Сколько блоков газобетона в 1 кубе: вес и размеры
Содержание
- 1 Размеры (с примерами)
- 2 Вес
- 3 Что влияет на вес газоблока?
- 4 Плотность
- 5 Размеры
- 6 Расчет веса блока
- 7 Сколько блоков газобетона в 1м3 (пример расчета)
- 8 Вывод
При помощи газоблоков можно строить долговечные здания высотой до 16 м. Сегодня популярность газоблоков стремительно растет. На современном рынке стройматериалов представлены блоки, плотность которых составляет D600, D700. Так как в строительстве высотных зданий автоклавный ячеистый бетон начинает шире использоваться, то и плотность газоблоков в будущем будет увеличиваться. Газобетон – стройматериал, в котором не содержатся вредные добавки. Его использование не вредит окружающей среде. Материал огнеупорен, морозоустойчив, не подвергается гниению, коррозии, обладает хорошими гидрофобными характеристиками. Внутри помещений, построенных из газобетона, создается определенный микроклимат.
В жаркое время в таких строениях прохладно, а в зимние месяцы – тепло. Блок из этого строительного материала содержит около 60 процентов мелких пузырьков воздуха, что обеспечивает звукоизоляцию и необходимый температурный режим в помещении. Это свойство блоков определяет их удельный вес. Объем стройматериала измеряется в кубе. Речь идет об условном обозначении стройматериала с внутренними размерами 1 м на 1 м. Размеры могут быть и другими, важно, чтобы произведение трех величин (ширина, высота, длина) было равно единице.
Размеры (с примерами)
Производители стройматериалов выпускают два вида газобетонного блока:
- прямоугольной формы;
- в виде буквы U (такие изделия часто применяются для создания перемычек).
Стандартные газоблоки бывают таких размеров:
- длина – 600 или 625 миллиметров;
- высота – 200 либо 250 миллиметров;
- ширина – 85-400 миллиметров.
Вышеуказанные параметры являются самыми распространенными, однако ширину стройматериалов можно изменить. Благодаря небольшому весу газобетонные изделия легко поддаются обработке, поэтому их размер можно с легкостью изменить. Блоки, выпускаемые в форме буквы U, выпускается в следующих параметрах:
- высота – 250 миллиметров;
- длина – 500 или 600 миллиметров;
- ширина – 200-400 миллиметров.
При покупке блока необходимого размера нужно учитывать параметры стенок и помещения (квадратные метры). Также необходимо рассчитать, сколько штук газоблоков вам понадобится для кладки в несколько метров. Кроме того, важно принимать во внимание назначение конструкций. В частности, для возведения наружных бетонных стенок подойдут газоблоки, минимальная ширина которых составляет 200 миллиметров. Для проведения работ внутри помещения часто используется блок шириной 85 миллиметров.
Вернуться к оглавлению
Вес
На удельном весе газобетонного блока сказываются заполнители, которые используются при их изготовлении. За счет удельного веса материал разделяют на несколько групп:
- Особо легкие. В структуре изделий содержится множество (85 процентов) ячеек с воздухом. Зачастую такие строительные материалы используются для утепления зданий. 1 м3 бетона этого вида, как правило, весит менее 500 килограммов.
- Легкие. Представляют собой растворы с наполнителями вроде ракушечника или керамзита (газоблоки, пеноблоки). Вес кубометра стройматериала составляет 500-1 800 килограммов, – все зависит от плотности стройматериала. Наиболее тяжелым компонентом смеси является песок.
- Тяжелые. Этот вид изделий считается более распространенным, чем все остальные. В состав раствора входят гравий, щебенка. Именно эти компоненты определяют, сколько будет весить блок. В большинстве случаев кубометр стройматериала весит около двух тонн и более. На массу бетона влияют цемент, щебенка, песок.
- Особо тяжелые. Такая смесь считается самой редкой. В растворе весом две с половиной-три тонны основную его массу составляет заполнитель крупных размеров.
Вернуться к оглавлению
Что влияет на вес газоблока?
Вес блока зависит от плотности.Вес газоблока будет зависеть от плотности. Эта величина указана на марке. К примеру, обозначение D600 указывает на то, что плотность газобетона составляет 600 килограммов на кубометр. Таким образом, в 1м3 насчитывается 600 килограммов газобетона. Если известно значение плотности, рабочие могут высчитать массу одной или нескольких штук газоблоков. Для проведения расчетов нужно узнать, сколько газоблоков насчитывается в одном кубометре. К примеру, одно изделие марки D500, размеры которого составляют 200 на 300 на 600 миллиметров, весит около 18 килограммов.
Вернуться к оглавлению
Плотность
Наиболее распространенными среди строителей стали стеновые газобетонные изделия. Их принято применять для возведения несущих стен и конструкций. Так как они постоянно выдерживают значительные нагрузки, их плотность должна соответствовать марке D400 или D500.
Вернуться к оглавлению
Размеры
Самый распространенный размер газобетона.Газобетон считается стеновым, когда толщина бетонной кладки превышает 20 сантиметров. Размеры кладки 20 или 25 сантиметров чаще всего встречаются в монолитно-каркасном и одноэтажном строительстве (сооружения, для которых не нужно особое энергосбережение). При проведении монолитно-каркасных строительных работ специалисты часто пользуются газобетонными изделиями, толщиной в 25 сантиметров. В итоге при отоплении, а также плотности бетона D500 такая толщина стеновой кладки по энергосбережению сравнима с толщиной кирпичной кладки толщиной в один м. Самыми распространенными считаются блоки высотой 20 миллиметров, шириной 30 сантиметров и длиной 60 миллиметров.
Вернуться к оглавлению
Расчет веса блока
Для определения удельного веса одного куба газобетона необходимо высчитать количество газоблоков в кубе. Нужно один куб поделить на объем изделия. Таким образом, можно рассчитать нужное значение. После этого количество следует умножить на массу единицы. Получившаяся цифра и есть вес куба материала.
Вернуться к оглавлению
Сколько блоков газобетона в 1м3 (пример расчета)
Если вам необходимо рассчитать, сколько газоблоков в одном кубе, нужно произвести два действия. Прежде всего, следует измерить параметры одного газоблока и определить объем изделия в кубометрах. После этого единицу необходимо разделить на число, полученное ранее. К примеру, если параметры составляют 300 на 250 на 625 миллиметров, то для расчета объема одного газоблока, необходимо высчитать произведение всех сторон изделия в метрах. Получается: 0,3*0,25*0,6 = 0,04 кубометра. Затем разделим один кубометр на объем газоблока: 1:0,04 = 21.3…штук. Таким образом в одном кубе 21 штука газоблоков.
Чтобы определить размеры газобетонных изделий, можно зайти на интернет-сайты их производителей, – там можно найти таблицы, в которых указаны все значения. Узнав, сколько именно штук газоблоков насчитывается в одном кубометре, вы можете приступать к расчетам количества стройматериала для строительства. Все зависит от параметров будущего сооружения. Чтобы сделать необходимые подсчеты материала, кроме его количества важно учитывать вес. Таким образом, зная число газоблоков и вес одного кубометра материала, вы сможете рассчитать общую массу.
Вернуться к оглавлению
Вывод
Использование современных строительных материалов помогает создавать надежные и долговечные конструкции с хорошими эксплуатационными характеристиками. К таким стройматериалам относится газобетон. Из него конструируются газоблоки, которые обладают звукоизоляционными, теплоизоляционными свойствами и небольшим весом.
Масса блоков позволяет в значительной степени упростить кладку.
Сколько штук блоков газобетона в кубе?
Данная статья относится к общеобразовательным и я постараюсь в ней не только расписать, но и разжевать основы математики первого класса школы, поэтому не обижайтесь если подумаете, что тут все написано для тех, кто на бронепоезде. Многие действительно не понимают смысла этого вопроса, а поэтому, чтобы в сезон продаж не заниматься репетиторством менеджеры в чатах будут отправлять Вас на эту страницу.
Что такое куб? Сколько кубов газобетона в кладке?
Кубом материала называется условный объем материала, заключенный в ящичек с размерами метр на метр на метр или любыми другими размерами но таким образом, чтобы произведение высоты, ширины и длины ящичка было равно единице. Материалом может быть что угодно: кирпич, газобетон, экструдированный пенополистирол, и т.д. и т.п. В классическом математическом кубе все три стороны ящичка равны единице. На рисунке справа изображен ответ на вопрос Что такое куб леса? Ящички, кубатуру которых нужно подсчитать бывают разные. Идеальных математических моделей с идеальными размерами 1мх1мх1м в природе не существует, а поэтому люди придумали как перевести в кубатуру размеры различных ящичков, набитых строительными материалами. Например предположим, что вы имеете стену из газобетона толщиной 30см, высотой 4 метра и длиной 8 метров. Основным математическим правилом рассчетов является необходимость приведения всех размеров в единую единицу измерения. В данном случае это будут метры. Как сантиметры перевести в метры? Нужно количество сантиметров разделить на 100. Как милиметры перевести в метры? Нужно количество милиметров разделить на 1000. В нашем задании две стороны указаны в метрах, а одна в сантиметрах, поэтому сантиметры переведем в метры. Для этого 30см разделим на 100 и получим толщину стены 0,3 метра. Как узнать кубатуру кладки? Нужно толщину стены из газобетона умножить на высоту стены и на ее длину. В нашем конкретном случае имеем: – высота стены – 4 метра; – толщина стены – 0,3 метра; – длина стены – 8 метров. 4 х 0,3 х 8 = 9,6 кубических метров. Просто? – Ато! Скоро вам будет не нужен архитектор 🙂 А сколько блоков газобетона было задействовано в эту стену? Для этого нам необходимо ответить на главный вопрос этой статьи: Сколько блоков газобетона в одном кубе!
Сколько блоков из газобетона в одном кубе?
Для того, чтобы ответить на этот вопрос необходимо выполнить всего два математических действия: а) узнать сколько кубов содержится в одном блоке б) единицу разделить на то, что получилось в пункте “а”. Почему делить нужно единицу? – Потому, что вы спрашиваете сколько блоков из газобетона в одном кубе, а не в пяти. Если бы вы спросили сколько блоков из газобетона в 5 кубах – я бы предложил вам сначала узнать сколько кубов содержится в одном газоблоке, а потом 5 разделить на то, что получили. Как будем узнавать сколько кубов в одном блоке из газобетона? Для этого нам нужно знать размеры одного блока. Прежде чем просить менеджера что-то подсчитать Вы должны обязательно определиться с размерами и производителями газобетона, который желаете приобрести! Мы ведь не экстрасенсы, а обычные люди. Итак предположим, что в кладку использовались стандартные блоки с размерами 200мм х 300мм х 600мм. Так, как говорим о кубическом метре, то миллиметры нужно перевести в метры. Получим размеры блока в метрах: 0,2м (200мм/100)х0,3м (300мм/100)х0,6м (600мм/100) Сократим для нормального восприятия эту строку до 0,2м х 0,3м х 0,6м = 0,036 м.куб. Итак, в одном блоке из газобетона размером 200*300*600мм содержится 0,036 м.кубических. Сколько блоков из газобетона в одном кубе? 1куб разделить на 0,036 = 27,77777777… Округлим до 27,78 штук. Итак, в одном кубическом метре содержится 27,78 штук газобетона. Если учесть, что самый дешевый блок из газобетона сегодня стоит 600грн/куб, То потеря на неграмотности и незнании математики составит: (600/28)*0,22=4,72грн*50 кубов = 235грн. Вроде бы мелочь, но если вместо блоков с размерами 200х300х600 вам подсунут экономы с размерами 200х288х588, то потеря на 50и кубах будет около 1500грн.
Вы думаете, что экономите покупая дешевый блок? Возьмите калькулятор и почитайте эту статью! | |||||
Формы-кубы для пенобетона – Специалисты по пенобетону
Формы-кубы для пенобетона
Пенобетон не следует испытывать с использованием традиционных стальных форм-кубов. отверждению на воздухе в течение заданного периода испытаний.
Изоляционные свойства полистирола позволяют образцам отверждаться и гидратироваться аналогично изоляционному пенобетонному материалу, из которого взят образец, и, следовательно, дает гораздо более близкий репрезентативный результат прочности.
Полистирол обеспечивает изоляцию и защиту от вибрации для кубов из свежего пенобетона, позволяя защитить ячеистую структуру в течение критического начального периода схватывания.
Полистирол, несмотря на то, что он относительно слаб и не соответствует стандартам BS:EN для изготовления традиционных бетонных кубов, обеспечивает идеальную оболочку для пенобетона. Традиционный бетон необходимо утрамбовать в кубе, после высыхания его необходимо зачистить и вылечить в воде, все это не требуется для пенобетона и вызовет неблагоприятные последствия.
Полистироловые формы также можно использовать для отбора проб цементного раствора, растворов, стяжек, проб грунта и многих других материалов.
Большое количество 100-мм и 150-мм кубических форм хранится на складе, их можно приобрести с доставкой на следующий день.
Чтобы узнать актуальные цены, позвоните в офис по телефону 01322 429 900 или по электронной почте info@propump.co.uk
10-литровые сосуды с калиброванной плотностью используются для отбора проб плотности материала, затем этот сосуд используется для производства набора 3 кубические формы на месте для последующего измельчения Полистироловые кубические формы производства Propump Engineering используются для испытаний и на месте.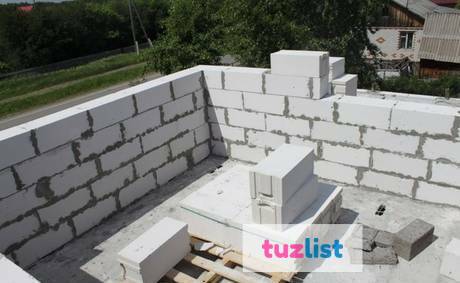
Использование форм-кубов на месте
Одноразовые формы-кубики после заполнения обычно оставляют на месте для отверждения перед перемещением.
Полистирол представляет собой прекрасную основу для записи информации об идентификации куба, месте заливки и дате заливки, а также гарантирует, что вся информация может быть четко записана и передана испытательной лабораторией, проводящей процессы испытаний на прочность.
После первоначальной сборки и готовности кубов к транспортировке они, как правило, собираются сторонней лабораторией, прошедшей аудит и одобренной для тестирования бетона. Затем они хранятся до необходимого возраста для тестирования. Затем образцы вынимают из полистироловых форм и испытывают в обычном режиме.
Propump ежедневно использует 150-миллиметровые кубические формы в рамках собственного процесса контроля и обеспечения качества, производя наборы из трех кубов для каждого испытания, проводимого в качестве репрезентативного образца укладываемого материала. Кубики обычно тестируют через 28 и 90 дней (2 через 28 дней, 1 через 90 дней), если не указано иное.
Консультационные услуги Propump
Выезд специалистов Propump Engineering по пенобетону и консультационные услугиУзнайте больше
Новости и статьи Propump
Поточная система производства пенобетона обеспечивает наиболее точный и эффективный метод производства пенобетонов на местеПочему стоит выбрать пенобетон?
Пенобетон Области применения, включая использование жидких и сыпучих материалов для стабилизации грунта и засыпкиПроекты Propump
Пенобетон, используемый для прокладки туннелей Crossrail, засыпки из пенобетона, туннелей и машин для проходки ТБМ Формы для пенобетонаБольшое количество форм для пенобетона 100 мм и 150 мм хранится на складе, их можно приобрести с доставкой на следующий день.
Чтобы узнать актуальные цены, позвоните в офис по телефону 01322 429 900 или по электронной почте info@propump. co.uk
Свойства и внутреннее отверждение бетона, содержащего переработанный автоклавный газобетон в качестве заполнителя
На этой странице
РезюмеВведениеМатериалыРезультатыВыводыКонфликты интересовСсылкиАвторское правоСтатьи по теме
Глобальное потепление является жизненно важной проблемой для всех секторов во всем мире, включая строительную отрасль. Для достижения концепции «зеленых» технологий было предпринято множество попыток разработать продукты с низким углеродным следом. В строительном секторе автоклавный газобетон (AAC) стал более популярным и производится для удовлетворения строительного спроса. Однако ошибки производственного процесса составляют примерно от 3 до 5% производства газобетона. Разработка отходов AAC в качестве легкого заполнителя в бетоне является одним из потенциальных подходов, которые подробно изучались в этой статье. Результаты показали, что прочность на сжатие бетона AAC-LWA снижалась с увеличением объема и крупности. Оптимальной пропорцией смеси был размер заполнителя AAC от 1/2″ до 3/8″ с заменой от 20 до 40% на заполнитель нормальной массы. Также наблюдалось внутреннее отверждение AAC-LWA, которое обеспечивало достаточное количество воды внутри образцов, что приводило к достижению более высокой прочности на сжатие. Основной целью этого исследования является не только утилизация нежелательных промышленных отходов (переработка отходов), но и получение новых знаний об использовании AAC-LWA в качестве внутреннего отвердителя, а также производство легких бетонных изделий с добавленной стоимостью.
1. Введение
Для достижения концепции технологии зеленого строительства было предпринято множество попыток разработать продукты или методы с низким уровнем выбросов углерода. Подход к преобразованию отходов из любых промышленных секторов в новое сырье для других отраслей привлек гораздо больше внимания в обществе без отходов. Как правило, самым простым устранением промышленных отходов является их использование в качестве заменителя цемента или бетона, например, добавки к цементу или заполнители для бетона. В Таиланде, несмотря на то, что обычная кирпичная кладка делается из местного глиняного кирпича, с запуском блоков из легкого автоклавного газобетона (AAC) они становятся новым выбором для инженеров и строителей, поэтому становятся все более и более популярными в строительной отрасли. Однако сообщалось, что лом и отходы от общего производства газобетонных блоков составляли примерно от 3 до 5% (58 тонн в месяц), в результате чего огромное количество остатков газобетонных блоков направлялось непосредственно на засыпанную площадку (рис. 1). Использование отходов газобетона в качестве легкого заполнителя в производстве бетона является одним из потенциальных подходов, который не только полезен для утилизации промышленных побочных продуктов и снижения энергопотребления, но также полезен для повышения прочности за счет внутреннего отверждения и уменьшения конечного бетона. вес [1, 2].
Внешнее отверждение – распространенный метод достижения достаточной гидратации портландцемента, что может быть достигнуто путем предотвращения потери влаги на поверхностях, обертывания любыми мокрыми покрытиями или даже погружением образцов бетона в водяную баню. Однако в некоторых случаях эффективность внешнего отверждения может быть ограничена из-за неудовлетворительного проникновения воды для отверждения в образцы из-за физического барьера или геометрии компонентов бетона [3]. Внутреннее отверждение является альтернативным подходом, заключающимся в использовании внутреннего резервуара с водой для отверждения внутри бетонных смесей. Уже доказано, что внутреннее твердение позволяет значительно повысить прочность и снизить автогенную усадку конечных бетонных изделий [4, 5]. В качестве внутреннего твердеющего заполнителя может быть использован любой легкий пористый материал (например, вермикулит, перлит, пемза, шлак, керамзит, керамзит, дробленые отходы газобетона) [6, 7], так как они могут поглощать воду при приготовлении и смешивании и затем постепенно высвобождать запасенную воду внутри смесей в процессе затвердевания [8]. Кроме того, шероховатая поверхность и крупная пористая структура этих легких заполнителей также могут способствовать блокировке в переходных зонах между цементным тестом и заполнителем (соединенные поверхности), что приводит к улучшению механических свойств [9].
].
Основной целью данной статьи является использование имеющихся местных отходов газобетона в качестве легкого заполнителя в производстве бетона, что может позволить преобразовать промышленные отходы в продукты с добавленной стоимостью. Легкий вес и высокоравномерная пористость являются ключевыми характеристиками газобетона, который может служить материалом для внутреннего отверждения, обеспечивающим достаточные условия отверждения для бетонной конструкции. Были исследованы подходящие размеры и оптимальный процент замены газобетонного заполнителя, а также конечные свойства свежего и затвердевшего бетона во время внутреннего отверждения.
2. Материалы и препараты
Портландцемент представлял собой товарный сорт I типа с удельным весом 3,15. В качестве мелкого заполнителя использовали местный речной песок с удельным весом и модулем крупности 2,39 и 2,90 соответственно. Влажность песка составила 0,80 % при насыпной плотности 1645 кг/м 3 . Крупный заполнитель представлял собой товарный гравий от местных поставщиков. Удельный вес, влажность и насыпной вес составляли 2,70, 0,50% и 1540 кг/м 9 .0081 3 соответственно. Отходы AAC были собраны в компании PCC Autoclave Concrete Company Limited, Чиангмай, Таиланд. Его удельный вес составлял 1,06 при массе сухой единицы 360 кг/м 3 . Полученный AAC со значением водопоглощения от 28 до 30% был измельчен до более мелкого размера с помощью стандартной щековой дробилки (рис. 2).
Затем градацию крупных заполнителей AAC анализировали с помощью стандартного ситового анализа США. Эффективный крупный размер, использованный в этом исследовании, составлял от 3/8” (90,5 мм) и 3/4 (19,0 мм), которые составляют около 50% от общего количества агрегатов AAC и имеют средний модуль крупности 7,20 (таблица 1). Отмечается, что большинство эффективных значений размера AAC-LWA составляли 3/4″, 1/2″ и 3/8″, а классы размера (как указано с S1 по S4) замены крупных заполнителей были поэтому используется в эксперименте. Маркировка смесей и описания бетонных смесей, включая классы крупности AAC-LWA, показаны в Таблице 2.
Распределение крупного заполнителя, товарного сорта и размеров в сравнении ASTM C33 с номером крупности 67. На Рисунке 3 показаны распределение по размерам крупнозернистых заполнителей нормальной массы (NWCA), используемых в смеси NC. Было обнаружено, что распределение размера заполнителя с нормальной массой находится между 1/2″ и 3/8″ и в основном соответствует верхней и нижней границам стандарта размера 67 ASTM C33. Кроме того, в зависимости от размера класса S1–S4, распределения размера замены AAC-LWA на агрегат нормальной массы на 20, 40 и 60% (LWA20, LWA40 и LWA60) также нанесены на верхнюю и нижнюю границы Критерий ASTM C33 номер 67.
По мере того, как определенные размеры классов AAC-LWA (S1–S4) были заменены на нормальную градацию товарного гравия, графики распределения размеров начали смещаться к верхнему пределу границ ASTM C33 (рис. 4). Видно, что группа всех размеров класса LWA20 тесно выровнена внутри верхней границы (рис. 4(а)). Более того, линии распределения по размерам, по-видимому, сместились вправо за верхний предел, когда количество замены AAC-LWA увеличилось с LWA40 (рис. 4(b)) до LWA60 (рис. 4(c)) во всех классах размеров. Таким образом, присутствие заполнителей AAC-LWA не только влияет на общую градацию крупного заполнителя бетона, но также может влиять на механические свойства конечного результата затвердевания бетона.
3. Детали эксперимента
3.1. Обозначения смесей
Обозначения смесей были выполнены в соответствии со стандартом ACI 211.1 для бетонных смесей. В контролируемую смесь (Normal Concrete, NC) с водоцементным (в/ц) отношением 0,35 добавляли заполнители нормальной массы с наибольшим размером частиц 3/4’’. Требуемая осадка бетона задается от 5 до 10 см. Кроме того, в смесях с отходами газобетона в виде легковесных заполнителей (ААС-LWA) объем нормальных заполнителей замещался насыщенным поверхностно-сухим (SSD) AAC-LWA, а именно 20, 40 и 60%, соответственно. Отмечается, что общий вес замены AAC-LWA рассчитывался из того же объема обычного заполнителя в кубометре бетона. Например, замена 20% AAC-LWA (LWA20), поскольку объемная плотность заполнителей нормальной массы и AAC-LWA составляла 1540 и 360 кг/м 3 соответственно, 188 кг заполнителей нормальной массы были заменены на 46 кг AAC-LWA. Все бетонные смеси смешивались в смесителе с опрокидывающимся барабаном до достижения подходящих условий. Затем свежий бетон подвергали испытанию на удобоукладываемость и помещали в подготовленные формы. Через 24 часа все образцы бетона были извлечены из формы и выдержаны в специально разработанных режимах твердения, водного и воздушного твердения. Пропорции смеси представлены в таблице 3.
3.2. Аналитические методы
Свойства свежего бетона определялись испытаниями на осадку и текучесть. Испытание на осадку бетона проводили по стандарту ASTM C143. Величина осадки 10 см. был установлен в соответствии с ACI 213R-87, который рекомендуется для строительства перекрытий, колонн и конструкций несущих стен. Текучесть бетона измеряли с помощью таблицы потоков вместе со стандартом ASTM C124. Свойства затвердевшего бетона определялись как стандартными, так и минутными испытаниями на прочность на сжатие. После извлечения из формы (в последующие 24 часа) все образцы отверждались в воде или на воздухе до достижения ими возраста испытаний 1, 3, 7 и 28 сут. Вес и размеры всех образцов измеряли перед дальнейшей обработкой для расчета кажущейся плотности. Стандартное испытание на прочность на сжатие всех цилиндрических образцов (диаметром 15 см и высотой 30 см) было проведено с использованием универсальной испытательной машины (UTM) в соответствии со стандартом ASTM C39.. С помощью оптического микроскопа наблюдали межфазную переходную зону (ITZ) AAC-LWA и цементного теста.
Минимальная прочность на сжатие (кубический образец 3 × 3 × 3 мм) была введена и проведена в этом испытании, чтобы определить влияние AAC-LWA на внутреннее отверждение [10]. Для изготовления образцов для испытаний на мельчайшую прочность используются образцы размером 150 × 150 × 150 мм. бетонный куб был замешан и отвержден в проектных условиях. Три места бетонного куба (внешняя зона и внутренние зоны) были вырезаны на 15 × 15 × 150 мм. призмы (рис. 5). Затем каждая призма была разрезана на слои толщиной 3 мм с размерной длиной 3 × 15 × 15 мм, а именно, L1, L2 и L3. Отмечается, что слой L1 находился рядом с AAC-LWA, а слои L2 и L3 были дополнительно выровнены (рис. 6). Эти слои (L1, L2 и L3) были окончательно разрезаны на 3 × 3 × 3 мм. кубов (рис. 7), а затем тестировался с помощью стандартного контрольного кольца, прикрепленного к UTM.
4. Результаты и обсуждение
4.1. Испытание на осадку
Результаты испытания бетона на осадку показаны на рис. 8. Классы размера AAC-LWA, обозначенные как S1, S2, S3 и S4 (см. Таблицу 2), не имели существенных различий в ходе испытания. Осадка контролируемого бетона (NC) составляла 5,80 см, в то время как значения осадки бетона AAC-LWA имели тенденцию к увеличению с более высоким процентом замены заполнителя AAC, например, примерно с 7,50 см. (LWA20) примерно до 10,60 см. (LWA60). Фактически, острая форма и шероховатая поверхность AAC-LWA могут уменьшить величину осадки из-за блокировки и внутреннего трения между материалами [11]. Однако в данном случае в величине осадки в основном преобладала водоудерживающая способность, избыток воды на поверхности частиц ААС. Таким образом, было увеличено водоцементное отношение, что привело к увеличению значения осадки бетона. Сингх и Сиддик (2016) сообщили об аналогичном результате, согласно которому материалы с высокой поглощающей способностью (например, зола угольного остатка) могут действовать как резервуар для воды и повышать конечное водоцементное отношение бетонных смесей [12].
4.2. Тест на текучесть
Не было выявлено существенной разницы в текучести между контролируемой смесью (NC) и смесями AAC-LWA. Средний поток бетона AAC-LWA, казалось, немного уменьшился, когда увеличилась замена заполнителя AAC. Среднее значение потока NC составило 53,3%, тогда как средние значения потока смесей LWA20, LWA40 и LWA60 составили 55%, 56% и 53% соответственно (рис. 9). Однако, поскольку значения текучести находились в диапазоне от 50 до 100%, бетонные смеси AAC-LWA были классифицированы как смеси средней консистенции, которые можно было легко укладывать и уплотнять в формы в процессе заливки.
4.

Как показано на рисунке 10, кажущаяся плотность контролируемой смеси (НК) составляла около 2380 кг/м 3 в возрасте 28 дней. Кроме того, общая кажущаяся плотность бетона LWA20 была немного снижена примерно на 3-4% до примерно 2290-2310 кг/м 3 по сравнению со смесью NC. Для смесей LWA40 и LWA60 кажущаяся плотность постоянно снижалась на 8–9 % (от 2 160 до 2 180 кг/м 3 ) и от 13 до 15% (от 2030 до 2070 кг/м 3 ) соответственно. Аналогичные результаты были получены Hossain et al. (2011) и Topçu и Işikdaǧ (2008), которые заменили заполнители нормальной массы пемзой и перлитом в качестве крупных заполнителей бетона [13]. Можно сделать вывод, что общая плотность бетона AAC-LWA значительно уменьшилась из-за замены LWA, так как его плотность составляла всего 360 кг/м 3 . Напротив, прочность на сжатие является следующей проблемой, которую необходимо рассматривать как наиболее важные свойства затвердевшего бетона.
4.4. Стандартное испытание на прочность при сжатии
Стандартное испытание на прочность при сжатии с использованием цилиндрических образцов проводили в возрасте 1, 3, 7 и 28 дней. Было изучено сравнительное измерение прочности между водой и сухим воздухом, включая классы размеров, которые представлены на рисунках 11 (a)–11 (c).
Хорошо видно, что все смеси, отвержденные в воде, достигли большей прочности, чем смеси, отвержденные в сухом воздухе, так как была достигнута большая степень гидратации [14]. Класс размера заполнителя S4-AAC (см. Таблицу 2) получил самую высокую прочность среди классов S1, S2 и S3 благодаря хорошей градации крупных заполнителей в бетонных смесях в соответствии с ASTM C33 № 67. Также была достигнута более плотная структура. а также соответствующее переплетение хорошо отсортированного крупного заполнителя. Сопоставимое улучшение прочности, очевидно, было получено за счет более высокой плотности затвердевшего цементного теста в межфазной переходной зоне (ITZ) при внутреннем отверждении [15]. Примеры нормального сцепления (NWCA) и хорошего сцепления (AAC-LWA) представлены на рисунке 12. Можно видеть, что разрушение NWCA с нормальным сцеплением произошло на цементном тесте, в то время как хорошо связанный AAC-LWA был разрушен. на агрегате AAC. Помимо свойств прочности каждого заполнителя, AAC-LWA явно продемонстрировал потрясающие характеристики сцепления в ITZ. Тем не менее, окончательная прочность газобетона в качестве заполнителя снижалась при увеличении количества AAC-LWA, потому что газобетон имеет чрезвычайно низкую несущую способность по сравнению с заполнителем нормальной массы.
4.5. Испытание на минутную прочность на сжатие
Минутная прочность на сжатие – это метод, используемый для проверки эффекта внутреннего отверждения пористым заполнителем в бетонных смесях. Прочность на сжатие 3×3×3 мм. Кубические образцы смесей LWA20, LWA40 и LWA60 (все с размерами класса S4, отвержденные на воздухе) были испытаны и представлены на рисунке 13. Очевидно, что прочность образцов, отобранных из внешней зоны, оказалась ниже прочности, чем у образцов, взятых из внешней зоны. внутренней зоны. Кроме того, прочность образца L1 (L1; слой, следующий за заполнителем AAC) явно достигла более высокой механической прочности, чем у дальних слоев, L2 и L3 (см. Рисунок 6). В целом, более полнота процесса внутренней гидратации газобетона-LWA может быть достигнута за счет водоудерживающей способности бетонной смеси. В частности, для пористых заполнителей дополнительная вода для внутреннего отверждения была получена не только за счет водопоглощения, но и за счет адсорбции воды, что непосредственно влияет на воду для отверждения бетона на более поздних стадиях [16]. Кроме того, процесс внутреннего отверждения также будет происходить с «капиллярным всасыванием», при котором происходит перенос воды из более крупных пор в более мелкие. В этом исследовании капиллярные поры агрегатов AAC (от 50 до 100 микрон, мкм мкм) были больше, чем у средних пор цементного теста (от 1 до 100 нанометров, нм).
При этом условии некоторое количество воды, запасенной в газобетонных заполнителях, будет, таким образом, передано цементному тесту через ITZ, повышая уровень гидратации цементных вяжущих. На улучшение прочности в более позднем возрасте в основном повлияло большее образование C-S-H и более плотные микроструктуры [9]. Использование AAC-LWA в насыщенном сухом состоянии (SSD) в этом исследовании обеспечило бы более высокую прочность во всех случаях, чем AAC-LWA в исходном/сухом состоянии [15]. Причина в том, что полученный AAC-LWA может активно поглощать воду в системе на начальной стадии смешивания. На ИТЗ появлялись микропоры и неполные микроструктуры, что отрицательно сказывалось на конечных свойствах бетона [15]. Те же самые тенденции и результаты были получены для минутной прочности на сжатие размеров LWA20, LWA40 и LWA60 класса S4, отвержденных в воде. Поскольку с внешней и внутренней стороны подавалось достаточное количество лечебной воды, средняя прочность 3×3 мм. cube, таким образом, был немного выше, чем другие, отвержденные в условиях сухого открытого воздуха (рис. 14).
4.6. Развитие прочности и взаимосвязь между стандартной и минимальной прочностью на сжатие
Развитие прочности слоя 1 (L1) при минутном сжатии в течение 7 и 28 дней представлено в таблице 4. При сохранении NC в качестве эталонной смеси, LWA20 достигла наибольшего разница в развитии прочности во всех условиях: 34,00 % (AC L1 Ext.), 51,10 % (AC L1 Int.), 33,33 % (WC L1 Ext.) и 42,80 % (WC L1 Int.). Между внешней и внутренней зонами LWA20 (26,98 % и 35,32 %) и LWA40 (39,03 % и 54,99 %), как показано в таблице 5. Очевидно, что минимальная прочность на сжатие в условиях отверждения на воздухе (AC) может быть улучшена с помощью режимов внутреннего отверждения, особенно для внутренняя зона. Оптимальные пропорции AAC-LWA, при которых внутреннее отверждение дает наибольшую пользу, находятся в диапазоне от LWA20 до LWA40 смесей.
Напротив, самая высокая минутная прочность на сжатие слоя 1 (L1) также была нанесена на график относительно стандартной цилиндрической прочности на сжатие с размером класса S4 в возрасте 7 и 28 дней. На Рисунке 15 представлено соотношение этой минутной и стандартной прочности на сжатие образцов, отвержденных в условиях отверждения в сухом воздухе (АС), как в их внешней зоне (Рисунок 15(а)) так и во внутренней зоне (Рисунок 15(б)). Как упоминалось ранее в разделе 4.4, средняя стандартная прочность на сжатие бетона AAC-LWA снизилась, когда количество замены AAC-LWA увеличилось с 35,1 МПа (7 d) и 41,2 МПа (28 d) в смесях LWA20 до примерно 26,2 МПа (7 d). г) и 28,1 МПа (28 d) в смесях LWA60. Однако ясно видно, что смеси LWA20 и LWA40, кажется, достигают более высокой прочности, чем у бетона с нормальным заполнителем (NC).
Минутная прочность на сжатие (как указано в разделе 4.5) внутренней зоны явно выше, чем внешней из-за внутреннего отверждения AAC-LWA с самым высоким значением смеси LWA20. Исследование показало, что замена AAC-LWA от 20% до 40% (LWA20 и LWA40) может быть оптимальной пропорцией для бетона AAC-LWA.
Этим можно объяснить, что эти пропорции в основном обеспечивают превосходную прочность заполнителя нормальной массы, в то время как подходящее количество замены заполнителя AAC обеспечивает дополнительное количество воды для внутреннего отверждения цементного теста. Увеличение образования C-S-H не только упрочняет бетонную матрицу, но и обеспечивает хорошее сцепление между газобетонным заполнителем и цементным тестом на их ВТЗ. Аналогичная тенденция увеличения прочности была обнаружена в образцах, отвержденных в условиях отверждения в воде (WC), как показано на рисунке 16. Кроме того, как упоминалось ранее, общая прочность на сжатие как мелких, так и стандартных образцов была значительно выше, чем у образцов, отвержденных в сухом воздухе. так как было получено достаточное количество воды для лечебных целей. Несмотря на небольшую разницу в прочности на сжатие между водяным и воздушным отверждением, запас воды в переработанном газобетонном заполнителе, по-видимому, не является необходимым для обеспечения влаги для дальнейшего процесса гидратации цемента, эффективность наружного отверждения может быть ограничена из-за неудовлетворительного проникновения твердеющей воды в образцы, и внутреннее отверждение затем расширит положительный режим отверждения изнутри бетонной конструкции в реальных приложениях (например, огромная конструкция или бетонный компонент).
5. Выводы
По результатам исследования выводы можно резюмировать следующим образом.
На значения оползня повлияло содержание воды. Величина осадки имеет тенденцию к увеличению с увеличением замены AAC-LWA по мере получения дополнительной воды на поверхности заполнителя. Однако значения текучести всех смесей были аналогичны бетону с нормальным заполнителем (NC) и относились к категории средней консистенции с текучестью от 50 до 60%.
Кажущаяся плотность уменьшилась, когда количество замены AAC-LWA увеличилось с 2380 кг/м 3 (NC) примерно до 2050 кг/м 3 (LWA60). Хотя минимальная плотность в этом испытании (2030 кг/м 3 в смеси LWA60) не соответствовала критериям легкого бетона, рекомендованным ACI 213R-87 при 1850 кг/м 3 , более низкое значение плотности в качестве альтернативы может быть достигается за счет увеличения доли AAC-LWA или даже за счет использования легких мелких заполнителей (например, легкого песка или зольного остатка).
Стандартная прочность на сжатие цилиндрических образцов была снижена с более высоким соотношением AAC-LWA как при отверждении в сухом воздухе, так и при отверждении в воде, даже несмотря на то, что при отверждении в воде достигается несколько более высокая прочность на сжатие. Смешанный размер AAC-LWA (размер класса S4) обеспечивал удовлетворительную градацию и превосходную прочность, чем одиночные заполнители (S1, S2 и S3).
Наивысшая прочность при небольшом испытании на сжатие была достигнута при размере 3 × 3 × 3 мм. куб, расположенный в слое 1 (L1), за которым следуют слой 2 (L2) и слой 3 (L3) соответственно. Можно сделать вывод, что внутреннее отверждение AAC-LWA, очевидно, улучшает прочность бетона, обеспечивая дополнительный внутренний водный ресурс для более возможного образования C-S-H. В сочетании с незначительной и стандартной прочностью на сжатие оптимальные пропорции замены AAC-LWA находились в диапазоне от LWA20 до LWA40. Эти пропорции смеси в основном обеспечивали превосходную прочность по сравнению с заполнителем нормальной массы, в то время как подходящее количество замены заполнителя AAC обеспечивало дополнительное количество воды для внутреннего отверждения цементного теста.
Разработка AAC в качестве замены крупного заполнителя в бетоне связана не только с утилизацией нежелательных промышленных отходов (переработка отходов), но и с накоплением новых знаний об использовании LWA в качестве внутреннего отвердителя, а также с производством ценных материалов. добавлены изделия из легкого бетона.
Конфликт интересов
Авторы заявляют об отсутствии конфликта интересов.
Ссылки
И.-Ж. Чиоу, К.-С. Ван, К.-Х. Чен и Ю.-Т. Лин, «Легкий заполнитель из осадка сточных вод и сжигаемой золы», Управление отходами , том. 26, нет. 12, стр. 1453–1461, 2006.
Посмотреть по адресу:
С. Чжао, К. Ли, М. Чжао и С. Чжан, «Экспериментальное исследование автогенной усадки и усадки при высыхании бетона с легким заполнителем, армированного стальным волокном», Достижения в области материаловедения и инженерии , об. 2016 г., идентификатор статьи 2589383, 9 страниц, 2016 г.
Посмотреть по адресу:
Сайт издателя | Академия Google
П. Лура, М. Выжиковски, К. Тан и Э. Леманн, «Внутреннее отверждение с легким заполнителем, полученным из отходов, полученных из биомассы», Cement and Concrete Research , vol.
59, стр. 24–33, 2014 г.
Посмотреть по адресу:
Сайт издателя | Google Scholar
Б. Акчай и М. А. Тасдемир, «Оптимизация использования легких заполнителей для уменьшения автогенной деформации бетона»,
Строительство и строительные материалы, , том. 23, нет. 1, стр. 353–363, 2009 г..Посмотреть по адресу:
Сайт издателя | Google Scholar
Комитет ACI 213, Guild for Structural Lightweight Increte Concrete , Американский институт бетона, Детройт, Мичиган, штат Мичиган, США, 1999.
Легкий бетон, содержащий смешанный цемент и заполнитель на основе пемзы: механические и прочностные характеристики», Строительство и строительные материалы , том. 25, нет. 3, стр. 1186–119.5, 2011.
Посмотреть по адресу:
Сайт издателя | Google Scholar
Д.
Сари и А. Г. Пасамехметоглу, «Влияние градации и добавок на бетон с легким заполнителем из пемзы», Cement and Concrete Research , vol. 35, нет. 5, стр. 936–942, 2005.Посмотреть по адресу:
Сайт издателя | Google Scholar
С. Вебер и Х. В. Рейнхардт, «Новое поколение высокоэффективного бетона: бетон с самоотверждением», Усовершенствованные материалы на основе цемента , vol. 6, нет. 2, стр. 59–68, 1997.
Посмотреть по адресу:
Сайт издателя | Google Scholar
Т. Ю. Ло, Х. З. Цуй и З. Г. Ли, «Влияние предварительного увлажнения заполнителя и летучей золы на механические свойства легкого бетона», Управление отходами, , том. 24, нет. 4, стр. 333–338, 2004 г.
Посмотреть по адресу:
Сайт издателя | Google ScholarW.
Yodsudjai, Оценка прочности и диффузии ионов хлорида в мельчайших участках бетона с использованием недавно разработанных методов [Ph.D. диссертация] , Токийский технологический институт, Япония, 2003 г.
Тан В. К., Райан П. К., Цуй Х. З. и Ляо В., «Свойства самоуплотняющегося бетона с переработанным крупным заполнителем», Достижения в области материаловедения и инженерии , том. 2016 г., идентификатор статьи 2761294, 2016 г.
Посмотреть по адресу:
Сайт издателя | Google Scholar
М. Сингх и Р. Сиддик, «Влияние золы угольного остатка в качестве частичной замены песка на удобоукладываемость и прочностные свойства бетона», Журнал чистого производства , том. 112, стр. 620–630, 2016.
Посмотреть по адресу:
Сайт издателя | Google Scholar
И. Б. Топчу и Б. Ишикда, «Влияние расширенного перлитного заполнителя на свойства легкого бетона», Journal of Materials Processing Technology , vol.
204, нет. 1–3, стр. 34–38, 2008 г.
Посмотреть по адресу:
Сайт издателя | Google Scholar
P. Wattanachai, N. Otsuki, T. Saito и R. Wongjeeraphat, «Влияние условий отверждения на свойства раствора из летучей золы mae moh на поверхности и внутри», в Proceedings of the Proceeding of the 6th Regional Symposium on Infrastructure Development , Бангкок, Таиланд, январь 2009 г. Использование пористых керамических заполнителей для внутреннего отверждения высокопрочного бетона»,
Cement and Concrete Research , vol. 39, нет. 5, стр. 373–381, 2009 г.Посмотреть по адресу:
Сайт издателя | Академия Google
R. Kasemchaisiri и S. Tangtermsirikul, «Метод определения водоудерживающей способности пористого мелкого заполнителя для проектирования и контроля качества свежего бетона», Construction and Building Materials , vol.