Общие положения | Технологическая карта регламентирует технологию нанесения эмали «ПФ-266» для покрытия окрашенных и неокрашенных деревянных полов по предварительно подготовленной поверхности. | ||||||||||
Подготовка деревянной поверхности | Сухая деревянная поверхность очищается от жира, грязи, пыли и старой отслоившейся краски. Желательна обработка наждачной шкуркой и обеспыливание. Для улучшения сцепления с деревом и уменьшения расхода эмали можно ранее не окрашенную поверхность перед нанесением эмали покрыть олифой и высушить. | ||||||||||
Грунтовочный слой | Нанесение эмали «ПФ-266» производится без грунтования. | ||||||||||
Подготовка эмали | ![]() |
||||||||||
Разбавление | При необходимости в эмаль добавить растворитель (уайт-спирит) постепенно небольшими порциями до получения равномерного факела или нужной вязкости. Минимальная рабочая вязкость эмали по вискозиметру ВЗ-246(4) при температуре 20 ºС в зависимости от метода нанесения: – пневматическое распыление – 35 с; – безвоздушное распыление – 40 с; – ручное нанесение 75 с. Количество растворителя на разбавление не должно превышать 10%. Запрещается применение иных разбавителей! Рекомендуется приобретение растворителя вместе с эмалью у производителя. При использовании эмали возможны перерывы в работе при хранении в плотно закрытой таре, при возобновлении работы ее необходимо перемешать мешалкой |
||||||||||
Нанесение эмали | |||||||||||
Климатические условия | Температура окружающей среды при нанесении эмали должна быть в интервале от плюс 5 ºС до плюс 30 ºС и влажности воздуха не более 80%; Окрасочные работы не производятся или останавливаются во время дождя и снега, а также при скорости ветра более 10 м/сек. ![]() Температура окрашиваемой поверхности должна быть на 3 ºС выше точки росы. |
||||||||||
Пневматическое распыление | Настройка окрасочного оборудования при пневматическом распылении производиться в соответствии с инструкцией на оборудование; Рекомендации по нанесению: – расстояние от сопла краскораспылителя до окрашиваемой поверхности – 200-400 мм; – диаметр сопла пневматического распылителя, мм: 1,4-1,7. |
||||||||||
Безвоздушное распыление | Настройка окрасочного оборудования при безвоздушном распылении производиться в соответствии с инструкцией на оборудование; Рекомендации по нанесению: – расстояние от сопла краскораспылителя до окрашиваемой поверхности – 300-500 мм; – давление материала 80-150 бар; – диаметр сопла безвоздушного распылителя мм: 0,38-0,58; |
||||||||||
Ручное нанесение | Ручное нанесение рекомендуется производить валиком без ворса или кистью из натурального волокна | ||||||||||
Полосовое окрашивание | Полосовое окрашивание сварных швов, торцевых кромок и других труднодоступных мест проводят кистью или валиком перед полным окрашиванием.![]() |
||||||||||
Толщина покрытия | Эмаль наносится в 2 слоя. Толщина однослойного покрытия «ПФ-266» (по сухому слою) – 18-24 мкм. Толщина покрытия не более 50 мкм. | ||||||||||
Расход эмали | Расход материала зависит от способа нанесения (распылитель, валик, кисть), от свойств окрашиваемой поверхности, незначительно варьируется в разных цветах, что следует учитывать при нормировании. Примерные нормы расхода на один слой: от 150 г/м². | ||||||||||
Межслойная сушка и время высыхания покрытия | Минимальное время высыхания до нанесения следующего слоя и окончательного высыхания покрытия при распылении, не менее, чем:
|
||||||||||
Промывка оборудования | Оборудование следует промывать ксилолом, Р-4, 646.![]() |
||||||||||
Важно! | По окончанию работ немедленно произвести очистку оборудования для предотвращения высыхания лакокрасочного материала. | ||||||||||
Формирование покрытия | Формирование покрытия эмали «ПФ-266» происходит без нагревания при естественных условиях. Окончательное формирование покрытия происходит в течении 3 суток при +20ºС. При более низких температурах срок увеличивается до 14 суток. |
||||||||||
Транспортирование | Транспортирование и монтаж окрашенных конструкций можно производить не ранее, чем через 24 часа после нанесения финишного слоя | ||||||||||
Ремонт покрытия | Ремонт поврежденного участка покрытия зачистить инструментом, обеспылить, обезжирить.![]() |
||||||||||
Хранение эмали | Гарантийный срок годности эмали «ПФ-266» – 6 месяцев со дня изготовления. Хранить материал необходимо в отдельном помещении, оборудованном приточновытяжной вентиляцией или под другим укрытием, препятствующим попаданию прямых солнечных лучей и влаги при температуре от минус 60 ºС до плюс 40 ºС. | ||||||||||
Требования безопасности | Данный продукт является пожароопасным и токсичным. Места проведения работ должны быть обеспечены средствами пожарной безопасности. Окрасочные работы производить при хорошей вентиляции, с использованием средств индивидуальной защиты (перчатки, халаты, респираторы и т.д.). Не допускать попадания в органы дыхания и пищеварения. | ||||||||||
Как определить расход растворителя при покраске металлической поверхности – ООО ДХЗ
Правильно выбранный растворитель для краски – это один из факторов, которые оказывает существенное влияние на конечный результат лакокрасочных работ. Эффективное использование данных составов значительно улучшает надежность и качество отделки, а наличие ошибок может привести к тому, что на рабочей поверхности появятся трещины и пузыри, следовательно, работу нужно будет переделывать.
Назначение и требования к растворителям.
Растворитель для ЛКМ представляет собой химическое вещество, которое в ходе смешивания с компонентами декоративного средства активно вступает в реакцию, а после этого испаряется. Следует отметить, что предпочтение зачастую отдается быстроиспаряющимся составам, так как за счет этого значительно уменьшается время полного высыхания обрабатываемой поверхности.
Кроме своего основного назначения, а именно достижения нужной концентрации лакокрасочного материала, эти составы также применяются для отмывки окрашенных инструментов, поверхностей, а также случайно загрязненных объектов. Например, растворитель для обычной порошковой краски зачастую используется именно для этих целей, так как технология нанесения пигмента в сухом виде предусматривает последующее его нагревание.
Основные требования, которым обязательно должен соответствовать растворитель:
- Во-первых, растворитель должен без особого труда смешиваться с лакокрасочным материалом и образовывать однородную массу. Это позволяет повысить качество окрашивания поверхности, а также сократить расходы на большое количество краски.
- Во-вторых, по окончанию работ, вещество должно за очень короткий срок полностью улетучиваться.
- В-третьих, реагирование растворителя с связующим и пигментов не допускается. В ином случае может произойти полное и незначительно свертывание краски. А использовать материал после этого невозможно.
Все растворители, которые используются в современной промышленности, делятся на две основные группы – неорганические и органические. Однако в ходе работ с большинством лакокрасочных материалов используются именно органические растворители: уайт-спирит, сольвент, бензин, скипидар, керосин, а также различные многокомпонентные растворители.
Расход растворителя в ходе окраски металлических изделий.
Существует огромное количество различных растворителей и все они обладают своими индивидуальными физико-химическими характеристиками. Поэтому очень важно знать какой расход растворителя на 1 кг краски того или иного типа пойдет, как добавлять растворитель, насколько быстро он улетучивается. Чтобы упростить процесс разбавления растворителя с лакокрасочных составов были созданы специальные нормативы по расходу лакокрасочных и вспомогательных материалов в ходе окраски конструкций из металла.
Такие нормативы распространяются на ЛКМ, которые применяются для антикоррозионной защиты металлических строительных сооружений и зданий на монтажной площадке. Главное назначение нормативов – это расчет контроля и потребности расходования ЛКМ при проведении различных окрасочных работ на монтажной площадке.
За основу расчетов норм расхода ЛКМ принимают норматив расхода ЛКМ. Норматив расхода – это максимально допустимое количество ЛКМ, которое нужно для получения покрытия толщиной в 1 мкм за один слой на поверхности общей площадью 1 м2. Норма расхода – это количество ЛКМ, устанавливаемое на единицу состава с учетом факторов, которые влияют на его величину. Во всех нормативных документах, за единицу расчета продукции принимают 1 тонну металлоконструкций.
К вспомогательным материалам относят растворители, а также вещества, которые входят в состав ЛКМ и являются их неотъемлемой частью в ходе нанесения на окрашиваемую поверхность. Нормы расхода отражают организационные, технологические и конструкторские особенности производства и способствуют максимальному использования материалов. Также они способствуют использованию и выявлению внутренних резервов.
Нормативы и нормы расхода растворителей.
Нормы расхода рассчитываются для нанесения ЛКМ при температуре воздуха от +15°С, не ниже. При сильных отклонениях температуры воздуха нужно обеспечить температуру рабочего состава в соответствии с указанными требованиями в нормативно-технических документациях, примерно 18-22°С.
Рассмотрим нормативы расхода растворителя для смешивания наиболее популярных видов лаков, грунтовок и эмалей.
Для лаков марки БТ-577 рекомендуется использовать уайт-спирит, скипидар или сольвент. Для пневматического распыления нужно к основному лакокрасочному материалу добавлять 15% растворителя. В случае безвоздушного распыления – 15% растворителя, а при окрашивании кистью – 10%. Такой лак как ХВ-784 разбавляется Р-4 растворителем. В этом случае для пневматического распыления понадобиться 50% растворителя, для воздушного – 25%, кистью этот лак не наносят.
Для грунтовки марки ВЛ-02 нужно купить растворитель 648, РФГ-1, толуол и Р-4. В случае пневматического и безвоздушного нанесения, степень разбавления должна составлять 20%. Кистью эта грунтовка не наносятся. Грунтовка ГФ-021 разбавляется сольвентом и ксилолом. Для пневматического распыления процентная доля растворителя в грунтовке должна составлять 15%, для безвоздушного распыления 10% и в случае нанесения кистью также 10%. Грунтовка ПФ-0142 разбавляется ксилолом. Для пневматического распыления нужно добавлять 25% растворителя, для безвоздушного 15%, а для покраски кистью – 12%. Грунтовка марки ХС-010 разбавляется только растворителем Р-4. Для пневматического способа распыления нужно добавить 40% растворителя, для безвоздушного 30%, кистью этот состав не наносится. Грунтовка ЭП-057 разбавляется растворителем РП, процентная доля должна составлять 20% для пневматического распыления и 10% для безвоздушного.
Для разбавления эмалей ПФ-115 и ПФ-133 процентная доля растворителя в составе одинаковая. Она составляет 15% для пневматического распыления, 12% для безвоздушного и 12% в случае нанесения кисточкой. Однако растворители для этих эмалей нужно использовать разные. Разбавление эмали ПФ-115 осуществляется сольвентом или скипидаром, для ПФ-133 сольвентом или ксилолом. Эмаль УРФ-1128 разбавляется сольвентом, ксилолом или уайт-спиритом. Процентная доля растворителя в веществе должна составлять 25% для пневматического распыления, 18% для безвоздушного распыления и 18% в случае нанесения кистью. Эмали ХВ-110 и ХВ-113 разбавляются растворителями Р-24. Для пневматического распыления эмалей нужно добавлять 40% растворителя, для безвоздушного 35. Кистью данные эмали не наносятся. Эмали ХВ-124 и ХВ-125 разбавляются растворителями Р4 и Р-5. Чтобы разбавить эмаль для покраски поверхности методом пневматического распыления нужно добавить 50% растворителя, в случае безвоздушного распыления – 35%.
Таким образом, знача нужную степень разбавления растворителя можно легко вычислить его расход для определенного количества краски. Например, нужно окрасить какую-либо металлическую поверхность. Для этого понадобиться 5 литр эмали ХВ-124. Для разбавления эмали этого типа нужно использовать растворитель Р-4 или Р-5. Степень разбавления эмали растворителем должна составлять 50% для пневматического распыления и 35% для безвоздушного. Таким образом, путем простых вычислений можно определить, что для окрашивания поверхности методом пневматического распыления понадобиться 2,5 л растворителя, а для безвоздушного распыления – 1,75 л.
Исследование состава эмалевого покрытия и его стойкости к коррозии парами активного металла
Реферат
После испарения металлического церия (имитация радиоактивного вещества) в пластину из нержавеющей стали в процессе производства элементы Ce и Fe взаимодиффузируют при склеивании на границе раздела фаз и образуется твердый раствор Ce-Fe. Существуют такие проблемы, как неполное восстановление прикрепленных материалов и повышенная шероховатость поверхности на границе раздела, которые нельзя использовать повторно. Чтобы уменьшить образование радиоактивных отходов, металлическое эмалевое покрытие готовят на подложке из нержавеющей стали с SiO 9 .0005 2 , Al 2 O 3 , Na 2 O, K 2 O, CaF 2 и CoO и его стойкость к активной коррозии паров металлов при высокой температуре. Результаты показывают, что эмалевое покрытие тесно связано с подложкой, образуя химическую связь фазы, богатой Fe-Co. Эмалевое покрытие может стабильно образовывать пленку с атомами металлического церия, а покрытие при испарении не отваливается. Результаты микроструктуры показывают, что оксид церия образуется на границе раздела между эмалевым покрытием и металлическим церием, образуя стабильную химическую связь. По сравнению с подложкой из нержавеющей стали отсутствует межфазная коррозия, вызванная взаимной диффузией между эмалевым покрытием и металлическим церием на границе склеивания, поэтому он может только десорбировать металлический церий без повреждения покрытия и осуществлять многократное повторное использование.
Ключевые слова
- Эмалевое покрытие
- Испарение
- Коррозия
- Диффузия
Скачать документ конференции в формате PDF
1 Введение
В процессе извлечения металла путем испарения и повторного использования пластин из нержавеющей стали возникают такие проблемы, как неполное извлечение и большое количество примесей железа. В результате пластину из нержавеющей стали можно использовать только один раз и нельзя использовать повторно много раз из-за остатков радиоактивных материалов. Хотя на этапе проверки это также вызвало большое скопление радиоактивных материалов. Поэтому необходимо исследование технологии повторного использования для реализации полного восстановления металла и многократного повторного использования пластины [1]. Атомы активных металлов обладают высокой теплопроводностью, высокой удельной теплоемкостью, низким давлением паров и другими характеристиками. Атомы металла и подложки очень легко диффундируют в процессе испарения, в результате чего металл покрытия трудно десорбируется полностью. Поэтому разработка и изготовление высокотемпературного коррозионно-стойкого покрытия против паров активных атомов металла является фактором, ограничивающим повторное использование листа [2, 3]. Традиционное высокотемпературное антикоррозионное защитное покрытие можно разделить на керамическое покрытие [4, 5] и металлическое покрытие [6, 7]. По составу в основном включает покрытие из оксида металла и другое покрытие. Благодаря составу керамики эмалевое покрытие может значительно снизить скорость коррозии. Многократное обслуживание не повлияет на состояние поверхности после пассивации. Поэтому в различных профессиональных областях имеют широкие перспективы применения.
Эмалевое покрытие является разновидностью покрытия из аморфного стекла. В процессе высокотемпературного обжига легко образовать прочное соединение с металлом или сплавом для повышения коррозионной стойкости всего листа [8–10]. Чен и др. [11] приготовили эмалевое покрытие с коэффициентом боросиликатности 0,6 (массовая доля). Температура размягчения эмали выше 750 ℃. Результаты термоудара показывают, что эксплуатационные характеристики композиционного покрытия металл-эмаль с частицами никеля значительно улучшаются. Чжу и др. [4] покрыли Ti60 эмалевым покрытием для изучения его поведения при высокотемпературном окислении и сульфатной горячей коррозии при 700 ℃ в течение 1000 ч. Эмалевое покрытие образует тонкий оксидный слой, состоящий из α-Al 9.0005 2 O 3 , TiO 2 , Al 2 SiO 5 и Al 2 TiO 5 , что обеспечивает стабильность при высоких температурах и позволяет избежать высоких температур. температурная коррозия.
Большая часть существующих исследований сосредоточена на стойкости эмалевого покрытия к высокотемпературному окислению и коррозии. Ввиду высокой потребности в восстановлении покрытия по состоянию поверхности подложки в лазерной технологии на атомарных парах [12–16] исследуется стойкость эмалевого покрытия к активной коррозии металлов при высокотемпературном испарении.
2 Состав эмалевого покрытия
Исходя из реальной ситуации эксплуатации, SiO 2 , Al 2 O 3 , Na 2 O, K 2 O, CaF 2 и CoO выбраны в качестве основных компонентов специального эмалевого покрытия. Состав гарантирует, что свободный кислород превращает все промежуточные соединения Al 2 O 3 в виде четырех координационных связей в сетку оксида кремния. Подготовлено эмалевое покрытие с высокой термостойкостью, устойчивостью к кислотной коррозии и сильной силой сцепления с нержавеющей сталью. Добавление CoO в основном связано с тем, что фаза, богатая Fe-Co, образующаяся при обжиге, может самовосстанавливать трещины в процессе эксплуатации и улучшать характеристики эмалевого покрытия при термическом ударе [17]. Состав эмалевого покрытия напрямую влияет на плотность, адгезию, кислотостойкость, твердость и другие свойства покрытия, а затем влияет на его эксплуатационные характеристики.
2.1 Технология подготовки эмалевого покрытия
В данном исследовании в качестве основного материала используется нержавеющая сталь 316L. Металлические чешуйки размером 50 мм × 50 мм ×1 мм нарезают электроразрядной проволокой. Чтобы во время обжига между порошком эмали и подложкой из нержавеющей стали формировалось больше физических и механических зубцов, требуется пескоструйная обработка для увеличения шероховатости. Используемое пескоструйное устройство показано на рис. 1.
Рис. 1.Пескоструйное оборудование.
Изображение в полный размер
Выберите корундовый песок 200–220 меш, контроль давления пескоструйной обработки менее 1 кг/см 2 , получена гладкая поверхность с матовым состоянием поверхности, как показано на рис. 2.
Рис. 2.Макро внешний вид пескоструйной обработки пластины из нержавеющей стали.
Основные компоненты эмалевой глазури (мас. %) 64,6 SiO 2 , 14,2 Al 2 O 3 , 9,61 Na 2 O, 4,65 К 2 О, 4,96 CaF 2 , 1,98 CoO. Сырье массой 500 г помещают в агатовую емкость и добавляют агатовые шарики. Затем проводят механическое перемешивание в планетарной шаровой мельнице с регулируемой скоростью 300 об/мин и временем перемешивания около 30 мин. После перемешивания сырье помещают в корундовый тигель в муфельную печь и нагревают до 1300 ℃ в течение 4 ч. Все расплавы эмали закаливают при комнатной температуре для получения эмалевой глазури. Планетарная шаровая мельница используется для сухого шарового измельчения эмалевой глазури и агатовых шаров. Скорость вращения установлена на уровне 300 об/мин, а время измельчения шаров составляет около 120 ч. Наконец, стандартное сито (200 меш) используется для просеивания порошка эмали, измельченного шариком, для удаления крупных неизмельченных частиц.
Способ приготовления специального эмалевого покрытия на поверхности подложки из нержавеющей стали заключается в смешивании спирта и порошка эмали в растворе суспензии в соотношении 2 г на 30 мл, а затем встряхивании высокочастотным ультразвуком до диспергирования в суспензию. Суспензию распыляют на поверхность нержавеющей стали методом атмосферного распыления. Давление распыления составляет около 0,3 МПа, а расстояние между соплом и пластиной из нержавеющей стали регулируется до 200 мм. Повторяющаяся последовательность распыления слева направо и сверху вниз для обеспечения однородного и гладкого покрытия эмали. Толщина каждого распыления составляет около 2 мкм в цикле распыления. Сделайте около 20 проходов, чтобы закончить распыление. Пластину из нержавеющей стали с покрытием помещают в печь и доводят до 70 ℃ на 10 минут для получения порошка. Затем он корректируется примерно до 900 ℃ в муфельной печи для обжига, и обжиг завершается примерно через 3 мин.
2.2 Поверхность раздела между эмалевым покрытием и нержавеющей сталью
На рисунке 3 показана морфология СЭМ на границе между эмалевым покрытием и матрицей из нержавеющей стали.
Рис. 3. СЭМ-морфология границы раздела эмалевого покрытия/матрицы.
Увеличить
Толщина эмалевого покрытия, образующегося при обжиге, составляет около 40 мкм, покрытие плотное, без отверстий (рис. 3). Эмалевое покрытие плотно прилегает к подложке, а поверхность имеет зазубрины. Наличие этих зазубренных поверхностей увеличивает физическую связь между покрытием и подложкой, с одной стороны. С другой стороны, зона реакции находится между покрытием и подложкой, что способствует химическому связыванию и обеспечивает хорошее сцепление покрытия с подложкой. Для дальнейшего анализа режима сцепления между эмалевым покрытием и матрицей на интерфейсе проводится анализ линейного сканирования ЭДС (рис. 4).
Рис. 4.ЭДС-сканирование границы раздела эмалевого покрытия/матрицы
Изображение в натуральную величину
Как показано на рис. 4, основным компонентом эмалевого покрытия является кремний. При наблюдении за границей обнаружено, что на границе есть переходный слой, как показано в середине двух желтых пунктирных линий. В этом переходном слое элемент Fe постепенно уменьшается от подложки к покрытию, указывая на то, что диффузия атомов Fe происходит во время подготовки покрытия. Кобальт также обнаружен в переходном слое, что подтверждает диффузию Со из покрытия к границе раздела.
3 Свойства эмалевого покрытия
3.1 Фазовая характеристика эмалевого покрытия
Фазовый состав эмалевого покрытия анализируется методом дифракции рентгеновских лучей (XRD) на образце размером 10 × 10 мм, вырезанном методом линейной резки. Используемое излучение Cu Kα (λ = 0,1548 нм), рабочее напряжение 50 кВ, скорость сканирования 2°/мин. Результаты XRD анализируют с помощью программного обеспечения Jade 6.0.
Рис. 5.Рентгенограмма эмалевого покрытия.
Полноразмерное изображение
Как видно на рис. 5, пик булочки на пару появляется на рентгенограмме под углом 25°, что является типичной морфологией аморфной структуры. Следовательно, эмалевое покрытие в основном состоит из ближней упорядоченной и дальней неупорядоченной стекловидной фазы. Также виден пик аустенита подложки.
3.2 Твердость эмалевого покрытия
Твердость эмалевого покрытия и подложки измеряется автоматическим микротвердомером. Испытательное давление 50 г, время выдержки 10 с. Средние измеренные результаты составляют 874,8 HV для эмалевого покрытия и 195.7 HV для основания из нержавеющей стали. Твердость эмалевого покрытия на поверхности из нержавеющей стали примерно в 4,5 раза выше, чем у подложки из нержавеющей стали. Повышение твердости может значительно улучшить износостойкость поверхности. Чтобы гарантировать, что поверхность заготовки не будет повреждена, когда она будет поцарапана снаружи, и поддерживать гладкую поверхность.
4 Эффективность высокотемпературного испарения
Применяется испарительное устройство с вакуумной камерой собственной разработки, предельный вакуум которого составляет 3 × 10 –4 Па. В качестве сосуда для электронно-лучевого испарения выбран медный тигель с водяным охлаждением. В качестве сырья используется металлический церий с чистотой 99,5%, а в качестве подложки используется гладкая пластина из нержавеющей стали 316 размером 360 мм × 240 мм × 1 мм и такая же пластина из нержавеющей стали с эмалевым покрытием. Мощность электронной пушки составляет 30 кВт, а температура нагрева пластины материала составляет 360 ℃. Когда степень вакуума лучше 5 × 10 –3 , металлический церий испаряется электронным лучом с образованием паров атомов металла, и начинается стабильное испарение. После испарения микроструктуру и фазовый состав границы раздела между металлическим церием и подложкой анализируют с помощью СЭМ и ЭДС.
4.1 Поверхность раздела между металлическим церием и нержавеющей сталью после испарения
Поверхность раздела между металлическим церием и нержавеющей сталью после испарения показана на рис. 6.
Рис. 6. ) 500X и (b) 100XПолноразмерное изображение
Поверхность склеивания между металлическим покрытием Ce и нержавеющей сталью хорошо видна на рис. 6a. Поверхность склеивания слегка потрескалась, и на поверхности нержавеющей стали можно наблюдать диффузию металлического церия в нержавеющую сталь. По мере того, как диффузия углубляется, диффузия слоя металлического церия приобретает характер узора. Результаты показывают, что металл Се сначала диффундировал на поверхность нержавеющей стали вдоль границы зерен нержавеющей стали 316L. Атомы металла Ce на границе зерен постепенно диффундировали в кристалл, образуя твердый раствор под термодинамическим воздействием, и, наконец, образовывали металлические соединения CeFe 2 , что согласуется с результатами рентгеноструктурного анализа. В относительно глубокой области нержавеющей стали 316L диффузионная способность атомов металла Ce ослаблена, поэтому атомы металла Ce диффундируют только вдоль границы зерна и редко диффундируют внутрь кристалла, что приводит к структурной диффузии [21]. Как видно из рис. 6b, диффузионное распределение металлического покрытия Ce относительно однородно. Распределение элементов на границе склеивания церий-нержавеющая сталь показано на рис. 7.
Спектр сканирования поверхности на границе раздела.
Изображение в полный размер
Из рис. 7а видно, что Fe диффундирует внутри металлического Ce. В отличие от диффузии металлического Се, Fe расширяется в зигзагообразную форму, что может быть связано с кристаллической структурой металлического Се и радиусом элемента Fe. Кроме того, поперечное сечение распределения элемента Cr является линейным. Это указывает на то, что элемент Cr не диффундировал внутрь металла Ce с образованием твердого раствора. Твердый раствор делится на межщелевой твердый раствор и замещающий твердый раствор. Для межзонного твердого раствора факторы его образования определяются щелью решетки, атомным радиусом и электроотрицательностью элементов. Для замещающих твердых растворов факторы образования связаны только с атомным радиусом и электроотрицательностью. Согласно табличному радиусу элемента, атомный радиус Fe составляет 64,5 пм, атомный радиус Cr до 52 пм, атомный радиус Ce 103,4 пм. Этот результат указывает на то, что твердый раствор, образованный металлом Ce и элементом Fe на границе раздела покрытия, является твердым раствором замещения.
Анализ линейного сканирования элемента на границе раздела
Изображение в полный размер
На рис. 8 показаны результаты анализа линейного сканирования поверхности подложки из селенового металла и нержавеющей стали. Из рисунка видно, что состав элементов Fe и Ce значительно менялся при изменении области сканирования. В области около 40 мкм слева и справа от границы раздела Fe и Ce представляют собой зигзаг. Этот результат еще раз доказывает, что Fe и Ce диффундировали друг в друга, а не в одну сторону. Содержание элемента Cr демонстрирует резкое изменение, что указывает на то, что элемент Cr не участвовал в диффузии. Приведенные выше результаты испытаний показывают, что пластина из нержавеющей стали подвергается коррозии атомами церия после длительного испарения, образуя диффузионный слой в десятки микрон. Из-за эффекта диффузии между металлом Се и слоем нержавеющей стали сила связи между ними высока, а атомы металла Се во внутреннем слое нержавеющей стали трудно десорбировать с помощью обработки паровым окислением, которая является корнем Причина материальной пластины не может быть использована повторно.
4.2 Поверхность раздела между металлическим церием и эмалевым покрытием после испарения
Макроморфология пластины из металлического церия и нержавеющей стали с эмалевым покрытием после испарения показана на рис. 9.
Рис. 9.Макроморфология нержавеющей стали с эмалевым покрытием стальной лист после напыления.
Увеличенное изображение
Как видно из рис. 9, эмалевое покрытие хорошо сочетается с парами церия. После взвешивания емкость осаждения левой, средней и правой пластин эквивалентна способности пластины из нержавеющей стали. Микроструктура пластины из нержавеющей стали с эмалевым покрытием на границе склеивания после пропарки представлена на рис. 10.
Рис. 10.СЭМ морфология пластины из нержавеющей стали с эмалевым покрытием после испарения
Изображение в натуральную величину после анализа ЭДС. Граница между эмалевым покрытием и матрицей по-прежнему хорошо сочетается, явных изменений по сравнению с тем, что было до эксплуатации, нет. Толщина эмалевого покрытия в основном не изменяется, что доказывает, что эмалевое покрытие может стабильно служить в целевой среде. Чтобы дополнительно проанализировать сцепление между эмалевым покрытием и автоклавами на граничном слое, анализ линейного сканирования ЭДС проводится на граничном слое эмалевого покрытия/автоклавов, и результаты показаны на рис. 11.9.0017 Рис. 11.
Карта линейного сканирования ЭДС границы раздела эмалевого покрытия/парового покрытия
Изображение в натуральную величину
Карта линейного сканирования ЭДС показывает, что на границе раздела между Се и эмалевым покрытием формируется переходная область. Толщина этой области составляет около 2 мкм, окруженной двойной желтой кривой на рис. 11. В этой переходной области содержание Si снижается, а содержание Ce увеличивается, а Si увеличивается в направлении парового золочения. Это явление указывает на то, что в переходной области происходили химические реакции, и из результатов распределения элементов можно сделать вывод о следующих реакциях. 9\text{c}}}Ceo_{2} + Si$$
(1)
Изменение свободной энергии Гиббса реакции -158,3 кДж/моль меньше -40 кДж/моль, оно может быть самопроизвольным. Восстановленные атомы Si диффундировали в металл Ce с низким содержанием Si, что приводило к обогащению элементами Si по направлению к металлическому слою Ce. Однако, как только в переходном слое образуется CeO 2 , слой CeO 2 может препятствовать дальнейшей диффузии Ce в эмалевое покрытие, тем самым предотвращая дальнейшую реакцию между Ce и эмалевым покрытием, что приводит к прекращению реакция. Из-за химической реакции, делающей эмалевое покрытие и пропаренную металлизированной, вызванной ван-дер-ваальсовой силой не только физическое соединение. Это химическая реакция с образованием химической комбинации Si, O и Ce. Так эмалевое покрытие хорошо сочетается с пропаренной металлизированной комбинацией.
4.3 Повторное использование пластины из нержавеющей стали с эмалированным покрытием
Метод травления используется для проверки возможности повторного использования пластины из нержавеющей стали с эмалированным покрытием. Изучая кислотостойкость эмалевого покрытия, можно сделать вывод, что эмалевое покрытие обладает высокой кислотостойкостью, поэтому травление не влияет на эмалевое покрытие при удалении парового золочения.
Макроморфология пластины из нержавеющей стали с эмалевым покрытием до и после травления.
Увеличить
Для того чтобы сравнить морфологию эмалевой пластины из нержавеющей стали с выпариванием до и после травления, проводят только часть травления. Травильная часть обведена желтой пунктирной линией на рис. 12. Как видно из рисунка, травильные части показывают, что гладкая поверхность эмалевого покрытия и отсутствие явления локальной коррозии показывают, что травление хорошо удаляет пар и гальванически заодно время, не повреждает основу эмали. Радужная полоса слева от травильной части должна быть разными элементами или оксидами с разными валентными состояниями одного и того же элемента. Конкретный химический состав здесь дополнительно не анализировался, но результаты локальной экспериментальной очистки разбавленной соляной кислотой показывают, что оксиды здесь также могут быть удалены травлением. Таким образом, пластина из материала с эмалированным покрытием теоретически может быть использована повторно.
5 Выводы
Характеризуя фазовый состав, состав, твердость и микроструктуру эмалевого покрытия на границе раздела покрытие-подложка, можно сделать следующие выводы.
- (1)
Эмалевое покрытие плотно прилегает к основе, а само покрытие имеет высокую плотность и низкую шероховатость. Эмалевое покрытие прочно сцеплено с подложкой благодаря химическому связыванию богатой Fe фазы Со и механическому скреплению зубов;
- (2)
Ce и Fe в нержавеющей стали будут взаимодействовать друг с другом с образованием твердого раствора, что приведет к большей шероховатости пластины из нержавеющей стали, не может быть использовано повторно;
- (3)
Эмалевое покрытие
может быть стабильным в условиях высоких температур.
Кремний и металлический церий образуют хорошую химическую связь, так что металлический пар не отпадает;
Эмалевое покрытие обладает способностью кислотной, щелочной и высокотемпературной окислительной коррозии. Режим склеивания с металлическим церием не является диффузионным, и на границе склеивания не возникает коррозии. Следовательно, травление или высокотемпературное окисление можно использовать для удаления металлического церия без повреждения эмалевого покрытия, чтобы добиться многократного повторного использования пластины материала.
Ссылки
Бринкманн У., Хартиг В., Телле Х. и др.: Изотопно-селективная фотоионизация кальция с использованием двухступенчатого лазерного возбуждения. заявл. физ. 5 , 109–115 (1974)
Google Scholar
Фромм, К.
: Теория. В: Спектральная эволюция в Blazars. СТ, стр. 11–36. Спрингер, Чам (2015). https://doi.org/10.1007/978-3-319-10768-4_2
Тан, З.Л., Ван, Ф.Х., Ву, В.Т.: Влияние напыленного покрытия TiAlCr на стойкость к окислению интерметаллического соединения TiAl. Оксид. Встретил. 48 , 511 (1997)
Google Scholar
Xiong, Y.M., Zhu, S.L., Wang, F.H.: Влияние сверхтонкого эмалевого покрытия на окисление и механические свойства сплава Ti60. Акта Металл. Грех. 40 (7), 768 (2004)
Google Scholar
Ляо, Ю.М., Фэн, М., Чен, М.Х., и др.: Сравнительное исследование поведения в условиях горячей коррозии композитных покрытий на основе эмали и дугового ионного покрытия NiCrAlY на сплаве TiAl. Акта Металл. Грех. 55 (2), 61–69 (2019)
Google Scholar
“>Ni, Y.R., Lu, CH, Zhang, Y.: Влияние редкоземельных элементов на стеклообразование и тепловое расширение бороалюмосиликатного стекла. Китайские редкоземельные элементы 27 (1), 83–86 (2006)
Google Scholar
An, Z.B., Zhang, P.Y., Shen, X.J., и др.: Влияние CeO 2 на микроструктуру и термостойкость высокотемпературного эмалевого покрытия W-2. Технология горячей обработки. 20 (45), 140–142 (2016)
Google Scholar
Хан, Т., Ван, Ю., Чен, Ю.Х. и др.: Влияние оксида церия на адгезионную способность стеклянного покрытия и основного металла.
Дж. Унив. Нефть 26 (5), 68–70 (2002)
Google Scholar
Чжу, Ю.М., Ван, Д.В.: Исследования теплообмена в бассейне тигля с помощью тепла электронной пушки. Атомная энергия наук. Технол. 34 (3), 238–243 (2000)
Google Scholar
Ли, Ф.Дж., Чен, М.Х., Чжан, З.М., и др.: Подготовка и термостойкость металл-эмалевого высокотемпературного защитного покрытия. Дж. Чин. соц. Защита от коррозии 39 (5), 411–416 (2019)
Google Scholar
Xiao, J.X., Wang, D.W.: Исследование теплообмена расплавленной полости с границей раздела твердое тело-жидкость, нагретой электронным лучом в тигле. Университет Дж. Цинхуа. д.т.н. 39 (10), 56–59 (1999)
Google Scholar
“>Xiao, J.X., Wang, D.W.: Исследование испарения атомов металла с помощью двухмерных стационарных потоков. Атомная энергия наук. Технол. 34 (3), 244–251 (2000)
Google Scholar
Се, Г.Ф., Ван, Д.В., Ин, К.Т.: Влияние коллекторной пластины на двухмерное испарение металла. Университет Дж. Цинхуа. (Наука и техника) 42 (5), 584–586 (2002)
Google Scholar
Юань, К.Х., Сюй, П.Ф., Ю, П.З. и др.: Исследование извлечения ионов при лазерном разделении изотопов. Дж. У. Мол. физ. 10 (3), 2839–2843 (1993)
Google Scholar
“>Li, W., Chen, M., Wu, M., et al.: Микроструктура и поведение при окислении SiC-Al 2 O 3 – стеклокомпозитное покрытие на Ti-47Al-2Cr- сплав 2Nb. Коррос. науч. 87 , 179–186 (2014)
Google Scholar
Wang, X., Chen, M., Zhu, S., et al.: Поведение при окислении композитного теплозащитного покрытия на основе стекла на суперсплаве K417G со связующим покрытием NiCoCrAlY при 1000 ℃. Серф. Пальто. Технол. 270 , 314–323 (2015)
Google Scholar
Ю, З.Д., Чен, М.Х., Чен, К. и др.: Коррозия эмали с CaF 2 и без него в расплавленном алюминии при 750 ℃. Коррос. науч. 148 , 228–236 (2019)
Google Scholar
“>
Го, К.А., Чен, М.Х., Ляо, Ю.М. и др.: Исследование механизма защиты композитных покрытий на основе эмали при моделировании удара горючего газа. Акта Металл. Грех. 54 (12), 113–120 (2018)
Google Scholar
Xiao, J.X., Wang, D.W.: Численное моделирование динамического процесса двумерного испарения металла. Дж. Цинхуа. ун-т (Наука и техника) 39 (10), 52–55 (1999)
Google Scholar
Shao, G.X., Gou, W.B., Wen, RC, et al.: Enamal. Издательство легкой промышленности, Пекин (1983)
Google Scholar
Чен, К., Чен, М.Х., Ю, З.Д., и др.: Изучение механизма, препятствующего элементу Ti прилипанию эмали/стали, содержащей CoO в один слой. Междунар. Дж. Заявл. Керам. Технол. 16 , 185–194 (2019)
Google Scholar
Ссылки для скачивания
Информация об авторе
Авторы и организации
The 404 Company Limited, China National Nuclear Corporation, Lanzhou, 732850, China
Y Ф. Цзян, Х. Ю. Ли, Дж. Чен, С. К. Ши и Ю. Х. Чжу
- Ю. Ф. Цзян
Посмотреть публикации автора
Вы также можете искать этого автора в PubMed Google Scholar
- H. Y. Li
Просмотр публикаций автора
Вы также можете искать этого автора в PubMed Google Scholar
- J. Chen
Просмотр публикаций автора
Вы также можете искать этого автора в PubMed Google Scholar
- X.
Q. Shi
Просмотр публикаций автора
Вы также можете искать этого автора в PubMed Google Академия
- Y. X. Zhu
Посмотреть публикации автора
Вы также можете искать этого автора в PubMed Google Scholar
Автор, ответственный за переписку
Ю. Ф. Цзян.
Информация для редактора
Редакторы и филиалы
Институт ядерной энергетики Китая, Чэнду, Китай
Ченгминь Лю
Права и разрешения
90 004 Открытый доступ Эта глава находится под лицензией Creative Commons Attribution 4.0 International License (http://creativecommons.org/licenses/by/4.0/), которая разрешает использование, совместное использование, адаптацию, распространение и воспроизведение на любом носителе. или формате, при условии, что вы укажете первоначальных авторов и источник, предоставите ссылку на лицензию Creative Commons и укажите, были ли внесены изменения.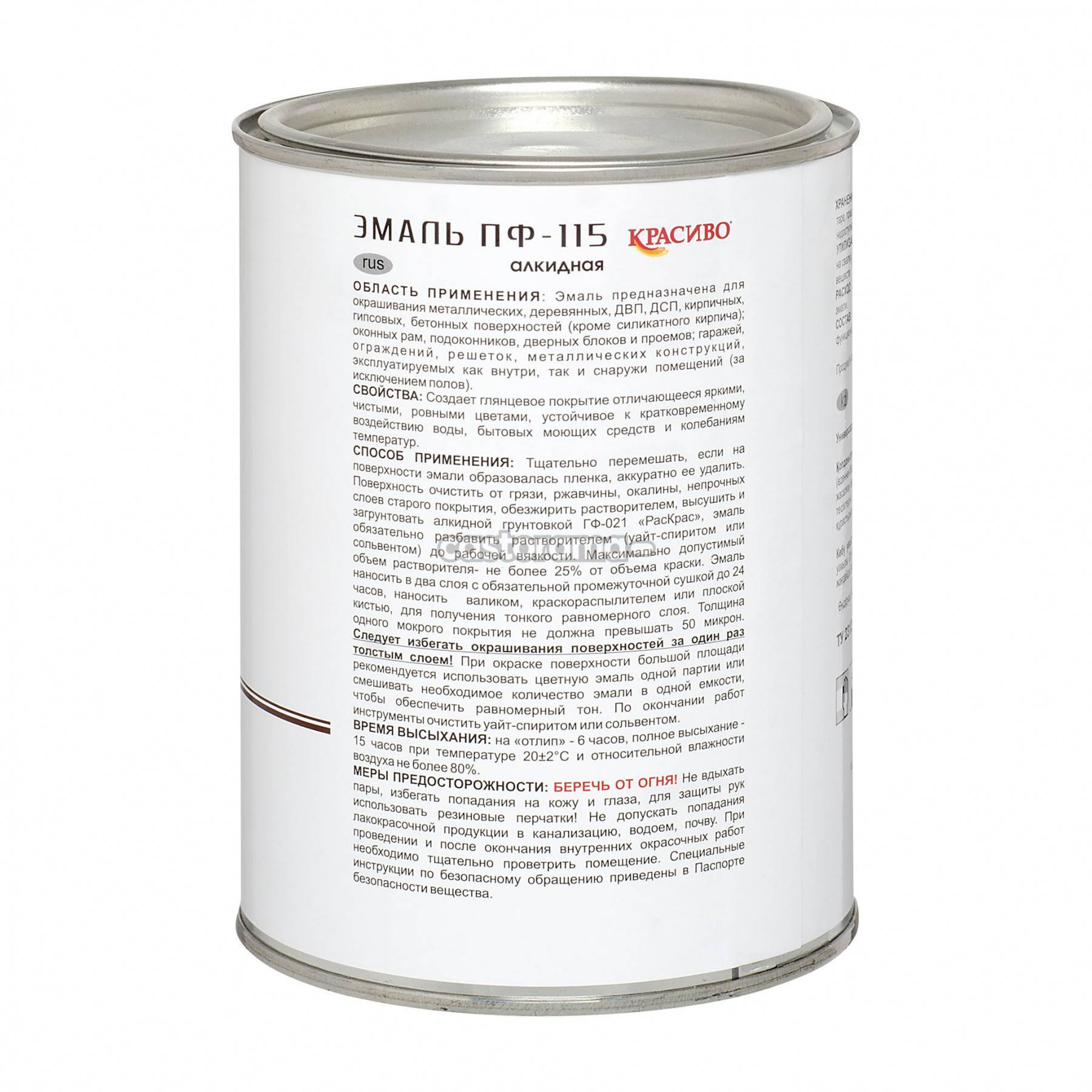
Изображения или другие сторонние материалы в этой главе включены в лицензию Creative Commons главы, если иное не указано в кредитной линии к материалу. Если материал не включен в лицензию Creative Commons главы, а предполагаемое использование вами не разрешено законом или выходит за рамки разрешенного использования, вам необходимо получить разрешение непосредственно от владельца авторских прав.
Перепечатки и разрешения
Информация об авторских правах
© 2023 Автор(ы)
О статье
Модульный пляжный комплекс – Vizdome Space
Полуфиналист международного конкурса-фестиваля Архив 2 021 в номинации «Курортный территории».
Проект представляет собой пляжный комплекс, который можно построить на берегу любого водоема в короткие сроки. Все здания комплекса – входной модуль, летние кафе, торговые павильоны, павильоны проката оборудования и мебели, технические модули – построены из типовых панелей заводского производства, что ускоряет строительство, упрощает доставку строительных материалов на площадку, а также помогает свести к минимуму загрязнение окружающей среды. Модульный пляж предназначен для сезонного использования.
Каркас стеновых панелей изготовлен из стальных изогнутых швеллеров высотой 60 мм. К швеллерам крепятся деревянные планки толщиной 25 мм внутри и толщиной 15 мм снаружи. Таким образом, общая толщина панелей составляет 100 мм. В качестве утеплителя в панелях используется полиуретан, КНАУФ Аквапанель Наружная используется в качестве внешней части стеновых панелей, КНАУФ и КНАУФ Аквапанель Внутренняя используются в качестве внутренней изоляции во влажных помещениях. Стеновые панели соединяются с панелями пола и друг с другом обычными прецизионными болтами. Пластины крепятся к раме с помощью шурупов, швеллеры соединяются друг с другом сваркой с 3 мм приварным коленом. Для монтажа инженерных коммуникаций внутри каркаса располагаются полипропиленовые трубы 40 мм, они крепятся к швеллеру пластиковыми стяжками. Металлоконструкции окрашиваются в два слоя эмали ПФ-115 и грунтовки ХФ-021, общая толщина покрытия не менее 55 мкм. В качестве внутренней и внешней отделки используется сосновая доска.
В панелях пола используются швеллеры высотой 140 мм. Если панель выполняет функцию кровли, то нижний слой панели – это гипсокартон Кнауф, а по верхнему слою укрепляются плиты Кнауф Аквапанель Аутдор на деревянном брусе толщиной 60 мм. Верхнее покрытие крыши – жидкая резина. Если панель служит напольным покрытием, то верхний слой – гипсовые плиты Кнауф Брио, а нижний – Кнауф Аквапанель Наружная. Для утепления, как и в стенах, служит поролон.
Благоустройство территории комплекса осуществляется путем размещения нестационарных объектов различного назначения. Также на пляже устроены пешеходные дорожки. Они изготовлены из композитной доски поверх деревянных брусков. Комплекс оснащен инженерным оборудованием, обеспечивающим наличие системы канализации и холодного водоснабжения. Дно акватории и пляжная зона перед началом купального сезона и в течение сезона очищается от стекла, острых камней, водорослей и других источников опасности. Ежегодно перед началом сезона в прибрежную зону насыпают чистый песок и гальку, рыхлят и выравнивают верхний слой песка.
Планировка комплекса предусматривает функциональное зонирование прибрежной зоны и акватории. При входе на пляж есть информационный щит, на котором размещена вся необходимая посетителям информация.
Граница зон купания на акватории обозначена буями оранжевого цвета, которые располагаются на расстоянии 20 – 30 м друг от друга. Расстояние между буями может быть уменьшено в зависимости от размера зоны купания и местных условий. Максимальное расстояние от воды до буев зависит от местных условий и технических возможностей спасательных служб.
На пляже есть спасательный и медицинский пункты. Спасательная служба, аварийно-спасательное оборудование и инструменты, медицинское оборудование и средства первой помощи размещены в административном павильоне. Также по всей территории пляжа рассредоточены медицинские посты на расстоянии не более 150 м друг от друга. Береговая линия оборудована наблюдательными вышками спасательного поста на расстоянии 100-150 м друг от друга.
Пляжная зона оборудована общественными туалетами из расчета 75 посетителей на туалет, кабинками для переодевания из расчета 1 кабина на 50 человек, навесами и стационарными зонтами на 40% посетителей пляжа, ящиками на каждые 1600 м 2 и контейнеры для мусора на каждые 3500 – 4000 м 2 пляжной зоны.
На общественном пляже есть зона для людей с ограниченными возможностями. Дорожки и площадки спроектированы из композитной доски поверх стойкого к агрессивным средам деревянного бруса. На платформах есть теневые навесы и зонты для отдыха людей в инвалидных колясках. Туалеты, душевые и раздевалки на этом участке спроектированы с учетом потребностей людей с ограниченными возможностями.
Пляж оборудован стационарными постами охраны для круглосуточного наблюдения за обстановкой. Посты охраны оборудованы системой видеонаблюдения для наблюдения за обстановкой на пляже и на территории от входа в воду.
Ориентировочная площадь застройки 11 200 м 2 , площадь пляжа в 20-метровой зоне – 3350 м 2 . Площадь дорожек – 1171 м 2 , кафе – 765 м 2 , пляжных сооружений – 495 м 2 , спортивных площадок – 360 м 2 , площадок для аттракционов – 255 м 2 .
Архитектурное бюро Vizdome Space создает дизайн-проекты пляжей, баз отдыха, эко-гостиниц в стиле модерн.