Π‘ΠΎΡΡΠ°Π² ΠΏΠΎΡΡΠ»Π°Π½Π΄ΡΠ΅ΠΌΠ΅Π½ΡΠ°, Π΅Π³ΠΎ Π²Π·Π°ΠΈΠΌΠΎΠ΄Π΅ΠΉΡΡΠ²ΠΈΠ΅ Ρ Π²ΠΎΠ΄ΠΎΠΉ, ΠΏΡΠΎΠΈΠ·Π²ΠΎΠ΄ΡΡΠ²ΠΎ
ΠΠΎΡΡΠ»Π°Π½Π΄ΡΠ΅ΠΌΠ΅Π½Ρ ΡΠ°ΡΡΠΎ Π½Π°Π·ΡΠ²Π°Π΅ΡΡΡ ΠΏΡΠΎΡΡΠΎ ΡΠ΅ΠΌΠ΅Π½ΡΠΎΠΌ β ΡΡΠΎ Π²Π°ΠΆΠ½Π΅ΠΉΡΠ΅Π΅ ΠΌΠΈΠ½Π΅ΡΠ°Π»ΡΠ½ΠΎΠ΅ Π²ΡΠΆΡΡΠ΅Π΅ Π²Π΅ΡΠ΅ΡΡΠ²ΠΎ. ΠΠΎΡΠΎΡΠΊΠΎΠΎΠ±ΡΠ°Π·Π½ΡΠΉ ΠΌΠ°ΡΠ΅ΡΠΈΠ°Π», ΡΠΎΠ΄Π΅ΡΠΆΠ°ΡΠΈΠΉ ΠΈΡΠΊΡΡΡΡΠ²Π΅Π½Π½ΡΠ΅ ΠΌΠΈΠ½Π΅ΡΠ°Π»Ρ, Π±ΠΎΠ»ΡΡΠΈΠ½ΡΡΠ²ΠΎ ΠΊΠΎΡΠΎΡΡΡ
Π² ΠΏΡΠΈΡΠΎΠ΄Π΅ Π½Π΅ Π²ΡΡΡΠ΅ΡΠ°ΡΡΡΡ ΠΈΠ»ΠΈ Π²ΡΡΡΠ΅ΡΠ°ΡΡΡΡ ΠΊΡΠ°ΠΉΠ½Π΅ ΡΠ΅Π΄ΠΊΠΎ. ΠΡΠΈ ΠΌΠΈΠ½Π΅ΡΠ°Π»Ρ ΠΎΠ±Π»Π°Π΄Π°ΡΡ Π²ΡΡΠΎΠΊΠΎΠΉ Ρ
ΠΈΠΌΠΈΡΠ΅ΡΠΊΠΎΠΉ Π°ΠΊΡΠΈΠ²Π½ΠΎΡΡΡΡ ΠΈ ΡΠΏΠΎΡΠΎΠ±Π½Ρ Π²Π·Π°ΠΈΠΌΠΎΠ΄Π΅ΠΉΡΡΠ²ΠΎΠ²Π°ΡΡ Ρ Π²ΠΎΠ΄ΠΎΠΉ. ΠΠΎΡΡΠ»Π°Π½Π΄ΡΠ΅ΠΌΠ΅Π½ΡΠΎΠΌ Π½Π°Π·ΡΠ²Π°Π΅ΡΡΡ Π³ΠΈΠ΄ΡΠ°Π²Π»ΠΈΡΠ΅ΡΠΊΠΎΠ΅ Π²ΡΠΆΡΡΠ΅Π΅ Π²Π΅ΡΠ΅ΡΡΠ²ΠΎ, ΠΏΠΎΠ»ΡΡΠ°Π΅ΠΌΠΎΠ΅ ΡΠΎΠ½ΠΊΠΈΠΌ ΠΈΠ·ΠΌΠ΅Π»ΡΡΠ΅Π½ΠΈΠ΅ΠΌ ΠΏΠΎΡΡΠ»Π°Π½Π΄ΡΠ΅ΠΌΠ΅Π½ΡΠ½ΠΎΠ³ΠΎ ΠΊΠ»ΠΈΠ½ΠΊΠ΅ΡΠ° Ρ Π³ΠΈΠΏΡΠΎΠΌ ΠΈ Π΄ΡΡΠ³ΠΈΠΌΠΈ ΡΠΏΠ΅ΡΠΈΠ°Π»ΡΠ½ΡΠΌΠΈ Π΄ΠΎΠ±Π°Π²ΠΊΠ°ΠΌΠΈ. ΠΠ»ΠΈΠ½ΠΊΠ΅Ρ ΠΏΠΎΠ»ΡΡΠ°ΡΡ ΠΎΠ±ΠΆΠΈΠ³ΠΎΠΌ Π΄ΠΎ ΡΠΏΠ΅ΠΊΠ°Π½ΠΈΡ ΡΠΎΠ½ΠΊΠΎΠ΄ΠΈΡΠΏΠ΅ΡΡΠ½ΠΎΠΉ ΠΎΠ΄Π½ΠΎΡΠΎΠ΄Π½ΠΎΠΉ ΡΡΡΡΠ΅Π²ΠΎΠΉ ΡΠΌΠ΅ΡΠΈ, ΡΠΎΡΡΠΎΡΡΠ΅ΠΉ ΠΈΠ· ΠΈΠ·Π²Π΅ΡΡΠ½ΡΠΊΠ°, Π³Π»ΠΈΠ½Ρ, ΠΊΡΠ΅ΠΌΠ½Π΅Π·ΡΠΌΠ°. ΠΠΈΠΏΡ Π²Π²ΠΎΠ΄ΠΈΡΡΡ Ρ ΡΠ΅Π»ΡΡ ΡΠ΅Π³ΡΠ»ΠΈΡΠΎΠ²Π°Π½ΠΈΡ, ΡΠΊΠΎΡΠΎΡΡΠΈ ΡΡ
Π²Π°ΡΡΠ²Π°Π½ΠΈΡ ΠΈ Π½Π΅ΠΊΠΎΡΠΎΡΡΡ
Π΄ΡΡΠ³ΠΈΡ
ΡΠ²ΠΎΠΉΡΡΠ². ΠΠ»ΠΈΠ½ΠΊΠ΅ΡΠ½ΡΠΉ ΠΏΠΎΡΠΎΡΠΎΠΊ Π±Π΅Π· Π³ΠΈΠΏΡΠ° ΠΏΡΠΈ ΡΠΌΠ΅ΡΠΈΠ²Π°Π½ΠΈΠΈ Ρ Π²ΠΎΠ΄ΠΎΠΉ Π±ΡΡΡΡΠΎ ΡΡ
Π²Π°ΡΡΠ²Π°Π΅ΡΡΡ ΠΈ Π·Π°ΡΠ²Π΅ΡΠ΄Π΅Π²Π°Π΅Ρ Π² ΡΠ΅ΠΌΠ΅Π½ΡΠ½ΡΠΉ ΠΊΠ°ΠΌΠ΅Π½Ρ Ρ ΠΏΠΎΠ½ΠΈΠΆΠ΅Π½Π½ΡΠΌΠΈ ΠΏΡΠΎΡΠ½ΠΎΡΡΠ½ΡΠΌΠΈ ΡΠ²ΠΎΠΉΡΡΠ²Π°ΠΌΠΈ. Π‘ΠΎΠ³Π»Π°ΡΠ½ΠΎ ΠΠΠ‘Π’ 1581-96 Π² ΠΏΠΎΡΡΠ»Π°Π½Π΄ΡΠ΅ΠΌΠ΅Π½Ρ ΡΠ°Π·ΡΠ΅ΡΠ°Π΅ΡΡΡ Π²Π²ΠΎΠ΄ΠΈΡΡ ΠΏΡΠΈ ΠΏΠΎΠΌΠΎΠ»Π΅ Π΄ΠΎ 15 % Π°ΠΊΡΠΈΠ²Π½ΡΡ
ΠΌΠΈΠ½Π΅ΡΠ°Π»ΡΠ½ΡΡ
Π΄ΠΎΠ±Π°Π²ΠΎΠΊ. ΠΡΠΈ ΡΡΠΎΠΌ, Π½Π°Π·Π²Π°Π½ΠΈΠ΅, ΡΠ΅ΠΌΠ΅Π½ΡΠ° Π½Π΅ ΠΌΠ΅Π½ΡΠ΅ΡΡΡ. Π‘Π²ΠΎΠΉΡΡΠ²Π° ΠΏΠΎΡΡΠ»Π°Π½Π΄ΡΠ΅ΠΌΠ΅Π½ΡΠ° ΠΎΠΏΡΠ΅Π΄Π΅Π»ΡΡΡΡΡ, ΠΏΡΠ΅ΠΆΠ΄Π΅ Π²ΡΠ΅Π³ΠΎ, ΠΊΠ°ΡΠ΅ΡΡΠ²ΠΎΠΌ ΠΊΠ»ΠΈΠ½ΠΊΠ΅ΡΠ°.
Π‘ΡΠΈΡΠ°Π΅ΡΡΡ, ΡΡΠΎ ΠΏΠΎΡΡΠ»Π°Π½Π΄ΡΠ΅ΠΌΠ΅Π½Ρ Π±ΡΠ» ΠΈΠ·ΠΎΠ±ΡΠ΅ΡΠ΅Π½ Π² ΠΠ½Π³Π»ΠΈΠΈ ΠΊΠ°ΠΌΠ΅Π½ΡΠΈΠΊΠΎΠΌ ΠΠΆΠΎΠ·Π΅ΡΠΎΠΌ ΠΡΠΏΠ΄ΠΈΠ½ΠΎΠΌ, ΠΊΠΎΡΠΎΡΡΠΉ ΠΏΠΎΠ»ΡΡΠΈΠ» ΠΏΠ°ΡΠ΅Π½Ρ Π² 1824 Π³ΠΎΠ΄Ρ Π½Π° ΠΈΠ·Π³ΠΎΡΠΎΠ²Π»Π΅Π½ΠΈΠ΅ Π²ΡΠΆΡΡΠ΅Π³ΠΎ Π²Π΅ΡΠ΅ΡΡΠ²Π° ΠΈΠ· ΡΠΌΠ΅ΡΠΈ ΠΈΠ·Π²Π΅ΡΡΠΈ Ρ Π³Π»ΠΈΠ½ΠΎΠΉ ΠΎΠ±ΠΆΠΈΠ³ΠΎΠΌ Π΅Ρ Π΄ΠΎ ΠΏΠΎΠ»Π½ΠΎΠ³ΠΎ ΡΠ΄Π°Π»Π΅Π½ΠΈΡ ΡΠ³Π»Π΅ΠΊΠΈΡΠ»ΠΎΡΡ. ΠΡΠΎ Π²ΡΠΆΡΡΠ΅Π΅ ΠΎΠ½ Π½Π°Π·Π²Π°Π» ΠΏΠΎΡΡΠ»Π°Π½Π΄ΡΠ΅ΠΌΠ΅Π½ΡΠΎΠΌ. ΠΠ΄Π½Π°ΠΊΠΎ Π² Π ΠΎΡΡΠΈΠΈ, ΠΏΠΎΡΡΠ»Π°Π½Π΄ΡΠ΅ΠΌΠ΅Π½Ρ Π±ΡΠ» ΠΏΠΎΠ»ΡΡΠ΅Π½ Π½Π΅ΡΠΊΠΎΠ»ΡΠΊΠΎ ΡΠ°Π½Π΅Π΅, Π² 1817 Π³ΠΎΠ΄Ρ Π½Π°ΡΠ°Π»ΡΠ½ΠΈΠΊΠΎΠΌ Π²ΠΎΠ΅Π½Π½ΠΎ-ΡΠ°Π±ΠΎΡΠ΅ΠΉ ΠΊΠΎΠΌΠ°Π½Π΄Ρ Π. Π. Π§Π΅Π»ΠΈΠ΅Π²ΡΠΌ. Π 1825 Π³ΠΎΠ΄Ρ ΠΈΠΌ Π±ΡΠ»Π°: ΠΈΠ·Π΄Π°Π½Π° ΠΊΠ½ΠΈΠ³Π° ΠΎ ΠΏΠΎΠ»ΡΡΠ΅Π½ΠΈΠΈ Π²ΡΠΆΡΡΠ΅Π³ΠΎ Π²Π΅ΡΠ΅ΡΡΠ²Π°, Π°Π½Π°Π»ΠΎΠ³ΠΈΡΠ½ΠΎΠ³ΠΎ ΠΏΠΎ ΡΠΎΡΡΠ°Π²Ρ ΠΏΡΠΈΠΌΠ΅Π½ΡΠ΅ΠΌΠΎΠΌΡ Π½ΡΠ½Π΅ ΠΏΠΎΡΡΠ»Π°Π½Π΄ΡΠ΅ΠΌΠ΅Π½ΡΡ.
ΠΡΡΠΎΡΠΈΡΠ΅ΡΠΊΠ°Ρ ΡΠΏΡΠ°Π²ΠΊΠ°
ΠΠΎΡΡΠ»Π°Π½Π΄ΡΠ΅ΠΌΠ΅Π½ΡΠ½ΡΠΉ ΠΊΠ»ΠΈΠ½ΠΊΠ΅Ρ ΠΈ Π΅Π³ΠΎ Ρ ΠΈΠΌΠΈΡΠ΅ΡΠΊΠΈΠΉ ΡΠΎΡΡΠ°Π²
ΠΠΎΡΡΠ»Π°Π½Π΄ΡΠ΅ΠΌΠ΅Π½ΡΠ½ΡΠΉ ΠΊΠ»ΠΈΠ½ΠΊΠ΅Ρ ΠΎΠ±ΡΡΠ½ΠΎ ΠΏΠΎΠ»ΡΡΠ°ΡΡ Π² Π²ΠΈΠ΄Π΅ ΡΠΏΡΠΊΡΠΈΡ
ΡΡ ΠΌΠ΅Π»ΠΊΠΈΡ
ΠΈ Π±ΠΎΠ»Π΅Π΅ ΠΊΡΡΠΏΠ½ΡΡ
Π³ΡΠ°Π½ΡΠ» ΠΈ ΠΊΡΡΠΊΠΎΠ² ΡΠ°Π·ΠΌΠ΅ΡΠΎΠΌ Π΄ΠΎ 10-20 ΠΈΠ»ΠΈ Π΄ΠΎ 50-60 ΠΌΠΌ Π² Π·Π°Π²ΠΈΡΠΈΠΌΠΎΡΡΠΈ: ΠΎΡ ΡΠΈΠΏΠ° ΠΏΠ΅ΡΠΈ. ΠΠΎ ΠΌΠΈΠΊΡΠΎΡΡΡΡΠΊΡΡΡΠ΅ ΠΊΠ»ΠΈΠ½ΠΊΠ΅Ρ, ΠΏΠΎΠ»ΡΡΠ°Π΅ΠΌΡΠΉ ΡΠΏΠ΅ΠΊΠ°Π½ΠΈΠ΅ΠΌ, ΠΏΡΠ΅Π΄ΡΡΠ°Π²Π»ΡΠ΅Ρ ΡΠΎΠ±ΠΎΠΉ ΡΠ»ΠΎΠΆΠ½ΡΡ ΡΠΎΠ½ΠΊΠΎΠ·Π΅ΡΠ½ΠΈΡΡΡΡ ΡΠΌΠ΅ΡΡ ΠΊΡΠΈΡΡΠ°Π»Π»ΠΈΡΠ΅ΡΠΊΠΈΡ
ΡΠ°Π· ΠΈ Π½Π΅Π±ΠΎΠ»ΡΡΠΎΠ³ΠΎ ΠΊΠΎΠ»ΠΈΡΠ΅ΡΡΠ²Π° ΡΡΠ΅ΠΊΠ»ΠΎΠ²ΠΈΠ΄Π½ΠΎΠΉ ΡΠ°Π·Ρ. Π₯ΠΈΠΌΠΈΡΠ΅ΡΠΊΠΈΠΉ ΡΠΎΡΡΠ°Π² ΠΊΠ»ΠΈΠ½ΠΊΠ΅ΡΠ° ΠΊΠΎΠ»Π΅Π±Π»Π΅ΡΡΡ Π² ΡΠΈΡΠΎΠΊΠΈΡ
ΠΏΡΠ΅Π΄Π΅Π»Π°Ρ
. ΠΠ»Π°Π²Π½ΡΠΌΠΈ ΠΎΠΊΠΈΡΠ»Π°ΠΌΠΈ ΡΠ΅ΠΌΠ΅Π½ΡΠ½ΠΎΠ³ΠΎ ΠΊΠ»ΠΈΠ½ΠΊΠ΅ΡΠ° ΡΠ²Π»ΡΠ΅ΡΡΡ ΠΎΠΊΠΈΡΡ ΠΊΠ°Π»ΡΡΠΈΡ CaO, Π΄Π²ΡΠΎΠΊΠΈΡΡ ΠΊΡΠ΅ΠΌΠ½ΠΈΡ SiΠ2, ΠΎΠΊΠΈΡΡ Π°Π»ΡΠΌΠΈΠ½ΠΈΡ Πl2O3 ΠΈ ΠΎΠΊΠΈΡΡ ΠΆΠ΅Π»Π΅Π·Π° Fe2O3, ΡΡΠΌΠΌΠ°ΡΠ½ΠΎΠ΅ ΡΠΎΠ΄Π΅ΡΠΆΠ°Π½ΠΈΠ΅ ΠΊΠΎΡΠΎΡΡΡ
Π΄ΠΎΡΡΠΈΠ³Π°Π΅Ρ ΠΎΠ±ΡΡΠ½ΠΎ 95-97%. ΠΡΠΎΠΌΠ΅ Π½ΠΈΡ
ΠΈΠΌΠ΅ΡΡΡΡ ΠΏΡΠΈΠΌΠ΅ΡΠΈ ΠΎΠΊΠΈΡΠΈ ΠΌΠ°Π³Π½ΠΈΡ MgΠ, ΡΠ΅ΡΠ½ΡΠΉ Π°Π½Π³ΠΈΠ΄ΡΠΈΡ SO3, Π΄Π²ΡΠΎΠΊΠΈΡΡ ΡΠΈΡΠ°Π½Π° Π’iΠ2, ΠΎΠΊΠΈΡΡ Ρ
ΡΠΎΠΌΠ° Cr2O3, ΠΎΠΊΠΈΡΡ ΠΌΠ°ΡΠ³Π°Π½ΡΠ° Πn2O3, ΡΡΠ»ΠΎΡΠΈ Na2O ΠΈ K2O, ΡΠΎΡΡΠΎΡΠ½ΡΠΉ Π°Π½Π³ΠΈΠ΄ΡΠΈΡ P2O5 ΠΈ Π΄Ρ. ΠΡΠΈΠ΅Π½ΡΠΈΡΠΎΠ²ΠΎΡΠ½ΠΎ Ρ
ΠΈΠΌΠΈΡΠ΅ΡΠΊΠΈΠΉ ΡΠΎΡΡΠ°Π² ΠΏΠΎΡΡΠ»Π°Π½Π΄ΡΠ΅ΠΌΠ΅Π½ΡΠ° Π²ΡΠ³Π»ΡΠ΄ΠΈΡ ΡΠ»Π΅Π΄ΡΡΡΠΈΠΌ ΠΎΠ±ΡΠ°Π·ΠΎΠΌ: CaO 63-66%; SiΠ2 21-24%; Πl2O3 4-8%; Fe2O3 2-4%; MgΠ 0,5-5%; SO3 0,3-1%; Na2O ΠΈ K2O 0,4-1%; Π’iΠ2 ΠΈ Π‘Π³2O 0,2-0,5%; P2O5 0,1-0,3%.
ΠΠΈΠ½Π΅ΡΠ°Π»ΠΎΠ³ΠΈΡΠ΅ΡΠΊΠΈΠΉ ΡΠΎΡΡΠ°Π² ΠΏΠΎΡΡΠ»Π°Π½Π΄ΡΠ΅ΠΌΠ΅Π½ΡΠ½ΠΎΠ³ΠΎ ΠΊΠ»ΠΈΠ½ΠΊΠ΅ΡΠ°
ΠΠ±ΡΠ°Π·ΡΡΡΠΈΠΉΡΡ Π² ΡΠ΅Π·ΡΠ»ΡΡΠ°ΡΠ΅ ΠΎΠ±ΠΆΠΈΠ³Π° ΡΡΡΡΠ΅Π²ΠΎΠΉ ΡΠΌΠ΅ΡΠΈ ΠΊΠ»ΠΈΠ½ΠΊΠ΅Ρ, ΠΈΠΌΠ΅Π΅Ρ Π΄ΠΎΡΡΠ°ΡΠΎΡΠ½ΠΎ ΡΠ»ΠΎΠΆΠ½ΡΠΉ ΠΌΠΈΠ½Π΅ΡΠ°Π»ΠΎΠ³ΠΈΡΠ΅ΡΠΊΠΈΠΉ ΡΠΎΡΡΠ°Π². ΠΡΠ½ΠΎΠ²Π½ΡΡ ΡΠΎΠ»Ρ Π² Π½Π΅ΠΌ ΠΈΠ³ΡΠ°ΡΡ ΡΠ΅ΡΡΡΠ΅ ΠΌΠΈΠ½Π΅ΡΠ°Π»Π°.
Π’ΡΡΡ
ΠΊΠ°Π»ΡΡΠΈΠ΅Π²ΡΠΉ ΡΠΈΠ»ΠΈΠΊΠ°Ρ Ca3SiO5 ΠΈΠ»ΠΈ 3CaOβ’SiO2Β (C3S).Β ΠΠ±ΡΠ°Π·ΡΡΡΠΈΠΉΡΡ Π² ΠΏΠΎΡΡΠ»Π°Π½Π΄ΡΠ΅ΠΌΠ΅Π½ΡΠ½ΠΎΠΌ ΠΊΠ»ΠΈΠ½ΠΊΠ΅ΡΠ΅ ΡΡΡΡ
ΠΊΠ°Π»ΡΡΠΈΠ΅Π²ΡΠΉ ΡΠΈΠ»ΠΈΠΊΠ°Ρ ΡΠΎΠ΄Π΅ΡΠΆΠΈΡ Π½Π΅ΠΊΠΎΡΠΎΡΠΎΠ΅ ΠΊΠΎΠ»ΠΈΡΠ΅ΡΡΠ²ΠΎ ΠΏΡΠΈΠΌΠ΅ΡΠ΅ΠΉ MgO, Al2O3, Fe2O3, Cr2O3, ΠΊΠΎΡΠΎΡΡΠ΅ Π²Π»ΠΈΡΡΡ Π½Π° Π΅Π³ΠΎ ΡΡΡΡΠΊΡΡΡΡ ΠΈ ΡΠ²ΠΎΠΉΡΡΠ²Π°. ΠΡΠ° ΡΠ°Π·Π½ΠΎΠ²ΠΈΠ΄Π½ΠΎΡΡΡ Π½Π°Π·ΡΠ²Π°Π΅ΡΡΡ Π°Π»ΠΈΡΠΎΠΌ ΠΈ ΠΎΠ±ΠΎΠ·Π½Π°ΡΠ°Π΅ΡΡΡ Π‘3S. Π‘ΠΎΠ΄Π΅ΡΠΆΠ°Π½ΠΈΠ΅ Π°Π»ΠΈΡΠ° Π² ΠΊΠ»ΠΈΠ½ΠΊΠ΅ΡΠ΅ Π½Π°ΠΈΠ±ΠΎΠ»ΡΡΠ΅Π΅ ΠΈ ΡΠΎΡΡΠ°Π²Π»ΡΠ΅Ρ 40-55%. ΠΡΠΈ ΡΠ°ΡΡΠΌΠΎΡΡΠ΅Π½ΠΈΠΈ ΠΏΡΠΎΡΠ΅ΡΡΠΎΠ² Π³ΠΈΠ΄ΡΠ°ΡΠ°ΡΠΈΠΈ ΡΠ΅ΠΌΠ΅Π½ΡΠΎΠ² ΠΏΡΠΈΠΌΠ΅ΡΡΠΌΠΈ, Π²Ρ
ΠΎΠ΄ΡΡΠΈΠΌΠΈ Π² ΡΡΡΡ
ΠΊΠ°Π»ΡΡΠΈΠ΅Π²ΡΠΉ ΡΠΈΠ»ΠΈΠΊΠ°Ρ, ΠΊΠ°ΠΊ ΠΏΡΠ°Π²ΠΈΠ»ΠΎ, ΠΏΡΠ΅Π½Π΅Π±ΡΠ΅Π³Π°ΡΡ, ΠΈ Π²ΡΠ΅ ΡΠ°ΡΡΡΡΡ Π²Π΅Π΄ΡΡΡΡ Π½Π° ΡΠΈΡΡΡΡ ΡΠΈΡΡΠ΅ΠΌΡ 3CaOβ’SiO2. Π ΠΏΠΎΡΡΠ»Π°Π½Π΄ΡΠ΅ΠΌΠ΅Π½ΡΠ΅ Π°Π»ΠΈΡ ΠΎΠ±Π΅ΡΠΏΠ΅ΡΠΈΠ²Π°Π΅Ρ Π½Π°Π±ΠΎΡ ΡΠΎΡΠ½ΠΎΡΡΠΈ ΠΊΠ°ΠΌΠ½Ρ Π² ΡΠ°Π½Π½ΠΈΠ΅ ΡΡΠΎΠΊΠΈ ΡΠ²Π΅ΡΠ΄Π΅Π½ΠΈΡ (ΠΎΡ Π½Π΅ΡΠΊΠΎΠ»ΡΠΊΠΈΡ
Π΄Π½Π΅ΠΉ Π΄ΠΎ 3-Ρ
Β ΠΌΠ΅ΡΡΡΠ΅Π²).Β Π’ΡΡΡ
ΠΊΠ°Π»ΡΡΠΈΠ΅Π²ΡΠΉ ΡΠΈΠ»ΠΈΠΊΠ°Ρ ΠΏΠΎΠ»ΡΡΠ°ΡΡ Π² Π»Π°Π±ΠΎΡΠ°ΡΠΎΡΠ½ΡΡ
ΡΡΠ»ΠΎΠ²ΠΈΡΡ
ΠΈΠ· Ρ
ΠΈΠΌΠΈΡΠ΅ΡΠΊΠΈ ΡΠΈΡΡΡΡ
ΠΊΠΎΠΌΠΏΠΎΠ½Π΅Π½ΡΠΎΠ². ΠΡΠΈΡΡΠ°Π»Π»Ρ Π°Π»ΠΈΡΠ° ΠΈΠΌΠ΅ΡΡ ΠΎΠ±ΡΡΠ½ΠΎ ΡΠ΅ΡΡΠΈΠ³ΡΠ°Π½Π½ΡΡ ΠΈΠ»ΠΈ ΠΏΡΡΠΌΠΎΡΠ³ΠΎΠ»ΡΠ½ΡΡ ΡΠΎΡΠΌΡ, ΠΊΠΎΡΠΎΡΠ°Ρ Ρ
ΠΎΡΠΎΡΠΎ ΠΏΡΠΎΡΠΌΠ°ΡΡΠΈΠ²Π°Π΅ΡΡΡ Π² ΡΠ»ΠΈΡΠ°Ρ
ΠΊΠ»ΠΈΠ½ΠΊΠ΅ΡΠ° Π² ΠΎΡΡΠ°ΠΆΠ΅Π½Π½ΠΎΠΌ ΡΠ²Π΅ΡΠ΅.
ΠΠ²ΡΡ
ΠΊΠ°Π»ΡΡΠΈΠ΅Π²ΡΠΉ ΡΠΈΠ»ΠΈΠΊΠ°Ρ Ca2SiO4 ΠΈΠ»ΠΈ 2CaOβ’SiO2Β (C2S). ΠΒ ΠΏΠΎΡΡΠ»Π°Π½Π΄ΡΠ΅ΠΌΠ΅Π½ΡΠ½ΠΎΠΌ ΠΊΠ»ΠΈΠ½ΠΊΠ΅ΡΠ΅ ΠΏΡΠΈΡΡΡΡΡΠ²ΡΠ΅Ρ Π² Π±Π΅ΡΠ°Β – ΠΌΠΎΠ΄ΠΈΡΠΈΠΊΠ°ΡΠΈΠΈ, Π½Π°Π·ΡΠ²Π°Π΅ΠΌΠΎΠΉ Π±Π΅Π»ΠΈΡΠΎΠΌ. ΠΠΎΠ»ΠΈΡΠ΅ΡΡΠ²ΠΎ Π΅Π³ΠΎ Π² ΠΊΠ»ΠΈΠ½ΠΊΠ΅ΡΠ΅ ΡΠΎΡΡΠ°Π²Π»ΡΠ΅Ρ 20 – 30%. ΠΠ΅Π»ΠΈΡ ΠΈΠΌΠ΅Π΅Ρ ΠΌΠ΅Π½ΡΡΡΡ Π³ΠΈΠ΄ΡΠ°Π²Π»ΠΈΡΠ΅ΡΠΊΡΡ Π°ΠΊΡΠΈΠ²Π½ΠΎΡΡΡ, ΠΏΠΎ ΡΡΠ°Π²Π½Π΅Π½ΠΈΡ Ρ Π°Π»ΠΈΡΠΎΠΌ ΠΈ ΠΎΠ±Π΅ΡΠΏΠ΅ΡΠΈΠ²Π°Π΅Ρ ΡΠΎΡΡ ΠΏΡΠΎΡΠ½ΠΎΡΡΠΈ ΡΠ΅ΠΌΠ΅Π½ΡΠ½ΠΎΠ³ΠΎ ΠΊΠ°ΠΌΠ½Ρ Π½Π° ΠΏΠΎΠ·Π΄Π½ΠΈΡ
ΡΡΠ°Π΄ΠΈΡΡ
ΡΠ²Π΅ΡΠ΄Π΅Π½ΠΈΡ. ΠΠ΅Π»ΠΈΡ, ΠΊΠ°ΠΊ ΠΈ Π°Π»ΠΈΡ ΠΏΡΠ΅Π΄ΡΡΠ°Π²Π»ΡΠ΅Ρ ΡΠΎΠ±ΠΎΠΉ ΡΠ²ΡΡΠ΄ΡΠΉ ΡΠ°ΡΡΠ²ΠΎΡ Π±Π΅ΡΠ° – Π΄Π²ΡΡ
ΠΊΠ°Π»ΡΡΠΈΠ΅Π²ΠΎΠ³ΠΎ ΡΠΈΠ»ΠΈΠΊΠ°ΡΠ° (Π±Π΅ΡΠ° – 2Π‘Π°Oβ’SiO2) ΠΈ Π½Π΅Π±ΠΎΠ»ΡΡΠΎΠ³ΠΎ ΠΊΠΎΠ»ΠΈΡΠ΅ΡΡΠ²Π° (1-3) ΡΠ°ΠΊΠΈΡ
ΠΏΡΠΈΠΌΠ΅ΡΠ΅ΠΉ ΠΊΠ°ΠΊ Πl2O3, FΠ΅2O3, Π‘r2Π3 ΠΈ Π΄Ρ. ΠΠΈΠ΄ΡΠ°Π²Π»ΠΈΡΠ΅ΡΠΊΠ°Ρ Π°ΠΊΡΠΈΠ²Π½ΠΎΡΡΡ Π±Π΅Π»ΠΈΡΠ° ΡΠ°ΠΊΠΆΠ΅ Π·Π°Π²ΠΈΡΠΈΡ ΠΎΡ ΡΡΡΠΎΠ΅Π½ΠΈΡ ΠΊΡΠΈΡΡΠ°Π»Π»ΠΎΠ². Π¦Π΅ΠΌΠ΅Π½ΡΡ, Π² ΠΊΠΎΡΠΎΡΡΡ
Π±Π΅Π»ΠΈΡ ΠΏΡΠ΅Π΄ΡΡΠ°Π²Π»Π΅Π½ ΠΎΠΊΡΡΠ³Π»ΡΠΌΠΈ ΠΏΠ»ΠΎΡΠ½ΡΠΌΠΈ ΠΊΡΠΈΡΡΠ°Π»Π»Π°ΠΌΠΈ Ρ Π·Π°Π·ΡΠ±ΡΠ΅Π½Π½ΡΠΌΠΈ ΠΊΡΠ°ΡΠΌΠΈ ΡΠΎ ΡΡΠ΅Π΄Π½ΠΈΠΌ ΡΠ°Π·ΠΌΠ΅ΡΠΎΠΌ 20-50 ΠΌΠΊΠΌΒ Ρ
Π°ΡΠ°ΠΊΡΠ΅ΡΠΈΠ·ΡΡΡΡΡ ΠΏΠΎΠ²ΡΡΠ΅Π½Π½ΠΎΠΉ ΠΏΡΠΎΡΠ½ΠΎΡΡΡΡ. Π Π°ΡΡΠ΅ΠΏΠ»Π΅Π½ΠΈΠ΅ ΠΊΡΠΈΡΡΠ°Π»Π»ΠΎΠ² ΡΠΏΠΎΡΠΎΠ±ΡΡΠ²ΡΠ΅Ρ ΠΏΠΎΠ²ΡΡΠ΅Π½ΠΈΡ Π΅Ρ Π³ΠΈΠ΄ΡΠ°Π²Π»ΠΈΡΠ΅ΡΠΊΠΎΠΉ Π°ΠΊΡΠΈΠ²Π½ΠΎΡΡΠΈ.Β ΠΡΠΎΠΌΠ΅ΠΆΡΡΠΎΡΠ½ΠΎΠ΅ Π²Π΅ΡΠ΅ΡΡΠ²ΠΎ, ΡΠ°ΡΠΏΠΎΠ»ΠΎΠΆΠ΅Π½Π½ΠΎΠ΅ ΠΌΠ΅ΠΆΠ΄Ρ ΠΊΡΠΈΡΡΠ°Π»Π»Π°ΠΌΠΈ Π°Π»ΠΈΡΠ° Π±Π΅Π»ΠΈΡΠ° Π²ΠΊΠ»ΡΡΠ°Π΅Ρ Π°Π»ΡΠΌΠΎΡΠ΅ΡΡΠΈΡΠ½ΡΡ ΠΈ Π°Π»ΡΠΌΠΈΠ½Π°ΡΠ½ΡΡ ΡΠ°Π·Ρ. Β
ΠΠ»ΡΠΌΠΈΠ½Π°ΡΡ ΠΊΠ°Π»ΡΡΠΈΡ ΠΎΠ±ΡΡΠ½ΠΎ Π²ΡΡΡΠ΅ΡΠ°ΡΡΡΡ Π² ΠΊΠ»ΠΈΠ½ΠΊΠ΅ΡΠ΅ Π² Π²ΠΈΠ΄Π΅ ΡΡΡΡ
ΠΊΠ°Π»ΡΡΠΈΠ΅Π²ΠΎΠ³ΠΎ Π°Π»ΡΠΌΠΈΠ½Π°ΡΠ° Π‘3Πl2O6 ΠΈΠ»ΠΈ 3CaOβ’Al2O3 (Π‘3Π).Β Π‘3Π ΠΊΡΠΈΡΡΠ°Π»Π»ΠΈΠ·ΡΠ΅ΡΡΡ Π² ΠΊΡΠ±ΠΈΡΠ΅ΡΠΊΠΎΠΉ ΡΠΈΡΡΠ΅ΠΌΠ΅ Π² Π²ΠΈΠ΄Π΅ ΠΎΡΠ΅Π½Ρ ΠΌΠ΅Π»ΠΊΠΈΡ
ΡΠ΅ΡΡΠΈΡΠ³ΠΎΠ»ΡΠ½ΠΈΠΊΠΎΠ² ΠΈ ΠΏΡΡΠΌΠΎΡΠ³ΠΎΠ»ΡΠ½ΠΈΠΊΠΎΠ². Π‘ΠΎΠ΄Π΅ΡΠΆΠΈΡΡΡ Π² ΡΠ΅ΠΌΠ΅Π½ΡΠ½ΠΎΠΌ ΠΊΠ»ΠΈΠ½ΠΊΠ΅ΡΠ΅ Π² ΠΊΠΎΠ»ΠΈΡΠ΅ΡΡΠ²Π΅ Π΄ΠΎ 15%. ΠΡΠΎ Π½Π°ΠΈΠ±ΠΎΠ»Π΅Π΅ Ρ
ΠΈΠΌΠΈΡΠ΅ΡΠΊΠΈ Π°ΠΊΡΠΈΠ²Π½ΡΠΉ ΠΌΠΈΠ½Π΅ΡΠ°Π» ΠΊΠ»ΠΈΠ½ΠΊΠ΅ΡΠ° ΠΈ ΠΈΠΌΠ΅Π½Π½ΠΎ Π΅Π³ΠΎ Π³ΠΈΠ΄ΡΠ°ΡΠ°ΡΠΈΡ ΠΎΠΏΡΠ΅Π΄Π΅Π»ΡΠ΅Ρ ΡΡΠΎΠΊΠΈ ΡΡ
Π²Π°ΡΡΠ²Π°Π½ΠΈΡ ΡΠ΅ΠΌΠ΅Π½ΡΠ½ΡΡ
ΡΠ°ΡΡΠ²ΠΎΡΠΎΠ².Β ΠΠ³ΠΎ ΠΏΡΠΈΡΡΡΡΡΠ²ΠΈΠ΅ Π² Π±ΠΎΠ»ΡΡΠΈΡ
ΠΊΠΎΠ»ΠΈΡΠ΅ΡΡΠ²Π°Ρ
ΡΡΠΊΠΎΡΡΠ΅Ρ ΡΡ
Π²Π°ΡΡΠ²Π°Π½ΠΈΠ΅ Β ΠΈ ΡΠ²Π΅ΡΠ΄Π΅Π½ΠΈΠ΅ ΠΏΠΎΡΡΠ»Π°Π½Π΄ΡΠ΅ΠΌΠ΅Π½ΡΠ½ΠΎΠ³ΠΎ ΡΠ°ΡΡΠ²ΠΎΡΠ° ΠΏΡΠΈ Π½ΠΈΠ·ΠΊΠΈΡ
ΡΠ΅ΠΌΠΏΠ΅ΡΠ°ΡΡΡΠ°Ρ
. ΠΡΠΈ ΠΏΠΎΠ²ΡΡΠ΅Π½Π½ΠΎΠΌ ΡΠΎΠ΄Π΅ΡΠΆΠ°Π½ΠΈΠΈ ΡΡΠ΅Ρ
ΠΊΠ°Π»ΡΡΠΈΠ΅Π²ΠΎΠ³ΠΎ Π°Π»ΡΠΌΠΈΠ½Π°ΡΠ° ΠΎΡΠ»Π°Π±Π»ΡΠ΅ΡΡΡ ΡΡΡΠΎΠΉΡΠΈΠ²ΠΎΡΡΡ ΡΠ΅ΠΌΠ΅Π½ΡΠ½ΠΎΠ³ΠΎ ΠΊΠ°ΠΌΠ½Ρ Π² ΡΡΠ΅Π΄Π°Ρ
, ΡΠΎΠ΄Π΅ΡΠΆΠ°ΡΠΈΡ
ΡΡΠ»ΡΡΠ°ΡΡ ΠΈ ΡΠ΅ΡΠΎΠ²ΠΎΠ΄ΠΎΡΠΎΠ΄.Β ΠΠ»ΡΠΌΠΎΡΠ΅ΡΡΠΈΡΠ½Π°Ρ ΡΠ°Π·Π° ΠΏΡΠ΅Π΄ΡΡΠ°Π²Π»ΡΠ΅Ρ ΡΠΎΠ±ΠΎΠΉ ΡΠ²Π΅ΡΠ΄ΡΠΉ ΡΠ°ΡΡΠ²ΠΎΡ Π°Π»ΡΠΌΠΎΡΠ΅ΡΡΠΈΡΠΎΠ² ΠΊΠ°Π»ΡΡΠΈΡ ΡΠ°Π·Π½ΠΎΠ³ΠΎ ΡΠΎΡΡΠ°Π²Π°, ΠΊΠΎΡΠΎΡΡΠΉ Π² ΡΠ²ΠΎΡ ΠΎΡΠ΅ΡΠ΅Π΄Ρ Π·Π°Π²ΠΈΡΠΈΡ ΠΎΡ ΡΠΎΡΡΠ°Π²Π° ΡΡΡΡΠ΅Π²ΡΡ
ΡΠΌΠ΅ΡΠ΅ΠΉ, ΡΡΠ»ΠΎΠ²ΠΈΠΉ ΠΎΠ±ΠΆΠΈΠ³Π° ΠΈ Ρ.ΠΏ. ΠΡΠΈ ΡΡΠΎΠΌ Π²ΠΎΠ·ΠΌΠΎΠΆΠ½ΠΎ ΠΎΠ±ΡΠ°Π·ΠΎΠ²Π°Π½ΠΈΠ΅ ΡΠ΅ΡΠΈΠΈ ΡΠ²Π΅ΡΠ΄ΡΡ
ΡΠ°ΡΡΠ²ΠΎΡΠΎΠ² ΠΌΠ΅ΠΆΠ΄Ρ Π‘6Π2F, Π‘4ΠF, C6AF2 ΠΈ Π‘2F. Π ΠΊΠ»ΠΈΠ½ΠΊΠ΅ΡΠ΅ Π°Π»ΡΠΌΠΎΡΠ΅ΡΡΠΈΡΠ½Π°Ρ ΡΠ°Π·Π° ΠΏΠΎ ΡΠ²ΠΎΠ΅ΠΌΡ ΡΠΎΡΡΠ°Π²Ρ Π±Π»ΠΈΠ·ΠΊΠ° ΠΊ ΡΠ΅ΡΡΡΡΡ
ΠΊΠ°Π»ΡΡΠΈΠ΅Π²ΠΎΠΌΡ Π°Π»ΡΠΌΠΎΡΠ΅ΡΡΠΈΡΡ.
Π§Π΅ΡΡΡΡΡ
ΠΊΠ°Π»ΡΡΠΈΠ΅Π²ΡΠΉ Π°Π»ΡΠΌΠΎΡΠ΅ΡΡΠΈΡ Ca4β’Al2O5β’Fe2O5Β ΠΈΠ»ΠΈ 4CaOβ’AI2O3β’Fe2O3Β (C4AF) (Π±ΡΠ°ΡΠ½ΠΌΠΈΠ»Π»Π΅ΡΠΈΡ) – ΠΆΠ΅Π»Π΅Π·ΠΎΡΠΎΠ΄Π΅ΡΠΆΠ°ΡΠΈΠΉ ΠΌΠΈΠ½Π΅ΡΠ°Π» ΠΎΠ±Π»Π°Π΄Π°ΡΡΠΈΠΉ Π΄ΠΎΡΡΠ°ΡΠΎΡΠ½ΠΎ Π²ΡΡΠΎΠΊΠΎΠΉ ΡΠΊΠΎΡΠΎΡΡΡΡ Π³ΠΈΠ΄ΡΠ°ΡΠ°ΡΠΈΠΈ ΠΈ ΠΎΠ±Π΅ΡΠΏΠ΅ΡΠΈΠ²Π°ΡΡΠΈΠΉ ΡΠΎΡΡ ΠΏΡΠΎΡΠ½ΠΎΡΡΠΈ ΡΠΈΡΡΠ΅ΠΌΡ Π² ΠΏΠ΅ΡΠ²ΡΠ΅ ΡΠ°ΡΡΒ ΡΠ²Π΅ΡΠ΄Π΅Π½ΠΈΡ. Π ΠΏΠΎΡΡΠ»Π°Π½Π΄ΡΠ΅ΠΌΠ΅Π½ΡΠ°Ρ
Π΅Π³ΠΎ ΠΊΠΎΠ»ΠΈΡΠ΅ΡΡΠ²ΠΎ Π½Π°Ρ
ΠΎΠ΄ΠΈΡΡΡ Π² ΠΏΡΠ΅Π΄Π΅Π»Π°Ρ
10-20%. Π‘ΠΊΠΎΡΠΎΡΡΠΈ ΠΏΡΠΎΡΠ΅ΡΡΠΎΠ² Π³ΠΈΠ΄ΡΠ°ΡΠ°ΡΠΈΠΈΒ – ΠΏΡΠΈΠΌΠ΅ΡΠ½ΠΎ ΡΠ°Π²Π½Ρ.
ΠΡΠΎΠΌΠ΅ ΡΠΊΠ°Π·Π°Π½Π½ΡΡ
ΠΌΠΈΠ½Π΅ΡΠ°Π»ΠΎΠ² Π² ΡΠΎΡΡΠ°Π² ΠΊΠ»ΠΈΠ½ΠΊΠ΅ΡΠ° Π²Ρ
ΠΎΠ΄ΠΈΡ ΡΡΠ΅ΠΊΠ»ΠΎΠ²ΠΈΠ΄Π½Π°Ρ ΡΠ°Π·Π°, ΡΠΎΠ΄Π΅ΡΠΆΠ°ΡΠ°Ρ Π² ΡΠ²ΠΎΠ΅ΠΌ ΡΠΎΡΡΠ°Π²Π΅ Π½Π΅Π·Π°ΠΊΡΠΈΡΡΠ°Π»Π»ΠΈΠ·ΠΎΠ²Π°Π½Π½ΡΠ΅ ΡΠ΅ΡΡΠΈΡΡ, Π°Π»ΡΠΌΠΈΠ½Π°ΡΡ, ΠΎΠΊΡΠΈΠ΄ ΠΌΠ°Π³Π½ΠΈΡ, ΡΠ΅Π»ΠΎΡΠ½ΡΠ΅ ΡΠΎΠ΅Π΄ΠΈΠ½Π΅Π½ΠΈΡ ΠΈ Π΄Ρ. ΠΡΠΈ ΡΠ΅Π·ΠΊΠΎΠΌ ΠΎΡ
Π»Π°ΠΆΠ΄Π΅Π½ΠΈΠΈ ΡΠ΅ΠΌΠ΅Π½ΡΠ½ΠΎΠ³ΠΎ ΠΊΠ»ΠΈΠ½ΠΊΠ΅ΡΠ° ΡΡΠ΅ΠΊΠ»ΠΎΡΠ°Π·Π°, ΠΏΠΎΠΊΡΡΠ²Π°Ρ ΠΏΠΎΠ²Π΅ΡΡ
Π½ΠΎΡΡΡ ΠΌΠΈΠ½Π΅ΡΠ°Π»ΠΎΠ², ΠΏΡΠ΅Π΄ΠΎΡΠ²ΡΠ°ΡΠ°Π΅Ρ ΡΠ°Π·ΠΎΠ²ΡΠ΅ ΠΏΠ΅ΡΠ΅Ρ
ΠΎΠ΄.Β ΠΠΊΠΈΡΡ ΠΌΠ°Π³Π½ΠΈΡ Π½Π°Ρ
ΠΎΠ΄ΠΈΡΡΡ Π² ΠΊΠ»ΠΈΠ½ΠΊΠ΅ΡΠ΅ Π² Π²ΠΈΠ΄Π΅: Π°) ΠΌΠΈΠ½Π΅ΡΠ°Π»Π° ΠΏΠ΅ΡΠΈΠΊΠ»Π°Π·Π°; Π±) ΡΠ²Π΅ΡΠ΄ΠΎΠ³ΠΎ ΡΠ°ΡΡΠ²ΠΎΡΠ° Π² Π°Π»ΡΠΌΠΎΡΠ΅ΡΠΈΡΠ½ΠΎΠΉ Β ΡΠ°Π·Π΅ ΠΈΠ»ΠΈ Π² ΡΡΠ΅Ρ
ΠΊΠ°Π»ΡΡΠΈΠ΅Π²ΠΎΠΌ ΡΠΈΠ»ΠΈΠΊΠ°ΡΠ΅; Π²) Π² ΠΊΠ»ΠΈΠ½ΠΊΠ΅ΡΠ½ΠΎΠΌ ΡΡΠ΅ΠΊΠ»Π΅. ΠΡΠ΅Π΄Π½ΠΎΠ΅ Π²Π»ΠΈΡΠ½ΠΈΠ΅ MgO ΠΏΡΠΈ ΡΠΎΠ΄Π΅ΡΠΆΠ°Π½ΠΈΠΈ Π±ΠΎΠ»Π΅Π΅ 5% Π½Π° ΡΠ°Π²Π½ΠΎΠΌΠ΅ΡΠ½ΠΎΡΡΡ ΠΈΠ·ΠΌΠ΅Π½Π΅Π½ΠΈΡ ΠΎΠ±ΡΠ΅ΠΌΠ° ΡΠ΅ΠΌΠ΅Π½ΡΠ° ΠΏΡΠΎΡΠ²Π»ΡΠ΅ΡΡΡ Π² ΡΠΎΠΌ ΡΠ»ΡΡΠ°Π΅, ΠΊΠΎΠ³Π΄Π° ΠΎΠ½Π° ΠΏΡΠΈΡΡΡΡΡΠ²ΡΠ΅Ρ Π² Π²ΠΈΠ΄Π΅ ΠΊΡΠΈΡΡΠ°Π»Π»ΠΎΠ² ΠΏΠ΅ΡΠΈΠΊΠ»Π°Π·Π°, ΠΌΠ΅Π΄Π»Π΅Π½Π½ΠΎ ΡΠ΅Π°Π³ΠΈΡΡΡΡΠΈΡ
Ρ Π²ΠΎΠ΄ΠΎΠΉ Π² ΡΠΆΠ΅ Π·Π°ΡΠ²Π΅ΡΠ΄Π΅Π²ΡΠ΅ΠΌ ΡΠ΅ΠΌΠ΅Π½ΡΠ΅ ΠΈ Π΄Π°ΡΡΠΈΡ
Mg(ΠΠ)2 Ρ
Π°ΡΠ°ΠΊΡΠ΅ΡΠΈΠ·ΡΡΡΠΈΠΉΡΡ ΡΠ²Π΅Π»ΠΈΡΠ΅Π½Π½ΡΠΌ, ΡΠ΄Π΅Π»ΡΠ½ΡΠΌ ΠΎΠ±ΡΠ΅ΠΌΠΎΠΌ.Β Π©Π΅Π»ΠΎΡΠΈ: Π½Π°ΡΡΠΈΠΉ ΠΈ ΠΊΠ°Π»ΠΈΠΉ ΠΏΡΠΈΡΡΡΡΡΠ²ΡΡΡ Π² ΠΊΠ»ΠΈΠ½ΠΊΠ΅ΡΠ΅ Π² Π²ΠΈΠ΄Π΅ ΡΡΠ»ΡΡΠ°ΡΠΎΠ², Π° ΡΠ°ΠΊΠΆΠ΅ Π²Ρ
ΠΎΠ΄ΡΡ Π² Π°Π»ΡΠΌΠΈΠ½Π°ΡΠ½ΡΡ ΠΈ Π°Π»ΡΠΌΠΎΡΠ΅ΡΡΠΈΡΠ½ΡΡ ΡΠ°Π·Ρ.
ΠΠ»Ρ ΡΠ΅Π³ΡΠ»ΠΈΡΠΎΠ²Π°Π½ΠΈΡ ΡΡΠΎΠΊΠΎΠ² ΡΡ
Π²Π°ΡΡΠ²Π°Π½ΠΈΡ ΡΠ΅ΠΌΠ΅Π½ΡΠ° ΠΏΡΠΈ ΠΏΠΎΠΌΠΎΠ»Π΅ ΠΊΠ»ΠΈΠ½ΠΊΠ΅ΡΠ° Π²Π²ΠΎΠ΄ΠΈΡΡΡ 3-5% Π΄Π²ΡΠ²ΠΎΠ΄Π½ΠΎΠ³ΠΎ Π³ΠΈΠΏΡΠ°. ΠΡΠΎΠΌΠ΅ ΡΡΠΎΠ³ΠΎ ΠΏΠΎΡΡΠ»Π°Π½Π΄ΡΠ΅ΠΌΠ΅Π½Ρ ΠΌΠΎΠΆΠ΅Ρ ΡΠΎΠ΄Π΅ΡΠΆΠ°ΡΡ Π΄ΠΎ 15% ΠΊΡΠ΅ΠΌΠ½Π΅Π·ΡΠΌΠΎΡΠΎΠ΄Π΅ΡΠΆΠ°ΡΠΈΡ
ΠΊΠΎΠΌΠΏΠΎΠ½Π΅Π½ΡΠΎΠ², Π² ΠΊΠ°ΡΠ΅ΡΡΠ²Π΅ ΠΊΠΎΡΠΎΡΡΡ
ΠΌΠΎΠ³ΡΡ ΠΈΡΠΏΠΎΠ»ΡΠ·ΠΎΠ²Π°ΡΡΡΡ ΠΌΠΎΠ»ΠΎΡΡΠΉ ΠΏΠ΅ΡΠΎΠΊ, ΡΠ»Π°ΠΊΠΈ, Π·ΠΎΠ»Ρ ΠΎΡ ΡΠΆΠΈΠ³Π°Π½ΠΈΡ ΡΠ²ΡΡΠ΄ΡΡ
ΡΠΎΠΏΠ»ΠΈΠ². ΠΠ²Π΅Π΄Π΅Π½ΠΈΠ΅ΠΌ Π΄ΠΎΠ±Π°Π²ΠΎΠΊ Π΄ΠΎΡΡΠΈΠ³Π°Π΅ΡΡΡ Π΄Π²Π° ΠΏΡΠ΅ΠΈΠΌΡΡΠ΅ΡΡΠ²Π°: Π²ΠΎ-ΠΏΠ΅ΡΠ²ΡΡ
, ΡΠ΅ΠΌΠ΅Π½Ρ ΡΡΠΎΠΈΡ Π΄Π΅ΡΠ΅Π²Π»Π΅ Ρ.ΠΊ. ΠΏΠΎΡΡΠ»Π°Π½Π΄ΡΠ΅ΠΌΠ΅Π½ΡΠ½ΡΠΉ ΠΊΠ»ΠΈΠ½ΠΊΠ΅Ρ Π΄ΠΎΡΠΎΠΆΠ΅ Π»ΡΠ±ΠΎΠΉ Π΄ΠΎΠ±Π°Π²ΠΊΠΈ; Π²ΠΎ-Π²ΡΠΎΡΡΡ
, Π΄ΠΎΠ±Π°Π²ΠΊΠ°ΠΌΠΈ ΠΌΠΎΠΆΠ½ΠΎ ΡΠ΅Π³ΡΠ»ΠΈΡΠΎΠ²Π°ΡΡ ΡΠ²ΠΎΠΉΡΡΠ²Π° ΡΠ°ΡΡΠ²ΠΎΡΠ° ΠΈ ΠΊΠ°ΠΌΠ½Ρ. ΠΠ»Ρ ΠΏΡΠΈΠ΄Π°Π½ΠΈΡ ΡΠΏΠ΅ΡΠΈΠ°Π»ΡΠ½ΡΡ
ΠΊΠ°ΡΠ΅ΡΡΠ² ΡΠ΅ΠΌΠ΅Π½ΡΡ ΠΏΡΠΈ Π΅Π³ΠΎ ΠΏΠΎΠΌΠΎΠ»Π΅ Π²Π²ΠΎΠ΄ΡΡΡΡ Π³ΠΈΠ΄ΡΠΎΡΠΎΠ±ΠΈΠ·Π°ΡΠΎΡΡ, ΠΏΠ»Π°ΡΡΠΈΡΠΈΠΊΠ°ΡΠΎΡΡ ΠΈ Π΄ΡΡΠ³ΠΈΠ΅Β Π²Π΅ΡΠ΅ΡΡΠ²Π°.
Π’Π²Π΅ΡΠ΄Π΅Π½ΠΈΠ΅ ΠΏΠΎΡΡΠ»Π°Π½Π΄ΡΠ΅ΠΌΠ΅Π½ΡΠ°
ΠΡΠΈ ΡΠΌΠ΅ΡΠ΅Π½ΠΈΠΈ ΡΠ΅ΠΌΠ΅Π½ΡΠ° Ρ Π²ΠΎΠ΄ΠΎΠΉ Π½Π° Π½Π°ΡΠ°Π»ΡΠ½ΡΡ
ΡΡΠ°Π΄ΠΈΡΡ
ΡΠ²Π΅ΡΠ΄Π΅Π½ΠΈΡ Π² ΡΠ΅Π°ΠΊΡΠΈΡ Π³ΠΈΠ΄ΡΠ°ΡΠ°ΡΠΈΠΈ ΠΈΠ½ΡΠ΅Π½ΡΠΈΠ²Π½ΠΎ Π²ΡΡΡΠΏΠ°ΡΡ Π°Π»ΡΠΌΠΈΠ½Π°ΡΡ ΠΈ Π°Π»ΡΠΌΠΎΡΠ΅ΡΡΠΈΡΡ ΠΊΠ°Π»ΡΡΠΈΡ, Π±Π»Π°Π³ΠΎΠ΄Π°ΡΡ Π±ΠΎΠ»Π΅Π΅ Π²ΡΡΠΎΠΊΠΎΠΉ ΠΊΠΎΠ½ΡΡΠ°Π½ΡΠ΅ ΡΠΊΠΎΡΠΎΡΡΠΈ ΡΠ°ΡΡΠ²ΠΎΡΠ΅Π½ΠΈΡ ΠΏΠΎ ΡΡΠ°Π²Π½Π΅Π½ΠΈΡ Ρ Π°Π»ΠΈΡΠΎΠΌ ΠΈ Π±Π΅Π»ΠΈΡΠΎΠΌ. Π Π°ΡΡΠ²ΠΎΡ ΡΡΠ°Π½ΠΎΠ²ΠΈΡΡΡ ΠΏΠ΅ΡΠ΅ΡΡΡΠ΅Π½Π½ΡΠΌ ΠΏΠΎ ΠΎΡΠ½ΠΎΡΠ΅Π½ΠΈΡ ΠΊ ΠΊΠΎΠ½Π΅ΡΠ½ΠΎΠΌΡ ΠΏΡΠΎΠ΄ΡΠΊΡΡ ΠΈ ΠΈΠ· Π½Π΅Π³ΠΎ Π½Π° ΠΏΠΎΠ²Π΅ΡΡ
Π½ΠΎΡΡΠΈ Π·ΡΡΠ΅Π½ ΠΊΠ»ΠΈΠ½ΠΊΠ΅ΡΠ° ΠΈ Π² ΠΎΠ±ΡΡΠΌΠ΅ ΡΠ°ΡΡΠ²ΠΎΡΠ° ΠΎΠ±ΡΠ°Π·ΡΡΡΡΡ ΠΈΠ³Π»ΠΎΠΎΠ±ΡΠ°Π·Π½ΡΠ΅ ΠΊΡΠΈΡΡΠ°Π»Π»Ρ Π³ΠΈΠ΄ΡΠΎΠ°Π»ΡΠΌΠΈΠ½Π°ΡΠΎΠ² ΠΈ Π³ΠΈΠ΄ΡΠΎΡΠ΅ΡΡΠΈΡΠΎΠ² ΠΊΠ°Π»ΡΡΠΈΡ ΡΠ°Π·Π»ΠΈΡΠ½ΠΎΠ³ΠΎ ΡΠΎΡΡΠ°Π²Π°. Π ΠΎΠ±ΡΠ΅ΠΌ, Π²ΠΈΠ΄Π΅ ΠΈΡ
ΡΠΎΡΡΠ°Π² ΠΌΠΎΠΆΠ½ΠΎ ΠΎΠ±ΠΎΠ·Π½Π°ΡΠΈΡΡ xCaOβ’yAI2O3β’mΠ2Π ΠΈ xΠ‘Π°Πβ’yFe2O3β’mΠ2O. ΠΠ½Π°ΡΠ΅Π½ΠΈΡ ΠΊΠΎΡΡΡΠΈΡΠΈΠ΅Π½ΡΠΎΠ² x, y, m ΠΈΠ·ΠΌΠ΅Π½ΡΡΡΡΡ Π² ΡΠ°Π·Π»ΠΈΡΠ½ΡΡ
ΡΠΎΠΎΡΠ½ΠΎΡΠ΅Π½ΠΈΡΡ
ΠΈ Π·Π°Π²ΠΈΡΡΡ, Π³Π»Π°Π²Π½ΡΠΌ ΠΎΠ±ΡΠ°Π·ΠΎΠΌ, ΠΎΡ ΡΠ΅ΡΠΌΠΎΠ΄ΠΈΠ½Π°ΠΌΠΈΡΠ΅ΡΠΊΠΈΡ
ΡΡΠ»ΠΎΠ²ΠΈΠΉ ΠΏΡΠΎΡΠ΅ΡΡΠΎΠ² Π³ΠΈΠ΄ΡΠ°ΡΠ°ΡΠΈΠΈ.Β Π§Π΅ΡΠ΅Π· Π½Π΅ΠΊΠΎΡΠΎΡΠΎΠ΅ Π²ΡΠ΅ΠΌΡ (3-6 ΡΠ°ΡΠΎΠ²) Π² ΡΠΈΡΡΠ΅ΠΌΠ΅ Π½Π°ΠΊΠ°ΠΏΠ»ΠΈΠ²Π°Π΅ΡΡΡ Π΄ΠΎΡΡΠ°ΡΠΎΡΠ½ΠΎ ΠΌΠ½ΠΎΠ³ΠΎ ΠΊΡΠΈΡΡΠ°Π»Π»ΠΎΠ³ΠΈΠ΄ΡΠ°ΡΠΎΠ² ΠΈ ΠΎΠ±ΡΠ°Π·ΡΡΡΡΡ “ΡΡΠ΅ΡΠ½ΡΠ½Π½ΡΠ΅” ΡΡΠ»ΠΎΠ²ΠΈΡ, ΠΏΡΠΈΠ²ΠΎΠ΄ΡΡΠΈΠ΅ ΠΊ ΠΎΠ±ΡΠ°Π·ΠΎΠ²Π°Π½ΠΈΡ ΠΊΠΎΠ°Π³ΡΠ»ΡΡΠΈΠΎΠ½Π½ΠΎΠΉ ΡΡΡΡΠΊΡΡΡΡ, ΠΊΠΎΡΠΎΡΠ°Ρ ΠΏΠΎ ΠΌΠ΅ΡΠ΅ Π½Π°ΠΊΠΎΠΏΠ»Π΅Π½ΠΈΡ Π³ΠΈΠ΄ΡΠΎΠ°Π»ΡΠΌΠΈΠ½Π°ΡΠΎΠ² ΠΏΠ΅ΡΠ΅Ρ
ΠΎΠ΄ΠΈΡ Π² ΠΊΡΠΈΡΡΠ°Π»Π»ΠΈΠ·Π°ΡΠΈΠΎΠ½Π½ΡΡ. Π§Π΅ΡΠ΅Π· 6 – 10 ΡΠ°ΡΠΎΠ² Π²Π΅ΡΡ ΠΎΠ±ΡΡΠΌ ΠΌΠ΅ΠΆΠ΄Ρ ΠΏΠΎΡΡΠ΅ΠΏΠ΅Π½Π½ΠΎ ΡΠΌΠ΅Π½ΡΡΠ°ΡΡΠΈΠΌΠΈΡΡ Π·ΡΡΠ½Π°ΠΌΠΈ ΡΠ΅ΠΌΠ΅Π½ΡΠ° Π·Π°ΠΏΠΎΠ»Π½ΡΠ΅ΡΡΡ ΡΠΊΠ΅Π»Π΅ΡΠΎΠΌ ΠΈΠ³Π»ΠΎΠΎΠ±ΡΠ°Π·Π½ΡΡ
ΠΊΡΠΈΡΡΠ°Π»Π»ΠΎΠ² – ΠΏΡΠΎΠ΄ΡΠΊΡΠΎΠ² Π³ΠΈΠ΄ΡΠ°ΡΠ°ΡΠΈΠΈ Π°Π»ΡΠΌΠΈΠ½Π°ΡΠ½ΡΡ
ΡΠΎΡΡΠ°Π²Π»ΡΡΡΠΈΡ
ΠΊΠ»ΠΈΠ½ΠΊΠ΅ΡΠ°. ΠΡΠ° ΡΡΡΡΠΊΡΡΡΠ° ΠΈΠ½ΠΎΠ³Π΄Π° Π½Π°Π·ΡΠ²Π°Π΅ΡΡΡ Π°Π»ΡΠΌΠΈΠ½Π°ΡΠ½ΠΎΠΉ. Π¦Π΅ΠΌΠ΅Π½ΡΠ½ΡΠΉ ΡΠ°ΡΡΠ²ΠΎΡ, Π±ΡΠ²ΡΠΈΠΉ Π΄ΠΎ ΡΡΠΎΠ³ΠΎ ΠΏΠ»Π°ΡΡΠΈΡΠ½ΡΠΌ, Π½Π°ΡΠΈΠ½Π°Π΅Ρ ΡΠ΅ΡΡΡΡ ΠΏΠΎΠ΄Π²ΠΈΠΆΠ½ΠΎΡΡΡ ΠΈ Π½Π°Π±ΠΈΡΠ°ΡΡ ΠΏΡΠΎΡΠ½ΠΎΡΡΡ.
Π ΠΎΡΡΠ°Π²ΡΠ΅ΠΌΡΡ ΠΎΠ±ΡΡΠΌΠ΅ ΠΎΠ΄Π½ΠΎΠ²ΡΠ΅ΠΌΠ΅Π½Π½ΠΎ Ρ Π°Π»ΡΠΌΠΈΠ½Π°ΡΠ½ΠΎΠΉ, Π½ΠΎ ΡΠΎ Π·Π½Π°ΡΠΈΡΠ΅Π»ΡΠ½ΠΎ ΠΌΠ΅Π½ΡΡΠ΅ΠΉ ΡΠΊΠΎΡΠΎΡΡΡΡ, Π²ΠΎΠ·Π½ΠΈΠΊΠ°ΡΡ ΠΏΡΠΎΠ΄ΡΠΊΡΡ Π³ΠΈΠ΄ΡΠ°ΡΠ°ΡΠΈΠΈ ΡΠΈΠ»ΠΈΠΊΠ°ΡΠ½ΡΡ
ΠΊΠ»ΠΈΠ½ΠΊΠ΅ΡΠ½ΡΡ
ΠΌΠΈΠ½Π΅ΡΠ°Π»ΠΎΠ² Π°Π»ΠΈΡΠ° ΠΈ Π±Π΅Π»ΠΈΡΠ°.Β ΠΠΎΡΠ»Π΅Π΄Π½ΠΈΠ΅ ΠΎΠ±ΡΠ°Π·ΡΡΡ ΡΡΠ΅Π·Π²ΡΡΠ°ΠΉΠ½ΠΎ ΡΠΎΠ½ΠΊΠΎ ΠΏΠΎΡΠΈΡΡΡΠΉ Π²ΠΎΡΡ ΠΈΠ· ΠΎΡΠ΅Π½Ρ ΠΌΠ°Π»ΡΡ
ΠΊΡΠΈΡΡΠ°Π»Π»ΠΎΠ², ΡΠ°ΠΊ Π½Π°Π·ΡΠ²Π°Π΅ΠΌΡΡ ΡΠΈΠ»ΠΈΠΊΠ°ΡΠ½ΡΡ ΡΡΡΡΠΊΡΡΡΡ. ΠΠ»ΠΈΡΠ½ΠΈΠ΅ ΡΡΠΎΠΉ ΡΡΡΡΠΊΡΡΡΡ Π½Π° ΠΏΡΠΎΡΠ½ΠΎΡΡΡ ΡΠ²Π΅ΡΠ΄Π΅ΡΡΠ΅Π³ΠΎ ΡΠ΅ΠΌΠ΅Π½ΡΠ½ΠΎΠ³ΠΎ ΠΊΠ°ΠΌΠ½Ρ ΡΠΎ Π²ΡΠ΅ΠΌΠ΅Π½Π΅ΠΌ Π²ΡΡ Π±ΠΎΠ»Π΅Π΅ ΡΠ²Π΅Π»ΠΈΡΠΈΠ²Π°Π΅ΡΡΡ. ΠΠ½Π° ΡΠΆΠ΅ ΡΠ²Π»ΡΠ΅ΡΡΡ ΡΠΎΠ±ΡΡΠ²Π΅Π½Π½ΠΎ Π½ΠΎΡΠΈΡΠ΅Π»Π΅ΠΌ ΠΏΡΠΎΡΠ½ΠΎΡΡΠΈ ΡΠ΅ΠΌΠ΅Π½ΡΠ½ΠΎΠ³ΠΎ ΠΊΠ°ΠΌΠ½Ρ ΠΈ ΠΏΡΠΈΠ±Π»ΠΈΠ·ΠΈΡΠ΅Π»ΡΠ½ΠΎ ΡΠ΅ΡΠ΅Π· 1 ΡΡΡΠΊΠΈ Π½Π°ΡΠΈΠ½Π°Π΅Ρ ΠΏΡΠ΅ΠΎΠ±Π»Π°Π΄Π°ΡΡ Π½Π°Π΄ Π°Π»ΡΠΌΠΈΠ½Π°ΡΠ½ΠΎΠΉ. Π ΠΌΠ΅ΡΡΡΠ½ΠΎΠΌΡ ΡΡΠΎΠΊΡ Π² ΡΠ΅ΠΌΠ΅Π½ΡΠ½ΠΎΠΌ ΠΊΠ°ΠΌΠ½Π΅ ΠΎΠ±Π½Π°ΡΡΠΆΠΈΠ²Π°Π΅ΡΡΡ ΠΏΡΠ°ΠΊΡΠΈΡΠ΅ΡΠΊΠΈ ΡΠΎΠ»ΡΠΊΠΎ ΡΠΈΠ»ΠΈΠΊΠ°ΡΠ½Π°Ρ ΡΡΡΡΠΊΡΡΡΠ°. Π ΡΡΠΎΠΌΡ Π²ΡΠ΅ΠΌΠ΅Π½ΠΈ ΠΏΡΠΎΡΠ΅ΡΡ Π³ΠΈΠ΄ΡΠ°ΡΠ°ΡΠΈΠΈ Π½Π΅ Π·Π°ΠΊΠ°Π½ΡΠΈΠ²Π°Π΅ΡΡΡ ΠΈ Π² ΡΡΠ΄Π΅ ΡΠ»ΡΡΠ°Π΅Π² ΠΌΠΎΠΆΠ΅Ρ ΠΏΡΠΎΠ΄ΠΎΠ»ΠΆΠ°ΡΡΡΡ Π³ΠΎΠ΄Π°ΠΌΠΈ Π·Π° ΡΡΡΡ Π½Π΅ΠΈΡΠΏΠΎΠ»ΡΠ·ΠΎΠ²Π°Π½Π½ΠΎΠ³ΠΎ ΠΊΠ»ΠΈΠ½ΠΊΠ΅ΡΠ½ΠΎΠ³ΠΎ ΡΠΎΠ½Π΄Π° ΡΠ΅ΠΌΠ΅Π½ΡΠ°.
Π‘ΡΡΡΠΊΡΡΡΠ°Β ΡΠ΅ΠΌΠ΅Π½ΡΠ½ΠΎΠ³ΠΎ ΠΊΠ°ΠΌΠ½Ρ
ΠΠ»Ρ ΠΏΠΎΠ»Π½ΠΎΠΉ Π³ΠΈΠ΄ΡΠ°ΡΠ°ΡΠΈΠΈ ΡΠ΅ΠΌΠ΅Π½ΡΠ½ΠΎΠ³ΠΎ Π·Π΅ΡΠ½Π° Π½Π΅ΠΎΠ±Ρ ΠΎΠ΄ΠΈΠΌΠΎ Π½Π°Π»ΠΈΡΠΈΠ΅ 0,4 ΠΊΡΠ°ΡΠ½ΠΎΠ³ΠΎ ΠΊΠΎΠ»ΠΈΡΠ΅ΡΡΠ²Π° Π²ΠΎΠ΄Ρ ΠΎΡ Π΅Π³ΠΎ ΠΌΠ°ΡΡΡ. ΠΡΠΈ ΡΡΠΎΠΌ ΡΠΎΠ»ΡΠΊΠΎ 60% Π΅Ρ (Ρ.Π΅. 0,25 ΠΎΡ ΠΌΠ°ΡΡΡ ΡΠ΅ΠΌΠ΅Π½ΡΠ°) ΡΠ²ΡΠ·ΡΠ²Π°Π΅ΡΡΡ Ρ ΠΈΠΌΠΈΡΠ΅ΡΠΊΠΈ, ΠΎΡΡΠ°Π»ΡΠ½ΡΠ΅ (40 % ΠΈΡΡ ΠΎΠ΄Π½ΠΎΠΉ Π²ΠΎΠ΄Ρ) ΠΎΡΡΠ°ΡΡΡΡ Π² ΠΏΠΎΡΠ°Ρ ΡΠ΅ΠΌΠ΅Π½ΡΠ½ΠΎΠ³ΠΎ Π³Π΅Π»Ρ Π² ΡΠ»Π°Π±ΠΎΡΠ²ΡΠ·Π°Π½Π½ΠΎΠΌ ΡΠΎΡΡΠΎΡΠ½ΠΈΠΈ. Π Π°Π·ΠΌΠ΅Ρ, Π³Π΅Π»Π΅Π²ΡΡ ΠΏΠΎΡ ΠΎΠΊΠΎΠ»ΠΎ 3β’10-8 ΡΠΌ. ΠΠ½ΠΈ Π½Π΅ΠΈΠ·Π±Π΅ΠΆΠ½Ρ ΠΈ ΡΠ»ΡΠΆΠ°Ρ ΠΏΡΠΈΡΠΈΠ½ΠΎΠΉ ΡΠΎΠ½ΠΊΠΎΠΏΠΎΡΠΈΡΡΠΎΠ³ΠΎ ΡΡΡΠΎΠ΅Π½ΠΈΡ Π³Π΅Π»Π΅Π²ΠΎΠΉ ΠΌΠ°ΡΡΡ. ΠΡΠΈ Ρ ΠΈΠΌΠΈΡΠ΅ΡΠΊΠΎΠΌ ΡΠ²ΡΠ·ΡΠ²Π°Π½ΠΈΠΈ Π²ΠΎΠ΄Π° ΠΏΡΠ΅ΡΠ΅ΡΠΏΠ΅Π²Π°Π΅Ρ ΠΎΠ±ΡΡΠΌΠ½ΡΡ ΠΊΠΎΠ½ΡΡΠ°ΠΊΡΠΈΡ, ΠΊΠΎΡΠΎΡΠ°Ρ ΡΠΎΡΡΠ°Π²Π»ΡΠ΅Ρ ΠΎΠΊΠΎΠ»ΠΎ 1/4 Π΅Ρ ΠΏΠ΅ΡΠ²ΠΎΠ½Π°ΡΠ°Π»ΡΠ½ΠΎΠ³ΠΎ ΠΎΠ±ΡΡΠΌΠ°. ΠΠΎΡΡΠΎΠΌΡ ΠΏΠ»ΠΎΡΠ½ΡΠΉ ΠΎΠ±ΡΡΠΌ Π³Π΅Π»Ρ (Π±Π΅Π· ΠΏΠΎΡ) Π½Π° ΡΠ°ΠΊΡΡ ΠΆΠ΅ Π²Π΅Π»ΠΈΡΠΈΠ½Ρ ΠΌΠ΅Π½ΡΡΠ΅ ΡΡΠΌΠΌΡ ΠΎΠ±ΡΡΠΌΠΎΠ² ΠΈΡΡ ΠΎΠ΄Π½ΡΡ ΠΊΠΎΠΌΠΏΠΎΠ½Π΅Π½ΡΠΎΠ² ΡΠ΅ΠΌΠ΅Π½ΡΠ° ΠΈ Π²ΠΎΠ΄Ρ. ΠΡΠΎΡ ΠΏΡΠΎΡΠ΅ΡΡ Π½Π°Π·ΡΠ²Π°ΡΡ ΡΡΠ°Π΄ΠΊΠΎΠΉ, Π° ΠΎΡΠ²ΠΎΠ±ΠΎΠΆΠ΄Π°Π²ΡΠΈΠΉΡΡ Π² ΡΠ΅ΠΌΠ΅Π½ΡΠ½ΠΎΠΌ ΠΊΠ°ΠΌΠ½Π΅ ΠΎΠ±ΡΡΠΌ – ΠΎΠ±ΡΡΠΌΠΎΠΌ ΡΡΠ°Π΄ΠΊΠΈ. ΠΡΠΈ ΡΠ²Π΅ΡΠ΄Π΅Π½ΠΈΠΈ ΡΠ΅ΠΌΠ΅Π½ΡΠ½ΠΎΠ³ΠΎ ΠΊΠ°ΠΌΠ½Ρ Π² Π²ΠΎΠ΄Π½ΠΎΠΉ ΡΡΠ΅Π΄Π΅ ΠΈΠ»ΠΈ ΠΏΡΠΈ Π²ΡΡΠΎΠΊΠΎΠΉ Π²Π»Π°ΠΆΠ½ΠΎΡΡΠΈ ΡΠ°ΡΡΠΌΠΎΡΡΠ΅Π½Π½ΡΠΉ ΠΎΠ±ΡΡΠΌ ΠΏΠΎΡ Π·Π°ΠΏΠΎΠ»Π½ΡΠ΅ΡΡΡ Π²ΠΎΠ΄ΠΎΠΉ. Π’Π°ΠΊΠΈΠΌ ΠΎΠ±ΡΠ°Π·ΠΎΠΌ, ΠΏΡΠΈ ΠΏΠΎΠ»Π½ΠΎΠΉ Π³ΠΈΠ΄ΡΠ°ΡΠ°ΡΠΈΠΈ ΡΠ΅ΠΌΠ΅Π½ΡΠ° ΠΏΠΎΠ»ΡΡΠ°Π΅ΡΡΡ Π³Π΅Π»Ρ, ΠΎΠ±ΡΡΠΌ ΠΊΠΎΡΠΎΡΠΎΠ³ΠΎ ΠΏΡΠΈΠΌΠ΅ΡΠ½ΠΎ Π½Π° 30% ΡΠΎΡΡΠΎΠΈΡ ΠΈΠ· ΠΏΠΎΡ.Β
Π Π°ΡΡΠΌΠΎΡΡΠ΅Π½Π½ΡΠΉ ΡΠ»ΡΡΠ°ΠΉ ΡΠ²Π»ΡΠ΅ΡΡΡ ΠΈΠ΄Π΅Π°Π»ΡΠ½ΡΠΌ ΠΈ Π½Π° ΠΏΡΠ°ΠΊΡΠΈΠΊΠ΅ ΠΏΡΠ°ΠΊΡΠΈΡΠ΅ΡΠΊΠΈ Π½ΠΈΠΊΠΎΠ³Π΄Π° Π½Π΅ Π²ΡΡΡΠ΅ΡΠ°Π΅ΡΡΡ. ΠΡΠ»ΠΈ ΠΊΠΎΠ»ΠΈΡΠ΅ΡΡΠ²ΠΎ Π²ΠΎΠ΄Ρ Π±ΡΠ΄Π΅Ρ ΠΌΠ΅Π½ΡΡΠ΅ 0,4 ΠΎΡ ΠΌΠ°ΡΡΡ ΡΠ΅ΠΌΠ΅Π½ΡΠ°, ΡΠΎ Π΅Ρ Π±ΡΠ΄Π΅Ρ Π½Π΅Π΄ΠΎΡΡΠ°ΡΠΎΡΠ½ΠΎ Π΄Π»Ρ ΠΏΠΎΠ»Π½ΠΎΠΉ Π³ΠΈΠ΄ΡΠ°ΡΠ°ΡΠΈΠΈ ΡΠ΅ΠΌΠ΅Π½ΡΠ½ΡΡ
Π·ΡΡΠ΅Π½, ΠΈ Π² ΡΠ΅ΠΌΠ΅Π½ΡΠ½ΠΎΠΌ ΠΊΠ°ΠΌΠ½Π΅ ΠΎΡΡΠ°Π½ΡΡΡΡ Π½Π΅ΠΏΡΠΎΡΠ΅Π°Π³ΠΈΡΠΎΠ²Π°Π²ΡΠΈΠ΅ Π·ΡΡΠ½Π° ΡΠ΅ΠΌΠ΅Π½ΡΠ°. ΠΡΠΈ ΠΈΠ·Π±ΡΡΠΎΡΠ½ΠΎΠΌ ΠΊΠΎΠ»ΠΈΡΠ΅ΡΡΠ²Π΅ Π²ΠΎΠ΄Ρ ΡΠ°ΡΡΡ Π΅Ρ Π½Π΅ ΡΡΠ°ΡΡΠ²ΡΠ΅Ρ Π² ΠΏΡΠΎΡΠ΅ΡΡΠ΅ Π³ΠΈΠ΄ΡΠ°ΡΠ°ΡΠΈΠΈ ΠΈ ΠΎΠ±ΡΠ°Π·ΡΠ΅Ρ Π² ΠΊΠ°ΠΌΠ½Π΅ ΠΊΠ°ΠΏΠΈΠ»Π»ΡΡΠ½ΡΠ΅ ΠΏΠΎΡΡ Π΄ΠΈΠ°ΠΌΠ΅ΡΡΠΎΠΌ ΠΎΠΊΠΎΠ»ΠΎ 10-4 ΡΠΌ, ΠΊΠΎΡΠΎΡΡΠ΅ Π½Π° Π½Π΅ΡΠΊΠΎΠ»ΡΠΊΠΎ ΠΏΠΎΡΡΠ΄ΠΊΠΎΠ² Π±ΠΎΠ»ΡΡΠ΅ Π³Π΅Π»Π΅Π²ΡΡ
ΠΏΠΎΡ. ΠΡΠΈΠΌΠ΅ΡΠ½ΠΎ ΡΠ°ΠΊΠΈΡ
ΠΆΠ΅ ΡΠ°Π·ΠΌΠ΅ΡΠΎΠ² Π΄ΠΎΡΡΠΈΠ³Π°ΡΡ ΠΈ ΠΏΡΡΡΠΎΡΡ, Π²ΠΎΠ·Π½ΠΈΠΊΠ°ΡΡΠΈΠ΅ Π² ΡΠ΅Π·ΡΠ»ΡΡΠ°ΡΠ΅ ΡΠΆΠ΅ ΡΠΏΠΎΠΌΡΠ½ΡΡΠΎΠΉ ΡΡΠ°Π΄ΠΊΠΈ. Π’Π°ΠΊΠΈΠΌ ΠΎΠ±ΡΠ°Π·ΠΎΠΌ, Π²ΠΎΠ΄ΠΎΡΠ΅ΠΌΠ΅Π½ΡΠ½ΠΎΠ΅ ΠΎΡΠ½ΠΎΡΠ΅Π½ΠΈΠ΅ (Π/Π¦) Π² Π·Π½Π°ΡΠΈΡΠ΅Π»ΡΠ½ΠΎΠΉ ΠΌΠ΅ΡΠ΅ ΠΎΠΏΡΠ΅Π΄Π΅Π»ΡΠ΅Ρ ΡΡΡΡΠΊΡΡΡΡ ΡΠ΅ΠΌΠ΅Π½ΡΠ½ΠΎΠ³ΠΎ ΠΊΠ°ΠΌΠ½Ρ ΠΈ Π΅Π³ΠΎ ΡΠΈΠ·ΠΈΠΊΠΎ-ΠΌΠ΅Ρ
Π°Π½ΠΈΡΠ΅ΡΠΊΠΈΠ΅ ΡΠ²ΠΎΠΉΡΡΠ²Π°. Π‘ΡΠΌΠΌΠ°ΡΠ½Π°Ρ ΠΏΠΎΡΠΈΡΡΠΎΡΡΡ ΠΊΠ°ΠΌΠ½Ρ Π²ΠΎΠ·ΡΠ°ΡΡΠ°Π΅Ρ Ρ ΡΠ²Π΅Π»ΠΈΡΠ΅Π½ΠΈΠ΅ΠΌ Π/Π¦.
ΠΡΠΎΠΈΠ·Π²ΠΎΠ΄ΡΡΠ²ΠΎ ΠΏΠΎΡΡΠ»Π°Π½Π΄ΡΠ΅ΠΌΠ΅Π½ΡΠ°
ΠΡΠΎΠΈΠ·Π²ΠΎΠ΄ΡΡΠ²ΠΎ ΠΏΠΎΡΡΠ»Π°Π½Π΄ΡΠ΅ΠΌΠ΅Π½ΡΠ° ΠΌΠΎΠΆΠ΅Ρ Π±ΡΡΡ ΡΠ°Π·Π΄Π΅Π»Π΅Π½ΠΎ Π½Π° Π΄Π²Π° ΠΊΠΎΠΌΠΏΠ»Π΅ΠΊΡΠ° ΠΎΠΏΠ΅ΡΠ°ΡΠΈΠΉ. ΠΠ΅ΡΠ²ΡΠΉ ΠΈΠ· Π½ΠΈΡ
Π²ΠΊΠ»ΡΡΠ°Π΅Ρ ΠΈΠ·Π³ΠΎΡΠΎΠ²Π»Π΅Π½ΠΈΠ΅ ΠΊΠ»ΠΈΠ½ΠΊΠ΅ΡΠ°, Π²ΡΠΎΡΠΎΠΉ – ΠΏΠΎΠ»ΡΡΠ΅Π½ΠΈΠ΅ ΠΏΠΎΡΡΠ»Π°Π½Π΄ΡΠ΅ΠΌΠ΅Π½ΡΠ° ΠΈΠ·ΠΌΠ΅Π»ΡΡΠ΅Π½ΠΈΠ΅ΠΌ ΠΊΠ»ΠΈΠ½ΠΊΠ΅ΡΠ° ΡΠΎΠ²ΠΌΠ΅ΡΡΠ½ΠΎ Ρ Π³ΠΈΠΏΡΠΎΠΌ, Π°ΠΊΡΠΈΠ²Π½ΡΠΌΠΈ ΠΌΠΈΠ½Π΅ΡΠ°Π»ΡΠ½ΡΠΌΠΈ ΠΈ Π΄ΡΡΠ³ΠΈΠΌΠΈ Π΄ΠΎΠ±Π°Π²ΠΊΠ°ΠΌΠΈ. ΠΠΎΠ»ΡΡΠ΅Π½ΠΈΠ΅ ΠΊΠ»ΠΈΠ½ΠΊΠ΅ΡΠ° – Π½Π°ΠΈΠ±ΠΎΠ»Π΅Π΅ ΡΠ»ΠΎΠΆΠ½ΡΠΉ ΠΈ ΡΠ½Π΅ΡΠ³ΠΎΡΠΌΠΊΠΈΠΉ ΠΏΡΠΎΡΠ΅ΡΡ, Π·Π°ΠΊΠ»ΡΡΠ°ΡΡΠΈΠΉΡΡ Π² Π΄ΠΎΠ±ΡΡΠ΅ ΡΡΡΡΡ, Π΅Π³ΠΎ ΡΠΌΠ΅ΡΠ΅Π½ΠΈΠΈ ΠΈ ΠΎΠ±ΠΆΠΈΠ³Π΅. Π Π½Π°ΡΡΠΎΡΡΠ΅Π΅ Π²ΡΠ΅ΠΌΡ ΠΏΡΠΈΠΌΠ΅Π½ΡΡΡ Π΄Π²Π° ΠΎΡΠ½ΠΎΠ²Π½ΡΡ
Β ΡΠΏΠΎΡΠΎΠ±Π° ΠΏΠΎΠ΄Π³ΠΎΡΠΎΠ²ΠΊΠΈ ΡΡΡΡΠ΅Π²ΠΎΠΉ ΡΠΌΠ΅ΡΠΈ ΠΈΠ· ΠΈΡΡ
ΠΎΠ΄Π½ΡΡ
ΠΊΠΎΠΌΠΏΠΎΠ½Π΅Π½ΡΠΎΠ²: “ΠΌΠΎΠΊΡΡΠΉ”, ΠΏΡΠΈ ΠΊΠΎΡΠΎΡΠΎΠΌ ΠΏΠΎΠΌΠΎΠ» ΠΈ ΡΠΌΠ΅ΡΠ΅Π½ΠΈΠ΅ ΡΡΡΡΡ ΠΎΡΡΡΠ΅ΡΡΠ²Π»ΡΠ΅ΡΡΡ Π² Π²ΠΎΠ΄Π½ΠΎΠΉ ΡΡΠ΅Π΄Π΅, ΠΈ “ΡΡΡ
ΠΎΠΉ”, ΠΊΠΎΠ³Π΄Π° ΠΌΠ°ΡΠ΅ΡΠΈΠ°Π»Ρ ΠΈΠ·ΠΌΠ΅Π»ΡΡΠ°ΡΡΡΡ ΠΈ ΡΠΌΠ΅ΡΠΈΠ²Π°Π΅ΡΡΡ Π² ΡΡΡ
ΠΎΠΌ Π²ΠΈΠ΄Π΅.Β ΠΠ°ΠΆΠ΄ΡΠΉ ΠΈΠ· ΡΡΠΈΡ
ΡΠΏΠΎΡΠΎΠ±ΠΎΠ² ΠΈΠΌΠ΅Π΅Ρ ΡΠ²ΠΎΠΈ ΠΏΠΎΠ»ΠΎΠΆΠΈΡΠ΅Π»ΡΠ½ΡΠ΅ ΠΈ ΠΎΡΡΠΈΡΠ°ΡΠ΅Π»ΡΠ½ΡΠ΅ ΡΡΠΎΡΠΎΠ½Ρ. Π Π²ΠΎΠ΄Π½ΠΎΠΉ ΡΡΠ΅Π΄Π΅ ΠΎΠ±Π»Π΅Π³ΡΠ°Π΅ΡΡΡ ΠΈΠ·ΠΌΠ΅Π»ΡΡΠ΅Π½ΠΈΠ΅ ΠΌΠ°ΡΠ΅ΡΠΈΠ°Π»ΠΎΠ², ΠΏΡΠΈ ΠΈΡ
ΡΠΎΠ²ΠΌΠ΅ΡΡΠ½ΠΎΠΌ ΠΏΠΎΠΌΠΎΠ»Π΅ Π±ΡΡΡΡΠΎ Π΄ΠΎΡΡΠΈΠ³Π°Π΅ΡΡΡ Π²ΡΡΠΎΠΊΠ°Ρ ΠΎΠ΄Π½ΠΎΡΠΎΠ΄Π½ΠΎΡΡΡ ΡΠΌΠ΅ΡΠΈ, Π½ΠΎ ΡΠ°ΡΡ
ΠΎΠ΄ ΡΠΎΠΏΠ»ΠΈΠ²Π° Π½Π° ΠΎΠ±ΠΆΠΈΠ³ Π² 1,5-2 ΡΠ°Π·Π° Π±ΠΎΠ»ΡΡΠ΅ ΡΠ΅ΠΌ ΠΏΡΠΈ ΡΡΡ
ΠΎΠΌ.Β Π‘ΡΡ
ΠΎΠΉ ΡΠΏΠΎΡΠΎΠ±, Π½Π΅ΡΠΌΠΎΡΡΡ Π½Π° Π΅Π³ΠΎ ΡΠ΅Ρ
Π½ΠΈΠΊΠΎ-ΡΠΊΠΎΠ½ΠΎΠΌΠΈΡΠ΅ΡΠΊΠΈΠ΅ ΠΏΡΠ΅ΠΈΠΌΡΡΠ΅ΡΡΠ²Π° ΠΏΠΎ ΡΡΠ°Π²Π½Π΅Π½ΠΈΡ Ρ ΠΌΠΎΠΊΡΡΠΌ, Π΄Π»ΠΈΡΠ΅Π»ΡΠ½ΠΎΠ΅ Π²ΡΠ΅ΠΌΡ Π½Π°Ρ
ΠΎΠ΄ΠΈΠ» ΠΎΠ³ΡΠ°Π½ΠΈΡΠ΅Π½Π½ΠΎΠ΅ ΠΏΡΠΈΠΌΠ΅Π½Π΅Π½ΠΈΠ΅ ΠΈΠ·-Π·Π° ΠΏΠΎΠ½ΠΈΠΆΠ΅Π½Π½ΠΎΠ³ΠΎ ΠΊΠ°ΡΠ΅ΡΡΠ²Π° ΠΏΠΎΠ»ΡΡΠ°Π΅ΠΌΠΎΠ³ΠΎ ΠΊΠ»ΠΈΠ½ΠΊΠ΅ΡΠ°, ΠΎΠ΄Π½Π°ΠΊΠΎ, ΡΡΠΏΠ΅Ρ
ΠΈ Π² ΡΠ΅Ρ
Π½ΠΈΠΊΠ΅ ΡΠΎΠ½ΠΊΠΎΠ³ΠΎ ΠΈΠ·ΠΌΠ΅Π»ΡΡΠ΅Π½ΠΈΡ ΠΈ Π³ΠΎΠΌΠΎΠ³Π΅Π½ΠΈΠ·Π°ΡΠΈΠΈ ΡΡΡ
ΠΈΡ
ΡΠΌΠ΅ΡΠ΅ΠΉ ΠΎΠ±Π΅ΡΠΏΠ΅ΡΠΈΠ»ΠΈ Π²ΠΎΠ·ΠΌΠΎΠΆΠ½ΠΎΡΡΡ ΠΏΠΎΠ»ΡΡΠ΅Π½ΠΈΡ Π²ΡΡΠΎΠΊΠΎΠΊΠ°ΡΠ΅ΡΡΠ²Π΅Π½Π½ΡΡ
, ΠΏΠΎΡΡΠ»Π°Π½Π΄ΡΠ΅ΠΌΠ΅Π½ΡΠΎΠ² ΠΈ ΠΏΠΎ ΡΡΡ
ΠΎΠΌΡ ΡΠΏΠΎΡΠΎΠ±Ρ.Β ΠΡΠΈΠΌΠ΅Π½Π΅Π½ΠΈΠ΅ Π½Π°Ρ
ΠΎΠ΄ΠΈΡ ΠΈ ΡΡΠ΅ΡΠΈΠΉ, ΡΠ°ΠΊ Π½Π°Π·ΡΠ²Π°Π΅ΠΌΡΠΉ, ΠΊΠΎΠΌΠ±ΠΈΠ½ΠΈΡΠΎΠ²Π°Π½Π½ΡΠΉ ΡΠΏΠΎΡΠΎΠ±. Π‘ΡΡΠ½ΠΎΡΡΡ Π΅Π³ΠΎ Π·Π°ΠΊΠ»ΡΡΠ°Π΅ΡΡΡ Π² ΡΠΎΠΌ, ΡΡΠΎ ΠΏΠΎΠ΄Π³ΠΎΡΠΎΠ²ΠΊΠ° ΡΡΡΡΠ΅Π²ΠΎΠΉ ΡΠΌΠ΅ΡΠΈ ΠΎΡΡΡΠ΅ΡΡΠ²Π»ΡΠ΅ΡΡΡ ΠΏΠΎ ΠΌΠΎΠΊΡΠΎΠΌΡ ΡΠΏΠΎΡΠΎΠ±Ρ, Π·Π°ΡΠ΅ΠΌ ΡΠ»Π°ΠΌ ΠΎΠ±Π΅Π·Π²ΠΎΠΆΠΈΠ²Π°Π΅ΡΡΡ Π½Π° ΡΠΏΠ΅ΡΠΈΠ°Π»ΡΠ½ΡΡ
ΡΡΡΠ°Π½ΠΎΠ²ΠΊΠ°Ρ
ΠΈ Π½Π°ΠΏΡΠ°Π²Π»ΡΠ΅ΡΡΡ Π² ΠΏΠ΅ΡΡ.
ΠΠΎΠΌΠ±ΠΈΠ½ΠΈΡΠΎΠ²Π°Π½Π½ΡΠΉ ΡΠΏΠΎΡΠΎΠ± ΠΏΠΎ ΡΡΠ΄Ρ Π΄Π°Π½Π½ΡΡ
ΠΏΠΎΡΡΠΈ Π½Π° 20-30% ΡΠ½ΠΈΠΆΠ°Π΅Ρ ΡΠ°ΡΡ
ΠΎΠ΄ ΡΠΎΠΏΠ»ΠΈΠ²Π° ΠΏΠΎ ΡΡΠ°Π²Π½Π΅Π½ΠΈΡ Ρ ΠΌΠΎΠΊΡΡΠΌ, Π½ΠΎ ΠΏΡΠΈ ΡΡΠΎΠΌ Π²ΠΎΠ·ΡΠ°ΡΡΠ°Π΅Ρ ΡΡΡΠ΄ΠΎΡΠΌΠΊΠΎΡΡΡ ΠΏΡΠΎΠΈΠ·Π²ΠΎΠ΄ΡΡΠ²Π° ΠΈ ΡΠ°ΡΡ
ΠΎΠ΄ ΡΠ»Π΅ΠΊΡΡΠΎΡΠ½Π΅ΡΠ³ΠΈΠΈ.
ΠΠ±ΠΆΠΈΠ³ ΡΡΡΡΠ΅Π²ΠΎΠΉ ΡΠΌΠ΅ΡΠΈ ΠΎΡΡΡΠ΅ΡΡΠ²Π»ΡΠ΅ΡΡΡ Π²ΠΎ Π²ΡΠ°ΡΠ°ΡΡΠΈΡ
ΡΡ ΠΏΠ΅ΡΠ°Ρ
. ΠΠ»ΠΈΠ½Π° ΡΠΎΠ²ΡΠ΅ΠΌΠ΅Π½Π½ΡΡ
, Π²ΡΠ°ΡΠ°ΡΡΠΈΡ
ΡΡ ΠΏΠ΅ΡΠ΅ΠΉ Π΄ΠΎΡΡΠΈΠ³Π°Π΅Ρ 150-185 ΠΌ ΠΈ Π±ΠΎΠ»Π΅Π΅, Π° Π΄ΠΈΠ°ΠΌΠ΅ΡΡΒ 4-7 ΠΌ. Π‘ΠΊΠΎΡΠΎΡΡΡ Π²ΡΠ°ΡΠ΅Π½ΠΈΡ ΠΏΠ΅ΡΠΈ ΡΠΎΡΡΠ°Π²Π»ΡΠ΅Ρ 0,5-1,2 ΠΎΠ±/ΠΌΠΈΠ½. Π¨Π»Π°ΠΌ, ΠΏΡΠΎΡ
ΠΎΠ΄Ρ ΡΠ΅ΡΠ΅Π· ΠΏΠ΅ΡΡ ΠΈ ΠΏΠΎΠ΄Π²Π΅ΡΠ³Π°ΡΡΡ Π²ΠΎΠ·Π΄Π΅ΠΉΡΡΠ²ΠΈΡ Π³Π°Π·ΠΎΠ² Π²ΡΡ Π±ΠΎΠ»Π΅Π΅ Π²ΡΡΠΎΠΊΠΎΠΉ ΡΠ΅ΠΌΠΏΠ΅ΡΠ°ΡΡΡΡ, ΠΏΡΠ΅ΡΠ΅ΡΠΏΠ΅Π²Π°Π΅Ρ ΡΡΠ΄ ΡΠΈΠ·ΠΈΡΠ΅ΡΠΊΠΈΡ
ΠΈ ΡΠΈΠ·ΠΈΠΊΠΎ-Ρ
ΠΈΠΌΠΈΡΠ΅ΡΠΊΠΈΡ
ΠΏΡΠ΅Π²ΡΠ°ΡΠ΅Π½ΠΈΠΉ. ΠΡΠΈ ΡΠ΅ΠΌΠΏΠ΅ΡΠ°ΡΡΡΠ°Ρ
ΠΆΠ΅ 1300-1500 Β°Π‘ ΠΌΠ°ΡΠ΅ΡΠΈΠ°Π» ΡΠΏΠ΅ΠΊΠ°Π΅ΡΡΡ, ΠΏΡΠΈΡΡΠΌ ΠΎΠ±ΡΠ°Π·ΡΡΡΡΡ ΠΊΠ»ΠΈΠ½ΠΊΠ΅ΡΠ½ΡΠ΅ Π·Π΅ΡΠ½Π° ΡΠ°Π·ΠΌΠ΅ΡΠΎΠΌ Π΄ΠΎ 15-20 ΠΌΠΌ ΠΈ Π±ΠΎΠ»ΡΡΠ΅. ΠΡΠΎΠΉΠ΄Ρ Π·ΠΎΠ½Ρ Π²ΡΡΠΎΠΊΠΈΡ
ΡΠ΅ΠΌΠΏΠ΅ΡΠ°ΡΡΡ, ΠΊΠ»ΠΈΠ½ΠΊΠ΅Ρ Π½Π°ΡΠΈΠ½Π°Π΅Ρ ΠΎΡ
Π»Π°ΠΆΠ΄Π°ΡΡΡΡ ΠΏΠΎΡΠΎΠΊΠ°ΠΌΠΈ Π±ΠΎΠ»Π΅Π΅ Ρ
ΠΎΠ»ΠΎΠ΄Π½ΠΎΠ³ΠΎ Π²ΠΎΠ·Π΄ΡΡ
Π°. ΠΠ· ΠΏΠ΅ΡΠΈ ΠΎΠ½ Π²ΡΡ
ΠΎΠ΄ΠΈΡ Ρ ΡΠ΅ΠΌΠΏΠ΅ΡΠ°ΡΡΡΠΎΠΉ 1000-1100Β Β°Π‘ ΠΈ Π½Π°ΠΏΡΠ°Π²Π»ΡΠ΅ΡΡΡ Π² ΠΊΠΎΠ»ΠΎΡΠ½ΠΈΠΊΠΎΠ²ΡΠΉ Ρ
ΠΎΠ»ΠΎΠ΄ΠΈΠ»ΡΠ½ΠΈΠΊ, Π³Π΄Π΅ ΠΎΡ
Π»Π°ΠΆΠ΄Π°Π΅ΡΡΡ Π΄ΠΎ 30-50Β Β°Π‘. ΠΡ
Π»Π°ΠΆΠ΄ΡΠ½Π½ΡΠΉ ΠΊΠ»ΠΈΠ½ΠΊΠ΅Ρ ΠΏΠΎΡΡΡΠΏΠ°Π΅Ρ Π½Π° ΡΠΊΠ»Π°Π΄. Π ΠΏΡΠΎΡΠ΅ΡΡΠ΅ Π΄Π²ΠΈΠΆΠ΅Π½ΠΈΡ ΡΠ»Π°ΠΌΠ° ΠΏΠΎ ΠΏΠ΅ΡΠΈ ΠΏΡΠΎΡΠ΅ΠΊΠ°ΡΡ ΡΠ»Π΅Π΄ΡΡΡΠΈΠ΅ ΡΠΈΠ·ΠΈΠΊΠΎ-Ρ
ΠΈΠΌΠΈΡΠ΅ΡΠΊΠΈΠ΅ ΠΏΡΠΎΡΠ΅ΡΡΡ. Π ΡΠΎΠΉ ΡΠ°ΡΡΠΈ ΠΏΠ΅ΡΠΈ, Π³Π΄Π΅ ΡΠ΅ΠΌΠΏΠ΅ΡΠ°ΡΡΡΠ° ΡΠΎΡΡΠ°Π²Π»ΡΠ΅Ρ 300-600Β Β°Π‘ Π½Π°ΡΠΈΠ½Π°Π΅ΡΡΡ ΡΠ½Π΅ΡΠ³ΠΈΡΠ½ΠΎΠ΅ ΠΈΡΠΏΠ°ΡΠ΅Π½ΠΈΠ΅ Π²ΠΎΠ΄Ρ, ΠΊΠΎΡΠΎΡΠΎΠ΅ ΡΠΎΠΏΡΠΎΠ²ΠΎΠΆΠ΄Π°Π΅ΡΡΡ ΠΏΠΎΡΡΠ΅ΠΏΠ΅Π½Π½ΡΠΌ Π·Π°Π³ΡΡΡΠ΅Π²Π°Π½ΠΈΠ΅ΠΌ ΡΠ»Π°ΠΌΠ°. ΠΠ±ΡΠ°Π·ΡΡΡΡΡ ΠΊΡΡΠΏΠ½ΡΠ΅ ΠΊΠΎΠΌΡΡ. ΠΠ°ΡΠ΅ΠΌ, ΡΡΠΈ ΡΠ΅ΠΌΠΏΠ΅ΡΠ°ΡΡΡΠ΅ 400-500 Β°Π‘ ΠΈΠ· ΠΌΠ°ΡΠ΅ΡΠΈΠ°Π»Π° Π²ΡΠ³ΠΎΡΠ°ΡΡ ΠΎΡΠ³Π°Π½ΠΈΡΠ΅ΡΠΊΠΈΠ΅ ΠΏpΠΈΠΌΠ΅ΡΠΈ; Π½Π°ΡΠΈΠ½Π°Π΅ΡΡΡ Π΄Π΅Π³ΠΈΠ΄ΡΠ°ΡΠ°ΡΠΈΡ ΠΊΠ°ΠΎΠ»ΠΈΠ½ΠΈΡΠ°, ΠΈ Π΄ΡΡΠ³ΠΈΡ
Π³Π»ΠΈΠ½ΠΈΡΡΡΡ
ΠΌΠΈΠ½Π΅ΡΠ°Π»ΠΎΠ² Ρ ΠΎΠ±ΡΠ°Π·ΠΎΠ²Π°Π½ΠΈΠ΅ΠΌ, Π² ΡΠ°ΡΡΠ½ΠΎΡΡΠΈ; ΠΊΠ°ΠΎΠ»ΠΈΠ½ΠΈΡΠΎΠ²ΠΎΠ³ΠΎ Π°Π½Π³ΠΈΠ΄ΡΠΈΠ΄Π°. Π£Π΄Π°Π»Π΅Π½ΠΈΠ΅ ΠΈΠ· Π³Π»ΠΈΠ½Ρ Π³ΠΈΠ΄ΡΠ°ΡΠ½ΠΎΠΉ Π²ΠΎΠ΄Ρ ΡΠΎΠΏΡΠΎΠ²ΠΎΠΆΠ΄Π°Π΅ΡΡΡ ΠΏΠΎΡΠ΅ΡΠ΅ΠΉ ΠΏΠ»Π°ΡΡΠΈΡΠ½ΠΎΡΡΠΈ ΠΈ ΡΠ²ΡΠ·ΡΡΡΠΈΡ
ΡΠ²ΠΎΠΉΡΡΠ², ΡΡΠΎ ΠΏΡΠΈΠ²ΠΎΠ΄ΠΈΡ ΠΊ ΡΠ°ΡΠΏΠ°Π΄Ρ ΠΎΠ±ΡΠ°Π·ΠΎΠ²Π°Π²ΡΠΈΡ
ΡΡ ΡΠ°Π½Π΅Π΅ ΠΊΠΎΠΌΡΠ΅Π² ΠΌΠ°ΡΠ΅ΡΠΈΠ°Π»Π° Π² ΠΏΠΎΠ΄Π²ΠΈΠΆΠ½ΡΠΉ ΠΏΠΎΡΠΎΡΠΎΠΊ. Π£ΡΠ°ΡΡΠΎΠΊ ΠΏΠ΅ΡΠΈ, Π³Π΄Π΅ Π²ΠΎΠ΄Π° ΠΈΡΠΏΠ°ΡΡΠ΅ΡΡΡ, ΠΈ ΠΌΠ°ΡΠ΅ΡΠΈΠ°Π» Π²ΡΡΡΡ
Π°Π΅Ρ, Π½Π°Π·ΡΠ²Π°Π΅ΡΡΡ Π·ΠΎΠ½ΠΎΠΉ ΡΡΡΠΊΠΈ. Π‘Π»Π΅Π΄ΡΡΡΠ°Ρ Π·ΠΎΠ½Π°, Π³Π΄Π΅ ΠΏΡΠΎΠΈΡΡ
ΠΎΠ΄ΠΈΡ Π΄Π΅Π³ΠΈΠ΄ΡΠ°ΡΠ°ΡΠΈΡ Π³Π»ΠΈΠ½Ρ ΠΈ ΠΈΠ΄Π΅Ρ Π΄Π°Π»ΡΠ½Π΅ΠΉΡΠ΅Π΅ Π½Π°Π³ΡΠ΅Π²Π°Π½ΠΈΠ΅ Π΄ΠΎ 700-800Β Β°Π‘, Π½Π°Π·ΡΠ²Π°Π΅ΡΡΡ Π·ΠΎΠ½ΠΎΠΉ ΠΏΠΎΠ΄ΠΎΠ³ΡΠ΅Π²Π°. ΠΡΠΈ Π΄Π²Π΅ Π·ΠΎΠ½Ρ Π·Π°Π½ΠΈΠΌΠ°ΡΡ Π΄ΠΎ 50 – 55% Π΄Π»ΠΈΠ½Ρ ΠΏΠ΅ΡΠΈ. ΠΡΠΈ ΡΠ΅ΠΌΠΏΠ΅ΡΠ°ΡΡΡΠ°Ρ
750-800Β Β°Π‘ ΠΈ Π²ΡΡΠ΅ Π² ΠΌΠ°ΡΠ΅ΡΠΈΠ°Π»Π΅ Π½Π°ΡΠΈΠ½Π°ΡΡΡΡ ΡΠ΅Π°ΠΊΡΠΈΠΈ Π² ΡΠ²Π΅ΡΠ΄ΠΎΠΌ ΡΠΎΡΡΠΎΡΠ½ΠΈΠΉ ΠΌΠ΅ΠΆΠ΄Ρ Π΅Π³ΠΎ ΡΠΎΡΡΠ°Π²Π»ΡΡΡΠΈΠΌΠΈ. ΠΠ½Π°ΡΠ°Π»Π΅ ΠΎΠ½ΠΈ Π΅Π΄Π²Π° Π·Π°ΠΌΠ΅ΡΠ½Ρ, ΠΎΠ΄Π½Π°ΠΊΠΎ Ρ ΠΏΠΎΠ²ΡΡΠ΅Π½ΠΈΠ΅ΠΌ ΡΠ΅ΠΌΠΏΠ΅ΡΠ°ΡΡΡΡ ΠΌΠ°ΡΠ΅ΡΠΈΠ°Π»Π° Π΄ΠΎ 1000Β Β°Π‘ ΠΈ Π±ΠΎΠ»Π΅Π΅ ΠΈΠ½ΡΠ΅Π½ΡΠΈΠ²Π½ΠΎΡΡΡ ΠΈΡ
ΡΠ΅Π·ΠΊΠΎ Π²ΠΎΠ·ΡΠ°ΡΡΠ°Π΅Ρ. Π‘Π½Π°ΡΠ°Π»Π° Π² ΡΠ΅Π°ΠΊΡΠΈΠΈ Π²ΡΡΡΠΏΠ°ΡΡ ΠΎΠΊΡΠΈΠ΄Ρ Π°Π»ΡΠΌΠΈΠ½ΠΈΡ ΠΈ ΠΆΠ΅Π»Π΅Π·Π°. ΠΠ½ΠΈ ΠΏΡΠΈΡΠΎΠ΅Π΄ΠΈΠ½ΡΡΡ ΠΊ ΡΠ΅Π±Π΅ ΠΎΠΊΡΠΈΠ΄ ΠΊΠ°Π»ΡΡΠΈΡ ΠΈ ΠΎΠ±ΡΠ°Π·ΡΡΡΡΡ ΠΎΠ΄Π½ΠΎΠΊΠ°Π»ΡΡΠΈΠ΅Π²ΡΠΉ Π°Π»ΡΠΌΠΈΠ½Π°Ρ ΠΈ ΠΎΠ΄Π½ΠΎΠΊΠ°Π»ΡΡΠΈΠ΅Π²ΡΠΉ ΡΠ΅ΡΡΠΈΡ.
Π ΡΠΈΡΡΠΎΠΌ Π²ΠΈΠ΄Π΅ ΡΡΠΈ ΡΠΎΠ΅Π΄ΠΈΠ½Π΅Π½ΠΈΡ Π½Π΅ ΡΡΡΠ΅ΡΡΠ²ΡΡΡ, Π° ΠΎΠ±ΡΠ°Π·ΡΡΡ ΡΠ²ΡΡΠ΄ΡΠΉ ΡΠ°ΡΡΠ²ΠΎΡ, ΡΠ°ΡΡΠ²ΠΎΡΡΡΡΡΡ Π΄ΡΡΠ³ Π² Π΄ΡΡΠ³Π΅. ΠΠΎΠ»ΠΈΡΠ΅ΡΡΠ²ΠΎ ΠΏΡΠΈΡΠΎΠ΅Π΄ΠΈΠ½ΡΠ½Π½ΠΎΠ³ΠΎ ΠΎΠΊΡΠΈΠ΄Π° ΠΊΠ°Π»ΡΡΠΈΡ ΡΠ²Π΅Π»ΠΈΡΠΈΠ²Π°Π΅ΡΡΡ Ρ ΡΠΎΡΡΠΎΠΌ ΡΠ΅ΠΌΠΏΠ΅ΡΠ°ΡΡΡΡ. ΠΡΠΈ 900-1000Β Β°Π‘ ΡΠ΅Π·ΠΊΠΎ ΡΡΠΈΠ»ΠΈΠ²Π°Π΅ΡΡΡ ΡΠ°Π·Π»ΠΎΠΆΠ΅Π½ΠΈΠ΅ ΠΊΠ°ΡΠ±ΠΎΠ½Π°ΡΠ° ΠΊΠ°Π»ΡΡΠΈΡ Ρ ΠΎΠ±ΡΠ°Π·ΠΎΠ²Π°Π½ΠΈΠ΅ΠΌ ΠΎΠΊΠΈΡΠΈ ΠΊΠ°Π»ΡΡΠΈΡ Π² ΡΠ²ΠΎΠ±ΠΎΠ΄Π½ΠΎΠΌ Π²ΠΈΠ΄Π΅ ΠΈ ΡΠ³Π»Π΅ΠΊΠΈΡΠ»ΠΎΠ³ΠΎ Π³Π°Π·Π° Π‘Π2. ΠΡΠΎΡ ΡΡΠ°ΡΡΠΎΠΊ ΠΏΠ΅ΡΠΈ Π½Π°Π·ΡΠ²Π°ΡΡ Π·ΠΎΠ½ΠΎΠΉ ΠΊΠ°Π»ΡΡΠΈΠ½ΠΈΡΠΎΠ²Π°Π½ΠΈΡ. Π ΡΡΠΎΠΉ Π·ΠΎΠ½Π΅ Π²ΡΠ»Π΅Π΄ΡΡΠ²ΠΈΠ΅ ΡΠΎΠ³ΠΎ, ΡΡΠΎ ΡΠ°Π·Π»ΠΎΠΆΠ΅Π½ΠΈΠ΅ Π‘Π°Π‘Π3 ΠΈΠ΄ΡΡ Ρ ΠΏΠΎΠ³Π»ΠΎΡΠ΅Π½ΠΈΠ΅ΠΌ ΡΠ΅ΠΏΠ»Π° ΠΏΠΎΡΡΠ΅Π±Π»Π΅Π½ΠΈΠ΅ ΠΏΠΎΡΠ»Π΅Π΄Π½Π΅Π³ΠΎ Π½Π°ΠΈΠ±ΠΎΠ»ΡΡΠ΅Π΅. ΠΠ° ΡΡΠ°ΡΡΠΊΠ΅ ΠΏΠ΅ΡΠΈ, Π³Π΄Π΅ ΡΠ΅ΠΌΠΏΠ΅ΡΠ°ΡΡΡΠ° ΠΌΠ°ΡΠ΅ΡΠΈΠ°Π»Π° Π΄ΠΎΡΡΠΈΠ³Π°Π΅Ρ 1000-1100Β Β°Π‘ ΠΈ Π³Π΄Π΅ ΠΎΡΠ½ΠΎΠ²Π½Π°Ρ ΠΌΠ°ΡΡΠ° Π‘aΠ‘O3 ΡΠΆΠ΅ ΠΏΡΠ΅Π²ΡΠ°ΡΠΈΠ»Π°ΡΡ Π² ΡΠ²ΠΎΠ±ΠΎΠ΄Π½ΡΡ ΠΎΠΊΠΈΡΡ ΠΊΠ°Π»ΡΡΠΈΡ Π·Π΄Π΅ΡΡ ΡΠ΅Π·ΠΊΠΎ Π²ΠΎΠ·ΡΠ°ΡΡΠ°Π΅Ρ ΠΈΠ½ΡΠ΅Π½ΡΠΈΠ²Π½ΠΎΡΡΡ ΡΠ΅Π°ΠΊΡΠΈΠΉ Π² ΡΠ²ΡΡΠ΄ΠΎΠΌ ΡΠΎΡΡΠΎΡΠ½ΠΈΠΈ. Π Π°ΡΡΠ²ΠΎΡ Π°Π»ΡΠΌΠΈΠ½Π°ΡΠ° ΠΈ ΡΠ΅ΡΡΠΈΡΠ° ΠΊΠ°Π»ΡΡΠΈΡ ΡΠ²ΡΠ·ΡΠ²Π°Π΅Ρ Π²ΡΡ Π±ΠΎΠ»ΡΡΠ΅Π΅ ΠΊΠΎΠ»ΠΈΡΠ΅ΡΡΠ²ΠΎ ΠΎΠΊΡΠΈΠ΄Π° ΠΊΠ°Π»ΡΡΠΈΡ ΠΈ ΡΠΆΠ΅ ΠΎΠ±ΡΠ°Π·ΡΡΡΡΡ Π΄Π²ΡΡ
ΠΊΠ°Π»ΡΡΠΈΠ΅Π²ΡΠΉ Π°Π»ΡΠΌΠΈΠ½Π°Ρ ΠΈ ΡΠ΅ΡΡΠΈΡ ΠΊΠ°Π»ΡΡΠΈΡ. ΠΡΠΎΡ ΡΠ²ΡΡΠ΄ΡΠΉ ΡΠ°ΡΡΠ²ΠΎΡ ΡΠΎΠ΄Π΅ΡΠΆΠΈΡ ΡΠ°Π²Π½ΠΎΠ΅ ΠΊΠΎΠ»ΠΈΡΠ΅ΡΡΠ²ΠΎ ΠΎΠΊΡΠΈΠ΄Π° Π°Π»ΡΠΌΠΈΠ½ΠΈΡ ΠΈ ΠΎΠΊΡΠΈΠ΄Π° ΠΊΠ°Π»ΡΡΠΈΡ. ΠΡΠΎΡ ΡΠ°ΡΡΠ²ΠΎΡ ΠΈΠΌΠ΅Π΅Ρ ΡΠΎΡΡΠ°Π² 4CaOβ’AI2O3β’Fe2O3.
Π ΡΡΡΡΠ΅Π²ΠΎΠΉ ΡΠΌΠ΅ΡΠΈ ΠΎΠΊΡΠΈΠ΄Π° Π°Π»ΡΠΌΠΈΠ½ΠΈΡ ΡΠΎΠ΄Π΅ΡΠΆΠΈΡΡΡ Π±ΠΎΠ»ΡΡΠ΅ ΡΠ΅ΠΌ ΠΎΠΊΡΠΈΠ΄Π° ΠΆΠ΅Π»Π΅Π·Π°, ΠΏΠΎΡΡΠΎΠΌΡ ΠΎΡΡΠ°Π²ΡΠΈΠΉΡΡ Π°Π»ΡΠΌΠΈΠ½Π°Ρ ΠΊΠ°Π»ΡΡΠΈΡ ΠΏΡΠΎΠ΄ΠΎΠ»ΠΆΠ°Π΅Ρ ΡΠ²ΡΠ·ΡΠ²Π°ΡΡ ΠΎΠΊΡΠΈΠ΄ ΠΊΠ°Π»ΡΡΠΈΡ Ρ ΠΎΠ±ΡΠ°Π·ΠΎΠ²Π°Π½ΠΈΠ΅ΠΌ ΡΡΠ΅Ρ
ΠΊΠ°Π»ΡΡΠΈΠ΅Π²ΠΎΠ³ΠΎ Π°Π»ΡΠΌΠΈΠ½Π°ΡΠ°. ΠΠ³ΠΎ ΠΎΠ±ΡΠ°Π·ΠΎΠ²Π°Π½ΠΈΠ΅ Π·Π°ΠΊΠ°Π½ΡΠΈΠ²Π°Π΅ΡΡΡ ΠΏΡΠΈ ΡΠ΅ΠΌΠΏΠ΅ΡΠ°ΡΡΡΠ΅ 1200Β Β°Π‘. ΠΡΠΈΡΠΎΠ΅Π΄ΠΈΠ½Π΅Π½ΠΈΠ΅ ΠΎΠΊΡΠΈΠ΄Π° ΠΊΠ°Π»ΡΡΠΈΡ ΠΊ ΠΎΠΊΡΠΈΠ΄Ρ ΠΊΡΠ΅ΠΌΠ½ΠΈΡ Π½Π°ΡΠΈΠ½Π°Π΅ΡΡΡ ΠΏΡΠΈ 600Β Β°Π‘, Π½ΠΎ Π΄ΠΎΡΡΠ°ΡΠΎΡΠ½ΠΎ Π±ΡΡΡΡΠΎ ΠΏΡΠΎΠΈΡΡ
ΠΎΠ΄ΠΈΡ ΠΏΡΠΈ ΡΠ΅ΠΌΠΏΠ΅ΡΠ°ΡΡΡΠ΅ 900-1100Β Β°Π‘. Π Π΅Π°ΠΊΡΠΈΠΈ ΠΎΠ±ΡΠ°Π·ΠΎΠ²Π°Π½ΠΈΡ ΡΠΈΠ»ΠΈΠΊΠ°ΡΠΎΠ², Π°Π»ΡΠΌΠΈΠ½Π°ΡΠΎΠ² ΠΈ ΡΠ΅ΡΡΠΈΡΠΎΠ² ΠΊΠ°Π»ΡΡΠΈΡ ΡΠ²Π»ΡΡΡΡΡ ΡΠΊΠ·ΠΎΡΠ΅ΡΠΌΠΈΡΠ΅ΡΠΊΠΈΠΌΠΈ, ΡΡΠΎ ΠΏΡΠΈΠ²ΠΎΠ΄ΠΈΡ ΠΊ ΠΈΠ½ΡΠ΅Π½ΡΠΈΠ²Π½ΠΎΠΌΡ ΠΏΠΎΠ²ΡΡΠ΅Π½ΠΈΡ ΡΠ΅ΠΌΠΏΠ΅ΡΠ°ΡΡΡΡ ΠΌΠ°ΡΠ΅ΡΠΈΠ°Π»Π° Π½Π° 150-200Β Β°Π‘ Π½Π° ΠΊΠΎΡΠΎΡΠΊΠΎΠΌ ΡΡΠ°ΡΡΠΊΠ΅ ΠΏΠ΅ΡΠΈ Π² Π½Π΅ΡΠΊΠΎΠ»ΡΠΊΠΎ ΠΌΠ΅ΡΡΠΎΠ². ΠΡΠΎΡ ΡΡΠ°ΡΡΠΎΠΊ ΠΏΠ΅ΡΠΈ ΠΏΠΎΠ»ΡΡΠΈΠ» Π½Π°Π·Π²Π°Π½ΠΈΠ΅ ΡΠΊΠ·ΠΎΡΠ΅ΡΠΌΠΈΡΠ΅ΡΠΊΠΎΠΉ Π·ΠΎΠ½Ρ. Π ΠΊΠΎΠ½ΡΡ ΡΠΊΠ·ΠΎΡΠ΅ΡΠΌΠΈΡΠ΅ΡΠΊΠΎΠΉ Π·ΠΎΠ½Ρ ΡΠ΅ΠΌΠΏΠ΅ΡΠ°ΡΡΡΠ° ΠΌΠ°ΡΠ΅ΡΠΈΠ°Π»Π° Π΄ΠΎΡΡΠΈΠ³Π°Π΅Ρ, ΠΏΡΠΈΠΌΠ΅ΡΠ½ΠΎ, 1300Β Β°Π‘. ΠΡΠΈ ΡΠ΅ΠΌΠΏΠ΅ΡΠ°ΡΡΡΠ΅ 1250Β Β°Π‘ Π·Π°ΠΊΠ°Π½ΡΠΈΠ²Π°Π΅ΡΡΡ ΠΎΠ±ΡΠ°Π·ΠΎΠ²Π°Π½ΠΈΠ΅ Π΄Π²ΡΡ
ΠΊΠ°Π»ΡΡΠΈΠ΅Π²ΠΎΠ³ΠΎ ΡΠΈΠ»ΠΈΠΊΠ°ΡΠ°. ΠΠΎΡΠΊΠΎΠ»ΡΠΊΡ ΡΡΡΡΠ΅Π²Π°Ρ ΡΠΌΠ΅ΡΡ ΡΠΎΠ΄Π΅ΡΠΆΠΈΡ Π±ΠΎΠ»ΡΡΠ΅ ΠΎΠΊΡΠΈΠ΄Π° ΠΊΠ°Π»ΡΡΠΈΡ ΡΠ΅ΠΌ ΡΡΠΎ Π½ΡΠΆΠ½ΠΎ Π΄Π»Ρ ΠΎΠ±ΡΠ°Π·ΠΎΠ²Π°Π½ΠΈΡ Π‘2S, Π‘4ΠF, Π‘3Π,Β ΡΠΎ ΠΎΡΡΠ°Π»ΡΠ½ΠΎΠ΅ ΠΊΠΎΠ»ΠΈΡΠ΅ΡΡΠ²ΠΎ Π‘Π°Π ΠΈΠ΄ΡΡ Π½Π° ΠΎΠ±ΡΠ°Π·ΠΎΠ²Π°Π½ΠΈΠ΅ ΡΡΠ΅Ρ
ΠΊΠ°Π»ΡΡΠΈΠ΅Π²ΠΎΠ³ΠΎ ΡΠΈΠ»ΠΈΠΊΠ°ΡΠ°. ΠΡΠΈ ΡΠ΅ΠΌΠΏΠ΅ΡΠ°ΡΡΡΠ΅ 1300Β Β°Π‘ Π½Π°ΡΠΈΠ½Π°Π΅ΡΡΡ ΡΠΏΠ΅ΠΊΠ°Π½ΠΈΠ΅ ΠΌΠ°ΡΠ΅ΡΠΈΠ°Π»Π° Π²ΡΠ»Π΅Π΄ΡΡΠ²ΠΈΠ΅ ΠΎΠ±ΡΠ°Π·ΠΎΠ²Π°Π½ΠΈΡ Π² Π½ΡΠΌ ΡΠ°ΡΠΏΠ»Π°Π²Π° Π² ΠΊΠΎΠ»ΠΈΡΠ΅ΡΡΠ²Π΅ 20-30%Β ΠΎΠ±ΡΡΠΌΠ° Π½Π°ΡΠ°Π²ΡΠ΅ΠΉ ΡΠΏΠ΅ΠΊΠ°ΡΡΡΡ ΠΌΠ°ΡΡΡ.
Π Π½Π°ΡΠ°Π»ΡΠ½ΡΠΉ ΠΌΠΎΠΌΠ΅Π½Ρ ΡΠΏΠ΅ΠΊΠ°Π½ΠΈΡ Π² ΡΠ°ΡΠΏΠ»Π°Π² ΠΏΠ΅ΡΠ΅Ρ
ΠΎΠ΄ΡΡ Π‘3Π, Π‘4ΠF, ΠΈ Π‘Π°Π, Π² Π΄Π°Π»ΡΠ½Π΅ΠΉΡΠ΅ΠΌ Π² Π½ΡΠΌ Π½Π°ΡΠΈΠ½Π°Π΅Ρ ΡΠ°ΡΡΠ²ΠΎΡΡΡΡΡΡ ΠΈ Π΄Π²ΡΡ
ΠΊΠ°Π»ΡΡΠΈΠ΅Π²ΡΠΉ ΡΠΈΠ»ΠΈΠΊΠ°Ρ C2S. ΠΡΠΈ ΡΡΠΎΠΌ Π² ΠΆΠΈΠ΄ΠΊΠΎΠΉ ΡΠ°Π·Π΅ ΡΠΎΠ·Π΄Π°ΡΡΡΡ Π±Π»Π°Π³ΠΎΠΏΡΠΈΡΡΠ½ΡΠ΅ ΡΡΠ»ΠΎΠ²ΠΈΡ Π΄Π»Ρ ΠΎΠ±ΡΠ°Π·ΠΎΠ²Π°Π½ΠΈΡ ΠΎΡΠ½ΠΎΠ²Π½ΠΎΠ³ΠΎ ΠΌΠΈΠ½Π΅ΡΠ°Π»Π° ΠΏΠΎΡΡΠ»Π°Π½Π΄ΡΠ΅ΠΌΠ΅Π½ΡΠ° – ΡΡΠ΅Ρ
ΠΊΠ°Π»ΡΡΠΈΠ΅Π²ΠΎΠ³ΠΎ ΡΠΈΠ»ΠΈΠΊΠ°ΡΠ° C3S ΠΈΠ· C2S ΠΈ Π‘Π°Π. ΠΡΠΎ ΡΠΎΠ΅Π΄ΠΈΠ½Π΅Π½ΠΈΠ΅ ΠΏΠ»ΠΎΡ
ΠΎ ΡΠ°ΡΡΠ²ΠΎΡΠΈΠΌΠΎ Π² ΡΠ°ΡΠΏΠ»Π°Π²Π΅, Π²ΡΠ»Π΅Π΄ΡΡΠ²ΠΈΠ΅ ΡΠ΅Π³ΠΎ ΠΎΠ½ΠΎ Π²ΡΠ΄Π΅Π»ΡΠ΅ΡΡΡ ΠΈΠ· Π½Π΅Π³ΠΎ Π² Π²ΠΈΠ΄Π΅ ΠΌΠ΅Π»ΠΊΠΈΡ
ΠΊΡΠΈΡΡΠ°Π»Π»ΠΎΠ², ΠΊΠΎΡΠΎΡΡΠ΅ Π² ΠΏΠΎΡΠ»Π΅Π΄ΡΡΡΠ΅ΠΌ ΠΌΠΎΠ³ΡΡ Π·Π½Π°ΡΠΈΡΠ΅Π»ΡΠ½ΠΎ ΡΠ²Π΅Π»ΠΈΡΠΈΠ²Π°ΡΡΡΡ Π² ΡΠ°Π·ΠΌΠ΅ΡΠ°Ρ
. ΠΡΠ΄Π΅Π»Π΅Π½ΠΈΠ΅ ΠΈΠ· ΡΠ°ΡΠΏΠ»Π°Π²Π° C3S ΡΠΎΠΏΡΠΎΠ²ΠΎΠΆΠ΄Π°Π΅ΡΡΡ ΠΏΠΎΠ½ΠΈΠΆΠ΅Π½ΠΈΠ΅ΠΌ Π² Π½ΡΠΌ ΠΊΠΎΠ½ΡΠ΅Π½ΡΡΠ°ΡΠΈΠΈ: C2S ΠΈ ΠΎΠΊΠΈΡΠΈ ΠΊΠ°Π»ΡΡΠΈΡ, ΡΡΠΎ ΠΏΡΠΈΠ²ΠΎΠ΄ΠΈΡ ΠΊ ΠΏΠ΅ΡΠ΅Ρ
ΠΎΠ΄Ρ Π² ΡΠ°ΡΠΏΠ»Π°Π² Π½ΠΎΠ²ΡΡ
ΠΏΠΎΡΡΠΈΠΉ ΡΡΠΈΡ
Π²Π΅ΡΠ΅ΡΡΠ², ΠΎΡΡΠ°Π²ΡΠΈΡ
ΡΡ Π² ΡΠ²ΡΡΠ΄ΠΎΠΌ ΡΠΎΡΡΠΎΡΠ½ΠΈΠΈ Π² ΠΎΠ±ΡΠ΅ΠΉ ΠΌΠ°ΡΡΠ΅ ΠΌΠ°ΡΠ΅ΡΠΈΠ°Π»Π°. ΠΡΠΎ Π² ΡΠ²ΠΎΡ ΠΎΡΠ΅ΡΠ΅Π΄Ρ ΠΎΠ±ΡΡΠ»Π°Π²Π»ΠΈΠ²Π°Π΅Ρ Π΄Π°Π»ΡΠ½Π΅ΠΉΡΠΈΠΉ Ρ
ΠΎΠ΄ ΠΏΡΠΎΡΠ΅ΡΡΠ° ΠΎΠ±ΡΠ°Π·ΠΎΠ²Π°Π½ΠΈΡ Π² ΡΠ°ΡΠΏΠ»Π°Π²Π΅ ΠΈ Π²ΡΠ΄Π΅Π»Π΅Π½ΠΈΡ ΠΈΠ· Π½Π΅Π³ΠΎ Π‘3S Π΄ΠΎ ΠΏΠΎΡΡΠΈ ΠΏΠΎΠ»Π½ΠΎΠ³ΠΎ ΡΠ²ΡΠ·ΡΠ²Π°Π½ΠΈΡ ΡΠ²ΠΎΠ±ΠΎΠ΄Π½ΠΎΠΉ ΠΎΠΊΠΈΡΠΈ ΠΊΠ°Π»ΡΡΠΈΡ Ρ Π‘2S. Π’ΡΠ΅Ρ
ΠΊΠ°Π»ΡΡΠΈΠ΅Π²ΡΠΉ ΡΠΈΠ»ΠΈΠΊΠ°Ρ Π²ΡΠ΄Π΅Π»ΡΠ΅ΡΡΡ ΠΈΠ· ΡΠ°ΡΠΏΠ»Π°Π²Π° Π²ΠΌΠ΅ΡΡΠ΅ Ρ Π½Π΅Π±ΠΎΠ»ΡΡΠΈΠΌΠΈ ΠΊΠΎΠ»ΠΈΡΠ΅ΡΡΠ²Π°ΠΌΠΈ Al2O3 ΠΈ MgO, ΠΎΠ±ΡΠ°Π·ΡΡ Ρ Π½ΠΈΠΌΠΈ ΡΠ²ΡΡΠ΄ΡΠΉ ΡΠ°ΡΡΠ²ΠΎΡ, ΠΊΠΎΡΠΎΡΡΠΉ Π½Π°Π·ΡΠ²Π°ΡΡ Π°Π»ΠΈΡΠΎΠΌ.
Π£ΡΠ°ΡΡΠΎΠΊ ΠΏΠ΅ΡΠΈ, Π³Π΄Π΅ ΠΏΡΠΎΡ
ΠΎΠ΄ΠΈΡ ΡΠΏΠ΅ΠΊΠ°Π½ΠΈΠ΅ ΠΌΠ°ΡΠ΅ΡΠΈΠ°Π»Π°, ΠΈ ΠΎΠ±ΡΠ°Π·ΠΎΠ²Π°Π½ΠΈΠ΅ Π°Π»ΠΈΡΠ° Π½Π°Π·ΡΠ²Π°Π΅ΡΡΡ Π·ΠΎΠ½ΠΎΠΉ ΡΠΏΠ΅ΠΊΠ°Π½ΠΈΡ.Β ΠΠ΄Π΅ΡΡ ΠΌΠ°ΡΠ΅ΡΠΈΠ°Π»Ρ Π½Π°Π³ΡΠ΅Π²Π°Π΅ΡΡΡ ΠΏΡΠΈΠΌΠ΅ΡΠ½ΠΎ ΠΎΡ 1300 Π΄ΠΎ 1450Β Β°Π‘, ΡΡΠΎ ΡΠΏΠΎΡΠΎΠ±ΡΡΠ²ΡΠ΅Ρ Π±ΠΎΠ»Π΅Π΅ Π±ΡΡΡΡΠΎΠΌΡ ΡΡΠ²ΠΎΠ΅Π½ΠΈΡ ΠΎΠΊΠΈΡΠΈ ΠΊΠ°Π»ΡΡΠΈΡ Π΄Π²ΡΡ
ΠΊΠ°Π»ΡΡΠΈΠ΅Π²ΡΠΌ ΡΠΈΠ»ΠΈΠΊΠ°ΡΠΎΠΌ ΠΈ ΠΎΠ±ΡΠ°Π·ΠΎΠ²Π°Π½ΠΈΡ Π°Π»ΠΈΡΠ°. ΠΠΎΡΠ»Π΅ Π·ΠΎΠ½Ρ ΡΠΏΠ΅ΠΊΠ°Π½ΠΈΡ ΠΎΠ±ΠΆΠΈΠ³Π°Π΅ΠΌΡΠΉ ΠΌΠ°ΡΠ΅ΡΠΈΠ°Π» ΠΏΠ΅ΡΠ΅Ρ
ΠΎΠ΄ΠΈΡ Π² Π·ΠΎΠ½Ρ ΠΎΡ
Π»Π°ΠΆΠ΄Π΅Π½ΠΈΡ. ΠΠΎ ΡΠ΅ΠΌΠΏΠ΅ΡΠ°ΡΡΡΡ ΠΏΡΠΈΠΌΠ΅ΡΠ½ΠΎ 1300Β Β°Π‘ Π² Π½ΡΠΌ Π΅ΡΡ ΠΏΡΠΈΡΡΡΡΡΠ²ΡΠ΅Ρ ΠΆΠΈΠ΄ΠΊΠ°Ρ ΡΠ°Π·Π° ΠΈ ΠΏΡΠΎΠ΄ΠΎΠ»ΠΆΠ°Π΅ΡΡΡ ΡΠ΅Π°ΠΊΡΠΈΡ ΡΡΠ²ΠΎΠ΅Π½ΠΈΡ ΠΎΠΊΠΈΡΠΈ ΠΊΠ°Π»ΡΡΠΈΡ ΠΈ ΠΎΠ±ΡΠ°Π·ΠΎΠ²Π°Π½ΠΈΡ C3S. ΠΠ°ΡΠ΅ΠΌ ΠΆΠΈΠ΄ΠΊΠ°Ρ ΡΠ°Π·Π° Π·Π°ΡΡΡΠ²Π°Π΅Ρ ΠΈ ΡΠΏΠ΅ΠΊΠ°Π½ΠΈΠ΅ Π·Π°ΠΊΠ°Π½ΡΠΈΠ²Π°Π΅ΡΡΡ. ΠΠΎΡΠ»Π΅Π΄Π½ΠΈΠΉ ΡΡΠ°ΡΡΠΎΠΊ ΠΏΠ΅ΡΠΈ, Π³Π΄Π΅ ΠΏΠΎΠ»ΡΡΠ΅Π½Π½ΡΠΉ ΠΊΠ»ΠΈΠ½ΠΊΠ΅Ρ ΠΎΡ
Π»Π°ΠΆΠ΄Π°Π΅ΡΡΡ Π²ΠΎΠ·Π΄ΡΡ
ΠΎΠΌ ΠΎΡ 1300Β Β°Π‘ Π΄ΠΎ ΡΠ΅ΠΌΠΏΠ΅ΡΠ°ΡΡΡΡ ΠΏΡΠΈ ΠΊΠΎΡΠΎΡΠΎΠΉ Π²ΡΡ
ΠΎΠ΄ΠΈΡ ΠΈΠ· ΠΏΠ΅ΡΠΈ (1000-1100Β Β°Π‘) Π½Π°Π·ΡΠ²Π°Π΅ΡΡΡ Π·ΠΎΠ½ΠΎΠΉ ΠΎΡ
Π»Π°ΠΆΠ΄Π΅Π½ΠΈΡ. ΠΠ±ΡΡΠ½ΠΎ ΠΏΡΠΈ ΠΎΡ
Π»Π°ΠΆΠ΄Π΅Π½ΠΈΠΈ ΠΊΠ»ΠΈΠ½ΠΊΠ΅ΡΠ° Ρ 1450 Π΄ΠΎ 1300Β Β°Π‘ ΠΈ Π½ΠΈΠΆΠ΅ ΠΆΠΈΠ΄ΠΊΠ°Ρ ΡΠ°Π·Π° Π² Π½ΡΠΌ Π·Π°ΡΡΡΠ²Π°Π΅Ρ ΡΠ°ΡΡΠΈΡΠ½ΠΎ Π² Π²ΠΈΠ΄Π΅ ΡΡΠ΅ΠΊΠ»Π°, ΡΠ°ΡΡΠΈΡΠ½ΠΎ ΠΏΡΠΈ ΡΡΠΎΠΌ ΠΏΡΠΎΠΈΡΡ
ΠΎΠ΄ΠΈΡ ΠΊΡΠΈΡΡΠ°Π»Π»ΠΈΠ·Π°ΡΠΈΡ ΠΈΠ· ΡΠ°ΡΠΏΠ»Π°Π²Π° Π‘3A, C4AF, Π° ΡΠ°ΠΊΠΆΠ΅ MgO. Π‘ΡΠ΅ΠΏΠ΅Π½Ρ Π·Π°ΠΊΡΠΈΡΡΠ°Π»Π»ΠΈΠ·ΠΎΠ²Π°Π½Π½ΠΎΡΡΠΈ ΡΠ°ΡΠΏΠ»Π°Π²Π° Π·Π°Π²ΠΈΡΠΈΡ ΠΎΡ ΡΠΊΠΎΡΠΎΡΡΠΈ ΠΎΡ
Π»Π°ΠΆΠ΄Π΅Π½ΠΈΡ ΠΌΠ°ΡΠ΅ΡΠΈΠ°Π»Π° ΠΏΠΎΡΠ»Π΅ Π΅Π³ΠΎ Π²ΡΡ
ΠΎΠ΄Π° ΠΈΠ· Π·ΠΎΠ½Ρ ΡΠΏΠ΅ΠΊΠ°Π½ΠΈΡ.
ΠΡ
Π»Π°ΠΆΠ΄Π΅Π½Π½ΡΠΉ ΠΊΠ»ΠΈΠ½ΠΊΠ΅Ρ Π² ΠΎΡΠ½ΠΎΠ²Π½ΠΎΠΌ ΡΠΎΡΡΠΎΠΈΡ ΠΈΠ· ΠΊΡΠΈΡΡΠ°Π»Π»ΠΎΠ² ΠΌΠΈΠ½Π΅ΡΠ°Π»ΠΎΠ² – ΡΠΈΠ»ΠΈΠΊΠ°ΡΠΎΠ² (Π°Π»ΠΈΡΠ° ΠΈ Π±Π΅Π»ΠΈΡΠ°) ΠΈ ΠΏΡΠΎΠΌΠ΅ΠΆΡΡΠΎΡΠ½ΠΎΠ³ΠΎ Π²Π΅ΡΠ΅ΡΡΠ²Π°, Π² ΠΊΠΎΡΠΎΡΠΎΠ΅ Π²Ρ
ΠΎΠ΄ΠΈΡ ΡΡΠ΅ΠΊΠ»ΠΎ, ΠΌΠΈΠ½Π΅ΡΠ°Π»Ρ ΠΏΠ»Π°Π²ΠΊΠΈ (Π‘4ΠF, C3A, Π‘3Π3), Π° ΡΠ°ΠΊΠΆΠ΅ ΠΎΠΊΠΈΡΡ ΠΊΠ°Π»ΡΡΠΈΡ ΠΈ ΠΌΠ°Π³Π½ΠΈΡ (Π² Π²ΠΈΠ΄Π΅ ΠΊΡΠΈΡΡΠ°Π»Π»ΠΎΠ²).
Π¦Π΅ΠΌΠ΅Π½ΡΠ½ΡΠΉ ΠΊΠ»ΠΈΠ½ΠΊΠ΅Ρ
ΠΡΠ΅ΠΌΡ Π½Π° ΡΡΠ΅Π½ΠΈΠ΅:
5 ΠΌΠΈΠ½ΡΡ
5475
Π¦Π΅ΠΌΠ΅Π½ΡΠ½ΡΠΉ ΠΊΠ»ΠΈΠ½ΠΊΠ΅Ρ ΠΏΡΠ΅Π΄ΡΡΠ°Π²Π»ΡΠ΅Ρ ΡΠΎΠ±ΠΎΠΉ ΠΏΡΠΎΠ΄ΡΠΊΡ, ΠΊΠΎΡΠΎΡΡΠΉ ΠΏΡΠΎΠΈΠ·Π²ΠΎΠ΄ΡΡ Π² ΠΏΡΠΎΡΠ΅ΡΡΠ΅ ΠΎΠ±ΠΆΠΈΠ³Π° Π΄ΠΎ ΡΠΎΡΡΠΎΡΠ½ΠΈΡ ΠΏΠ»Π°Π²Π»Π΅Π½ΠΈΡ ΠΈΠ»ΠΈ ΡΠΏΠ΅ΠΊΠ°Π½ΠΈΡ ΡΡΡΡΠ΅Π²ΠΎΠΉ ΡΠΌΠ΅ΡΠΈ ΠΎΠΏΡΠ΅Π΄Π΅Π»Π΅Π½Π½ΠΎΠ³ΠΎ ΡΠΎΡΡΠ°Π²Π°. ΠΠ»ΠΈΠ½ΠΊΠ΅Ρ ΡΠ²Π»ΡΠ΅ΡΡΡ ΠΏΡΠΎΠΌΠ΅ΠΆΡΡΠΎΡΠ½ΡΠΌ ΠΏΡΠΎΠ΄ΡΠΊΡΠΎΠΌ Π² ΠΏΡΠΎΡΠ΅ΡΡΠ΅ ΠΏΡΠΎΠΈΠ·Π²ΠΎΠ΄ΡΡΠ²Π° ΡΠ΅ΠΌΠ΅Π½ΡΠ°.
Π ΡΠΏΠ΅ΡΠΈΠ°Π»ΡΠ½ΡΡ ΠΏΠ΅ΡΠ°Ρ , ΠΏΡΠΈ ΠΎΡΠ΅Π½Ρ Π²ΡΡΠΎΠΊΠΎΠΉ ΡΠ΅ΠΌΠΏΠ΅ΡΠ°ΡΡΡΠ΅ (Π²ΡΡΠ΅ 1000 Π³ΡΠ°Π΄ΡΡΠΎΠ²) Π½Π°Π³ΡΠ΅Π²Π°ΡΡ ΡΠΌΠ΅ΡΡ ΠΈΠ·Π²Π΅ΡΡΠ½ΡΠΊΠΎΠ² ΠΈ ΡΠ°Π·Π½ΡΡ Π³Π»ΠΈΠ½, Π² ΠΈΡΠΎΠ³Π΅ ΠΏΠΎΠ»ΡΡΠ°Ρ ΡΠΏΠ΅ΠΊΡΠΈΠΉΡΡ Π³ΡΠ°Π½ΡΠ»ΠΈΡΠΎΠ²Π°Π½Π½ΡΠΉ ΠΌΠ°ΡΠ΅ΡΠΈΠ°Π». Π₯ΠΈΠΌΠΈΡΠ΅ΡΠΊΠΈ ΡΡΠΎ ΡΠΌΠ΅ΡΡ Π°Π»ΡΠΌΠΈΠ½Π°ΡΠ° ΠΈ Π°Π»ΡΠΌΠΎΡΠ΅ΡΡΠΈΡΠ° ΠΊΠ°Π»ΡΡΠΈΡ Ρ ΡΠΈΠ»ΠΈΠΊΠ°ΡΠ°ΠΌΠΈ. ΠΠ»Ρ ΠΏΡΠΈΠ³ΠΎΡΠΎΠ²Π»Π΅Π½ΠΈΡ ΡΠ΅ΠΌΠ΅Π½ΡΠ° ΠΊΠ»ΠΈΠ½ΠΊΠ΅Ρ ΠΈΠ·ΠΌΠ΅Π»ΡΡΠ°ΡΡ, Π΄ΠΎΠ±Π°Π²Π»ΡΡΡ Π² Π½Π΅Π³ΠΎ Π³ΠΈΠΏΡ ΠΈ Π΄ΡΡΠ³ΠΈΠ΅ Π²Π΅ΡΠ΅ΡΡΠ²Π°.
Π‘ΡΠΎΠΈΠΌΠΎΡΡΡ ΠΊΠ»ΠΈΠ½ΠΊΠ΅ΡΠ° Π½Π°Ρ
ΠΎΠ΄ΠΈΡΡΡ Π² Π΄ΠΎΡΡΠ°ΡΠΎΡΠ½ΠΎ ΡΠΈΡΠΎΠΊΠΈΡ
ΠΏΡΠ΅Π΄Π΅Π»Π°Ρ
ΠΈ Π½Π°ΠΏΡΡΠΌΡΡ Π·Π°Π²ΠΈΡΠΈΡ ΠΎΡ ΡΠΎΡΡΠ°. ΠΡΠΈΠΌΠ΅Π½ΡΠ΅ΡΡΡ Π² ΡΠ°ΠΌΡΡ
ΡΠ°Π·Π½ΡΡ
ΡΠ΅ΠΌΠΎΠ½ΡΠ½ΠΎ-ΡΡΡΠΎΠΈΡΠ΅Π»ΡΠ½ΡΡ
ΡΠ°Π±ΠΎΡΠ°Ρ
.
Π‘ΠΎΠ΄Π΅ΡΠΆΠ°Π½ΠΈΠ΅
- 1 ΠΡΠΎΠΈΠ·Π²ΠΎΠ΄ΡΡΠ²ΠΎ ΡΠ΅ΠΌΠ΅Π½ΡΠ°
- 2 Π§Π΅ΡΡΡΠ΅ Π³Π»Π°Π²Π½ΡΠ΅ ΡΠ°Π·Ρ ΠΊΠ»ΠΈΠ½ΠΊΠ΅ΡΠ°
- 2.1 ΠΠ»ΠΈΡ
- 2.2 ΠΠ΅Π»ΠΈΡ
- 2.3 ΠΠ»ΡΠΌΠΈΠ½Π°ΡΠ½Π°Ρ ΡΠ°Π·Π°
- 2.4 ΠΠ»ΡΠΌΠΎΡΠ΅ΡΡΠΈΡΠ½Π°Ρ ΡΠ°Π·Π°
ΠΡΠΎΠΈΠ·Π²ΠΎΠ΄ΡΡΠ²ΠΎ ΡΠ΅ΠΌΠ΅Π½ΡΠ°
Π ΠΏΡΠΎΡΠ΅ΡΡΠ΅ Π½Π°Π³ΡΠ΅Π²Π°Π½ΠΈΡ ΡΠΌΠ΅ΡΠΈ, ΠΊΠΎΡΠΎΡΡΡ ΠΏΠΎΠ»ΡΡΠ°ΡΡ ΠΈΠ· ΠΈΠ·Π²Π΅ΡΡΠ½ΡΠΊΠ° (Π΄ΠΎ 75%), Π³Π»ΠΈΠ½Ρ (Π΄ΠΎ 25%) Π»ΠΈΠ±ΠΎ Π΄ΡΡΠ³ΠΈΡ ΠΏΠΎΡ ΠΎΠΆΠΈΡ ΠΏΠΎ ΡΠΎΡΡΠ°Π²Ρ ΠΈ Π°ΠΊΡΠΈΠ²Π½ΠΎΡΡΠΈ ΠΌΠ°ΡΠ΅ΡΠΈΠ°Π»ΠΎΠ², Π΄ΠΎ ΡΠ΅ΠΌΠΏΠ΅ΡΠ°ΡΡΡΡ +1450Π‘ Π΄ΠΎΡΡΠΈΠ³Π°Π΅ΡΡΡ ΡΠΎΡΡΠΎΡΠ½ΠΈΠ΅ ΡΠ°ΡΡΠΈΡΠ½ΠΎΠ³ΠΎ ΠΏΠ»Π°Π²Π»Π΅Π½ΠΈΡ β ΡΠ°ΠΊΠΈΠΌ ΠΎΠ±ΡΠ°Π·ΠΎΠΌ ΠΎΠ±ΡΠ°Π·ΡΡΡΡΡ Π³ΡΠ°Π½ΡΠ»Ρ ΠΊΠ»ΠΈΠ½ΠΊΠ΅ΡΠ°.
Π§ΡΠΎΠ±Ρ Π² ΠΈΡΠΎΠ³Π΅ ΠΏΠΎΠ»ΡΡΠΈΡΡ ΡΠ΅ΠΌΠ΅Π½Ρ, ΠΊΠ»ΠΈΠ½ΠΊΠ΅Ρ ΡΠΌΠ΅ΡΠΈΠ²Π°Π΅ΡΡΡ Ρ 2-5% Π³ΠΈΠΏΡΠ° (ΡΠΎΡΠ½ΡΠΉ ΠΎΠ±ΡΠ΅ΠΌ Π·Π°Π²ΠΈΡΠΈΡ ΠΎΡ ΡΠΎΠ΄Π΅ΡΠΆΠ°Π½ΠΈΡ SO3 Π² ΡΠ°ΠΌΠΎΠΌ ΠΊΠ»ΠΈΠ½ΠΊΠ΅ΡΠ΅ ΠΈ ΠΌΠ°ΡΠΊΠΈ Π³ΠΈΠΏΡΠ°), Π·Π°ΡΠ΅ΠΌ ΠΏΠ΅ΡΠ΅ΠΌΠ°Π»ΡΠ²Π°Π΅ΡΡΡ Π² ΡΠΎΠ½ΡΠ°ΠΉΡΡΡ ΠΏΡΠ»Ρ. ΠΠ»Π°Π³ΠΎΠ΄Π°ΡΡ Π³ΠΈΠΏΡΡ ΡΠ΄Π°Π΅ΡΡΡ ΠΎΠ±Π΅ΡΠΏΠ΅ΡΠΈΡΡ Π±ΡΡΡΡΠΎΠ΅ ΡΡ Π²Π°ΡΡΠ²Π°Π½ΠΈΠ΅ ΠΌΠ°ΡΠ΅ΡΠΈΠ°Π»Π°. Π₯ΠΎΡΡ, Π² Π½Π΅ΠΊΠΎΡΠΎΡΡΡ ΡΠ»ΡΡΠ°ΡΡ Π΅Π³ΠΎ ΡΠ°ΡΡΠΈΡΠ½ΠΎ Π·Π°ΠΌΠ΅Π½ΡΡΡ ΠΈΠ½ΡΠΌΠΈ ΡΠΎΡΠΌΠ°ΠΌΠΈ ΡΡΠ»ΡΡΠ°ΡΠ° ΠΊΠ°Π»ΡΡΠΈΡ. ΠΡΠΈ ΠΏΠΎΠΌΠΎΠ»Π΅ ΡΠ°ΠΊΠΆΠ΅ Π΄ΠΎΠΏΡΡΠΊΠ°Π΅ΡΡΡ Π²Π²ΠΎΠ΄ΠΈΡΡ Π΄ΡΡΠ³ΠΈΠ΅ Π΄ΠΎΠ±Π°Π²ΠΊΠΈ.
ΠΠΈΠ΄Ρ ΡΠ΅ΠΌΠ΅Π½ΡΠ°, ΠΊΠΎΡΠΎΡΡΠΉ ΠΏΡΠΎΠΈΠ·Π²ΠΎΠ΄ΡΡ ΠΈΠ· ΠΊΠ»ΠΈΠ½ΠΊΠ΅ΡΠ°:
- ΠΠΎΡΡΠ»Π°Π½Π΄ΡΠ΅ΠΌΠ΅Π½Ρ β ΠΏΠΎΡΠ»Π΅ ΠΎΠ±ΠΆΠΈΠ³Π° ΠΈΠ·Π²Π΅ΡΡΠ½ΡΠΊΠΎΠ², Π³Π»ΠΈΠ½ΠΈΡΡΡΡ
ΠΏΡΠΈΠΌΠ΅ΡΠ΅ΠΉ, ΠΌΠ΅ΡΠ³Π΅Π»Π΅ΠΉ ΠΏΠΎΠ»ΡΡΠ°ΡΡ ΡΠ°ΡΡΠ²ΠΎΡ ΡΠ΅ΠΌΠ΅Π½ΡΠ°.
ΠΠ»ΠΈΠ½ΠΊΠ΅Ρ ΠΎΠ±ΡΡΠ½ΠΎ ΡΠΌΠ΅ΡΠΈΠ²Π°ΡΡ Ρ Π΄ΠΎΠΌΠ΅Π½Π½ΡΠΌ ΡΠ»Π°ΠΊΠΎΠΌ, ΡΠ°ΠΊΡΡΠ΅ΡΠ½ΠΈΠΊΠΎΠΌ ΠΈ Π΄ΡΡΠ³ΠΈΠΌΠΈ Π΄ΠΎΠ±Π°Π²ΠΊΠ°ΠΌΠΈ. ΠΠΎΡΡΠ»Π°Π½Π΄ΡΠ΅ΠΌΠ΅Π½Ρ ΠΏΡΠΎΠΈΠ·Π²ΠΎΠ΄ΡΡ Π΄Π²ΡΠΌΡ ΡΠΏΠΎΡΠΎΠ±Π°ΠΌΠΈ: ΠΌΠΎΠΊΡΡΠΌ (ΠΊΠΎΠ³Π΄Π° ΠΊΠΎΠΌΠΏΠΎΠ½Π΅Π½ΡΡ ΡΠΌΠ°Π»ΡΠ²Π°ΡΡ ΠΈ ΡΠΌΠ΅ΡΠΈΠ²Π°ΡΡ Ρ Π²ΠΎΠ΄ΠΎΠΉ, ΠΏΠΎΡΠΎΠΌ ΠΎΠ±ΠΆΠΈΠ³Π°ΡΡ) ΠΈ ΡΡΡ ΠΈΠΌ (Π°Π½Π°Π»ΠΎΠ³ΠΈΡΠ½ΡΠ΅ Π΄Π΅ΠΉΡΡΠ²ΠΈΡ, Π½ΠΎ Π±Π΅Π· Π²ΠΎΠ΄Ρ). ΠΠ· ΠΏΠΎΡΡΠ»Π°Π½Π΄ΡΠ΅ΠΌΠ΅Π½ΡΠ° Π΄Π΅Π»Π°ΡΡ Π²ΡΡΠΎΠΊΠΎΠΏΡΠΎΡΠ½ΡΠ΅ Π±Π΅ΡΠΎΠ½Ρ, ΠΎΠ±Π»ΠΈΡΠΎΠ²ΠΎΡΠ½ΡΠ΅ ΠΏΠ»ΠΈΡΠΊΠΈ, ΠΌΠΎΠ½ΠΎΠ»ΠΈΡΠ½ΡΠ΅ ΠΊΠΎΠ½ΡΡΡΡΠΊΡΠΈΠΈ, Π΄Π°ΠΆΠ΅ ΠΈΡΠΊΡΡΡΡΠ²Π΅Π½Π½ΡΠΉ ΠΌΡΠ°ΠΌΠΎΡ ΠΈ Ρ.Π΄.
- Π ΠΎΠΌΠ°Π½ΡΠ΅ΠΌΠ΅Π½Ρ β ΡΠΎΠ·Π΄Π°Π΅ΡΡΡ ΠΏΠΎΡΡΠ΅Π΄ΡΡΠ²ΠΎΠΌ ΠΎΠ±ΠΆΠΈΠ³Π° ΠΈΠ·Π²Π΅ΡΡΠ½ΡΠΊΠΎΠ² (ΡΠΎΠ΄Π΅ΡΠΆΠ°Π½ΠΈΠ΅ Π³Π»ΠΈΠ½ΠΈΡΡΡΡ ΠΌΠΈΠ½ΠΈΠΌΡΠΌ 25%) ΠΏΡΠΈ ΡΠ΅ΠΌΠΏΠ΅ΡΠ°ΡΡΡΠ΅ ΡΠ²ΡΡΠ΅ +1000Π‘. ΠΡΠΈΠΌΠ΅Π½ΡΡΡ Π΄Π»Ρ ΠΏΡΠΎΠΈΠ·Π²ΠΎΠ΄ΡΡΠ²Π° Π±Π»ΠΎΠΊΠΎΠ², ΡΡΠ΅Π½ΠΎΠ²ΡΡ ΠΏΠ°Π½Π΅Π»Π΅ΠΉ, Π±Π΅ΡΠΎΠ½Π½ΡΡ ΡΠΌΠ΅ΡΠ΅ΠΉ Π½ΠΈΠ·ΠΊΠΈΡ ΠΌΠ°ΡΠΎΠΊ.
Π‘ΡΠ°Π½Π΄Π°ΡΡΠ½ΡΠΉ ΠΊΠ»ΠΈΠ½ΠΊΠ΅Ρ ΠΏΡΠ΅Π΄ΠΏΠΎΠ»Π°Π³Π°Π΅Ρ ΡΠ°ΠΊΠΎΠΉ ΡΠΎΡΡΠ°Π²:
- Π’ΡΠ΅Ρ ΠΊΠ°Π»ΡΡΠΈΠ΅Π²ΡΠΉ ΡΠΈΠ»ΠΈΠΊΠ°Ρ (Π°Π»ΠΈΡ) β Π°ΠΊΡΠΈΠ²Π½ΡΠΉ ΠΌΠΈΠ½Π΅ΡΠ°Π», Π΄ΠΎΡΡΠ°ΡΠΎΡΠ½ΠΎ ΠΈΠ½ΡΠ΅Π½ΡΠΈΠ²Π½ΠΎ Π½Π°Π±ΠΈΡΠ°Π΅Ρ ΠΏΡΠΎΡΠ½ΠΎΡΡΡ ΠΈ ΡΠ²Π΅ΡΠ΄ΠΎΡΡΡ Ρ Π²ΡΠ΄Π΅Π»Π΅Π½ΠΈΠ΅ΠΌ ΡΠ΅ΠΏΠ»Π°.
- ΠΠ²ΡΡ ΠΊΠ°Π»ΡΡΠΈΠ΅Π²ΡΠΉ ΡΠΈΠ»ΠΈΠΊΠ°Ρ (Π±Π΅Π»ΠΈΡ) β ΠΌΠ΅Π΄Π»Π΅Π½Π½ΠΎ ΡΠ²Π΅ΡΠ΄Π΅Π΅Ρ Π² ΠΏΠ΅ΡΠ²ΠΎΠ½Π°ΡΠ°Π»ΡΠ½ΠΎΠΉ ΡΡΠ°Π΄ΠΈΠΈ.
- Π’ΡΠ΅Ρ ΠΊΠ°Π»ΡΡΠΈΠ΅Π²ΡΠΉ Π°Π»ΡΠΌΠΈΠ½Π°Ρ β ΠΎΠ±Π»Π°Π΄Π°Π΅Ρ Π½ΠΈΠ·ΠΊΠΈΠΌ ΡΡΠΎΠ²Π½Π΅ΠΌ ΡΡΠΎΠΉΠΊΠΎΡΡΠΈ ΠΏΠΎΠ΄ Π²ΠΎΠ·Π΄Π΅ΠΉΡΡΠ²ΠΈΠ΅ΠΌ ΡΠ΅ΡΠ½ΠΎ-ΠΊΠΈΡΠ»ΡΡ ΡΠΎΠ΅Π΄ΠΈΠ½Π΅Π½ΠΈΠΉ.
- Π§Π΅ΡΡΡΠ΅Ρ
ΠΊΠ°Π»ΡΡΠΈΠ΅Π²ΡΠΉ Π°Π»ΡΠΌΠΎΡΠ΅ΡΡΠΈΡ β Π½Π°ΠΌΠ½ΠΎΠ³ΠΎ ΠΌΠ΅Π΄Π»Π΅Π½Π½Π΅Π΅ ΡΠ²Π΅ΡΠ΄Π΅Π΅Ρ Π² ΡΡΠ°Π²Π½Π΅Π½ΠΈΠΈ Ρ Π°Π»ΠΈΡΠΎΠΌ, Π½ΠΎ Π²ΡΠ΅ ΡΠ°Π²Π½ΠΎ Π±ΡΡΡΡΠ΅Π΅ Π±Π΅Π»ΠΈΡΠ°.
Π§Π΅ΡΡΡΠ΅ Π³Π»Π°Π²Π½ΡΠ΅ ΡΠ°Π·Ρ ΠΊΠ»ΠΈΠ½ΠΊΠ΅ΡΠ°
Π¦Π΅ΠΌΠ΅Π½ΡΠ½ΡΠΉ ΠΊΠ»ΠΈΠ½ΠΊΠ΅Ρ β ΡΡΠΎ ΠΎΡΠ½ΠΎΠ²Π½ΠΎΠΉ ΠΌΠ°ΡΠ΅ΡΠΈΠ°Π», ΠΊΠΎΡΠΎΡΡΠΉ ΠΈΡΠΏΠΎΠ»ΡΠ·ΡΠ΅ΡΡΡ Π΄Π»Ρ ΠΏΡΠΎΠΈΠ·Π²ΠΎΠ΄ΡΡΠ²Π° ΡΠ΅ΠΌΠ΅Π½ΡΠ° ΡΠ°Π·Π½ΡΡ ΠΌΠ°ΡΠΎΠΊ. Π’ΠΎ Π΅ΡΡΡ, ΠΏΡΠΎΠ²ΠΎΠ΄ΠΈΡΡΡ Π΄Π²Π° Π΄Π΅ΠΉΡΡΠ²ΠΈΡ: ΡΠ½Π°ΡΠ°Π»Π° ΠΏΡΠΎΠΈΠ·Π²ΠΎΠ΄ΠΈΡΡΡ ΠΊΠ»ΠΈΠ½ΠΊΠ΅Ρ Π² Π²ΠΈΠ΄Π΅ Π³ΡΠ°Π½ΡΠ», ΠΊΠΎΡΠΎΡΡΠΉ ΠΏΠΎΠ»ΡΡΠ°ΡΡ ΠΏΡΡΠ΅ΠΌ Π½Π°Π³ΡΠ΅Π²Π°Π½ΠΈΡ Π³Π»ΠΈΠ½Ρ ΠΈ ΠΈΠ·Π²Π΅ΡΡΠΈ (Ρ Π΄ΠΎΠ±Π°Π²ΠΊΠ°ΠΌΠΈ) ΠΌΠ΅ΡΠΎΠ΄ΠΎΠΌ ΠΏΠ»Π°Π²Π»Π΅Π½ΠΈΡ, ΠΏΠΎΡΠΎΠΌ ΠΊΠ»ΠΈΠ½ΠΊΠ΅Ρ ΡΠΌΠ°Π»ΡΠ²Π°Π΅ΡΡΡ, Π² Π½Π΅Π³ΠΎ Π΄ΠΎΠ±Π°Π²Π»ΡΠ΅ΡΡΡ Π³ΠΈΠΏΡ ΠΈ ΠΏΠΎΠ»ΡΡΠ°Π΅ΡΡΡ ΡΠ΅ΠΌΠ΅Π½Ρ.
Π Π°Π·Π½ΡΠ΅ ΡΠΏΠΎΡΠΎΠ±Ρ ΠΎΠ±ΡΠ°Π±ΠΎΡΠΊΠΈ ΠΎΠ±ΡΡΠ»Π°Π²Π»ΠΈΠ²Π°ΡΡ ΡΠΎ, ΡΡΠΎ ΠΊΠ»ΠΈΠ½ΠΊΠ΅Ρ ΠΌΠΎΠΆΠ΅Ρ Π±ΡΡΡ Ρ ΡΠ»Π΅ΠΌΠ΅Π½ΡΠ°ΡΠ½ΡΠΌ Ρ ΠΈΠΌΠΈΡΠ΅ΡΠΊΠΈΠΌ ΠΈΠ»ΠΈ ΠΌΠΈΠ½Π΅ΡΠ°Π»ΠΎΠ³ΠΈΡΠ΅ΡΠΊΠΈΠΌ ΡΠΎΡΡΠ°Π²ΠΎΠΌ. ΠΡ ΡΠΎΠ³ΠΎ, ΠΊΠ°ΠΊΠΈΠ΅ ΠΎΠ±ΡΠ΅ΠΌΡ ΠΊΠ»ΠΈΠ½ΠΊΠ΅ΡΠ½ΡΡ ΠΌΠ°ΡΠ΅ΡΠΈΠ°Π»ΠΎΠ² ΠΈΡΠΏΠΎΠ»ΡΠ·ΠΎΠ²Π°Π»ΠΈΡΡ ΠΏΡΠΈ ΠΎΠ±ΠΆΠΈΠ³Π΅, Π·Π°Π²ΠΈΡΡΡ ΡΠ²ΠΎΠΉΡΡΠ²Π° ΡΠ΅ΠΌΠ΅Π½ΡΠ°: ΠΎΠ½ ΠΌΠΎΠΆΠ΅Ρ Π±ΡΡΡ Π±ΡΡΡΡΠΎΡΠΎΡ Π½ΡΡΠΈΠΌ, ΡΠΎΠ·Π΄Π°Π½Π½ΡΠΌ ΡΠΏΠ΅ΡΠΈΠ°Π»ΡΠ½ΠΎ Π΄Π»Ρ ΠΈΡΠΏΠΎΠ»ΡΠ·ΠΎΠ²Π°Π½ΠΈΡ ΠΏΡΠΈ ΠΌΠΈΠ½ΡΡΠ΅, ΠΎΠ±Π»Π°Π΄Π°ΡΡ Π΄ΡΡΠ³ΠΈΠΌΠΈ ΡΠ²ΠΎΠΉΡΡΠ²Π°ΠΌΠΈ.
Π‘ΠΎΡΡΠ°Π² ΠΏΡΠ΅Π΄ΡΡΠ°Π²Π»ΡΠ΅Ρ ΡΠΎΠ±ΠΎΠΉ ΡΠΈΡΡΠ΅ΠΌΡ Π½Π΅ΡΠΊΠΎΠ»ΡΠΊΠΈΡ
ΠΊΠ»ΠΈΠ½ΠΊΠ΅ΡΠ½ΡΡ
ΠΌΠΈΠ½Π΅ΡΠ°Π»ΠΎΠ², ΠΊΠΎΡΠΎΡΡΠ΅ ΠΏΠΎΡΠ²Π»ΡΡΡΡΡ Π² ΠΏΡΠΎΡΠ΅ΡΡΠ΅ ΠΏΠ»Π°Π²ΠΊΠΈ ΠΈ ΠΎΠ±ΠΆΠΈΠ³Π°. ΠΠΎ Π·Π°ΠΌΠ΅ΡΠΈΡΡ ΡΠ°ΡΡΠΈ ΠΎΡΠ΄Π΅Π»ΡΠ½ΡΡ
ΡΠΎΡΡΠ°Π²Π»ΡΡΡΠΈΡ
ΠΊΠ»ΠΈΠ½ΠΊΠ΅ΡΠ° Π½Π΅Π²ΠΎΠ·ΠΌΠΎΠΆΠ½ΠΎ, ΡΠ°ΠΊ ΠΊΠ°ΠΊ ΡΠ΅ΡΡ ΠΈΠ΄Π΅Ρ ΠΎΠ± Π°ΠΌΠΎΡΡΠ½ΡΡ
ΠΈ ΡΠΎΠ½ΠΊΠΎΠ·Π΅ΡΠ½ΠΈΡΡΡΡ
ΠΊΡΠΈΡΡΠ°Π»Π»ΠΈΡΠ΅ΡΠΊΠΈΡ
ΡΠ°Π·Π°Ρ
.
ΠΡΠ΅ΠΆΠ΄Π΅, ΡΠ΅ΠΌ ΠΏΡΠΎΠΈΠ·Π²ΠΎΠ΄ΠΈΡΡ ΡΠ΅ΠΌΠ΅Π½Ρ, ΠΊΠ»ΠΈΠ½ΠΊΠ΅Ρ ΠΏΠΎΠ΄Π±ΠΈΡΠ°ΡΡ ΠΏΠΎ ΡΠΎΡΡΠ°Π²Ρ. ΠΠ±ΡΡΠ½ΠΎ ΡΠ΅ΡΡ ΠΈΠ΄Π΅Ρ ΠΎ ΡΠ΅ΡΡΡΠ΅Ρ ΠΎΡΠ½ΠΎΠ²Π½ΡΡ ΡΠ°Π·Π°Ρ , ΡΠΊΠ°Π·Π°Π½Π½ΡΡ Π½ΠΈΠΆΠ΅. ΠΡΠΎΠΌΠ΅ Π½ΠΈΡ , Π² Π½Π΅Π±ΠΎΠ»ΡΡΠΈΡ ΠΎΠ±ΡΠ΅ΠΌΠ°Ρ Π² Π²Π΅ΡΠ΅ΡΡΠ²Π΅ ΠΌΠΎΠ³ΡΡ ΠΏΡΠΈΡΡΡΡΡΠ²ΠΎΠ²Π°ΡΡ Π΄ΡΡΠ³ΠΈΠ΅ ΡΠ°Π·Ρ (ΠΎΠΊΡΠΈΠ΄ ΠΊΠ°Π»ΡΡΠΈΡ, ΡΠ΅Π»ΠΎΡΠ½ΡΠ΅ ΡΡΠ»ΡΡΠ°ΡΡ).
ΠΠ»ΠΈΡ
Π‘Π°ΠΌΠ°Ρ Π²Π°ΠΆΠ½Π°Ρ ΡΠΎΡΡΠ°Π²Π»ΡΡΡΠ°Ρ Π»ΡΠ±ΠΎΠ³ΠΎ ΠΊΠ»ΠΈΠ½ΠΊΠ΅ΡΠ° Π΄Π»Ρ ΡΠ΅ΠΌΠ΅Π½ΡΠ°. Π ΡΠΎΡΡΠ°Π²Π΅ Π΄ΠΎΠ»ΠΆΠ½ΠΎ Π±ΡΡΡ ΠΌΠΈΠ½ΠΈΠΌΡΠΌ 50-70% ΡΡΠ΅Ρ ΠΊΠ°Π»ΡΡΠΈΠ΅Π²ΠΎΠ³ΠΎ ΡΠΈΠ»ΠΈΠΊΠ°ΡΠ° (ΠΎΠ±ΠΎΠ·Π½Π°ΡΠ°Π΅ΡΡΡ 3Π‘Π°O*SiΠ2Β ΠΈΠ»ΠΈ ΡΠΎΠΊΡΠ°ΡΠ΅Π½Π½ΠΎ C3S). Π‘ΡΡΡΠΊΡΡΡΠ° ΠΈ ΡΠΎΡΡΠ°Π² Π΄Π°Π½Π½ΠΎΠΉ ΡΠ°Π·Ρ ΠΌΠΎΠ΄ΠΈΡΠΈΡΠΈΡΡΡΡΡΡ Π±Π»Π°Π³ΠΎΠ΄Π°ΡΡ ΡΠ°Π·ΠΌΠ΅ΡΠ΅Π½ΠΈΡ Π² ΡΠ΅ΡΠ΅ΡΠΊΠ΅ ΠΈΠ½ΠΎΡΠΎΠ΄Π½ΡΡ ΠΈΠΎΠ½ΠΎΠ² (Π² ΠΎΡΠΎΠ±Π΅Π½Π½ΠΎΡΡΠΈ Πl3+, Mg2+, FΠ΅3+). ΠΠ»ΠΈΡ ΡΡΡΠ΅ΠΌΠΈΡΠ΅Π»ΡΠ½ΠΎ ΡΠ΅Π°Π³ΠΈΡΡΠ΅Ρ Ρ Π²ΠΎΠ΄ΠΎΠΉ, Π² Π½ΠΎΡΠΌΠ°Π»ΡΠ½ΡΡ ΡΠ΅ΠΌΠ΅Π½ΡΠ°Ρ ΠΈΠΌΠ΅Π΅Ρ ΡΠ°ΠΌΠΎΠ΅ Π±ΠΎΠ»ΡΡΠΎΠ΅ Π·Π½Π°ΡΠ΅Π½ΠΈΠ΅ Π΄Π»Ρ ΠΎΠ±Π΅ΡΠΏΠ΅ΡΠ΅Π½ΠΈΡ ΠΏΡΠΎΡΠ½ΠΎΡΡΠΈ. ΠΡΠΎΠ±Π΅Π½Π½ΠΎ Π²Π°ΠΆΠ΅Π½ Π°Π»ΠΈΡ Π΄Π»Ρ ΠΎΠ±Π΅ΡΠΏΠ΅ΡΠ΅Π½ΠΈΡ Π½Π°Π±ΠΎΡΠ° ΠΏΡΠΎΡΠ½ΠΎΡΡΠΈ ΡΠ΅ΠΌΠ΅Π½ΡΠ° Π² ΡΠ΅ΡΠ΅Π½ΠΈΠ΅ 28 ΡΡΡΠΎΠΊ.
ΠΠ΅Π»ΠΈΡ
ΠΠΎΠ³Π΄Π° ΠΏΡΠΎΠΈΠ·Π²ΠΎΠ΄ΠΈΡΡΡ ΠΊΠ»ΠΈΠ½ΠΊΠ΅Ρ ΡΠ΅ΠΌΠ΅Π½ΡΠ½ΡΠΉ, ΡΠΎΠ΄Π΅ΡΠΆΠ°Π½ΠΈΠ΅ Π±Π΅Π»ΠΈΡΠ° Π΄ΠΎΠ»ΠΆΠ½ΠΎ Π±ΡΡΡ ΡΠ°Π²Π½ΠΎ 15-30%. ΠΠ²ΡΡ
ΠΊΠ°Π»ΡΡΠΈΠ΅Π²ΡΠΉ ΡΠΈΠ»ΠΈΠΊΠ°Ρ ΠΎΠ±ΠΎΠ·Π½Π°ΡΠ°Π΅ΡΡΡ ΠΊΠ°ΠΊ 2Π‘Π°O*SiΠ2 (Π»ΠΈΠ±ΠΎ ΡΠΎΠΊΡΠ°ΡΠ΅Π½Π½ΠΎ C2S), ΠΌΠΎΠ΄ΠΈΡΠΈΠΊΠ°ΡΠΈΡ ΠΏΡΠΎΠΈΡΡ
ΠΎΠ΄ΠΈΡ Π·Π° ΡΡΠ΅Ρ Π΄ΠΎΠ±Π°Π²Π»Π΅Π½ΠΈΡ Π² ΡΡΡΡΠΊΡΡΡΡ ΠΈΠ½ΠΎΡΠΎΠ΄Π½ΡΡ
ΠΈΠΎΠ½ΠΎΠ², ΡΠ°ΡΠ΅ Π²ΡΠ΅Π³ΠΎ Π±ΠΎΠ»ΡΡΠ΅ΠΉ ΡΠ°ΡΡΡΡ Π»ΠΈΠ±ΠΎ ΠΏΠΎΠ»Π½ΠΎΡΡΡΡ ΠΏΡΠΈΡΡΡΡΡΠ²ΡΠ΅Ρ Π² ΡΠΎΡΠΌΠ°ΡΠ΅ Ξ²-ΠΌΠΎΠ΄ΠΈΡΠΈΠΊΠ°ΡΠΈΠΈ.
ΠΠ΅Π»ΠΈΡ Ρ Π²ΠΎΠ΄ΠΎΠΉ ΡΠ΅Π°Π³ΠΈΡΡΠ΅Ρ Π΄ΠΎΡΡΠ°ΡΠΎΡΠ½ΠΎ ΠΌΠ΅Π΄Π»Π΅Π½Π½ΠΎ, Π½Π΅ ΠΎΠΊΠ°Π·ΡΠ²Π°Π΅Ρ Π²ΠΎΠ·Π΄Π΅ΠΉΡΡΠ²ΠΈΡ Π½Π° ΡΡΠΎΠ²Π΅Π½Ρ ΠΏΡΠΎΡΠ½ΠΎΡΡΠΈ ΡΠ΅ΠΌΠ΅Π½ΡΠ° Π½Π° ΠΏΡΠΎΡΡΠΆΠ΅Π½ΠΈΠΈ 28 ΡΡΡΠΎΠΊ. ΠΠΎ ΠΎΠ½ Π²Π»ΠΈΡΠ΅Ρ Π½Π° ΠΏΡΠΎΡΠ½ΠΎΡΡΡ Π² Π·Π½Π°ΡΠΈΡΠ΅Π»ΡΠ½ΠΎ ΠΏΠΎΠ·Π΄Π½ΠΈΠ΅ ΡΡΠΎΠΊΠΈ, ΡΡΠΎ ΡΠ°ΠΊΠΆΠ΅ Π½Π΅ΠΌΠ°Π»ΠΎΠ²Π°ΠΆΠ½ΠΎ. Π’Π°ΠΊ, ΡΠ΅ΡΠ΅Π· Π³ΠΎΠ΄ Π² ΠΈΠ΄Π΅Π½ΡΠΈΡΠ½ΡΡ ΡΡΠ»ΠΎΠ²ΠΈΡΡ ΠΏΠΎΠΊΠ°Π·Π°ΡΠ΅Π»Ρ ΠΏΡΠΎΡΠ½ΠΎΡΡΠΈ ΡΠΈΡΡΠΎΠ³ΠΎ Π±Π΅Π»ΠΈΡΠ° ΠΈ ΡΠΈΡΡΠΎΠ³ΠΎ Π°Π»ΠΈΡΠ° ΠΏΡΠΈΠΌΠ΅ΡΠ½ΠΎ ΠΎΠ΄ΠΈΠ½Π°ΠΊΠΎΠ².
ΠΠ»ΡΠΌΠΈΠ½Π°ΡΠ½Π°Ρ ΡΠ°Π·Π°
ΠΠ»ΡΠΌΠΈΠ½Π°ΡΠ½Π°Ρ ΡΠ°Π·Π° Π² ΠΊΠ»ΠΈΠ½ΠΊΠ΅ΡΠ΅ ΡΠ΅ΠΌΠ΅Π½ΡΠ½ΠΎΠΌ ΡΠΎΡΡΠ°Π²Π»ΡΠ΅Ρ 5-10%. Π’ΡΠ΅Ρ ΠΊΠ°Π»ΡΡΠΈΠ΅Π²ΡΠΉ Π°Π»ΡΠΌΠΈΠ½Π°Ρ ΠΎΠ±ΠΎΠ·Π½Π°ΡΠ°Π΅ΡΡΡ ΠΊΠ°ΠΊ 3Π‘Π°O*Al2O3, ΠΌΠ΅Π½ΡΠ΅ΡΡΡ ΠΏΠΎ ΡΠΎΡΡΠ°Π²Ρ ΠΈ ΡΡΡΡΠΊΡΡΡΠ΅ Π² Π½Π΅ΠΊΠΎΡΠΎΡΡΡ ΡΠ»ΡΡΠ°ΡΡ Π±Π»Π°Π³ΠΎΠ΄Π°ΡΡ ΠΈΠ½ΠΎΡΠΎΠ΄Π½ΡΠΌ ΠΈΠΎΠ½Π°ΠΌ (Π² ΠΎΡΠΎΠ±Π΅Π½Π½ΠΎΡΡΠΈ NΠ°+, Si4+, Π+, Fe3+). Π€Π°Π·Π° ΠΌΠ³Π½ΠΎΠ²Π΅Π½Π½ΠΎ ΡΠ΅Π°Π³ΠΈΡΡΠ΅Ρ Ρ Π²ΠΎΠ΄ΠΎΠΉ, ΠΈΠ·-Π·Π° ΡΠ΅Π³ΠΎ ΡΡΠ°Π½ΠΎΠ²ΠΈΡΡΡ ΠΏΡΠΈΡΠΈΠ½ΠΎΠΉ Π±ΡΡΡΡΠΎΠ³ΠΎ Π²ΡΡΡΡ Π°Π½ΠΈΡ, Π΅ΡΠ»ΠΈ Π² ΡΠΎΡΡΠ°Π² Π½Π΅ Π±ΡΠ» Π²Π²Π΅Π΄Π΅Π½ ΠΊΠΎΠ½ΡΡΠΎΠ»ΠΈΡΡΡΡΠΈΠΉ ΡΠΊΠΎΡΠΎΡΡΡ ΡΡ Π²Π°ΡΡΠ²Π°Π½ΠΈΡ ΡΠ΅Π°Π³Π΅Π½Ρ, Π² ΠΊΠ°ΡΠ΅ΡΡΠ²Π΅ ΠΊΠΎΡΠΎΡΠΎΠ³ΠΎ Π²ΡΡΡΡΠΏΠ°Π΅Ρ ΠΎΠ±ΡΡΠ½ΠΎ Π³ΠΈΠΏΡ.
ΠΠ»ΡΠΌΠΎΡΠ΅ΡΡΠΈΡΠ½Π°Ρ ΡΠ°Π·Π°
Π€Π΅ΡΡΠΈΡΠ½Π°Ρ ΡΠ°Π·Π° ΡΠΎΡΡΠ°Π²Π»ΡΠ΅Ρ ΠΎΠΊΠΎΠ»ΠΎ 5-15% ΡΠ΅ΠΌΠ΅Π½ΡΠ½ΠΎΠ³ΠΎ ΠΊΠ»ΠΈΠ½ΠΊΠ΅ΡΠ°, ΠΎΠ±ΠΎΠ·Π½Π°ΡΠ°Π΅ΡΡΡ ΠΊΠ°ΠΊ 4CaO*Al2O3*Fe2O3 (ΡΠΎΠΊΡΠ°ΡΠ΅Π½Π½ΠΎ CaAlFe). Π§Π΅ΡΡΡΠ΅Ρ
ΠΊΠ°Π»ΡΡΠΈΠ΅Π²ΡΠΉ Π°Π»ΡΠΌΠΎΡΠ΅ΡΡΠΈΡ ΡΡΡΠ΅ΡΡΠ²Π΅Π½Π½ΠΎ ΠΌΠ΅Π½ΡΠ΅Ρ ΡΠΎΡΡΠ°Π² ΠΏΡΠΈ ΠΈΠ·ΠΌΠ΅Π½Π΅Π½ΠΈΡΡ
ΠΏΡΠΎΠΏΠΎΡΡΠΈΠΈ Al/Fe ΠΈ Π½Π°Ρ
ΠΎΠΆΠ΄Π΅Π½ΠΈΠΈ Π² ΡΡΡΡΠΊΡΡΡΠ΅ ΠΈΠ½ΠΎΡΠΎΠ΄Π½ΡΡ
ΠΈΠΎΠ½ΠΎΠ².
Π‘ΠΊΠΎΡΠΎΡΡΡ ΡΠ΅Π°ΠΊΡΠΈΠΈ Π±Π°Π·Ρ Ρ Π²ΠΎΠ΄ΠΎΠΉ ΠΌΠΎΠΆΠ΅Ρ Π±ΡΡΡ ΡΠ°Π·Π½ΠΎΠΉ ΠΈΠ·-Π·Π° ΠΎΡΠ»ΠΈΡΠΈΠΉ Π² ΡΠΎΡΡΠ°Π²Π΅. ΠΠ°ΠΊ ΠΏΡΠ°Π²ΠΈΠ»ΠΎ, ΠΏΠΎΠΊΠ°Π·Π°ΡΠ΅Π»Ρ Π΄ΠΎΡΡΠ°ΡΠΎΡΠ½ΠΎ Π²ΡΡΠΎΠΊΠΈΠΉ Π½Π° ΠΏΠ΅ΡΠ²ΡΡ ΡΡΠ°ΠΏΠ°Ρ , Π² Π±ΠΎΠ»Π΅Π΅ ΠΏΠΎΠ·Π΄Π½ΠΈΠ΅ ΡΡΠΎΠΊΠΈ ΡΡΠ΅Π΄Π½ΠΈΠΉ ΠΌΠ΅ΠΆΠ΄Ρ ΠΏΠΎΠΊΠ°Π·Π°ΡΠ΅Π»ΡΠΌΠΈ Π°Π»ΠΈΡΠ° ΠΈ Π±Π΅Π»ΠΈΡΠ°.
ΠΠ»ΠΈΡΠ½ΠΈΠ΅ ΠΈ ΠΊΠΎΠ½ΡΡΠΎΠ»Ρ Ρ ΠΈΠΌΠΈΡΠ΅ΡΠΊΠΎΠ³ΠΎ ΡΠΎΡΡΠ°Π²Π° ΠΊΠ»ΠΈΠ½ΠΊΠ΅ΡΠ° Π΄Π»Ρ ΠΏΡΠΎΠΈΠ·Π²ΠΎΠ΄ΡΡΠ²Π° ΡΠ΅ΠΌΠ΅Π½ΡΠ°
Π‘Π°Π½ΡΡΠΈ ΠΡΡ Ρ 1, 2 , Π‘Π°ΠΌΠ°ΠΈΠ»Π° ΠΠ°Π΄Π°Π½ 3 , ΠΠ±ΡΠ±Π°ΠΊΠ°Ρ Π£ΠΌΠ°Ρ ΠΡΡ Π°ΠΌΠΌΠ°Π΄ 4
1 Π€Π°ΠΊΡΠ»ΡΡΠ΅Ρ Ρ ΠΈΠΌΠΈΡΠ΅ΡΠΊΠΎΠ³ΠΎ ΠΌΠ°ΡΠΈΠ½ΠΎΡΡΡΠΎΠ΅Π½ΠΈΡ, Umaru Ali Shinkafi Polytechnics Sokoto, ΠΠΈΠ³Π΅ΡΠΈΡ
2 Π‘ΡΡΠ΄Π΅Π½Ρ ΠΌΠ°Π³ΠΈΡΡΡΠ°ΡΡΡΡ, ΡΠ°ΠΊΡΠ»ΡΡΠ΅Ρ Ρ ΠΈΠΌΠΈΡΠ΅ΡΠΊΠΎΠ³ΠΎ ΠΌΠ°ΡΠΈΠ½ΠΎΡΡΡΠΎΠ΅Π½ΠΈΡ, Π£Π½ΠΈΠ²Π΅ΡΡΠΈΡΠ΅Ρ ΠΡ ΠΌΠ°Π΄Ρ ΠΠ΅Π»Π»ΠΎ ΠΠ°ΡΠΈΠ°, ΠΠΈΠ³Π΅ΡΠΈΡ
3 ΠΠ΅ΠΏΠ°ΡΡΠ°ΠΌΠ΅Π½Ρ ΠΌΠΎΠ½ΠΈΡΠΎΡΠΈΠ½Π³Π° ΠΈ ΠΎΡΠ΅Π½ΠΊΠΈ, Π’ΡΠ°ΡΡΠΎΠ²ΡΠΉ ΡΠΎΠ½Π΄ Π²ΡΡΡΠ΅Π³ΠΎ ΠΎΠ±ΡΠ°Π·ΠΎΠ²Π°Π½ΠΈΡ, ΠΠΈΠ³Π΅ΡΠΈΡ
4 Π€Π°ΠΊΡΠ»ΡΡΠ΅Ρ Π΅ΡΡΠ΅ΡΡΠ²Π΅Π½Π½ΡΡ ΠΈ ΠΏΡΠΈΠΊΠ»Π°Π΄Π½ΡΡ Π½Π°ΡΠΊ, Π£Π½ΠΈΠ²Π΅ΡΡΠΈΡΠ΅Ρ Π£ΡΠΌΠ°Π½Π° ΠΠ°Π½ΡΠΎΠ΄ΠΈΠΉΠΎ, Π‘ΠΎΠΊΠΎΡΠΎ, ΠΠΈΠ³Π΅ΡΠΈΡ
ΠΠ΄ΡΠ΅Ρ Π΄Π»Ρ ΠΊΠΎΡΡΠ΅ΡΠΏΠΎΠ½Π΄Π΅Π½ΡΠΈΠΈ: Π‘Π°Π½ΡΡΠΈ ΠΡΡ
Ρ, ΠΊΠ°ΡΠ΅Π΄ΡΠ° Ρ
ΠΈΠΌΠΈΡΠ΅ΡΠΊΠΎΠ³ΠΎ ΠΌΠ°ΡΠΈΠ½ΠΎΡΡΡΠΎΠ΅Π½ΠΈΡ, Umaru Ali Shinkafi Polytechnics Sokoto, ΠΠΈΠ³Π΅ΡΠΈΡ.
ΠΠ»Π΅ΠΊΡΡΠΎΠ½Π½Π°Ρ ΠΏΠΎΡΡΠ°: |
Copyright Β© 2020 ΠΠ²ΡΠΎΡ(Ρ). ΠΠΏΡΠ±Π»ΠΈΠΊΠΎΠ²Π°Π½ΠΎ Scientific & Academic Publishing.
ΠΡΠ° ΡΠ°Π±ΠΎΡΠ° Π½Π°Ρ
ΠΎΠ΄ΠΈΡΡΡ ΠΏΠΎΠ΄ Π»ΠΈΡΠ΅Π½Π·ΠΈΠ΅ΠΉ Creative Commons Attribution International License (CC BY).
http://creativecommons.org/licenses/by/4.0/
ΠΠ½Π½ΠΎΡΠ°ΡΠΈΡ
ΠΡΠΎ ΠΈΡΡΠ»Π΅Π΄ΠΎΠ²Π°Π½ΠΈΠ΅ Π±ΡΠ»ΠΎ ΡΠΎΡΡΠ΅Π΄ΠΎΡΠΎΡΠ΅Π½ΠΎ Π½Π° ΠΈΠ·ΡΡΠ΅Π½ΠΈΠΈ ΡΡΡΠ΅ΠΊΡΠΎΠ² ΠΈ ΡΠΏΠΎΡΠΎΠ±ΠΎΠ² ΠΊΠΎΠ½ΡΡΠΎΠ»Ρ Ρ
ΠΈΠΌΠΈΡΠ΅ΡΠΊΠΎΠ³ΠΎ ΡΠΎΡΡΠ°Π²Π° ΠΊΠ»ΠΈΠ½ΠΊΠ΅ΡΠ° Π΄Π»Ρ ΡΠ»ΡΡΡΠ΅Π½ΠΈΡ ΠΏΡΠΎΠΈΠ·Π²ΠΎΠ΄ΡΡΠ²Π° ΡΠ΅ΠΌΠ΅Π½ΡΠ°. Π¦Π΅ΠΌΠ΅Π½Ρ β ΡΡΠΎ Π²Π΅ΡΠ΅ΡΡΠ²ΠΎ, ΠΏΠΎΠ»ΡΡΠ°Π΅ΠΌΠΎΠ΅ ΠΏΡΡΠ΅ΠΌ ΠΈΠ·ΠΌΠ΅Π»ΡΡΠ΅Π½ΠΈΡ ΡΠΌΠ΅ΡΠΈ Π³Π»ΠΈΠ½Ρ ΠΈ ΠΈΠ·Π²Π΅ΡΡΠ½ΡΠΊΠ° ΠΈ Π½Π°Π³ΡΠ΅Π²Π°Π½ΠΈΡ Π΄ΠΎ ΡΠ΅ΠΌΠΏΠ΅ΡΠ°ΡΡΡΡ 1450Β°C, ΠΏΡΠΈ ΠΊΠΎΡΠΎΡΠΎΠΌ Π²Π½ΡΡΡΠΈ ΠΏΠ΅ΡΠΈ ΠΏΡΠΎΠΈΡΡ
ΠΎΠ΄ΠΈΡ Ρ
ΠΈΠΌΠΈΡΠ΅ΡΠΊΠΎΠ΅ ΠΏΡΠ΅Π²ΡΠ°ΡΠ΅Π½ΠΈΠ΅ Ρ ΠΎΠ±ΡΠ°Π·ΠΎΠ²Π°Π½ΠΈΠ΅ΠΌ Π½ΠΎΠ²ΠΎΠ³ΠΎ ΡΠΎΠ΅Π΄ΠΈΠ½Π΅Π½ΠΈΡ, Π½Π°Π·ΡΠ²Π°Π΅ΠΌΠΎΠ³ΠΎ ΠΊΠ»ΠΈΠ½ΠΊΠ΅ΡΠΎΠΌ. ΠΠ΅ΡΠΎΠ΄ΠΎΠ»ΠΎΠ³ΠΈΠ΅ΠΉ Π΄Π°Π½Π½ΠΎΠΉ ΠΈΡΡΠ»Π΅Π΄ΠΎΠ²Π°ΡΠ΅Π»ΡΡΠΊΠΎΠΉ ΡΠ°Π±ΠΎΡΡ ΡΠ²Π»ΡΡΡΡΡ; 10 ΠΎΠ±ΡΠ°Π·ΡΠΎΠ² ΠΊΠ»ΠΈΠ½ΠΊΠ΅ΡΠ° Π±ΡΠ»ΠΈ ΡΠΎΠ±ΡΠ°Π½Ρ Π½Π° ΠΏΠ»Π°ΡΡΠΈΠ½ΡΠ°ΡΠΎΠΌ ΠΊΠΎΠ½Π²Π΅ΠΉΠ΅ΡΠ΅, ΠΏΠΎ 10 Π³ ΠΊΠ°ΠΆΠ΄ΠΎΠ³ΠΎ ΠΎΠ±ΡΠ°Π·ΡΠ° Π±ΡΠ»ΠΈ Π²Π·Π²Π΅ΡΠ΅Π½Ρ, ΠΈΠ·ΠΌΠ΅Π»ΡΡΠ΅Π½Ρ ΠΈ Π³ΡΠ°Π½ΡΠ»ΠΈΡΠΎΠ²Π°Π½Ρ Ρ ΠΏΠΎΠΌΠΎΡΡΡ ΠΏΠΈΡΠΈΠ΄ΠΈΠ½Π° ΠΈ ΡΠ²ΡΠ·ΡΡΡΠ΅Π³ΠΎ. ΠΠ°ΡΠ΅ΠΌ ΠΎΠ±ΡΠ°Π·Π΅Ρ ΠΏΠΎΠ΄Π²Π΅ΡΠ³Π°Π»ΠΈ ΡΠ΅Π½ΡΠ³Π΅Π½ΠΎΠ²ΡΠΊΠΎΠΌΡ Π°Π½Π°Π»ΠΈΠ·Π°ΡΠΎΡΡ Π΄Π»Ρ ΠΎΠΏΡΠ΅Π΄Π΅Π»Π΅Π½ΠΈΡ ΠΌΠΈΠ½Π΅ΡΠ°Π»ΠΎΠ³ΠΈΡΠ΅ΡΠΊΠΎΠ³ΠΎ ΡΠΎΡΡΠ°Π²Π° ΠΊΠ»ΠΈΠ½ΠΊΠ΅ΡΠ°, ΠΎΠ±Π½Π°ΡΡΠΆΠ΅Π½Π½ΡΡ
ΠΌΠΈΠ½Π΅ΡΠ°Π»ΠΎΠ² ΠΈ ΠΎΠΊΡΠΈΠ΄ΠΎΠ²; Π‘ 3 S, C
ΠΠ»Ρ ΠΎΠ±Π΅ΡΠΏΠ΅ΡΠ΅Π½ΠΈΡ ΠΏΠΎΡΡΠΎΡΠ½Π½ΡΡ
ΠΈ ΠΎΠ΄Π½ΠΎΡΠΎΠ΄Π½ΡΡ
Ρ
ΠΈΠΌΠΈΡΠ΅ΡΠΊΠΈΡ
ΡΠΎΡΡΠ°Π²ΠΎΠ² ΠΈ ΠΊΠ°ΡΠ΅ΡΡΠ²Π° ΡΠ΅ΠΌΠ΅Π½ΡΠ½ΠΎΠ³ΠΎ ΠΊΠ»ΠΈΠ½ΠΊΠ΅ΡΠ° Ρ ΠΌΠΈΠ½ΠΈΠΌΠ°Π»ΡΠ½ΠΎ Π²ΠΎΠ·ΠΌΠΎΠΆΠ½ΡΠΌ ΠΏΠΎΡΡΠ΅Π±Π»Π΅Π½ΠΈΠ΅ΠΌ ΡΠ½Π΅ΡΠ³ΠΈΠΈ Π½Π΅ΠΎΠ±Ρ
ΠΎΠ΄ΠΈΠΌΠΎ ΡΠ΄Π΅Π»ΡΡΡ Π²Π½ΠΈΠΌΠ°Π½ΠΈΠ΅ ΠΏΠΈΡΠ°Π½ΠΈΡ ΠΏΠ΅ΡΠΈ ΠΈ Ρ
ΠΈΠΌΠΈΡΠ΅ΡΠΊΠΎΠΌΡ ΡΠΎΡΡΠ°Π²Ρ ΠΊΠ»ΠΈΠ½ΠΊΠ΅ΡΠ°.
ΠΠ»ΡΡΠ΅Π²ΡΠ΅ ΡΠ»ΠΎΠ²Π°: Π₯ΠΈΠΌΠΈΠΊΠ°Ρ, Π¦Π΅ΠΌΠ΅Π½Ρ, ΠΠ»ΠΈΠ½ΠΊΠ΅Ρ, Π‘ΠΎΡΡΠ°Π², ΠΠ΅ΡΡ, Π Π°ΡΡ ΠΎΠ΄
Π‘ΡΡΠ»Π°ΠΉΡΠ΅ΡΡ Π½Π° ΡΡΡ ΡΡΠ°ΡΡΡ: Π‘Π°Π½ΡΡΠΈ ΠΡΡ Ρ, Π‘Π°ΠΌΠ°ΠΉΠ»Π° ΠΠ°Π΄Π°Π½, ΠΠ±ΡΠ±Π°ΠΊΠ°Ρ Π£ΠΌΠ°Ρ ΠΡΡ Π°ΠΌΠΌΠ°Π΄, ΠΠ»ΠΈΡΠ½ΠΈΠ΅ ΠΈ ΠΊΠΎΠ½ΡΡΠΎΠ»Ρ Ρ ΠΈΠΌΠΈΡΠ΅ΡΠΊΠΎΠ³ΠΎ ΡΠΎΡΡΠ°Π²Π° ΠΊΠ»ΠΈΠ½ΠΊΠ΅ΡΠ° Π΄Π»Ρ ΠΏΡΠΎΠΈΠ·Π²ΠΎΠ΄ΡΡΠ²Π° ΡΠ΅ΠΌΠ΅Π½ΡΠ°, International Journal of Control Science and Engineering , Vol. 10 β 1, 2020. Π‘. 16-21. doi: 10.5923/j.control.20201001.03.
ΠΠΏΠΈΡΠ°Π½ΠΈΠ΅ ΡΡΠ°ΡΡΠΈ
- 1. ΠΠ²Π΅Π΄Π΅Π½ΠΈΠ΅
- Β Β Β Β 1.1. Π₯ΠΈΠΌΠΈΡ ΡΡΡΡΡ
- Β Β Β Β 1.2. ΠΡΠΎΡΠ΅ΡΡ ΡΠΆΠΈΠ³Π°Π½ΠΈΡ
- 2. ΠΠ°ΡΠ΅ΡΠΈΠ°Π»Ρ ΠΈ ΠΌΠ΅ΡΠΎΠ΄Ρ
- Β Β Β Β 2.1. ΠΠ°ΡΠ΅ΡΠΈΠ°Π»Ρ
- Β Β Β Β 2.2. ΠΠΊΡΠΏΠ΅ΡΠΈΠΌΠ΅Π½ΡΠ°Π»ΡΠ½Π°Ρ ΠΏΡΠΎΡΠ΅Π΄ΡΡΠ°
- 3.
Π Π΅Π·ΡΠ»ΡΡΠ°ΡΡ ΠΈ ΠΎΠ±ΡΡΠΆΠ΄Π΅Π½ΠΈΠ΅
- Β Β Β Β 3.1. Π’Π°Π±Π»ΠΈΡΠ° 1: Π Π΅Π½ΡΠ³Π΅Π½ΠΎΡΠ°Π·ΠΎΠ²ΡΠΉ Π°Π½Π°Π»ΠΈΠ· ΠΎΠ±ΡΠ°Π·ΡΠΎΠ² ΠΊΠ»ΠΈΠ½ΠΊΠ΅ΡΠ°
- 4. ΠΡΠ²ΠΎΠ΄Ρ ΠΈ ΡΠ΅ΠΊΠΎΠΌΠ΅Π½Π΄Π°ΡΠΈΠΈ
- Β Β Β Β 4.1. ΠΡΠ²ΠΎΠ΄Ρ
- Β Β Β Β 4.2. Π Π΅ΠΊΠΎΠΌΠ΅Π½Π΄Π°ΡΠΈΠΈ
- ΠΠΠΠΠΠΠΠ ΠΠΠ‘Π’Π
1. ΠΠ²Π΅Π΄Π΅Π½ΠΈΠ΅
- ΠΠ»ΠΈΡΠ½ΠΈΠ΅ ΠΈ ΠΊΠΎΠ½ΡΡΠΎΠ»Ρ Ρ
ΠΈΠΌΠΈΡΠ΅ΡΠΊΠΎΠ³ΠΎ ΡΠΎΡΡΠ°Π²Π° ΠΊΠ»ΠΈΠ½ΠΊΠ΅ΡΠ° ΡΠ²Π»ΡΠ΅ΡΡΡ Π²Π°ΠΆΠ½ΡΠΌ Π°ΡΠΏΠ΅ΠΊΡΠΎΠΌ ΡΠ΅ΠΌΠ΅Π½ΡΠ° ΠΏΡΠΎΠΈΠ·Π²ΠΎΠ΄ΡΡΠ²Π΅Π½Π½ΡΠΉ ΠΏΡΠΎΡΠ΅ΡΡ. Π ΠΏΡΠΎΠΈΠ·Π²ΠΎΠ΄ΡΡΠ²Π΅ ΡΠ΅ΠΌΠ΅Π½ΡΠ° Π²Π»ΠΈΡΠ½ΠΈΠ΅ Ρ
ΠΈΠΌΠΈΡΠ΅ΡΠΊΠΎΠ³ΠΎ ΡΠΎΡΡΠ°Π²Π° ΠΊΠ»ΠΈΠ½ΠΊΠ΅ΡΠ° Π½Π° ΡΠ΅Ρ
Π½ΠΎΠ»ΠΎΠ³ΠΈΡΠ΅ΡΠΊΠΈΠ΅ ΠΌΠ°ΡΠ΅ΡΠΈΠ°Π»Ρ ΠΈ Π³ΠΎΡΠΎΠ²ΡΡ ΠΏΡΠΎΠ΄ΡΠΊΡΠΈΡ Π½Π΅ΠΎΠ±Ρ
ΠΎΠ΄ΠΈΠΌΠΎ Π°Π½Π°Π»ΠΈΠ·ΠΈΡΠΎΠ²Π°ΡΡ, ΠΊΠΎΠ½ΡΡΠΎΠ»ΠΈΡΠΎΠ²Π°ΡΡ ΠΈ ΡΡΡΠ΅ΠΊΡΠΈΠ²Π½ΠΎ ΠΊΠΎΠ½ΡΡΠΎΠ»ΠΈΡΠΎΠ²Π°ΡΡ Π΄Π»Ρ ΠΎΠΏΡΠΈΠΌΠΈΠ·Π°ΡΠΈΠΈ ΠΏΡΠΎΡΠ΅ΡΡΠ° ΠΈ ΠΏΠΎΡΡΠΎΡΠ½Π½ΠΎΠ³ΠΎ ΠΆΠ΅Π»Π°Π΅ΠΌΠΎΠ³ΠΎ ΠΊΠ°ΡΠ΅ΡΡΠ²Π° ΠΏΡΠΎΠ΄ΡΠΊΡΠ° ΡΠ΅ΠΌΠ΅Π½ΡΠ°. Π¦Π΅ΠΌΠ΅Π½ΡΠ½ΠΎΠ΅ Π²Π΅ΡΠ΅ΡΡΠ²ΠΎ ΠΏΠΎΠ»ΡΡΠ°ΡΡ ΠΈΠ·ΠΌΠ΅Π»ΡΡΠ΅Π½ΠΈΠ΅ΠΌ ΡΠΌΠ΅ΡΠΈ Π³Π»ΠΈΠ½Ρ ΠΈ ΠΈΠ·Π²Π΅ΡΡΠ½ΡΠΊΠ° ΠΈ Π½Π°Π³ΡΠ΅Π²Π°Π½ΠΈΠ΅ΠΌ Π΄ΠΎ ΡΠ΅ΠΌΠΏΠ΅ΡΠ°ΡΡΡΡ 1450Β°Π‘. Π ΠΊΠΎΡΠΎΡΠΎΠΌ Ρ
ΠΈΠΌΠΈΡΠ΅ΡΠΊΠΎΠ΅ ΠΏΡΠ΅Π²ΡΠ°ΡΠ΅Π½ΠΈΠ΅ ΠΏΡΠΎΠΈΡΡ
ΠΎΠ΄ΠΈΡ Π²Π½ΡΡΡΠΈ ΠΏΠ΅ΡΠΈ Ρ ΠΎΠ±ΡΠ°Π·ΠΎΠ²Π°Π½ΠΈΠ΅ΠΌ Π½ΠΎΠ²ΠΎΠ³ΠΎ ΡΠΎΠ΅Π΄ΠΈΠ½Π΅Π½ΠΈΡ, Π½Π°Π·ΡΠ²Π°Π΅ΠΌΠΎΠ³ΠΎ ΠΊΠ»ΠΈΠ½ΠΊΠ΅ΡΠΎΠΌ. ΠΠ»ΠΈΠ½ΠΊΠ΅Ρ, ΠΎΠ±ΡΠ°Π·ΡΡΡΠΈΠΉΡΡ Π² ΡΠ΅Π·ΡΠ»ΡΡΠ°ΡΠ΅ ΠΎΠ±ΠΆΠΈΠ³Π° Π½Π° ΡΡΠ°Π΄ΠΈΠΈ ΠΏΠ΅ΡΠΈ, ΠΌΠΎΠΆΠ½ΠΎ ΠΎΠΏΠΈΡΠ°ΡΡ ΠΊΠ°ΠΊ ΠΊΠΎΠΌΠΊΠΈ ΠΈΠ»ΠΈ ΡΠ·Π΅Π»ΠΊΠΈ, ΠΎΠ±ΡΡΠ½ΠΎ Π΄ΠΈΠ°ΠΌΠ΅ΡΡΠΎΠΌ ΠΎΡ 3 ΠΌΠΌ Π΄ΠΎ 25 ΠΌΠΌ.
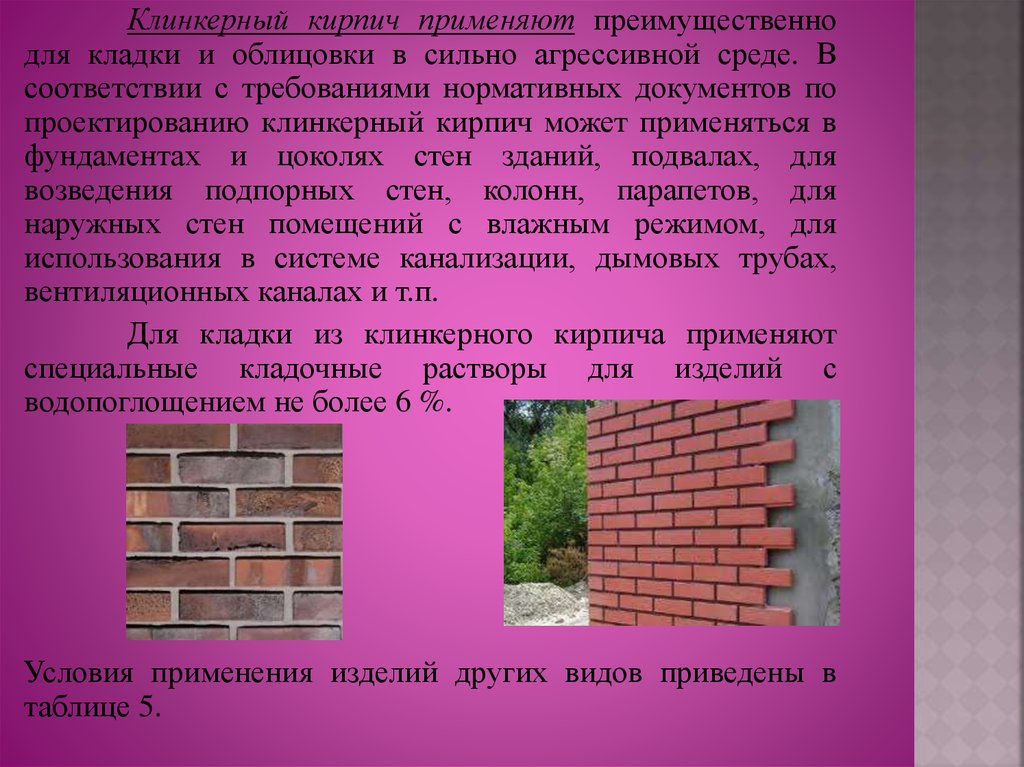
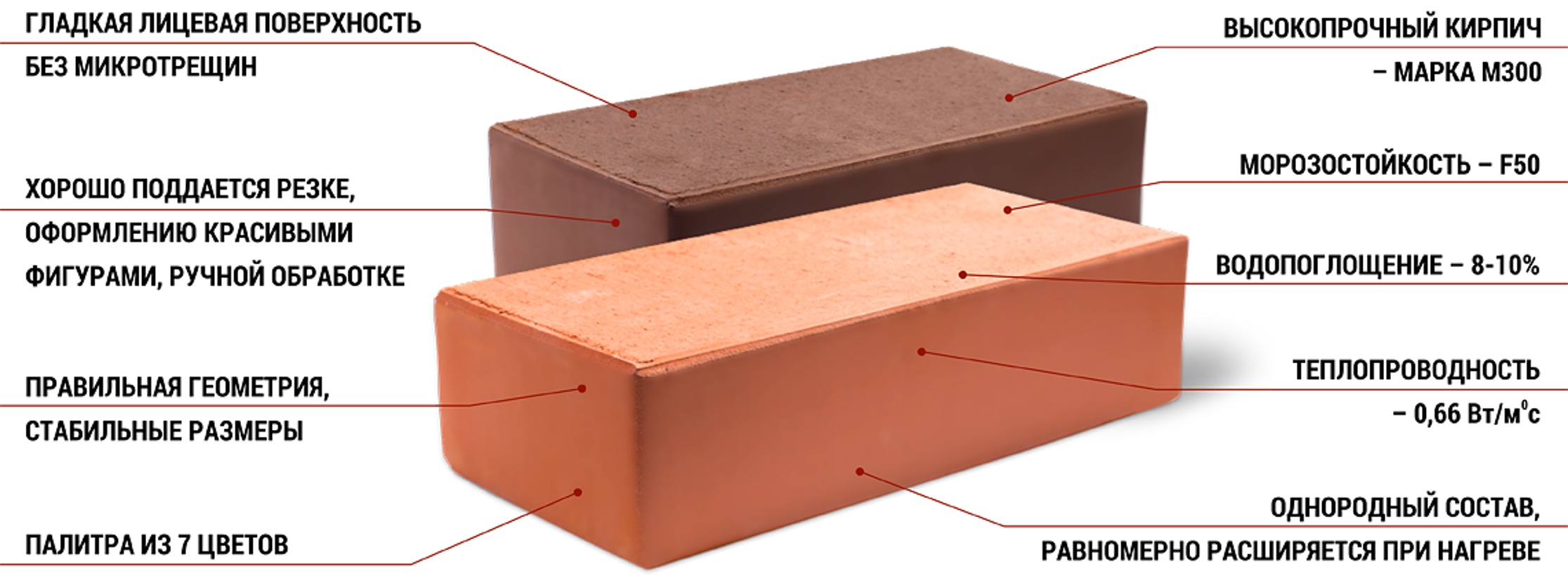
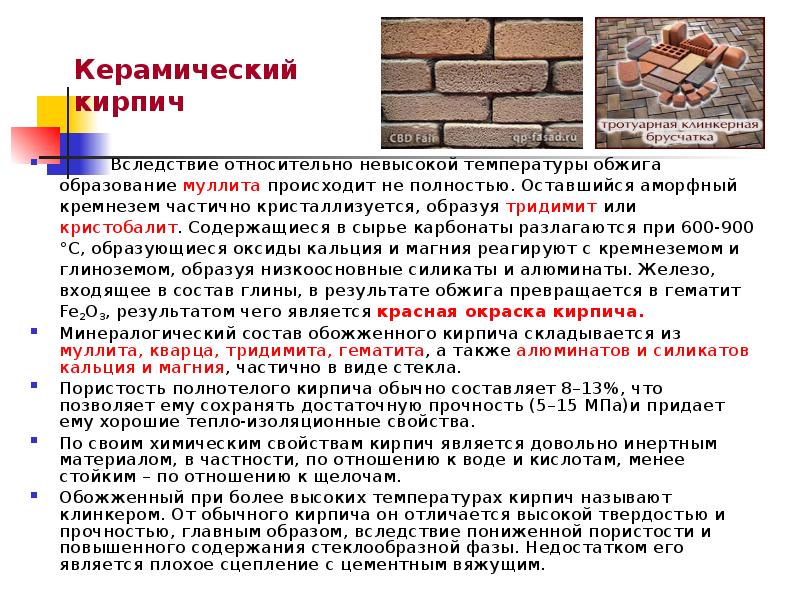
1.1. Π₯ΠΈΠΌΠΈΡΠ΅ΡΠΊΠΈΠΉ ΡΠΎΡΡΠ°Π² ΠΈΡΡ ΠΎΠ΄Π½ΠΎΠ³ΠΎ ΡΡΡΡΡ
- ΠΠ»Ρ Π΄ΠΎΡΡΠΈΠΆΠ΅Π½ΠΈΡ ΡΡΠ΅Π±ΡΠ΅ΠΌΠΎΠ³ΠΎ Ρ
ΠΈΠΌΠΈΡΠ΅ΡΠΊΠΎΠ³ΠΎ ΡΠΎΡΡΠ°Π²Π° ΠΊΠ»ΠΈΠ½ΠΊΠ΅ΡΠ° ΠΏΡΠΈ ΡΠΏΠ΅ΠΊΠ°Π½ΠΈΠΈ Π½Π΅ΠΎΠ±Ρ
ΠΎΠ΄ΠΈΠΌΠΎ Π·Π°Π΄Π°ΡΡ Ρ
ΠΈΠΌΠΈΡΠ΅ΡΠΊΠΈΠΉ ΡΠΎΡΡΠ°Π² ΠΈΡΡ
ΠΎΠ΄Π½ΠΎΠ³ΠΎ ΡΡΡΡΡ. Π Π°Π·Π»ΠΈΡΠ½ΡΠ΅ Ρ
ΠΈΠΌΠΈΡΠ΅ΡΠΊΠΈΠ΅ ΠΏΠ°ΡΠ°ΠΌΠ΅ΡΡΡ ΠΌΠΎΠ³ΡΡ Π±ΡΡΡ ΠΈΡΠΏΠΎΠ»ΡΠ·ΠΎΠ²Π°Π½Ρ Π΄Π»Ρ ΠΊΠΎΠ½ΡΡΠΎΠ»Ρ Π² Π·Π°Π²ΠΈΡΠΈΠΌΠΎΡΡΠΈ ΠΎΡ ΠΊΠΎΠ»ΠΈΡΠ΅ΡΡΠ²Π° ΡΡΡΡΡ, ΠΈΡΠΏΠΎΠ»ΡΠ·ΡΠ΅ΠΌΠΎΠ³ΠΎ Π΄Π»Ρ ΠΏΡΠΈΠ³ΠΎΡΠΎΠ²Π»Π΅Π½ΠΈΡ ΠΊΠΎΡΠΌΠ°. ΠΠ±ΡΡΠ½ΠΎ ΠΊΠΎΠ»ΠΈΡΠ΅ΡΡΠ²ΠΎ ΡΠ΅Π»Π΅Π²ΡΡ
ΠΏΠ°ΡΠ°ΠΌΠ΅ΡΡΠΎΠ², ΠΊΠΎΡΠΎΡΡΠ΅ ΠΌΠΎΠΆΠ½ΠΎ ΠΊΠΎΠ½ΡΡΠΎΠ»ΠΈΡΠΎΠ²Π°ΡΡ, Π½Π° Π΅Π΄ΠΈΠ½ΠΈΡΡ ΠΌΠ΅Π½ΡΡΠ΅, ΡΠ΅ΠΌ ΠΊΠΎΠ»ΠΈΡΠ΅ΡΡΠ²ΠΎ ΡΡΡΡΡ. Π’Π΅ΠΌ Π½Π΅ ΠΌΠ΅Π½Π΅Π΅, Π΄Π»Ρ ΠΊΠΎΠ½ΡΡΠΎΠ»Ρ ΡΡΡΡΠ΅Π²ΠΎΠΉ ΡΠΌΠ΅ΡΠΈ Ρ ΠΈΡΠΏΠΎΠ»ΡΠ·ΠΎΠ²Π°Π½ΠΈΠ΅ΠΌ ΠΊΠ°ΡΠ±ΠΎΠ½Π°ΡΠ° ΠΊΠ°Π»ΡΡΠΈΡ ΡΡΠ΅Π±ΡΠ΅ΡΡΡ Π΄Π²Π° Π²ΠΈΠ΄Π° ΡΡΡΡΡ β Π²ΡΡΠΎΠΊΠΎΠΊΠ°ΡΠ΅ΡΡΠ²Π΅Π½Π½ΡΠΉ ΠΈ Π½ΠΈΠ·ΠΊΠΎΡΠΎΡΡΠ½ΡΠΉ ΠΊΠ°ΠΌΠ΅Π½Ρ. ΠΡΠ»ΠΈ ΡΠ°ΠΊΠΆΠ΅ Π½Π΅ΠΎΠ±Ρ
ΠΎΠ΄ΠΈΠΌΠΎ ΠΊΠΎΠ½ΡΡΠΎΠ»ΠΈΡΠΎΠ²Π°ΡΡ ΡΠΎΠ΄Π΅ΡΠΆΠ°Π½ΠΈΠ΅ ΠΆΠ΅Π»Π΅Π·Π°, ΡΠΎ Π΄Π»Ρ Π½Π°Π΄Π»Π΅ΠΆΠ°ΡΠ΅ΠΉ ΡΠ΅Π³ΡΠ»ΠΈΡΠΎΠ²ΠΊΠΈ Π½Π΅ΠΎΠ±Ρ
ΠΎΠ΄ΠΈΠΌΠΎ Π΄ΠΎΠ±Π°Π²ΠΈΡΡ ΡΡΠ΅ΡΠΈΠΉ ΡΡΡΡΠ΅Π²ΠΎΠΉ ΠΌΠ°ΡΠ΅ΡΠΈΠ°Π», ΡΠΎΠ΄Π΅ΡΠΆΠ°ΡΠΈΠΉ ΠΎΠΊΡΠΈΠ΄ ΠΆΠ΅Π»Π΅Π·Π° (CCNN β Sokoto, 2009 Π³.).). ΠΠ±ΡΡΠ½ΠΎ ΡΠ΅Π»Π΅Π²ΡΠΌ ΡΡΡΡΠ΅ΠΌ, ΠΏΡΠΈΠΌΠ΅Π½ΡΠ΅ΠΌΡΠΌ Π½Π° Π·Π°Π²ΠΎΠ΄Π΅, ΡΠ²Π»ΡΠ΅ΡΡΡ Π΄ΠΎΡΡΡΠΏΠ½ΠΎΠ΅ ΡΡΡΡΠ΅ ΠΈ Π²Π°ΠΆΠ½ΡΠ΅ ΠΏΠ°ΡΠ°ΠΌΠ΅ΡΡΡ ΠΊΠ»ΠΈΠ½ΠΊΠ΅ΡΠ°. ΠΠ±ΡΡΠ½ΡΠ΅ ΠΊΠΎΠΌΠ±ΠΈΠ½Π°ΡΠΈΠΈ ΡΠ΅Π»Π΅Π²ΡΡ
ΠΏΠ°ΡΠ°ΠΌΠ΅ΡΡΠΎΠ² ΠΈΡΡ
ΠΎΠ΄Π½ΠΎΠ³ΠΎ ΡΡΡΡΡ ΠΌΠΎΠ³ΡΡ ΠΎΡΠ½ΠΎΠ²ΡΠ²Π°ΡΡΡΡ Π½Π°: Β§ Π₯ΠΈΠΌΠΈΡΠ΅ΡΠΊΠΈΠΉ ΡΠΎΡΡΠ°Π² β CaCO 3 , SiO 2 ΠΈ Fe 2 O 3 Β§ Π Π°ΡΡΠ΅ΡΠ½ΡΠΉ ΠΌΠΈΠ½Π΅ΡΠ°Π»ΠΎΠ³ΠΈΡΠ΅ΡΠΊΠΈΠΉ ΡΠΎΡΡΠ°Π² C 900 53 3 S, C 3 A ΠΈ C 4 AF Β§ Π Π°ΡΡΡΠΈΡΠ°Π½Π½ΡΠ΅ ΠΊΠΎΡΡΡΠΈΡΠΈΠ΅Π½ΡΡ, ΡΠ°ΠΊΠΈΠ΅ ΠΊΠ°ΠΊ LSF, SM ΠΈ AM Β§ ΠΠ»ΠΈ ΠΊΠΎΠΌΠ±ΠΈΠ½Π°ΡΠΈΡ ΠΏΠ°ΡΠ°ΠΌΠ΅ΡΡΠΎΠ² ΠΈΠ· Π²ΡΠ΅Ρ
ΡΡΠ΅Ρ
Π³ΡΡΠΏΠΏ.
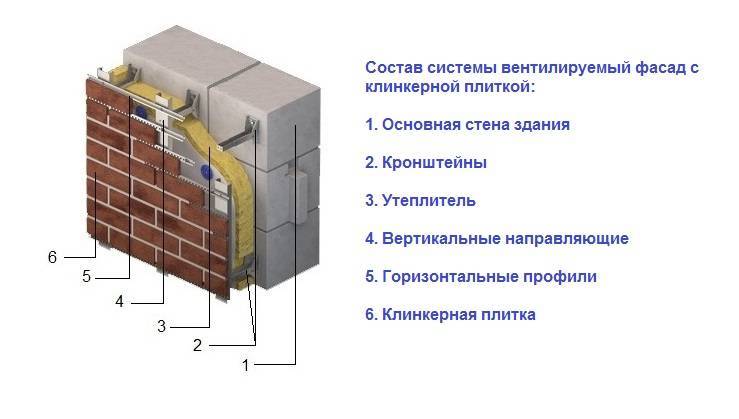
1.2. ΠΡΠΎΡΠ΅ΡΡ ΠΎΠ±ΠΆΠΈΠ³Π°
- Π‘ΠΎΠ²ΡΠ΅ΠΌΠ΅Π½Π½Π°Ρ ΡΠ΅Ρ
Π½ΠΎΠ»ΠΎΠ³ΠΈΡΠ΅ΡΠΊΠ°Ρ ΡΠΈΡΡΠ΅ΠΌΠ° ΠΏΡΠΎΠΈΠ·Π²ΠΎΠ΄ΡΡΠ²Π° ΡΠ΅ΠΌΠ΅Π½ΡΠ°, Π²ΡΠ΅ΠΌΡ ΠΏΡΠ΅Π±ΡΠ²Π°Π½ΠΈΡ ΠΌΠ°ΡΠ΅ΡΠΈΠ°Π»Π° Π²Π½ΡΡΡΠΈ ΠΏΠ΅ΡΠΈ ΡΠΎΡΡΠ°Π²Π»ΡΠ΅Ρ ΠΎΡ 30 Π΄ΠΎ 40 ΠΌΠΈΠ½ΡΡ, ΠΈΠ· ΠΊΠΎΡΠΎΡΡΡ
Π±ΠΎΠ»ΡΡΠ°Ρ ΡΠ°ΡΡΡ Π½Π°Ρ
ΠΎΠ΄ΠΈΡΡΡ Π² Π·ΠΎΠ½Π΅ ΠΎΠ±ΠΆΠΈΠ³Π°. Π’Π΅ΠΌΠΏΠ΅ΡΠ°ΡΡΡΠ° ΠΌΠ°ΡΠ΅ΡΠΈΠ°Π»Π° Π±ΡΡΡΡΠΎ ΡΠ²Π΅Π»ΠΈΡΠΈΠ²Π°Π΅ΡΡΡ Ρ 850Β°C Π΄ΠΎ 1250Β°C ΠΈ 1300Β°C, ΠΏΡΠΈ ΠΊΠΎΡΠΎΡΠΎΠΉ ΡΠΎΡΠΌΠΈΡΡΠ΅ΡΡΡ ΡΠ΅ΠΌΠΏΠ΅ΡΠ°ΡΡΡΠ° ΠΊΠ»ΠΈΠ½ΠΊΠ΅ΡΠ½ΠΎΠ³ΠΎ ΡΠ°ΡΠΏΠ»Π°Π²Π° (Mohamed A. Aldieb, 2010). Π₯ΠΈΠΌΠΈΡΠ΅ΡΠΊΠΈΠ΅ ΠΈ ΡΠΈΠ·ΠΈΡΠ΅ΡΠΊΠΈΠ΅ ΠΈΠ·ΠΌΠ΅Π½Π΅Π½ΠΈΡ ΠΌΠ°ΡΠ΅ΡΠΈΠ°Π»Π° ΠΏΡΠΎΠΈΡΡ
ΠΎΠ΄ΡΡ Π² Π·ΠΎΠ½Π΅ Π³ΠΎΡΠ΅Π½ΠΈΡ ΠΎΠ΄Π½ΠΎΠ²ΡΠ΅ΠΌΠ΅Π½Π½ΠΎ; ΡΡΠΎ Π²Π°ΠΆΠ½ΠΎ Ρ ΡΠΎΡΠΊΠΈ Π·ΡΠ΅Π½ΠΈΡ ΠΊΠΈΠ½Π΅ΡΠΈΠΊΠΈ ΡΠ΅Π°ΠΊΡΠΈΠΉ ΠΊΠ»ΠΈΠ½ΠΊΠ΅ΡΠΈΠ·Π°ΡΠΈΠΈ ΠΈ ΠΏΡΠΎΡΠ΅ΡΡΠ° Π°Π³Π»ΠΎΠΌΠ΅ΡΠ°ΡΠΈΠΈ. Π€Π°ΠΊΡΠΈΡΠ΅ΡΠΊΠ°Ρ ΡΠ΅ΠΌΠΏΠ΅ΡΠ°ΡΡΡΠ° ΠΎΠ±ΡΠ°Π·ΠΎΠ²Π°Π½ΠΈΡ ΡΠ°ΡΠΏΠ»Π°Π²Π° Π·Π°Π²ΠΈΡΠΈΡ ΠΎΡ Ρ
ΠΈΠΌΠΈΡΠ΅ΡΠΊΠΎΠ³ΠΎ ΡΠΎΡΡΠ°Π²Π° ΡΡΡΡΡ. Π’Π΅ΠΌ Π½Π΅ ΠΌΠ΅Π½Π΅Π΅, ΠΎΠΏΠ΅ΡΠ°ΡΠΎΡ ΠΏΠ΅ΡΠΈ Π΄ΠΎΠ»ΠΆΠ΅Π½ ΠΏΠΎΠ΄Π΄Π΅ΡΠΆΠΈΠ²Π°ΡΡ ΡΡΠ°Π±ΠΈΠ»ΡΠ½ΡΠ΅ ΡΠ΅ΠΌΠΏΠ΅ΡΠ°ΡΡΡΡ Π² ΠΊΠ°ΠΆΠ΄ΠΎΠΉ ΡΠ°ΡΡΠΈ ΡΠΈΡΡΠ΅ΠΌΡ ΠΏΠ΅ΡΠΈ, ΡΡΠΎΠ±Ρ ΠΏΡΠ΅ΠΎΠ±ΡΠ°Π·ΠΎΠ²Π°ΡΡ ΡΡΡΡΠ΅ (ΡΡΡΡΠ΅) Π² ΠΏΠ΅ΡΠΈ Π² ΠΊΠ»ΠΈΠ½ΠΊΠ΅ΡΠ½ΡΠ΅ ΠΌΠΈΠ½Π΅ΡΠ°Π»Ρ, ΠΏΠΎΡΠΎΠΌΡ ΡΡΠΎ ΠΏΡΠΈ ΠΎΡΠΊΠ»ΠΎΠ½Π΅Π½ΠΈΠΈ ΡΠ΅ΠΌΠΏΠ΅ΡΠ°ΡΡΡΡ ΡΠ°Π±ΠΎΡΠ° ΠΏΠ΅ΡΠΈ ΡΡΠ°Π½ΠΎΠ²ΠΈΡΡΡ Π½Π΅ΡΡΠ°Π±ΠΈΠ»ΡΠ½ΠΎΠΉ, Π° ΠΊΠ»ΠΈΠ½ΠΊΠ΅ΡΠ½ΡΠ΅ ΠΌΠΈΠ½Π΅ΡΠ°Π»Ρ Π½Π΅ ΠΎΠ±ΡΠ°Π·ΡΡΡΡΡ Π΄ΠΎΠ»ΠΆΠ½ΡΠΌ ΠΎΠ±ΡΠ°Π·ΠΎΠΌ, ΡΡΠΎ ΠΏΡΠΈΠ²ΠΎΠ΄ΠΈΡ ΠΊ ΠΈΠ·ΠΌΠ΅Π½Π΅Π½ΠΈΡ Ρ
Π°ΡΠ°ΠΊΡΠ΅ΡΠΈΡΡΠΈΠΊ ΡΠ΅ΠΌΠ΅Π½ΡΠ° (CCNN – Sokoto, 2009).

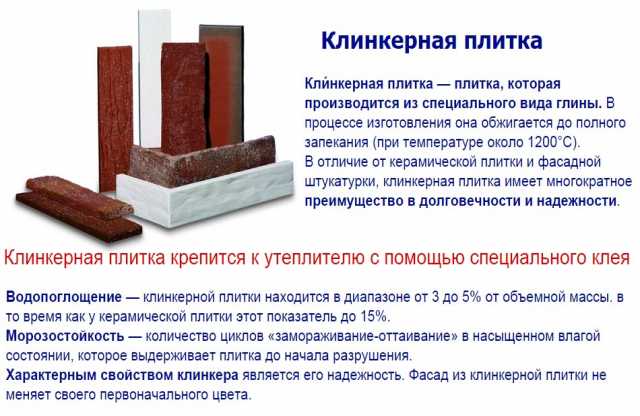
Π ΠΈΡ. 2003) |

2. ΠΠ°ΡΠ΅ΡΠΈΠ°Π»Ρ ΠΈ ΠΌΠ΅ΡΠΎΠ΄Ρ
- ΠΠ°ΡΠ΅ΡΠΈΠ°Π»Ρ ΠΈ ΠΌΠ΅ΡΠΎΠ΄Ρ, ΠΏΡΠΈΠΌΠ΅Π½ΡΠ΅ΠΌΡΠ΅ ΠΏΡΠΈ ΠΏΡΠΎΠ²Π΅Π΄Π΅Π½ΠΈΠΈ Ρ
ΠΈΠΌΠΈΡΠ΅ΡΠΊΠΎΠ³ΠΎ Π°Π½Π°Π»ΠΈΠ·Π° Ρ ΠΏΠΎΠΌΠΎΡΡΡ ΡΠ΅Π½ΡΠ³Π΅Π½ΠΎΡΡΡΡΠΊΡΡΡΠ½ΠΎΠ³ΠΎ Π°Π½Π°Π»ΠΈΠ·Π° Π² ΡΠ΅ΠΌΠ΅Π½ΡΠ½ΠΎΠΉ ΠΏΡΠΎΠΌΡΡΠ»Π΅Π½Π½ΠΎΡΡΠΈ Π΄Π»Ρ ΠΎΠΏΡΠ΅Π΄Π΅Π»Π΅Π½ΠΈΡ Π½Π°Π»ΠΈΡΠΈΡ ΠΈ ΠΊΠΎΠ»ΠΈΡΠ΅ΡΡΠ²Π° ΠΌΠΈΠ½Π΅ΡΠ°Π»ΡΠ½ΡΡ
ΠΏΠΎΡΠΎΠ΄ Π² ΠΏΡΠΎΠ±Π°Ρ
, Π° ΡΠ°ΠΊΠΆΠ΅ Π²ΡΠ΄Π΅Π»Π΅Π½ΠΈΡ ΡΠ°Π·. Π ΠΌΠ΅ΡΠΎΠ΄ ΠΈΡΠΏΡΡΠ°Π½ΠΈΡ ΠΏΡΠΎΡΠ½ΠΎΡΡΠΈ Π½Π° ΡΠΆΠ°ΡΠΈΠ΅.
2.1. ΠΠ°ΡΠ΅ΡΠΈΠ°Π»Ρ
- Β§ ΠΠΎΠ΄Π° Π΄ΠΈΡΡΠΈΠ»Π»ΠΈΡΠΎΠ²Π°Π½Π½Π°Ρ Β§ 10 ΠΠ±ΡΠ°Π·ΡΡ Π½Π°Π²Π΅ΡΠΊΠΈ ΠΊΠ»ΠΈΠ½ΠΊΠ΅ΡΠ° Β§ ΠΠ°ΡΠΈΠ½Π° Π΄Π»Ρ ΠΈΡΠΏΡΡΠ°Π½ΠΈΡ Π½Π° ΠΏΡΠΎΡΠ½ΠΎΡΡΡ ΠΏΡΠΈ ΡΠΆΠ°ΡΠΈΠΈ Β§ ΠΡΡΡΡΡ
ΠΈΠ²Π°ΡΡΠ°Ρ ΠΌΠ°ΡΠΈΠ½Π° Β§ ΠΡΠΈΠ·ΠΌΠ°ΡΠΈΡΠ΅ΡΠΊΠ°Ρ ΡΠΎΡΠΌΠ° Β§ Π‘ΠΌΠ΅ΡΠΈΡΠ΅Π»Ρ
2.
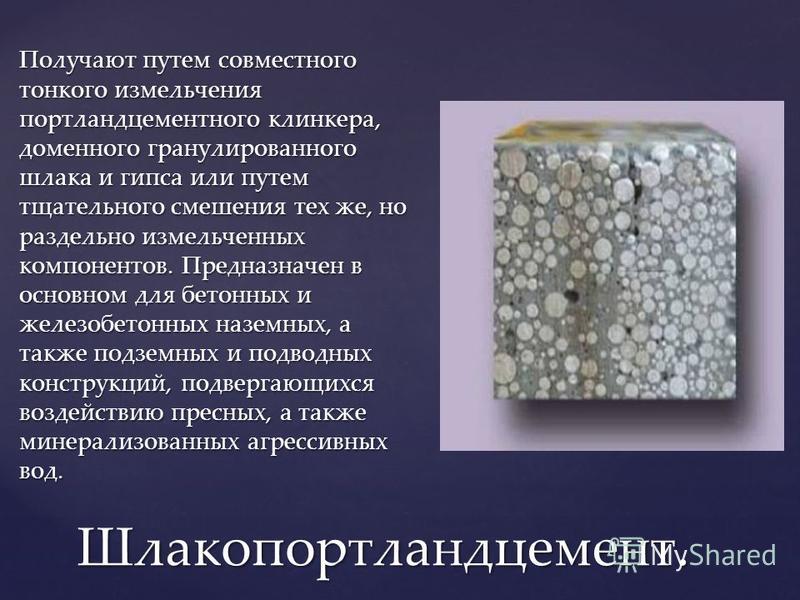
- Β§ 10 Π³ ΠΊΠ°ΠΆΠ΄ΠΎΠ³ΠΎ ΠΎΠ±ΡΠ°Π·ΡΠ° ΠΊΠ»ΠΈΠ½ΠΊΠ΅ΡΠ° Π²Π·Π²Π΅ΡΠΈΠ²Π°Π»ΠΈ, ΠΈΠ·ΠΌΠ΅Π»ΡΡΠ°Π»ΠΈ ββΠΈ Π³ΡΠ°Π½ΡΠ»ΠΈΡΠΎΠ²Π°Π»ΠΈ Ρ ΠΏΠΎΠΌΠΎΡΡΡ ΠΏΠΈΡΠΈΠ΄ΠΈΠ½Π° ΠΈ ΡΠ²ΡΠ·ΡΡΡΠ΅Π³ΠΎ Π²Π΅ΡΠ΅ΡΡΠ²Π°. Β§ ΠΠ±ΡΠ°Π·ΡΡ ΠΎΠΊΠ°ΡΡΡΠ΅ΠΉ Π±ΡΠ»ΠΈ ΠΏΠΎΠ΄Π²Π΅ΡΠ³Π½ΡΡΡ Π°Π½Π°Π»ΠΈΠ·Ρ XRD/XRF Π΄Π»Ρ ΠΎΠΏΡΠ΅Π΄Π΅Π»Π΅Π½ΠΈΡ ΠΌΠΈΠ½Π΅ΡΠ°Π»ΠΎΠ³ΠΈΡΠ΅ΡΠΊΠΎΠ³ΠΎ Ρ
ΠΈΠΌΠΈΡΠ΅ΡΠΊΠΎΠ³ΠΎ ΡΠΎΡΡΠ°Π²Π° ΠΎΠ±ΡΠ°Π·ΡΠΎΠ² ΠΊΠ»ΠΈΠ½ΠΊΠ΅ΡΠ° ΠΈ ΡΠΎΠΎΡΠ²Π΅ΡΡΡΠ²ΡΡΡΠΈΡ
ΠΈΠΌ ΠΎΠΊΡΠΈΠ΄ΠΎΠ² ΡΠ»Π΅ΠΌΠ΅Π½ΡΠΎΠ². ΠΠΈΠ½Π΅ΡΠ°Π»Ρ ΠΊΠ»ΠΈΠ½ΠΊΠ΅ΡΠ°, ΡΠΎΡΡΠ°Π²Ρ ΠΊΠΎΡΠΎΡΡΡ
Π±ΡΠ»ΠΈ ΠΎΠΏΡΠ΅Π΄Π΅Π»Π΅Π½Ρ Ρ ΠΏΠΎΠΌΠΎΡΡΡ XRDF / XRD, Π±ΡΠ»ΠΈ; Π‘ 3 S, C 2 S ΠΈ C 4 AF, Π° ΡΠ°ΠΊΠΆΠ΅ ΠΎΠΏΡΠ΅Π΄Π΅Π»Π΅Π½Ρ ΡΠΎΡΡΠ°Π²Ρ ΡΠ»Π΅ΠΌΠ΅Π½ΡΠ°ΡΠ½ΡΡ
ΠΎΠΊΡΠΈΠ΄ΠΎΠ²: CaO, SiO 2 , Al 2 O 3 ΠΈ MgO. ΠΠΎΠ΄ΡΠ»Ρ ΠΊΡΠ΅ΠΌΠ½Π΅Π·Π΅ΠΌΠ°, ΠΌΠΎΠ΄ΡΠ»Ρ Π³Π»ΠΈΠ½ΠΎΠ·Π΅ΠΌΠ°, ΠΊΠΎΡΡΡΠΈΡΠΈΠ΅Π½Ρ Π½Π°ΡΡΡΠ΅Π½ΠΈΡ ΠΈΠ·Π²Π΅ΡΡΡΡ ΠΎΠΏΡΠ΅Π΄Π΅Π»ΡΠ»ΠΈ ΠΈΠ· ΡΠΎΡΡΠ°Π²ΠΎΠ² ΠΎΠΊΡΠΈΠ΄ΠΎΠ² ΡΠ»Π΅ΠΌΠ΅Π½ΡΠΎΠ² Ρ ΠΈΡΠΏΠΎΠ»ΡΠ·ΠΎΠ²Π°Π½ΠΈΠ΅ΠΌ ΡΡΠ°Π²Π½Π΅Π½ΠΈΡ Bogues, ΡΠΎΡ
ΡΠ°Π½Π΅Π½Π½ΠΎΠ³ΠΎ Π² Π²ΠΈΠ΄Π΅ ΠΏΡΠΎΠ³ΡΠ°ΠΌΠΌΡ Π² Π°Π½Π°Π»ΠΈΠ·Π°ΡΠΎΡΠ΅ XRD/XRF. Β§ ΠΠ»Ρ ΠΏΡΠΎΡΠ½ΠΎΡΡΠΈ Π½Π° ΡΠΆΠ°ΡΠΈΠ΅. 1350 Π³, 450 Π³ ΠΈ 225 Π³ ΡΡΠ°Π½Π΄Π°ΡΡΠ½ΠΎΠ³ΠΎ ΠΏΠ΅ΡΠΊΠ°, ΠΎΠ±ΡΠ°Π·ΡΠ° ΡΠ΅ΠΌΠ΅Π½ΡΠ° ΠΈ Π΄ΠΈΡΡΠΈΠ»Π»ΠΈΡΠΎΠ²Π°Π½Π½ΠΎΠΉ Π²ΠΎΠ΄Ρ Π±ΡΠ»ΠΈ Π²Π·Π²Π΅ΡΠ΅Π½Ρ ΡΠΎΠΎΡΠ²Π΅ΡΡΡΠ²Π΅Π½Π½ΠΎ, Π° Π·Π°ΡΠ΅ΠΌ ΡΠΌΠ΅ΡΠ°Π½Ρ Π² Π°Π²ΡΠΎΠΌΠ°ΡΠΈΡΠ΅ΡΠΊΠΎΠΉ ΡΠΌΠ΅ΡΠΈΡΠ΅Π»ΡΠ½ΠΎΠΉ ΠΌΠ°ΡΠΈΠ½Π΅. ΠΠ°ΡΠ΅ΠΌ ΡΠΌΠ΅ΡΠΈ ΠΏΠ΅ΡΠ΅Π½ΠΎΡΠΈΠ»ΠΈ Π² ΠΏΡΠΈΠ·ΠΌΠ°ΡΠΈΡΠ΅ΡΠΊΡΡ ΡΠΎΡΠΌΡ, ΡΡΡΠ°Π½ΠΎΠ²Π»Π΅Π½Π½ΡΡ Π½Π° Π²ΡΡΡΡΡ
ΠΈΠ²Π°ΡΡΠ΅ΠΌ ΡΡΡΡΠΎΠΉΡΡΠ²Π΅, ΠΈ Π²ΡΡΡΡΡ
ΠΈΠ²Π°Π»ΠΈ Π² ΡΠ΅ΡΠ΅Π½ΠΈΠ΅ 2 ΠΌΠΈΠ½ΡΡ.
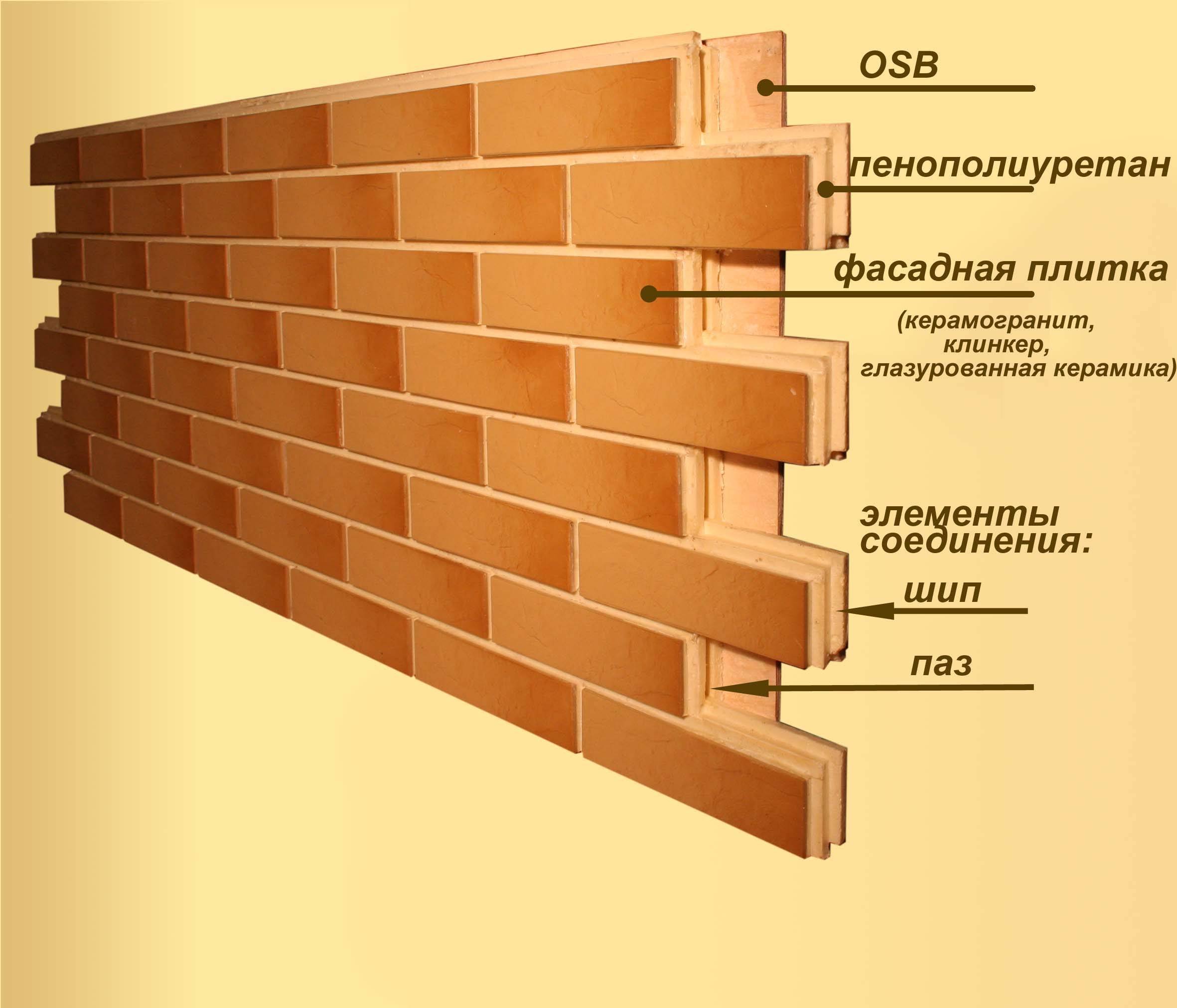
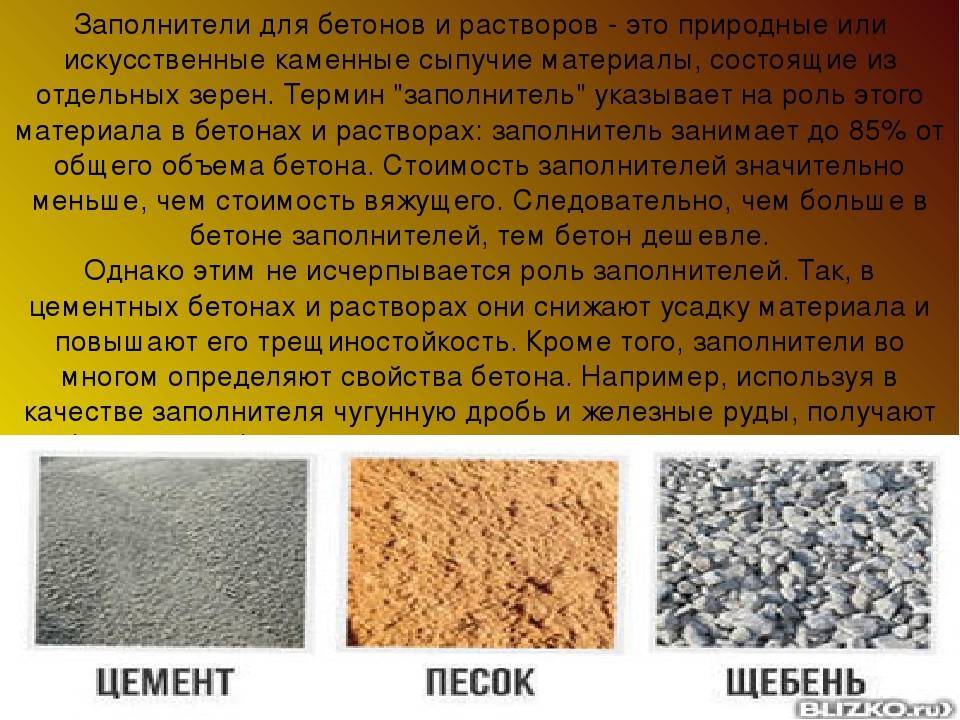
Π ΠΈΡ.![]() |
Π ΠΈΡ Π£ΡΠ΅ 3. ΠΡΡΡΡΡ ΠΈΠ²Π°ΡΡΠ°Ρ ΠΌΠ°ΡΠΈΠ½Π° |
Π ΠΈΡ 4 . ΠΠ΅ΡΡ |

Π ΠΈΡ. ΠΌΠ°ΡΠΈΠ½Π°, ΠΈΡΠΏΠΎΠ»ΡΠ·ΡΠ΅ΠΌΠ°Ρ Π² ΡΠ΅ΠΌΠ΅Π½ΡΠ½ΠΎΠΉ ΠΈΠ»ΠΈ Π»ΡΠ±ΠΎΠΉ Ρ
ΠΈΠΌΠΈΡΠ΅ΡΠΊΠΎΠΉ ΠΏΡΠΎΠΌΡΡΠ»Π΅Π½Π½ΠΎΡΡΠΈ Π΄Π»Ρ ΠΎΠΏΡΠ΅Π΄Π΅Π»Π΅Π½ΠΈΡ Π½Π°Π»ΠΈΡΠΈΡ ΠΈ ΠΊΠΎΠ»ΠΈΡΠ΅ΡΡΠ²Π° Π²ΠΈΠ΄ΠΎΠ² ΠΌΠΈΠ½Π΅ΡΠ°Π»ΠΎΠ² Π² ΠΎΠ±ΡΠ°Π·ΡΠ°Ρ
, Π° ΡΠ°ΠΊΠΆΠ΅ Π΄Π»Ρ ΠΎΠΏΡΠ΅Π΄Π΅Π»Π΅Π½ΠΈΡ ΡΠ°Π·.
3. Π Π΅Π·ΡΠ»ΡΡΠ°ΡΡ ΠΈ ΠΎΠ±ΡΡΠΆΠ΄Π΅Π½ΠΈΠ΅3.1. Π’Π°Π±Π»ΠΈΡΠ° 1: Π Π΅Π½ΡΠ³Π΅Π½ΠΎΡΠ°Π·ΠΎΠ²ΡΠΉ Π°Π½Π°Π»ΠΈΠ· ΠΎΠ±ΡΠ°Π·ΡΠΎΠ² ΠΊΠ»ΠΈΠ½ΠΊΠ΅ΡΠ°ββ |
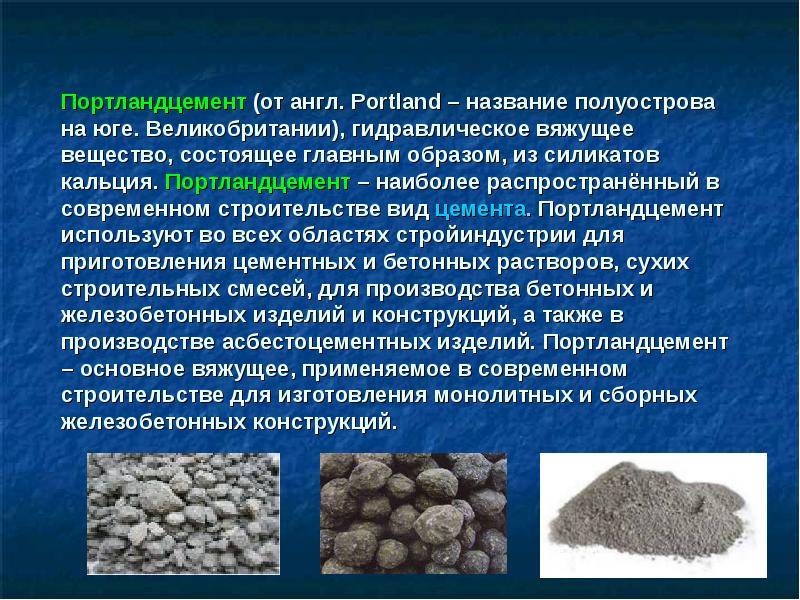
Π ΠΈΡ 8 . ΠΠΎΠ΄ΡΠ»Ρ Π³Π»ΠΈΠ½ΠΎΠ·Π΅ΠΌΠ° ΠΈ ΠΏΡΠΎΡΠ½ΠΎΡΡΡ Π½Π° ΡΠΆΠ°ΡΠΈΠ΅ Π² ΡΠ΅ΡΠ΅Π½ΠΈΠ΅ 7 Π΄Π½Π΅ΠΉ |
Π ΠΈΡ 9 . ΠΠΎΡΡΡΠΈΡΠΈΠ΅Π½Ρ Π½Π°ΡΡΡΠ΅Π½ΠΈΡ ΠΈΠ·Π²Π΅ΡΡΡΡ ΠΈ ΡΠ²ΠΎΠ±ΠΎΠ΄Π½Π°Ρ ΠΈΠ·Π²Π΅ΡΡΡ |
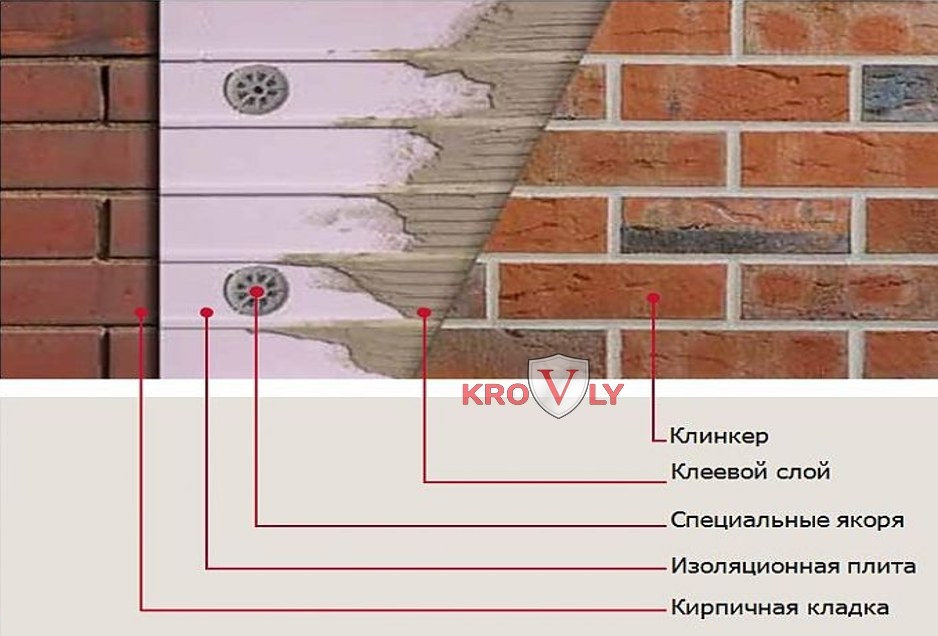
Π ΠΈΡ 10 . ΠΠΎΠ΄ΡΠ»Ρ ΠΊΡΠ΅ΠΌΠ½Π΅Π·Π΅ΠΌΠ° ΠΈ ΠΏΡΠΎΡΠ½ΠΎΡΡΡ Π½Π° ΡΠΆΠ°ΡΠΈΠ΅ Π² ΡΠ΅ΡΠ΅Π½ΠΈΠ΅ 2 Π΄Π½Π΅ΠΉ |
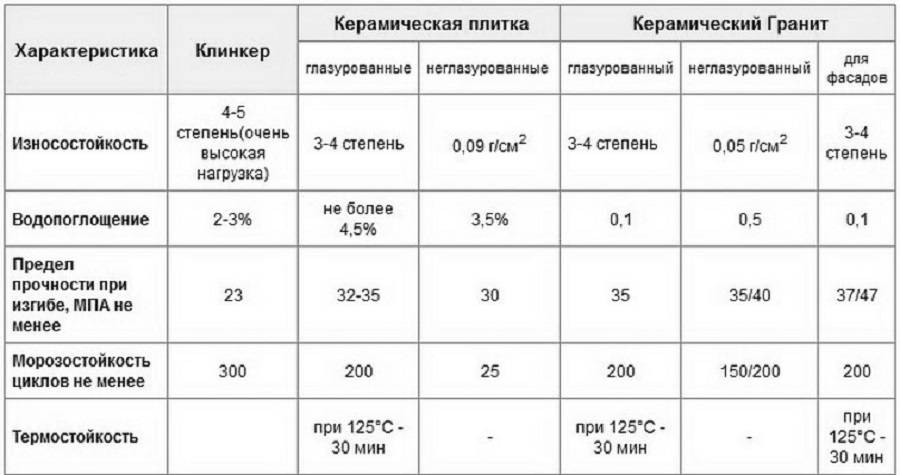
4. ΠΡΠ²ΠΎΠ΄Ρ ΠΈ ΡΠ΅ΠΊΠΎΠΌΠ΅Π½Π΄Π°ΡΠΈΠΈ
4.1. ΠΡΠ²ΠΎΠ΄Ρ
- ΠΠ°ΡΠ΅ΡΡΠ²ΠΎ ΡΠ΅ΠΌΠ΅Π½ΡΠ° ΠΎΠ±ΡΡΠ½ΠΎ ΠΎΡΠ΅Π½ΠΈΠ²Π°Π΅ΡΡΡ Π½Π° ΠΎΡΠ½ΠΎΠ²Π΅ Π½Π°Π±ΠΎΡΠ° ΠΏΡΠΎΡΠ½ΠΎΡΡΠΈ ΡΠ°ΡΡΠ²ΠΎΡΠ° ΠΈ Π±Π΅ΡΠΎΠ½Π° Π½Π° ΡΠΆΠ°ΡΠΈΠ΅. Π‘ΠΎΠΎΡΠ½ΠΎΡΠ΅Π½ΠΈΠ΅ ΠΈΠ½Π³ΡΠ΅Π΄ΠΈΠ΅Π½ΡΠΎΠ² ΡΠ΅ΠΌΠ΅Π½ΡΠ½ΠΎΠ³ΠΎ ΡΡΡΡΡ Π²Π»ΠΈΡΠ΅Ρ Π½Π° ΠΊΠ°ΡΠ΅ΡΡΠ²ΠΎ ΠΈ ΡΠ²ΠΎΠΉΡΡΠ²Π° ΡΠ΅ΠΌΠ΅Π½ΡΠ½ΠΎΠ³ΠΎ ΠΊΠ»ΠΈΠ½ΠΊΠ΅ΡΠ° ΠΈ ΠΏΠΎΡΡΠ»Π°Π½Π΄ΡΠ΅ΠΌΠ΅Π½ΡΠ°, Π° ΡΠ°ΠΊΠΆΠ΅ ΠΎΠΏΡΠΈΠΌΠ°Π»ΡΠ½ΠΎΠ΅ ΡΠΎΠΎΡΠ½ΠΎΡΠ΅Π½ΠΈΠ΅ ΠΈΠ½Π³ΡΠ΅Π΄ΠΈΠ΅Π½ΡΠΎΠ² ΡΠΏΠΎΡΠΎΠ±ΡΡΠ²ΡΠ΅Ρ ΠΈ ΡΡΠ°Π±ΠΈΠ»ΠΈΠ·ΠΈΡΡΠ΅Ρ ΡΠ΅ΠΌΠ΅Π½ΡΠ½ΡΠΉ ΠΊΠ»ΠΈΠ½ΠΊΠ΅Ρ. ΠΠ° ΡΠΈΡ. 8 ΠΏΠΎΠΊΠ°Π·Π°Π½ΠΎ ΡΠ²Π΅Π»ΠΈΡΠ΅Π½ΠΈΠ΅ ΠΏΡΠΎΡΠ½ΠΎΡΡΠΈ Π½Π° ΡΠΆΠ°ΡΠΈΠ΅ ΠΏΠΎ ΠΌΠ΅ΡΠ΅ ΡΠ²Π΅Π»ΠΈΡΠ΅Π½ΠΈΡ AM, ΡΡΠΎ ΠΏΠΎΠ΄ΡΠ²Π΅ΡΠΆΠ΄Π°Π΅Ρ, ΡΡΠΎ Π±ΠΎΠ»ΡΡΠ΅Π΅ ΠΎΠ±ΡΠ°Π·ΠΎΠ²Π°Π½ΠΈΠ΅ AM ΠΏΡΠΈΠ²ΠΎΠ΄ΠΈΡ ΠΊ ΠΎΠ±ΡΠ°Π·ΠΎΠ²Π°Π½ΠΈΡ ΠΆΠΈΠ΄ΠΊΠΎΠΉ ΡΠ°Π·Ρ ΠΈΠ»ΠΈ ΡΠ»ΡΡΠ° Π² ΠΏΠ΅ΡΠΈ Ρ ΡΠ°ΠΌΠΎΠΉ Π½ΠΈΠ·ΠΊΠΎΠΉ ΡΠ΅ΠΌΠΏΠ΅ΡΠ°ΡΡΡΠΎΠΉ, Π° ΡΠ°Π½Π½Π΅Π΅ ΠΎΠ±ΡΠ°Π·ΠΎΠ²Π°Π½ΠΈΠ΅ ΠΆΠΈΠ΄ΠΊΠΎΠΉ ΡΠ°Π·Ρ ΠΈΠ»ΠΈ ΡΠ»ΡΡΠ° Π² ΠΏΠ΅ΡΠΈ ΡΠΏΠΎΡΠΎΠ±ΡΡΠ²ΡΠ΅Ρ ΠΎΠ±ΡΠ°Π·ΠΎΠ²Π°Π½ΠΈΡ Π°Π»ΠΈΡΠ°, ΠΊΠΎΡΠΎΡΡΠΉ ΡΠ²Π»ΡΠ΅ΡΡΡ ΠΎΡΠ½ΠΎΠ²Π½ΡΠΌ ΠΊΠΎΠΌΠΏΠΎΠ½Π΅Π½ΡΠΎΠΌ ΡΠ°Π½Π½Π΅ΠΉ ΠΏΡΠΎΡΠ½ΠΎΡΡΠΈ ΡΠ΅ΠΌΠ΅Π½ΡΠ°. ΠΠ° ΡΠΈΡ. 10 ΠΏΠΎΠΊΠ°Π·Π°Π½ΠΎ, ΠΊΠ°ΠΊ Π‘Π Π²Π»ΠΈΡΠ΅Ρ Π½Π° ΡΠ°Π½Π½ΡΡ ΠΏΡΠΎΡΠ½ΠΎΡΡΡ ΡΠ΅ΠΌΠ΅Π½ΡΠ°. ΠΡΠ½ΠΊΡ 3, 9ΠΈ 10 Π‘Π ΡΡΠ½ΡΡ Π΄ΠΎ ΡΠΎΡΠΊΠΈ 20,1 ΠΈ ΠΏΡΠΎΡΠ½ΠΎΡΡΠΈ 20 ΠΠΠ° ΠΏΡΠΈ 2-Ρ
Π΄Π½Π΅Π²Π½ΠΎΠΉ ΠΏΡΠΎΡΠ½ΠΎΡΡΠΈ Π½Π° ΡΠΆΠ°ΡΠΈΠ΅, ΡΡΠΎ ΡΠΎΡ ΡΠ°ΠΊΡ, ΡΡΠΎ ΠΊΡΠ΅ΠΌΠ½Π΅Π·Π΅ΠΌΠ½ΡΠΉ ΠΌΠΎΠ΄ΡΠ»Ρ ΡΠ²Π»ΡΠ΅ΡΡΡ ΠΏΠΎΠΊΠ°Π·Π°ΡΠ΅Π»Π΅ΠΌ Π³ΠΎΡΡΡΠ΅ΡΡΠΈ ΡΡΡΡΡ Π΄Π»Ρ ΠΊΠ»ΠΈΠ½ΠΊΠ΅ΡΠ°. ΠΠΎΠ²ΡΡΠ΅Π½ΠΈΠ΅ Π‘Π Π²Π»ΠΈΡΠ΅Ρ Π½Π° ΠΎΠ±ΡΠ°Π·ΠΎΠ²Π°Π½ΠΈΠ΅ ΠΆΠΈΠ΄ΠΊΠΎΠΉ ΡΠ°Π·Ρ, Π·Π°ΡΡΡΠ΄Π½ΡΠ΅Ρ Π³ΠΎΡΠ΅Π½ΠΈΠ΅ ΠΊΠ»ΠΈΠ½ΠΊΠ΅ΡΠ° ΠΈ ΠΏΠ»ΠΎΡ
ΠΎΠ΅ ΠΊΠ°ΡΠ΅ΡΡΠ²ΠΎ ΡΠ΅ΠΌΠ΅Π½ΡΠ°, ΠΏΠΎΡΡΠΎΠΌΡ Π½Π΅ΠΎΠ±Ρ
ΠΎΠ΄ΠΈΠΌΠΎ ΡΠ΄Π΅Π»ΡΡΡ Π²Π½ΠΈΠΌΠ°Π½ΠΈΠ΅ Π΄ΠΎΡΡΠΈΠΆΠ΅Π½ΠΈΡ ΠΆΠ΅Π»Π°Π΅ΠΌΠΎΠ³ΠΎ ΡΠ΅Π»Π΅Π²ΠΎΠ³ΠΎ Π‘Π.

4.2. Π Π΅ΠΊΠΎΠΌΠ΅Π½Π΄Π°ΡΠΈΠΈ
- ΠΡΠΎΠ±ΠΎΠ΅ Π²Π½ΠΈΠΌΠ°Π½ΠΈΠ΅ ΡΠ»Π΅Π΄ΡΠ΅Ρ ΡΠ΄Π΅Π»ΠΈΡΡ ΠΏΡΠ΅Π΄Π²Π°ΡΠΈΡΠ΅Π»ΡΠ½ΠΎΠΌΡ ΠΎΠ±ΠΆΠΈΠ³Ρ ΡΠΈΡ
ΡΠΎΠ²ΠΎΠ³ΠΎ ΠΌΠ°ΡΠ΅ΡΠΈΠ°Π»Π° Π² ΠΏΠ΅ΡΠΈ Π΄Π»Ρ ΡΠ²ΠΎΠ±ΠΎΠ΄Π½ΠΎΠ³ΠΎ ΠΊΠ°Π»ΡΡΠΈΠ½Π°ΡΠΎΡΠ°, Π° ΡΠ°ΠΊΠΆΠ΅ ΡΠ»Π΅Π΄ΡΠ΅Ρ ΠΏΡΠΎΠ²Π΅ΡΡΠΈ ΠΊΠΎΡΡΠ΅Π»ΡΡΠΈΡ ΠΌΠ΅ΠΆΠ΄Ρ ΡΠΈΡ
ΡΠΎΠ²ΡΠΌ ΡΡΡΡΠ΅ΠΌ ΠΈ LSF ΠΊΠ»ΠΈΠ½ΠΊΠ΅ΡΠ° Π΄Π»Ρ ΡΡΡΡΠ°Π½Π΅Π½ΠΈΡ Π²ΡΡΠΎΠΊΠΎΠ³ΠΎ ΡΠΎΠ΄Π΅ΡΠΆΠ°Π½ΠΈΡ ΡΠ²ΠΎΠ±ΠΎΠ΄Π½ΠΎΠΉ ΠΈΠ·Π²Π΅ΡΡΠΈ.
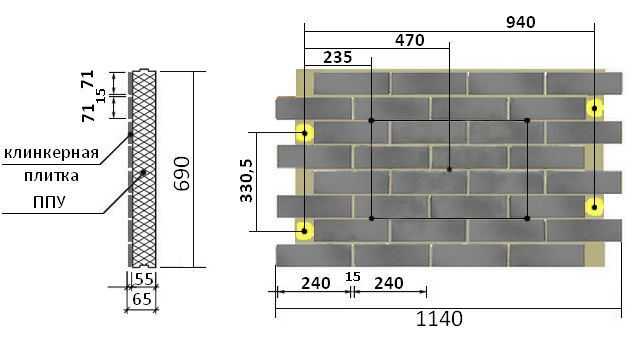
ΠΠΠΠΠΠΠΠ ΠΠΠ‘Π’Π¬
- ΠΠ²ΡΠΎΡ Π²ΡΡΠ°ΠΆΠ°Π΅Ρ Π±Π»Π°Π³ΠΎΠ΄Π°ΡΠ½ΠΎΡΡΡ ΠΎΡΠ΄Π΅Π»Ρ Ρ
ΠΈΠΌΠΈΡΠ΅ΡΠΊΠΎΠ³ΠΎ ΠΌΠ°ΡΠΈΠ½ΠΎΡΡΡΠΎΠ΅Π½ΠΈΡ Π£ΠΌΠ°ΡΡ ΠΠ»ΠΈ Π¨ΠΈΠ½ΠΊΠ°ΡΠΈ ΠΠΎΠ»ΠΈΡΠ΅Ρ
Π½ΠΈΡΠ΅ΡΠΊΠΎΠ³ΠΎ ΠΈΠ½ΡΡΠΈΡΡΡΠ° Π‘ΠΎΠΊΠΎΡΠΎ, Π° ΡΠ°ΠΊΠΆΠ΅ Π³Π»Π°Π²Π½ΠΎΠΌΡ ΠΈΠ½ΠΆΠ΅Π½Π΅ΡΡ ΠΏΡΠΎΠΈΠ·Π²ΠΎΠ΄ΡΡΠ²Π°, ΠΈΠ½ΠΆΠ΅Π½Π΅ΡΡ ΡΠ΅ΠΌΠ΅Π½ΡΠ½ΠΎΠ³ΠΎ Π·Π°Π²ΠΎΠ΄Π° Π‘ΠΎΠΊΠΎΡΠΎ ΠΠ°ΡΠΈΡΡ ΠΠ°Π΄Π° Π·Π° Π²ΡΡ ΠΏΠΎΠ΄Π΄Π΅ΡΠΆΠΊΡ ΠΈ ΠΏΠΎΠΎΡΡΠ΅Π½ΠΈΠ΅.
ΠΠ°ΡΠ°Π»ΠΎΠΆΠ½ΡΠ΅ Π½ΠΎΠΌΠ΅ΡΠ°
[1]Β Β | Π₯Π°ΠΉΠ±ΠΈΠ½. (2012). ΠΠΎΠ΄Π΅Π»ΠΈΡΠΎΠ²Π°Π½ΠΈΠ΅ ΠΈ ΠΎΠΏΡΠΈΠΌΠΈΠ·Π°ΡΠΈΡ ΠΏΡΠΎΡΠ΅ΡΡΠ° ΡΠΌΠ΅ΡΠ΅Π½ΠΈΡ ΡΠ΅ΠΌΠ΅Π½ΡΠ½ΠΎΠ³ΠΎ ΡΡΡΡΡ. Hindaw Publishing Corporation Mathematical Problem in Engineering, 2. |
[2]Β Β | Sanusi et al (2019). ΠΠ»ΠΈΡΠ½ΠΈΠ΅ ΡΠ²ΠΎΠ±ΠΎΠ΄Π½ΠΎΠΉ ΠΈΠ·Π²Π΅ΡΡΠΈ ΠΈ ΠΊΠΎΡΡΡΠΈΡΠΈΠ΅Π½ΡΠ° Π½Π°ΡΡΡΠ΅Π½ΠΈΡ Π½Π° ΠΈΠ·ΠΌΠ΅Π»ΡΡΠ°Π΅ΠΌΠΎΡΡΡ ΡΠ΅ΠΌΠ΅Π½ΡΠ½ΠΎΠ³ΠΎ ΠΊΠ»ΠΈΠ½ΠΊΠ΅ΡΠ°. |
[3]Β Β | markus, HM (2003). ΠΠΎΠ΄Π΅Π»ΠΈΡΠΎΠ²Π°Π½ΠΈΠ΅ ΠΏΡΠΎΡΠ΅ΡΡΠ° ΠΏΡΠΎΠΈΠ·Π²ΠΎΠ΄ΡΡΠ²Π° ΡΠ΅ΠΌΠ΅Π½ΡΠ° Π΄Π»Ρ ΠΈΠ·ΡΡΠ΅Π½ΠΈΡ Π²ΠΎΠ·ΠΌΠΎΠΆΠ½ΠΎΠ³ΠΎ Π²ΠΎΠ·Π΄Π΅ΠΉΡΡΠ²ΠΈΡ Π°Π»ΡΡΠ΅ΡΠ½Π°ΡΠΈΠ²Π½ΡΡ
Π²ΠΈΠ΄ΠΎΠ² ΡΠΎΠΏΠ»ΠΈΠ²Π°, ΡΠ°ΡΡΡ A.![]() |
[4]Β Β | Mohamed A. Aldieb, e. Π°. (2010). ΠΠ·ΠΌΠ΅Π½Π΅Π½ΠΈΠ΅ Ρ ΠΈΠΌΠΈΡΠ΅ΡΠΊΠΎΠ³ΠΎ ΡΠΎΡΡΠ°Π²Π° ΡΡΡΡΡ ΠΈ Π΅Π³ΠΎ Π²Π»ΠΈΡΠ½ΠΈΠ΅ Π½Π° ΠΏΡΠΎΡΠ΅ΡΡ ΠΊΠ»ΠΈΠ½ΠΊΠ΅ΡΠΎΠΎΠ±ΡΠ°Π·ΠΎΠ²Π°Π½ΠΈΡ β ΠΌΠΎΠ΄Π΅Π»ΠΈΡΠΎΠ²Π°Π½ΠΈΠ΅. |
[5]Β Β | Π‘Π°ΠΌΠΈΡΠ°, Π’. (2012). ΠΠΈΠ½Π΅ΡΠΈΠΊΠ° ΠΈ ΠΌΠ΅Ρ Π°Π½ΠΈΠ·ΠΌ Π³ΠΎΡΠ΅Π½ΠΈΡ ΠΊΠ»ΠΈΠ½ΠΊΠ΅ΡΠ°. ΠΠ°Π½ΠΈΡ: Π’Π΅Π»ΡΠΎΡ, Π‘. (2012). ΠΠΈΠ½Π΅ΡΠΈΠΊΠ° ΠΈ ΠΌΠ΅Ρ Π°Π½ΠΈΠ·ΠΌ ΠΊΠ»ΠΈΠ½ΠΊΠ΅ΡΠ°. ΠΊΠ³ ΠΡΠ½Π³Π±Ρ: Π’Π΅Ρ Π½ΠΈΡΠ΅ΡΠΊΠΈΠΉ ΡΠ½ΠΈΠ²Π΅ΡΡΠΈΡΠ΅Ρ ΠΠ΅. |
[6]Β Β | Sanusi et al, (2020). ΠΠ΅ΡΠΎΠΏΡΠΈΡΡΠΈΡ ΠΏΠΎ ΡΠ½Π΅ΡΠ³ΠΎΡΠ±Π΅ΡΠ΅ΠΆΠ΅Π½ΠΈΡ Π² ΠΏΠ΅ΡΠΈ Π΄Π»Ρ ΠΏΡΠΎΠΈΠ·Π²ΠΎΠ΄ΡΡΠ²Π° ΠΊΠ»ΠΈΠ½ΠΊΠ΅ΡΠ°. International Journal of Engineering Science and Invention, 64. |
[7]Β Β | Taylor and Francis Group. (2018). ΠΡΠΈΠ½ΡΠΈΠΏΡ ΠΈ ΠΏΡΠ°ΠΊΡΠΈΠΊΠ° ΡΠ΅Ρ Π½ΠΎΠ»ΠΎΠ³ΠΈΠΈ ΠΏΡΠΎΠΈΠ·Π²ΠΎΠ΄ΡΡΠ²Π° ΡΠ΅ΠΌΠ΅Π½ΡΠ°. ΠΠΎΠ½Π΄ΠΎΠ½: ΠΡΡΠΏΠΏΠ° Π’Π΅ΠΉΠ»ΠΎΡ ΠΈ Π€ΡΡΠ½ΡΠΈΡ. |
[8]Β Β | Π₯Π°ΠΉΠ±ΠΈΠ½. (2012). ΠΠΎΠ΄Π΅Π»ΠΈΡΠΎΠ²Π°Π½ΠΈΠ΅ ΠΈ ΠΎΠΏΡΠΈΠΌΠΈΠ·Π°ΡΠΈΡ ΠΏΡΠΎΡΠ΅ΡΡΠ° ΡΠΌΠ΅ΡΠ΅Π½ΠΈΡ ΡΠ΅ΠΌΠ΅Π½ΡΠ½ΠΎΠ³ΠΎ ΡΡΡΡΡ.![]() |
[9]Β Β | ΠΠΎΡ Π°ΠΌΠ΅Π΄ Π. ΠΠ»Π΄ΠΈΠ΅Π±, e. Π°. (2010). ΠΠ·ΠΌΠ΅Π½Π΅Π½ΠΈΠ΅ Ρ ΠΈΠΌΠΈΡΠ΅ΡΠΊΠΎΠ³ΠΎ ΡΠΎΡΡΠ°Π²Π° ΡΡΡΡΡ ΠΈ Π΅Π³ΠΎ Π²Π»ΠΈΡΠ½ΠΈΠ΅ Π½Π° ΠΏΡΠΎΡΠ΅ΡΡ ΠΊΠ»ΠΈΠ½ΠΊΠ΅ΡΠΎΠΎΠ±ΡΠ°Π·ΠΎΠ²Π°Π½ΠΈΡ β ΠΌΠΎΠ΄Π΅Π»ΠΈΡΠΎΠ²Π°Π½ΠΈΠ΅. |
[10]Β Β | ΠΡΠΎΠΌΡΡΠ»Π΅Π½Π½ΡΠΉ ΡΡΠ°Π½Π΄Π°ΡΡ ΠΠΈΠ³Π΅ΡΠΈΠΈ, Π‘ΡΠ°Π½Π΄Π°ΡΡ ΡΠ΅ΠΌΠ΅Π½ΡΠ°, ΡΡΡ. 9, ΠΠ·Π΄Π°Π½ΠΈΠ΅ ΠΎΡΠ³Π°Π½ΠΈΠ·Π°ΡΠΈΠΈ ΠΏΠΎ ΡΡΠ°Π½Π΄Π°ΡΡΠΈΠ·Π°ΡΠΈΠΈ ΠΠΈΠ³Π΅ΡΠΈΠΈ, ΠΠΎΠ½Π° ΠΡΡΠ΅ 7, ΠΠ±ΡΠ΄ΠΆΠ°, ΠΠΈΠ³Π΅ΡΠΈΡ. |
[11]Β Β | (CCNN, 2004) Π£ΡΠ΅Π±Π½ΠΎΠ΅ ΠΏΠΎΡΠΎΠ±ΠΈΠ΅ ΠΏΠΎ ΡΠ»ΠΈΡΠΎΠ²Π°Π½ΠΈΡ ΡΠ΅ΠΌΠ΅Π½ΡΠ°, ΡΡΡ. 11β13. |
[12]Β Β | (CCNN, 2003) ΠΡΡΡ ΠΏΠΎ ΠΏΡΠΎΠΈΠ·Π²ΠΎΠ΄ΡΡΠ²Ρ ΡΠ΅ΠΌΠ΅Π½ΡΠ°, Π’Π΅Ρ Π½ΠΎΠ»ΠΎΠ³ΠΈΡ ΠΈΠ·ΠΌΠ΅Π»ΡΡΠ΅Π½ΠΈΡ, ΡΡΡ. 6-16. |
[13]Β Β | Nwokedi, 2014. ΠΡΡΠ»Π΅Π΄ΠΎΠ²Π°Π½ΠΈΠ΅ Π²Π»ΠΈΡΠ½ΠΈΡ ΡΠ²ΠΎΠ±ΠΎΠ΄Π½ΠΎΠΉ ΠΈΠ·Π²Π΅ΡΡΠΈ ΠΈ ΠΊΠΎΡΡΡΠΈΡΠΈΠ΅Π½ΡΠ° Π½Π°ΡΡΡΠ΅Π½ΠΈΡ ΠΈΠ·Π²Π΅ΡΡΡΡ Π½Π° ΠΈΠ·ΠΌΠ΅Π»ΡΡΠ°Π΅ΠΌΠΎΡΡΡ ΡΠ΅ΠΌΠ΅Π½ΡΠ½ΠΎΠ³ΠΎ ΠΊΠ»ΠΈΠ½ΠΊΠ΅ΡΠ°, Π½Π°ΡΡΠ½ΠΎ-ΠΈΡΡΠ»Π΅Π΄ΠΎΠ²Π°ΡΠ΅Π»ΡΡΠΊΠ°Ρ ΡΠ°Π±ΠΎΡΠ°. Π€Π΅Π΄Π΅ΡΠ°Π»ΡΠ½ΡΠΉ ΡΠ΅Ρ Π½ΠΎΠ»ΠΎΠ³ΠΈΡΠ΅ΡΠΊΠΈΠΉ ΡΠ½ΠΈΠ²Π΅ΡΡΠΈΡΠ΅Ρ, ΠΠΈΠ½Π½Π°. Π¨ΡΠ°Ρ ΠΠΈΠ³Π΅Ρ, ΠΠΈΠ³Π΅ΡΠΈΡ. |
[14]Β Β | Π₯Π°ΡΠΈΠΌ.![]() |
[15]Β Β | Π’ΠΎΠΊΠΈΠΎ. Π. (1999). ΠΠ»ΠΈΡΠ½ΠΈΠ΅ Ρ ΠΈΠΌΠΈΡΠ΅ΡΠΊΠΎΠ³ΠΎ ΡΠΎΡΡΠ°Π²Π° ΠΊΠ»ΠΈΠ½ΠΊΠ΅ΡΠ° Π½Π° ΡΠ½Π΅ΡΠ³ΠΎΠ΅ΠΌΠΊΠΎΡΡΡ ΠΈΠ·ΠΌΠ΅Π»ΡΡΠ΅Π½ΠΈΡ. Π€Π°ΠΊΡΠ»ΡΡΠ΅Ρ Π³ΡΠ°ΠΆΠ΄Π°Π½ΡΠΊΠΎΠ³ΠΎ ΡΡΡΠΎΠΈΡΠ΅Π»ΡΡΡΠ²Π°, ΠΠ»ΠΈΠΆΠ½Π΅Π²ΠΎΡΡΠΎΡΠ½ΡΠΉ ΡΠ΅Ρ Π½ΠΈΡΠ΅ΡΠΊΠΈΠΉ ΡΠ½ΠΈΠ²Π΅ΡΡΠΈΡΠ΅Ρ, 06531 ΠΠ½ΠΊΠ°ΡΠ°, Π’ΡΡΡΠΈΡ. ΠΡΡΠ»Π΅Π΄ΠΎΠ²Π°Π½ΠΈΡ ΡΠ΅ΠΌΠ΅Π½ΡΠ° ΠΈ Π±Π΅ΡΠΎΠ½Π° (29) 531-535. |
ΠΠ°ΡΠ΅ΡΡΠ²ΠΎ ΠΊΠ»ΠΈΠ½ΠΊΠ΅ΡΠ° Π·Π°Π²ΠΈΡΠΈΡ ΠΎΡ ΡΠΎΡΡΠ°Π²Π° ΡΡΡΡΡ.
ΠΠ°ΡΠ΅ΡΡΠ²ΠΎ ΠΊΠ»ΠΈΠ½ΠΊΠ΅ΡΠ° Π·Π°Π²ΠΈΡΠΈΡ ΠΎΡ ΡΠΎΡΡΠ°Π²Π° ΡΡΡΡΡ.
ΠΠΎΡΡΠ»Π°Π½Π΄ΡΠ΅ΠΌΠ΅Π½Ρ ΡΠ²Π»ΡΠ΅ΡΡΡ Π½Π°ΠΈΠ±ΠΎΠ»Π΅Π΅ ΡΠ°ΡΠΏΡΠΎΡΡΡΠ°Π½Π΅Π½Π½ΡΠΌ ΡΠΈΠΏΠΎΠΌ ΡΠ΅ΠΌΠ΅Π½ΡΠ° Π² ΠΌΠΈΡΠ΅. ΠΠ½ ΠΈΡΠΏΠΎΠ»ΡΠ·ΡΠ΅ΡΡΡ Π² ΠΎΡΠ½ΠΎΠ²Π½ΠΎΠΌ Π΄Π»Ρ ΠΈΠ·Π³ΠΎΡΠΎΠ²Π»Π΅Π½ΠΈΡ Π±Π΅ΡΠΎΠ½Π°, ΡΠ°ΡΡΠ²ΠΎΡΠ° ΠΈ ΡΠ΅ΠΌΠ΅Π½ΡΠ½ΠΎΠ³ΠΎ ΡΠ°ΡΡΠ²ΠΎΡΠ°. ΠΡΠΎΠΈΠ·Π²ΠΎΠ΄ΡΡΠ²ΠΎ ΠΏΠΎΡΡΠ»Π°Π½Π΄ΡΠ΅ΠΌΠ΅Π½ΡΠ° Π½Π°ΡΠΈΠ½Π°Π΅ΡΡΡ Ρ Π΄ΠΎΠ±ΡΡΠΈ ΠΈ ΠΏΠΎΡΠ»Π΅Π΄ΡΡΡΠ΅Π³ΠΎ ΠΈΠ·ΠΌΠ΅Π»ΡΡΠ΅Π½ΠΈΡ ΡΡΡΡΡ, Π²ΠΊΠ»ΡΡΠ°ΡΡΠ΅Π³ΠΎ ΠΈΠ·Π²Π΅ΡΡΠ½ΡΠΊ ΠΈ Π³Π»ΠΈΠ½Ρ, Π² ΠΌΠ΅Π»ΠΊΠΈΠΉ ΠΏΠΎΡΠΎΡΠΎΠΊ, Π½Π°Π·ΡΠ²Π°Π΅ΠΌΡΠΉ ΡΡΡΡΠ΅Π²ΠΎΠΉ ΠΌΡΠΊΠΎΠΉ, ΠΊΠΎΡΠΎΡΡΠΉ Π·Π°ΡΠ΅ΠΌ Π½Π°Π³ΡΠ΅Π²Π°Π΅ΡΡΡ Π΄ΠΎ ΡΠ΅ΠΌΠΏΠ΅ΡΠ°ΡΡΡΡ ΡΠΏΠ΅ΠΊΠ°Π½ΠΈΡ Π΄ΠΎ 1450Β Β°C Π² ΡΠ΅ΠΌΠ΅Π½ΡΠ½ΠΎΠΉ ΠΏΠ΅ΡΠΈ. Π ΡΡΠΎΠΌ ΠΏΡΠΎΡΠ΅ΡΡΠ΅ Ρ
ΠΈΠΌΠΈΡΠ΅ΡΠΊΠΈΠ΅ ΡΠ²ΡΠ·ΠΈ ΡΡΡΡΡ ΡΠ°Π·ΡΡΡΠ°ΡΡΡΡ, Π° Π·Π°ΡΠ΅ΠΌ ΡΠ΅ΠΊΠΎΠΌΠ±ΠΈΠ½ΠΈΡΡΡΡΡΡ Π² Π½ΠΎΠ²ΡΠ΅ ΡΠΎΠ΅Π΄ΠΈΠ½Π΅Π½ΠΈΡ. ΠΠΎΠ»ΡΡΠ΅Π½Π½ΡΠΉ ΠΊΠ»ΠΈΠ½ΠΊΠ΅Ρ (ΠΎΠΊΡΡΠ³Π»ΡΠ΅ ΡΠ·Π΅Π»ΠΊΠΈ Π΄ΠΈΠ°ΠΌΠ΅ΡΡΠΎΠΌ ΠΎΡ 1 ΠΌΠΌ Π΄ΠΎ 25 ΠΌΠΌ) ΠΈΠ·ΠΌΠ΅Π»ΡΡΠ°ΡΡ Π² ΠΌΠ΅Π»ΠΊΠΈΠΉ ΠΏΠΎΡΠΎΡΠΎΠΊ Π½Π° ΡΠ΅ΠΌΠ΅Π½ΡΠ½ΠΎΠΉ ΠΌΠ΅Π»ΡΠ½ΠΈΡΠ΅ ΠΈ ΡΠΌΠ΅ΡΠΈΠ²Π°ΡΡ Ρ Π³ΠΈΠΏΡΠΎΠΌ Π΄Π»Ρ ΠΏΠΎΠ»ΡΡΠ΅Π½ΠΈΡ ΡΠ΅ΠΌΠ΅Π½ΡΠ°. ΠΠ°ΡΠ΅ΠΌ ΠΏΠΎΡΠΎΡΠΊΠΎΠΎΠ±ΡΠ°Π·Π½ΡΠΉ ΡΠ΅ΠΌΠ΅Π½Ρ ΡΠΌΠ΅ΡΠΈΠ²Π°ΡΡ Ρ Π²ΠΎΠ΄ΠΎΠΉ ΠΈ Π·Π°ΠΏΠΎΠ»Π½ΠΈΡΠ΅Π»ΡΠΌΠΈ Π΄Π»Ρ ΠΏΠΎΠ»ΡΡΠ΅Π½ΠΈΡ Π±Π΅ΡΠΎΠ½Π°, ΠΊΠΎΡΠΎΡΡΠΉ ΠΈΡΠΏΠΎΠ»ΡΠ·ΡΠ΅ΡΡΡ Π² ΡΡΡΠΎΠΈΡΠ΅Π»ΡΡΡΠ²Π΅.
ΠΠ°ΡΠ΅ΡΡΠ²ΠΎ ΠΊΠ»ΠΈΠ½ΠΊΠ΅ΡΠ° Π·Π°Π²ΠΈΡΠΈΡ ΠΎΡ ΡΠΎΡΡΠ°Π²Π° ΡΡΡΡΡ. ΠΡΠ»ΠΈ ΠΈΡΡ ΠΎΠ΄Π½ΡΠ΅ ΠΌΠ°ΡΠ΅ΡΠΈΠ°Π»Ρ Π½Π΅ ΠΏΠΎΠ΄Ρ ΠΎΠ΄ΡΡ ΠΈΠ»ΠΈ ΡΠΌΠ΅ΡΠ°Π½Ρ Π½Π΅ΠΏΡΠ°Π²ΠΈΠ»ΡΠ½ΠΎ, Π·Π΄Π°Π½ΠΈΡ ΠΈ Π΄ΠΎΡΠΎΠ³ΠΈ, ΡΠ΄Π΅Π»Π°Π½Π½ΡΠ΅ ΠΈΠ· Π±Π΅ΡΠΎΠ½Π°, Π±ΡΠ΄ΡΡ ΠΈΠΌΠ΅ΡΡ Π½ΠΈΠ·ΠΊΡΡ ΠΏΡΠΎΡΠ½ΠΎΡΡΡ ΠΈ Π΄ΠΎΠ»Π³ΠΎΠ²Π΅ΡΠ½ΠΎΡΡΡ. ΠΠ΅Π΄Π°Π²Π½ΠΈΠ΅ ΠΏΡΠΈΠΌΠ΅ΡΡ ΠΌΠΎΠΆΠ½ΠΎ Π½Π°ΠΉΡΠΈ Π² ΡΠ°ΠΊΠΈΡ ΡΡΡΠ°Π½Π°Ρ , ΠΊΠ°ΠΊ ΠΠΈΡΠ°ΠΉ ΠΈ ΠΠ°ΡΠ°Ρ, Π³Π΄Π΅ ΡΡΡΠΎΠΈΡΠ΅Π»ΡΠ½ΡΠ΅ ΠΏΡΠΎΠ΅ΠΊΡΡ Π±ΡΠ»ΠΈ ΠΏΡΠΈΠΎΡΡΠ°Π½ΠΎΠ²Π»Π΅Π½Ρ, ΠΊΠΎΠ³Π΄Π° Π±ΡΠ»ΠΎ ΠΎΠ±Π½Π°ΡΡΠΆΠ΅Π½ΠΎ, ΡΡΠΎ ΠΈΡΠΏΠΎΠ»ΡΠ·ΡΠ΅ΡΡΡ Π½Π΅ΠΊΠ°ΡΠ΅ΡΡΠ²Π΅Π½Π½ΡΠΉ Π±Π΅ΡΠΎΠ½, ΠΈΠ·Π³ΠΎΡΠΎΠ²Π»Π΅Π½Π½ΡΠΉ ΠΈΠ· Π½Π΅ΠΊΠ°ΡΠ΅ΡΡΠ²Π΅Π½Π½ΠΎΠΉ ΡΠΌΠ΅ΡΠΈ.
ΠΠΎΡΠΊΠΎΠ»ΡΠΊΡ ΠΏΠΎΡΡΠΎΡΠ½Π½ΠΎΠ΅ ΠΊΠ°ΡΠ΅ΡΡΠ²ΠΎ ΠΊΠ»ΠΈΠ½ΠΊΠ΅ΡΠ° ΠΈΠΌΠ΅Π΅Ρ ΡΠ΅ΡΠ°ΡΡΠ΅Π΅ Π·Π½Π°ΡΠ΅Π½ΠΈΠ΅ Π΄Π»Ρ ΠΏΡΠΎΠΈΠ·Π²ΠΎΠ΄ΡΡΠ²Π° Π²ΡΡΠΎΠΊΠΎΠΏΡΠΎΡΠ½ΠΎΠ³ΠΎ Π±Π΅ΡΠΎΠ½Π°, ΡΡΠΎΠ±Ρ ΠΈΠ·Π±Π΅ΠΆΠ°ΡΡ ΡΠ°Π·ΡΡΡΠ΅Π½ΠΈΡ Π·Π΄Π°Π½ΠΈΠΉ, ΠΏΡΠΎΠΈΠ·Π²ΠΎΠ΄ΠΈΡΠ΅Π»ΠΈ ΡΠ΅ΠΌΠ΅Π½ΡΠ° Π²ΠΊΠ»Π°Π΄ΡΠ²Π°ΡΡ ΡΡΠ΅Π΄ΡΡΠ²Π° Π² Π½ΠΎΠ²ΡΠ΅ ΡΠ΅Ρ
Π½ΠΎΠ»ΠΎΠ³ΠΈΠΈ Π΄Π»Ρ ΡΠ»ΡΡΡΠ΅Π½ΠΈΡ ΠΏΡΠΎΡΠ΅ΡΡΠ°. Π Π½Π΅Π΄Π°Π²Π½Π΅ΠΉ ΡΡΠ°ΡΡΠ΅ Π² Cement International (verlagbt.de) ΠΎΠΏΠΈΡΡΠ²Π°Π΅ΡΡΡ, ΠΊΠ°ΠΊ ΡΠ΅ΠΌΠ΅Π½ΡΠ½Π°Ρ ΠΊΠΎΠΌΠΏΠ°Π½ΠΈΡ ΡΡΡΠ΅ΠΌΠΈΠ»Π°ΡΡ ΡΡΠ°Π±ΠΈΠ»ΠΈΠ·ΠΈΡΠΎΠ²Π°ΡΡ ΠΊΠ°ΡΠ΅ΡΡΠ²ΠΎ ΡΠ²ΠΎΠ΅ΠΉ ΡΡΡΡΠ΅Π²ΠΎΠΉ ΠΌΡΠΊΠΈ, ΡΡΠΎΠ±Ρ ΡΠ΅Π³ΡΠ»ΠΈΡΠΎΠ²Π°ΡΡ ΠΊΠ°ΡΠ΅ΡΡΠ²ΠΎ ΠΊΠ»ΠΈΠ½ΠΊΠ΅ΡΠ°.
Π‘ΡΠ°Π±ΠΈΠ»ΠΈΠ·Π°ΡΠΈΡ ΠΊΠ°ΡΠ΅ΡΡΠ²Π° ΡΡΡΠΎΠΉ ΠΌΡΠΊΠΈ Π΄Π»Ρ ΡΠ΅Π³ΡΠ»ΠΈΡΠΎΠ²Π°Π½ΠΈΡ ΠΊΠ°ΡΠ΅ΡΡΠ²Π° ΠΊΠ»ΠΈΠ½ΠΊΠ΅ΡΠ°
ΠΠΎΠΌΠΏΠ°Π½ΠΈΡ ΡΡΠΈΡΠ°Π»Π°, ΡΡΠΎ Π·Π° ΡΡΠ΅Ρ ΠΈΡΠΏΠΎΠ»ΡΠ·ΠΎΠ²Π°Π½ΠΈΡ Π²ΡΡΠΎΠΊΠΎΡΠ°ΡΡΠΎΡΠ½ΠΎΠ³ΠΎ ΠΎΠ½Π»Π°ΠΉΠ½-Π°Π½Π°Π»ΠΈΠ·Π° ΠΈ Π°Π²ΡΠΎΠΌΠ°ΡΠΈΠ·ΠΈΡΠΎΠ²Π°Π½Π½ΠΎΠ³ΠΎ ΠΊΠΎΠ½ΡΡΠΎΠ»Ρ ΠΎΠ½ΠΈ ΡΠΌΠΎΠ³ΡΡ ΠΏΡΠΎΠΈΠ·Π²ΠΎΠ΄ΠΈΡΡ Π±ΠΎΠ»Π΅Π΅ ΠΎΠ΄Π½ΠΎΡΠΎΠ΄Π½ΡΡ ΠΈ ΡΡΠ°Π±ΠΈΠ»ΡΠ½ΡΡ ΡΡΡΡΠ΅Π²ΡΡ ΠΌΡΠΊΡ. ΠΠ° ΡΡΠ΅Ρ ΡΠΌΠ΅Π½ΡΡΠ΅Π½ΠΈΡ ΠΈΠ·ΠΌΠ΅Π½ΡΠΈΠ²ΠΎΡΡΠΈ Ρ
ΠΈΠΌΠΈΡΠ΅ΡΠΊΠΎΠ³ΠΎ ΡΠΎΡΡΠ°Π²Π° ΡΡΡΡΡ ΠΈ ΠΏΠΎΠ΄Π΄Π΅ΡΠΆΠ°Π½ΠΈΡ ΡΡΠΎΠ³ΠΎ Ρ
ΠΈΠΌΠΈΡΠ΅ΡΠΊΠΎΠ³ΠΎ ΡΠΎΡΡΠ°Π²Π° Β«ΡΠ΅Π»Π΅Π²ΡΠΌΒ» Π² ΡΠΎΠΎΡΠ²Π΅ΡΡΡΠ²ΡΡΡΠΈΡ
ΡΠΎΠΎΡΠ½ΠΎΡΠ΅Π½ΠΈΡΡ
ΠΊΠ°ΡΠ΅ΡΡΠ²ΠΎ ΠΏΡΠΎΠΈΠ·Π²ΠΎΠ΄ΠΈΠΌΠΎΠ³ΠΎ ΡΠ΅ΠΌΠ΅Π½ΡΠ° ΠΎΡΡΠ°Π΅ΡΡΡ Π²ΡΡΠΎΠΊΠΈΠΌ ΠΈ ΡΡΠ°Π±ΠΈΠ»ΡΠ½ΡΠΌ. Π¦Π΅Π»Ρ ΠΊΠΎΠΌΠΏΠ°Π½ΠΈΠΈ ΡΠΎΡΡΠΎΡΠ»Π° Π² ΡΠΎΠΌ, ΡΡΠΎΠ±Ρ ΡΠΌΠ΅Π½ΡΡΠΈΡΡ ΡΡΠ°Π½Π΄Π°ΡΡΠ½ΠΎΠ΅ ΠΎΡΠΊΠ»ΠΎΠ½Π΅Π½ΠΈΠ΅ ΠΈΠ·ΠΌΠ΅Π½ΡΠΈΠ²ΠΎΡΡΠΈ ΠΈΡ
ΡΡΡΠΎΠΉ ΠΌΡΠΊΠΈ Π½Π° 40%, ΠΈΡΠΏΠΎΠ»ΡΠ·ΡΡ Π² ΠΊΠ°ΡΠ΅ΡΡΠ²Π΅ ΡΡΠ°Π»ΠΎΠ½Π° ΠΏΠΎΠΊΠ°Π·Π°ΡΠ΅Π»Ρ ΠΊΠ°ΡΠ΅ΡΡΠ²Π° ΠΏΠΎΠ΄ Π½Π°Π·Π²Π°Π½ΠΈΠ΅ΠΌ Β«ΠΠΎΡΡΡΠΈΡΠΈΠ΅Π½Ρ Π½Π°ΡΡΡΠ΅Π½ΠΈΡ ΠΈΠ·Π²Π΅ΡΡΠΈΒ». ΠΠ»Ρ Π΄ΠΎΡΡΠΈΠΆΠ΅Π½ΠΈΡ ΡΠ²ΠΎΠ΅ΠΉ ΡΠ΅Π»ΠΈ ΠΊΠΎΠΌΠΏΠ°Π½ΠΈΡ ΡΡΡΠ°Π½ΠΎΠ²ΠΈΠ»Π° Π΄Π²Π΅ Π½ΠΎΠ²ΡΠ΅ ΡΠΈΡΡΠ΅ΠΌΡ Π°Π½Π°Π»ΠΈΠ·Π°: Π»Π°Π±ΠΎΡΠ°ΡΠΎΡΠ½ΡΡ ΡΠΈΡΡΠ΅ΠΌΡ ΡΠ΅Π½ΡΠ³Π΅Π½ΠΎΠ²ΡΠΊΠΎΠ³ΠΎ ΡΠ»ΡΠΎΡΠ΅ΡΡΠ΅Π½ΡΠ½ΠΎΠ³ΠΎ Π°Π½Π°Π»ΠΈΠ·Π° (XRF) ΠΈ ΠΎΠ½Π»Π°ΠΉΠ½-ΡΠΈΡΡΠ΅ΠΌΡ Π±ΡΡΡΡΠΎΠ³ΠΎ Π³Π°ΠΌΠΌΠ°-Π½Π΅ΠΉΡΡΠΎΠ½Π½ΠΎ-Π°ΠΊΡΠΈΠ²Π°ΡΠΈΠΎΠ½Π½ΠΎΠ³ΠΎ Π°Π½Π°Π»ΠΈΠ·Π° (PGNAA).
ΠΠ»ΠΈΠ΅Π½Ρ ΠΈΡΠΏΠΎΠ»ΡΠ·ΡΠ΅Ρ ΡΡΠΈ Π²ΠΈΠ΄Π° ΡΡΡΡΡ: ΠΈΠ·Π²Π΅ΡΡΠ½ΡΠΊ, Π³Π»ΠΈΠ½Ρ ΠΈ ΠΌΠ΅ΡΠ³Π΅Π»Ρ Π² ΠΏΡΠΎΡΠ΅ΡΡΠ΅ ΠΏΡΠ΅Π΄Π²Π°ΡΠΈΡΠ΅Π»ΡΠ½ΠΎΠ³ΠΎ ΡΠΌΠ΅ΡΠΈΠ²Π°Π½ΠΈΡ. Π‘ΡΡΡΠ΅ ΠΈΠ·ΠΌΠ΅Π»ΡΡΠ°Π΅ΡΡΡ ΠΎΡΠ΄Π΅Π»ΡΠ½ΠΎ ΠΈ ΠΎΡΠ±ΠΈΡΠ°Π΅ΡΡΡ Π²ΡΡΡΠ½ΡΡ ΠΊΠ°ΠΆΠ΄ΡΠ΅ Π΄Π²Π° ΡΠ°ΡΠ°. ΠΠ±ΡΠ°Π·ΡΡ Π°Π½Π°Π»ΠΈΠ·ΠΈΡΡΡΡΡΡ Ρ ΠΏΠΎΠΌΠΎΡΡΡ ΡΠΈΡΡΠ΅ΠΌΡ XRF, ΠΈ ΡΠ°ΡΡΡΠΈΡΡΠ²Π°ΡΡΡΡ ΡΠΎΠΎΡΠ²Π΅ΡΡΡΠ²ΡΡΡΠΈΠ΅ ΠΏΡΠΎΠΏΠΎΡΡΠΈΠΈ ΠΏΡΠ΅Π΄Π²Π°ΡΠΈΡΠ΅Π»ΡΠ½ΠΎΠΉ ΡΠΌΠ΅ΡΠΈ Π΄Π»Ρ Π΄ΠΎΡΡΠΈΠΆΠ΅Π½ΠΈΡ ΡΠ΅Π»Π΅Π²ΠΎΠ³ΠΎ ΠΊΠ°ΡΠ΅ΡΡΠ²Π° ΠΏΡΠ΅Π΄Π²Π°ΡΠΈΡΠ΅Π»ΡΠ½ΠΎΠΉ ΡΠΌΠ΅ΡΠΈ. ΠΠ°ΡΠ΅ΠΌ ΡΡΠΈ Π²ΠΈΠ΄Π° ΡΡΡΡΡ Π·Π°Π³ΡΡΠΆΠ°ΡΡΡΡ Π² ΠΊΡΡΡ ΠΏΡΠ΅Π΄Π²Π°ΡΠΈΡΠ΅Π»ΡΠ½ΠΎΠ³ΠΎ ΡΠΌΠ΅ΡΠΈΠ²Π°Π½ΠΈΡ. ΠΠ°ΡΠ΅ΠΌ ΠΏΡΠ΅Π΄Π²Π°ΡΠΈΡΠ΅Π»ΡΠ½ΠΎ ΡΠΌΠ΅ΡΠ°Π½Π½ΡΠΉ ΠΌΠ°ΡΠ΅ΡΠΈΠ°Π» ΡΡΠΈΠ»ΠΈΠ·ΠΈΡΡΠ΅ΡΡΡ ΠΈ ΠΏΠΎΠΌΠ΅ΡΠ°Π΅ΡΡΡ Π² ΠΎΠ΄ΠΈΠ½ ΠΈΠ· ΡΡΠ΅Ρ
Π±ΡΠ½ΠΊΠ΅ΡΠΎΠ² Π΄Π»Ρ ΡΡΡΡΡ ΠΏΠ΅ΡΠ΅Π΄ ΡΡΡΡΠ΅Π²ΠΎΠΉ ΠΌΠ΅Π»ΡΠ½ΠΈΡΠ΅ΠΉ. ΠΠ·Π²Π΅ΡΡΠ½ΡΠΊ Π²ΡΡΠΎΠΊΠΎΠ³ΠΎ ΠΊΠ°ΡΠ΅ΡΡΠ²Π° ΠΈ ΠΆΠ΅Π»Π΅Π·Π½Π°Ρ ΡΡΠ΄Π° Π½Π°Ρ
ΠΎΠ΄ΡΡΡΡ, ΡΠΎΠΎΡΠ²Π΅ΡΡΡΠ²Π΅Π½Π½ΠΎ, Π² Π΄Π²ΡΡ
Π΄ΡΡΠ³ΠΈΡ
Π±ΡΠ½ΠΊΠ΅ΡΠ°Ρ
. ΠΠ·Π²Π΅ΡΡΠ½ΡΠΊ ΠΈΡΠΏΠΎΠ»ΡΠ·ΡΠ΅ΡΡΡ Π΄Π»Ρ ΠΊΠΎΡΡΠ΅ΠΊΡΠΈΡΠΎΠ²ΠΊΠΈ ΠΊΠΎΡΡΡΠΈΡΠΈΠ΅Π½ΡΠ° Π½Π°ΡΡΡΠ΅Π½ΠΈΡ ΠΈΠ·Π²Π΅ΡΡΡΡ (LSF), Π° ΠΆΠ΅Π»Π΅Π·Π½Π°Ρ ΡΡΠ΄Π° β Π΄Π»Ρ ΠΊΠΎΡΡΠ΅ΠΊΡΠΈΡΠΎΠ²ΠΊΠΈ ΠΊΠ°ΠΊ ΠΌΠΎΠ΄ΡΠ»Ρ ΠΊΡΠ΅ΠΌΠ½Π΅Π·Π΅ΠΌΠ° (SM), ΡΠ°ΠΊ ΠΈ ΠΌΠΎΠ΄ΡΠ»Ρ Π³Π»ΠΈΠ½ΠΎΠ·Π΅ΠΌΠ° (AM). ΠΠ²ΡΠΎΠΌΠ°ΡΠΈΡΠ΅ΡΠΊΠΈΠΉ ΠΏΡΠΎΠ±ΠΎΠΎΡΠ±ΠΎΡΠ½ΠΈΠΊ ΠΏΠΎΡΠ»Π΅ ΠΌΠ΅Π»ΡΠ½ΠΈΡΡ ΠΊΠ°ΠΆΠ΄ΡΠΉ ΡΠ°Ρ ΠΎΡΠ±ΠΈΡΠ°Π΅Ρ ΠΏΡΠΎΠ±Ρ ΡΡΡΠΎΠΉ ΠΌΡΠΊΠΈ, Π° Π·Π°ΡΠ΅ΠΌ ΠΏΠ΅ΡΠ΅Π΄Π°Π΅Ρ ΠΈΡ
Π² Π»Π°Π±ΠΎΡΠ°ΡΠΎΡΠΈΡ ΠΏΠΎ ΡΠΈΡΡΠ΅ΠΌΠ΅ Π²ΠΎΠ·Π΄ΡΡ
ΠΎΠ²ΠΎΠ΄ΠΎΠ². ΠΠ΅ΡΠ΅Π΄ ΡΡΡΠ°Π½ΠΎΠ²ΠΊΠΎΠΉ ΠΎΠ½Π»Π°ΠΉΠ½-Π°Π½Π°Π»ΠΈΠ·Π°ΡΠΎΡΠ° ΠΎΠ±ΡΠ°Π·ΡΡ Π°Π½Π°Π»ΠΈΠ·ΠΈΡΠΎΠ²Π°Π»ΠΈΡΡ Π² Π»Π°Π±ΠΎΡΠ°ΡΠΎΡΠΈΠΈ, Π·Π°ΡΠ΅ΠΌ ΡΠ°ΡΡΡΠΈΡΡΠ²Π°Π»ΠΈΡΡ ΠΏΡΠΎΠΏΠΎΡΡΠΈΠΈ ΡΠΌΠ΅ΡΠΈ ΠΈ Π²Π½ΠΎΡΠΈΠ»ΠΈΡΡ ΠΊΠΎΡΡΠ΅ΠΊΡΠΈΠ²Ρ Π² ΡΡΡΡΠ΅Π²ΡΡ ΡΠΌΠ΅ΡΡ β Π²ΡΠ΅ ΡΡΠΎ Π²ΡΠΏΠΎΠ»Π½ΡΠ»ΠΎΡΡ Π²ΡΡΡΠ½ΡΡ. ΠΠ°Π΄Π΅ΡΠΆΠΊΠ° Π²ΠΎ Π²ΡΠ΅ΠΌΠ΅Π½ΠΈ Π΄Π»Ρ ΠΏΠΎΠ΄Π³ΠΎΡΠΎΠ²ΠΊΠΈ ΠΈ Π°Π½Π°Π»ΠΈΠ·Π° ΠΏΡΠΎΠ± Π² ΡΠΎΡΠ΅ΡΠ°Π½ΠΈΠΈ Ρ Π²ΠΎΠ·ΠΌΠΎΠΆΠ½ΠΎΡΡΡΡ ΠΎΡΠΈΠ±ΠΊΠΈ Π² ΠΏΡΠΎΠ±Π΅ Π·Π°ΡΡΡΠ΄Π½ΡΠ»Π° ΠΎΠΏΡΠΈΠΌΠΈΠ·Π°ΡΠΈΡ ΠΊΠΎΠ½ΡΡΠΎΠ»Ρ ΠΏΡΠΈ ΠΈΠ·ΠΌΠ΅Π½Π΅Π½ΠΈΠΈ ΠΈΡΡ
ΠΎΠ΄Π½ΡΡ
ΠΌΠ°ΡΠ΅ΡΠΈΠ°Π»ΠΎΠ².
Π£Π»ΡΡΡΠ΅Π½ΠΈΠ΅ ΡΠ΅Ρ Π½ΠΎΠ»ΠΎΠ³ΠΈΡΠ΅ΡΠΊΠΎΠ³ΠΎ ΠΏΡΠΎΡΠ΅ΡΡΠ°
ΠΠ»Ρ ΡΡΠΎΠ²Π΅ΡΡΠ΅Π½ΡΡΠ²ΠΎΠ²Π°Π½ΠΈΡ ΡΠ΅Ρ
Π½ΠΎΠ»ΠΎΠ³ΠΈΡΠ΅ΡΠΊΠΎΠ³ΠΎ ΠΏΡΠΎΡΠ΅ΡΡΠ° ΠΈ ΡΠΈΡΡΠ΅ΠΌΡ ΡΠΏΡΠ°Π²Π»Π΅Π½ΠΈΡ Π½Π° Π·Π°Π²ΠΎΠ΄Π΅ Π±ΡΠ» ΡΡΡΠ°Π½ΠΎΠ²Π»Π΅Π½ ΠΎΠ½Π»Π°ΠΉΠ½-Π°Π½Π°Π»ΠΈΠ·Π°ΡΠΎΡ ΡΠ»Π΅ΠΌΠ΅Π½ΡΠΎΠ² ΠΏΠΎΠΏΠ΅ΡΠ΅ΡΠ½ΠΎΠ³ΠΎ ΠΊΠΎΠ½Π²Π΅ΠΉΠ΅ΡΠ° Π½Π° ΠΎΡΠ½ΠΎΠ²Π΅ Π±ΡΡΡΡΠΎΠ³ΠΎ Π³Π°ΠΌΠΌΠ°-Π½Π΅ΠΉΡΡΠΎΠ½Π½ΠΎ-Π°ΠΊΡΠΈΠ²Π°ΡΠΈΠΎΠ½Π½ΠΎΠ³ΠΎ Π°Π½Π°Π»ΠΈΠ·Π° (PGNAA) Π² ΡΠΎΡΠ΅ΡΠ°Π½ΠΈΠΈ Ρ ΠΏΡΠΎΠ³ΡΠ°ΠΌΠΌΠ½ΡΠΌ ΠΎΠ±Π΅ΡΠΏΠ΅ΡΠ΅Π½ΠΈΠ΅ΠΌ Π΄Π»Ρ Π°Π²ΡΠΎΠΌΠ°ΡΠΈΡΠ΅ΡΠΊΠΎΠ³ΠΎ ΡΠΌΠ΅ΡΠΈΠ²Π°Π½ΠΈΡ ΡΡΡΡΡ ΠΏΠΎΡΠ»Π΅ ΠΊΠΎΡΡΠ΅ΠΊΡΠΈΡΡΡΡΠΈΡ
Π±ΡΠ½ΠΊΠ΅ΡΠΎΠ², Π½ΠΎ ΠΏΠ΅ΡΠ΅Π΄ ΡΡΡΡΠ΅Π²ΠΎΠΉ ΠΌΠ΅Π»ΡΠ½ΠΈΡΠ΅ΠΉ. ΠΠΎΡΠΊΠΎΠ»ΡΠΊΡ PGNAA ΡΠ²Π»ΡΠ΅ΡΡΡ ΠΏΠΎΠ»Π½ΠΎΡΡΡΡ ΠΏΡΠΎΠ½ΠΈΠΊΠ°ΡΡΠ΅ΠΉ ΡΠ΅Ρ
Π½ΠΎΠ»ΠΎΠ³ΠΈΠ΅ΠΉ Π°Π½Π°Π»ΠΈΠ·Π°, ΠΎΠ½Π»Π°ΠΉΠ½-Π°Π½Π°Π»ΠΈΠ·Π°ΡΠΎΡ ΠΏΡΠ΅Π΄ΠΎΡΡΠ°Π²Π»ΡΠ΅Ρ ΠΏΠΎΠΌΠΈΠ½ΡΡΠ½ΡΠ΅ ΡΠ΅Π·ΡΠ»ΡΡΠ°ΡΡ Π°Π½Π°Π»ΠΈΠ·Π° Π²ΡΠ΅Π³ΠΎ ΠΏΠΎΡΠΎΠΊΠ° ΠΌΠ°ΡΠ΅ΡΠΈΠ°Π»Π°, Π° Π½Π΅ ΡΠΎΠ»ΡΠΊΠΎ Π°Π½Π°Π»ΠΈΠ·Π° ΠΏΠΎΠ²Π΅ΡΡ
Π½ΠΎΡΡΠΈ. Π Π΅Π·ΡΠ»ΡΡΠ°ΡΡ Π²ΡΡΠΎΠΊΠΎΡΠ°ΡΡΠΎΡΠ½ΠΎΠ³ΠΎ Π°Π½Π°Π»ΠΈΠ·Π° ΠΊΠ°ΠΆΠ΄ΡΡ ΠΌΠΈΠ½ΡΡΡ ΠΏΠ΅ΡΠ΅Π΄Π°ΡΡΡΡ Π² ΠΏΡΠΎΠ³ΡΠ°ΠΌΠΌΠ½ΠΎΠ΅ ΠΎΠ±Π΅ΡΠΏΠ΅ΡΠ΅Π½ΠΈΠ΅ Π°Π²ΡΠΎΠΌΠ°ΡΠΈΡΠ΅ΡΠΊΠΎΠ³ΠΎ ΡΠΌΠ΅ΡΠΈΠ²Π°Π½ΠΈΡ, Π³Π΄Π΅ ΡΠ°ΡΡΡΠΈΡΡΠ²Π°ΡΡΡΡ Π½ΠΎΠ²ΡΠ΅ ΡΠΎΠΎΡΠ½ΠΎΡΠ΅Π½ΠΈΡ ΡΠΌΠ΅ΡΠΈΠ²Π°Π½ΠΈΡ. ΠΡΠΎΠ³ΡΠ°ΠΌΠΌΠ½ΠΎΠ΅ ΠΎΠ±Π΅ΡΠΏΠ΅ΡΠ΅Π½ΠΈΠ΅ ΠΈΠ½ΡΠ΅Π³ΡΠΈΡΠΎΠ²Π°Π½ΠΎ Ρ ΡΠΈΡΡΠ΅ΠΌΠΎΠΉ ΡΠΏΡΠ°Π²Π»Π΅Π½ΠΈΡ, ΠΈ Π·Π°Π΄Π°Π½Π½ΡΠ΅ Π·Π½Π°ΡΠ΅Π½ΠΈΡ Π²Π΅ΡΠΎΠ²ΠΎΠ³ΠΎ Π΄ΠΎΠ·Π°ΡΠΎΡΠ° Π°Π²ΡΠΎΠΌΠ°ΡΠΈΡΠ΅ΡΠΊΠΈ ΠΊΠΎΡΡΠ΅ΠΊΡΠΈΡΡΡΡΡΡ ΠΊΠ°ΠΆΠ΄ΡΡ ΠΌΠΈΠ½ΡΡΡ.