Допуск плоскостности
На плоскостях деталей в ходе обработки образуются поверхности с характерными отклонениями. Чтобы указать допустимые погрешности плоскостности, не снижающие качество последующего использования этой детали, на чертеже наносится знак в виде ромба и цифровое значение.
Допуск плоскостности поверхности 0.1 мм
.
Допуск плоскостности поверхности 0.1 мм
на площади 100 × 100 мм
.
Допуск плоскостности поверхностей относительно общей прилегающей 0.1 мм
.
Допуск плоскостности
каждой поверхности 0.01 мм
.
Способов контроля величины отклонения плоскостности описываемых в научно-технической литературе существует достаточно много, но направление методов измерения можно разделить на два вида, это оптическое и не оптическое измерение.
Оптические способы измерения основаны на сравнении реального состояния профиля с визирной осью светового луча. Не оптические средства контроля, производят анализ поверхности элементами конструкции измерительного прибора.
Для установления величины плоскостности чаще всего задействуются приборы с механическим оптическим и гидростатическим методом преобразования снимаемых данных.
В механических приборах измерительный механизм построен на кинематическом принципе действия, преобразующем небольшие перемещения измеряемых значений, в увеличенные передвижения которые принимаются регистрирующими устройствами.
Гидростатические приборы используют методы измерения с использованием жидкости. Принцип измерения основан на сравнении плоскости, которая образовывается поверхностью жидкости, всегда располагающейся горизонтально, с проверяемой поверхностью.
Измерительные оптические приборы
являются средствами измерения, в которых при выполнении измерений задействован ряд оптических элементов таких как: объективы, зеркала, призмы, окуляры и передвигающие их рычаги, кронштейны, направляющие и т.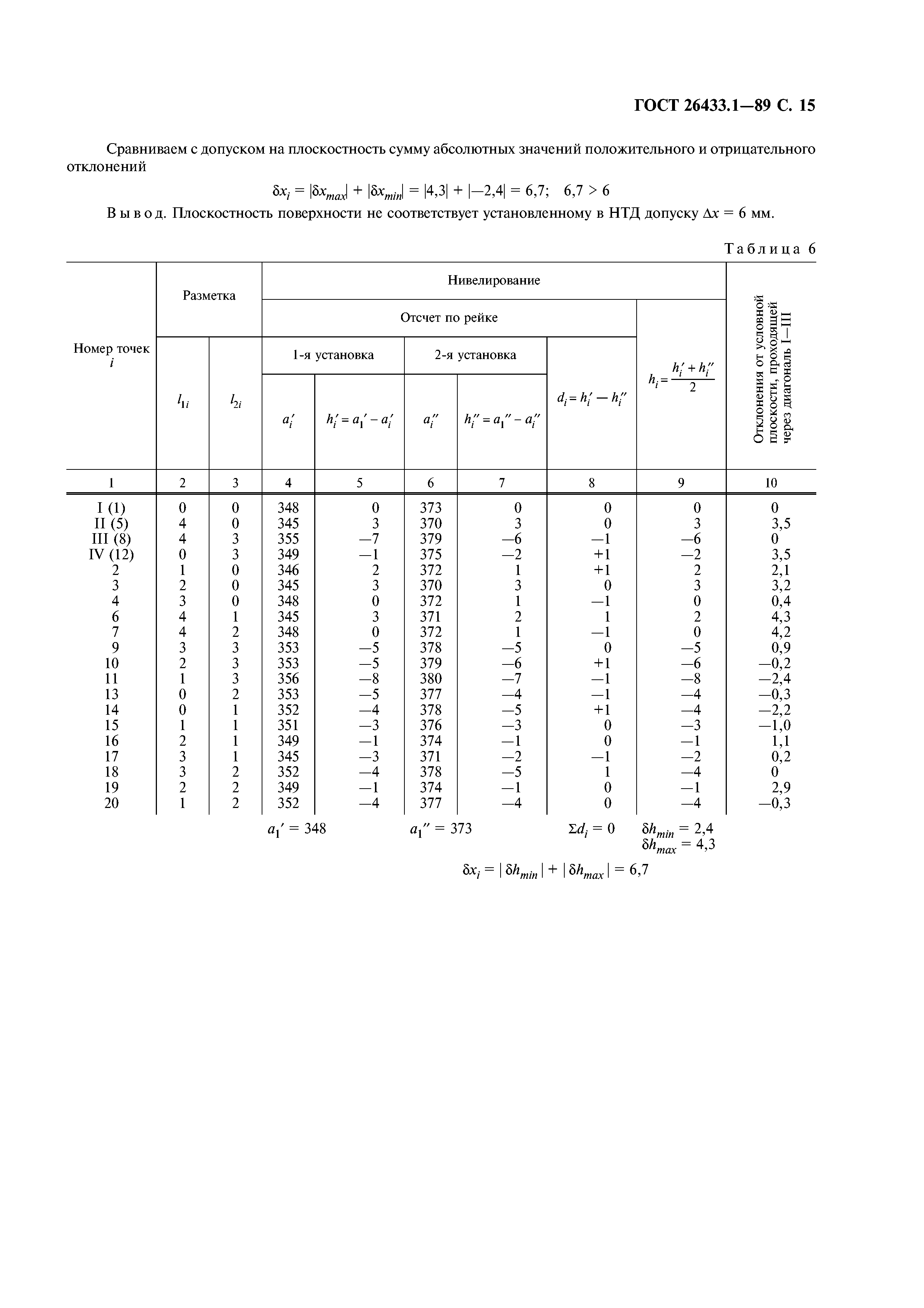
Анализ поверхности, производимый оптическими средствами измерения, осуществляется за счёт потока лучей, несущих информацию об измеряемой детали, проходящих через ряд элементов оптико-механической или оптико-электронной конструкции.
Поверочные плиты
Измерение отклонений от плоскостности производят с помощью специальных поверочных плит, принцип определения которыми заключается в том, что рабочую поверхность плиты принимают за исходную плоскость, по которой определяют отклонения реальной плоскости изделия.
Процесс измерения плитами в большинстве случаев связано с нанесением специальной краски, по которой выявляют неровности. На плиту наносят тонкий слой краски, после чего кладут на плоскость проверяемой детали. В результате перемещения плиты по поверхности детали определяют количество пятен, оставляемых после выдавливания краски во впадинах неоднородной поверхности.
Поверочные плиты, как правило, изготавливаются из серого чугуна, которые имеют свои достоинства и недостатки.
Помимо чугуна для изготовления поверочных плит используется ряд твердых каменных пород. Основным из преимуществ, каменных поверочных плит является износостойкость, и долгий срок службы по сравнению с чугунными плитами. В каменных плитах отсутствует внутреннее напряжение. Поверочные плиты из гранита меньше подвержены деформации из-за изменения температуры внешней среды, так как коэффициент теплового расширения у них меньше, чем у чугуна. Каменные поверочные плиты менее чувствительны к вибрациям.
Стандартные плиты выпускаются с размерами от 250 × 250
до 4000 × 1600 мм
и используются как для измерения плоскости, так и для контрольно измерительных работ.
плоскостность – это… Что такое плоскостность?
3.6 плоскостность: Отклонение от плоскостности, при которой поверхность металлопродукции или ее отдельные части имеют вид чередующихся выпуклостей или вогнутостей, образующих не менее двух вершин отдельных волн, не предусмотренных формой проката (ГОСТ 26877).
Смотри также родственные термины:
3.4.67 плоскостность бумаги или картона: Состояние бумаги или картона, характеризуемое отсутствием волнистости или скручиваемости, видимых невооруженным глазом на образце, положенном на плоскую горизонтальную поверхность.
3.2. Плоскостность и шероховатость обработанной поверхности заготовки (черт. 10).
Черт. 10
Допуск 0,40 мм на длине 400 мм
Шероховатость обработанной поверхности заготовки должна быть
На обработанную поверхность 1 устанавливают поверочную линейку 2. Измерения проводят в продольном и поперечном направлениях не менее чем в трех сечениях (двух крайних и среднем) и диагональных направлениях.
Измерения проводят на расстоянии не менее 20 мм от торца.
Просвет между рабочей поверхностью поверочной линейки и проверяемой поверхностью измеряют щупом. В каждом направлении определяют наибольшую величину просвета.
Отклонение от плоскостности определяют как наибольший из полученных результатов измерений.
Шероховатость обработанных поверхностей определяют профилометром, профилографом или по образцу.
2.5. Плоскостность обработанной поверхности Б (черт. 26 и 27).
Черт. 27
Таблица 17
Наибольшая длина обрабатываемой поверхности, мм | Допуск, мкм, для станков класса точности | ||
П | В | А | |
До 160 | 6 | 4 | 2,5 |
Св. 160 до 250 | 8 | 5 | – |
» 250 » 400 | 10 | 6 | – |
»400 » 630 | 12 | 8 | – |
Проверку проводят при помощи приспособления, состоящего из поверочной плиты 3
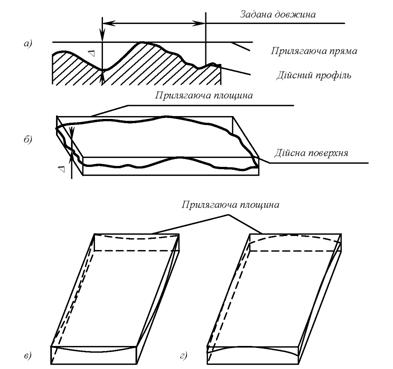
3.1. Плоскостность обработанной поверхности образца
Таблица 12
Ширина В бабок, мм | Допуск, мкм, для бабок класса точности | ||
Н | п | в | |
125; 160 | 12 | 8 | 5 |
200; 250 | 16 | 10 | 6 |
320; 400 | 20 | 12 | 8 |
500; 630 | 25 | 16 | 10 |
Образец закрепляют (стационарно или на узле подачи) на специальном стенде или на станке. На том же стенде (станке) закрепляют (соответственно на узле подачи или стационарно) бабку и после предварительного фрезерования проводят чистовую обработку.
Обработку проводят с перекрытием.
Проверку обработанной поверхности закрепленного образца проводят при помощи поверочной линейки и плоскопараллельных концевых мер длины.
Отклонение от плоскостности равно разности наибольшего и наименьшего просветов между линейкой и обработанной поверхностью.
3.2. Плоскостность по пласти образца
Допуск плоскостности по пласти в продольном и диагональном направлениях 2 мм на длине 1000 мм, в поперечном направлении 1 мм на длине 100 мм.
Проверка проводится в соответствии со схемой, указанной на черт. 6а.
2.2. Плоскостность поверхности 2 (черт. 33)
Черт. 34 | Черт. |
Таблица 20
Длина измерения, мм | Допуск, мкм, для станков класса точности | ||
П | В | А | |
До 160 | 10 | 6 | 5 |
Св. 160 до 250 | 12 | 8 | 6 |
» 250 » 400 | 16 | 10 | 8 |
Измерения – по ГОСТ 22267, разд. 4, методы 2 и 3 (черт. 34, 35) не менее чем в двух продольных, трех поперечных и двух диагональных сечениях.
2.7. Плоскостность поверхности основания бабки
Черт. 6
Таблица 6
Ширина В бабок, мм | Допуск, мкм, для класса точности | ||
Н | п | в | |
125, 160 | 16 | 10 | 6 |
200, 250 | 20 | 12 | 8 |
320, 400 | 25 | 16 | 10 |
500, 630 | 30 | 20 | 12 |
Выпуклость не допускается.
Измерения – по ГОСТ 22267, разд. 4, метод 2 или 3.
2.5. Плоскостность поверхности основания бабки
Черт. 4
Таблица 4
Ширина Вбабок, мм | Допуск, мкм |
125; 160 | 16 |
200; 250 | 20 |
320; 400 | 25 Выпуклость не допускается |
Измерения – по ГОСТ 22267, разд. 4, метод 2 или 3.
2.7. Плоскостность поверхности основания бабки
Таблица 6
Ширина В бабок, мм | Допуск, мкм, для бабок класса точности | ||
Н | п | в | |
125; 160 | 16 | 10 | 6 |
200; 250 | 20 | 12 | 8 |
320; 400 | 25 | 16 | 10 |
500; 630 | 30 | 20 | 12 |
Выпуклость не допускается |
Черт. 6
Измерения – по ГОСТ 22267, разд. 4, метод 2 или 3.
2.4. Плоскостность подрезанной торцовой поверхности
Таблица 13
Наибольший диаметр патрона, мм | Допуск, мкм, для полуавтоматов класса точности | ||
Для станков, спроектированных после 01.01.84 | Для станков, спроектированных до 01.01.84 | Н | П |
До 125 | До 125 | 16 | 10 |
Св. 125 до 200 | Св. 125 до 160 | 20 | 12 |
» 200 | » 160 » 250 | 25 | 16 |
Выпуклость не допускается |
На контролируемом торце образца-изделия устанавливают контрольную линейку, на которой закрепляют измерительный прибор.
Наконечник измерительного прибора должен касаться проверяемой поверхности и располагаться перпендикулярно к ней. Контрольную линейку перемещают по торцу образца так, чтобы наконечник измерительного прибора перемещался по диаметральному сечению торца. Отклонение от плоскостности равно наибольшей алгебраической разности показаний измерительного прибора на длине 100 мм.
Контролируют не менее одного образца-изделия, обработанного на каждом шпинделе.
1.3.1. Плоскостность рабоче й поверхности фундаментной плиты (тумбы, стола-плиты)
Черт. 1
Черт. 2
Черт. 3
Черт. 4
Таблица 1
Длина измерения L (В), мм | Допуск, мкм, для станков класса точности | |
Н | П | |
До 630 | 40 | 25 |
Св. | 50 | 30 |
» 1000 » 1600 | 60 | 40 |
» 1600 » 2500 | 80 | 50 |
» 2500 » 4000 | 100 | 60 |
Выпуклость не допускается |
Измерения – по ГОСТ 22267-76, разд. 4, методы 2, 3 и 6 (черт. 1 – 3) не менее, чем в двух продольных, трех поперечных и двух диагональных сечениях плиты (тумбы, стола-плиты) (черт. 4).
Расстояние между точками измерения не должно превышать 0,2длины проверяемой поверхности в продольном и в поперечном направлениях.
Начальная точка измерения в контролируемых сечениях должна отстоять от края плиты на 0,5 расстояния между точками измерения.
Для плиты (тумбы, откидного стола, стола-плиты) с соотношением L:В свыше 2 измерение в диагональных сечениях не производят.
Для станков исполнения 3 по ГОСТ 1222-80 проверятьплоскостность плиты и откидного стола.
2.3. Плоскостность рабочей поверхности опорной плиты
Таблица 2
Черт. 2
Примечание. Выпуклость не допускается.
Длина большей стороны рабочей поверхности опорной плиты, мм | Допуск, мкм |
До 400 | 30 |
Св. 400 » 630 | 40 |
» 630 »1000 | 50 |
Измерение – по ГОСТ 22267, разд. 4, метод 3 (черт. 2).
Количество и расположение проверяемых сечений – в соответствии с черт. 2.
2.4. Плоскостность рабочей поверхности планшайбы
Черт. 2
Черт. 3
Таблица 2
D, мм | Допуск, мкм, для станков классов точности | |
Н | П | |
До 1000 | 30 | 20 |
Св. 1000 » 1600 | 40 | 25 |
» 1600 » 2500 | 50 | 30 |
» 2500 » 4000 | 60 | 40 |
» 4000 » 6300 | 80 | 50 |
» 6300 » 10000 | 100 | 60 |
» 10000 » 16000 | 120 | 80 |
» 16000 | 160 | 100 |
Измерения – по ГОСТ 22267, разд. 4, методы 3, 6 (черт. 2, 3).
Измерения проводят в двух взаимно перпендикулярных диаметральных сечениях планшайбы. Интервал измерения должен быть равен примерно 0,2 длины проверяемого сечения и быть не более 1000 мм.
5.1.4 Плоскостность рабочей поверхности планшайбы стола
Рисунок 1 | Рисунок 2 |
Рисунок 3 | Рисунок 4 |
Рисунок 5 |
Таблица 1
Диаметр планшайбы, км | Допуск, мкм, для столов класса точности | ||
Н | П | В | |
До 200 | 12 | 8 | 6 |
Св. | 16 | 10 | 8 |
» 320 » 500 | 20 | 12 | 10 |
» 500 » 800 | 25 | 16 | 12 |
» 800 » 1250 | 32 | 20 | 16 |
Выпуклость поверхности не допускается |
Измерения (по ГОСТ 22267, разд. 4, методы 2, 3 и 4 (рисунки 1, 2, 3).
Измерения проводят в сечениях, указанных на рисунке 5. Длина интервала между соседними точками измерения не должна превышать 0,2 соответствующей длины измерения.
Для столов с диаметром планшайбы до 200 мм допускается проведение измерений по ГОСТ 22267, разд. 4, метод 1 (рисунок 4).
Число пятен на площади размером 25×25 мм для столов класса точности Н – не менее 9, для столов класса точности П – не менее 16, для столов класса точности В – не менее 20.
2.4. Плоскостность рабочей поверхности стола
Черт. 2
Таблица 2
Диаметр рабочей поверхности стола, мм | Допуск, мкм, для станков классов точности | |
П | В | |
До 500 | 8 | 5 |
Св. 500 » 1000 | 10 | 6 |
» 1000 » 1600 | 14 | 8 |
Выпуклость не допускается |
Измерения – по ГОСТ 22267, разд. 4, метод 3, черт. 2.
Для столов диаметром до 1000 мм проверка должна быть проведена не менее чем в 3 продольных и 3 поперечных сечениях, для столов диаметрам св. 1000 мм – не менее чем в 4 продольных и 4 поперечных сечениях, расположенных взаимно-перпендикулярно.
3.5 Плоскостность рабочей поверхности стола
Рисунок 1 | Рисунок 2 |
Рисунок 3 | Рисунок 4 |
Таблица 1
Длина измерения, мм | Допуск, мкм |
До 320 | 3 |
Св. | 4 |
« 500 « 800 | 5 |
« 800 « 1250 | 6 |
« 1250 « 2000 | 8 |
« 2000 | 10 |
Измерения – по ГОСТ 22267, раздел 4, методы 3, 4 или 6 (рисунки 1 – 3).
Крайние сечения должны быть расположены от края стола на расстоянии не более 0,1 его ширины В и длины L (рисунок 4).
Расстояние между точками измерений 0,08 – 0,12 длины (ширины) стола.
2.9. Плоскостность рабочей поверхности стола
Таблица 4
Длина большей стороны стола, мм | Допуск, мкм |
До 400 | 30 |
Св. | 40 |
» 630 » 1000 | 50 |
Примечание. Выпуклость не допускается.
Черт. 8
Измерение – по ГОСТ 22267, разд. 4, метод 3.
Количество и расположение проверяемых сечений в соответствии с черт. 8.
2.3.1. Плоскостность рабочей поверхности стола (черт. 2)
Черт. 2
Допуск, мм, для длины стола, мм:
до 800……………………………………………….. 0,06
св. 800 до 1120…………………………………. 0,08
св. 1120 до 1600………………………………. 0,16
Выпуклость не допускается
На рабочую поверхность стола 3 в двух точках заданного сечения устанавливают две специальные опоры 2, на которые рабочей поверхностью кладут поверочную линейку 1 так, чтобы расстояния от проверяемой поверхности до рабочей поверхности линейки у ее опор были равны.
Расстояние между линейкой и проверяемой поверхностью измеряют щупом или блоком плоскопараллельных концевых мер длины. Измерения проводят в поперечном и продольном направлениях не менее чем в трех сечениях по длине базовых поверхностей стола (двух крайних и среднем) и диагональных направлениях. В каждом сечении определяют наибольшую разность измеренных расстояний.
Отклонение от плоскостности равно наибольшему из полученных результатов.
3.8 Плоскостность рабочей поверхности стола
Рисунок 1 | Рисунок 2 |
Рисунок 3 | Рисунок 4 |
Рисунок 5
Рисунок 6
Таблица 1
Длина измерения, мм | Допуск, мкм, для станков классов точности | |
П | А | |
До 500 | 16 | 8 |
Св. | 20 | 10 |
» 800 » 1250 | 25 | 12 |
» 1250 » 2000 | 30 | 16 |
» 2600 » 3200 | 40 | 20 |
» 3200 » 5000 | 50 | – |
» 5000 » 8000 | 60 | – |
» 8000 » 12600 | 80 |
Примечания
1 Местный допуск на длине 500 мм (для длин измерения свыше 800 мм) для станков классов точности П – 20 мкм, А – 10 мкм.
2 Для неподвижных столов-плит допуск увеличивают в 1,25 раза.
3 Для столов с отношением L:B менее 4 выпуклость не допускается.
Измерение – по ГОСТ 22267, разд. 4, методы 3, 6, 8, 9 или 12 (рисунки 1, 2, 3, 4, или 5).
Расположение продольных, поперечных и диагональных сечений, в которых проводят измерения, а также точек измерения в этих сечениях показаны на рисунке 6.
Количество контролируемых сечений должно быть: не менее трех продольных и трех поперечных, два диагональных. Для столов с соотношением L:B более 2 допускается проводить измерения только в продольных и поперечных сечениях.
В каждом сечении длина измерения должна быть не менее 0,9 от длины сечения и расположена симметрично в пределах длины сечения.
Длина интервала между соседними точками измерения не должна превышать 0,2 соответствующей длины измерения для станков класса точности П и 0,1 соответствующей длины измерения для станков классов точности А, но не более 1000 мм в продольном и 500 мм в поперечном сечениях.
4.3.1 Плоскостность рабочей поверхности стола
Рисунок 2
Рисунок 3
Рисунок 4
Таблица 2
Длина измерения, мм | Допуск, мкм |
До 500 | 10 |
Св. 500 » 800 | 12 |
» 800 » 1250 | 16 |
» 1250 » 2000 | 20 |
» 2000 » 3200 | 25 |
» 3200 » 5000 | 30 |
Примечание. На длине измерения до 2000 мм выпуклость не допускается. |
Измерения – по ГОСТ 22267, раздел 4, метод 3 при длине перемещения до 1600 мм (рисунок 2), раздел 4, методы 6 и 9 – при длине перемещения свыше 1600 мм (рисунки 3, 4).
При шаговом методе измерений (методы 6 и 9) расстояние между точками измерения выбирается не более 0,1 длины стола и не менее 100 мм.
Измерения проводят не менее чем в двух продольных и трех поперечных сечениях стола, расположенных в середине и по краям, на расстояниях соответственно равных 0,2 ширины (длины) стола.
Измерения проводят в среднем или одном из крайних положений стола.
1.2. Плоскостность рабочей поверхности стола (черт. 1)
Черт. 1
Таблица 1
Длина измерения, мм | Допуск, мкм, для станков класса точности | ||
П | В | А | |
До 250 | 8 | 6 | 4 |
Св. 250 до 400 | 10 | 8 | – |
» 400 » 630 | 12 | 10 | – |
Выпуклость не допускается |
Измерения – по ГОСТ 22267-76, разд. 4, п. 4.3.3, метод 3.
3.6. Плоскостность рабочей поверхности стола
Рисунок 1 | Рисунок 2 |
Рисунок 3 | Рисунок 4 |
Рисунок 5 | Рисунок 6 |
Рисунок 7 | Рисунок 8 |
Таблица 1
Длина измерения, мм | Допуск, мкм, для станков классов точности | |
Н | П | |
До 1000 | 25 | 20 |
Св. | 30 | 25 |
« 1600 « 2500 | 40 | 30 |
« 2500 « 4000 | 50 | 40 |
Примечания
1 Для столов с отношением L:В менее 4 выпуклость не допускается.
2 При длине измерения свыше 1000 мм допуск 25 мкм для класса Н и 20 мкм для класса П на любом интервале перемещения 1000 мм является обязательным в пределах всей длины измерения.
Измерение – по ГОСТ 22267, разд. 4, методы 3, 6 или 9 (рисунки 1 – 3).
Допускается проводить измерение по ГОСТ 22267, разд. 4, методы 2, 4 или 8 (рисунки 4 – 6).
Крайние сечения должны быть расположены от края стола на расстоянии 0,1 его ширины В, диаметра D или длины L (рисунки 7, 8).
Расстояние между точками измерений не должно превышать 0,1 длины измерения.
Допускается для столов с отношением L:В свыше 2 измерение в диагональных сечениях не проводить.
3.7 Прямолинейность траектории перемещения в горизонтальной и вертикальной плоскостях:
3.7.1 Стола по станине.
1.3. Плоскостность рабочей поверхности стола (вертикального, углового горизонтального и универсальног о)
Черт. 1 | Черт. 2 | Черт. 3 |
Таблица 1
Длина измерения, мм | Допуск, мкм, для станков класса точности | ||
П | В | А | |
До 400 | 12 | 8 | 6 |
Св. | 16 | 10 | 8 |
» 630 » 1000 | 20 | 12 | 10 |
» 1000 » 1600 | 25 | 16 | 12 |
Выпуклость не допускается |
Измерения – по ГОСТ 22267, разд. 4, методы 2 и 3 (черт. 1, 2) не менее чем в двух продольных, трех поперечных и двух диагональных сечениях стола (черт. 3).
2.2. Плоскостность рабочей поверхности стола (для станков с плоским столом)
Допуск 0,2 мм на длине 500 мм (выпуклость не допускается).
Измерение – по ГОСТ 22267, разд. 4, метод 2.
Черт. 1
Черт. 2
2.2.1. Плоскостность рабочей поверхности стола (шпинделя изделия)
Таблица 2
Длина измерения, мм | Допуск, мкм для станков классов точности | |||
Н | П | В | А | |
До 125 | 12 | 8 | 5 | 3 |
Св. | 16 | 10 | 6 | 4 |
» 200 » 320 | 20 | 12 | 8 | 5 |
» 320 » 500 | 25 | 16 | 10 | 6 |
» 500 » 800 | 30 | 20 | 12 | 8 |
» 800 » 1250 | 40 | 25 | 16 | 10 |
» 1250 » 2000 | 50 | 30 | 20 | 12 |
» 2000 » 3150 | 65 | 40 | 25 | 16 |
» 3150 » 5000 | 80 | 50 | 30 | 20 |
» 5000 » 8000 | 100 | – | – | – |
Выпуклость не допускается |
Черт. 2
Измерения – по ГОСТ 22267, разд. 4, метод 6, (черт. 2), не менее чем в 8 сечениях, включая два диаметральных. В случае, если отверстие в столе (шпинделе изделия) больше чем 0,15d, то измерения в диаметральных сечениях не производятся.
2.8. Плоскостность рабочей поверхности стола, стола-плиты, плиты
Черт. 2
Черт. 3
Таблица 2
Длина измерения, мм | Допуск, мкм, для станков классов точности | |
Н | П | |
До 200 | 20 | 12 |
Св. 200 до 320 | 25 | 16 |
» 320 » 500 | 30 | 20 |
» 500 » 800 | 40 | 25 |
» 800 » 1250 | 50 | 30 |
Выпуклость не допускается |
Измерения – по ГОСТ 22267, разд. 4, метод 3 (черт. 2, 3). Крайние сечения должны быть расположены от края рабочей поверхности на расстоянии не более 0,2 проверяемой длины.
Примечание. В многошпиндельных станках с общим столом длина измерения располагается симметрично относительно каждого шпинделя и не должна превышать длины измерения аналогичного одношпиндельного станка.
1.4. Плоскостность рабочей поверхности стола.
Черт. 1 | Черт. 2 |
Черт. 3 | Черт. 4 |
Таблица 1
Длина измерения, мм | Допуск, мкм, станков класса точности | ||
В | А | С | |
До 400 | 8 | 5 | 4 |
Св. | 10 | 6 | 5 |
« 630 « 1000 | 12 | 8 | 6 |
« 1000 « 1600 | 16 | 10 | 8 |
Выпуклость не допускается. В случае, когда обрабатываемая заготовка не закрепляется непосредственно на рабочей поверхности стола, допуски для станков классов точности А, С устанавливают по классу точности В. |
Измерения – по ГОСТ 22267-76, разд. 4, методы 6 (черт. 1), 3 (черт. 2) или 2 (черт. 3) не менее чем в двух продольных, трех поперечных и двух диагональных сечениях рабочей поверхности стола (черт. 4).
Крайние сечения должны быть расположены от края рабочей поверхности на расстоянии 0,2 ее ширины В или длины L.
3.5. Плоскостность торцовой поверхности
Таблица 9
D, мм | Допуск, мкм, для станков классов точности | |
Н | П | |
До 1600 | 30 | 20 |
Св. 1600 » 2500 | 40 | 25 |
» 2500 » 4000 | 50 | 30 |
» 4000 » 6300 | 60 | 40 |
» 6300 |
Измерения – см. п. 2.4.
Проверка боковым суппортом не проводится.
Допускается проводить проверку на образце-изделии с размерами и допусками в соответствии с табл. 10.
Таблица 10
D1, мм | d2 | Допуск, мкм, для станков классов точности | |
Н | П | ||
До 1000 | 500 | 20 | 12 |
Св. 1000 » 3000 | 1000 | 30 | 20 |
» 3000 | 1500 | 40 | 30 |
3.5.3. Плоскостность торцовой поверхности образца (выпуклость не допускается)
Таблица 23
Наибольший диаметр устанавливаемой заготовки, мм | Допуск, мкм, для станков классов точности | |||
П | В | А | С | |
До 200 | 6 | 5 | 4 | 3 |
Св. | 8 | 6 | 5 | 4 |
» 400 | 10 | 8 | 6 | 5 |
Отклонение от плоскостности определяется как разность наибольшего и наименьшего показаний измерительного прибора в различных точках проверяемой поверхности, полученных при перемещении прибора по базовой плоскости. Наконечник измерительного прибора устанавливается перпендикулярно проверяемой поверхности.
Проверка по ГОСТ 22267, разд. 4
2.8. Плоскостность торцовой поверхности повернутого параллелепипеда:
а) 10
3.7. Плоскостность торцовой поверхности шлифованного образца-изделия (для станков со специальным устройством для торцового шлифования)
Таблица 11
Наибольший диаметр D устанавливаемой заготовки, мм | Допуск, мкм, для станков классов точности | ||
П | В | А | |
200 | 5 | 3 | 2 |
Св. | 6 | 4 | 3 |
» 400 » 800 | 8 | 5 | 3 |
» 800 » 1600 | 10 | 6 | 1 |
Выпуклость не допускается |
Образец-втулку с размерами, указанными на черт. 14б и в табл. 9, закрепляют (без люнета) на станке и обрабатывают его торцовую поверхность за одну установку с цилиндрической внутренней поверхностью.
После чистового шлифования торцовой поверхности проверяют вне станка ее плоскостность по ГОСТ 22267, разд. 4, метод. 2.
3.8. Шероховатость поверхности шлифованного образца-изделия:
3.8.1. Цилиндрической внутренней
Словарь-справочник терминов нормативно-технической документации. academic.ru.
2015.
Плоскостность – поверхность – Большая Энциклопедия Нефти и Газа, статья, страница 2
Плоскостность – поверхность
Cтраница 2
Отклонения плоскостности поверхности детали обычно допускаются только в сторону вогнутости. [16]
Нарушение плоскостности поверхностей колец может произойти также в результате старения. [17]
Прямолинейность и плоскостность поверхностей проверяется на просвет или краску с помощью линеек ( по ГОСТ 8026 – 75) или плит ( по ГОСТ 10905 – 86) первого или второго класса точности. [18]
Прямолинейность и плоскостность поверхностей проверяют с помощью линеек или плит методом на просвет или на краску. При использовании первого метода зазор между контролируемой поверхностью и рабочей поверхностью линейки или плиты определяют щупом. При использовании второго метода пятна краски должны равномерно располагаться по всей контролируемой поверхности.
[20]
Отклонение от плоскостности поверхности 1 допускается только по вогнутости 0 1 на 1000 мм, отклонение от перпендикулярности направляющих 2 и 3 поверхности / – до 0 08 мм на 500 мм. [21]
Отклонение от плоскостности поверхностей подложек диаметром 75 – 100 мм после двусторонней доводки ( полирования) на эксцентрико-планетарных станках конструкции МВТУ находится в пределах 2 – 8 мкм. [22]
Отклонение от плоскостности поверхности трения не должно превышать 0 0009 мм. При проверке плоскостности стеклянными пластинами ПИ полосы интерференции света должны быть расположены концентрично оси уплотнитель-ного кольца, что обеспечивает наилучшие условия смазки поверхности трения при эксплуатации. [23]
Методы контроля плоскостности поверхностей, кото -: рые применяют для замера и воспроизведения высотных отметок фланцев горизонтальных разъемов корпусных деталей турбоагрегата, могут быть использованы для исследования изменения пространственного положения той или и-ной корпусной детали по истечению различных периодов эксплуатации, что иногда представляет интерес при выполнении ремонтных работ.
[24]
Проверку прямолинейности и плоскостности поверхностей проводят методом на просвет или краску с помощью линеек ( по ГОСТу 8026 – 75) или плит ( по ГОСТу 10905 – 75) первого или второго класса точности. [25]
При ремонте восстанавливают плоскостность поверхности 1 ( рис. 78) и прямолинейность стенок 2 Т – образных пазов. [27]
В зависимости от плоскостности поверхности пластины сортируются на три типа: ультраплоские, прецизион-ноплоские и микроплоские. Плоскостность определяется интерференционным или пневматическим методом, который позволяет проводить измерения без контактирования с поверхностью. Микроплоские пластины используются для фотоповторителей, прецизионноплоские – для редукционных камер, ультраплоские – для контактной печати. [29]
При наличии отклонения от плоскостности поверхности / до 0 1 мм шабрить опорную плоскость планшайбы по плите, проверяя ее параллельность плоскости А станины индикатором.
[30]
Страницы: 1 2 3 4 5
Поверхности Плоскостность – Энциклопедия по машиностроению XXL
Отклонения формы плоских поверхностей плоскостность, прямолинейность [c.115]Многие изделия в машиностроении характеризуются симметрией криволинейной, или гомологией. В отличие от симметричных фигур с равными расстояниями между соответственными точками, гомологические фигуры имеют неравные расстояния между точками (отражение фигур искривленными поверхностями). Плоскостные и прямолинейные элементы симметрии представляют собой лишь частные случаи элементов криволинейной симметрии. Гомологические фигуры можно получить и другими способами, например, отражением фигуры в зеркальной плоскости -с помощью не перпендикулярных, а косых лучей в этом случае круг после отражения превращается в гомологический эллипс. То есть, может быть не только прямоугольная или ортогональная симметрия, но и косая — точки на линиях, наклонных к плоскости. Можно представить себе такие оси симметрии, вокруг которых точки фигур вращаются не в перпендикулярных, а в косо расположенных плоскостях, не по кругам, а по эллипсам, и т. д. Таким образом, симметрия, характеризуемая равенством расстояний между соответственными точками двух фигур 4
[c.51]
Проверка плоскостности и прямолинейности исправляемой поверхности плоскостным контрольным инструментом ведется двумя способами [c.601]
Детали типа рычагов и вилок, отверстия которых могут быть расположены параллельно, перпендикулярно и под углом к базовой поверхности Плоскостные детали — прямоугольные крышки, прокладки, планки, рейки, угольники, отверстия которых могут быть расположены параллельно, перпендикулярно или под углом к базовой поверхности Детали типа серег, вилок, стяжек, головок Корпусные и сварные детали типа стоек, опор, отверстия которых располагаются параллельно, перпендикулярно и под углом к базовым поверхностям
[c. 509]
Обработка на строгальном станке по наружному контуру (прямоугольник, квадрат) и растачивание внутренней полости на расточном или карусельном станке. По этой схеме обрабатываются литые цилиндры, имеющие по наружным поверхностям плоскостную обработку. [c.269]
Большие допуски формы и расположения. Отклонения от цилиндрич-ности (для сопрягаемых поверхностей), плоскостности, прямолинейности (для призматических деталей), параллельности в тех случаях, когда нет функциональной или иной необходимости в назначении для [c.727]
Допускаемое отклонение от плоскостности измерительных поверхностей микрометра равно 0,9 мкм. Это соответствует трем интерференционным полосам для белого света без учета расстояния 0,5 мм от краев измерительной поверхности. Плоскостность проверяют с помощью плоскопараллельных стеклянных интерференционных пластин наложением их на измерительную поверхность. Отклонение от плоскостности имеет большое влияние на величину ошибки црй измерении краями измерительных поверхностей микрометра.
[c.223]
Протягивание применяют для обработки симметричных и асимметричных сквозных отверстий различных форм (рис. 356, о), сквозных пазов и полуоткрытых отверстий (рис. 356, б), наружных поверхностей плоскостных, канавок, фасонных (рис. 356, в), тел враш,ения (рис. 356, г). [c.545]
Плоскостная калибровка осуществляется обжатием между плитками отдельных элементов штамповки и применяется для получения точных размеров и требуемой чистоты отдельных плоских и криволинейных поверхностей. Плоскостной калибровке могут также подвергаться грубо обработанные резанием поверхности деталей. При плоскостной калибровке происходит свободное течение металла в направлении, перпендикулярном перемещению деформирующего инструмента. [c.189]
В качестве контрольно-измерительного инструмента применяют микрометры, штангенциркули, штихмассы, глубиномеры, жесткие шаблоны и контршаблоны, теодолиты, нивелиры и т. д. Поверочные плиты и линейки используют для проверки шаброванных поверхностей, плоскостности и прямолинейности. Щупы, индикаторы, угольники, угломеры служат для измерения зазоров, контроля геометрической формы и т. д.
[c.167]
Точность формы, т. е. степень соответствия элементарных поверхностей детали геометрически правильным поверхностям (плоскостность, цилиндричность, конусность). [c.92]
Шлифование периферией широкого круга обеспечивает большую производительность за счет снятия большего количества металла в единицу времени и применяется при сравнительно невысоких требованиях к точности и чистоте обработанных поверхностей. Плоскостность обработанной поверхности в этом случае во многом определяется плоскостностью профиля круга, которая зависит от качества правки и характера износа шлифовального круга. Иногда при таком виде шлифования применяется небольшая поперечная подача. Однако в этом случае вся тяжесть снятия припуска переносится на зерна, расположенные ближе к торцам круга, в результате чего последние выкрашиваются быстрее и круг приобретает небольшую конусность.
[c.170]
Контроль и р и т и р к и. Качество притираемых поверхностей проверяют на краску. На хорошо притертых поверхностях краска равномерно ложится по всей поверхности. Плоскостность при притирке проверяют лекальной линейкой с точностью 0,001 мм. [c.433]
У шабренных поверхностей плоскостность и угол пересекающихся поверхностей проверяют перемещением проверяемых поверхностей относительно рабочих сторон плит или угловых линеек, [c.13]
Допустимые отклонения величин делений от номинала определяются по DIN (фиг. 221-2). При проверке точности масштаб должен лежать на поверхности, плоскостность которой не ниже 11-й степени точности по DIN 876. Нормы точности относятся к расстояниям между штрихами, отстоящими не меньше чем на 0.5 мм от концов шкалы. [c.336]
Круглость наружной (I) и внутренней 2) поверхностей, плоскостности (прямолинейности) торцовой поверхности 2, 3), шероховатость поверхности
[c. 724]
Допуск плоскостности поверхности (А) 0,02 мм на площади 100 X 100 мм [c.123]
Допуск плоскостности поверхности 0,06 мм [c.119]
Отклонение формы плоских поверхностей (сы. рис. 7.1, а)—отклонение от плоскостности равно наибольшему отклонению А. Частными видами отклонений от плоскостности являются выпуклость (см. рис. 7.1, в) и вогнутость (см. рис. 7.1, г). [c.90]
Поверхности направляющих Скорость. Допуск плоскостности на 100 мм, мкм [c.239]
Допуск плоскостности поверхности 0,1 мм. [c.86]
Допуск плоскостности поверхности 0,1 мм на площади 100 х 100 мм. [c.86]
Допуск плоскостности поверхностей относительно общей прилегающей плоскости о, 1 мм. [c.86]
Допуск плоскостности каждой поверхности 0,01 мм. [c.87]
Суммарный допуск параллельности и плоскостности поверхности относительно основания о, 1 мм. [c.94]
Инди-рон позволяет записывать круглограммы в полярных координатах с увеличением от 400 до 50 000 на диаграммных дисках с шириной поля 50 мм. Точность вращения шпинделя, по данным фирмы, характеризуется погрешностью, равной приблизительно 0,04 мкм. С помощью прибора можно также контролировать концентричность и соосность наружных и внутренних поверхностей, плоскостность, непараллельность, неперпен- [c.161]
Особенность этих приборов состоит в том, что при записи круглограммы не требуется точно центрировгггь деталь на предметном столе, так как эксцентриситет исключается из записи самим прибором электрическим способом. Например, с помощью кругломера модели Индри-рон фирмы Бендикс можно записывать круглограммы в полярных координатах с увеличением от 400 до 50 ОООХ на диаграммных дисках с шириной поля 50 мм. Точность вращения шпинделя, по данным фирмы, характеризуется погрешностью, равной приблизительно 0,04 мкм. С помощью прибора можно также контролировать концентричность и соосность наружных и внутренних поверхностей, плоскостность, непараллельность, неперпендикулярность и т. п. Скорость вращения шпинделя изменяется в пределах от 0,4 до 12 об мин. С помощью фильтров можно регулировать частотную характеристику прибора четырьмя ступенями так. что на круглограмме регистрируются с уменьшением не более [c.488]
Поверхности плоскостно-шероховатые (с заметной окисной пленкой после эксперимента) [c.127]
На плоскостном изображении диаграммы (см. рис. 120) температурной оси мет. Можно проследить последовательно за процессом кристаллизации, не отмечая, при какой температуре, какая фаза начинает кристаллизоваться. Если на диаграмму нанести линии, соответствующие о.динаковым температурам (изотермы), т. е. линии, которые представляют собой пересечения горизонтальных (изотермических) плоскостей с поверхностями диаграммы, то можно будет с некоторым приближением судить о температурах превращения. [c.152]
Нижнюю опорную поверхность плиты обрабатывают грубо. Поверхности плиты, служащие базой для установки других деталей, обрабатывают боле( точно, чтобы получить меньшие отклонения от плоскостности и свести к минимуму деформации деталей при их закреплении на плите. Для крепления устанавливаемых на плите узлов 1тре-дусматривают резьбовые отверстия. [c.316]
Ширину Ь поверхности трения кольца 1 принимают при диаметре вала (мм) свыше 20 до 40 — 3 мм, свьпие 40 до 80—4 мм и свыше 80— 5 мм. Ширину поверхности трения кольца Сделают больше Ь на 2…4 мм. Рабочие поверхности уплотнительных колец должны иметь отклонения от плоскостности не более 0,9 мкм, а шероховатость Ка [c.182]
К обработке нижней опорной поверхности плиты особых требований не предъявляют. Поверхности, служащие базой для установки сопряженных с плитой узлов, обрабатывают точно, иобы получить меньшие отклонения от плоскостности и уменьшить деформирование узлов при их закреплении на плите. [c.339]
Проверка плоскостности обрабатываемых поверхностей производится с помощью поверочных плит и линеек на краску (по числу пятен). Поверочная плита покрывается краской и при соприкосновении с шабреной поверхностью детали оставляет на последней в местах соприкосновения пятна краски. Число пятен краски, приходящееся на квадрат обработанной поверхности размером 25X25 мм , характеризует неровность поверхности. Так, для поверхности высокой точности (детали измерительных приборов и инструментов) число пятен должно быть 25—30 для поверхностей средней, обычной точности — 20—25 и для поверхностей пониженной точности — 12—20 пятен. [c.274]
В большинстве стандартных систем допуски размеров определяются на основе единицы допуска /, зависящей от номинального размера D. Для гладких цилиндрических соединений размером 1. .. 500 мм единица допуска, мкм i = 0,5 Yd (в общесоюзной системе ОСТ), i = 0,45 + 0,001D (в международной системе ISO), где D — среднее значение номинальных размеров, мм, для данного интервала, в пределах которого допуск принимают постоянным. Под номинальным размером понимают номинальный размер диаметра поверхности при определении допусков цилинд-ричности, круглости и профиля продольного сечения или размер наибольшей стороны плоской поверхности при определении допусков прямолинейности, плоскостности и параллельности поверхностей в зависимости от квалитета допуска размера. При составлении стандартизованных числовых значений допусков диапазона 1—500 мм отобрано 13 значений единиц допусков, равных ординатам средних геометрических значений интервалов до 3, 3—6, 6—10, 10—18, 18—30, 30—50, 50—80, 80—120,120—180,180—250, 250—315, 315—400, 400—500. [c.75]
I — угловые плитки с одним рабочим углом со срезанной вершиной (рис. 14.1, а) 11 — угловые плитки с одним рабочим острым углом (рис. 14.1,6) 111 — угловые плитки с четырьмя рабочими углами (рис. 14.1, в) IV — шестигранные призмы с иеравно.мерным угловым шагом V — многогранные призмы с равномерным угловым шагом (восьми- и двенадцатигранные). Угловые меры выпускают в виде набора плиток толщиной 5 мм с таким расчетом, чтобы из трех-пяти мер можно было составлять блоки в пределах от 10 до 90 , В зависимости от отклонения действительных значений рабочих углов от номинальных и отклонений от плоскостности измерительных поверхностей угловые меры изготовляют трех классов точности (0,1 и 2). Точность угла плиток в 1-м классе 10″, во 2-м — 30″. По точности аттестации образцовые угловые меры подра.зделяют на четыре разряда (1, 2, 3 н 4). Предельные погрешнссти аттестации рабочих углов не должны превышать для угловых мер 1-го разряда 0,5″ 2-го — 1″ 3-го — 3″ 4-го — 6″. Угловые меры собирают в блоки с помощью специальных державок. [c.171]
Поверхности, работающие под нагрузкой в условиях линейного или плоскостного контакта, целесообразно выполнять слегка выпуклыми, что обеспечивает центральное приложение нагрузки и устраняет повышенные кромочные давления, возникающие пз-за неточностей изготовления II монтажа. Этот прием, называемый бомбинированием, широко применяют для деталей, работающих под высокой нагрузкой в условиях трения или скольжения. [c.582]
На рис. 159, а показана ошибочная конструкция корпусной детали с консолью, подвергаемой обработке по плоскости ш. Консоль под усилием резания отгибается (вид б), а после обработки выпрямляется (вид в) плоскостность поверхности нарушается. При повышенной подат- [c.141]
Г) сталь горячекатаная, термически обработанная, травленая, толстолистовая, марки 20X13, группы поверхности МЗб, нормальной точности прокатки, с необрезной кромкой (HO i, нормальной плоскостности (ПН), размером 40 X XI 400×3000 мм [c.205]
Точность деталей проверяют универсальными инсгруметами и приборами дчя измерения длин, углов, некруглости, ще-[Х)ховатости поверхности и приборами для измерений отдельных деталей — зубчатых колес, резьб >1, по цпипников качения. К сложным проверкам огносят проверку прямолинейности и плоскостности, а также точности кинема гических цепей. [c.477]
Плоскостность плиты основания – Fluidbusiness
В течение последних нескольких лет у пользователей оборудования, которые ищут способы упростить установку оборудования, настройку и увеличить среднее время между сбоями остро встала проблема плоскостности плиты основания.Что такое плоская поверхность?
Обычная стальная плита основания для ANSI или стандартного промышленного насоса будет плоской с точностью 0,127 мм на 300 мм. К примеру, если расстояние между монтажной плоскостью насоса и двигателя будет составлять 1220 мм, то площадка двигателя может находиться на 0,508 мм ниже или выше площадки насоса. А если посадочная площадка будет протяженностью 300 мм, то на другом конце она может быть выше или ниже на 0,127 мм. Улучшенная плита основания для той же самой модели будет иметь 0,0508 мм на 305 мм, что меньше чем в 2 раза по сравнению с обычной плитой основания. Точность плит основания изготовленных по API стандарту составляет также 0,0508 мм. Некоторые заказчики задают плоскостность 0,0381 мм на 300 мм.
Преимущества
Плоская поверхность позволит монтажнику более эффективно выровнять плиту основания перед заливкой, а затем сделать центрирование двигателя и насоса за счет шиммирования опор двигателя. При попытке выровнять насос и вал двигателя с точностью 0,0508 мм (полное замеренное биение), проще начать это делать на ровной площадке, чем подкладывать разное количество прокладок под каждую опору двигателя. “Не плотно прилегающая опора”, где одна или более опор не имеют контакта с посадочной поверхностью, когда агрегат еще не прикручен (это должно исправляться за счет шиммирования, а не за счет затяжки болтов, что может привести к деформации корпуса двигателя).
Плоскостность и уровень
Плоскостность измерима. Во время производственного процесса плоскостность плиты основания измеряется путем присоединения индикатора с цифровой шкалой к шпиндельной головке, которая разжимает плиту основания таким образом, что она остается в свободном состоянии, и затем измеряются различные точки на фрезерованных поверхностях. Плоскостность это технологический допуск обработанной поверхности. Измерение и прием плоскостности делается в производственных точках.
Уровень представляет собой “состояние” или “условие”. На месте установки, монтажники используют точный уровень и клинья (или винты для горизонтальной установки), чтобы привести плоскую поверхность монтажных площадок плиты основания к уровню в обоих направлениях (плита основания не будет изогнутой или перекошенной).
Ограничения
Существуют производственные ограничения, такие как точность фрезерного станка. Т.к. фрезы передвигаются по длине плиты основания, таким образом может быть достигнута только определенная плоскостность. Различная конструкция плит обладает разными возможностями сопротивляться деформациям во время механической обработки. Точно также, изготовленные плиты оснований могут иметь различные внутренние напряжения, которые могут послужить причиной деформаций формы во время ее обработки. Все плиты имеют некоторое количество деформаций и перед заливкой они должны быть должным образом выровнены. Правильное выравнивание очень важно, дабы в будущем избежать проблем с центрированием, и, следовательно, оптимизировать срок службы насоса.
Что делать?
- обзор спецификаций заказчика и любых требований к плоскостности плиты основания
- сравнение требований с опубликованной информацией интересующей модели насоса
- при необходимости, обсудить допуски со специалистом по продукту на заводе
- обсуждаемые опции включают в себя модернизацию плиты основания, подготовку для установки и выравнивания, эксплуатационное обслуживание для контроля и установочной сертификации, а также систему ProSmart™ для контроля состояния оборудования (например, неточное центрирование может стать причиной более высокой вибрации и может повлиять на температуру подшипников)
Поговорим о плоскостности листа — ПРОМСТРОЙМЕТАЛЛ
Что значит это слово – плоскостность? Как ее измерить? На что влияет? В день знаний 1-го сентября мы решили ответить на все эти вопросы и освежить в памяти понятие “плоскостность”.
Что такое плоскостность?
Основные характеристики, которые определяют какой прокат подойдет именно под ваш производственный процесс, это его механические свойства, геометрия и форма, а так же качество поверхности.
Мы бы хотели чуть более подробно остановиться на форме. Один из важнейших параметров формы прокатного листа, это его плоскостность, а проще говоря, ровность. В реальной жизни мы редко сталкиваемся с идеально ровными поверхностями, но если представить себе, что такая поверхность есть, то идеально ровный лист будет соприкасаться с ней каждой точкой.
В ГОСТ 19904 закреплены 4 типа плоскостности: особо высокая, высокая, улучшенная, нормальная. А ГОСТ 26877 устанавливает нормы «волнистости» на 1 м листового проката.
На практике же требований ГОСТ уже становится недостаточно. Современное оборудование, в частности, лазерные и координатно-пробивные станки, очень чувствительны к любым неровностям материала, поэтому при производстве на них используются только прокатные листы повышенной плоскостности.
Из-за чего появляются неровности?
Причины, по которым прокатный лист приобретает на своей поверхности волны и складки, могут возникнуть на любом этапе производства. Чаще всего дефекты появляются из-за действия термических напряжений при нагреве/остывании листов и из-за неравномерного распределения вытяжек по ширине очага деформации во время прокатки. Но так же травмировать лист может внешнее воздействие при резке или неправильная транспортировка. И если вторую группу причин можно, условно, отнести к человеческому фактору и на нее довольно легко повлиять, то основные причины нарушения плоскостности относятся непосредственно к производственному процессу.
Корень причин, из-за которых возникает деформация, лежит в самом процессе изготовления прокатного листа. После отливки метал, застывает неравномерно, что приводит к появлению внутреннего напряжения в заготовке. Поэтому, во время раскатки, какие то части листа проще поддаются воздействию, а какие то тяжелее. Чтобы это явление было проще понять, вспомните, как ведет себя тесто при раскатывании или даже можете провести небольшой эксперимент. Если взять прямоугольный кусочек теста и попробовать его сделать тоньше, не потеряв при этом форму, то даже если вы обеспечите максимально равномерное давление при раскатывании, то тесто будет распределяться неравномерно. Конечно, сталь это далеко не тесто и технологии обработки совершенно другие, но принципы того, как ведет себя материал, примерно такой же.
Как измерить плоскостность?
Для контроля плоскостности листа во время производства можно использовать контактные и бесконтактные методы. Контактные методы подходят только для холодной прокатки и могут травмировать поверхность листа в процессе замера, но дают более точный результат. Бесконтактный способ измерения менее точен, но может быть применен как для холодного, так и для горячего проката.
Принцип контактного измерения предельно прост: нужно сравнить поверхность листа с идеально ровной поверхностью. Такой поверхностью может быть уровень жидкости, луч света, поверочные плиты и линейки и т.д.
Самый простой и распространенный способ это измерение при помощи лекальной линейки и светового луча. Источник света нужно расположить перпендикулярно листу, затем поставить на лист лекальную линейку и оценить наличие просветов по линии соприкосновения листа с линейкой. Чем их меньше, тем более ровный перед вами лист.
Бесконтактное измерение же чаще всего заключается в обнаружении механического напряжения, о котором мы уже упоминали, при помощи магнитов, индукционных катушек или радиолокационных датчиков.
Если дефект плоскостности обнаруживается в процессе проката, то необходимо принять меры по стабилизации процесса прокатки. Говоря проще, где то чуть сильнее надавить, а где то наоборот.
Равнение на Промстройметалл
В нашей компании очень строго следят за качеством продукции на протяжении всего производственного процесса. Ключевой этап контроля качества происходит перед рубкой. Каждый рулон прокатывается через гидравлическую листоправильную машину. Если на листе остается дефект, то такой лист отбраковывается и не попадает в рубку.
И, напоследок, мы пользуемся защитной пластиковой упаковкой, чтобы избежать травмирования листа при транспортировке.
Помимо эстетической составляющей, качественный ровный лист позволит вам увеличить производительность на станке, избежать поломки узлов оборудования, брака при изготовлении деталей, а значит, сэкономит время и деньги.
Публикация “Плоскостность” — ЗАО «Балтийская нержавеющая сталь» Санкт-Петербург
АО «БНС» разработало и внедрило уникальные технологические режимы производства горячекатаных плит стали 08Х18Н10Т и 12Х18Н10Т, обеспечивающие минимальные отклонения от плоскостности.
Горячекатаные толстые листы и плиты из нержавеющей стали 08Х18Н10Т и 12Х18Н10Т предназначены, как правило, для дальнейшей механической обработки и сварки при производстве различных изделий в энергетическом и химическом машиностроении, в судостроении, резервуаростроении и других отраслях промышленности. Для уменьшения металлоёмкости конструкций наряду с точностью геометрических размеров заготовок важнейшее значение имеет отклонение от плоскостности, которое определяется как максимальное расстояние от любой точки поверхности изделия до прилегающей контрольной линейки в пределах заданного участка. Обычно контрольная линейка имеет длину 1 метр и ею определяют отклонения от плоскостности в любых направлениях на поверхности листа.
Поверхность считается абсолютно ровной, когда все точки измерений располагаются в одной плоскости. Несмотря на совершенство современной металлообрабатывающей техники, добиться таких показателей практически невозможно, поэтому в определении ровности поверхности речь идет о значениях, в пределах которых должны находиться все точки измерений. В зависимости от величины допусков, выделяют четыре основных класса плоскостности листового проката: ПО — особо высокая плоскостность стали; ПВ — высокая плоскостность; ПУ — улучшенная; ПН — нормальная.
Отклонениями от плоскостности называют выпуклости, вогнутости, волнистость, прогиб и другие дефекты поверхности. Их величина регламентируется и в стандартах, и в технических условиях на поставку плоского проката. В табл. 1 приведены требования к этому показателю качества некоторых нормативных документов для нержавеющей стали 08Х18Н10Т и 12Х18Н10Т.
Таблица 1 – Отклонения от плоскостности листового проката стали 08Х18Н10Т и 12Х18Н10Т
Нормативный документ |
Группа качества |
Отклонение от плоскостности, мм, не более |
Толщина проката, мм |
Расположение контрольного участка длиной 1 метр на листе |
|
Обозначение |
Название |
||||
ГОСТ 7350 – 77 |
Сталь толстолистовая коррозионностойкая, жаростойкая и жаропрочная |
ПО |
5 |
<6 |
В любом месте |
ПВ |
8 |
6 – 50 |
В любом месте |
||
ПУ |
10 |
6 – 50 |
В любом месте |
||
ПН |
12 |
6 – 50 |
В любом месте |
||
ОСТ 108.109. 01 – 95 |
Заготовки корпусных деталей из коррозионностойких сталей аустенитного класса |
ПВ |
8 |
40 – 250 |
В любом месте |
Спецификации АО «БНС» на поставку толстых листов и плит |
ПО* |
2 |
40 – 100 |
На расстоянии до 250 мм от боковых кромок |
|
3 |
40 – 100 |
В любом месте |
|||
ПО |
5 |
10 -250 |
В любом месте |
||
ПВ |
8 |
10 -250 |
В любом месте |
(ПО* — особо высокая плоскостность стали – сверх требований ГОСТ к группе качества ПО)
Чем шире и длиннее лист, тем труднее обеспечить заданную плоскостность на всех технологических операциях: при прокатке, охлаждении проката, при термической обработке и правке. Обеспечение минимальных отклонений от плоскостности на всех технологических операциях позволяет получить готовый лист необходимого качества.
АО «БНС» разработало и внедрило в условиях ЛПЦ-3 ПАО «Северсталь» технологические режимы нагрева непрерывнолитых слябов и листовых слитков стали 08Х18Н10Т и 12Х18Н10Т перед прокаткой, режимы деформации на реверсивном толстолистовом стане 5000 и последеформационного охлаждения толстых листов и плит, термической обработки и правки, обеспечивающие минимальные отклонения от плоскостности. Технологический процесс исключает большие степени деформации при правке, так как правка с большими степенями деформации во время изгиба способствует возникновению значительных остаточных напряжений, которые при последующей механической обработке со снятием поверхностного слоя или с обрезкой кромок в листе создают недопустимые отклонения от плоскостности. Горячекатаные толстые листы и плиты стали 08Х18Н10Т и 12Х18Н10Т, произведенные АО «БНС», характеризуются минимальными отклонениями от плоскостности, обеспечивающими наряду с высокой точностью геометрических размеров по толщине минимальный расход металла в стружку у потребителя металла. Повышается технологичность процессов сварки и механической обработки толстых листов и плит.
За последние три года АО «БНС» произведено более 4000 тонн горячекатаных плит стали 08Х18Н10Т и 12Х18Н10Т с особо высокой плоскостностью в основном для строящихся АЭС. От потребителей металла получены положительные отзывы.
Учитывая большие технические трудности при обеспечении желаемой потребителями плоскостности толстолистового проката, ни один стандарт не оговаривает требования к этому показателю качества на всю длину и ширину листа. Однако АО «БНС» разработаны технологические процессы, позволяющие производить плиты толщиной 40 – 100 мм стали 08Х18Н10Т и 12Х18Н10Т с отклонениями от плоскостности не более 5 мм на всю длину до 4 метров и всю ширину листа до 4 метров. Произведено более 200 тонн такого проката для АЭС и от потребителей металла также получены положительные отзывы.
Главный металлург, к.т.н. А.Н.Тумко
АО «БНС» (с)
Плоскостность– Основы GD&T
Символ:
Относительно базы: Нет
Применимо MMC или LMC: Да – Новое в 2009 году
Обозначение на чертеже:
Описание:Плоскостность GD&T очень проста. Это общий символ, указывающий на то, насколько плоская поверхность независимо от любых других базовых данных или элементов. Это полезно, если на чертеже должен быть определен элемент, который должен быть равномерно плоским, без увеличения каких-либо других размеров на чертеже.Допуск плоскостности ссылается на две параллельные плоскости (параллельные поверхности, на которой он вызывается), которые определяют зону, в которой должна лежать вся справочная поверхность. Допуск плоскостности всегда меньше связанного с ним допуска на размер.
Зона допуска:Два набора параллельных плоскостей, на которых должна лежать вся ссылочная поверхность.
Измерение / измерение:Плоскостность может быть измерена с помощью высотомера, проходящего по поверхности детали, если только опорный элемент удерживается параллельно.Вы пытаетесь убедиться, что любая точка на поверхности не выходит за пределы зоны допуска. Современные КИМ лучше всего подходят для измерения детали, поскольку они могут создавать виртуальные плоскости, с которыми можно сравнивать истинный профиль поверхности. Это трехмерное измерение, поэтому точки должны быть измерены по длине и ширине детали, чтобы гарантировать, что вся поверхность находится в пределах допуска. Плоскостность нельзя измерить, просто поместив деталь на гранитную плиту и проведя над ней высотомер или микровысотный прибор. Вместо этого это будет измерение параллельности, поскольку вы фиксируете нижнюю часть детали в качестве базы.
Связь с другими символами:Плоскостность – это трехмерная версия прямолинейности поверхности – вместо зоны допуска между двумя линиями ; зона допуска существует между двумя плоскостями .
Когда используется:Когда вы хотите ограничить количество волнистости или отклонения на поверхности без ужесточения допуска на размер указанной поверхности. Обычно плоскостность используется для обеспечения равномерного износа поверхности или для надлежащего уплотнения сопрягаемой детали.Обычно используется на приспособлении, которое должно стыковаться заподлицо с другой деталью без раскачивания, но где ориентация не важна.
Пример:Если вы хотите убедиться, что столешница идеально плоская, если у вас нет обозначения плоскостности, вам придется очень сильно ограничить высоту стола, чтобы убедиться, что вся поверхность прямой. Благодаря плоскостности вы можете сделать стол ровным, не сильно ограничивая толщину столешницы. (Вы бы отклонили таблицы с хорошей толщиной и обычно соответствующие спецификации, если используете GD&T)
Плоскостность Пример 2 Таблица без GD&T
Таблица с использованием символа плоскостности GD&T
Заключительные примечания:Плоскостность не то же, что и параллелизм.Параллельность использует базу для управления поверхностью, а плоскостность – нет. Представьте себе стол с двумя отсутствующими ножками, расположенными под углом к полу. Столешница может находиться в пределах допуска по плоскостности, но не должна быть параллельна полу.
, автор Tommy, 3 ноября 2014 г.
Будьте ведущим инженером в своей компании
Изучите GD&T в удобном для вас темпе и с уверенностью примените его в реальном мире.
Пройдите обучение GD&T.Плоскостность – поверхность по сравнению с элементом размера
В этом видео Брэндон обсуждает разницу между измерением плоскостности поверхности и плоскостности элемента размера (FOS).
Плоскостность поверхности
Плоскостность поверхности – это тип плоскостности, который знаком большинству людей. На чертеже обозначение плоскостности может указывать прямо на поверхность со стрелкой-выноской или выходить за пределы поверхности в сторону от элемента размера. Как вы можете видеть на рисунке 1, требования к плоскостности поверхности не соответствуют размеру. Заметка о расположении символа плоскостности имеет решающее значение для определения того, требуется ли плоскостность для поверхности или элемента размера (FOS).
Рисунок 1: Плоскостность поверхности на чертежеПлоскостность поверхности просто определяет, насколько плоской должен быть элемент поверхности, и является условием того, чтобы она была чисто плоской. Зона допуска плоскостности – это 3D-зона допуска, что означает, что при проверке плоскостности поверхности вы проверяете величину отклонения вверх и вниз по оси Y по всей плоскости. На рис. 2 показана зона допуска для плоскостности поверхности, обозначенная на чертеже на рис. 1.
Рисунок 2: Зона допуска плоскостности поверхностиНа рисунке 2 измеряемая поверхность показана красным цветом.Допуск считается, если все точки на поверхности лежат в пределах поля допуска 0,05. Поперечное сечение, показанное на рисунке 2, показывает, что до тех пор, пока поверхность находится между двумя параллельными плоскостями зоны допуска, требование плоскостности выполняется.
Плоскостность элемента размером
Плоскостность элемента размера (FOS) отображается с использованием того же символа плоскостности, что и для плоскостности поверхности. (Имеется только один символ плоскостности.) Плоскостность элемента размера указывается на чертеже, если обозначение плоскостности прямо совпадает с элементом размера.Как видно на рисунке 3, требование плоскостности ставится непосредственно под требование размера.
Рисунок 3: Плоскостность элемента размераПлоскостность элемента размера определяется путем сначала получения производной средней плоскости элемента, а затем проверки того, что полученная средняя плоскость находится в пределах допустимой зоны допуска. Плоскостность производной средней плоскости (плоскостность DMP) применяется к объектам, которые, как мы знаем, будут иметь изгиб, например, к большому листу металла. Его можно использовать только для плоских элементов такого размера, как пластины, выступы и пазы.
Зона допуска плоскостности элемента размера также является зоной допуска 3D. Чтобы плоскостность элемента находилась в пределах допуска, его производная средняя плоскость должна находиться в пределах зоны допуска. На рисунке 4 показана зона допуска для элемента размера, показанного на рисунке 3. Две параллельные плоскости, показанные синим цветом, указывают зону допуска, а полученная средняя плоскость показана красным.
Рис. 4. Зона допуска для элемента размераДва момента, на которые следует обратить внимание о плоскостности элемента размера (плоскостность DMP) по сравнению с плоскостностью поверхности:
- Плоскостность, применяемая к элементу размера, автоматически отменяет Правило № 1 GD&T.(Правило № 1 все еще действует для плоскостности поверхности.)
- Плоскостность для элемента размера (плоскостность DMP) может применяться независимо от размера элемента (RFS) или при максимальном состоянии материала (MMC). Чаще всего мы наблюдаем это в MMC. Если он находится в MMC, мы можем использовать функциональный датчик для его проверки. (Модификатор MMC нельзя использовать для определения плоскостности поверхности, потому что нет MMC поверхности.)
Сравнение измерений плоскостности
Плоскостность поверхности и плоскостность DMP можно измерить с помощью КИМ.На рисунке 5 показано, как можно определить плоскостность и плоскостность DMP для приведенных выше примеров с помощью КИМ.
Рис. 5. Плоскостность, измеренная с помощью КИМ.Плоскостность поверхности, измеренная с помощью КИМ, показана на рисунке 5 слева. Зонд КИМ измеряет и собирает точки на одной поверхности. Чтобы поверхность в нашем примере соответствовала допуску, все точки на поверхности должны лежать между двумя параллельными плоскостями, расстояние между которыми составляет 0,05.
Плоскостность элемента размера (плоскостность DMP), измеренная с помощью КИМ, показана на рисунке 5 справа.Зонд измеряет обе стороны детали, чтобы установить производные средние точки каждого поперечного сечения. Точки вычисляются и суммируются для производной медианной плоскости на основе внутренних расчетов программного обеспечения КИМ. Затем DMP сравнивается с зоной допуска двух параллельных плоскостей, которые в нашем примере разнесены на 0,05 друг от друга. Никакая часть DMP не может пересекать зону допуска; в противном случае деталь выйдет за пределы допуска.
от GD&T Basics 12 февраля 2021 г.
GD&T – ПЛОСКОСТЬ ‘CIRCLE 1’
ПлоскостностьВВЕДЕНИЕ
Рассмотрим две показанные поверхности. Какая поверхность идеально ровная? На самом деле нет идеально ровной поверхности. Как мы можем создать поверхность, которая не будет идеально плоской, но достаточно плоской, чтобы функционировать должным образом? Допуск контроля плоскостности .
КОНТРОЛЬ ПЛОСКОСТИ
Элемент управления плоскостностью (c) определяет, насколько поверхность детали может отклоняться от ее идеальной плоской формы.
Контроль плоскостности: Идеальная плоскостность – это когда все точки поверхности лежат в одной плоскости. Плоскость – это форма управления. Элемент управления плоскостностью (c) определяет, насколько поверхность реальной детали может отличаться от идеальной плоской плоскости.
Зона допуска: Зона допуска плоскостности – это объем между двумя параллельными плоскостями. Расстояние между параллельными плоскостями соответствует заявленному значению допуска контроля плоскостности .Контролируемая поверхность должна находиться в пределах объема, определенного зоной допуска.
Рамка управления функциями: Чтобы контролировать плоскостность поверхности, рамка управления элементом (FCF) используется для применения допуска к желаемой поверхности.
Чтобы применить контроль плоскостности к поверхности, FCF может указывать на поверхность или может указывать на нее или опираться на нее. выносная линия, идущая от поверхности.FCF размещается на виде, на котором поверхность рассматривается как линия. FCF, показанный ниже, применяет допуск плоскостности ко всей поверхности. Эта поверхность должна лежать между двумя параллельными плоскостями, расстояние между которыми составляет 0,2 мм.
ИСПОЛЬЗУЕТ
Контроль плоскостности используется для обеспечения лучшего контакта между сопряженными частями, или когда необходимо использовать прокладку или уплотнение. Он также используется для ограничения точечной коррозии и волнистости поверхности.
ПРОВЕРКА
Контроль плоскостности можно проверить следующим образом:
- Поверхность деталей размещается на поверхностной пластине. Эта поверхностная пластина представляет собой одну из плоскостей зоны допуска контроля плоскостности.
- Циферблатный индикатор помещается в отверстие в пластине поверхности и измеряет расстояние от поверхности пластин к поверхности деталей.
- Когда деталь вращается, измерительный инструмент должен поднимать или опускать деталь, и профиль цилиндра фиксируется.
- Поверхность детали произвольно перемещается по отверстию. Если в любой момент FIM (полное движение индикатора) больше чем допуск контроля плоскостности, деталь не соответствует спецификациям.
GD&T, определение геометрических размеров и допусков, GD&T, плоскостность, круглость, допуск плоскостности, допуск круглости
Прямолинейность на плоской поверхности показана ниже;
Плоскостность:
Плоскостность – это состояние указанной поверхности, в которой все элементы находятся в одной плоскости.Допуск плоскостности обеспечивает зону допуска указанного и определяется двумя параллельными плоскостями, в которых должна лежать указанная поверхность. Плоскостность применяется к отдельной поверхности, допуск плоскостности не обязательно связывать с датумом. Рамка элемента управления крепится к поверхности с помощью выноски или удлинителя. линия. Когда функция рамка управления с допуском плоскостности применяется к размеру размера, допуск плоскостности применяется к средней плоскости для нецилиндрических поверхности.Полученная медианная плоскость состоит из средней точки фактического локального размера. Средняя плоскость не обязательно квартира. Плоскостность Допуск может использоваться для управления формой производной средней плоскости. Также допуск прямолинейности можно использовать для управления формой производной линии.
Поверхность должна лежать между двумя плоскостями на расстоянии 0,004 друг от друга, а указанная поверхность должна находиться в пределах указанный предел допуска размера.
Круглость:
Круглость – это состояние поверхности детали.Допуск округлости используется для контроля округлости круглых деталей или элементов. Круглые элементы могут быть обозначены цилиндрами, сферами и конусами. Допуск круглости контролирует каждый круговой элемент цилиндра независимо друг от друга. Допуск круглости применяется к отдельной поверхности, допуск круглости не обязательно должен быть связан с ДАТУМ. Допуск круглости Производственная деталь указывает, где все точки поверхности круглой детали должны лежать в зоне, ограниченной двумя концентрическими окружностями, радиусы которых различаются. по значению допуска концентричности.
Указанная поверхность должна быть обработана с заданным полем допуска в пределах 0,005
Как оценить плоскостность в GD&T | Статья
.В этом посте мы рассмотрим несколько методов оценки плоскостности в GD&T и определим, какой из них является оптимальным.
Плоскостность – это допуск формы GD&T, который концептуально прост. Согласно стандарту ASME Y14.5 , он «определяет зону допуска, определяемую двумя параллельными плоскостями, внутри которых должна лежать поверхность.”
Рис. 1. Пример плоскостности ASME GD&T
Рисунок 1 очень хорошо иллюстрирует эту концепцию. Вверху мы видим чертеж с допуском плоскостности 0,25 единицы. Согласно стандарту это означает, что верхняя поверхность должна полностью лежать между двумя параллельными плоскостями, расстояние между которыми не превышает 0,25 единицы. Представьте, что поверхность как можно плотнее располагается между двумя параллельными плоскостями; допуск прошел бы, если бы вы могли собрать их ближе, чем 0,25 единицы.Важно отметить, что две параллельные плоскости не обязательно выровнены ни с чем, как мы можем видеть в примере внизу рисунка 1.
Использование высотомера для оценки плоскостности
Рис. 2. Высотомер на колоннах, установленный для оценки плоскостности
В приложении один из способов физического измерения плоскостности – использовать высотомер, как мы видим на рисунке 2. Для правильного использования высотомера измеряемая деталь сначала помещается на 3 колонны с регулируемой высотой.Затем высотомер проводится по поверхности, глядя на амплитуду иглы. Метролог регулирует три колонки, чтобы минимизировать амплитуду стрелки. Они корректируют ориентацию самолета, чтобы получить самый маленький теоретический бутерброд. Как вы понимаете, этот метод требует большого терпения и тренировки.
Рис. 3. Использование высотомера с деталью, расположенной непосредственно на поверхности, может привести к ложным отрицательным результатам.
Более распространенный метод использования высотомера для оценки плоскостности заключается в размещении детали непосредственно на столе (рис. 3).Однако без возможности регулировать ориентацию детали, чтобы минимизировать амплитуду иглы, вы, по сути, оцениваете параллельность на основе таблицы, что является неоптимальным. Хотя это намного быстрее, чем использование метода с тремя столбцами, важно знать, что использование этого метода может привести к ложноотрицательным результатам; детали, прошедшие эту оценку, всегда верны, но детали, которые не выдерживают испытания, необходимо оценивать другим способом, чтобы гарантировать, что хорошие детали не будут отправлены обратно для дорогостоящей переделки.
Оценка плоскостности цифровыми методами
Рис. 4. Поверхность с допуском плоскостности GD&T 0,57 единиц
Давайте посмотрим на пример. У нас есть поверхность с допуском плоскостности GD&T 0,57 единицы (рис. 4). В цифровой сфере, если вы проводите измерения с помощью КИМ (переносной или другой), программное обеспечение имеет два метода оценки плоскостности: наилучшее соответствие или минимальная зона.
Рис. 5. Плоскость наилучшего вписывания, рассчитанная по нашему облаку точек
Наилучшее соответствие, также известное как плоскость среднеквадратичного отклонения, представляет собой уравнение, которое оптимально вписывает плоскость в ваше облако точек, находит среднее значение и минимизирует влияние любых выбросов (рис. 5).Затем алгоритм вычисляет максимальное отклонение выше и ниже подобранной плоскости, создает две параллельные теоретические плоскости, которые проходят через эти отклонения, и вычисляет расстояние между ними. Это используется для оценки допуска, как вы можете видеть на рисунке 6.
Рисунок 6. Плоскость наилучшей посадки с отклонениями в 0,6121 единицы. Алгоритм вычисляет максимальное отклонение выше и ниже подобранной плоскости, отмеченной как Point_High_BF и Point_Low_BF. Он создает две параллельные теоретические плоскости (серые), которые проходят через эти отклонения, и вычисляет расстояние между ними
Подобно использованию высотомера без регулируемых колонн, Best Fit является неоптимальным методом оценки плоскостности в GD&T.Он также склонен к ложным отрицаниям. Это означает, что возможна поломка деталей, которые прошли бы проверку, если бы плоскостность была оценена правильно. В нашем примере допуск плоскостности для этой плоскости составляет 0,57 единицы. При использовании метода оценки плоскостности наилучшего соответствия отклонения составляют 0,6125 единиц, что приводит к тому, что деталь не проходит оценку. Это ложноотрицательный результат. Это связано с тем, что плоскость наилучшего совпадения, созданная алгоритмом, не обязательно параллельна двум идеальным плоскостям, внутри которых должна лежать поверхность в соответствии со стандартом GD&T ASME.Ориентация плоскости Best Fit заблокирована, что лишает алгоритм возможности настраивать сэндвич для минимизации отклонений. Этот метод исторически использовался метрологическим программным обеспечением, поскольку он был надежным, быстрым и менее трудоемким в вычислениях. Однако с современными вычислительными возможностями теперь у нас есть возможность использовать гораздо лучший метод: минимальная зона.
Рисунок 7. Оценка минимальной плоскостности зоны с отклонениями 0,5419 единиц.
Метод минимальной зоны для оценки плоскостности в GD&T на сегодняшний день является наиболее точным, так как он наиболее близок к стандарту ASME.Выше (рис. 7) мы видим, что программа создала две теоретические параллельные плоскости зеленого цвета, чтобы максимально плотно расположить точки между собой. Используя тот же пример поверхности, что и выше, расстояние между двумя плоскостями составляет 0,5419 единицы, что соответствует нашему допуску в 0,57 единицы.
Ниже на рис. 8 показаны различия в ориентации сэндвичей при оценке плоскостности с помощью методов наилучшего совмещения и минимальной зоны.
Рис. 8. Сравнение оценок плоскостности оптимальной и минимальной зон показывает разницу в ориентации плоскостей, используемых для расчета сэндвича.В нашем примере вы также можете видеть, что при каждом расчете были выбраны разные высшие точки.
Заключение: Как следует оценивать плоскостность в GD&T?
С появлением цифровых методов оценки GD&T с использованием портативных КИМ и передового программного обеспечения для 3D-метрологии, нет причин продолжать использовать неоптимальные или трудоемкие методы. Использование наилучшего вписывания для оценки плоскостности не дает значительных преимуществ в скорости или ресурсах. Минимальная зона – это оптимальный метод, поскольку он соответствует стандарту и имеет дополнительное преимущество, заключающееся в невозможности отправки хороших деталей на дорогостоящую переделку.
Артикул
.Производство
Контроль и проверка качества
Аэрокосмическая промышленность
Автомобильная промышленность
Программное обеспечение – Метрология и контроль качества
BuildIT Метрология
Контроль и инспекция качества (БП)
Адвокат
Плоскостность [символ, допуск, измерение]
Символ плоскостности GD&T
Определение плоскостности
Символ плоскостности GD&T указывает на то, насколько плоская поверхность.Он не зависит от каких-либо других баз или элементов. Плоскостность – это элемент управления формой, потому что он используется для управления формой или формой элемента. Он контролирует, насколько поверхность детали может отклоняться от идеальной плоскости.
Зона допуска для допуска плоскостности основана на двух параллельных плоскостях. Один находится на пике самой высокой неровности поверхности. Другой лежит в самом глубоком желобе любой неровности поверхности. Контролируемая поверхность должна полностью лежать в пространстве между двумя плоскостями.Расстояние между этими двумя плоскостями – это плоскостность поверхности.
Поскольку плоскостность уточняет поверхность, ее можно использовать в стеке допуска.
Плоскостность в сравнении с параллельностью
Эти два часто путают, но на самом деле они совершенно разные. Параллелизм использует датум для управления поверхностью, но нет никаких базовых данных, связанных с плоскостностью. Поверхность может находиться в пределах допуска плоскостности, но не параллельна любой другой поверхности или исходной точке.
Прямолинейность и плоскостность
Думайте о прямолинейности как о двухмерном эквиваленте плоскостности.В то время как плоскостность измеряется по плоскости, прямолинейность измеряется по линии.
Измерение плоскостности
Плоскостность обычно измеряется проведением индикатора, зонда или другого датчика по поверхности. Развертка должна располагаться в плоскости, параллельной желаемой плоскости измерения плоскостности.
Один из способов выполнить это измерение – поместить циферблатный индикатор так, чтобы его наконечник выходил через отверстие в пластине на поверхности. Поместите измеряемую поверхность лицевой стороной вниз на пластину и проведите ею по наконечнику индикатора.Диапазон хода индикатора должен быть меньше указанного допуска плоскостности.
Плоскостность чертежей
Использование плоскостности на чертеже…
Использовать плоскостность в чертеже просто. Просто назовите допуск на плоскостность в рамке управления функцией со стрелкой, обозначающей контролируемую поверхность. Рамка управления элементом «Плоскостность» может также опираться на выносную линию для измерения поверхности.
Плоскостность и чистота поверхности
Плоскостность и чистота поверхности обычно имеют совершенно разные масштабы, причем чистота поверхности является гораздо более тонкой шкалой.Большинство измерений шероховатости поверхности являются средними значениями, а плоскостность – наихудшим случаем.
Щелкните, чтобы посетить нашу справочную страницу для получения дополнительной информации о поверхностной обработке.
GD&T Оглавление Символы GD&T
Влияние плоскостности зеркальной поверхности лазера
Для лазерных системчасто требуются очень точные оптические компоненты, такие как зеркала и линзы, со спецификациями, приближающимися к пределам возможностей производства. При создании оптической системы, в которой будет использоваться лазер, важно руководствоваться ожиданиями в отношении того, что будет производиться по желаемой цене.Понимание того, какие факторы производительности являются решающими, а какие – желательными, но ненужными, может сэкономить время и деньги. В зависимости от области применения для лазерной системы могут потребоваться или не потребоваться высокопроизводительные специальные оптические компоненты. В данной заметке по применению будет продемонстрирован этот момент путем изучения смоделированных эффектов плоскостности поверхности зеркала на размер сфокусированного пятна входного гауссовского лазерного луча, распространяющегося через смоделированную систему обработки лазерных материалов.
Это указание по применению имеет значение для любой лазерной системы, включая одно или несколько лазерных зеркал.Чтобы максимизировать эффективность лазерной системы, лазерные зеркала обычно покрываются ионно-лучевым напылением (IBS) покрытиями или покрытиями из испарения. Покрытия IBS являются популярными типами зеркальных покрытий из-за их чрезвычайно высоких спектральных характеристик, что означает, что они могут достигать очень высоких коэффициентов отражения. Однако они создают очень высокое напряжение на поверхности, на которую они наносятся, потенциально деформируя поверхность зеркала, если не будет нанесено компенсирующее покрытие на задней стороне оптики или длительный отжиг.Испарительные покрытия оказывают небольшое напряжение на поверхность зеркала, но их спектральные характеристики ниже, чем у покрытий IBS. Хотя в этой инструкции по применению не рассматривается напрямую влияние покрытий, смоделированные кривизны зеркал приблизительно соответствуют кривизне, придаваемой зеркалам симметричными напряжениями покрытия IBS.
Оптические ограничения и рекомендации
Радиус кривизны
Плоскостность и кривизна поверхности относятся к форме поверхности зеркала.В то время как плоскостность поверхности – это отклонение поверхности от ее номинальной формы, кривизна определяется как величина, обратная радиусу кривизны (, уравнение 1, ).
(1) $$ C = \ frac {1} {R} $$
Поскольку это моделирование требует ввода радиуса кривизны R, он должен быть определен из нескольких других размеров и свойств зеркала. Сначала предполагается, что зеркало будет иметь сферическую кривизну, которая часто имеет место для напряженных покрытий, и что максимальный прогиб (сокращение от sagitta) будет точно равен плоскостности поверхности SF (, уравнение 2, ).
(2) \ begin {align} \ text {sag} & = \ text {SF} \ left [\ text {waves} \ right] \\ & = \ text {SF} \ left [\ lambda \ right ] \ end {align}
В случае, когда луч отражается от одного зеркала, плоскостность поверхности также будет равна ошибке отраженного волнового фронта или искажению волнового фронта. Плоскостность поверхности обычно указывается в единицах полос или волн, и, как таковая, плоскостность поверхности зеркала сообщается как положительная действительная доля или целое число, кратное длине волны света, используемого с зеркалом.2} {\ text {SF}} $$
Поскольку кривизна обратно пропорциональна радиусу кривизны, кривизна прямо пропорциональна плоскостности поверхности. Это важно различать, потому что кривизна зеркала будет изменена только путем изменения плоскостности поверхности в этом примечании по применению. Например, зеркало диаметром 25 мм имеет механический полудиаметр 12,5 мм. При светосиле 85% чистый полудиаметр ( ρ ) зеркала составляет 10,625 мм. При плоскостности поверхности λ / 10 и длине волны 1064 нм радиус кривизны составляет примерно 5.3 × 105 мм и кривизна 1,9 × 10-6 мм-1.
Предел дифракции
Предел дифракции сфокусированного пятна, описываемый уравнением диска Эйри, может использоваться для определения нижнего предела, при котором диаметр пятна луча может быть сфокусирован, обозначается как d и с учетом длины волны света λ, фокусное расстояние собирающей линзы f и размер или диаметр луча D. Этот нижний предел определяется исходя из предположения, что собирающая линза является идеальной параксиальной линзой без каких-либо аберраций (, уравнение 6, ).
(6) $$ d \ приблизительно 2.44 \ frac {f \, \ lambda} {D} $$
Например, лазерный луч с длиной волны 1064 нм и диаметром 5 мм, фокусируемый параксиальной линзой с фокусным расстоянием 100 мм, имеет диаметр пятна Эйри примерно 52 мкм. Луч света невозможно сфокусировать меньше без использования линзы с большей оптической силой, однако, поскольку идеальных параксиальных линз без аберраций на самом деле не существует, размер пятна, вероятно, будет больше, чем это значение. Уравнение диска Эйри просто обеспечивает нижний предел, известный как предел дифракции, до которого можно сфокусировать размер пятна.
Zemax OpticStudio Моделирование и результаты
Моделирование, используемое для проверки влияния кривизны зеркала на размер сфокусированного луча, было создано в Zemax OpticStudio 18.9. В модели используется гауссов пучок диаметром 2,5 мм с заданной длиной волны, проходящий через систему, состоящую из шести идентичных зеркал (имеющих одинаковый диаметр и плоскостность поверхности) и трех линз Edmund Optics, как показано на рис. 1 .
Рисунок 1: Эта смоделированная система расширителя луча включает шесть идентичных зеркал переменной кривизны, линзу PCV № 48-049 и линзу PCX № 48-281 в качестве 5-кратного расширителя луча и линзу PCX № 37-817 в качестве конденсорной линзы.
В этой модели зеркалам был задан механический полудиаметр 12.5 мм и прозрачный полудиаметр 10,625 мм в соответствии с соглашением, согласно которому чистая апертура для оптики должна составлять 85% от его диаметра. Этот диаметр был выбран для обеспечения того, чтобы пучок лучей находился в пределах прозрачной апертуры второй линзы в расширителе луча, хотя в реальных приложениях для этого размера луча будут выбраны гораздо большие диаметры, чтобы избежать ограничения гауссова луча. Расширитель луча 5X состоял из линз Edmund Optics № 48-049 и № 48-281. Зеркала 2–6 были размещены на расстоянии 50 мм друг от друга, чтобы складывать оптический путь, имитируя ограниченное пространство в реальной лазерной системе.Расстояние между двумя линзами, состоящими из расширителя луча, а также расстояние от последнего зеркала до линзы конденсатора были оптимизированы для фокусировки луча в конечной плоскости фокусировки, чтобы получить геометрические (GEO) размеры пятна для сфокусированного луча. при различной кривизне зеркал.
Для того, чтобы оценить размер пятна при разных значениях плоскостности поверхности, но на той же длине волны, плоскостность поверхности была определена как положительное действительное число, кратное длине волны, и это кратное значение было увеличено.Этот кратный коэффициент для простоты будет называться коэффициентом кривизны C ‘. Этот коэффициент кривизны, который является безразмерным значением, не следует путать с кривизной, которая является обратной величиной радиуса кривизны и имеет единицы длины, как указано в уравнении , уравнение 1, . Кривизна также может охватывать несколько величин, тогда как коэффициент кривизны, который может быть любым положительным числом, обычно составляет долю меньше 1. Таким образом, прогиб может быть представлен как длина волны света в системе λ, умноженная на коэффициент кривизны ( Уравнение 7 ).
(7) \ begin {align} C ‘& \ in \ mathbb {R} _ {\ geq 0} \\ \ text {SF} \ left [\ lambda \ right] & = C’ \\ \ text {SF} \ left [\ text {nm} \ right] & = C ‘\ times \ lambda \ end {align}
Соответствующие результаты для трех длин волн и девяти значений коэффициентов кривизны показаны в таблице 1 и на рисунке 2 .
| GEO Размер пятна (мкм) | ||||||||
Плоскостность поверхности (P-V) | 0λ | λ / 20 | λ / 10 | λ / 8 | λ / 4 | λ / 2 | 1λ | 2λ | 5λ |
1064 нм | 22.4 | 22,9 | 25,1 | 26,3 | 32,0 | 43,7 | 67,2 | 116,4 | 270,8 |
532 нм | 21,7 | 21,6 | 22,3 | 22,8 | 25,6 | 31,3 | 42,9 | 66,1 | 139,0 |
355 нм | 20,7 | 21,6 | 21,6 | 21,9 | 22.7 | 26,5 | 34,1 | 34,1 | 96,1 |
Рисунок 2 показывает, что размеры сфокусированного пятна для зеркал с плоскостностью поверхности λ / 20 в масштабе 300 мкм кажутся почти одинаковыми.По мере того, как плоскостность поверхности ухудшается, размеры сфокусированного пятна становятся больше, чем для более длинных волн. После выравнивания поверхности λ / 4 размер сфокусированного пятна начинает более заметно увеличиваться для всех длин волн.
Ключевые эффекты и рекомендации
На самом деле идеально плоских зеркал не бывает. При более высоком качестве характеристик плоскостности поверхности или уменьшении кривизны зеркала размер пятна увеличивается, а отраженный волновой фронт ухудшается. Когда профиль поверхности зеркала значительно отличается от его номинальной формы, может быть полезно сопоставить аберрации на поверхности с набором функций, называемых полиномами Цернике.В зависимости от точного профиля поверхности зеркала и углов, под которыми зеркала расположены по отношению к падающему лучу, эффекты аберрации от расположенных ниже по потоку линз и зеркал могут агрегироваться конструктивно или разрушительно.
В этой модели для простоты зеркала трактовались только как сферические или плоские. В результате профили балок стали менее круглыми и более разложенными. Однако важно отметить, что сферические аберрации изначально присутствовали в расширителе луча и линзах для фокусировки луча, и эти эффекты неизбежно переносились через систему и искажались из-за наклона и сферической кривизны зеркал.Поскольку эти взаимодействия являются сложными и могут быть потенциально аддитивными или вычитающими в зависимости от того, где размещены зеркала, для минимизации аберрационных эффектов и фокусировки пятна потребовалась оптимизация OpticStudio расстояния между линзами. Другой фактор, который не учитывался, – это использование оптических покрытий.
Также важно не упустить из виду то, как длина волны света в сочетании с кривизной зеркала влияет на размер и форму пятна. На больших длинах волн отклонения в размере и форме пятна больше и более выражены, чем на более коротких длинах волн (, рис. 3, ).
Рисунок 3: Размер сфокусированного пятна луча 1064 нм при увеличении коэффициентов кривизны в трех масштабах: 600 мкм (вверху), 200 мкм (в центре) и 100 мкм (внизу)Поскольку это моделирование было строго теоретическим, каждое зеркало и линза отражали и пропускали 100% падающего света соответственно. На самом деле в лазерных системах используются высокоэффективные отражающие покрытия для максимального увеличения коэффициента отражения зеркала и антибликовые покрытия для максимального пропускания линз.Эти покрытия, однако, имеют определенные длины волн или диапазоны длин волн и пороги лазерно-индуцированного повреждения (LIDT), которые необходимо учитывать для реальных систем.