цены на подсистемы для вентфасада за м2 от компании «Кронос Фасад»
Главная > Облицовочные материалы > Алюминиевые композитные панели
ООО «КРОНОС ФАСАД» предлагает купить композитные панели для фасада по цене производителя. Материал представляет собой систему из двух алюминиевых листов, пространство между которыми заполнено полимерным или минеральным утеплителем. Лицевая сторона изделий имеет декоративное покрытие. Композитные панели предназначены для устройства декоративных и рекламных элементов, а также вентилируемых фасадов.
Преимущества конструкции
Высокая плоскостность. Листы противостоят скручивающим нагрузкам. В производстве алюминиевых композитных панелей для фасадов используется метод прокатки, а не прессовки, поэтому напряжения между слоями распределяются равномернее. Конструкция жесткая, устойчивая к деформации.
Широкий выбор дизайнов. Панели производят в широком ассортименте по фактуре и цвету. Заказчик может выбрать цвет ЛКП в соответствии со своими вкусовыми предпочтениями. Возможно окрашивание в стандартные цвета RAL, в оттенки металлик, воспроизведение текстуры природного камня или дерева и т. д. Мы также предлагаем материалы с хромированным и золотистым покрытием.
Небольшой вес. Вентилируемые фасады из композитных панелей не создают чрезмерной нагрузки на несущие элементы. Усиливать несущие стены не потребуется.
Устойчивость к внешним воздействиям. Декоративное покрытие на металл наносится в современных распылительных аппаратах. Краска на полимерной основе устойчива к выцветанию, к механическим воздействиям, долго сохраняет свой первоначальный вид. Покрытие дополнительно защищает алюминий от ржавчины.
Удобство в обработке. В процессе монтажа панели можно сверлить, резать, фрезеровать, склеивать, сгибать, обрабатывать другими способами. Лакокрасочное покрытие, металл и внутреннее наполнение остаются целостными. Панели не расслаиваются и легко принимают нужную геометрическую форму.
Особенности производства алюминиевых фасадных панелей
Процесс включает следующие этапы.
- Подготовка металлических листов. Алюминий очищают от загрязнений, обезжиривают с помощью специальных химических смывок.
- Окрашивание металла. На поверхность листов наносят полимерное покрытие или декоративную пленку.
- Склеивание панели. Между двумя алюминиевыми обшивками прокладывают утеплитель и склеивают конструкцию под действием повышенной температуры и давления.
Материал сходит с производственной линии в виде непрерывной ленты. Отдельные панели нарезает специальный станок.
Виды наполнителей для композитных панелей
Минеральный. В качестве наполнителя для панелей используется вспененный полиэтилен. Мы применяем полимер высокого давления, так как он имеет большую плотность и прочность. В состав добавлены антипирены, которые исключают каплеобразование при горении, уменьшают количество дыма, вызывают самозатухание материала при отсутствии воздействия открытого огня. Группа горючести – Г1.
Алюминиевый. В качестве наполнителя использована гидроокись алюминия. Это вещество белого цвета, которое не горит и не выделяет токсичного дыма при нагревании. Монтаж панелей с минеральным наполнителем можно выполнять без устройства дополнительных противопожарных отсечек в проемах. Группа горючести – НГ.
Полимерный. Наполнитель изготавливают из пенополиэтилена и сотового полипропилена. Материал легкий, поэтому широко используется для облицовки перегородок, каркасных конструкций с невысокой несущей способностью преимущественно внутри помещений.
Виды декоративно-защитных покрытий композитных панелей
PE (полиэстер). Краска на основе полиэфиров создает прочное покрытие с хорошими декоративными свойствами. Материал недорогой, но панель придется подкрашивать с периодичностью 1 раз в несколько лет.
PVDF (поливинилиденфторид). Покрытия устойчивы к воздействию ультрафиолета, атмосферных факторов. Наличие фтора придает краске повышенную прочность и улучшает адгезию пленки к алюминию. Покрытия представлены широким ассортиментом по цвету. Срок службы поливинилиденфторидного окрашивания – 15–20 лет.
Оксидные пленки. Покрытие получают методом электрохимического анодирования алюминия. На поверхности металла образуется тонкий слой оксида, непроницаемый для воды и кислорода. Алюминий дополнительно покрывают прозрачной защитной пленкой. Цвета пленок ограничены гаммой металлик, оттенками бронзы, серебра.
Ламинирующие покрытия. Панели покрывают декоративно-защитной пленкой, которую можно окрасить или нанести на нее рисунок. Ламинированные материалы имитируют фактуру камня, дерева, поэтому используются для оформления отдельных участков фасада, например цоколя.
Особенности монтажа композитных панелей на фасады
Отделка такого типа подходит для кирпичных, деревянных, бетонных стен и конструкций из других материалов. Поверхность очищают, выравнивают, заделывают дефекты строительным раствором.
Порядок монтажа следующий.
- Устройство обрешетки.
- Крепление панелей. Элементы начинают укладывать с нижнего края, выравнивая положение каждого по вертикали и горизонтали. В качестве крепежа используют заклепки из алюминия или нержавеющей стали.
- Оформление углов. Существует два варианта. Можно крепить панели в углах встык, оставляя компенсационный зазор, либо выгибать отдельные элементы с помощью станка.
Сверлить металл рекомендуется низкооборотистой дрелью на скорости 500–800 об/мин. Если частота вращения будет выше, то защитное покрытие по краям отверстия будет повреждено. В этом месте возникнет коррозия. Если необходимо просверлить несколько отверстий сразу, то сверло периодически охлаждают водой. Для заточки лучше использовать автоматический инструмент. Чем острее кончик, тем меньше повреждение материала.
При выгибании панели тщательно очищают. На поверхности не должно быть песка, стружки, других механических загрязнений. Твердые частицы при давлении оставят на лицевой стороне царапины или сколы.
Как выбрать панели для фасада
При выборе в первую очередь учитывают требования пожарной безопасности к ограждающим конструкциям зданий. Облицовка класса Г1 и выше стоит дороже, но отделку Г2-Г4 можно использовать в строительстве только в декоративных целях.
Второй важный фактор – цвет панелей. В базовую цену обычно включают окрашивание в один из стандартных цветов RAL: бежевый, белый, серый и т. д. Оттенки металлик, имитация текстур придают материалу оригинальность, но потребуют дополнительной оплаты.
Сколько стоят алюминиевые панели для вентфасадов
Цена за м2 композитных панелей для фасада зависит от выбранного наполнителя, дизайна, размера и общего количества материала. Услуги доставки и монтажа оплачиваются отдельно. Для расчета полной стоимости достаточно выслать на нашу электронную почту чертежи фасада, его фотографии либо спецификацию элементов. Также можно посетить наш офис, где вам помогут с выбором облицовочного материала для фасада, подконструкции и проконсультируют по всем интересующим вопросам.
Композитные алюминиевые панели от ООО «КРОНОС ФАСАД»
Наша компания производит широкий ассортимент панелей и других комплектующих для вентилируемых фасадов. Мы проектируем, изготавливаем и монтируем системы любой сложности.
Наши преимущества:
- разработка индивидуальных решений, соответствующих пожеланиям заказчика;
- строгое соблюдение строительных норм и отраслевых стандартов;
- гарантия качества, надежности предлагаемых конструкций;
- выгодные цены без переплат посредникам;
- исполнение заказов любой сложности в сжатые сроки;
- широкий выбор материалов в наличии на складе.
Для получения подробной консультации приезжайте в наш офис или позвоните по телефону, указанному на сайте.
Смотрите также:
Прототип изготовленных цифровым способом тонких стеклокомпозитных фасадных панелей
Введение
Цифровые методы производства позволяют нам улучшить наше производство за счет преобразования традиционных подходов и предоставления новых возможностей дизайна [1]. Традиционные методы строительства имеют тенденцию к чрезмерному использованию материалов с точки зрения стоимости, базовой геометрии и безопасности. Благодаря переносу строительства на фабрики с использованием модульной сборной конструкции и робототехники для реализации новых подходов к проектированию материалы можно использовать эффективно без ущерба для безопасности. Цифровое производство позволяет нам расширить наше дизайнерское воображение, что приводит к более разнообразным, эффективным и амбициозным геометриям. В то время как процессы проектирования и расчета в значительной степени стали цифровыми, производство и сборка в основном по-прежнему выполняются традиционным способом с использованием ручного труда. Чтобы справиться с растущей сложностью структур произвольной формы, цифровые производственные процессы становятся все более важными. Стремление к свободе и гибкости дизайна, особенно в фасадах, неуклонно растет. Помимо визуального эффекта фасадов произвольной формы они также могут создавать более эффективные конструкции, например, с использованием мембранного эффекта [2].
В данной статье исследуется, как цифровые технологии могут быть использованы при проектировании и производстве инновационной композитной фасадной панели, состоящей из аддитивно изготовленного полимерного ядра и приклеенных тонких стеклянных наружных листов. В дополнение к новым архитектурным возможностям, возникающим в результате использования тонкого стекла, экологические и экономические критерии являются важной мотивацией для строительства ограждающих конструкций с использованием меньшего количества материала. Параллельно с изменением климата, нехваткой ресурсов и ростом цен на энергоносители в будущем стекло должно использоваться более разумно. Использование тонкого стекла толщиной менее 2 мм из электронной промышленности обещает создание легких фасадов с меньшим использованием сырья. Благодаря высокой гибкости тонкого стекла оно открывает новые возможности для архитектурных приложений и в равной степени приводит к новым инженерным задачам [3,4,5,6].
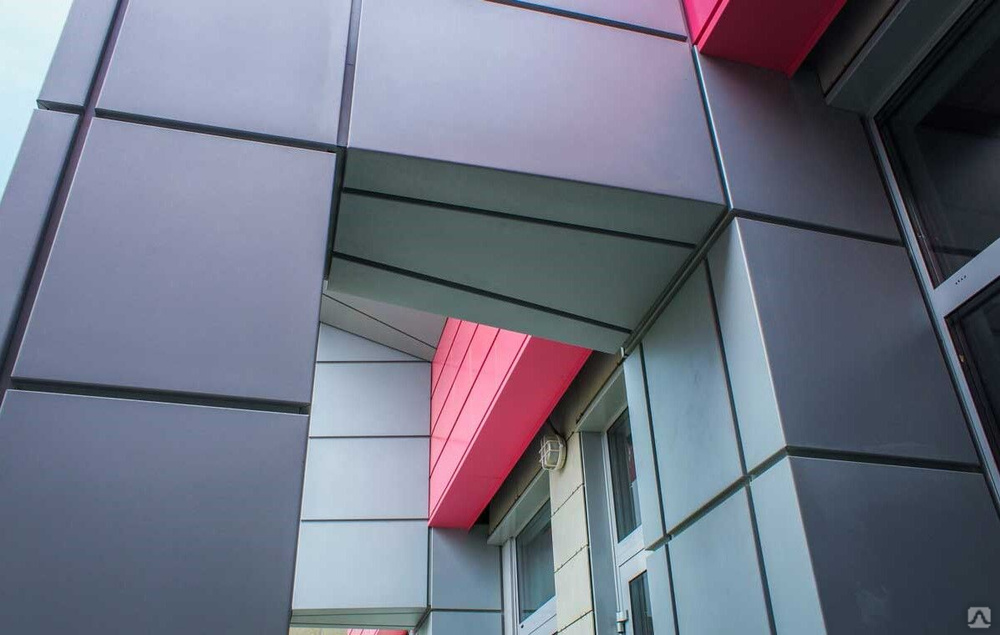
Тонкая стеклянная композитная панель
Композитная панель (рис. 1) состоит из двух покровных слоев тонкого стекла, которые заключают в себе полимерное ядро, изготовленное аддитивным способом. Оба компонента соединены клеем. Целью данной конструкции является максимально эффективное распределение нагрузок по всему сечению. Изгибающие моменты создают нормальные напряжения в покровных слоях. Поперечные усилия приводят к касательным напряжениям в сердечнике и в клеевом соединении.
Рендеринг композитной панели с тонким стеклом в качестве покровного слоя, клеевым соединением и аддитивной структурой сердцевины
Изображение полного размера
Покровный слой
Внешний слой многослойной конструкции состоит из тонкого стекла. В принципе, будет использоваться известково-натриевое силикатное стекло. Из-за целевой толщины < 2 мм процессы термического отпуска достигают своих текущих технических пределов. Если из-за конструкции (например, холодногнутые изогнутые панели) или использования требуется более высокая прочность, химически упрочненное алюмосиликатное стекло можно рассматривать как особенно подходящее [12]. Функция светопропускания и защиты от воздействий окружающей среды будет дополнена благоприятными механическими свойствами, такими как хорошая стойкость к царапинам и относительно высокий модуль Юнга по сравнению с другими материалами, используемыми в композите. Поскольку доступные размеры химически закаленного тонкого стекла ограничены, для изготовления первого крупноформатного прототипа здесь используются полностью закаленные листы известково-натриевого силикатного стекла толщиной 3 мм.
Основа
Основа считается формообразующей частью композитной панели. Почти все свойства могут быть затронуты им. Он также находится в центре внимания процесса цифрового производства из-за его аддитивного метода производства. Термопласты обрабатываются методом наплавления. Это дает возможность использовать большое количество различных полимеров для конкретных применений. Топология основного элемента может быть разработана в соответствии с его функцией с помощью различных основных направлений. Для этой цели поиск формы можно разделить на следующие четыре категории дизайна: структурный дизайн, функциональный дизайн, эстетический дизайн и производственный дизайн. Каждая из этих категорий может иметь разные цели, что может привести к разным топологиям.
В ходе предварительных исследований некоторые основные конструкции уже были проверены на пригодность их структурного дизайна [11]. Тройная периодическая минимальная поверхность структуры ядра Gyroid оказалась особенно эффективной с механической точки зрения. Это позволило достичь высокой механической устойчивости к изгибу при сравнительно небольшом использовании материала. В дополнение к этим базовым структурам, подобным ячейкам, которые дублируются по площади поверхности, топология также может быть сгенерирована другими методами нахождения формы. Генерация линии напряжения — это возможный подход к оптимизации жесткости при максимально возможном снижении веса [13]. Тем не менее, структура сотового заполнителя, которая широко используется для многослойных конструкций, используется в качестве отправной точки для разработки производственной линии. Эта базовая форма обеспечивает быстрый прогресс в производстве, особенно благодаря простому программированию траектории движения инструмента. Его свойства в композитных панелях были тщательно исследованы [14, 15, 16], и внешний вид можно изменить различными способами с помощью параметризации, а также можно использовать для первоначальных концепций оптимизации.
При выборе полимера можно учитывать широкий спектр термопластичных полимеров с используемым процессом экструзии. Первоначальные предварительные исследования малоформатных материалов уже сократили количество полимеров, которые считаются подходящими для использования в фасаде [11]. Поликарбонат (ПК) перспективен из-за его термо- и УФ-стойкости, а также высокой жесткости. Из-за дополнительных технических и финансовых затрат, связанных с переработкой поликарбоната, для производства первых прототипов используется полиэтилентерефталат, модифицированный гликолем (PETG). Это особенно просто для обработки при относительно низких температурах и снижает риск термических напряжений и деформации компонента. Представленные здесь прототипы изготовлены из переработанного PETG, называемого PIPG. Материал перерабатывают в виде гранул с содержанием стекловолокна 20% после предварительной сушки при 60°С в течение не менее 4 ч [17].
Клей
Клей обеспечивает прочную связь между структурой полимерного ядра и тонким покровным слоем стекла. Когда композитная панель подвергается изгибающим нагрузкам, клеевое соединение испытывает напряжение сдвига. Следовательно, более жесткие клеи предпочтительнее, и прогибы могут быть уменьшены. В сочетании со стеклом из прозрачного материала прозрачные клеи также подходят для обеспечения высокого визуального качества. Еще одним важным фактором при выборе клея является технологичность и интеграция в автоматизированный производственный процесс. Здесь клеи УФ-отверждения с гибким временем отверждения могут значительно упростить позиционирование покровных слоев. На основе предварительных испытаний уже был протестирован ряд клеев на предмет их пригодности для тонких стеклокомпозитных панелей [18]. УФ-отверждаемый акрилат Loctite® AA 3345™ [19] оказался особенно подходящим и используется в следующем процессе.
Процесс изготовления прототипа
Чтобы воспользоваться преимуществами аддитивного производства и гибкости тонкого стекла, весь процесс должен функционировать в цифровом и параметрическом режиме. Grasshopper используется как визуальный интерфейс программирования, чтобы избежать интерфейсов между различными программами. Все дисциплины (проектирование, проектирование и производство) будут поддерживать и дополнять друг друга в одном файле и обеспечивать прямую обратную связь с оператором. На данном этапе исследования рабочий процесс все еще находится в разработке и следует схеме, изображенной на рис. 2. Различные цели можно обобщить внутри дисциплин в виде категорий. В то время как ориентированный на пользователя дизайн и автоматизация подготовки производства уже используются для производства сэндвич-панелей в этой статье, интеграция и проверка отдельных инженерных инструментов еще не полностью реализованы. Начиная с параметрического проектирования геометрии фасада, внешняя оболочка здания может быть спроектирована на макроуровне (фасад) и мезо (фасадная панель). На втором этапе инженерная петля обратной связи предназначена для оценки безопасности и удобства обслуживания, а также возможности изготовления фасада. Наконец, полученные панели готовятся к цифровому производству. Программа обрабатывает разработанные основные структуры в машиночитаемом G-коде и подготавливает аддитивное производство, субтрактивную постобработку и клеевое соединение со стеклом.
Обзор целей оптимизации, разделенных на 4 категории в 3 дисциплинах
Изображение в натуральную величину
Проектирование (САПР)
Процесс проектирования рассматривается на двух разных уровнях. В дополнение к макроскопической форме фасада, которая влияет на геометрию каждой композитной панели, сама топология ядра также может быть спроектирована на мезоуровне. С помощью параметрической модели фасада на форму и внешний вид можно влиять с помощью ползунков, показанных на рис. 3, с использованием примерного участка фасада. Таким образом, общая поверхность состоит из определяемой пользователем масштабируемой поверхности, которую можно деформировать с помощью точечного аттрактора и изменить, указав минимальную и максимальную степень деформации. Это обеспечивает высокую степень гибкости при проектировании ограждающих конструкций. Однако эта свобода ограничена техническими и производственными ограничениями, которые вступают в силу через алгоритмы в инженерной части позже.
Параметрическая модель секции фасада и ее возможная параметризация на макро- и мезоуровне
Изображение в натуральную величину также определено. Что касается отдельных фасадных панелей, то их можно точнее определить на мезоуровне. Можно влиять на топологию самой структуры ядра, а также на толщину стекла. Обе эти переменные вместе с размерами панели имеют важное значение для механического моделирования в инженерной части. Весь дизайн и инжиниринг на макро- и мезоуровне могут быть выполнены с перспективой оптимизации в четырех категориях: структурный, функциональный, эстетический и производственный дизайн. Пользователь может разработать общий вид, а также характеристики оболочки здания, определив приоритеты в этих областях.
Engineering (CAE)
Проект поддерживается инженерной частью с помощью контура обратной связи. Для этой цели целевые и граничные условия определяются в категориях оптимизации, показанных на рис. 2. Они обеспечивают коридор того, что технически возможно, обосновано с точки зрения строительной физики и безопасно с инженерной точки зрения, что оказывает значительное влияние на проектирование. . Это отправная точка для широкого спектра инструментов, которые можно интегрировать непосредственно в Grasshopper. При дальнейших исследованиях механические свойства можно оценить с помощью анализа конечных элементов (FEA) или даже аналитических расчетов. Кроме того, исследования солнечного излучения, анализ линии обзора, моделирование часов солнечного света могут оценить влияние композитной панели на физику здания. Важно не слишком ограничивать скорость, эффективность и гибкость процесса проектирования. Таким образом, полученные здесь результаты разработаны в качестве дополнительной ориентации и поддержки процесса проектирования и не заменяют детальный анализ и проверку в конце процесса проектирования. Этот стратегический план формирует основу для дальнейших исследований в отдельных категориях для получения подтвержденных результатов. Например, пока мало что известно о механическом поведении композитной панели при различных условиях нагрузки и поддержки.
Производство (CAM)
После завершения проектирования и проектирования модель подготавливается для цифрового производства. Производственный процесс разделен на четыре подэтапа (рис. 4). Во-первых, основная структура изготавливается аддитивно с помощью крупномасштабной роботизированной установки для 3D-печати. Затем поверхность фрезеруется с помощью той же роботизированной системы для улучшения качества поверхности, необходимого для качественного склеивания. После фрезерования клей наносится вдоль структуры сердцевины с помощью специально разработанной системы дозирования, установленной на той же роботизированной системе, которая используется для процессов печати и фрезерования. Наконец, стекло позиционируется и кладется вниз до того, как клеевой шов будет отвержден УФ-светом.
Подэтапы роботизированного процесса производства тонкой стеклянной композитной панели слева направо: аддитивное производство, подготовка поверхности, нанесение клея и сборка со стеклом
Изображение в полный размер
Аддитивное производство сердцевины
Для аддитивного производства определенная топология базовой структуры должна быть переведена на язык машин с числовым программным управлением (GCode). Для однородных и высококачественных результатов цель состоит в том, чтобы каждый слой можно было печатать без отрыва сопла экструдера. Это предотвращает нежелательное чрезмерное выдавливание в начальной и конечной точках перемещения. Поэтому сценарий непрерывной генерации траектории написан для используемого сотового шаблона. Это создает параметрическую непрерывную полилинию с одинаковой начальной и конечной точкой, которая адаптируется к выбранному размеру панели, количеству и размеру сотовых ячеек в соответствии с проектом.
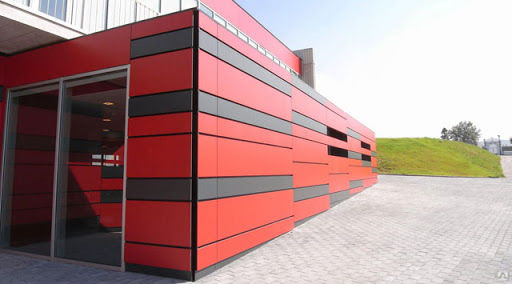
Крупномасштабное аддитивное производство роботом сотового шаблона с однолинейной траекторией
Изображение в полный размер
Фрезерование сердцевины
Предварительные тесты уже показали разницу в силе сцепления между клеем и напечатанным на 3D-принтере полимером в зависимости от свойств его поверхности. С этой целью образцы для испытаний, изготовленные методом аддитивного производства, были склеены клеем или приклеены к стеклу и нагружены растяжением или сдвигом. Значительное увеличение прочности обнаружено при механической предварительной обработке поверхности полимера фрезерованием (рис. 6). Кроме того, он улучшает планарность сердцевины и предотвращает дефекты, вызванные чрезмерной экструзией. УФ-отверждаемый акрилат LOCTITE® AA 3345™ [19], используемые здесь, оказались чувствительными к условиям обработки. Это обычно приводит к более высоким стандартным отклонениям для образцов, склеенных клеем. После аддитивного производства основная структура фрезеруется на копировальном станке. Необходимый для этого G-код генерируется автоматически в соответствии с траекторией движения инструмента, уже созданной для процесса 3D-печати. Необходимо напечатать структуру сердцевины немного выше предполагаемой высоты сердцевины. В этом примере структура сердцевины толщиной 18 мм была уменьшена до 14 мм.
Механическая адгезионная прочность многослойных и склеенных образцов полимерного стекла при растягивающих и сдвигающих нагрузках
Изображение в натуральную величину
Нанесение клея
Эта часть производственного процесса представляет серьезную проблему для полной автоматизации . Нанесение клея требует высокой степени точности и прецизионности машины. Пневматическая система дозирования используется для нанесения клея вдоль структуры сердцевины. Робот ведет его по фрезерованной поверхности в соответствии с уже определенной траекторией движения инструмента. Вместо обычных наконечников-дозаторов особенно удобным оказалось нанесение с помощью наконечника-щетки. Это приводит к равномерному дозированию объема для клеев с низкой вязкостью. Количество определяется давлением в системе, а также скоростью робота. Для более высокой точности и качественного клеевого соединения предпочтительны низкие скорости перемещения от 200 до 800 мм/мин. При приложенном давлении от 0,3 до 0,6 мбар используемый акрилат со средней вязкостью 1500 мПа*с наносили на полимерную сердцевину-стенку шириной 6 мм с помощью дозирующей щетки с внутренним диаметром 0,84 мм и шириной кисти 5 мм. Затем клей распределяется по поверхности подложки и образует покрытие толщиной 1 мм за счет поверхностного натяжения. Точное определение толщины клея еще не могло быть реализовано автоматически. Продолжительность процесса является важным критерием выбора клея. Изготовленная здесь структура сердечника имеет длину дорожки 26 м, в результате чего время нанесения составляет от 30 до 60 минут.
Сборка и отверждение
После нанесения клея стекло устанавливается на место. Поскольку тонкое стекло уже сильно деформируется под собственным весом из-за малой толщины материала, при установке стекло следует держать как можно более плоским. Для этого используется пневматическая стеклянная присоска с точечно расположенными присосками. Он размещается над компонентом с помощью крана, а в будущем, возможно, и непосредственно с помощью робота. Стеклопакет укладывается параллельно поверхности каркаса на клейкий слой. Давление на него из-за небольшого веса увеличивается за счет еще одного стекла (толщиной от 4 до 6 мм). В результате должно получиться полное увлажнение поверхности стекла по структуре сердцевины, о чем можно судить при первоначальном визуальном осмотре по четким цветовым различиям. Процесс нанесения также может оказывать существенное влияние на качество получаемого клеевого соединения. После нанесения стекло нельзя перемещать, так как это приведет к видимым остаткам клея на стекле и несовершенствам фактического слоя клея. Клей окончательно отверждается УФ-излучением с длиной волны 365 нм. Для этого использовалась УФ-лампа с плотностью мощности 6 мВт/см 2 проводится поэтапно по всей клейкой поверхности в течение 60 с.
Механические испытания
Исследуемая здесь концепция легкой и индивидуализируемой тонкой стеклокомпозитной панели с аддитивно изготовленным полимерным сердечником предназначена для использования в будущих фасадах. Следовательно, композитная панель должна соответствовать применимым стандартам и удовлетворять требованиям по предельным состояниям эксплуатационной пригодности (SLS), предельным состояниям по предельной прочности (ULS) и требованиям безопасности. Таким образом, композитная панель должна быть достаточно безопасной, прочной и жесткой, чтобы выдерживать нагрузки (например, поверхностные нагрузки) без разрушения или слишком больших деформаций. Чтобы исследовать механическую реакцию ранее изготовленной тонкой стеклянной композитной панели, представленной в разделе «Механические испытания», она была подвергнута испытанию на ветровую нагрузку, как описано в следующих подразделах.
Установка для физических испытаний
Целью физических испытаний является исследование механических свойств композитной фасадной панели под действием ветровой нагрузки. Для этой цели с помощью клея Loctite AA 3345 от Henkel по вышеописанному методу изготавливается композитная панель, состоящая из внешних листов полностью закаленного стекла толщиной 3 мм и аддитивно изготовленной сердцевинной структуры толщиной 14 мм из PIPG-GF20 (рис. 7 слева). ). Затем композитная панель крепится к деревянной опорной раме с помощью металлических винтов, которые ввинчиваются через деревянную раму в боковую часть несущей конструкции. 30 винтов размещаются по периметру панели (см. черные линии на рис. 7 слева) и предназначены для максимально точного воспроизведения условий линейной поддержки по периметру. Затем тестовая рама герметично устанавливается в тестовую стену фасада, которая создает давление ветра или всасывание ветра за композитной панелью (рис. 7, вверху справа). Для записи данных используется цифровая корреляционная система (DIC). С этой целью внешнее стекло композитной панели покрыто тонким и эластичным листом, на который нанесен узор Perlin Noise (рис. 7, внизу справа).
DIC регистрирует относительное положение всех точек измерения по всей поверхности стекла с помощью двух камер. Два изображения в секунду записываются и используются для оценки. Давление в камере, окруженной композитной панелью, увеличивается с помощью вентилятора с шагом 1000 Па до максимального значения 4000 Па, при этом каждый уровень нагрузки поддерживается в течение 10 с.
Технический чертеж испытательной установки (слева), испытательный образец в установленном состоянии (вверху справа) и с измерительной фольгой ДИК (внизу справа)
Изображение в натуральную величину
Численное моделирование
Постановка эксперимента также представлена численной моделью с теми же геометрическими размерами. Для этого используется числовая программа Ansys Mechanical. Геометрия представляет собой сетку с использованием шестигранных элементов SOLID 185 с длиной ребра 20 мм для оконных стекол и четырехгранных элементов SOLID 187 с длиной ребра 3 мм для основной структуры. Для упрощения моделирования на данном этапе исследования используемый акрилат считается идеализированным жестким и тонким и определяется как жесткое соединение между стеклом и сердцевиной. Композитная панель закреплена по линии вокруг внешней части сердцевины, а одно стекло нагружено поверхностной нагрузкой давлением 4000 Па. Хотя при моделировании учитываются геометрические нелинейности, на данном этапе исследования использовались только линейные модели материалов. Хотя это справедливое предположение для линейно-упругого отклика стекла (с E = 70 000 МПа), принятая линейная жесткость E = 8245 МПа согласно техническому описанию производителя [17] (вязкоупругого) полимерного материала сердцевины должны быть критически рассмотрены в текущем анализе и будут изучены в будущих исследованиях. 9{2}}\справа)\). Для этого изображение, зарегистрированное ДИК, сравнивается с результатами численного моделирования (МКЭ) (рис. 8, внизу справа). В то время как идеализированная общая деформация 0 мм с «идеально» линейной опорой в краевой области (т.
е. по периметру панели) рассчитывается в FEA, физическое смещение краевой области должно учитываться при оценке DIC. . Это происходит из-за допусков при монтаже, а также из-за деформации испытательной рамы и ее уплотнения. Для сравнения среднее смещение краевой области (белая пунктирная линия на рис. 8) вычитается из максимального смещения в центре панели. Смещения, определенные методом DIC и FEA, сравниваются в таблице 1 и отображаются в виде графиков в левом верхнем углу рис. 8.
Экспериментальные и численные результаты испытаний на ветровую нагрузку при давлении ветра 4000 Па
Изображение полного размера экспериментальная модель используется в качестве ориентира для оценки, а также оценивается в МКЭ. Максимальное центральное смещение на ненагруженной композитной панели было определено измерениями DIC на уровне 2,18 мм при уровне нагрузки 4 000 Па. В то время как смещение МКЭ при более низких нагрузках (до 2 000 Па) все еще может достаточно точно воспроизводить экспериментальные значения. точно, нелинейный рост деформации при более высоких нагрузках рассчитан неточно.
Однако исследование уже показывает, что композитная панель способна выдерживать экстремальные ветровые нагрузки. Особо следует отметить высокую жесткость легкой панели. При аналитическом расчете, основанном на линейной теории пластин по Кирхгофу [20], деформация 2,18 мм при 4000 Па соответствует деформации монолитного 12-мм оконного стекла при тех же граничных условиях. Таким образом, толщина стекла (энергоемкого) в этой композитной панели может быть уменьшена до стекла 2 × 3 мм, что приводит к экономии материала на 50%. Это уменьшение общего веса панели приводит к дополнительным преимуществам при сборке. В то время как с композитной панелью весом 30 кг могут легко справиться два человека, для безопасной работы с обычным 50-килограммовым стеклом требуется техническая поддержка. Для точного представления механического поведения в будущих исследованиях необходима более подробная численная модель. FEA может быть дополнительно улучшен за счет более обширных нелинейных моделей материала полимера и моделирования клеевого соединения.
Резюме
Развитие и совершенствование цифровых процессов играет ключевую роль в строительной отрасли для улучшения как экономических, так и экологических показателей. Кроме того, использование тонкого стекла в фасадах обещает потенциальную экономию энергии и ресурсов и открывает новые возможности в архитектуре. Однако из-за малой толщины стекла необходимы новые конструктивные решения для достаточной жесткости стекла. Таким образом, исследование, представленное в этой статье, посвящено концепции композитной панели, изготовленной из тонкого стекла и приклеенной полимерной сердцевины с жесткостью, напечатанной на 3D-принтере. Весь производственный процесс, от проектирования до производства, был оцифрован и автоматизирован. С помощью Grasshopper был разработан рабочий процесс от файла до фабрики, позволяющий использовать тонкие стеклянные композитные панели в будущих фасадах. Производство первого прототипа уже показало осуществимость и проблемы роботизированного производства. В то время как аддитивное и субтрактивное производство уже могут быть очень хорошо интегрированы, особенно полностью автоматизированное нанесение и сборка клея представляет собой еще больше проблем, которые необходимо решить в будущих исследованиях. С помощью предварительных механических испытаний и связанного с ними экспериментального конечно-элементного моделирования показано, что легкая тонкая стеклокомпозитная панель обеспечивает достаточную жесткость на изгиб для предполагаемого применения в фасадах даже в условиях экстремальной ветровой нагрузки. Текущие исследования авторов будут способствовать дальнейшему изучению потенциала и демонстрации производительности тонких стеклянных композитных панелей, изготовленных цифровым способом, для фасадных применений.
Архив алюминиевых композитных панелей – Фасады+, Премьер-конференция по высокоэффективным ограждениям зданий.
Метка: Алюминиевые композитные панели
Темное шале Tom Wiscombe Architecture возвышается над Паудер-Маунтин из алюминиевого композита «черное на черном».

Пирс 4 компании Elkus Manfredi Architects соединяется с морским портом Бостона волнообразным массивом
Район морского порта Бостона не новичок в развитии; Участок площадью 23 акра находится к востоку от канала Форт-Пойнт во Внутренней гавани и за последние два десятилетия превратился из практически бесплодной деиндустриализованной набережной в эффективное продолжение центра города. Пирс 4, многофункциональный проект площадью 400 000 квадратных футов, разработанный местной фирмой Elkus Manfredi
.Штаб-квартира RAMSA American Water поставляет детализированный алюминий на набережную Камдена
Штаб-квартира American Water, открытая в декабре 2018 года, является самым последним важным дополнением к набережной реки Камден, штат Нью-Джерси, Делавэр, и находится прямо напротив центра Филадельфии. Разработан Робертом А.М. из Нью-Йорка. Корпоративный проект Stern Architects (RAMSA) отражает прежний индустриальный характер пояса ржавчины с фасадом из алюминиевого композита
ARO компании CetraRuddy представляет собой волнистую форму в Мидтауне с композитным алюминием и стеклом
Нью-йоркская архитектурная компания CetraRuddy не новичок в проектировании жилых небоскребов на Манхэттене, причем комплекс работ отличается от типичных современных стеклянных сталагмитов благодаря включению значительных участков камня. и металл. ARO, стройная 62-этажная башня, расположенная в Западном Мидтауне, завершенная в этом году, продолжает эту тенденцию с фасадом в
Израильский аэропорт поднимается из пустыни с искривленным алюминиевым фасадом
В израильской пустыне Негев в пелене Эйлатских гор поднялась граненая масса. Международный аэропорт Рамон, спроектированный Amir Mann / Ami Shinar Architects and Planners и Moshe Zur Architects, облицован большими алюминиевыми композитными панелями.