ГОСТ 6133 99 основные технические характеристики
Содержание
- Разновидности блоков по ГОСТ
- Камень стеновой бетонный
- Состав блока
- Советы по выбору материала
- Параметры материала
- Маркировка блочного материала
- Порядок приемки, хранения и перевозки
- Заключение
Этот стройматериал пользуется популярностью, что объясняется особенностями его свойств и качественными характеристиками. Скорей всего, большинство частых застройщиков даже планировали вариант строительства из таких блоков. Как и в случае с иными строительными материалами, к керамзитобетону предъявлены некоторые требования. Поэтому сегодня разберемся, о чем гласят стандарты на керамзитобетонные блоки ГОСТ.
Разновидности блоков по ГОСТ
Керамзитобетон применяется для строительства стен. Подготовленная масса, отвечающая требованиям по определенным характеристикам, разливается по формам. После этого ей предоставляется время для застывания. Каждый элемент имеет внутри щели сквозного либо несквозного вида.
В соответствии с ГОСТ керамзитобетон разделяется на:
- Полнотелый. Внутри нет отверстий и щелей. Исключение – специальные отверстия для удобной переноски материала.
- Рядовой. Эти блоки нуждаются в последующей финишной отделке всей поверхности.
- Лицевые. Имеют декоративные покрытия на одну или две стороны. Используются в строительстве и в качестве облицовочного материала.
Отметим, что блоки, имеющие пазы, гораздо лучше соединяются, повышая показатели прочности всего сооружения.
ГОСТ на керамзитобетонные блоки устанавливает разделение материала по текстурным отличиям поверхности на:
- Колотые – поверхность элементов ровностью не отличается. Превышения могут достигать восьми миллиметров;
- Рифленые – блоки подвергаются обработке, поверхность сочетает впадины и выступы;
- Шлифованные – бока элемента шероховатые:
- Гладкие – покрытие со всех сторон одинаковое.
Камень стеновой бетонный
Технические характеристики керамзитобетонных блоков ГОСТ 6133 99 следующие:
- размеры (см) – 39 х 19 х 18.
8;
- вес блока – от 14 до 16 кг;
- показатель прочности при сжатии – М-35 В 2.5;
- устойчивость к морозам – F 25;
- способность проводить тепло – 0.43 Вт;
- по уровню радиоактивности – соответствует норме;
- значение плотности – от 950 до 1000 кг на м. куб;
- показатель плотности бетонной массы – от 1 250 до 1 300 кг на м. куб;
- категорируется по группе А-7.
Состав блока
ГОСТ 6133 99 керамзитобетонных блоков определяет, что для их изготовления используют определенное сырье. В стандартном исполнении блок состоит из песка, цементного состава, воды и керамзита, играющего роль пористого наполнителя.
Кроме этого, разрешается добавлять щебенку, алгопорит, гравий пемзовой или шлаковой группы.
Соотношения компонентов и их точная дозировка окажут прямое влияние на показатели изделия.
Советы по выбору материала
Есть несколько особенностей, которые необходимо учитывать, приобретая керамзитобетонный материал:
- ГОСТ на керамзитобетон определяет, что для изготовления используется портландцемент, марка которого не ниже М 400.
Дело в том, что нужную прочность может дать только он;
- если строительный материал планируется подвергать тепловой обработке, то применяется алитовый цемент;
- в производстве может быть использован песок кварцевый, который повышает прочность, гравий керамзитовый, не содержащий песчаных примесей, гидрофобный цементный состав, понижающий способность материала поглощать влагу.
Чтобы исключить понижение прочности керамзитобетонных блоков, пластификаторные добавки не применяются.
Параметры материала
ГОСТ 6133 99 на блоки керамзитобетонные определяет качество изделий. Только здесь можно найти все технические параметры, присущие блокам из керамзитобетона.
По своему предназначению материал используется в возведении наружных или внутренних стен, при облицовке готовых объектов. Исходя из назначения, блок может или одну лицевую поверхность, или две – с боку и с торца. ГОСТ «бетоны с керамзитом» определил, что лицевая сторона может обрабатываться разными способами. Шлифование блочной поверхности выполняют исключительно по предпочтению покупателя.
По оттенкам керамзитобетонный блок бывает без цвета либо окрашен в разные цвета за счет добавки специальных составов.
Каждый блок изготавливается в параллепипедной форме, но с учетом пожеланий заказчика формы могут варьироваться.
Торцевые части блоков могут быть гладкими, иметь пазы либо зазубрины. Элемент углового типа может выполняться по прямоугольной форме или иметь закругление. Масса одного блока, не зависимо от его вида, не должна превышать тридцати одного килограмма.
Когда рассматривается блок с пустотами, то его наружная стенка по толщине не должна быть менее двух сантиметров, что совпадает с размерами перегородок внутреннего типа. Как правило, такое требование распространяется на блоки, имеющие сквозные щели. Если пустоты несквозные, то внутренние перегородки по толщине могут быть около одного сантиметра.
Значение прочности сжатия для блока керамзитобетонного варьируется, составляя 50 – 300 для элементов из тяжелых бетонных составов, и 100 – 25 для материала из легкой бетонной массы.
Класс по устойчивости к морозам определяется для материалов, которые предназначены для возведения наружных стен, потому что воздействию холодных масс будут подвержены именно они.
Важное значение придается уровню огнестойкости. Керамзитобетонные блоки относятся к А 1. Это означает, что материал, подверженный воздействию открытого пламени, начинает разрушаться через семь – десять часов.
Хоть характеристики по качественному состоянию высокие, керамзитобетонные блоки запрещается применять в непосредственном контакте с почвенными составами.
Показатель паропроницаемости сегодня обладает особенным значением, определяющим окончательный выбор строительных материалов. Блоки из керамзитобетона значительно лучше проводят через свои пустоты воздушные потоки. Объект, построенный из этого материала, в помещениях будет отличаться комфортным климатом, даже когда уровень вентилирования будет недостаточным.
Для размеров существует два основных стандарта:
- стеновые – 39 х 19 – 18.
8 см;
- перегородочные – 39 х 9 х 19 см.
Маркировка блочного материала
Для правильного выбора керамзитобетонных блоков, рекомендуется разбираться в фирменной маркировке, которая в сокращенном виде обозначает главные технические параметры. Состоит она из определенного набора букв и цифр:
- сначала идет буква «К», которой определяется, что материал относится к группе камней искусственного происхождения;
- двумя последующими буквами определяется область применения материала (С, П, Л, Р – стеновые, перегородочные, лицевые, рядовые). Это очень удобно для заказчиков, кому необходима отделка;
- четвертая и пятая буквы означают предназначение блочного материала в кладке (УГ, ПР, ПЗ, ПС – угловые, порядочные, для перевязывания швов и пустотелые;
- число, следующее в маркировке за буквами, обозначает длину элемента;
- после всего следуют параметры по уровню прочности, устойчивости к морозам и показателю плотности.
Разбираясь в алгоритме чтения маркировки керамзитобетона, вы всегда найдете себе нужный для кладки материал.
Порядок приемки, хранения и перевозки
Кроме параметров физического и технического характера, ГОСТ устанавливает и такие правила.
Инструкция по приемке блоков гласит:
- блоки должны проходить контроль качества на производстве;
- прием ведется на основании заключений по испытаниям продукции на соответствие стандартам;
- максимальная партия не должна превышать 150 кубометров. В нее входят изделия, произведенные в течение одной смены, из одной сырьевой партии, аналогичные по качеству и свойствам;
- приемо-сдаточные испытания подразумевают проверку на сжатие, отпускную прочность, отклонения от геометрических параметров, прочие характеристики внешнего характера;
- к периодическим проверкам относятся испытания на проводимость тепла, морозоустойчивость, плотность и шумоизоляцию.
Для каждой партии оформляются сопроводительные документы на соответствие блоков качеству, содержащие в себе следующие данные:
- номер партии, день выпуска и оформления;
- номер ГОСТ;
- число изделий;
- дату приемки;
- показатель прочности при проверке на сжатие;
- устойчивость к промерзанию;
- марку по плотности;
- адрес изготовителя и его полное наименование;
- условное обозначение товара.
Керамзитобетонные блоки разрешается транспортировать различными видами транспортных средств. Во время перевозки необходимо соблюдать требования по закреплению груза и его упаковке. Загружать или разгружать материал навальным способом запрещено.
Хранятся блоки чаще всего на деревянных поддонах. Изделия следует защитить от воздействия природных явлений, изолируя их пленочным материалом. Хранение разрешено на площадках не только закрытого, но и открытого типа.
Заключение
Все материалы, предназначенные для проведения строительных работ, производятся по требованиям стандарта качества, и блоки из керамзитобетона не относятся к исключениям. Для выбора правильного материала необходимо знать показатели, которым блоки должны полностью соответствовать. Только от качества будет зависеть успех эксплуатации будущего объекта.
Влажность материала будет напрямую оказывать влияние на показатель теплопроводности.
Помните, что блок из керамзитобетона широко применяется в строительстве сооружений различного предназначения, начиная от хозпостроек и заканчивая крупными жилыми объектами. И все это благодаря тому, что материал обладает соответствующими ГОСТ характеристиками качественного и технического характера.
Характеристики керамзитобетонных блоков: достоинства и недостатки
Керамзитобетонные блоки характеризуются свойстами материалов, из которых они состоят. Большое значение в определении характеристик этих конструкций имеют особенности технологии их производства.
Какой же состав керамзитобетонных блоков?
Исходным материалом для них служит керамзит, бетон и вода.
Разберемся с составом бетона. Что это за материал? В его состав входит цемент и наполнитель, в качестве которого может выступать песок или щебень. После застывания бетона получается твердый материал, похожий свойствами на щебень. С истечением времени твердость бетона увеличивается и не прекращается даже при воздействии воды. Это очень плотный и жесткий материал, имеющий большую теплопроводимость, в связи с этим его обязательно нужно хорошо утеплять.
Керамзит представляет собой пористый материал, выпускаемый в форме гранул или шариков. Он производится путем обжига глины в специальных печах, которые вращаются. Особенностью керамзита является то, что каждый шарик имеет корку из спекшейся глины, поэтому он легко впитывает влагу и удерживает ее в себе. Это свойство играет большую роль в сельском хозяйстве при выращивании культур на гидропонике. В строительстве такие свойства не очень полезны, из-за впитывания влаги. Для керамзита характерна низкая теплопроводность, сравнима с теплопроводностью дерева, поэтому в качестве утеплителя его использование нежелательно, так как есть много материалов с намного большей теплопроводностью за ту же стоимость.
Теперь о керамзитобетоне. Использование керамзита в качестве наполнителя бетона позволило получить очень интересные и полезные свойства этого материала, благодаря которым керамзитобетон получил большую популярность в строительстве. Изменяя количество наполнителя, можно получить бетон различной плотности. Самая распространенная плотность от 1800 кг на куб.м до 500 кг на куб. м. Чем плотнее керамзитобетон, тем он тяжелее и тем выше его прочность, благодаря чему из этого материала можно возвести здание выше, чем из другого стройматериала, но из-за высокой теплопроводности он нуждается в дополнительной утеплении.
Преимущества керамзитобетонных блоков
Керамзитобетонные блоки значительно упрощают труд строителей. Блоки керамзитобетона обычно крупнее от кирпичей, поэтому возведение здания занимает меньше времени, да и количество блоков тоже меньше, чем кирпичей на строительство одной и той же стены. Отсюда меньший расход раствора и следовательно меньшие трудозатраты. Керамзитобетонные блоки обычно не такие большие, как пено-газобетонные блоки, потому что керамзитобетон намного тяжелее, потому чем больше блок, тем тяжелее его поднять. Обычно керамзитобетонные блоки производят размерами 20х20х40 см.
Керамзитобетонные блоки имеют ряд достоинств. Одним из них является легкость и простота их производства, для которого не нужно дорогостоящее оборудование. Блоки можно производить даже в домашних условиях, благодаря чему, логично предположить, что должна снизиться стоимость этого блока. Но в нашем обществе, как всегда, выигрывает и получает выгоду не конечный потребитель, и даже не производитель, как логически предполагается, а продавец, но эта проблема уже совсем не по сегодняшней теме.
Керамзитобетонные блоки высокой плотности хорошо подходят для возведения домов повышенной этажности. Постройки из керамзитобетона не подвергаются усадке, не деформируются и не образуют трещин в процессе эксплуатации.
Также они обладают высокой паропроницаемостью и для них не нужно устраивать специальную пароизоляцию. Паропроницаемость этого материала вполне можно сравнить с паропроницаемостью кирпича.
В частном строительстве уместно использовать более легкие блоки в сравнении с высотным строительством. Их теплопроводность подобна теплопроводности дерева, а благодаря плотности можно возвести 2-3 этажный дом с железобетонными перекрытиями этажей. В результате использования керамзитобетона в строительстве снижается общий вес дома и производится экономия затрат на сложный фундамент и утепление.
Выгодное отличие керамзитобетона от пено-газобетона состоит в том, что в керамзитобетонные блоки легко вбиваются и держатся обычные дюбели с такимим же обычными шурупами. Этого нельзя сказать о пено-газобетоне, в котором они не держатся, и приходится использовать специальные крепежи.
В некоторых регионах нашей страны есть много полезных ископаемых, таких как глина и известняк. Логично предположить, что в таких регионах должны быть заводы по переработке этих ископаемых и производства из них керамзита, цемента и керамзитобетона. Поэтому, прежде чем отправляться в магазин и переплачивать кругленькую сумму, необходимо узнать, можно ли приобрести эти материалы прямо с завода, без участия посредников и их накруток, что в значительной степени могло бы уменьшить затраты на строительство. К сожалению, в большинстве случаев конечный потребитель оказывается в самом невыгодном положении. Но все же попытаться стоит.
Недостатки керамзитобетонных блоков
Керамзитобетон имеет недостатки, о которых нельзя умолчать. Много факторов создают трудности частным строителям. Прежде всего, это несоблюдение технологии изготовления блоков, некачественное сырье, используемое для удешевления продукции и умалчивание этих фактов. Так и просится вырваться известная присказка, о том, что любая хорошая идея может быть доведена до абсурда недобросовестным исполнением.
Покупая керамзитобетонные блоки, обязательно следует обратить внимание, насколько точно выдержаны их размеры. Возьмите блок в руку и взвесьте хоть примерно, соответствует ли он указанной плотности. Например блок параметрами 20х20х40 см должен иметь объем 16 тис. куб.см. Один кубический метр содержит миллион кубических сантиметров. Если поделить миллион на 16 тысяч, мы совершенно неожиданно получаем в одном кубическом метре 62 с половиной блока. Если кубометр керамзитобетона весит 500 кг, то один блок получается весов 8 кг, что слишком мало. А если блоки пустотелые, то весить они будут еще меньше. В этом случае расчет трудно произвести из-за сложности подсчета точного объема блока.
Как уже говорилось выше, строение из керамзитобетонных блоков будет легче от строения, возведенного из кирпичей, но тяжеловатым для возведения его на облегченном фундаменте. Поэтому здесь тоже нужен правильный расчет.
Из керамзитобетонных блоков рекомендуется возводить тонкие стены с обязательной теплоизоляцией, потому что при кладке стен всегда образуются мостики холода.
Кладка должна быть сразу отделанная утеплительными материалами, потому что со временем его отсутствие может отрицательно сказаться на ее долговечности.
Воздухопроницаемость керамзитобетонного блока слабее, чем кирпича, но с учетом внутренней отделки стен это не имеет существенного значения.
Утепляя стену из керамзитобетона, желательно делать это с внешней стороны сооружения. Для этой цели хорошо подходят минераловатные плиты, имеющие среднюю или малую плотность. Чтобы правильно подсчитать нужную толщину утеплителя, попробуйте воспользоваться калькулятором теплопроводности, если вы в курсе, как это сделать.
Какие можно сделать выводы исходя из характеристик керамзитобетонных блоков?
Керамзитобетонные блоки являются прекрасным строительным материалом, широко используемым на практике многими строителями, которые ценят его высокую прочность, одновременно сочетаемую со сравнительно низким весом. Этот строительный материал по своим физико-механическим характеристикам превосходят по цене и качеству зарубежные аналоги, особенно это касается морозостойкости, теплопроводности, точности геометрических пропорций.
А если вам удастся приобрести этот материал прямо на заводе, без участия посреднических накруток в цене, это будет самое удачное решение возведения дома на сегодняшний день!
Блоки из керамзитобетона. Видео
Экспертиза эффективных параметров производства керамзитобетона title={Исследование эффективных параметров производства керамзитобетона}, автор = {Ахмет Озгувен и Л.
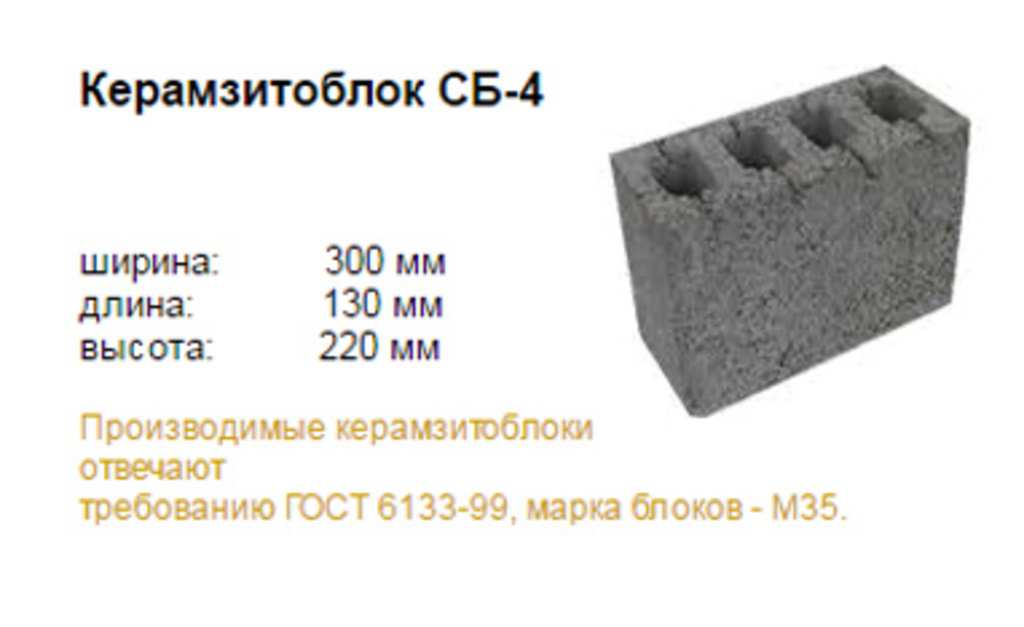
- А. Озгювен, Л. Гюндуз
- Опубликовано 1 июля 2012 г.
- Материаловедение
- Цементно-бетонные композиты
Просмотр через Publisher
Влияние предварительного увлажнения керамзитобетона на морозостойкость керамзитобетона
23 M. Musiał, F. Grzymski, T. Trapko
Материаловедение, инженерия
Studia Geotechnica et Mechanica
Реферат В данной статье представлены экспериментальные исследования керамзитобетона. Цель исследований состояла в том, чтобы определить, влияет ли предварительное смачивание керамзитобетона на…
Оценка свойств и минеральных фаз керамзитовых заполнителей с бентонитовой добавкой
Добавки представляют собой идеальное решение для улучшения физических, механических и расширяющих свойств легких керамзитовых заполнителей (LECA). Эта работа была посвящена изучению влияния…
Моделирование распределения параметров материала вспененных гранул
- C. Woitzik, A. Düster
Материаловедение
Гранулированное вещество
- 2017
Данная работа посвящена определению параметров материала для различных гранул керамзитобетона и глины. При использовании этих материалов в качестве гасителей ударов прочность на раздавливание и модуль Юнга…
Моделирование распределения параметров материала вспененных гранул
- C. Woitzik, A. Düster
Материаловедение
- 2017 90 сделок Эта работа с определением параметров материала для различных гранул пеностекла и глины. При использовании этих материалов в качестве амортизаторов прочность на раздавливание и модуль Юнга…
- J.
Latosinska, M. Żygadło, P. Czapik
Materials Science
Materials
- 2021
- Haithhem Ben Jamaa, L. Elghezal, M. Jamei
Материаловедение
Гранулированный материал
- 2020
- Буманис Г.
, Бахар Д., Локс Дж., Корякинс А.
Материаловедение
- 2013
- C. Burbano-Garcia, A Уртадо, Ю. Силва, С. Дельвасто, Г. Арая-Летелье
Материаловая наука
- 2020
- P. C. C. Chiadighikaobi, Rilwan Olakunbi Tarka
Mabrity Sciention
- 111111111111111111111111111111111111111111111tion для структурного анализа кладки LECA
- Т. Кванде
Инжиниринг
- 2001
Кирпичная кладка из бетонных блоков из легкого керамзитобетона (LECA) на сегодняшний день является самой популярной каменной кладкой в Норвегии.
LECA представляет собой легкий заполнитель (LWA). Основная цель этого ст…
Кирпичи из ячеистого бетона с переработанным пенополистироловым заполнителем
На этой странице
РезюмеВведениеМетодыРезультаты и обсуждениеВыводыСсылкиАвторское правоСтатьи по теме переработанный пенополистироловый заполнитель вместо песчаных материалов. После определения свойств блока (впитываемость, прочность на сжатие и растягивающие напряжения) было установлено, что этот кирпич соответствует требованиям стандартов кладки, применяемых в Мексике. Полученный материал легче коммерческих, что облегчает их быструю обработку, контроль качества и транспортировку. Он менее проницаем, что помогает предотвратить образование влаги, сохраняя при этом прочность благодаря большей адгезии, проявляемой сухим полистиролом. Он был более гибким, что делало его менее уязвимым к растрескиванию стен из-за смещения грунта. Кроме того, он экономичен, поскольку использует перерабатываемый материал и обладает свойствами, которые предотвращают износ, увеличивая срок его службы.
Мы рекомендуем использовать полностью сухой EP в сухой среде, чтобы получить наилучшие свойства кирпича.
1. Введение
Легкий строительный раствор может быть получен различными способами и в основном зависит от воздушного фактора, то есть снижение плотности материала заключается во включении в его структуру воздуха, что можно осуществить заменой крупного заполнителя (песок) по воздуху. Таким образом, включение воздуха в структуру материала способствует образованию пузырей (пустого пространства) внутри бетона или раствора. Поэтому, когда он высыхает, воздушные отверстия образуют легкий материал. Этот тип бетона известен как Ячеистый бетон . Было предложено определить легкий бетон как бетон, изготовленный с легким заполнителем или без заполнителя, что позволяет получить вес меньше, чем у обычного бетона 2400 кг/м 3 [1].
Что касается использования полистирола в бетонах, в литературе упоминается использование гранул пенополистирола (ЭП) в качестве легкого заполнителя как в бетонах, так и в строительных растворах, содержащих микрокремнезем в качестве дополнительного вяжущего материала.
Полученные бетоны имели плотность от 1500 до 2000 кг/м 9 .0183 3 , с соответствующими прочностными характеристиками от 10 до 21?МПа [2]. Другое исследование посвящено использованию шариков из пенополистирола (EPS) и нерасширенного полистирола (UEPS) в качестве легкого заполнителя в бетонах, содержащих летучую золу в качестве дополнительного вяжущего материала. Легкие бетоны с широким диапазоном плотностей бетона (1000–1900 кг/м 3 ) изучались в основном на прочность на сжатие, прочность на разрыв при растяжении, миграцию влаги и поглощение. Результаты показывают, что при сопоставимом размере заполнителя и плотности бетона бетон с заполнителем UEPS показал прочность на сжатие на 70% выше, чем заполнитель EPS [3].
Тонкодисперсный микрокремнезем значительно улучшил сцепление между гранулами EP и цементным тестом и увеличил прочность на сжатие EP бетона. Исследования показали, что пенополистирол плотностью 800–1800 кг/м 3 и прочностью на сжатие 10–25 МПа можно получить путем частичной замены крупного и мелкого заполнителя гранулами пенополистирола.
Кроме того, добавление стальной фибры значительно улучшило усадку при высыхании [4].
Другое исследование показывает сравнение механических свойств бетонов EP, содержащих летучую золу, с литературными данными по бетонам, содержащим в качестве связующего только обычный портландцемент [5]. В исследовании предложена разработка класса конструкционных полистиролбетонов с широким диапазоном плотностей бетона от 1400 до 2100 кг/м 9 .0183 3 путем частичной замены крупного заполнителя полистирольным заполнителем в контрольном бетоне [6].
Латекс стирол-бутадиенового каучука в качестве полимерной добавки применялся в легком пенополистирольном (ЭП) бетоне. Было исследовано влияние условий отверждения и соотношения полимер-цемент на прочность на сжатие и изгиб модифицированных полимерами EP-бетонов [7]. Затвердевший бетон, содержащий химически обработанные гранулы пенополистирола, показал, что на прочность, жесткость и химическую стойкость полистиролбетона постоянной плотности влияет водоцементное отношение [8].
В первой части этого исследования, основанного на определении и характеристиках легкого бетона, был проведен поиск перерабатываемого материала с низкой плотностью, который можно было бы перерабатывать с использованием дешевого устойчивого метода переработки. Этим материалом был пенополистирол (EP). С помощью этого материала был получен раствор, в котором крупные заполнители были полностью заменены частицами с низкой плотностью. Итак, кирпичи состоят из переработанного пенополистирола в качестве заполнителя и коммерческого портландцемента в качестве связующего. В отличие от большинства работ, опубликованных в литературе, в этом растворе не используются ни пуццоланы, ни добавки, ни дополнительные заполнители. В этом предыдущем исследовании этот материал имел хорошее сцепление с гидратированным цементом, а наилучшие механические свойства ячеистого бетона были получены при водоцементном отношении 0,4 и 600 мкг пенополистирола [9].].
На втором этапе, ядром этого исследования, и с определенной технологией, специфическим технологическим применением раствора из вторсырья было изготовление ячеистого кирпича.
Они должны быть конкурентоспособными по цене, качеству, механическим и физическим свойствам по сравнению с существующими на рынке. Кроме того, ячеистые кирпичи должны использовать экологически чистый материал, пригодный для вторичной переработки.
2. Методы и приемы
Операции, перечисленные ниже, позволили изготовить и провести механическую и физическую оценку кирпичей из ячеистого бетона; (i) получение и измельчение ЭП; (ii) применение водоцементного отношения 0,4; (iii) производство ячеистого бетона; (iv) изготовление кирпича с использованием стальных форм диаметром ? см; (v) расформовка и получение сухой массы кирпича; (vi) испытания на впитывание, сжатие и растяжение; Стандарт ASTM C67-03a включает три теста [10]; (vii) отчет о результатах; (viii) сравнение результатов с заявленными значениями некоторых коммерческих кирпичей в Мексике. Прочность на сжатие легкого бетона из пенополистирола (EPS) значительно увеличивается. с уменьшением размера гранул ЭПС [11, 12]. Кроме того, другое исследование включает три размера частиц полистирола (1, 2,5 и 6,3 мкм) в бетоне и делает вывод, что размер 1 мкм имеет большее сопротивление сжатию [12].
Затем, поскольку целью проекта было повторное использование перерабатываемого материала, такого как пенополистирол, размеры частиц зависели от устойчивого и дешевого процесса измельчения. На самом деле достигнутые размеры (2–4 мкм) были очень близки к тем, о которых сообщается как о большей прочности на сжатие [12].
В первую очередь был проведен поиск отходов ЭП. Эти остатки ВП были получены в основном из упаковки компьютеров. После того, как материал был собран, его измельчали с водой в кухонном блендере, потому что без воды не было бы измельчения. Полученный размер частиц составлял 2–4 мкм. Затем удаляли избыток воды и сушили ЭП в естественных условиях, без использования печей.
В соответствии с предыдущими исследованиями, ячеистый бетон был получен путем смешивания 600 мкг полистирола и водоцементного отношения 0,4. В качестве цемента использовали CPC (композитный портландцемент).
Следует отметить, что одним из важных факторов, повлиявших на это исследование, была высокая влажность окружающей среды в месте проведения исследования (Росарио, Аргентина).
Этот факт привел к получению жидкого композита, который позволял легко заполнять стальные формы.
Были испытаны два типа образцов, обозначенных буквами А и В, с размерами мкм. Тип А имел водоцементное отношение 0,4, вес 0,600 кг ЭП в полувлажном состоянии и возраст 28 дней. Тип В имел такое же водоцементное отношение, но с массой полусухого ЭП 0,520 кг. Возраст B-теста составил всего 14 дней из-за окончания проекта.
Из-за условий влажности окружающей среды, когда мы сушим влажный полистирол (получаемый материал для процесса измельчения) в течение 7 дней, мы получили вес 600 мкг для кирпичей А и В. Сразу же обрабатываем кирпичи А (с 600 мкг) на первом этапе проекта. Затем, когда через 28 дней был использован оставшийся полистирол, мы заметили, что вес уменьшился. Поэтому этот оставшийся материал был разделен и использован в пяти кирпичах B. Таким образом, кирпичи B содержали 520 мкг полистирола. Поэтому кирпичи А были изготовлены из «полувлажного» полистирола, а кирпичи В — из «полусухого» полистирола.
Полностью сухую массу ЭП мы не получили из-за состояния локальной сырости окружающей среды.
Уровни влажности окружающей среды для «полувлажного» и «полусухого» полистирола были одинаковыми; разница заключалась во времени воздействия в этих условиях. Влажность окружающей среды в этом месте в дни проведения эксперимента составляла 62–95 % [14] (Росарио, Аргентина, август 2012 г.). Полистирол, названный «полувлажным», выдерживался 7 дней в этой среде и 28 дней в «полусухом».
Через 27 дней для кирпичей А и 13 дней для кирпичей В кирпичи были подвергнуты испытанию на абсорбцию (это экспериментальное испытание требует 24 ч [10] насыщения кирпичей для его оценки). Таким образом, результаты испытаний на абсорбцию были получены через 28 дней для кирпичей А и через 14 дней для кирпичей В при испытаниях на сжатие и растяжение.
Теоретически при хранении во влажной среде около 90% прочности набирается в течение первых 28 дней. Основным критерием оценки прочности бетона на сжатие является прочность бетона на 28-е сутки.
Образец бетона испытывается через 28 дней, и результат этого испытания рассматривается как критерий качества и жесткости этого бетона [15].
3. Результаты и обсуждение
Статистическая оценка процента абсорбции А и В представлена в таблице 1. Для измерения абсорбционных свойств стандарт ASTM C67-03a указывает, что материал выдерживают погруженным в воду в течение 24 часов. [10]. Процент поглощения определяли по (1) [10]. Сухая и насыщенная массы ( и , соответственно) кирпича были до и после его насыщения соответственно: Из Таблицы 1 мы заметили, что кирпич В (полусухой ЕР) имеет меньшую абсорбцию, чем кирпич А (полувлажный ЕР). Хотя время исследования кирпича В вдвое меньше, чем А, тенденция к увеличению поглощения очень мала. Таким образом, очевидно, что этот материал может уменьшить влажность, образующуюся в стенах, построенных из других типов кирпичей, поглощение которых выше из-за типа используемых заполнителей, таких как песок.
Статистические результаты испытаний на сжатие [10] обоих типов образцов площадью мкм приведены в таблице 1. Следует напомнить, что возраст кирпичей А составил 28 дней, а возраст кирпичей В – 14 дней. Из-за вышеизложенного различия в силе могут быть оправданы. Можно также заметить, что тенденция к увеличению прочности продолжается в образцах В, и она превысит значение, достигнутое образцами типа А, благодаря большей адгезии (меньшему поглощению), создаваемой полусухим ЕР.
Прочность на растяжение или модуль разрыва [10] рассчитывали как где – предел прочности при растяжении или модуль разрыва (МПа), приложенная максимальная нагрузка (кг), – расстояние между опорами (см) (рассчитывается как длина образца минус 2 дюйма, поскольку опоры находятся на расстоянии 1 дюйм от каждого конца) , — горизонтальное расстояние от точки приложения нагрузки до места возникновения трещины (см), и — соответственно ширина и толщина образца (см).
Статистические результаты испытания на растяжение образцов типов A и B показаны в таблице 1.
Они были определены по (2).
Из таблицы 1 среднее значение предела прочности при растяжении для образцов А и В составляет 2,195 и 1,632 МПа соответственно. Образец типа В показал частичную прочность на растяжение по сравнению с той, которая может развиться за 28 дней.
При условии, что традиционные бетонные кирпичи с крупным заполнителем и обожженные глиняные кирпичи имеют очень низкие значения предела прочности, в среднем около 0,8?МПа [13]. Таким образом, EP придает кирпичу свойства изгиба, которые способствуют стабильности стены, особенно когда он испытывает восходящие и нисходящие движения, вызванные проблемными грунтами, такими как расширяющиеся и просадочные грунты, изменения уровня грунтовых вод и землетрясения, среди прочего. Поэтому этот материал уменьшает появление трещин в стене. Этот аспект не учитывался при изготовлении традиционных кирпичей.
Бетон вряд ли можно считать однородным, потому что свойства его компонентов различны, и он в некоторой степени анизотропен.
Тем не менее подход механики разрушения помогает понять механизм разрушения бетона. Фактические пути разрушения обычно следуют по границам раздела самых крупных частиц заполнителя и прорезают цементное тесто, а иногда и сами частицы заполнителя [16].
Как и в случае с бетоном, пути разрушения обычно проходят по границе раздела частиц полистиролового заполнителя и прорезают цементное тесто и сами частицы заполнителя. При сжатии трещины примерно параллельны приложенной нагрузке, но некоторые трещины образуются под углом к приложенной нагрузке (рис. 1). Параллельные трещины вызваны локализованным растягивающим напряжением в направлении, нормальном к сжимающей нагрузке; наклонные трещины возникают из-за обрушения, вызванного развитием плоскостей сдвига. Следует отметить, что картины разрушения испытания на сжатие относятся только к прямым напряжениям [16].
При испытании на изгиб максимальное растягивающее напряжение достигается в нижнем волокне испытательной балки, поэтому трещины расположены вертикально и находятся вблизи точки приложения нагрузки (рис.
2). При испытании на растяжение верхняя поверхность подвергается сжатию, а нижняя поверхность подвергается растяжению. Концентрация напряжения в вершине трещины фактически является трехмерной, но наибольшая слабость возникает, когда ориентация трещины перпендикулярна направлению приложенной нагрузки. В действительно хрупком материале (равномерное распределение напряжения) энергия, выделяемая при начале распространения трещины, достаточна для продолжения этого распространения, поскольку по мере расширения трещины максимальное напряжение увеличивается, а предел хрупкого разрушения снижается. В результате процесс ускоряется. В случае неравномерного напряжения (например, при изгибе) распространение трещины блокируется дополнительно окружающим материалом при более низком напряжении [16].
В таблице 2 показаны результаты свойств, полученных на образцах. Они сравниваются с параметрами, о которых сообщается в другом месте [13]. Из этой таблицы видно, что кирпич ЭП легче остальных, что облегчает его разработку, производство и транспортировку.
Затем этот материал обладает свойством низкой впитываемости, что помогает предотвратить возможную влажность стен. Кроме того, этот материал устойчив, так как его прочность на сжатие (с полусухим EP) аналогична заявленным максимальным коммерческим значениям, которые, возможно, могут превышать при использовании EP в сухом состоянии. Наконец, этот материал может быть в четыре раза более гибким, чем некоторые коммерческие блоки, что делает его менее уязвимым для возможных трещин в стенах, вызванных восходящими или нисходящими движениями подстилающего грунта.
Относительно высокие значения коэффициента вариации (табл. 1) в тесте зависели от типа теста и количества данных. Испытания на впитывание и сжатие имеют близкие значения коэффициента вариации; то есть мы видим тот же диапазон ошибок при выполнении теста, который можно уменьшить, увеличив количество тестов. Затем испытание на растяжение показывает два очень разных коэффициента вариации, в основном из-за завершения испытания, которое требует большой точности и осторожности.
В этом тесте мы заметили, что образец А имеет большую погрешность, чем В, потому что А был испытан первым. Однако все данные по всем свойствам были выше контрольных значений в таблице 2.
Оба материала (А и В) не имеют одинакового времени и количества полистирола. Образец A имеет полные начальные переменные, а B — нет. Поэтому их нельзя сравнивать между собой. Итак, в этой работе мы сообщаем и анализируем свойства, приобретенные в образце А, а затем свойства, приобретенные в образце В (по отношению к образцу А), потому что, хотя этот материал имеет свои неполные исходные переменные, он становится важными свойствами именно из-за эта ситуация. Наконец, оба образца были лучше, чем эталонные материалы в таблице 2.
4. Выводы
Кирпич, разработанный в данном исследовании, показал хорошие механические свойства и может быть использован в качестве кладочного материала в строительстве, так как этот материал соответствует требуемым параметрам. Он состоит из переработанного пенополистирола в качестве заполнителя и коммерческого портландцемента в качестве связующего.
В отличие от большинства работ, опубликованных в литературе, в этом растворе не используются пуццоланы, добавки или дополнительные заполнители.
В отличие от бетона (с крупным заполнителем), пути разрушения всегда проходят по границе раздела частиц полистиролового заполнителя и прорезают цементное тесто и сами частицы заполнителя. Трещины в полистироловом кирпиче аналогичны трещинам в бетоне, о которых сообщалось в испытаниях на сжатие и растяжение.
В результатах свойств мы наблюдали тот же диапазон погрешности при выполнении тестов, который можно уменьшить, увеличив количество тестов.
Устойчивое использование пенополистирола в кирпичах из ячеистого бетона было очень выгодным по сравнению с существующими на рынке. Полученный материал легче, что облегчает его производство и транспортировку, и менее проницаем, что позволяет избежать образования влаги при сохранении его прочности. Кроме того, он более устойчив и гибок, что делает его менее уязвимым к растрескиванию стен, вызванному движением грунта.
Наконец, этот материал дешевле, потому что в нем используется материал, пригодный для вторичной переработки, и он обладает свойствами, которые предотвращают его износ, увеличивая срок его службы.
Мы наблюдаем, что влага окружающей среды и влага EP уменьшают свойства сопротивления кирпича и увеличивают его плотность и абсорбцию. Мы рекомендуем использовать полностью сухой EP в сухой среде, чтобы получить наилучшие свойства кирпича.
Каталожные номера
С. Чандра и Л. Бернтссон, Бетон с легким заполнителем. Science, Technology and Applications , Noyes Publications, New York, NY, USA, 2003.
Бабу К.Г. и Бабу Д.С. Поведение легкого пенополистирольного бетона, содержащего микрокремнезем.0181 Исследование цемента и бетона , vol. 33, нет. 5, стр. 755–762, 2003 г.
Посмотреть по адресу:
Сайт издателя | Google Scholar
Д. С. Бабу, Г.
К. Бабу и В. Тионг-Хуан, «Влияние размера заполнителя полистирола на характеристики прочности и миграции влаги легкого бетона», Cement and Concrete Composites , vol. 28, нет. 6, стр. 520–527, 2006 г.
Посмотреть по адресу:
Сайт издателя | Google Scholar
Чен Б., Лю Дж. Свойства легкого пенополистирольного бетона, армированного стальной фиброй, стр. 9.0181 Исследование цемента и бетона , vol. 34, нет. 7, стр. 1259–1263, 2004.
Посмотреть по адресу:
Сайт издателя | Google Scholar
Д. С. Бабу, Г. К. Бабу и В. Тионг-Хуан, «Свойства легких бетонов на вспененном полистироле, содержащих летучую золу», Cement and Concrete Research , vol. 35, нет. 6, стр. 1218–1223, 2005.
Посмотреть по адресу:
Сайт издателя | Google Scholar
У.
К. Танг, Ю. Ло и А. Надим, «Механические свойства и усадка при высыхании конструкционного бетона на полистироловом заполнителе», Цементные и бетонные композиты , vol. 30, нет. 5, стр. 403–409, 2008 г.
Посмотреть по адресу:
Сайт издателя | Google Scholar
Б. Чен и Дж. Лю, «Механические свойства полимер-модифицированных бетонов, содержащих гранулы пенополистирола», Construction and Building Materials , vol. 21, нет. 1, стр. 7–11, 2007 г.
Посмотреть по адресу:
Сайт издателя | Google Scholar
Р. Шри Равиндрараджа и А. Дж. Так, «Свойства затвердевшего бетона, содержащего обработанные гранулы пенополистирола», Цементные и бетонные композиты , vol. 16, нет. 4, pp. 273–277, 1994.
Посмотреть по адресу:
Google Scholar
O.
García-Díaz, Mortero de baja densidad con poliestireno reciclado [M.S. диссертация] , Facultad de Ingeniería, Universidad Autonoma de Querétaro, Querétaro, México, 2011.
«Стандартные методы испытаний для отбора проб и испытаний кирпича и конструкционной глиняной плитки», ASTM C67-03a, Ежегодный сборник стандартов ASTM. , 2003.
Посмотреть по адресу:
Google Scholar
А. Лаукайтис, Р. Жураускас и Дж. Керине, «Влияние гранул пенополистирола на свойства цементного композита», Цемент и бетонные композиты , том. 27, нет. 1, стр. 41–47, 2005 г.
Посмотреть по адресу:
Сайт издателя | Google Scholar
К. Майлед, К. Саб и Р. Ле Рой, «Влияние размера частиц пенополистирола на прочность легкого бетона на сжатие: экспериментальное исследование и моделирование», Механика материалов , том.
39, нет. 3, стр. 222–240, 2007 г.
Посмотреть по адресу:
Сайт издателя | Google Scholar
А. Тена, А. Хуарес и В. Х. Салинас, «Resistencia y deformación de muros de mampostería combinada y confinada sujetos a cargas laterales», Revista de Ingeniería Sísmica , vol. 76, стр. 29–60, 2007.
Посмотреть по адресу:
Google Scholar
WeatherOnline Ltd, 1999–2013, Погода в Росарио, Аргентина, август 2012 г., http://www.woespana.es.
В. К. Алилоу и М. Тешнехлаб, «Прогнозирование прочности бетона на сжатие в течение 28 дней на третий день с использованием искусственных нейронных сетей», International Journal of Engineering , vol. 3, нет. 6, pp. 565–576, 2010.
View по адресу:
Google Scholar
A.
The Influence of Sewage Sludge Content and Sintering Temperature on Selected Properties of Lightweight Expanded Clay Aggregate
It was доказано, что в сырьевой массе для производства ЛЭКА допустим широкий диапазон содержания СС, а температура спекания оказывает существенное влияние на удельную плотность, кажущуюся плотность, общую пористость, закрытую пористость), общий объем пор, и водопоглощение.
Эдометрическое поведение керамзита при сжатии, включая способность к дроблению отдельных частиц поведение керамзитового материала с учетом дробимости его отдельных зерен. Исследуемый материал характеризуется высокой внутренней пористостью;…
Одометрические свойства керамзита при сжатии, в том числе дробимость отдельных частиц
. Исследуемый материал характеризуется высокой внутренней пористостью;…
Щелочно-кремнеземная реакционная способность гранул пеностекла в структуре легкого бетона
Основным компонентом легкого бетона, обеспечивающим его свойства, является заполнитель. Было проведено множество исследований щелочно-кремнеземной реакции (ASR) между цементом и легкими заполнителями…