатие полипропиленовое волокно выдержало давление вместе со стенкой пор, что повысило сжимающую способность FAFC и повысило прочность на сжатие.
3.3. Результаты испытаний на теплопроводность
3.3.1. Анализ теплопроводности дозируемого количества пенообразователя
Из , теплопроводность FAFC имеет тенденцию к снижению с увеличением дозировки пероксида водорода. При дозировке перекиси водорода от 4 до 6% максимальное снижение теплопроводности составило 7,79%. Поскольку плотность FAFC уменьшается, стенка пор становится тоньше; содержание пены в единице объема внутри пенобетона увеличивается, а пена конденсируется и затвердевает в порах пенобетона, препятствуя распространению тепла от конвекции внутрь конструкции, снижая теплопроводность и повышая теплоизоляцию [45] .
Открыть в отдельном окне
Влияние добавки пены на теплопроводность.
3.3.2. Анализ влияния дозировки кремнеземной пыли на теплопроводность
Можно наблюдать, что теплопроводность имеет тенденцию к увеличению, а затем уменьшается с увеличением дозировки кремнеземной пыли. Теплопроводность была наибольшей при дозировке микрокремнезема 4%. Это связано с компактностью стенки поры и размером пор; Эффект заполнения микрокремнеземом увеличивает плотность стенок пор. При этом SiO 2 в микрокремнеземе способствует вторичной реакции гидратации цемента, что повышает плотность стенок пор; чем значительнее компактность стенки поры, тем выше теплоемкость и больше теплопроводность. В то же время добавление микрокремнезема увеличивает количество крошечных пор, облегчая теплопередачу и повышая теплопроводность. Дальнейшее увеличение примеси микрокремнезема приводит к замедлению скорости реакции вулканического дыма и снижению плотности стенок пор, что не способствует теплопередаче и приводит к снижению теплопроводности, текучести шлама, большему размеру пор, меньшей теплопередающей способности. крупных пор и пониженной теплопроводности [46].
Открыть в отдельном окне
Влияние дозирования микрокремнезема на теплопроводность.
3.3.3. Анализ теплопроводности дозированного количества полипропиленового волокна
Теплопроводность сначала увеличивалась, а затем уменьшалась с увеличением количества примеси полипропиленового волокна, как показано на рис. Это связано с тем, что полипропиленовые волокна равномерно диспергируются в FAFC, улучшается однородность цементного раствора, улучшается стабильность пены, контролируется плавление, размеры пор относительно малы, а полипропиленовые волокна лучше интегрируются в цементный раствор, что повышает теплостойкость. проводимость и компактность стенок пор.
Открыть в отдельном окне
Влияние дозировки полипропиленового волокна на теплопроводность.
В исследовании количество полипропиленового волокна в смеси увеличилось с 0,1 до 0,4%, что привело к неравномерному распределению, что привело к растрескиванию вокруг полипропиленового волокна; увеличился размер пропитки, уменьшилась плотность стенок пор и ухудшилась структура пор; однако, поскольку газ имеет более низкую теплопроводность, чем твердое тело, характеристики изоляции улучшились.
3.4. Результаты испытаний параметров пористой структуры
3.4.1. Закон изменения добавки пенообразователя и структуры пор пенобетона
показывает структуру пор до и после обработки поперечного сечения при дозировке пены 4%. визуализирует закон изменения пористости смеси для различных соотношений смеси в зависимости от количества дозируемого пенообразователя. Пористость FAFC значительно увеличилась с увеличением дозировки пенообразователя в почти линейной зависимости. Пористость колебалась от 82,69 до 91,48 %. Это связано с тем, что с увеличением добавки пенообразователя количество пены в единице объема ТВС увеличивается в процессе вспенивания и шламового схватывания и твердения, масса вяжущего материала относительно уменьшается, а стенка поры становится тоньше, что создает увеличение пористости FAFC.
Открыть в отдельном окне
Изображение поперечного сечения пор 4% дозированной пены: ( a ) исходное изображение, ( b ) изображение поперечного сечения.
Открыть в отдельном окне
Влияние дозирования пены на пористость.
Как показано на рисунке, средний размер пор FAFC увеличивался с увеличением количества примеси перекиси водорода. Средний размер пор колебался от 694,08 до 1506,03 мкм. В ответ на увеличение содержания перекиси водорода образуется больше пены, количество цементирующего материала, окружающего пену, уменьшается, и пена становится менее стабильной [47].
Открыть в отдельном окне
Влияние перекиси водорода на средний размер пор.
Может легко сливаться с окружающей пеной, увеличивая средний размер пор. Причем, чем больше перекиси водорода было смешано, тем больше скорость пенообразования и больше сила удара; после затвердевания и затвердевания суспензии средний размер пор увеличивался. Если объем плавленой пены слишком велик или если средний размер пор слишком велик, тестовый блок в определенной степени разрушится во время вспенивания. Поэтому количество перекиси водорода не должно быть слишком большим [48].
Как показано на рисунке, добавка перекиси водорода повлияла на распределение пор по размерам пенобетона. По мере увеличения примеси перекиси водорода распределение пор по размерам в FAFC смещалось в сторону более крупных размеров пор, а увеличение поверхностной примеси перекиси водорода приводило к увеличению размеров пор. С увеличением дозировки перекиси водорода баланс мелких пор с размером пор менее 900 мкм в FAFC постепенно снижается. С увеличением дозы перекиси водорода доминирующий интервал размеров пор (диапазон размеров пор с наиболее значительным процентом размера пор) непрерывно увеличивался. При дозе перекиси водорода 5 % преобладающий интервал размеров пор составлял 900~1200 мкм; при дозе перекиси водорода 5,5% преобладающий интервал размеров пор составлял 1200~1500 мкм; и когда доза перекиси водорода составляла 6%, преобладающий интервал размеров пор превышал 1500 мкм.
Открыть в отдельном окне
Влияние дозировки перекиси водорода на распределение пор по размерам.
Фактор формы пор FAFC имеет тенденцию к уменьшению, а затем к увеличению с увеличением примеси перекиси водорода, как показано на рис. При увеличении примеси пероксида водорода количество пены увеличивалось, и большое количество пен контактировало друг с другом, сплавлялось в крупные поры и выдавливалось между собой; в результате формы имеют тенденцию к деформации, а коэффициенты формы пор увеличиваются.
Открыть в отдельном окне
Влияние перекиси водорода на коэффициент формы пор.
3.4.2. Закон изменения дозировки микрокремнезема на структуру пор пенобетона
показывает структуру пор до и после обработки поперечного сечения при содержании микрокремнезема 4%. Из этого видно, что с увеличением примеси микрокремнезема пористость ТВТЭ имеет тенденцию сначала уменьшаться, а затем увеличиваться, а при увеличении примеси микрокремнезема от 0 до 4 % продолжает снижаться. В результате того, что микрокремнеземная пыль обладает эффектом заполнения микроагрегатов и активностью вулканического пепла, частицы кремнеземной пыли заполнили поры суспензии FAFC, а активный SiO 2 в микрокремнеземе вступает в реакцию с цементом с образованием геля. Вещество, гидратированный гель силиката кальция и т.п., увеличивает компактность FAFC, улучшает стабильность пены и уменьшает пористость FAFC. По мере увеличения содержания микрокремнезема с 4 до 8% содержание активного SiO 2 в растворе увеличивалось, содержание цемента снижалось, как и содержание Ca(OH) 2 . Активность вулканического пепла микрокремнезема снижалась, степень реакции вторичной гидратации уменьшалась, однородность и плотность пульпы уменьшались, а пена легко разрушалась и сплавлялась, увеличивая пористость FAFC. Избыток микрокремнезема будет приводить к разрушению и расплавлению части пены с образованием шовных пор, что увеличивает пористость ФАТЭ [48]. Показано, что соответствующее количество микрокремнезема в FAFC может улучшить его пористость.
Открыть в отдельном окне
Изображение поперечного сечения пор при дозировании микрокремнезема 4%: ( a ) исходное изображение, ( b ) изображение поперечного сечения.
Открыть в отдельном окне
Влияние дозирования микрокремнезема на пористость.
Как показано на , средний размер пор FAFC имеет тенденцию к уменьшению, а затем к увеличению с увеличением дозировки микрокремнезема. Когда дозировка микрокремнезема увеличилась с 0 до 4%, эффект заполнения микрозаполнителями и эффект вулканического пепла микрокремнезема улучшили однородность и плотность суспензии FAFC, повысили стабильность пены, уменьшили размер пор, и средний размер пор уменьшился. Когда количество микрокремнезема было увеличено с 4 до 8%, количество микрокремнезема было слишком велико, содержание цемента было относительно снижено, степень вторичной реакции гидратации была уменьшена, продукты гидратации были уменьшены, плотность и однородность цементного раствора, уменьшилась текучесть раствора, снизилась устойчивость пены, произошло расплавление пены, увеличился средний размер пор.
Открыть в отдельном окне
Влияние дозирования микрокремнезема на средний размер пор.
Влияние дозировки микрокремнезема на распределение размера пор FAFC показано на рис. При увеличении дозировки микрокремнезема распределение пор по размерам ТЖК было примерно нормальным, и оно сначала мигрировало в сторону меньшего размера пор, а затем мигрировало в сторону большего размера пор. Доля мелких пор с размерами пор FAFC менее 900 мкм сначала увеличивалась, а затем уменьшалась с увеличением дозировки микрокремнезема. Среди них диапазон распределения пор по размерам был одинаковым при дозах микрокремнезема 2% и 4%, а отличие заключалось в том, что при интервале размеров пор <900 мкм, процент пор FAFC с дозой 4% микрокремнезема был более значительным, чем с дозой 2% микрокремнезема.
Открыть в отдельном окне
Влияние дозирования микрокремнезема на распределение пор по размерам.
показывает, что с увеличением дозировки микрокремнезема коэффициент формы пор FAFC сначала уменьшался, а затем увеличивался; чем меньше коэффициент формы поры, тем ближе размер поры к сфере. Таким образом, при дозировке микрокремнезема 4% коэффициент формы пор является самым низким, равным 1,250, и форма пор является наиболее округлой. Увеличение дозировки микрокремнезема от 0 до 4% постоянно снижало коэффициент формы пор; из-за микроагрегатного эффекта микрокремнезема он мог заполнить FAFC, что повысило однородность цементного теста и эффект вулканического пепла, что улучшило стабильность цементного теста, и эффект опрокидывания, который уменьшил коэффициент формы пор. По мере увеличения содержания микрокремнезема с 4 до 8% коэффициент формы пор постоянно увеличивался, поскольку с увеличением содержания микрокремнезема текучесть цементного теста снижалась.
Открыть в отдельном окне
Влияние дозировки микрокремнезема на коэффициент формы пор.
Пена не может быть равномерно распределена в пасте в процессе вспенивания. Взаимная агрегация приводит к слиянию пены с разрывом, увеличивается количество неправильных пен, увеличивается коэффициент формы пор. Таким образом, смешивание правильного количества микрокремнезема может уменьшить коэффициент формы пор FAFC.
3.4.3. Закон изменения добавки полипропиленового волокна на пористую структуру пенобетона
показывает структуру пор до и после обработки поперечного сечения при дозировке волокна 0,1%. В соответствии с , пористость ВТАК увеличивалась, а затем уменьшалась с дозой полипропиленовых волокон, но средний размер пор ВТАК уменьшался, а затем увеличивался с дозой полипропиленовых волокон, а пористость, средний размер пор и коэффициент формы были самыми низкими при 0,1% дозы полипропиленовых волокон.
Открыть в отдельном окне
Изображение поперечного сечения пор при дозировке волокна 0,1%: ( a ) исходное изображение, ( b ) поперечное сечение.
Открыть в отдельном окне
Влияние легирования волокна на пористость.
Распределение размеров пор FAFC приближалось к обычному закону распределения при увеличении дозировки полипропиленового волокна, как показано на рисунках и . Распределение размеров пор FAFC имеет тенденцию к большому размеру пор. С увеличением дозировки ПП преобладающий интервал размеров пор FAFC сначала уменьшался, а затем увеличивался. Доминирующий интервал размера пор FAFC всегда находился в диапазоне 600~900 мкм при дозировке волокна ПП 0, 0,2 и 0,4 %. Процент крошечных пор размером менее 900 мкм был наибольшим, и распределение пор по размерам было приемлемым. Поэтому было выбрано 0,1% полипропиленовых волокон.
Открыть в отдельном окне
Влияние легирования волокна на средний размер пор.
Открыть в отдельном окне
Влияние легирования волокна на распределение пор по размерам.
Тенденции изменения коэффициента формы пор для пяти соотношений смесей показаны на рис. Фактор формы пор FAFC сначала уменьшался, а затем увеличивался с увеличением дозировки полипропиленового волокна. Фактор формы пор был наименьшим при 0,1% полипропиленовых волокон, что составило 1,218, а форма пор была наиболее близкой к сферической. Фактор формы пор уменьшился при дозировке 0,1% полипропиленового волокна по сравнению с FAFC без полипропиленового волокна.
Открыть в отдельном окне
Влияние легирования волокна на коэффициент формы пор.
Вышеупомянутое явление произошло из-за того, что полипропиленовые волокна создали трехмерную пространственную сетчатую структуру в FAFC [49], увеличивая стабильность пены и уменьшая пористость. При увеличении дозировки полипропиленового волокна с 0,1 до 0,4% появлялась агломерация полипропиленовых волокон, снижалась однородность цементного теста, снижалась устойчивость пены, происходило ее растрескивание и оплавление, увеличивались поры в стыках, пористость, средний размер пор, и коэффициент формы увеличился. Это показывает, что смешивание соответствующего количества полипропиленовых волокон может уменьшить пористость и средний размер пор FAFC, но чрезмерное количество полипропиленовых волокон будет иметь неблагоприятные последствия.
3.5. Результаты испытаний цикла замораживания-оттаивания
3.5.1. Анализ скорости потери качества при замораживании-оттаивании Закон
Скорость потери массы тестовых блоков FAFC рассчитывается по формуле
Mm=M0−MsM0×100%
(2)
где M m – скорость потери массы при испытании циклом замораживания-оттаивания, %; M 0 – сухая масса испытательного блока перед циклом замораживания–оттаивания, г; M s – сухая масса испытательного блока после испытания циклом замораживания–оттаивания, г.
Как видно из рисунка, скорость потери массы тестовых блоков FAFC без дозировки полипропиленового волокна увеличивалась с увеличением количества циклов замораживания-оттаивания. Потеря массы достигла 36,9 % после 15 циклов замораживания-оттаивания, при этом все поверхностные слои тестовых блоков отвалились, что привело к значительной потере массы. Скорость потери массы образцов ТАТЭ с различным количеством полипропиленового волокна постепенно возрастала с увеличением количества циклов замораживания-оттаивания.
Открыть в отдельном окне
Скорость потери массы при циклическом замораживании-оттаивании.
Когда дозировка полипропиленовых волокон составляла 0,4%, скорость потери массы тестового блока FAFC была наименьшей, что указывает на то, что дозировка полипропиленовых волокон может эффективно снизить потерю массы тестового блока и улучшить морозостойкость тестового блока FAFC . В результате процесса замораживания в поры пенобетона всасывается большое количество жидкой воды, которая при воздействии давления замораживания замерзает в твердый лед [50,51]. Прочность на сжатие FAFC низкая, когда растягивающее напряжение больше, чем прочность на растяжение стенки поры. В стенке пор образуются микротрещины, в результате чего плотная структура стенки поры становится рыхлой; в процессе таяния твердый лед превращается в жидкую воду, стенка отверстия сжимается, и вода попадает внутрь тестового блока через трещины в стенке отверстия, увеличивая содержание воды в нем. Следовательно, скорость потери массы увеличивается с увеличением числа циклов замораживания-оттаивания.
Если образцы не смешиваются с полипропиленовыми волокнами, то в первую очередь повреждаются углы образцов ВСК и происходит их выкрашивание. С увеличением количества циклов замораживания-оттаивания явление растрескивания становилось все более серьезным, а скорость потери качества увеличивалась. При сравнении тестовых блоков с полипропиленовыми волокнами и без них, при содержании полипропиленовых волокон 0,1% пористость уменьшалась, плотность структуры стенки пор увеличивалась, прочность стенки пор на сжатие увеличивалась, содержание влаги внутри тестового блока уменьшалось, давление замерзания, вызванное замерзанием, уменьшилось, а морозостойкость улучшилась. При этом равномерно диспергированные полипропиленовые волокна сцеплялись с цементным тестом. Полипропиленовые волокна обеспечивали растягивающее напряжение для испытательных блоков FAFC. Для тестовых блоков, стенки пор которых были повреждены замерзанием и набуханием, обломки с большими трещинами в основной части тестовых блоков не могли быть полностью отделены, и они все еще были связаны с основной частью тестовых блоков через полипропиленовые волокна [52]. Эффект улучшения полипропиленовых волокон становится более очевидным по мере увеличения количества циклов замораживания-оттаивания.
При увеличении дозировки полипропиленового волокна с 0,1 до 0,4% пористость увеличивалась, стенка пор становилась тоньше, продукты гидратации уменьшались, а также уменьшалась плотность стенки поры.
Стенка пор FAFC легче разрушалась в цикле замораживания-оттаивания, поскольку вода быстро проникала через трещины в стенке поры. Содержание воды в испытательном блоке увеличилось, давление замерзания увеличилось, и стенка пор FAFC легче повреждалась. Однако с увеличением количества полипропиленового волокна растягивающее напряжение, обеспечиваемое полипропиленовыми волокнами, постепенно увеличивается. Стенка пор была повреждена в цикле замораживания-оттаивания, и структура цементного теста вокруг полипропиленовых волокон стала рыхлой. После крошения испытательные блоки отвалились, в результате чего полипропиленовые волокна обнажились, но их растягивающее напряжение удержало центральную часть испытательных блоков соединенной. Следовательно, скорость потери массы уменьшалась с увеличением количества полипропиленового волокна.
При определенном количестве полипропиленового волокна скорость потери качества медленно увеличивается с увеличением количества циклов замораживания-оттаивания; когда количество циклов замораживания-оттаивания определено, скорость потери качества медленно снижается при добавлении полипропиленовых волокон, а при 0,4% полипропиленового волокна скорость потери качества является самой низкой после 5, 10, 15, 20 и 25 циклы замораживания-оттаивания.
3.5.2. Анализ степени потери прочности на сжатие при замораживании-оттаивании Закон
Следующая формула рассчитывает скорость потери прочности на сжатие испытательных блоков FAFC:
Δfc=fc0−fcnfc0×100%
(3)
где Δ f c – скорость потери прочности при сжатии в цикле замораживания-оттаивания, %; f cn – прочность на сжатие испытательного блока после испытания циклом замораживания–оттаивания, МПа; f c 0 – прочность образца на сжатие до испытания циклом замораживания–оттаивания, МПа.
показывает, что для ТВС без полипропиленовых волокон после 15 циклов замораживания-оттаивания испытательный блок был сильно поврежден, скорость потери прочности на сжатие достигла 74,1%, а циклы замораживания-оттаивания были прекращены. С увеличением количества циклов замораживания-оттаивания скорость потери прочности на сжатие ВКВС постепенно увеличивалась. Скорость потери прочности на сжатие постепенно снижалась с увеличением дозировки полипропиленового волокна.
Открыть в отдельном окне
Скорость потери прочности на сжатие при испытании на цикл замораживания-оттаивания.
Поскольку вода в порах FAFC жидкая, молекулы воды сближаются из-за силы водородной связи, что уменьшает объем. Когда жидкая вода замерзает в твердый лед, на молекулы воды действует молекулярная сила, которая снижает силу водородных связей. Вода попадает в поры через трещины, образовавшиеся в стенке поры в цикле замораживания-оттаивания, и чем больше воды попадает в поры, тем больше объемное расширение при замерзании воды. Во время циклов замораживания-оттаивания трещины в стенках пор постепенно развиваются и расширяются, плотность стенок пор постепенно уменьшается, образуются внутренние стыковые поры, постепенно снижается прочность на сжатие, а скорость потери прочности на сжатие постепенно увеличивается.
В результате испытания циклом замораживания-оттаивания на ТВС без ПП-волокна внутренние поры тестового блока увеличились, стенка пор разрыхлилась, внутренняя структура ухудшилась, поверхностные трещины расширились в более крупные, отломки откололись , прочность на сжатие быстро снижалась, а скорость потери прочности на сжатие постепенно увеличивалась. FAFC смешивали с полипропиленовыми волокнами, и цементная паста хорошо сцеплялась. Трещиноблокирующий эффект полипропиленовых волокон предотвращает и рассеивает трещины FAFC, повышает плотность тестового блока, предотвращает попадание воды в поры и снижает содержание воды в порах [53,54].
Давление замораживания, создаваемое во время замораживания, незначительно, что может улучшить способность FAFC сопротивляться повреждениям от замораживания и оттаивания. В то же время полипропиленовые волокна внутри FAFC могут разделить часть внутреннего напряжения и часть давления замерзания, создаваемого образцом при изменении температуры, препятствуя образованию и развитию трещин, обозначенных стенкой поры, и улучшая сопротивление поры. стена к повреждению. В ВВС наблюдается трехмерное хаотичное распределение волокон ПП, а эффект склеивания цементным тестом предотвращает отслаивание поверхности и повышает способность ВВС выдерживать циклы замораживания-оттаивания. Чем больше примесь полипропиленовых волокон, тем выше устойчивость образца к выкрашиванию.
Полипропиленовое волокно является хорошей заменой полиэфирному волокну, но при дозировке полипропиленового волокна 0,4% скорость потери качества была наименьшей после 5, 10, 15, 20 и 25 циклов замораживания-оттаивания; при содержании ПП-волокна 0,4 % и при содержании ПП-волокна 0,4 % скорость потери качества была наименьшей после 5, 10, 15, 20 и 25 циклов замораживания-оттаивания.
3.

Под действием циклов замораживания-оттаивания стенка пор испытательного блока FAFC образует микротрещины; трещины будут поглощать и рассеивать ультразвуковую энергию, а скорость распространения ультразвуковых волн будет уменьшаться с увеличением дефектов, таких как трещины, внутри испытательного блока из пенобетона.
По мере увеличения числа циклов замораживания-оттаивания трещины внутри тестового блока увеличиваются, а скорость ультразвуковой волны уменьшается [55]. Скорость ультразвуковой волны можно использовать для анализа способности FAFC противостоять циклам замораживания-оттаивания; в этой статье используется коэффициент повреждения D для оценки степени повреждения испытательного блока FAFC в результате циклов замораживания-оттаивания. Коэффициент повреждения D рассчитывается как
D=1-EnE0=1-Vn2V02
(4)
где Е н – модуль упругости образца после n-го цикла замораживания–оттаивания, МПа; E 0 – начальный модуль упругости образца, МПа; V n – скорость ультразвуковой волны после n-го цикла замораживания-оттаивания, км/с; V 0 – начальная скорость ультразвуковой волны в образце, км/с.
Результаты ультразвукового контроля испытательного блока перед циклом замораживания-оттаивания показаны на . При наличии легирования полипропиленовыми волокнами скорость ультразвуковой волны увеличивалась, а затем уменьшалась из-за связывающего эффекта между цементным раствором и полипропиленовыми волокнами, с более равномерным распределением пор по размерам, уменьшением пористости и среднего размера пор, увеличением толщины стенок FAFC. компактность, малые потери энергии и большая скорость волны. При избытке полипропиленовых волокон в тест-блоке происходит разрыв пены, разрастание пор шва, увеличение пористости и среднего размера пор, обеднение внутренней структуры тест-блока, снижение скорости ультразвуковой волны.
Таблица 5
Результаты ультразвукового контроля тестовых блоков перед циклами замораживания-оттаивания.
Test Block Proportioning | Wave Speed v (km/s) |
---|---|
0% | 1.![]() |
0.1% | 1.54 |
0.2% | 1.52 |
0,3% | 1,51 |
0,4% | 1,50 |
Открыть в отдельном окне
Таким образом, начальная скорость ультразвуковой волны была максимальной при дозировке 0,1% полипропиленового волокна и снижалась с увеличением дозировки полипропиленового волокна. Тем не менее, скорость ультразвуковой волны увеличилась по сравнению с FAFC без дозировки полипропиленового волокна.
Влияние полипропиленовых волокон на скорость ультразвука FAFC после циклов замораживания-оттаивания показано на рис. Помимо увеличения трещин в стенках пор, вызванного циклами замораживания-оттаивания, снижается плотность и увеличиваются потери энергии ультразвука при прохождении волны через дефекты. Во время цикла замораживания-оттаивания растягивающее напряжение полипропиленовых волокон сопротивляется повреждению стенки пор из-за давления замерзания. Улучшение антифризных характеристик полипропиленовых волокон становится более очевидным при увеличении дозировки полипропиленовых волокон [56]. Это согласуется с изменением характера волокон ПП на скорость потери массы и скорость потери прочности FAFC, указывая на то, что использование ультразвуковых волн может хорошо отражать влияние волокон PP на внутреннюю пористую структуру пенобетона после циклов замораживания-оттаивания. .
Открыть в отдельном окне
Скорость ультразвуковой волны для испытания цикла замораживания-оттаивания.
Влияние полипропиленовых волокон на повреждаемость ТВС после циклов замораживания-оттаивания показано на рис. Фактор повреждения увеличивался с увеличением количества циклов замораживания-оттаивания, а фактор повреждения уменьшался с увеличением дозировки полипропиленового волокна [57]. При содержании полипропиленовых волокон 0,4 % коэффициент повреждения был наименьшим. Он увеличивался с циклами замораживания-оттаивания и уменьшался с высокой дозировкой полипропиленового волокна. После смешивания с полипропиленовыми волокнами полипропиленовое волокно и цементная паста были тесно связаны, что увеличило размер стенки поры, способной противостоять давлению замерзания, и уменьшило образование и развитие трещин в стенке поры под давлением замерзания. Повреждение пористой структуры в FAFC было уменьшено, и фактор повреждения был уменьшен. Этот вывод согласуется с влиянием дозирования ПП-волокна на скорость ультразвуковой волны ТВС после испытания циклом замораживания-оттаивания, что указывает на то, что фактор повреждения может хорошо характеризовать влияние ПП-волокна на морозостойкость ТВС.
Открыть в отдельном окне
Коэффициент повреждения при испытании циклом замораживания-оттаивания.
В результате этого экспериментального исследования прочности на сжатие, теплопроводности и долговечности FAFC были сделаны следующие выводы.
Foam concrete | FC |
Polypropylene fiber | PP fiber |
Current fly ash foam concrete | FAFC |
Natural Science Foundation of Ningxia (2021AAC03080), Key Research и Программа развития Нинся (2021BDE
), дисциплина первого уровня (гидротехническая дисциплина) университетов Нинся (NXYLXK2021A03).
Концептуализация, С.Л.; Формальный анализ, CY; Приобретение финансирования, HL; Расследование, Ю.Д., Х.З. и Дж.З.; Методология, HL; Администрация проекта, C.Y. и Ю.Д.; Ресурсы, HL; Программное обеспечение, С.Л.; Надзор, HL; Валидация, С.Л. и Х.Л.; Визуализация, X.Z. и Дж.З.; Письмо — первоначальный вариант, SL; Написание — рецензирование и редактирование, HL Все авторы прочитали и согласились с опубликованной версией рукописи.
Неприменимо.
Неприменимо.
Данные, подтверждающие результаты этого исследования, можно получить у соответствующего автора по обоснованному запросу.
Авторы заявляют об отсутствии конфликта интересов. Спонсоры не участвовали в разработке исследования; при сборе, анализе или интерпретации данных; в написании рукописи или в решении опубликовать результаты.
Примечание издателя: MDPI сохраняет нейтралитет в отношении юрисдикционных претензий в опубликованных картах и институциональной принадлежности.
1. Чика Л., Альзате А. Обзор ячеистого бетона: новые направления применения в строительстве. Констр. Строить. Матер. 2019;200:637–647. doi: 10.1016/j.conbuildmat.2018.12.136. [CrossRef] [Google Scholar]
2. Кирубайни П., Саянтан Р., Джей С. Получение экологически чистого геополимерного пенобетона путем щелочной активации кирпичных отходов. Дж. Чистый. Произв. 2021;325:129180. doi: 10.1016/j.jclepro.2021.129180. [CrossRef] [Google Scholar]
3. Zhang S., Qi X., Guo S., Zhang L., Ren J. Систематическое исследование пенобетона: влияние содержания пены, летучей золы, шлака, микрокремнезема. и отношение воды к вяжущему. Констр. Строить. Матер. 2022;339:127683. doi: 10.1016/j.conbuildmat.2022.127683. [CrossRef] [Google Scholar]
4. Liu X., Ni C., Meng K., Zhang L., Liu D., Sun L. Механизм усиления легкого ячеистого бетона, наполненного летучей золой. Констр. Строить. Матер. 2020;251:118954. doi: 10.1016/j.conbuildmat.2020.118954. [CrossRef] [Google Scholar]
5. Zhang S., Cao K., Wang C., Wang X., Wang J., Sun B. Влияние микрокремнезема и отходов мраморного порошка на механические свойства и долговечность ячеистых материалов. конкретный. Констр. Строить. Матер. 2020;241:117980. doi: 10.1016/j.conbuildmat.2019.117980. [CrossRef] [Google Scholar]
6. Su Z., Hou W., Sun Z., Lv W. Исследование вспененного на месте геополимера летучей золы. Материалы. 2020;13:4059. doi: 10.3390/ma13184059. [Бесплатная статья PMC] [PubMed] [CrossRef] [Google Scholar]
7. Джонс М.Р., Маккарти А. Теплота гидратации в пенобетоне: влияние компонентов смеси и пластической плотности. Цем. Конкр. Рез. 2006; 36: 1032–1041. doi: 10.1016/j.cemconres.2006.01.011. [CrossRef] [Академия Google]
8. Джичайапхум К., Синсири Т., Чиндапрасирт П. Ячеистый легкий бетон, содержащий пуццолановые материалы. Procedia англ. 2011;14:1157–1164. doi: 10.1016/j.proeng.2011.07.145. [CrossRef] [Google Scholar]
9. Chen X., Yan Y., Liu Y., Hu Z. Использование летучей золы в циркулирующем кипящем слое для приготовления пенобетона. Констр. Строить. Матер. 2014;54:137–146. doi: 10.1016/j.conbuildmat.2013.12.020. [CrossRef] [Google Scholar]
10. Хилал А.А., Том Н.Х., Доусон А.Р. Применение добавок для улучшения свойств предварительно формованного пенобетона. Междунар. Дж. Инж. Технол. 2015; 7: 286–293. doi: 10.7763/IJET.2015.V7.806. [CrossRef] [Google Scholar]
11. Li Z., Yuan H., Gao F., Zhang H., Ge Z., Wang K., Sun R., Guan Y., Ling Y., Jiang N. Технико-экономическое обоснование пенобетона с низким содержанием цемента с использованием большого объема отработанного известкового шлама и летучей золы для дорожной насыпи. Материалы. 2022;15:86. doi: 10.3390/ma15010086. [Бесплатная статья PMC] [PubMed] [CrossRef] [Google Scholar]
12. Эсмаили Фалак М., Лотфи Э.А., Нематзаде С. Улучшение механических параметров бетона, полученного из пуццоланового цемента, для ирригационных и дренажных проектов. Дж. Структура. Констр. англ. 2019;6:43–58. [Google Scholar]
13. Ji Y., Zhang J., Wu Y.W., Shang C. C., Fan J.H. Влияние золы-уноса на пористую структуру и прочность пенобетона. Кремний. Бык. 2018; 37: 3657–3662. [Google Scholar]
14. Дей В., Бонакдар А., Мобашер Б. Низкоскоростная реакция на изгиб фибробетона на изгиб. Цем. Конкр. Композиции 2014;49:100–110. doi: 10.1016/j.cemconcomp.2013.12.006. [CrossRef] [Google Scholar]
15. Zhou D., Gao H., Liao H., Fang L., Cheng F. Улучшение характеристик пенобетона, содержащего летучую золу и стальной шлак, с помощью процесса вспенивания под давлением. Дж. Чистый. Произв. 2021;329:129664. doi: 10.1016/j.jclepro.2021.129664. [CrossRef] [Google Scholar]
16. Джатиал А.А., Гох В.И., Мастой А.К., Траоре А.Ф., Оад М. Экологическая оценка и механические свойства пенобетона, армированного полипропиленовыми волокнами на тройном вяжущем. Окружающая среда. науч. Загрязн. Рез. 2021;29:2985–3007. doi: 10.1007/s11356-021-15076-x. [PubMed] [CrossRef] [Google Scholar]
17. Falliano D., Parmigiani S., Suarez-Riera D., Ferro G. A., Restuccia L. Устойчивость, поведение при изгибе и прочность на сжатие сверхлегкого пенобетона, армированного волокнами с сухой плотностью менее 100 кг/м 3 . Дж. Билд. англ. 2022;51:104329. doi: 10.1016/j.jobe.2022.104329. [CrossRef] [Google Scholar]
18. Генсель О., Байрактар О.Ю., Каплан Г., Бенли А., Мартинес-Баррера Г., Бростоу В., Тек М., Бодур Б. Характеристики пенобетонов, армированных конопляным волокном с летучей золой и оптимизацией Тагучи. Констр. Строить. Матер. 2021;294:123607. doi: 10.1016/j.conbuildmat.2021.123607. [CrossRef] [Google Scholar]
19. Шекер Б., Гекче М., Токлу К. Исследование влияния микрокремнезема и синтетической добавки к пене на ячеистую структуру пенобетона сверхнизкой плотности. Кейс Стад. Констр. Матер. 2022;16:e01062. doi: 10.1016/j.cscm.2022.e01062. [Перекрестная ссылка] [Академия Google]
20. Приянка Э., Сатьян Д., Мини К.М. Функциональные и прочностные характеристики стеновых панелей из пенополистирола, встроенных в пенополистирол. Матер. Сегодня проц. 2021;46:5167–5170. doi: 10.1016/j.matpr.2021.01.592. [CrossRef] [Google Scholar]
21. Chung S.-Y., Lehmann C., Elrahman M.A., Stephan D. Характеристики пор и их влияние на свойства материала пенобетона, оцененные с использованием изображений микро-КТ и численных подходов. заявл. науч. 2017;7:550. doi: 10.3390/app7060550. [Перекрестная ссылка] [Академия Google]
22. Guo Y., Chen X., Chen B., Wen R., Wu P. Анализ пористой структуры пенобетона железнодорожного полотна на основе рентгеновской компьютерной томографии. Констр. Строить. Матер. 2021;273:121773. doi: 10.1016/j.conbuildmat.2020.121773. [CrossRef] [Google Scholar]
23. Zhao J., Deng Y., Gao P., Lu X., Zhang J., Zong J. Структура пор, морфология и прочность самоуплотняющегося вспененного материала, засыпанного за подземная труба-стена реки Хуанхэ. Материалы. 2020;13:5724. дои: 10.3390/ma13245724. [Бесплатная статья PMC] [PubMed] [CrossRef] [Google Scholar]
24. Zhu B.Q., Wei G.P. , Li H.C. Характеристики распределения пор по размерам пористых теплоизоляционных огнеупоров на основе анализа изображений. Дж. Силич. 2012;40:1369–1375. [Google Scholar]
25. Hu Y.L., Hao J.G., Zhao X.M., Peng H.L., Yang W.B., Gao P.W. Исследование взаимосвязи между характеристиками пенобетона и структурой пор. Дж. Нанкин унив. науч. Технол. 2019;43:363–366. [Академия Google]
26. Пэн Дж.З., Пэн X.Q., Гуй М.М., Цай З.З. Метод анализа изображений для характеристики структуры пор автоклавного ячеистого бетона. Матер. Гид. 2011;25:125–129. [Google Scholar]
27. Хаджимохаммади А., Нго Т., Мендис П., Нгуен Т., Кашани А., ван Девентер Дж.С. Характеристики пор в однокомпонентных геополимерных смесях, вспененных H 2 O 2 : Влияние состава смеси. Матер. Дес. 2017; 130:381–391. doi: 10.1016/j.matdes.2017.05.084. [Перекрестная ссылка] [Академия Google]
28. Хаджимохаммади А., Нго Т., Мендис П. Повышение прочности готовых пенопластов для пенобетона. Цем. Конкр. Композиции 2018; 87: 164–171. doi: 10.1016/j.cemconcomp.2017.12.014. [CrossRef] [Google Scholar]
29. Гонг Дж. К., Чжан В. Дж. Влияние пуццоланового порошка на структуру пор пенобетона и морозостойкость. Констр. Строить. Матер. 2019;208:135–143. doi: 10.1016/j.conbuildmat.2019.02.021. [CrossRef] [Google Scholar]
30. Pang C.M., Wang S.H. Характеристика пористой структуры пенобетона и ее влияние на эксплуатационные характеристики. Дж. Констр. Матер. 2017;20:93–98. doi: 10.1016/j.conbuildmat.2020.120958. [CrossRef] [Google Scholar]
31. Zhang X., Yang Q., Shi Y., Zheng G., Li Q., Chen H., Cheng X. Влияние различных методов контроля на механические и термические свойства сверхлегкий пенобетон. Констр. Строить. Матер. 2020;262:120082. doi: 10.1016/j.conbuildmat.2020.120082. [CrossRef] [Google Scholar]
32. Liang X.Q., Huang P.B., Huang B.Z., Yang L.M., Sun W.X., Lin Y.M., Ren Z.Q., Li Y.D., Liu H. Экспериментальное исследование долговечности автоклавного ячеистого бетона на основе пор структуру в циклах замораживания-оттаивания. Матер. Гид. 2021; 35: 200–204. [Академия Google]
33. Гу Ю.С., Ван Ю.З., Ван Х.М. Прогресс исследования пенобетона с различными процессами. Конкретный. 2013;12:148–152. [Google Scholar]
34. Пенобетон. Национальные стандарты Китайской Народной Республики; Пекин, Китай: 2011. [Google Scholar]
35. Теплоизоляционные материалы. Определение стационарного теплового сопротивления и связанных с ним свойств. Метод измерения теплового потока. Национальные стандарты Китайской Народной Республики; Пекин, Китай: 2008 г. [Google Scholar] 9.0003
36. Теплоизоляционные материалы. Определение стационарного теплового сопротивления и связанных с ним свойств. Метод защитной горячей плиты. Национальные стандарты Китайской Народной Республики; Пекин, Китай: 2008. [Google Scholar]
37. Технические условия на применение пенобетона. Национальные стандарты Китайской Народной Республики; Пекин, Китай: 2014. [Google Scholar]
38. Su L.J., Sun Q., Li S.W. Влияние дозировки пенообразователя на прочность зольного пенобетона. Неуд. 2017; 40:53–55. [Академия Google]
39. Лю З.К. Влияние комплексных минеральных добавок на характеристики пенобетона. Конкр. Цем. Произв. 2021; 8: 1–4. doi: 10.19761/j.1000-4637.2021.08.001.04. [CrossRef] [Google Scholar]
40. Zhang X.S., Zhu Y.F., Huang L.C. Влияние полипропиленовой фибры на свойства пенобетона. Новая сборка. Матер. 2019;46:140–142. [Google Scholar]
41. Li H., Jun L., Lu Z.Y., Niu Y.H. Влияние пенообразователя на цемент и пенобетон. Констр. Строить. Матер. 2021;280:122399. doi: 10.1016/j.conbuildmat.2021.122399. [CrossRef] [Google Scholar]
42. Чжао Х., Сунь В., Ву Х.М., Бо Г. Свойства самоуплотняющегося бетона с минеральными добавками золы-уноса и измельченного гранулированного доменного шлака. Дж. Чистый. Произв. 2015;95:66–74. doi: 10.1016/j.jclepro.2015.02.050. [CrossRef] [Google Scholar]
43. Ян П.Ю., Чжан Б. Механические свойства высокопрочного бетона, приготовленного с использованием различных форм микрокремнезема. Дж. Силич. 2016;44:196–201. doi: 10.14062/j.issn.0454-5648.2016.02.03. [Перекрестная ссылка] [Академия Google]
44. Гэн Л. Магистерская диссертация. Ляонинский университет науки и технологий; Аньшань, Китай: 2018 г. Экспериментальное исследование соотношения компонентов смеси и характеристик сверхлегких изоляционных материалов из пенобетона. [Google Scholar]
45. Batool F., Rafi M.M., Bindiganavile V. Микроструктура и теплопроводность цементной пены: обзор. Дж. Билд. англ. 2018;20:696–704. doi: 10.1016/j.jobe.2018.09.008. [CrossRef] [Google Scholar]
46. Гекче Х.С., Хатунгимана Д., Рамьяр К. Влияние летучей золы и микрокремнезема на твердые свойства пенобетона. Констр. Строить. Матер. 2019;194:1–11. doi: 10.1016/j.conbuildmat.2018.11.036. [CrossRef] [Google Scholar]
47. Хилал А.А., Том Н.Х., Доусон А.Р. Структура пор и характеристики проницаемости пенобетона. Дж. Адв. Конкр. Технол. 2014;12:535–544. doi: 10.3151/jact.12.535. [CrossRef] [Google Scholar]
48. Амран Ю.М., Фарзадния Н., Али А.А. Свойства и области применения пенобетона; Обзор. Констр. Строить. Матер. 2015;101:990–1005. doi: 10.1016/j.conbuildmat.2015.10.112. [Перекрестная ссылка] [Академия Google]
49. Нин Х., Ху Ю., Чжун Ю., Лю С.Р. Пористая структура и морозостойкость многослойного полипропиленового фибробетона. Дж. Чунцинский университет 2019;42:38–46. [Google Scholar]
50. Zhou X.Y., Yang D.Y., Zhu C.X., Wang T.Z., Zhao X.T., Liu M. Долговечность бетона, армированного полипропиленовым волокном, на основе анализа пористой структуры. Матер. науч. англ. Дж. 2022; 40:110–115. doi: 10.14136/j.cnki.issn1673-2812.2022.01.018. [CrossRef] [Google Scholar]
51. Шан Х.С., Йи Т.Х. Морозостойкость воздухововлекающего бетона. науч. Мир J. 2013; 2013: 650791. doi: 10.1155/2013/650791. [Бесплатная статья PMC] [PubMed] [CrossRef] [Google Scholar]
52. Ричардсон А.Е., Ковентри К.А., Уилкинсон С. Морозостойкость бетона с добавками синтетических волокон. Холодный рег. науч. Технол. 2012;83–84:49–56. doi: 10.1016/j.coldregions.2012.06.006. [CrossRef] [Google Scholar]
53. Эбрахими К., Даизаде М.Дж., Закертабризи М., Захматкеш Ф., Кораем А.Х. Обзор влияния микро- и наночастиц на морозостойкость затвердевшего бетона: перспектива механизма. Констр. Строить. Матер. 2018;186:1105–1113. doi: 10.1016/j.conbuildmat.2018.08.029. [CrossRef] [Google Scholar]
54. Peng Z., Li Q.F. Влияние полипропиленовой фибры на долговечность бетонного композита, содержащего летучую золу и микрокремнезем. Композиции Часть Б англ. 2013;45:1587–1594. doi: 10.1016/j.compositesb.2012.10.006. [CrossRef] [Google Scholar]
55. Wang C.X., Liu L., Cao F.B., Lu L. Экспериментальное исследование механических свойств переработанного бетона после циклов замораживания-оттаивания. Дж. Билд. Структура 2020; 41: 193–202. doi: 10.14006/j.jzjgxb.2018.0542. [Перекрестная ссылка] [Академия Google]
56. Данети С.Б., Ви Т.Х., Тангая Т.С. Влияние полипропиленовых волокон на растрескивание легкого бетона при усадке. Маг. Конкр. Рез. 2011;63:871–881. doi: 10.1680/macr.2011.63.11.871. [CrossRef] [Google Scholar]
57. Cheng H.Q., Gao D.Y. Экспериментальное исследование морозостойкости бетона, армированного полипропиленовой фиброй. Дж. Юго-Восточный ун-т. (Нац. науч. ред.) 2010; 40: 197–200. [Google Scholar]
Статьи из Материалов предоставлены здесь любезно предоставлены Многопрофильный институт цифровых публикаций (MDPI)
Как производится пена и какие материалы используются для ее изготовления?
После утомительного рабочего дня мы все ожидаем, что качественный отдых вознаградит нас за все усердие, которое мы вложили в работу. Матрасы, несмотря на то, что им очень пренебрегают, играют важную роль в обеспечении крепкого сна и отдыха ночью.
Времена меняются, и типы матрасов меняются колоссально. Эти матрасы удовлетворяют потребности различных людей и значительно уменьшают боль в спине или суставах, причиняемую определенным людям.
«Пенополиуретан» в последнее время стал модным словечком применительно к матрасам. Но возникает вопрос: что такое поролон, как он делается и какие материалы используются? Продолжайте читать, чтобы получить достоверные ответы на все эти вопросы.
Машины для производства пены Что такое завод по производству пены?Завод по производству пенопласта — это производственная единица, производящая пену, которую мы видим вокруг себя. Он может производить многие типы пенопластов, например,
Пену можно найти везде, от автомобильных сидений до бытовых приборов в качестве изоляторов. Он образуется путем создания пузырьков газа в пластике с помощью вспенивающего агента. В то время как производство ламинатного пенопласта представляет собой непрерывный процесс, придающий ему различные размеры и формы, он производится партиями с помощью различных станков для резки пенопласта.
Теперь в машинах для резки пенопласта используются различные материалы, такие как резаки или лезвия. Более того, в этих машинах чаще всего используется горячая проволока. На заводе по производству пенопласта используется множество пеногенераторов различных форм и размеров, предназначенных для различных целей.
Эластичный пенопласт имеет открытую структуру и производится в двух вариантах плотности: высокой и низкой. Хотя, напротив, пена низкой плотности идеальна для амортизирующих целей, жесткая пена высокой плотности сильно сшита и препятствует движению газа. Поэтому они используются в качестве изолятора в зданиях и морозильных камерах.
Как делают пену? Самая основная функция производства пены на заводе – это жидкая стадия; он расширяется в виде пузырьков воздуха, а затем затвердевает в виде геля. Co2 является одним из основных пенообразователей при производстве пенопласта. Он вдувается в полиуретан, образуя небольшие воздушные карманы для создания пены.
As mentioned above, there are two processes of manufacturing, so separate machines serve different purposes:
Помимо машин для производства пены, для производства пены используются несколько химикатов и ингредиентов.
Резка пенопласта Поскольку пенопласт является очень адаптивным материалом, который может принимать любую форму, размер или плотность, он используется во многих отраслях промышленности. Следовательно, для различных продуктов требуются определенные формы пенопласта, которых можно достичь с помощью различных типов резки пенопласта. Поэтому давайте кратко рассмотрим несколько типов станков для резки пенопласта .
Обычно пена состоит из следующих химических веществ: 40 % полиизоцианатов, 10 % воды и 50 % полиола. Полиизоцианаты и полиолы представляют собой жидкие полимеры, которые производят экзотермическую (выделяющую тепло) реакцию с образованием полиуретана. Двумя полиизоцианатами являются дифенилметандиизоцианат (МДИ) и толуолдиизоцианат (ТДИ). В то время как MDI используется в жестких пенах, TDI используется в более гибких пенах.
В этом процессе используется широкий спектр добавок. Катализаторы, такие как олово и амины, ускоряют реакцию, позволяя производить их в больших количествах.
Заключение
Матрасы значительно эволюционировали, и технология, используемая в этом процессе, требует абсолютного совершенства, а машины являются жизненно важным элементом, который помогает достичь того же. Поэтому для обеспечения отличного качества необходимо полагаться на лучших производителей пенообразователей и машин для резки.
Santech Industries является ведущим производителем пенопластовых машин . Компания полна решимости разрабатывать лучшие машины с более чем 22-летним опытом, что делает ее надежным и заслуживающим доверия именем, когда речь идет о машинах для производства пенопласта и резки.
Полное руководство по изготовлению Aircrete и многое другое – Domegaia
Вы скоро научитесь строить из Aircrete, шаг за шагом, даже если вы никогда раньше не строили из подобного материала. Создание чего-либо из ничего может быть совершенно запутанным, но мы собираемся сделать это простым и выполнимым для вас, чтобы вы могли построить структуру и даже разрешить ее. Мы помогли сотням людей строить из газобетона, и мы знаем, что вы тоже можете это сделать.
Get Started Building with Aircrete
Table of Contents
1. What is Aircrete
2. Benefits of Aircrete
3. Ways to Use Aircrete
4. The Domegaia Aircrete Building System
5. Как сделать Aircrete
6. Как сделать блоки Aircrete
7. Насколько прочен Aircrete?
8. Сколько стоит Aircrete
9. Сколько весит Aircrete
10. Какова изоляционная ценность Aircrete
Причина № 1, почему люди работают с Aircrete
Сотни людей, практически не имеющих опыта строительства, присоединились к строительной мастерской и приобрели необходимую уверенность начать собственный проект.
Загружаемая и бесплатная электронная книга
Загрузите наше лучшее руководство «Сделай сам» по:
Подробные инструкции о том, как сделать газобетонные блоки, залить пеноблоки и многое другое, чтобы вы могли мечтать о большем.
Загрузить бесплатную электронную книгу
Компания Domegaia ввела термин Aircrete в 2014 году, но он также известен под торговыми марками газобетона, ячеистого бетона, пенобетона или легкого бетона.
Aircrete — это легкая, нетоксичная и недорогая кладка материал, который производится путем введения крошечных пузырьков воздуха в виде пены в цементный раствор портландцемента. Пена многократно увеличивает объем цемента.
Проще говоря, Aircrete представляет собой смесь воды, цементного порошка и пены на водной основе.
Газобетон огнестойкий, устойчивый к насекомым и не повреждается влагой – он не гниет и не разлагается. Он обеспечивает хорошую тепло- и звукоизоляцию. В отличие от бетона, который твердый, тяжелый, холодный и с ним трудно работать; С Aircrete легко работать. Он затвердевает в течение ночи, и его можно резать, резать, сверлить и придавать форму деревообрабатывающим инструментам. Он принимает гвозди, шурупы и легко ремонтируется. Он продолжает затвердевать с течением времени и из него получаются отличные фундаменты, черновые полы, строительные блоки, стены, купола, арки или что-то еще. Ему можно придать форму или придать практически любую форму.
Ключ в пене
Газобетонная пена производится путем перемешивания пенообразователя сжатым воздухом. В качестве пенообразователя можно использовать обезжиривающее моющее средство для посуды хорошего качества.
Для газобетона подходит не любая пена, это высококачественная специализированная формула с определенной плотностью.
В течение многих лет газобетон производился только в промышленных масштабах с использованием мощного оборудования. Однако, когда основатель Domegaia Хаджар Джебран обнаружил свойства газобетона, он изобрел специальные генераторы пены под названием Little Dragon и DragonXL, чтобы сделать его доступным для всех.
Теперь каждый, кто хочет строить из газобетона, может производить пену, необходимую для газобетона, путем смешивания воздуха под высоким давлением и мыльного раствора.
Существует множество преимуществ использования Aircrete, но все зависит от области применения. В то время как aircrete
Основные преимущества:
Чтобы прочитать исчерпывающую статью о «Почему Aircrete неотразим для домашних мастеров» .
Газобетон — это материал мечты, который можно сделать своими руками. Но что именно вы можете сделать с Aircrete?
Он универсален, так как принимает форму всего, во что вы его превращаете. Даже после того, как газобетон затвердеет, его легко долбить, пилить, вырезать отверстия, придавать ему неправильную форму и многое другое.
Чтобы дать вам представление о том, для чего вы используете Aircrete, мы составили здесь забавный список.
Использование Aircrete:
Полный список из более чем 75 способов использования газобетона читайте здесь.
Чтобы лучше понять, как все работает вместе. Давайте начнем с рассмотрения всей строительной системы Aircrete. Когда все настроено, эта система производит столько партий газобетона, сколько вам нужно для вашего строительного проекта.
Все вместе…
1. ВОЗДУШНЫЙ КОМПРЕССОР
Создает воздух, необходимый для создания пузырьков в пене
2. ВЕДРО ДЛЯ ПЕНООБРАЗОВАТЕЛЯ
Содержит мыло и воду для подачи пены с пенообразователем.
ЭТИ ОБА ПОДСОЕДИНЯЮТСЯ К…
3. ПЕНОГЕНЕРАТОР – Dragon XL
Это позволяет регулировать давление воздуха, чтобы обеспечить необходимое количество пенообразователя
, и перекачивать эту пену в смеситель.
ПОДКЛЮЧАЕТСЯ К…
4. СМЕСИТЕЛЬ ДЛЯ ИНЖЕКТОРА ПЕНЫ
Когда пена закачивается в смеситель, насадка-трубка позволит вам сначала измерить вес пены. Затем, когда у вас будет идеальный вес пены, вы прикрепите палочку и начнете смешивать.
СМЕСИ…
5. ВЕДРО ДЛЯ СМЕШИВАНИЯ
Теперь миксер будет смешивать и нагнетать пену в ведро для смешивания, в котором находится мешок с цементом и водой весом 94 фунта.
ЗАЛИВАЕТ В…
6. ФОРМЫ
Эти формы можно подогнать под блоки размером 4, 6 или 12 дюймов.
Блоки затвердевают не менее 24 часов.
Газобетон недорогой, простой в изготовлении и с ним легко работать. Он требует только базовых навыков.
В этой статье дается краткий обзор того, как сделать Aircrete.
Для получения более подробных инструкций загрузите наше бесплатное руководство по Aircrete с пошаговыми инструкциями.0003
Газобетон легко приготовить, но это очень похоже на выпечку торта, вам нужно правильно подобрать рецепт. Большое значение имеет качество и плотность пены. Используйте точные почтовые или кухонные весы, чтобы проверить вес вашей пены. Она должна быть в пределах 90-100 граммов на литр (около 3 унций на кварту).
Вы можете использовать средство для мытья посуды хорошего качества, чтобы сделать пену с Little Dragon, нашим генератором пены непрерывного действия. Ищите обезжиривающее моющее средство с высоким пенообразованием. Мы протестировали натуральную жидкость для тарелок седьмого поколения, концентрат Dawn Ultra и Safeway Home. Все они давали достаточную пену, разбавленную водой 40/1. (5 галлонов воды / 2 стакана пенообразователя). Добавьте моющее средство в воду и тщательно перемешайте.
Вы также можете использовать коммерческие пенообразователи, предназначенные для изготовления ячеистого бетона. Для получения дополнительной информации и списка источников ознакомьтесь с этой ссылкой.
ВОЗДУШНЫЙ КОМПРЕССОР
Вам нужен воздушный компрессор мощностью не менее 2,5 куб. Вы также можете использовать компрессор большего размера, если он у вас есть.
ЭТАП СМЕШИВАНИЯ
Смешайте один мешок цемента весом 94 фунта с 6 галлонами (США) воды. Сначала налейте в емкость всю воду и добавляйте цемент во время смешивания, чтобы избежать образования комков. Когда цемент и вода хорошо перемешаются, включите «Маленького дракона» и добавьте в смесь пену. Добавьте столько пены, чтобы получилось 45 галлонов Aircrete. Это примерно 30 дюймов в высоту в стандартной бочке на 55 галлонов.
Пена очень легкая, поэтому она будет плавать поверх цементной смеси. Наш смеситель для впрыска пены впрыскивает пену непосредственно в смесительные лопасти в нижней части бочки, где она смешивается с цементом, прежде чем она сможет всплыть наверх.
Вы также можете использовать мощную дрель с мешалкой, как эта из Home Depot. Просто убедитесь, что пена вмешивается в смесь, пока она не будет тщательно перемешана.
ЗАЛИВКА СВЕЖЕЙ ПАРТИИ АГРЕГАТА
Газобетон необходимо залить в форму и дать ему затвердеть в течение ночи. Из него получаются хорошие фундаменты, плиты и черновые полы. Положите пластик, чтобы вода не испарялась и он полностью затвердел. В сухом климате сбрызните его водой, чтобы он оставался влажным в течение нескольких дней, чтобы ускорить процесс отверждения.
Aircrete можно использовать методом «вырубки» для изготовления строительных блоков. Сделайте прямоугольные деревянные формы из Aircrete, соединив углы дверными петлями со съемными штифтами для легкой сборки и разборки.
Положите пластиковый лист под рамы и вокруг них, чтобы Aircrete не вытекал. Нанесите растительное масло или другое разделительное средство на рамы. Заполните формы Aircrete. После того, как Aircrete схватится в течение ночи, нарежьте его на блоки с помощью ножа или длинного лезвия из стали 16 калибра. Полные инструкции по изготовлению форм из Aircrete своими руками вы найдете в нашем бесплатно загружаемом электронном руководстве по Aircrete здесь.
Если вы не хотите делать формы своими руками, в нашем магазине есть многоразовые сборные формы.
Покройте наружную поверхность тонким слоем латексного клея и армирующей тканью. Это очень хорошо работает для получения поверхности с защитой от трещин и очень прочной структуры. Вот ссылка на один тип ткани, который хорошо работает. Вы также можете усилить Aircrete, добавив в смесь волокно.
Существует множество штукатурок, герметиков и покрытий, обладающих хорошими качествами, на которые стоит обратить внимание. Или используйте смесь мелкого песка/цемента 2/1.
Смотреть производство кирпича из газобетона…
Структура должна выдерживать как растяжение, так и сжатие – это два вездесущих бога, толкающие и притягивающие все физические формы.
Газобетон имеет хорошую прочность на сжатие, но низкую прочность на растяжение. Когда армированный волокном цемент приклеивается к поверхности Aircrete, образуется композитный материал (Aircrete с поверхностным связыванием), обладающий прочностью как на сжатие, так и на растяжение. Наклеенный на поверхность Aircrete можно превратить в элегантную архитектуру, которая выдержит силы природы и испытание временем.
В случае купольной конструкции это самонесущая сжатая оболочка, которая требует минимальной или вообще не требует растягивающей арматуры выше экватора. Структурная целостность купола Aircrete с поверхностным соединением формируется за счет соотношения между композитным материалом и жесткостью, присущей куполу с двойной кривизной.
При прочих равных условиях, чем больше кривизна, тем прочнее форма. И наоборот, более плоские поверхности создают более слабые формы.
Когда силы, действующие на сжатую оболочку, понимаются и учитываются, мы можем строить элегантные конструкции великолепной целостности. Искусство создания равновесия в структуре может создавать поэтические формы, состоящие из гармонической геометрии, выражающие изящный танец с силами природы.
Прекрасная аналогия, которую мы любим использовать, когда речь заходит о повышении прочности Aircrete, заключается в сравнении Aircrete с доской для серфинга.
Внутренняя часть доски для серфинга легкая и хрупкая, однако, когда вы наносите на доску прочность на растяжение и покрытие, она становится прочным и прочным объектом. То же самое касается Aircrete. Сам по себе Aircrete разрушим, однако, если вы окружите его слоями, вы получите прочную структуру.
Изготовление конструкции из Aircrete очень похоже на изготовление доски для серфинга путем наклеивания стекловолокна на пенопласт или на гипсокартон путем наклеивания бумаги на гипс. Слой бумаги, стекловолокна или прочной ткани создает на поверхности натяжную мембрану, которая не трескается и не ломается. AirCrete с поверхностным соединением может снизить затраты по сравнению с традиционными методами строительства в 10 раз.
Мы разработали систему прочности на растяжение, чтобы создать силу, на которую вы можете положиться.
Все мы помним, что узнали в детстве от трех поросят. Если вы построите свой дом из веток, Большой Злой волк будет пыхтеть, пыхтеть и сдувать ваш дом. Купольный дом из аэробетона с поверхностным соединением аэродинамический и очень прочный против Большого Злого Волка.
Большой вопрос, который вы, вероятно, задаете себе, это…
Действительно ли строительство с использованием Aircrete экономит ваши деньги?
Да, это действительно так. Это может быть очень сложно рассчитать напрямую из-за толщины, размеров, типа дома и используемого материала, но вот основная идея.
Стоимость шлакоблока для строительства 1000 кв. м.
В среднем 11 долл. США за кв. фут x 1000 кв.
В среднем 4 доллара США за квадратный фут x 1000 квадратных футов = 4000 долларов США Итого
Это действительно может сильно измениться, где вы получаете материалы, покупаете ли вы блоки или изготавливаете их сами и многие другие аспекты. Так что примите это как недоверие и изучите стоимость собственных проектов соответственно.
Стоимость рабочей силы и необходимых материалов может стать реальной экономией. Учитывая, что вес блока Aircrete примерно на 80% легче, ребенок может легко переносить его. Это означает, что для перемещения на один блок выше в здании не нужны лифты или оборудование. Простая веревка могла легко поднять его или даже с легкостью поднять по пандусу.
Также для самодельных блоков ваши инвестиции в инструменты для изготовления блоков Aircrete по сравнению с шлакоблоками также являются большой разницей.
Когда мы говорим о весе Aircrete, мы говорим о весе одного строительного блока Aircrete.
Типичный размер наших газобетонных блоков составляет 3,7–4 дюйма в толщину и 12 дюймов x 12 дюймов.
Каждый блок в среднем весит: 6 фунтов. 11 унций
Чтобы сравнить это со шлакоблоками размерами 8 дюймов x 8 дюймов x 16 дюймов и весом 38 фунтов/17 кг
Плотность газобетона:
22 фунта. /куб.фут.
Говоря простым языком, Aircrete действует как конструкционный материал и изолятор. В отличие от традиционного дома с деревянным каркасом, который требует нескольких слоев для создания структуры и изоляции, Aircrete сочетает в себе и то, и другое.
ЧТО ТАКОЕ R-ЗНАЧЕНИЕ: R-значение относится к способности материала сопротивляться тепловому потоку.
Измеряется путем приложения источника тепла к одной стороне материала и измерения потерь тепла на противоположной стороне материала. Например, 70 градусов прикладывают к одной стороне стены, а 50 градусов измеряют к другой стороне стены. Это 20 градусов потери тепла.
Чем выше значение R, тем меньше тепла передается на другую сторону и, следовательно, обеспечивается более высокая теплоизоляция или тепловые характеристики.
Вообще говоря, R-значение Aircrete составляет 1,8-2,2. Это основано на многих цитируемых исследованиях Aircrete.
Однако, когда мы говорим об Aircrete, гораздо полезнее думать о R-значении в сочетании с тепловой массой.
Чтобы узнать больше об R-Value, прочитайте нашу статью «R-Value: раскрытие истории».
ТЕПЛОВАЯ МАССА: Тепловая масса – это способность материала поглощать и накапливать тепловую энергию, а затем постепенно ее выделять. Изоляционные материалы, с другой стороны, препятствуют прохождению тепла через них.
Давайте рассмотрим несколько примеров взаимодействия между тепловой массой и R-значением.
Сплошная бетонная стена имеет высокую теплоемкость, но очень низкое значение теплопроводности. Если вы приложите тепло к одной стороне в течение короткого времени, оно не будет ощущаться с другой в течение длительного времени. Как только тепло будет передано, большая часть тепла будет ощущаться, потому что низкое значение R не уменьшит передаваемое количество.
Это означает, что потребуется время, чтобы тепло перешло с одной стороны на другую, но как только это произойдет, потеря температуры будет незначительной.
Напротив, тонкая стальная стенка имеет как низкую термическую массу, так и R-значение. В этом случае тепло, подаваемое на поверхность, будет мгновенно ощущаться на другой стороне, а также быстро остывать после отвода тепла.
АГРЕГАТ ИМЕЕТ И ЗНАЧЕНИЕ R, И ТЕПЛОВУЮ МАССУ
Газобетон имеет как R-значение, так и термическую массу, что является уникальным свойством для строительного материала. Примите во внимание тот факт, что большинство изоляционных материалов не имеют тепловой массы, но имеют высокое значение R, а строительные материалы, такие как бетон, саман и утрамбованная земля, имеют тепловую массу, но имеют очень низкое значение R.
Для более глубокого изучения ценности R прочитайте нашу статью “Миф о ценности R”.
Помните, если вы еще этого не сделали, мы вложили нашу любовь и энергию в создание удобной и бесплатной электронной книги в формате pdf: Aircrete 101.