Пенополистирол и экструдированный пенополистирол. |
Прежде чем обсуждать характеристики, достоинства и недостатки пенополиситрола, следует внести ясность в терминологию.
Начнем с пенопласта. Что такое пенопласт? Обычно пенопластом мы называем легкий белый материал, состоящий из прессованных маленьких шариков. В общем, это правильно, но не совсем. Если быть точным, то пенопласт – это группа материалов получаемых путем вспенивания пластмасс. «Вспенивать» можно разные виды пластмасс, поэтому существует много разных видов пенопластов: полистирольный пенопласт, полиуретановый пенопласт, поливинилхлоридный пенопласт, фенол-формальдегидный и другие. Например, поролон – тоже пенопласт.
Общая технология производства пенопластов состоит из трех стадий: 1). Смешивание основных компонентов, 2). Газонаполнение, 3). Фиксация полученной структуры пенопласта. Именно газонаполнение является ключевым технологическим звеном, от которого зависят конечные свойства пенопласта. Если сказать в общем, то пенопласты отличаются исходным материалом и технологией газонаполнения (вспенивания), от этого и возникает большое их разнообразие.
Важных факторов определяющим качество пенопластов является соотношение числа открытых и закрытых ячеек в их структуре. От этого в большой степени зависят физико-механические свойства материала. Чем выше процент содержания закрытых ячеек, тем лучше свойства пенопласта.
Высоким процентом содержания замкнутых ячеек отличаются полистирольные и поливинилхлоридовые пенопласты, а также жесткие пенополиуретаны. Низкая теплопроводность и гигроскопичность этих пенопластов определили их широкое применение в строительстве, в качестве теплоизоляционных материалов. Самое широкое применение получили пенополистирол и экструдированный пенополистирол.
Пенополистирол (EPS).
С этим материалом мы часто встречаемся в быту, обычно в виде упаковки для бытовой техники. Поэтому под пенопластом обычно понимают именно пенополистирол. Как уже говорилось, пенополистирол получил широкое распространение в строительстве, в качестве утеплителя с широким спектром применения. Это произошло после того как удалось решить проблемы с горючестью пенополистирола.
Технология получения достаточно проста. Сначала смешивают компоненты, обычно на основе полистирола (иногда полимонохлорстирол или полидихлорстирол). Затем добавляют вспенивающие компоненты, легкокипящие углеводороды (пентан, изопентан, дихлорметан и др.) и добавки (антипирены, пластификаторы и красители). В результате получаются гранулы, в которых легкокипящая жидкость равномерно распределена в полистироле. Затем эти гранулы обрабатывают горячим воздухом или паром, при этом легкокипящие компоненты испаряются, и гранулы сильно увеличиваются в объеме (в 50 и более раз). При этом ячейки начинают твердеть и склеиваться между собой. В результате получается легкий, однородный, устойчивый к сжатию и сохраняющий исходные размеры изоляционный материал.
В момент, когда гранулы полистирола начинают расширяться и заполнять форму можно не ограничивать объем занимаемый пенопластом. В этом случае получается так называемый «беспрессовый» пенополистирол. Если процесс расширения будет происходить под внешним давлением (под прессом) то получается более плотный материал, называемый «прессовый» пенополистирол.
Внешне эти виды пенополистирола практически не отличаются. Но прессовый имеет большую плотность (от 40 до 250 кг / м3), меньшую гигроскопичность и лучшие физико-механические свойства. По теплопроводности они примерно одинаковые. Технология производства прессового пенополистирола сложнее, поэтому он дороже и его применяют, как правило, там, где требуется повышенная влагостойкость и механическая прочность – утепление фундаментов и подземных коммуникаций. Марки отечественных прессовых пенопластов обозначаются аббревиатурой ПС, например, ПС-1, ПС-4.
Беспрессовые пенополистиролы получили в строительстве наибольшее распространение в качестве утеплителей из-за хорошего соотношения характеристик и цены. Более того, они очень хорошо подходят для производства сэндвич панелей. Беспрессовые пенополистиролы имеют обозначение ПСБ. При добавлении в состав пенопласта антипиренов, получается самозатухающий пенопласт марки ПСБ-С с классом горючести Г1. Этот материал устойчив к воздействию влаги и старению, он биологически безопасен и не подвержен воздействию вредных микроорганизмов. Именно эти пенопласты применяются в строительстве.
Марки, применение и характеристики пенополистиролов.
Пенопласты марки ПСБ-С-15 имеют самую маленькую плотность. Их применяют для звуковой и теплоизоляции конструкций, которые подвергаются минимальным механическим нагрузкам. Например, бытовки, контейнеры, внутренние перегородки и т.п.
Пенопласт марки ПСБ-С-25 применяется для утепления фасадов зданий, стен, лоджий и полов небольшой нагрузки. В качестве утеплителя его используют для производства сэндвич панелей. У этой марки очень хорошее соотношение характеристик и цены.
Пенопласт марки ПСБ-С-35 имеет большую механическую прочность и менее гигроскопичен. Поэтому используется для утепления фундаментов, подземных коммуникаций, для предотвращения промерзания и вспучивания грунтов, подходит для строительства спортивных площадок и бассейнов.
Пенопласт марки ПСБ-С-50 имеет высокую механическую прочность и может выдерживать большие нагрузки. Его используют для теплоизоляции полов в промышленных зданиях, гаражах, стоянках. Он применяется для строительства дорог на заболоченной местности, для предотвращения промерзания и вспучивания грунтов.
Характеристики пенополистиролов, определены ГОСТом 15588-86.
Характеристика | ПСБ-С-15 | ПСБ-С-25 | ПСБ-С-35 | ПСБ-С-50 |
Плотность, кг/м3 | до 15 | 15,1…25,0 | 25,1…35,0 | 35,1…50,0 |
Прочность на сжатие при 10 % линейной деформации, МПа, не менее | 0,05 | 0,1 | 0,16 | 0,2 |
Предел прочности при изгибе, МПа, не менее | 0,07 | 0,18 | 0,25 | 0,35 |
Теплопроводность в сухом состоянии при (25±5)°С, Вт/(м·К), не более | 0,042 | 0,039 | 0,037 | 0,04 |
Время самостоятельного горения плит типа ПСБ-С, с, не более | 4 | 4 | 4 | 4 |
Водопоглощение за 24 ч, % по объему, не более | 3 | 2 | 2 | 1,8 |
Паропроницаемость не менее мг(м.![]() | 0,05 | 0,05 | 0,05 | 0,05 |
Удельная теплоёмкость, кДж/(кг °С) | 1,34 | 1,34 | 1,34 | 1,34 |
Экструдированный (экструзионный) пенополистирол (XPS).
Экструдированный пенополистирол производится из тех же составляющих, что и обычный полистирол, но есть отличие в технологии изготовления. Обычный пенопласт создается путем прогревания гранул водяным паром, при этом гранулы увеличиваются в размере и занимают весь объем формы. Экструзионный пенополистирол производится методом экструзии. Вспененную массу нагревают и выдавливают через фильеры. В результате получается пенопласт с закрытопористыми ячейками диаметром 0,1 – 0,2 мм и плотностью 25 … 45 кг / м3.
Благодаря своей структуре экструдированный пенополистирол обладает очень хорошими характеристиками, что отличает его от других пенопластовых утеплителей.
Материал отличается очень низкой теплопроводностью (0,029-0,034 Вт/(м·К)) и водопоглащением (0,2-0,4%). Практически не изменяет теплопроводности во влажных условиях, поэтому его можно использовать без дополнительной гидроизоляции. Устойчив к промерзанию и выдерживает много циклов замораживания-оттаивания без заметного изменения теплоизолирующих свойств. Он обладает хорошей химической стойкостью по отношению к большинству строительных материалов, кроме органических растворителей, бензина и кислот. Кроме того он обладает высокой механической прочностью.
Это очень хороший теплоизоляционный материал и может применяться практически везде. Но есть и недостатки. Разрушается при контакте со сложными углеводородами, например, поливинилхлоридом, который используется для изготовления сайдинга. Горюч, относится к классу горючести Г3 — Г4. Разрушается под действием ультрафиолетовых лучей, поэтому его нельзя использовать в открытом виде. Не рекомендуется использовать для утепления крыш и утепления бань и саун, так как при нагревании более 75 оС разрушается. К минусам можно отнести и достаточно высокую цену по сравнению с обычным пенополистиролом.
Характеристики экструдированных пенополистиролов.
Характеристика | XPS 25 | XPS 30 | XPS 35 | XPS 45 |
Плотность, кг/м3 | 24…25 | 25,1…30,0 | 30,1…35,0,0 | 35,1…45,0 |
Прочность на сжатие при 10 % линейной деформации, МПа, не менее | 0,20 | 0,25 | 0,30 | 0,50 |
Предел прочности при изгибе, МПа, не менее | 0,30 | 0,30 | 0,40 | 0,35 |
Теплопроводность в сухом состоянии при (25±5)°С, Вт/(м·К), не более | 0,029 | 0,029 | 0,028 | 0,031 |
Группа горючести | Г4 | Г4 | Г3 | Г4 |
Водопоглощение за 24 ч, % по объему, не более | 0,2 | 0,2 | 0,2 | 0,2 |
Паропроницаемость не менее мг(м.ч.Па) | 0,011 | 0,011 | 0,011 | 0,011 |
Удельная теплоёмкость, кДж/(кг °С) | 1,45 | 1,45 | 1,45 | 1,5 |
Пеноизол- новый шаг карбидных пенопластов
Все большее внимание специалистов и строителей привлекают карбамидные пенопласты, применение которых открывает широкие возможности для значительного снижения стоимости работ по теплоизоляции зданий и сооружений различного назначения. Такие пенопласты уже применялись у нас в стране и за рубежом под различными товарными названиями: в Англии — флотофаум, Японии — ипорка, Германии — аминотерм, Чехии — мофотерм, Швейцарии — изошаум, Дании — инсульспрей, Франции — изолеж, Канаде — инсулспрей, в Советском Союзе — мипора.
За последнее 10-летие учеными и специалистами ЗАО «НТЦ МЕТТЭМ» создано новое поколение карбамидного пенопласта «МЕТТЭМПЛАСТ»
ЗАО «НТЦ МЕТТЭМ» работает на рынке теплоизоляционных материалов уже 15 лет. За эти годы отработана технология изготовления пенопласта, создан целый ряд технологического оборудования (установки ГЖУ-1 и ГЖУ-Н1, производственные линии ПЛ-10 и ПЛ-30), а также, что самое главное, специально для пенопласта (!) разработана новая полимерная смола холодного отверждения, выпускаемая под марками «ВПС-Г»® и «КАРБАМЕТ-Т» ®.
В связи с ростом применения «МЕТТЭМПЛАСТ»® (далее по тексту — «пенопласт», но не путать с полистирольным) у потребителя появляется множество вопросов, касающихся эксплуатационных качеств теплоизоляционного материала.
Основными показателями, характеризующими теплоизоляционные материалы — пенопласты, являются коэффициент теплопроводности, кажущаяся плотность, коэффициент паропроница-емости, водопоглощение, температура эксплуатации, горючесть.
Применение пенопласта в жилищном и промышленном строительстве определяется:
- во-первых, его способностью выполнять теплоизоляционные функции в течение длительного срока эксплуатации. Согласно заключению НИИСФ «время надежной работы пенопласта в качестве ненесущего среднего слоя трехслойных конструкций зданий и сооружений при любых условиях эксплуатации исследованного диапазона неограниченно»
- во-вторых, его лучшими пожаробезопасными свойствами по сравнению с другими полимерными материалами (например, время горения составляет ноль секунд;
- в-третьих, его самой низкой стоимостью по сравнению со всеми существующими теплоизоляционными материалами.
По параметру «цена — качество» это самый оптимальный утеплитель.
1. Физико-механические свойства
1.1. Коэффициент теплопроводности.
В зависимости от эксплуатационных требований пенопласт может быть получен с различной кажущейся плотностью от 5 до 25 кг/м3. Наиболее широкое распространение получил блочный пенопласт марки М-20, имеющий среднюю плотность 18 кг/м3. С повышением кажущейся плотности количество закрытых пор увеличивается. Заливочный пенопласт через одни сутки после изготовления обладает повышенной влажностью, которая достигает 300% (по массе). Несмотря на высокую начальную технологическую влажность пенопласта, через 3–5 суток при наружной температуре плюс 20ВВВВВ°С материал становится практически сухим и кажущаяся плотность совпадает с заданной. При переходе пенопласта из абсолютно сухого состояния к эксплуатационному (при? — 80%) кажущаяся плотность пенопласта увеличивается (ЛенЗНИИЭП. «Исследование свойств карбамидных пенопластов и их применение в строительстве»).
На основании проведенных исследований (Временные указания по применению быстротвердеющей пены как теплоизоляции в суровых климатических условиях. Л., «Энергия»; И. С. Камеррер.«Теплоизоляция в промышленности и строительстве». М., «Стройиздат»; И. Г. Романенко. «Физико-механические свойства пенистых пластмасс». М., «Стройиздат»; Справочник по производству теплоизоляционных и акустических материалов (под редакцией В. А. Китайцева). М., «Стройиздат») можно сделать вывод о незначительном влиянии температуры на коэффициент теплопроводности карбамидных пенопластов по сравнению с изменениями кажущейся плотности. Обобщение данных исследований позволяет установить корреляционную связь между коэффициентом теплопроводности и температурой в интервале от О°С до плюс 80°С и от О°С до минус 100°С. Увеличение температуры от О°С до плюс 80°С приводит к увеличению коэффициента теплопроводности до 70%, а в интервале температур от 0 до минус 100°С изменение находится в пределах 40%.
1.2. Теплоемкость — свойство материала поглощать тепло при повышении температуры. Удельная теплоемкость карбамидных пенопластов определяется твердой фазой материала, поэтому остается величиной постоянной независимо от кажущейся плотности пенопласта и при температуре 20°С составляет 1,39 Дж/(кг? °С).
1.3. Коэффициент паропроницаемости зависит от физических свойств пенопласта и определяет эксплуатационные качества строительных ограждающих конструкций.
2. Механические характеристики
Прочность теплоизоляционных материалов является важным показателем, обеспечиваю-щим транспортабельность изделий и сохранность их на строительной площадке. Все карбамидные пенопласты имеют незначительную механическую прочность, которая зависит от кажущейся плотности и колеблется в пределах 0,01…0,05 МПа. С целью оптимизации плотности, транспортабельности, коэффициента теплопроводности, сохранности и цены строительные предприятия России применяют пенопласт средней плотностью 18 кг/м3 или менее плотный, но в упаковке. Известны способы, увеличивающие плотность пенопластов, но одновременно ухудшаются их теплоизоляционные свойства за счет увеличения кажущейся плотности. Так, при увеличении кажущейся плотности до 90 кг/м3 возрастает прочность пенопластов до 0,15 МПа, но при этом стоимость его увеличивается в 5–7 раз.
Все карбамидные пенопласты обладают значительной усадкой в период отверждения, что учитывается в технологическом процессе. На величину усадки влияют температура и время сушки. Как у отечественных, так и у зарубежных заливочных пенопластов усадка составляет 1,8…6,0% (М.Кухарж. «Мофотерм — пенообразный теплоизоляционный материал»). Техноло-гическая усадка в производственных условиях заканчивается через 3…7 суток и при попадании блоков пенопласта на строительную площадку дальнейшая усадка материала не происходит.
3. Адгезионные свойства
Заливочные карбамидные пенопласты имеют удовлетворительную адгезию к материалам с шероховатой поверхностью, как, например, к гидроизоляционным рулонным материалам, необработанной поверхности бетона, армоцемента. К материалам с гладкой поверхностью, как, например, к слоистому пластику, стеклу, металлу, адгезия не наблюдается.
Блочный пенопласт, наиболее часто применяемый для теплоизоляции зданий, соединяется с другими материалами с помощью различных клеев. При правильном подборе клеевого состава прочность шва выше прочности пенопласта. Поверхность отрыва всегда проходит по пенопласту. Температуры в диапазоне от минус 10°С до плюс 50°С существенно не влияют на прочность и отрыв заливочных и блочных карбамидных пенопластов.
4. Морозостойкость
Карбамидные пенопласты относятся к морозостойким материалам. По этой причине они нашли широкое распространение в северных странах Западной Европы, в США под различными товарными названиями: в Англии — флотофаум, Японии — ипорка, Германии — аминотерм, Чехии — мофотерм, Швейцарии — изошаум, Дании — инсульспрей, Франции — изолеж, Канаде — инсулспрей. Отечественные пенопласты выдерживают более 50 циклов попеременного замораживания образцов с 80% влажностью при температуре минус 19С в течение 4-х часов и оттаивания на воздухе при температуре плюс 18С в течение 2-х часов. При попеременном замораживании и оттаивании в воде в течение 2-х часов при температуре плюс 15°С образцы выдерживают 25 циклов испытаний (ЛенЗНИИЭП. «Исследование свойств карбамидных пенопластов и их применение в строительстве», Временные указания по применению быстротвердеющей пены как теплоизоляции в суровых климатических условиях. Л., «Энергия»).
«МЕТТЭМПЛАСТ»® выдержал 1000 циклов (!) попеременного замораживания при температуре минус 30оС в течение 3-х часов и оттаивания на воздухе при температуре плюс 40оС в течение 3-х часов.
5. Вибростойкость и шумопоглощение
По данным Н. Баумана и др., образцы карбамидных пенопластов (аминотерм — торговое название блочного пенопласта в Германии) успешно выдерживают испытания вибрационной нагрузкой 180 кол./мин. в течение 120 часов. При этом масса образовавшейся пыли составляет 3%. В Московском ЦНИИ железнодорожного транспорта были проведены аналогичные испытания с пенопластом — заметных изменений в материале обнаружено не было.
На предприятии АО «Метровагонмаш» проведены вибрационные испытания образцов панелей обшивки автобуса с пенопластом (отчет No7716 от 25.07.97).
Ввиду отсутствия информации о вибронагруженности обшивки автобуса испытания проводились в соответствии с ГОСТ 16962.2–90 «Изделия электротехнические. Методы испытаний на стойкость к механическим внешним воздействующим факторам для изделий группы эксплуатации (передвижные наземные рельсовые установки, самоходные и несамоходные — в кузовах и под кузовами транспортных средств по ГОСТ 17516. 1–90)». Испытания проводились методом фиксированных частот (от 15 до 100 Гц), амплитудой 1,5 мм в течение 8…16 часов. Результаты испытаний: «Образцы панелей с приклеенным пенопластом вибрационные испытания выдержали в полном объеме без каких-либо разрушений».
Так, по данным Н. Баумана, звукопоглощение перфорированного изошаума (торговое название заливочного пенопласта в Швейцарии) с плотностью 10 кг/м3, толщиной 30 мм и с воздушной прослойкой 100 мм при частоте звука 400 Гц достигает 72%.
Испытания на шумопоглощение пенопласта проведены отделом акустики конструкторско-экспериментального производства АООТ «Автомобильный завод им. И. А. Лихачева». Частота испытаний — от 200 до 2400 Гц, толщина образцов пенопласта — 95 мм, 44 мм, 24 мм.
Вышеприведенные испытания показывают о широкой возможности использовать пенопласт в качестве шумопоглощающего материала в различных областях промышленности.
6. Горючесть
Карбамидный пенопласт применяется при температурах от минус 50°С до плюс 120°С. Из всех применяемых в строительстве пенопластов только пенопласт относится к группе горючести Г2 (широко применяемый полистирольный пенопласт относится к группе горючести Г4). Карбамидный пенопласт (единственный из полимерных материалов) имеет продолжительность горения ноль секунд (!), т. е. распространения пламени по длине не имеется. На открытом пламени материал лишь обугливается и выделяет небольшое количество СО и СО2 (как при горении древесины).
При этом необходимо отметить, что из 4-х параметров горючести 2 соответствуют показателям для группы горючести Г1. К ним относятся: параметр «продолжительность самостоятельного горения» — он составил ноль секунд при испытаниях в испытательных центрах (лабораториях) Москвы, С.-Петербурга и Омска и параметр «степень повреждения по длине» — от 42% до 57% при нормативе для группы горючести Г1 не более 65%. Параметр «степень повреждения по массе» находится при всех испытаниях от 22% до 36% при нормативе для группы горючести Г2 не более 50%.
Исходя из этих показателей можно сделать вывод, что если бы пенопласт был применен при строительстве сгоревшего здания УВД Самарской области, имевших место печальных последствий могло не быть, поэтому соответствующим организациям при реконструкции аналогичных зданий или при проведении противопожарных мероприятий на них можно с уверенностью использовать пенопласт.
7. Экология
Не для кого не секрет, что основной причиной сдерживания широкого внедрения карбамидного пенопласта (который был изобретен в Германии еще в тридцатых годах, а в Советском Союзе появился в пятидесятых годах прошлого века) было большое выделение свободного формальдегида как при изготовлении, так и в процессе эксплуатации. Основной причиной этого являлось то, что для его изготовления применялись смолы «горячего отверждения», предназначенные для фанеры, ДСП, ДВП и т. д. Попытки отверждения этих смол при температурах 20.25оС приводили к тому, что процесс их полимеризации (с одновременным выделением формальдегида) длился месяцы, а то и годы.
Принято считать, что чем меньше свободного формальдегида в смоле, тем ниже токсичность материалов, полученных на ее основе. Содержание свободного формальдегида в смоле зависит от соотношения формалина к карбамиду и в определенных границах может регулироваться технологическими приемами ведения процесса синтеза. Однако, чем ниже это отношение в рецептуре смолы, тем трудней соблюсти баланс между высокими физико-техническими свойствами и низким содержанием свободного формальдегида в ней.
Поэтому прямые попытки снижения свободного формальдегида в смолах не приводили к положительным результатам, а соответственно для материалов, изготовленных на их основе и применяемых в строительной промышленности, проблема токсичности остается по-прежнему открытой до настоящего времени.
Проводимые на протяжении последних 15 лет научно-исследовательские работы в этом направлении показали, что положительный результат может быть достигнут только при комплексном подходе к изготовлению материалов на этапах их «создания»:
- при синтезе смолы;
- при подготовке готовой смолы к применению;
- при производстве самих материалов и изделий;
Причем, основная роль в производстве экологически безопасных материалов и изделий принадлежит именно этапу синтеза смолы. Подтверждением этого вывода является реализованная на практике новая технология синтеза смол марок «ВПС-Г»® (ОАО «УХК», г. Н.Тагил) и «КАРБАМЕТ-Т»® (ОАО «Карболит», г. Орехово-Зуево МО), серийно выпускаемых в настоящее время и применяемых для производства пенопласта «МЕТТЭМПЛАСТ» ®.
В основу разработанной технологии положены новые методы гомогенизации смолы при ее синтезе и рабочих растворов при производстве пенопласта. В смоле практически отсутствуют вещества, являющиеся источником выделения свободного формальдегида в процессе эксплуатации пенопласта.
Исследования показали, что у пенопласта, изготовленного из указанных смол, выделения свободного формальдегида в десятки и сотни (!) раз ниже, чем у пенопластов, изготовленных на основе смол марок КФ-МТ, КФ-МТ-15, КФ-Ж, крепитель М-3 и др., как при производстве, так и при эксплуатации.
Следует отметить, что при применении новых смол марок «ВПС-Г»® и «КАРБАМЕТ-Т»® значительно улучшается экология самого производства пенопласта, что существенно сокращает затраты на охрану труда.
Но чем больший авторитет завоевывает «МЕТТЭМПЛАСТ» Карбамидные пенопласты, изготовленные на основе других смол, никакого отношения к «МЕТТЭМПЛАСТу»® не имеют. И более того, применение других более дешевых смол приводит к потере экологической безопасности пенопластов и резкому сокращению сроков их эксплуатации.
Еще хочется отметить, что санитарно-гигиеническая безопасность пенопласта, изготовленного из вышеуказанных смол, подтверждена многочисленными заключениями Госкомитетом СЭН в различных регионах России. Пенопласт также сертифицирован Госстандартом, Госстроем, прошел испытания на пожарную безопасность во ВНИИПО МВД и его филиалах в Санкт-Петербурге и Омске, в испытательном центре «Огнестойкость» ГУП ЦНИИСК им. В. А. Кучеренко, а также проверку теплофизических характеристик в НИИСФ, в НИИМосстроя и т. д.
Так, что и пенопласты бывают безопасными!
Оценка тепловых свойств изоляции в транспортных контейнерах для UF/sub 6/ транспорта (Конференция)
Оценка тепловых свойств изоляции в транспортных контейнерах для UF/sub 6/ транспорта (Конференция) | ОСТИ.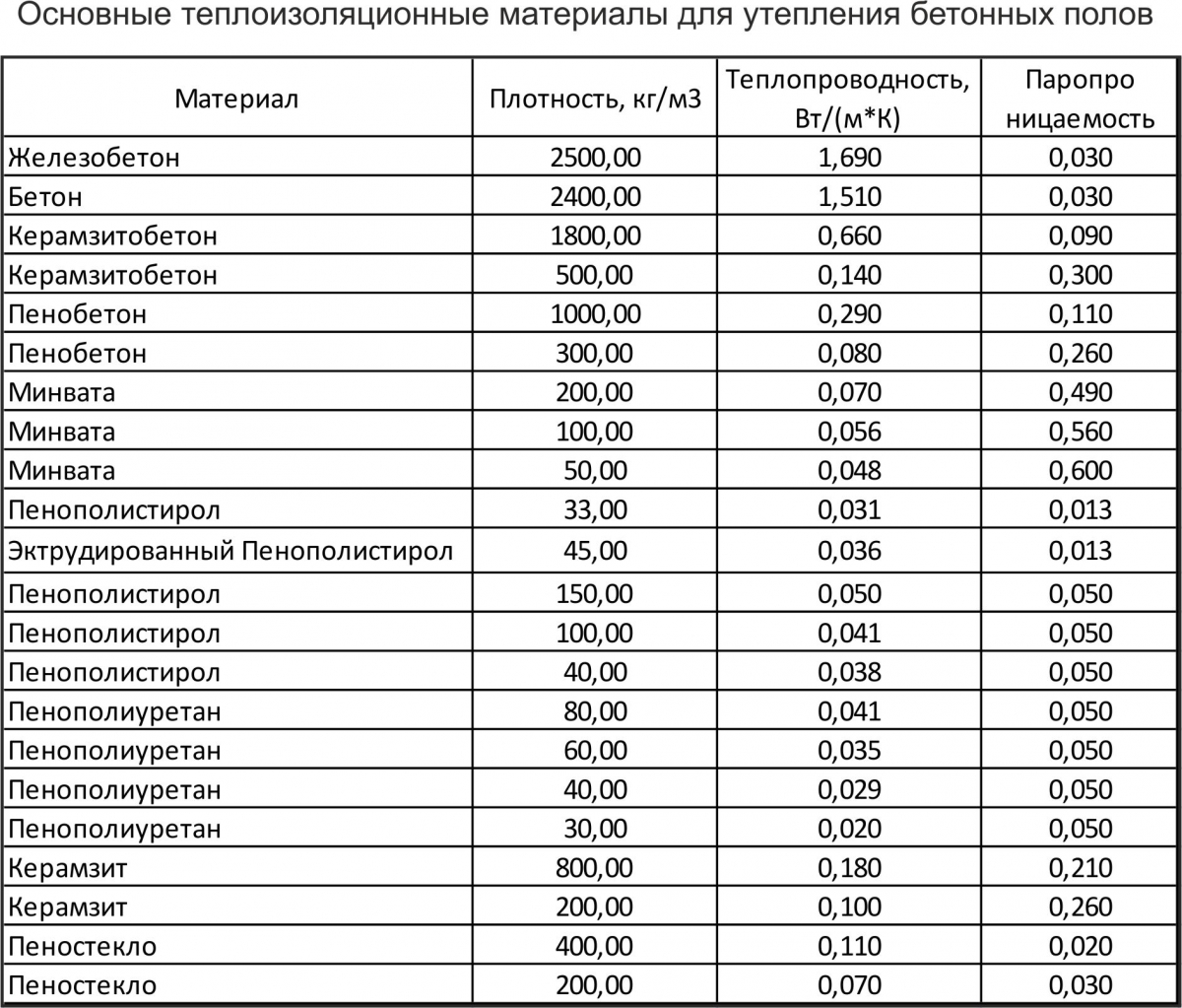
перейти к основному содержанию
- Полная запись
- Другое связанное исследование
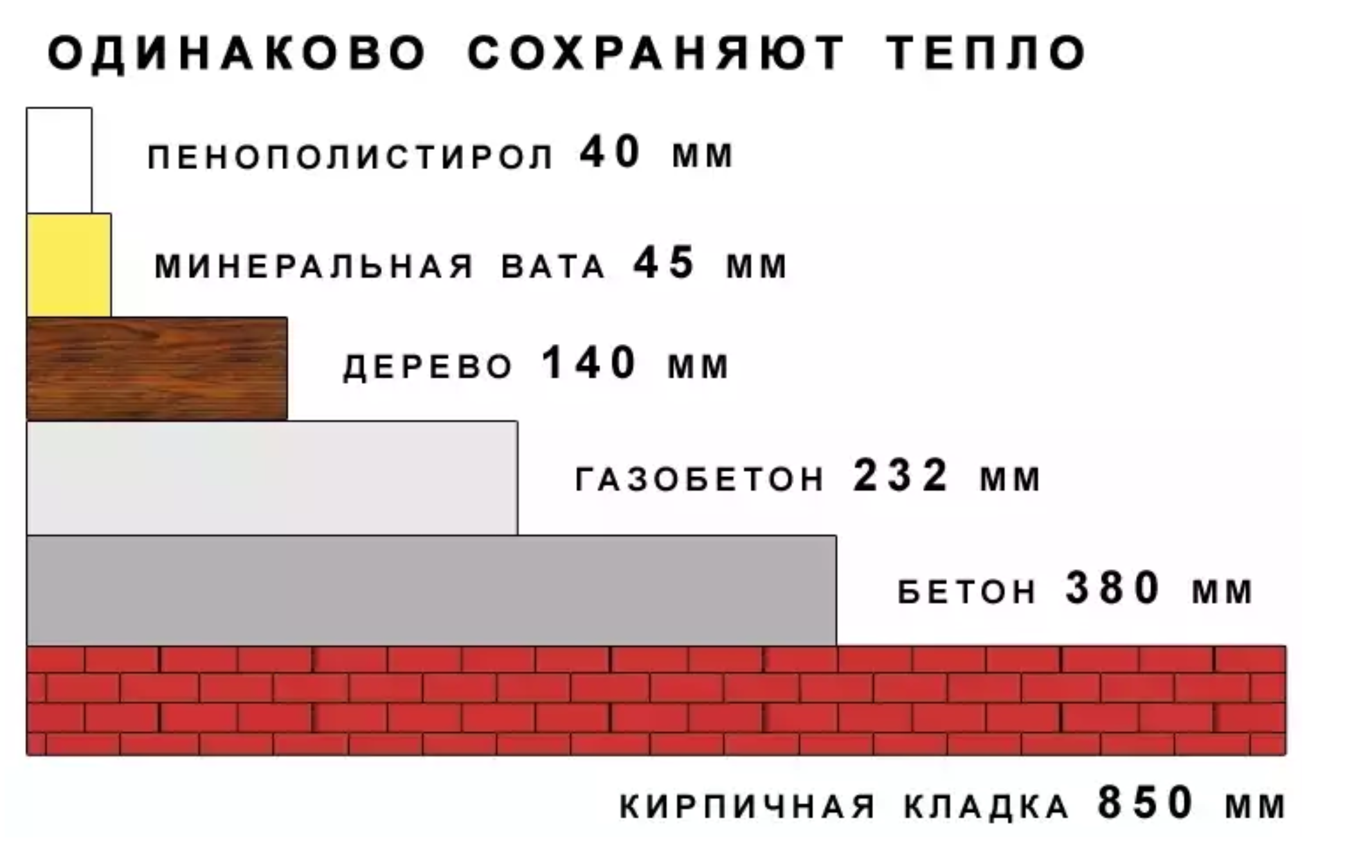
- Авторов:
- Фрейзер, Дж. Л.
- Дата публикации:
- Исследовательская организация:
- Газодиффузионный завод в Ок-Ридже, Теннесси (США)
- Идентификатор ОСТИ:
- 6368656
- Номер(а) отчета:
- К/QT-301; CONF-890631-39
ВКЛ.: DE822
- Номер контракта с Министерством энергетики:
- АК05-84ОТ21400
- Тип ресурса:
- Конференция
- Отношение ресурсов:
- Конференция: Международный симпозиум по упаковке и транспортировке радиоактивных материалов, Вашингтон, округ Колумбия, США, 11 июня 1989 г.; Дополнительная информация: Части этого документа неразборчивы на микрофишах .
- Страна публикации:
- США
- Язык:
- Английский
- Тема:
- 12 ОБРАЩЕНИЕ С РАДИОАКТИВНЫМИ И НЕРАДИОАКТИВНЫМИ ОТХОДАМИ ЯДЕРНЫХ ОБЪЕКТОВ; 11 ЯДЕРНО-ТОПЛИВНЫЙ ЦИКЛ И ТОПЛИВНЫЕ МАТЕРИАЛЫ; ПЕНЫ; ТЕРМИЧЕСКИЙ АНАЛИЗ; ГЕКСАФТОРИД УРАНА; ТРАНСПОРТ; ТЕПЛОПРОВОДНОСТЬ; АКТИНИДНЫЕ СОЕДИНЕНИЯ; КОЛЛОИДЫ; ДИСПЕРСИИ; ФТОРИДЫ; СОЕДИНЕНИЯ ФТОРА; ГАЛИДЫ; ГАЛОГЕННЫЕ СОЕДИНЕНИЯ; ФИЗИЧЕСКИЕ СВОЙСТВА; ТЕРМОДИНАМИЧЕСКИЕ СВОЙСТВА; СОЕДИНЕНИЯ УРАНА; ФТОРИДЫ УРАНА; 052001* – Ядерное топливо – Переработка отходов; 053000 – Ядерное топливо – Экологические аспекты
Форматы цитирования
- MLA
- АПА
- Чикаго
- БибТекс
Frazier, J.
L. Оценка тепловых свойств изоляции в транспортных контейнерах для UF/суб6/транспорта . США: Н. П., 1989.
Веб.
Копировать в буфер обмена
Frazier, J.L. Оценка тепловых свойств изоляции в транспортных контейнерах для UF/суб6/транспорта . Соединенные Штаты.
Копировать в буфер обмена
Фрейзер, JL. 1989.
«Оценка тепловых свойств изоляции в транспортных контейнерах для UF/sub 6/транспорта». Соединенные Штаты. https://www.osti.gov/servlets/purl/6368656.
Копировать в буфер обмена
@статья{osti_6368656,
title = {Оценка тепловых свойств изоляции в транспортных контейнерах для UF/sub 6/ транспорта},
автор = {Фрейзер, Дж. Л.},
abstractNote = {Два типа изоляции в настоящее время используются в транспортных упаковках, используемых для защиты UF/sub 6/ во время транспортировки.
Фенольная пена использовалась в семействе транспортных пакетов UF/sub 6/ в соответствии со спецификациями Министерства транспорта США. Недавно были разработаны внешние пакеты нового поколения, в которых используется пенополиуретан. Проведен сравнительный анализ тепловых характеристик пенофенола с полиуретаном двух различных плотностей. Термические свойства материалов меняются в зависимости от температуры, и эта взаимосвязь представляет собой сложное взаимодействие свойств основных материалов, переменных обработки и условий окружающей среды. Необходимость включения тепловых свойств, зависящих от температуры, в аналитические коды методом конечных элементов привела к созданию экспериментальной программы для измерения тепловых свойств, главным образом, теплопроводности, для пенопласта 21ПФ-1 для внешней упаковки. Зависимость теплопроводности от температуры для этого изолятора была измерена от комнатной температуры до более чем 1000F. Альтернативный внешний контейнер UF/sub 6/цилиндров с продуктом недавно был введен в эксплуатацию; конструкция транспортного пакета, включающая полиуретан в качестве основного теплового сопротивления вместо фенольной пены в транспортном пакете цилиндра весом 2 1/2 тонны.
Представлены измерения термических свойств системы полиуретановых материалов при повышенных температурах.},
дои = {},
URL = {https://www.osti.gov/biblio/6368656},
журнал = {},
номер =,
объем = ,
место = {США},
год = {1989},
месяц = {1}
}
Копировать в буфер обмена
Просмотр конференции (0,40 МБ)
Дополнительную информацию о получении полнотекстового документа см. в разделе «Доступность документа». Постоянные посетители библиотек могут искать в WorldCat библиотеки, в которых проводится эта конференция.
Экспорт метаданных Сохранить в моей библиотеке
Вы должны войти в систему или создать учетную запись, чтобы сохранять документы в своей библиотеке.
Аналогичных записей в сборниках OSTI.GOV:
- Аналогичные записи
Испытание полиуретановой резины и пены на термическую эффузивность
Измерительная платформа-2 (MP-2) представляет собой усовершенствованный прибор с уникальным набором датчиков переходной теплопроводности для различных применений с упором на первичные измерения.
Рисунок 1. Измеритель теплопроводности Thermtest MP-2
Измеритель теплопроводности MP-2 выигрывает от удобства и точности, получаемых при использовании первичных методов измерения. Контроллер МП-2 автоматически определяет подключенный датчик и загружает соответствующие параметры тестирования. Измерения легко выполняются с помощью интеллектуального встроенного программного обеспечения и передаются на компьютер с помощью прилагаемой служебной программы Windows.
Рисунок 2. Датчик Thermtest TPS-EFF для использования с переносным счетчиком МП-2..
TPS-EFF представляет собой портативный измеритель коэффициента эффузивности для текстиля, тканей и твердых материалов, который соответствует международно признанному стандарту испытаний в соответствии со стандартом ASTM D7984-16 . Этот датчик имеет диапазон измерения тепловой эффузии от 35 до 1700 (Вт√с/м 2 K) и температурный диапазон от от -10 ºC до 50 ºC . Продолжительность одного измерения может быть установлена на 2 или 10 секунд. TPS-EFF имеет точность 5% и воспроизводимость измерений 2%, что делает его высокоточным и прецизионным инструментом для измерения термической эффузии различных образцов.
Тепловая эффузивность чаще всего измеряется для прогнозирования того, насколько «холодным» или «теплым» на ощупь является материал. Она пропорциональна квадратному корню плотности, теплопроводности и удельной теплоемкости материала. Высокоплотные образцы из материалов с высокими значениями теплопроводности и удельной теплоемкости имеют высокие значения коэффициента теплоотдачи, и наоборот. В этом листе приложений используется датчик Thermtest TPS-EFF для измерения коэффициента теплового эффузивного действия пенополиуретана и полиуретанового каучука.
Тепловая эффузивность полиуретанового каучука и пены
Полиуретан может быть превращен во множество различных материалов различной прочности и долговечности, от пены до резины. В этом листе применения термическая эффузивность пенополиуретана сравнивается с двумя различными твердостями полиуретанового каучука, 40A и 60A. Дюрометр материала — это стандартизированная мера его твердости. Пены часто используются в мебели и обивке, а каучуки обычно используются в качестве прокладочного материала. Прокладки представляют собой тип механического уплотнения между двумя или более поверхностями, как правило, для предотвращения утечек жидкости или газа. Тепловая эффузивность и твердость любого полиуретанового материала важны для обеспечения его надлежащей работы в окружающей среде или на машине, для которой он предназначен.