Cостав арболита: пропорции, химдобавки, технология изготовления
Общая характеристика арболита
Арболит – строительный материал, являющийся разновидностью легкого бетона, в нашей стране еще недостаточно широко распространен. В то время как за границей он существует под названиями дюризол и велокс и служит теплоизоляционным и конструктивно – теплоизоляционным материалом.
Основу арболита составляет древесный заполнитель и цемент. Его не следует путать с опилкобетоном, потому что щепа для него изготавливается специально и имеет свою фракцию и геометрию. Эти особенности утверждены ГОСТОМ 19222-84 «Арболит и изделия из него». Изделия из этого материала производят в виде блоков, плит, панелей.
Изделия из арболита классифицируют, в зависимости от назначения:
- для теплоизоляции и конструктивной теплоизоляции;
- армирования – армированные и неармированные;
- наружного профиля – гладкие и из сложного профиля;
- отделки поверхности – фактурные и нефактурные.
Арболит разделяется в зависимости от марок: 5; 10; 15; 25; 35; 50. Марки означают прочность арболитовых блоков, в зависимости от их предназначения. Теплоизоляционный имеет плотность до 500 кг/м3, конструкционный – плотность свыше 500 до 850 кг/м3. К теплоизоляционному относится арболит М 5,М 10, М15; к конструктивному М 25, М 35, М50.
Арболит используется при возведении жилых, гражданских, производственных зданий не более двух этажей, в качестве наружных несущих конструкций и внутренних стен помещений, теплоизоляции.
Преимущества и недостатки арболита
- высокий уровень тепло и звукоизоляции;
- высокая пожароустойчивость;
- устойчив к гниению;
- экономичен и недорог в строительстве;
- достаточно прочен, при нагрузке не ломается, а только продавливается. экологически чистый материал;
- в нем надежно крепятся гвозди, шурупы без дополнительного применения деревянных основ.
Однако, арболитовые конструкции без применения пароизоляции допущены к эксплуатации только в условиях сухого и нормального влажностного режима. При относительной влажности воздуха внутри помещения более 60% стены из него должны быть защищены пароизоляционным материалом.
Арболит не применяют для строительства цокольных этажей, карнизов, стен подвалов. Арболит следует защищать от атмосферных осадков путем гидрофобной окраски.
Состав арболита
Арболит изготавливается из древесного заполнителя, минерализатора, химических добавок и воды.
Органические составляющие
В качестве древесного наполнителя используют отходы древесины (сосна, ель, пихта, береза, осина, тополь) камыш, костру конопли, льна. Наиболее используемым древесным составом является деревянная щепа или дробленка и древесная стружка в соотношении 1:1 или 1:2. Вместо опилок можно использовать конопляные стебли или костру льна. Костру льна, из-за содержания в ней сахаров, разрушающих цемент, необходимо предварительно погрузить в известковое молоко (расход 50 кг извести на 200 кг костры) и выдержать 1-2 дня в куче. Другим способом является — выдерживание костры конопли, льна на открытом воздухе в течение 3-4 месяцев, тогда арболитовые блоки будут соответствовать показателям прочности. Форма костры имеет важное значение – она должна быть игольчатой длиной от 15 до 25 мм, шириной в 2-5 мм.
Минеральные вяжущие составляющие
Минерализатором в составе арболита выступает портландцемент 400, 500 или более высоких марок. Его расход зависит от его марки заполнителя арболита.
Обычно расход цемента рассчитывают следующим образом: для приготовления 1м3 арболита марки 15, необходимо умножить его значение на на коэффициент 17, например, 15 х 17 = 255 кг.
Химические составляющие арболита
Технические и строительные свойства арболита определяются химическими добавками. Их применение обязательно вне зависимости от климатических условий, в которых будет сооружаться здание из арболита. Именно химические вещества позволят использовать любой древесный наполнитель без предварительной обработки и выдержки, благодаря их способности нейтрализовать сахара.
В производстве арболита используют следующие химические добавки: хлористый кальций, гашеная известь, сернокислый алюминий, растворимое стекло. Наиболее эффективными являются хлористый кальций и алюминий. Сернокислый алюминий в соединении с сахарами нейтрализует их, обеспечивая возрастание прочности арболита.
Общее количество химических добавок в 1 м3 арболита составляет 2-4 % от общего веса цемента (около 6-12 кг). Добавки применяют как отдельно, так и смешивая алюминий с хлористым кальцием в пропорции 1:1, либо соединяя гашеную известь и растворимое стекло (1:1). Перед соединением с арболитовой смесью эти добавки необходимо растворить в воде.
Необходимые пропорции добавок зависят от вида арболита. Для арболитовых блоков марки 30 соотношение добавок следующее: сернокислый алюминий и хлористый кальций (1:1) в пропорции 4% от веса цемента; сернокислый натрий и хлористый кальций (1:1) в объеме 4% от веса цемента; сернокислый натрий и хлористый алюминий (1:1) в пропорции 2% от веса цемента; хлористый алюминий и хлористый кальций (1:1) в пропорции 4% от веса цемента.
Для арболитовой смеси марки 35 хлористый кальций добавляют в пропорции 2% от всей массы цемента. Использование хлористого кальция повышает прочность арболита. Для этого применяется жидкое стекло — силикат натрия или кальция, растворенные в горячей воде в количестве 8—10 кг на 1 м3 арболита.
Технология изготовления арболита
Производственная схема содержит следующие стадии:
- Дробление и придание необходимой формы заполнителю.
- Предварительная обработка органического заполнителя химическими составами.
- Дозирование составляющих компонентов для арболитовой массы.
- Подготовка арболитовой смеси.
- Формирование арболитовых блоков.
Дробление и придание необходимой формы заполнителю.
Перед дроблением куски и отходы древесины складываются в кучи и выдерживаются под навесом около месяца при положительной температуре. Затем эти отходы необходимо превратить в щепу на специальных машинах.
Отходы от деревопереработки, лесопиления подаются на приемную площадку, там они складируются, потом направляются в принимающую воронку рубильного механизма (ДУ-2). Для измельчения древесины рекомендуют пользоваться барабанной рубительной машиной, имеющей широкий спектр применения. Она может обработать практически каждый тип древесных отходов — рейки, кругляки, горбыль, обрезки, отторцовку, кривоствольную древесину. Обработанная таким образом щепа направляется в бункер, а затем идет в молотковую дробильную машину (ДМ-1), после этого древесная дробленка отправляется на вибрационный грохот, в целях отсеивания отходов и слишком крупных частиц.
На выходе дробленка представляет собой фракции древесины игольчатого или пластинчатого вида длиной от 2 до 20 мм, шириной от 2 до 5 мм, толщиной не больше 5 мм.
Предварительная обработка органического заполнителя химическими составами
Измельченная щепа с необходимым гранулометрическим составом направляется через промежуточный бункер в бак с водой для вымачивания и удаления, вредных для производства сахаров и веществ. Туда же направляют хлорид кальция. Вымачивание щепы при гидромодуле 1:10 продолжается 6 часов при температурном режиме 20°С. Применение предварительной гидротермической обработки улучшает физико-механические качества арболита. В воде древесина разбухает и этот процесс происходит до насыщения влагой волокна на 30%, при этом объем древесины и отдельные ее составляющие увеличиваются.
Дозирование составляющих компонентов для арболитовой массы
Важным условием однородности состава арболитовой массы и ее высокой стабильности является точное дозирование и качественное смешивание всех компонентов. Древесную щепу дозируют с помощью объемно – весового способа, с учетом коррекции насыпной плотности материала. Дробленке перед подачей на дозирование нужно иметь положительную температуру.
Для дозирования воды и химических добавок (хлорида кальция) используют автоматические дозаторы турбинного типа, работающие в цикличном либо непрерывном режиме. Возможен вариант дозирования добавок с помощью весового дозатора воды. При расчете дозировки воды и химических наполнителей учитывается влажность органического заполнителя и, соответственно, корректируются объемы добавляемой жидкости. Расчет доз цемента производится с помощью автоматических весовых дозаторов.
Загрузка и дозирование составляющих арболитовой смеси должна идти в следующей последовательности:
1) Древесный органический заполнитель.
2) Цемент.
3) Вода или водный раствор химических компонентов, регулируемый через расходомер.
4) Химические добавки, поступающие в течение всего процесса.
Подготовка арболитовой смеси
После вымачивания, дробленные деревянные фракции направляют в циклический смесительный механизм, являющийся бетономешалкой с принудительным действием. В смеситель подают из дозаторов вяжущие компоненты, воду, химические добавки. Там происходит смешивание всех составляющих до однородного состояния. Во время смешения вводят хлорид кальция с помощью метода дождевания и дозирования из перфорированных труб-распылителей. Данный способ точно вводит хлорид кальция и равномерно распределяет его, улучшая технологические свойства арболита. Все составляющие примешиваются в течение 10 минут. После смешивания из массы можно формировать арболитовые блоки.
Формирование арболитовых блоков
Приготовленная арболитовая смесь направляется через специальные бункеры-укладчики в металлические формы или разборные деревянные формы, там смесь утрамбовывается и уплотняется, с помощью пресса, силового вибропроката и виброштампования. Чтобы арболит, произведенный на стандартном портландцементе , достиг 50% прочности от марки, его выдерживают в формах 5 суток при температуре 15° С и относительной влажностью воздуха около 60-70%.
Можно также залить арболитовую массу в формы и выдержать ее в течение 24 часов при температуре 40° С и аналогичной влажностью. В таких условиях блоки выдерживаются 2 суток с сохранением постоянной температуры не ниже 15° С.
Далее происходит распалубка смеси на блоки, панели и изделия поступают на склад.
Наряду с описанной выше технологией, существует вариант приготовления арболитовых блоков, с древесным заполнителем из одубины — щепы древесины дуба, являющейся отходом производства экстрактов дуба.
Процесс производства арболита из одубины более прост, так как данный заполнитель не нуждается в дополнительном измельчении. Также существует технология изготовления арболита из высокопрочного гипса, которая гораздо проще, чем на базе цемента. Это происходит из-за того что гипс, взаимодействуя с водой, образует нейтральную среду, а не щелочную, которая вызывает выделение сахара из дерева. Так как нет факторов, снижающих отвердение цемента, то использование минерализующих добавок в производстве не требуется. Технология упрощается еще и в связи с тем, что используя высокопрочный гипс, можно применять дробленку гораздо крупнее по фракции, прошедшую только одно измельчение в рубильном механизме.
Таким образом, производство арболита на основе гипса менее затратное, чем при использовании цемента.
Щепа для арболита своими руками Арболит: недостатки и достоинства строительного материала Достоинства и недостатки кремнегранитных блоков
Изготовление арболита в домашних условиях: состав и пропорции
Изготовление арболита в домашних условиях
Разделы статьи:
- 1 Изготовление арболита в домашних условиях
- 1.
1 Состав арболита
- 1.
- 2 Формы для арболитовых блоков
Кроме того, арболит делают из натуральных компонентов, основными из которых выступает портландцемент и различные отходы деревообработки. Вследствие этого, арболитовые блоки безвредны в использовании, а дома из них имеют приятный микроклимат внутри на всём протяжении эксплуатации.
Изготовление арболита в домашних условиях
Арболит — это уникальный в своём роде строительный материал, который имеет простой состав. За границей, дома из арболита строят уже сравнительно давно, в то время как у нас, этот стройматериал появился относительно недавно, лишь в середине прошлого столетия.
Дома из арболита, как было сказано выше, обладают целым рядом преимуществ, среди которых, особенно следует отметить такие:
- Прекрасные теплоизоляционные характеристики арболита;
- Возможность использования арболитовых блоков, как в качестве основного стройматериала, так и в роли утеплителя;
- Лёгкость в монтаже и обработке;
- Экологическая безвредность арболита;
- Достойные звукоизоляционные свойства и доступная стоимость.
Перечислять достоинства арболита можно еще долго, но в особенности хотелось бы отметить простоту изготовления этого стройматериала в домашних условиях.
Арболитовый дом легко поддаётся отделке после строительства, хотя некоторые нюансы при осуществлении оштукатуривания арболита всё же, имеются.
Состав арболита
Изготовление арболита в домашних условиях достаточное простое мероприятие. В качестве основного связующего вещества выступает портландцемент. Важно обратить внимание на марку цемента, поскольку для изготовления арболитовых блоков, цемент нужен марок либо 400, либо 500.
Расход цемента для изготовления арболита сильно зависит от используемого наполнителя, в роли которого могут выступать различные отходы деревообработки. Как правило, это стружка таких хвойных пород древесины, как сосна и ель. Также для изготовления арболита, может быть использована щепа берёзы, тополя, осины или бука.
И, как показывает практика, расход цемента при изготовлении арболитовых блоков, можно определить следующим образом: чтобы сделать один кубометр арболитовых блоков М15, нужно приблизительно израсходовать около 250 кг портландцемента.
Кроме цемента и древесного наполнителя, важной составляющей при изготовлении арболита в домашних условиях, являются химические добавки. В качестве химических добавок в арболит, используется известь, кальций (хлористый), быстрорастворимое стекло и сернокислый алюминий.
Химические добавки в составе арболита нужны для того, чтобы предотвратить развитие нежелательных микроорганизмов в наполнителе, а также использовать его без какой-либо выдержки.
Пропорции химических добавок в арболит, всецело зависят от общего веса цемента, но редко достигают более 4%. Перед их применением, большинство химических добавок в арболит растворяют предварительно в воде, которую потом и используют для замешивания арболитовой смеси.
Формы для арболитовых блоков
После смешивания всех компонентов, смесь распределяется в специальные формы для арболитовых блоков. Это могут быть как специальные, заводские формы, так и формы ручного изготовления. Размеры форм, часто соответствуют стандартным размерам шлакоблока.
Кроме того, нередко можно встретить закладку арболита прямо в опалубку, с последующим армированием стены, арматурой или металлическими прутьями. Сделать формы для арболитовых блоков своими руками в принципе несложно, об этом можно прочитать в соответствующей статье сайта https://remstroisovet.ru — формы для заливки.
Что же касается минусов домов из арболита, то их практически нет. Единственным, пожалуй, самым серьезным недостатком арболита, является то, что он способен очень сильно впитывать влагу в себя. Тем не менее, при соответствующей отделке стен, дома из арболита лучшие в своём роде, с отличными тепло и звукоизоляционными показателями.
Древесные отходы в бетонных блоках
%PDF-1.5 % 1 0 объект >/Metadata 363 0 R/OCProperties>>>]/ON[464 0 R]/Order[]/RBGroups[]>>/OCGs[364 0 R 464 0 R]>>/Outlines 360 0 R/Pages 2 0 R/StructTreeRoot 3 0 R/Тип/Каталог>> эндообъект 362 0 объект >/Шрифт>>>/Поля 368 0 R>> эндообъект 363 0 объект >поток приложение/pdf
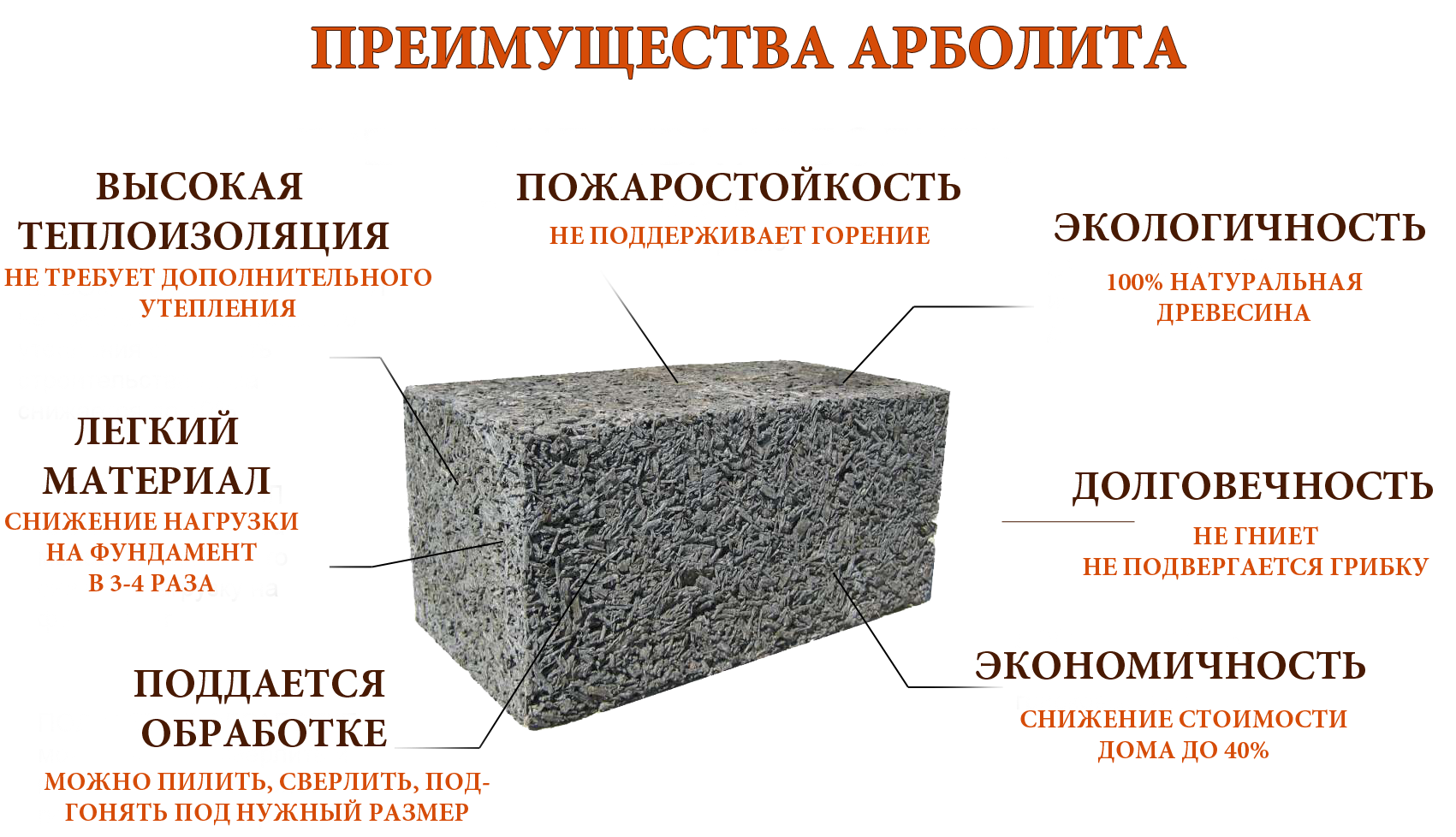

Обзорное исследование различных свойств пустотелых бетонных блоков – IJERT
DOI: 10.17577/IJERTCONV4IS03032 Скачать полнотекстовый PDF Процитировать эту публикациюХаршит Варшней, 2015, Обзорное исследование различных свойств пустотелых бетонных блоков, МЕЖДУНАРОДНЫЙ ЖУРНАЛ ИНЖЕНЕРНЫХ ИССЛЕДОВАНИЙ И ТЕХНОЛОГИЙ (IJERT) RACEE – 2015 (Том 4 – Выпуск 03),
- Открытый доступ
Загрузка статьи/просмотров: 4 252
- Всего загрузок : 8
- Авторы : Харшит Варшней
- Идентификатор бумаги: IJERTCONV4IS03032
- Том и выпуск: RACEE – 2015 (Том 4 – Выпуск 03)
- Опубликовано (впервые в сети): 30 июля 2018 г.
- ISSN (онлайн): 2278-0181
- Имя издателя: IJERT
- Лицензия: Эта работа находится под лицензией Creative Commons Attribution 4.
0 International License
Просмотр
Только текстовая версияОбзорное исследование различных свойств пустотелых бетонных блоков
Харшит Варшни
Департамент гражданского строительства
Технологический институт Рурки, Рурки 247667, Индия,
В настоящее время бетонные пустотелые блоки очень популярны при возведении различных несущих ненесущих конструкций. В этой статье мы обсуждаем прочность на сжатие пустотелых блоков, изготовленных в различных пропорциях смеси с различными заменами. Основной целью этой статьи является исследование различных свойств различных пустотелых блоков, изготовленных из разных размеров, материалов и пропорций в смеси. В этом исследовании результат дает разницу в прочности на сжатие при замене мелкого и крупного заполнителя отходами, такими как вермикулит, цементная пыль, карьерная пыль и т. д.
Ключевые слова:
ВВЕДЕНИЕ
Основной потребностью человека является убежище.
В древности люди начали жить в пещерах ниже уровня земли, после чего начали возводить стены из глины, разработали технику кладки из обожженного глиняного кирпича, чтобы сделать конструкцию частью убежища.
В настоящее время в строительстве очень популярны пустотелые бетонные блоки. Эти блоки в основном используются при строительстве многоэтажных домов, заводов и жилых домов. Эти бетонные пустотелые блоки обычно используются в составных стенах из-за дешевизны. Эти бетонные пустотелые блоки более полезны из-за своего легкого веса, а наиболее важной особенностью является легкость вентиляции. Бетонные пустотелые блоки изготавливаются из смеси цемента, песка и каменной крошки. Это уменьшает количество цемента в каменной кладке и снижает стоимость строительства.
Пустотелые бетонные блоки, обнаруженные благодаря различным преимуществам
Управление звуком
Малая статическая нагрузка
Огнестойкость
Адекватная сила
Превосходная теплоизоляция
Эконом
Очень прочный
Экологически чистый Экологичный
Снижение расхода раствора
Быстрая и простая строительная система
Улучшенные архитектурные особенности
Первый бетонный блок в качестве замены камня и дерева в строительстве был использован в США.
Первый дом из бетонных блоков, построенный в 1837 году на Статен-Айленде в Нью-Йорке.
Хармон С. Палмер спроектировал первый пустотелый бетонный блок в 1890 году. Палмер запатентовал конструкцию полого блока в 1900 году после 10 лет экспериментальных исследований. Блоки Палмерса были 8 дюймов (20,3 см) х 10 дюймов (25,4 см) х 30 дюймов (76,2 см), и они
были тяжелыми по весу. Эти ранние пустотелые блоки отливались вручную, и средняя производительность составляла около 10 блоков в час. Сейчас бетонные блоки изготавливаются по автоматизированному процессу, который может производить до 2000 блоков в час.
Прочность каменной кладки на сжатие является одним из наиболее важных свойств при проектировании каменной конструкции. Эта прочность зависит от нескольких факторов, таких как прочность блока, прочность раствора, затирка, прочность затирки, геометрия блоков, строительный раствор, а также тип принятой связи и засыпки. В странах с экстремально жарким или холодным климатом эти бетонные блоки обладают низкой теплопроводностью, а также служат теплоизоляционным материалом, который минимизирует потребление энергии, сводя к минимуму зависимость от электричества для кондиционирования воздуха или отопления.
Во всех странах различные традиционные материалы заменяются бетонными пустотелыми блоками, поскольку стоимость большинства традиционных материалов растет. В обзорном исследовании мы обнаружили, что пустотелые блоки двойной Н-образной формы дают большую прочность при кладке с полузалитым раствором и низкую прочность при кладке с полным раствором.
ОБЗОР ЛИТЕРАТУРЫ
Х. С. Сурешчандра, Г. Сарангапани и Б. Г. Нареш Кумар (2014) [1] определяют прочность на сжатие пустотелых блоков с частичной и полной заменой песка карьерной пылью. После замены он обнаружил, что 50% замена песка дает высокую прочность, а 100% замена песка дает низкую прочность.
Эрнесто С. Фортес, Гильерме А. Парсекян и Фернандо С. Фонсека, А.М. (2014 г.)[2] изучили прочность на сжатие необработанной и залитой раствором каменной кладки и каменных блоков. Данные исследования свидетельствуют об увеличении прочности кладки на сжатие при увеличении прочности блоков на сжатие.
Лян Хуан, Лецзя Ляо, Либо Ян, С.
М. и Hongwei Yi (2014) [3] изучали прочность на сжатие призм кладки из бетонных блоков с двойным Н-образным сечением при одноосном сжатии. Он обсудил влияние прочности раствора, затирки и влияния прочности затирки на прочность призмы на сжатие. Результат испытаний показывает, что прочность на сжатие призмы H-блока уменьшилась с увеличением заливки цементным раствором, а предельная нагрузка на призмы значительно увеличилась.
К. С. Аль-Джабри, А. В. Хаго, Р. Таха, А. С. Альнуайми и А. Х. Аль-Саиди (2009 г.))[4] производит блок из отходов: вермикулита и полистирола, которые использовались в качестве легких заполнителей, и цементной пыли (CKD), которая частично заменяла цемент. Результат показывает, что легкие бетонные блоки, изготовленные из полистирола, имели
низкая теплопроводность по сравнению с вермикулитовыми и обычными бетонными блоками, а добавление до 15% ЦКД в качестве замены цемента дает незначительное влияние на прочность. Дениз С. Санчес и Лиза Р. Фельдман (2014) [5] определили, что расчетное сопротивление арматуры растяжению было выше для стержней, находящихся в контакте, и, кроме того, чувствительно к величине поперечного расстояния, предусмотренного в случае бесконтактного нахлеста.
сращивания.
Тания Каосол (2010)[6] провела исследование повторного использования бетонных отходов в качестве щебня для пустотелых бетонных блоков кладки. Основная цель состояла в том, чтобы повысить ценность бетонных отходов, создать устойчивую и выгодную альтернативу утилизации бетонных отходов. Предпринимались попытки использования отходов бетона в виде щебня в составе бетонной смеси для изготовления пустотелых бетонных блоков. Были опробованы различные проценты камней с коркой (т.е. 0%, 10%, 20%, 50% и 100%). В результате они обнаружили, что бетонные отходы можно использовать для производства полых блоков кладки из бетонных блоков.
Maroliya (2012) [7] обнаружил, что структура трещин, образовавшаяся в конструктивных элементах, таких как стена, и прочность стены, построенной из пустотелых бетонных блоков, дает меньшую прочность по сравнению с кирпичной кладкой, но стоимость строительства очень меньше.
МАТЕРИАЛЫ
Наконец, завершите содержание и организационное редактирование перед форматированием.
При проверке орфографии и грамматики обратите внимание на следующие пункты:
Цемент
Цемент — вяжущий материал, используемый в бетонных пустотелых блоках. Мы можем использовать обычный портландцемент для изготовления бетонных пустотелых блоков, чтобы получить высокую прочность. Основная функция цемента заключается в связывании между собой мелких и крупных частиц заполнителя. Сегодня цемент находит избыточное применение во всех видах строительных работ, где требуется высокая прочность.
Крупные и мелкие заполнители
Минеральные заполнители обычно делятся на два типа в зависимости от размера их частиц. Совокупные частицы, проходящие через
Индийское стандартное сито 4,7 мм известно как мелкий заполнитель, а частицы, оставшиеся на сите 4,7 мм индийского стандарта, известны как крупный заполнитель. Природный песок часто используется в качестве мелкого заполнителя в бетонной смеси. Крупные заполнители представляют собой щебень из дробленых каменных валунов.
В качестве мелкого заполнителя может использоваться также щебень крупностью, проходящей через сито 4,7 мм. Максимальный размер крупного заполнителя, который можно использовать в бетонных пустотелых блоках, составляет 12,5 мм. Следует отметить, что размер частиц должен быть до 1/3 толщины самой тонкой стенки пустотелых бетонных блоков
Карьерная пыль
Карьерная пыль является побочным продуктом гранитных камней, которые могут образовываться при дроблении камней на крупные агрегаты разных размеров. Эта пыль является частичной или полной заменой песка при изготовлении пустотелых бетонных блоков.
Вермикулит
Вермикулит — природный минерал, расширяющийся при нагревании. Это пластинчатая структура, похожая на структуру слюды, которая встречается во многих странах, таких как Южная Африка, Китай, Бразилия и некоторых других странах. Вермикулит может расширяться до 30 раз от своего первоначального объема за счет расслаивания тонких пластин при нагревании до температур 650-1000°С.
Цементная пыль (CKD)
Пыль цементных печей является побочным продуктом производства цемента в цементных печах сухим способом. Он образуется в процессе обжига в печи и также известен как цементная пыль. Когда сырье нагревается, в печи образуются частицы пыли, которые затем выносятся с отходящими газами в верхний конец печи. Эти газы охлаждаются, а частицы пыли улавливаются эффективной системой сбора пыли
.
СПЕЦИФИКАЦИЯ КАЧЕСТВА
В соответствии со спецификацией индийского стандарта полый блок определяется как блок, имеющий одно или несколько больших отверстий или полостей, проходящих через блок, и содержащий твердый материал в пределах от 50 до 75 процентов от общего объема блока, рассчитанного по общему размеру. Все различные типы пустотелых и жестких кирпичей из цементного бетона подпадают под действие спецификации Бюро индийских стандартов (BIS), указанной ниже:
.Форма и размер
Таблица 1 Размеры и вес различных пустотелых блоков
№ изделия
Описание
Размеры в (см)
Приблизительный вес в кг.
G4В1
Полная полая
39 х 09 х 19
10,0
G4Â2
Полая половина
19 х 09 х 19
5.1
G5В1
Полная полая
39 х 12,5 х 19
13,0
G5Â2
Полая половина
19 х 12,5 х 19
6,3
G6В1
Полная полая
39 х 14 х 19
13,9
G6Â2
Полая половина
19 х 14 х 19
6,5
G6Â3
Половина перемычки
19 х 14 х 19
7,5
G8В1
Полная полая
39 х 19 х 19
16,7
G8Â2
Полая половина
19 х 19 х 19
8,8
G8Â3
Половина перемычки
19 х 19 х 19
9,3
G8Â8
Полная полая
40 х 20 х 20
17,6
G9В1
Полная полая
39 х 23 х 19
28,4
G10В1
Плита перекрытия
50x20x12,5
18.
00
Рис. 1 Различные формы пустотелых блоков
Максимальный разброс размеров не должен составлять + 1,5 мм по высоте и ширине и + 300 мм по длине. Размер, отличный от указанных выше, также может быть использован по взаимному согласию между покупателем и производителями/поставщиками.
Полости
Общая ширина полости в блоке под прямым углом к лицевой стороне блока при укладке в стену (т.е. поверхность основания будет находиться под прямым углом к лицевой стороне блока не должна превышать 65% от общей ширины блока
Толщина оболочки
Толщина оболочки блоков должна быть не менее 40 мм.
Соединения
Концы блоков, образующие вертикальные швы, могут быть прямоугольными с канавками или двойными канавками.
Плотность
Плотность блоков пустотелых бетонных блоков должна быть не более 1600 кг/куб.м общего объема.
Усадка при высыхании
Усадка при высыхании в среднем трех блоков не должна превышать 0,004%.
Содержание влаги
Влажность высушенных блоков при погружении в воду не должна превышать 0,03 %.
Водопоглощение
Водопоглощение не должно превышать 10% по весу.
ИСПЫТАНИЕ НА ПРОЧНОСТЬ СЖАТИЯ
Каждый блок сначала сушили, взвешивали и помещали между плитами машины для испытаний на сжатие. Пластины из мягкой древесины были помещены под и сверху блока, отделяющего его от плит машины. Нагрузку прикладывали небольшими приращениями до разрушения, а разрушающую нагрузку блока регистрировали. Напряжение при разрушении рассчитывали, используя общую площадь блока по нормали к нагрузке
СРАВНЕНИЕ СЖАТИЯ
ПРОЧНОСТЬ
В таблице ниже приведено сравнение прочности на сжатие пустотелых блоков размером 20 см х 20 см х 20 см, изготовленных из разных пропорций смеси. Некоторая замена также имеет место, например, вермикулит с заполнителем, CKD с цементом и карьерная пыль с песком.
Таблица 2 Прочность на сжатие при различных пропорциях смеси
Размер
(см)
Микс
Соотношение
Материал
замена
%
Прочность
(МПа)
20х20х40
1:2:0,5
0
28
20х20х40
1:2:0,5
Вермикулит с
агрегат
30
14.1
20х20х40
1:2:0,5
0
10
20х20х40
1:2:0,5
ЦКД с цементом
5
15
20х20х40
1:2:0,5
ЦКД с цементом
10
10,6
20х20х40
1:3:6
0
2,25
20х20х40
1:4:0
0
1,9
40х20х20
1:3:6
0
3,69
40х20х20
1:3:6
Карьерная пыль с
песок
50
6.
03
40х20х20
1:3:6
Карьерная пыль с песком
100
5,78
ЗАКЛЮЧЕНИЕ
Блоки бетонные пустотелые размером 20х20х40 см, выполненные в пропорции 1:2:0,5, дают наилучшую прочность на сжатие 28 МПа блоки пустотелые бетонные размером 20х20х40 с вермикулитом в качестве частичной замены заполнителя дают только половинную прочность на сжатие прочность, которая иногда вызывает возражения, но не вызывает возражений при использовании в ненесущих конструкциях. Использование таких отходов, как вермикулит, пыль цементных печей и карьерная пыль делает окружающую среду максимально чистой и снижает себестоимость строительства из пустотелых блоков, что выгодно как производителю, так и потребителю. Многие компании сталкиваются с большими проблемами при утилизации этих отходов, поэтому использование этих отходов снижает утилизацию отходов и экономит сельскохозяйственные земли от этих отходов.
ССЫЛКИ
Х. С. Сурешчандра, Г. Сарангапани и Б. Г. Нареш Кумар, 2014 г. Экспериментальное исследование влияния замены песка карьерной пылью в пустотелых бетонных блоках для различных пропорций смеси. Международный журнал экологических наук и разработок, Vol. 5, № 1.
Эрнесто С. Фортес, Гильерме А. Парсекян и Фернандо С. Фонсека, AMASCE, 2014 г. Взаимосвязь между прочностью бетонной кладки на сжатие и прочностью бетонной кладки на сжатие Американское общество инженеров-строителей.
Лян Хуан, Лейя Ляо, Либо Ян, S.M.ASCE и Хунвэй И, 2014 Прочность на сжатие призм из бетонных блоков Double H Американское общество инженеров-строителей.
К.С. Аль-Джабри, А.В. Хаго, Р.Таха, А.С. Альнуайми и А.Х. Аль-Саиди, 2009 г. Прочность и изоляционные свойства строительных блоков, изготовленных из отходов материалов ЖУРНАЛ МАТЕРИАЛОВ В ГРАЖДАНСКОМ СТРОИТЕЛЬСТВЕ.
Дениз С.