Арболитовый блок состав | Арболит 150
Арболит или Древоблок это одна из лучших и практичных разновидностей легких бетонов. При производстве Арболитовых блоков согласно ГОСТу РФ 19222-84, применяются такие составляющие, как: цемент (марки 400, 500 и выше), химическая добавка (безопасная для здоровья человека, применяемая также для очистки воды), древесная щепа и вода.Органическим наполнителем здесь является древесная щепа, возможно применение опилок, стеблей хлопчатника, отходов деревообработки, костры конопли, льна. Безвредная химическая добавка в свою очередь обеспечивает выведение сахара из щепы, улучшая сцепление древесного наполнителя с цементом, сокращает время твердения блока, предотвращает гниение и заражение блока различными грибками. Не стоит путать Арболит с опилкобетоном, так как песок входящий в состав опилкобетона не используется при изготовлении Арболитовых блоков.
Арболит делится на два вида: конструкционный и теплоизоляционный.
Конструкционный применяется при возведении несущих стен здания и как правило имеет большую плотность и марку прочности нежели теплоизоляционный.
Теплоизоляционный вид блока прекрасно подходит для утепления жилых домов, зданий построенных из кирпича, керемзитобетонных и других строительных блоков и имеет легкий вес и меньшую плотность чем конструкционный.
Вид Арболита: | Плотность кг/м3 | Прочность кг/м3 | Класс по прочности при сжатии | Применение в строительстве |
Конструкционный | 500-700 | М 25, 35, 50 | В 1,5 – 3,5 | Возведение несущих стен |
Теплоизоляционный | 400-500 | М 5, 10, 15 | В 0,35 – В 1,5 | Утепление стен |
Технические характеристики Арболита:
- Средняя протность 650 кг/м3
- Прочность на изгиб 0,8-1 МПа.
- Прочность на сжатие 1,5-3 МПа.
- Теплопроводность 0,11 Вт/(м*С).
- Усадка в % 0,4-0,5.
- Морозостойкость 25-50 циклов.
- Огнестойкость 1-1,5 часа.
- Биостойкость V группа.
- Влагопоглощение % 40 — 80.
- Звукопоглощение(126-2000Гц) 0,17-0,6.
Превосходство арболита по техническим характеристикам над другими видами строительных материалов приведены ниже в таблице:
Материал: | Плотность: кг/м3 | Теплопроводность: Вт/(кв.м *С) | Паропроницаемость: мг/(м*ч*па) | Требуемая толщина стен: м | Морозостойкость: циклы |
Арболит | 600 | 0,7-0,15 | 0,19 | 0,3 | 25 и выше |
Древесина | 500 | 0,09 | 0,6 – 0,32 | 0,2 | – |
Газобетон | 500 | 0,21 | 0,14 | 0,5 | 15 и выше |
Кирпич | 1250 | 0,76 | 0,15 | 1 | 15 и выше |
Пенобетон | 700 | 0,15 | 0,14 | 0,5 | 15 и выше |
Главные преимущества арболита:
Что выбрать: кирпич илиАрболит
Кирпич на сегодняшний день один из самых популярных строительных материаллов, но применение его в строительстве жилых и не жилых зданий не всегда оправдана и с экономической точки зрения выгодно.
Начнем с теплопроводности:
Кирпич различного типа имеет теплопроводность в среднем 0,5-1,5Вт/(кв.м *С).
У арболитовых блоков она составляет – 0,07-0,15Вт/(м*К).
Следовательно стена толщиной 30 см. из арболита по теплопроводности будет соответствовать 100 см. стене выложенной из кирпича. Не мало важным фактором теплосбережения является применяемое количество раствора для кладки. Так называемый «мостик холода». Объем одного арболитового блока размером 500х300х200мм (0,03 м3) равен объему 15 кирпичам 250х120х65мм (объём 0,00195 м3), соответственно количество данных мостиков холода при строительстве дома из арболита будет в 2-3 раза меньше чем при применении кирпича.
Плотность:
Применяемый в строительстве жилых домов до 3 этажей, конструкционный арболит имеет среднию плотность 650 кг/м3 при размерах 500х300х200мм (0,03 м3).
При своем размере, кирпич имеет плотность – 1000-1500кг/м3
Вес, одинакового по объему, кирпича будет примерно в 3 раза больше Арболита. Этот показатель приводит к увеличению стоимости фундамента при строительстве кирпичного дома. Доставка такого большого количества кирпича скажется на увеличении стоимости затрат при строительстве.
Горючесть:
Арболит и кирпич входят в группу материалов, не поддерживающих горение, способствующих противостоять высоким температурам продолжительное время. Применяемый утеплитель не всегда имеет нужную пожаростойкость, что делает кирпичный дом более уязвимым к действию огня.
Биостойкость:
Входящие в состав Арболита безопасные добавки делают его устойчевым к разрушающему действию различных грибков, микробов и т.п. Кирпич аналогично арболиту также не подвержен действию микробных биологических культур.
Легкость в строительстве:
Арболитовые блоки с легкостью пилятся в отличии от кирпича, в арболит закручивают саморезы, вбивают гвозди, подгоняют под любой размер при необходимости, кирпич похвастаться этим не может. Количество применяемого раствора в 2-3 раза меньше при возведении стен из Арболита чем из кирпича, сокращаются сами сроки строительства. Арболит без проблем штукатурится.
Экологичность:
Арболит состоит в среднем из 80% древесной щепы, оставшиеся 20% это цемент марки 500 и полностью безопасные добавки.
Выбирая Арболитовые блоки производимые на нашем производстве, Вы:
– Экономите в целом на строительстве дома в 30-40%
– Сокращаете сроки возведения дома в 2-4 раза
– Экономите на доставке, хранении, фундаменте, утеплении
– Получаете гарантию и все необходимые документы
Арболитовые блоки – состав смеси, пропорции для приготовления
Арболит не является современным строительным материалом – он изобретен еще в середине прошлого века и до сих пор применяется в строительстве. Здания, построенные еще в начале его использования, сегодня наглядно демонстрируют преимущества и целесообразность использования арболитовых блоков, состав смеси и точные пропорции для их изготовления уже многократно проверены в теории и испытаны на практике.
Что такое арболит, его состав
Современным языком, это называется «композитный материал» — сочетание нескольких компонентов – основы, связующих и добавок для улучшения качества исходного материала. Состав арболита и его пропорции найдены удачно – новый материал получает преимущества старых, а также частично или полностью избавляется от их недостатков.
Методика изготовления разработана в Голландии, где были созданы монолитный арболит и блочный – что это такое, мир узнал еще в 1930-е годы. Новый материал стал достаточно быстро популярен в Европе, США и СССР, куда он пришел в 1960-е года.
Получаемый в промышленных условиях арболит состоит из следующих компонентов:
- Древесные щепки (щепа), размерами 3-5х5-10х25 мм. Лучший арболит получается из измельченной хвои, но использовать для изготовления можно и другие породы, а также костру (одеревеневшие части стеблей), рисовую солому или хлопчатник. Этот компонент дает материалу теплоизоляционные свойства деревянного бруса.
- Наполнители. Их основной задачей является нейтрализация сахаров, находящихся в древесине и провоцирующие ее последующее гниение. Они же привлекают термитов и прочих насекомых, питающихся деревом. В промышленных условиях арболит в свой состав включает сульфат алюминия – известная пищевая добавка E520, реже применяется хлорид или нитрат кальция. В частном строительстве, при невозможности достать эти компоненты, в раствор добавляют жидкое стекло.
- Цемент. Это главный связующий элемент, также напрямую влияющий на свойства получаемого материала – от него зависит плотность и сопротивление механическим повреждениям. Чаще всего применяется марка 500.
- Вода. Растворитель наполнителей, инициатор и катализатор реакции цемента.
В состав арболита компоненты входят в таких соотношениях: цемент – 25 кг, щепа – 120-150 л, вода – 40 л, жидкое стекло – 0,5 л.
Наглядно про арболит на видео:
Технические характеристики материала
Второе название материала – древобетон или древоблок, он получил из-за наличия в нем большого количества дерева. Арболитовые блоки в свой состав включают 90% щепы – желательно хвойной. Но нельзя воспринимать их как полный аналог дерева — стандартизирован арболит именно как бетон или строительный камень.
Технические характеристики арболита объединяют в себе свойства древесины и цемента, что выделяет его даже среди аналогов – пенобетона и газобетона.
Как минимум, по показаниям теплопроводности, простоте обработки и укладки, арболит значительно превосходит кирпич.
Характеристика материала в таблице:
Свойство | Значения |
Плотность (сколько весит кубический метр материала), кг/м3 | 500-850 |
Прочность на сжатие (необходимое усилие для сжатия блока), МПа | 0,5-3,5 |
Прочность на изгиб (необходимое усилие для изгиба блока), МПа | 0,7-1 |
Теплопроводность (чем меньше, тем лучше), Вт/(м*С) | 0,08-0,17 |
Модуль упругости (способность сжиматься без деформации), МПа | 250-2300 |
Морозостойкость (сколько раз мокрый блок можно заморозить) | 25-50 |
Водопоглощение (впитываемая вода относительно веса), % | 40-85 |
Усадка (изменение размеров после укладки), % | 0,4-0,5 |
Биостойкость (чем больше, тем лучше), группа | V |
Огнеустойчивость (время до разрушения материала в огне), мин | 45-90 |
Звукоизоляция (процент пропускаемых звуков до 2000 Гц), % | 0,17-0,6 |
Многие характеристики материала зависят от его плотности, которая варьируется из-за использования различных сортов цемента и наполнителей. В первую очередь это влияет на плотность и теплопроводность.
Параметры водопоглощения изменить невозможно, но для их уменьшения, как и с остальными материалами, применяется оштукатуривание стен или декоративные фасадные панели.
Плюсы, минусы и ограничения использования
Арболит применяется в строительстве давно и успешно. За это время полностью выявлены все преимущества и недостатки материала, а также способы борьбы с последними. Единственное серьезное ограничение на использование есть на применение арболита в многоэтажном строительстве – дом выше трех этажей из него возводить нельзя.
В остальных случаях, целесообразность его использования рассматривается в зависимости от преимуществ и недостатков материала.
Чем хорош арболит
Этот стройматериал достаточно прост в изготовлении – его можно делать даже вручную, для чего достаточно простой бетономешалки. Кроме этого, достаточно и других преимуществ:
- Хорошая устойчивость к механическим воздействиям.
При этом, блок можно распилить обычной ножовкой по дереву, чтобы придать нужную форму.
- Арболит это легкий материал, поэтому для выстроенного из него дома не нужен мощный фундамент.
- Технология изготовления делает материал непривлекательным для термитов и подобных насекомых, а также делает стены устойчивыми к грибкам и плесени.
- Арболитовые блоки крупнее и легче аналогов из шлакоблока, пено или газобетона. Размеры позволяют уменьшить количество операций (принес-уложил) что ускорит общий темп строительства. Если шлакоблок весит 8 кг, то равный по размеру арболитовый материал около 4 – меньше сил потратится на его транспортировку. При этом прочность арболита примерно такая же.
- Арболитовые стены хорошо поддаются сверлению – в них можно забивать гвозди или закручивать шурупы, где они держатся как в деревянных досках.
- Отличный теплоизолирующий материал – иногда используется как утеплитель.
- Арболит не горит. При длительном воздействии высокой температуры может начать тлеть, но дыма при этом выделяется немного.
- В отличие от хрупкого бетона, арболитовые блоки способны выдерживать гораздо большие нагрузки на растяжение, поэтому трещины в стенах из этого материала могут появиться только вследствие грубого нарушения технологии строительства.
- Арболит не содержит вредных химических соединений, что делает его экологически чистым материалом.
- Значения паропроницаемости материала схожи с деревянными изделиями – стены «дышащие» и не нуждаются в дополнительной вентиляции.
- Долговечность. По техническим характеристикам, морозостойкость арболита до 50 циклов заморозки. Если же учитывать, что замораживание может повредить только влажному материалу, при правильной и своевременной обработке стен штукатуркой, срок их службы составить гораздо больше, чем 50 лет.
Недостатки материала
Технология производства подразумевает большое количество ручного труда – к примеру, автоматика не способна произвести распалубку и на ее долю остается смешивание компонентов. Остальное по возможности делается в полуавтоматическом режиме, но если на обслуживании станка по производству арболита будет меньше 3-4 человек, то скорость работы значительно упадет. Материал для изготовления сам по себе недорогой, но значительная часть себестоимости составляет оплата труда рабочих.
«Дышащие» стены одновременно подразумевают высокий уровень их гигроскопичности материала. Если блоки напитаются влагой, особенно перед заморозками, то срок их службы резко снизится. Оштукатуривание стен позволяет справиться и с этой проблемой.
В осенне-зимний период, хранящиеся на складе блоки штукатуркой не покроешь, поэтому их надо беречь от намокания.
Один из минусов материала можно увидеть глазами – это его внешний вид – выглядит как ДСП, но цвет как у бетонного покрытия. Для решения этой проблемы стены штукатурятся или покрываются сайдингом. Некоторые производители предлагают арболит с уже оштукатуренной одной стороной, но особого смысла в этом нет, так как штукатурить стены все равно надо, хотя бы и для предотвращения их намокания.
В кустарных условиях, чем часто грешат мелкие производители, сложно получить точную геометрию блоков. Это значит, что швы между ними будут толстыми, а это кроме перерасхода цемента, еще и дополнительные «мостики холода».
Технология производства
Есть несколько способов получить арболит – ручное производство и на полуавтоматических станках. Полностью автоматизированной линией пока не хвастался ни один производитель. Наиболее «продвинутой» пока остается технология показанная на видео:
Полный цикл производства, делается арболит своими руками или в заводских условиях, схематично выглядит следующим образом:
- Подготовка досок. Очистка их от коры, грязи и прочего мусора. Если в арболитовый блок попадет подгнивший кусок коры, то это нарушение технологии.
- Дробление досок на щепу. Надо не выходить за рамки определенных ГОСТом размеров 3-5х5-10х25 мм (высота-ширина-длина), иначе качество арболита будет сомнительным.
- Подготовка, дозировка и смешивание компонентов.
Перед применением щепа выдерживается под открытым небом не меньше 4-х месяцев или же вымачивается в минерализованном растворе (сульфат алюминия, хлорид кальция, жидкое стекло). Дозировка выполняется весовым или объемным методом. Смешивание проводится 5-10 минут, чтобы цемент покрыл всю щепу.
- Далее полученная масса засыпается в формы, предварительно смоченные водой, и трамбуется. Это ключевой этап и с трамбовкой надо соблюдать осторожность – если применять для этих целей вибростол, то процедура не должна быть дольше 30 секунд. В противном случае цемент, как более тяжелый, просто начнет опускаться на дно. В опалубке и под гнетом блоки оставляются на сутки.
- После распалубки блоки сохнут на солнце в течение 3-4 дней. Для полного соблюдения технологии их надо выдержать на сушке 3 недели. После этого будет разрешена их транспортировка.
Пропорции компонентов для изготовления арболита
Соотношение компонентов для смеси объемом 1 м³ в таблице:
Для изготовления блоков | ||||
Марка арболита | Цемент М 400, кг | Щепа, кг | Добавки, кг | Вода, л |
М-15 | 250-280 | 240-300 | 12 | 350-400 |
М-25 | 300-330 | 240-300 | 12 | 350-400 |
Для создания монолитной стены (заливки в опалубку) | ||||
В-0,75 | 280-300 | 180-190 | 8 | 330-360 |
В-1 | 300-330 | 200-210 | 8 | 360-390 |
В-1,5 | 330-360 | 220-230 | 8 | 390-430 |
В-2,5 | 360-400 | 240-250 | 8 | 430-480 |
Арболит В-0,75 используется для утепления; В-1 для возведения одноэтажных домов, плюс мансарды; В-1,5 для гаражей и прочих построек, В-2,5 для 2-3 этажных домов.
Состав арболита и правильные пропорции
georarecom52
RU,Chuvashia,Vurnary;RU,Chuvashia,Kanash;RU,Chuvashia,Novocheboksarsk;RU,Chuvashia,Cheboksary;RU,Chuvashia,Shumerlya;RU,Chuvashia,Yadrin;RU,Vladimirskaya Oblast,Yuryevets;RU,Vladimirskaya Oblast,Aleksandrov;RU,Vladimirskaya Oblast,Aleksandrow;RU,Vladimirskaya Oblast,Vladimir;RU,Vladimirskaya Oblast,Volginskiy;RU,Vladimirskaya Oblast,Gus-Khrustal;RU,Vladimirskaya Oblast,Demidovo;RU,Vladimirskaya Oblast,Kirzhach;RU,Vladimirskaya Oblast,Kovrov;RU,Vladimirskaya Oblast,Kolchugino;RU,Vladimirskaya Oblast,Kosterevo;RU,Vladimirskaya Oblast,Murom;RU,Vladimirskaya Oblast,Pokrov;RU,Vladimirskaya Oblast,Raduzhnyy;RU,Vladimirskaya Oblast,Sobinka;RU,Nizhegorodskaya Oblast,Vilya;RU,Nizhegorodskaya Oblast,Arzamas;RU,Nizhegorodskaya Oblast,Balakhna;RU,Nizhegorodskaya Oblast,Bogorodsk;RU,Nizhegorodskaya Oblast,Bor;RU,Nizhegorodskaya Oblast,Vyksa;RU,Nizhegorodskaya Oblast,Gorodets;RU,Nizhegorodskaya Oblast,Dzerzhinsk;RU,Nizhegorodskaya Oblast,Zavolzhye;RU,Nizhegorodskaya Oblast,Kstovo;RU,Nizhegorodskaya Oblast,Kulebaki;RU,Nizhegorodskaya Oblast,Lyskovo;RU,Nizhegorodskaya Oblast,Navashino;RU,Nizhegorodskaya Oblast,Nizhniy Novgorod;RU,Nizhegorodskaya Oblast,Pavlovo;RU,Nizhegorodskaya Oblast,Pervomaysk;RU,Nizhegorodskaya Oblast,Sarov;RU,Nizhegorodskaya Oblast,Semenov;RU,Nizhegorodskaya Oblast,Sergach;RU,Nizhegorodskaya Oblast,Uren;RU,Nizhegorodskaya Oblast,Shakhunya
georarecom37
RU,Ivanovskaya Oblast,Ivanovo;RU,Ivanovskaya Oblast,Kineshma;RU,Ivanovskaya Oblast,Kolobovo;RU,Ivanovskaya Oblast,Palekh;RU,Ivanovskaya Oblast,Ples;RU,Ivanovskaya Oblast,Podozerskiy;RU,Ivanovskaya Oblast,Rodniki;RU,Ivanovskaya Oblast,Teykovo;RU,Ivanovskaya Oblast,Furmanov;RU,Ivanovskaya Oblast,Shuya
georarecom23
RU,Krasnodarskiy Kray,Abinsk;RU,Krasnodarskiy Kray,Adler;RU,Krasnodarskiy Kray,Anapa;RU,Krasnodarskiy Kray,Armavir;RU,Krasnodarskiy Kray,Belorechensk;RU,Krasnodarskiy Kray,Vyselki;RU,Krasnodarskiy Kray,Gelendzhik;RU,Krasnodarskiy Kray,Gulkevichi;RU,Krasnodarskiy Kray,Yeysk;RU,Krasnodarskiy Kray,Kanevskaya;RU,Krasnodarskiy Kray,Krasnodar;RU,Krasnodarskiy Kray,Krymsk;RU,Krasnodarskiy Kray,Novokubansk;RU,Krasnodarskiy Kray,Novorossiysk;RU,Krasnodarskiy Kray,Primorsko-Akhtarsk;RU,Krasnodarskiy Kray,Slavyansk-na-Kubani;RU,Krasnodarskiy Kray,Sochi;RU,Krasnodarskiy Kray,Temryuk;RU,Krasnodarskiy Kray,Timashevsk;RU,Krasnodarskiy Kray,Tikhoretsk;RU,Krasnodarskiy Kray,Tuapse;RU,Rostovskaya Oblast,Azov;RU,Rostovskaya Oblast,Aksay;RU,Rostovskaya Oblast,Bagayevskaya;RU,Rostovskaya Oblast,Bataysk;RU,Rostovskaya Oblast,Belaya Kalitva;RU,Rostovskaya Oblast,Veselyy;RU,Rostovskaya Oblast,Veshenskaya;RU,Rostovskaya Oblast,Volgodonsk;RU,Rostovskaya Oblast,Gukovo;RU,Rostovskaya Oblast,Donetsk;RU,Rostovskaya Oblast,Yegorlykskaya;RU,Rostovskaya Oblast,Zernograd;RU,Rostovskaya Oblast,Zimovniki;RU,Rostovskaya Oblast,Kagalnitskaya;RU,Rostovskaya Oblast,Kamenolomni;RU,Rostovskaya Oblast,Kamensk-Shakhtinskiy;RU,Rostovskaya Oblast,Kashary;RU,Rostovskaya Oblast,Konstantinovsk;RU,Rostovskaya Oblast,Krasnyy Sulin;RU,Rostovskaya Oblast,Matveyev Kurgan;RU,Rostovskaya Oblast,Millerovo;RU,Rostovskaya Oblast,Morozovsk;RU,Rostovskaya Oblast,Novocherkassk;RU,Rostovskaya Oblast,Novoshakhtinsk;RU,Rostovskaya Oblast,Orlovskiy;RU,Rostovskaya Oblast,Remontnoye;RU,Rostovskaya Oblast,Rodionovo-Nesvetayskaya;RU,Rostovskaya Oblast,Romanovskaya;RU,Rostovskaya Oblast,Rostov-na-Donu;RU,Rostovskaya Oblast,Salsk;RU,Rostovskaya Oblast,Semikarakorsk;RU,Rostovskaya Oblast,Taganrog;RU,Rostovskaya Oblast,Tarasovskiy;RU,Rostovskaya Oblast,Tselina;RU,Rostovskaya Oblast,Tsimlyansk;RU,Rostovskaya Oblast,Chaltyr;RU,Rostovskaya Oblast,Chertkovo;RU,Rostovskaya Oblast,Shakhty;RU,Stavropol,Georgiyevsk;RU,Stavropol,Yessentuki;RU,Stavropol,Zheleznovodsk;RU,Stavropol,Kislovodsk;RU,Stavropol,Lermontov;RU,Stavropol,Mineralnye Vody;RU,Stavropol,Nevinnomyssk;RU,Stavropol,Pyatigorsk;RU,Stavropol,Svetlograd;RU,Stavropol,Solnechnodolsk;RU,Stavropol,Stavropol
georarecom45
RU,Kurganskaya Oblast,Dalmatovo;RU,Kurganskaya Oblast,Kurgan;RU,Kurganskaya Oblast,Shadrinsk;RU,Kurganskaya Oblast,Shumikha
georarecom99
RU,Moskva,Zelenograd;RU,Moskva,Moscow;RU,Moskva,Rumyantsevo;RU,Moskva,Troitsk;RU,Moskva,Khimki;RU,Moskva,Shcherbinka;RU,Moskovskaya Oblast,Aprelevka;RU,Moskovskaya Oblast,Balabanovo;RU,Moskovskaya Oblast,Balashikha;RU,Moskovskaya Oblast,Bekasovo;RU,Moskovskaya Oblast,Beloozerskiy;RU,Moskovskaya Oblast,Besedy;RU,Moskovskaya Oblast,Bronnitsy;RU,Moskovskaya Oblast,Veshki;RU,Moskovskaya Oblast,Vidnoye;RU,Moskovskaya Oblast,Vnukovo;RU,Moskovskaya Oblast,Volokolamsk;RU,Moskovskaya Oblast,Voskresensk;RU,Moskovskaya Oblast,Voskresenskoye;RU,Moskovskaya Oblast,Golitsyno;RU,Moskovskaya Oblast,Gorki-2;RU,Moskovskaya Oblast,Dedovsk;RU,Moskovskaya Oblast,Dzerzhinskiy;RU,Moskovskaya Oblast,Dmitrov;RU,Moskovskaya Oblast,Dolgoprudnyy;RU,Moskovskaya Oblast,Domodedovo;RU,Moskovskaya Oblast,Dubna;RU,Moskovskaya Oblast,Yegoryevsk;RU,Moskovskaya Oblast,Zheleznodorozhnyy;RU,Moskovskaya Oblast,Zhukovskiy;RU,Moskovskaya Oblast,Zaraysk;RU,Moskovskaya Oblast,Zvenigorod;RU,Moskovskaya Oblast,Ivanteyevka;RU,Moskovskaya Oblast,Istra;RU,Moskovskaya Oblast,Kashira;RU,Moskovskaya Oblast,Klimovsk;RU,Moskovskaya Oblast,Klin;RU,Moskovskaya Oblast,Kolomna;RU,Moskovskaya Oblast,Konstantinovo;RU,Moskovskaya Oblast,Korolev;RU,Moskovskaya Oblast,Kotelniki;RU,Moskovskaya Oblast,Krasnoarmeysk;RU,Moskovskaya Oblast,Krasnogorsk;RU,Moskovskaya Oblast,Krasnoznamensk;RU,Moskovskaya Oblast,Krekshino;RU,Moskovskaya Oblast,Kubinka;RU,Moskovskaya Oblast,Kurovskoye;RU,Moskovskaya Oblast,Lesnoy;RU,Moskovskaya Oblast,Lesnoy Gorodok;RU,Moskovskaya Oblast,Lobnya;RU,Moskovskaya Oblast,Losino-Petrovskiy;RU,Moskovskaya Oblast,Lukhovitsy;RU,Moskovskaya Oblast,Lytkarino;RU,Moskovskaya Oblast,Lyubertsy;RU,Moskovskaya Oblast,Malakhovka;RU,Moskovskaya Oblast,Malino;RU,Moskovskaya Oblast,Medvezhi Ozera;RU,Moskovskaya Oblast,Milkovo;RU,Moskovskaya Oblast,Mikhnevo;RU,Moskovskaya Oblast,Mozhaysk;RU,Moskovskaya Oblast,Mytishchi;RU,Moskovskaya Oblast,Naro-Fominsk;RU,Moskovskaya Oblast,Nakhabino;RU,Moskovskaya Oblast,Nikolina Gora;RU,Moskovskaya Oblast,Noginsk;RU,Moskovskaya Oblast,Odintsovo;RU,Moskovskaya Oblast,Oktyabrskiy;RU,Moskovskaya Oblast,Orekhovo-Zuyevo;RU,Moskovskaya Oblast,Pavlovskiy Posad;RU,Moskovskaya Oblast,Podolsk;RU,Moskovskaya Oblast,Protvino;RU,Moskovskaya Oblast,Putilkovo;RU,Moskovskaya Oblast,Pushkino;RU,Moskovskaya Oblast,Pushchino;RU,Moskovskaya Oblast,Ramenskoye;RU,Moskovskaya Oblast,Reutov;RU,Moskovskaya Oblast,Ruza;RU,Moskovskaya Oblast,Selyatino;RU,Moskovskaya Oblast,Sergiyev Posad;RU,Moskovskaya Oblast,Serebryanyye Prudy;RU,Moskovskaya Oblast,Serpukhov;RU,Moskovskaya Oblast,Solnechnogorsk;RU,Moskovskaya Oblast,Staraya Kupavna;RU,Moskovskaya Oblast,Stolbovaya;RU,Moskovskaya Oblast,Stupino;RU,Moskovskaya Oblast,Skhodnya;RU,Moskovskaya Oblast,Tagankovo;RU,Moskovskaya Oblast,Tomilino;RU,Moskovskaya Oblast,Fryazino;RU,Moskovskaya Oblast,Khorlovo;RU,Moskovskaya Oblast,Chernogolovka;RU,Moskovskaya Oblast,Cherusti;RU,Moskovskaya Oblast,Chekhov;RU,Moskovskaya Oblast,Chigasovo;RU,Moskovskaya Oblast,Shatura;RU,Moskovskaya Oblast,Shchelkovo;RU,Moskovskaya Oblast,Elektrogorsk;RU,Moskovskaya Oblast,Elektrostal;RU,Moskovskaya Oblast,Elektrougli;RU,Moskovskaya Oblast,Yubileyny;RU,Moskovskaya Oblast,Yakhroma
georarecom13
RU,Mordoviya,Krasnyy Uzel;RU,Mordoviya,Ruzayevka;RU,Mordoviya,Saransk;RU,Mordoviya,Chamzinka;RU,Chuvashia,Alatyr
georarecom75
RU,Zabaykal,Borzya;RU,Zabaykal,Zabaykalsk;RU,Zabaykal,Krasnokamensk;RU,Zabaykal,Kuanda;RU,Zabaykal,Mogocha;RU,Zabaykal,Novaya Chara;RU,Zabaykal,Khilok;RU,Zabaykal,Chernyshevsk;RU,Zabaykal,Chita;RU,Zabaykal,Shilka
georarecom67
RU,Smolenskaya Oblast,Vyazma;RU,Smolenskaya Oblast,Gagarin;RU,Smolenskaya Oblast,Desnogorsk;RU,Smolenskaya Oblast,Yelnya;RU,Smolenskaya Oblast,Ray;RU,Smolenskaya Oblast,Roslavl;RU,Smolenskaya Oblast,Safonovo;RU,Smolenskaya Oblast,Smolensk;RU,Smolenskaya Oblast,Yartsevo
georarecom47
RU,Leningradskaya Oblast,Volosovo;RU,Leningradskaya Oblast,Volkhov;RU,Leningradskaya Oblast,Vsevolozhsk;RU,Leningradskaya Oblast,Vyborg;RU,Leningradskaya Oblast,Vyritsa;RU,Leningradskaya Oblast,Gatchina;RU,Leningradskaya Oblast,Kingisepp;RU,Leningradskaya Oblast,Kirishi;RU,Leningradskaya Oblast,Kirovsk;RU,Leningradskaya Oblast,Kudrovo;RU,Leningradskaya Oblast,Lopukhinka;RU,Leningradskaya Oblast,Luga;RU,Leningradskaya Oblast,Nikolskoye;RU,Leningradskaya Oblast,Otradnoye;RU,Leningradskaya Oblast,Pikalevo;RU,Leningradskaya Oblast,Podporozhye;RU,Leningradskaya Oblast,Primorsk;RU,Leningradskaya Oblast,Sertolovo;RU,Leningradskaya Oblast,Sosnovyy Bor;RU,Leningradskaya Oblast,Tikhvin;RU,Sankt-Peterburg,Kolpino;RU,Sankt-Peterburg,Pushkin;RU,Sankt-Peterburg,Saint Petersburg;RU,Sankt-Peterburg,Sestroretsk
Подбор состава арболитобетона для производства качественных арболитовых блоков
Подбор состава арболита для изготовления арболитовых блоков на вибростанках Вибромастер производится в лабораторных условиях любым проверенным на практике способом. Производственный состав арболита утверждается главным инженером предприятия и контролируется лабораторией.
На подбор состава арболита дается задание, в котором указывается заданная средняя плотность (марка по средней плотности) и марка по прочности на сжатие (класс по прочности при сжатии). Могут быть указаны дополнительные требования к
Предварительно, перед подбором состава арболита, устанавливают характеристики всех используемых материалов.
Для цемента устанавливают марку и активность, нормальную густоту, минералогический состав, среднюю плотность, истинную плотность р0. Для заполнителя определяют насыпную среднюю плотность р3, плотность в куске рх, водопоглощение по массе W. Качество химических добавок (ХД) устанавливается паспортом или на основании данных их непосредственного испытания.
Наиболее распространенным и удобным способом подбора и назначения исходного состава арболитовой смеси является способ подбора по разработанным таблицам.
Средняя плотность арболита в высушенном состоянии в зависимости от класса (марки) и вида используемых органических заполнителей должна находиться в пределах, указанных в таблице.
Заполнитель | Расход цемента кг/м3, в зависимости от класса (марки) арболита | |||||
---|---|---|---|---|---|---|
Дробленка из отходов: | 80,35(5) | В,75(10) | В1 (15) | В2 (25) | 82,5(35) | |
– лесопиления и деревообработки хвойных пород | 260 | 280 | 300 | 330 | 360 | |
– лесозаготовок хвойных пород | 280 | 300.![]() |
320 | 350 | 380 | |
– лесопиления и деревообработки смешанных пород | 290 | 310 | 330 | 360 | 390 | |
– лесозаготовок смешанных пород | 310 | 330 | 350 | 380 | – | |
– дробленка рисовой соломы | 300 | – | 370 | 400 | – | |
– костра конопли и льна | 220 | 310 | 360 | 450 | – | |
– дробленые стебли хлопчатника | 260 | 290 | 320 | 360 | – |
Примечание: приведенные расходы цемента рекомендуются лишь для приготовления первого исходного замеса при подборе состава арболитовой смеси и не могут служить нормами расхода цемента в производственных условиях.
При применении цемента иных марок (отличного от марки 400) величина расхода цемента умножается на коэффициенты, приведенные в таблице.
Марка цемента | Коэффициенты изменения расхода цемента для арболита класса (марки) | |||||
---|---|---|---|---|---|---|
В0,35(5) | В,75(10) | B1(15) | В2 (25) | В2,5(35) | ||
300 |
1,05 |
1,05 |
1,05 |
1,10 |
1,16 | |
400 | 1 | 1 | 1 | 1 | 1 | |
500 | 0,96 | 0,96 | 0,95 | 0,95 | 0,94 | |
600 | 0,93 | 0,93 | 0,92 | 0,92 | 0,9 |
Расход органического заполнителя в сухом состоянии и назначается по следующей таблице. .
Заполнитель | Расход сухого органического заполнителя, кг/м, арболита класса (марки) | |||||
---|---|---|---|---|---|---|
В0,35(5) | В,75(10) | В1(16) | В2(26) | В2,5(35) | ||
Дробленка из отходов: | ||||||
– лесопиления и деревообработки хвойных пород | 160 | 180 | 200 | 220 | 240 | |
– лесозаготовок хвойных пород | 170 | 190 | 210 | 230 | 250 | |
– лесопиления и деревообработки смешанных пород | 180 | 200 | 220 | 240 | 250 | |
– лесозаготовок смешанных пород | 160 | 180 | 200 | 220 | 240 | |
– дробленка рисовой соломы | 180 | – | 220 | 250 | – | |
– костра конопли и льна | 200 | 190 | 180 | 170 | – | |
– дробленые стебли хлопчатника | 200 | 210 | 220 | 230 | – |
Расходы воды определяются по по следующей таблице.
Заполнитель | Расход воды, л/м в смеси при классе (марке) арболита | |||||
---|---|---|---|---|---|---|
В0,35(5) | В,75(10) | В1 (15) | В2 (25) | В2,5(35) | ||
Дробленка из отходов: | ||||||
– лесопиления и деревообработки хвойных пород | 280 | 300 | 330 | 360 | 400 | |
– лесозаготовок хвойных пород | 300 | 330 | 360 | 400 | 440 | |
– лесопиления и деревообработки смешанных пород | 330 | 360 | 390 | 430 | 460 | |
– лесозаготовок смешанных пород | 330 | 360 | 390 | 430 | 460 | |
– дробленка рисовой соломы | 350 | – | 400 | 450 | – | |
– костра конопли и льна | 400 | 470 | 450 | 420 | – | |
– дробленые стебли хлопчатника | 400 | 460 | 480 | 510 | – |
Расходы цемента, воды и органических заполнителей при производстве арболитовых блоков зависят от многих факторов и, в первую очередь, от способа уплотнения арболитовой смеси. Их необходимо устанавливать опытным путем в зависимости от производственных условий.
Предварительный расход химических добавок назначается по следующей таблице.
Химическая добавка | Расход химической добавки, кг/м3, в зависимости от вида заполнителя | |||
---|---|---|---|---|
древесная дробленка | костра конопли или льна | дробленые стебли хлопчатника | ||
Кальций хлористый технический | 8 | 6 | 11 | |
Стекло натриевое жидкое | 8 | 9 | – | |
Комплексная добавка: сернокислый алюминий + известь-пушенка | 20 25 |
15 20 |
– – |
Рассчитанные составы проверяют в лабораторных или производственных условиях , путём изготовления и испытания контрольных образцов. Опытные образцы для определения класса (марки) арболита по прочности при сжатии твердеют в течение 28 суток при температуре при температуре 20 +/- 2°С и относительной влажности воздуха 70 +/- 10%. Для установления распалубочной и отпускной прочности изготавливают и испытывают образцы в возрасте 1-х, 3-х и 7-и суток.
Рабочий состав арболитобетона назначается по результатам испытания контрольных образцов.
Пример подбора состава арболита
Требуется подобрать состав конструкционно-теплоизоляционного арболита класса В2 для производства арболитовых блоков, средней плотностью не более 650 кг/м3 (в высушенном состоянии) для стеновых строительных блоков.
Имеется заполнитель – дробления из отходов деревообработки хвойных пород. Зерновой состав дроблеики удовлетворяет требованиям стандарта. Насыпная средняя плотность дробленки в сухом состоянии 120 кг/м3, влажность по массе – 50%. Вяжущее – портландцемент марки 400. Подбор состава арболита производим расчетно-экспериментальным методом. Расход цемента определяем по табл.1, Ц=330 кг/м3. По табл.3 расход сухой дробленки Дсух.=220кгД|3, с учетом влажности – расход дробленки составит 330 кг/м3. Для назначенного расхода цемента по табл.6 определяем предварительный расход воды В=360 л/м3.
Расход химической добавки (ХД) устанавливаем по табл.5 – это 8 кг/м3 хлорида кальция. Хлорид кальция берется 10%-ной концентрации. Содержание соли в 1 л. такого раствора (с плотностью 1,084) составляет 0,108 кг. Следовательно, для введения в арболит необходимого количества соли в виде 10%-ного раствора на 1 м3 арболитовой смеси его потребуется: 8:0,108=74,07 л. В найденном количестве раствора соли воды содержится 1,084×74,07-8=72,3 л.
С учетом воды, содержащейся в древесной дробленке и в растворе добавки, количество воды для приготовления 1 м3 арболитовой смеси будет равно 360-72,3=217,7 л. Средняя плотность свежеуложенной арболитовой смеси составит: 330+220+360+8=918 кг/м3.
Средняя плотность арболита в сухом состоянии определяется по формуле:
1,15Ц – масса цементного камня с учетом химически-связанной воды, кг на 1 м3 арболита.
Для установления оптимального расхода цемента необходимо изготовить и испытать три серии образцов с разным расходом цемента: одну с намеченным исходным расходом 330 кг/м3 и две дополнительные серии с расходом цемента на 15% меньше и больше принятого, т.е. 280 и 380 кг/м3.
Для каждого расхода цемента принимаем три предварительных расхода воды – установленный по табл.4 (360 л/м3) и на 5% больше и меньше, т.е. с учетом воды в растворе ХД и заполнителе. Расход древесного заполнителя оставляем неизменный. Для проведения опытных замесов для всех трех составов определяем расходы материалов на 15 литров по формулам, для первого состава (исходного):
Расход цемента Ц1 = (Ц*15)/1000=(380+15)/1000=4.96кг
Расход дробленки Дсух1=(Дсух*15)/1000=(220*15)/1000=3.30кг
Расход воды В1 = (В*15)/1000=(360*15)/1000=5,4кг
Расход химической добавки ХД1= (ХД*15)/1000=(8*15)/1000=0. 12кг
Для остальных двух составов расходы материалов рассчитываются аналогично.
Химические добавки растворяются в воде затворения опытного замеса.
Проводятся опытные замесы, в процессе которых проверяется жесткость арболитовой смеси по техническому вискозиметру. Жесткость арболитовой смеси должна соответствовать – 60 сек. и регулируется предварительным расходом воды. Если рассчитанное количество воды не обеспечивает получение требуемой жесткости, его увеличивают или уменьшают. Подогнав жесткость арболитовой смеси под требуемую, определяют среднюю плотность смеси, для этого заполняют стандартный мерный цилиндр объемом 5 л. Мерный цилиндр вместе с насадкой устанавливают на вибростол и закрепляют, а затем заполняют арболитовой смесью до половины насадки, устанавливают сверху на поверхность смеси пригруз, обеспечивающий давление, равное принятому при производстве стеновых строительных блоков, но не менее 0,004 МПа и вибрируют в течение 30-60 сек. до прекращения оседания пригруза. После этого снимают пригруз и насадку, срезают избыток смеси и заглаживают поверхность. Затем взвешивают. Среднюю плотность арболитовой смеси в кг/м3, вычисляют как среднюю двух определений по формуле:
Pcm= (m-m1)/V,
где m – масса мерного сосуда с бетонной смесью, гр;
m1 – масса мерного сосуда без смеси, гр;
V – объем мерного сосуда, см3.
Определив среднюю плотность, определяем объем приготовленной арболитовой смеси – Vсм по формуле:
Vom= СуммаP/pm,
где SР=Ц1 +Дсух 1 +В1 +ХД1 сумма материалов используемых при опытном замесе.
Определив объем приготовленной смеси, вычисляю фактические расходы материалов в кг/мпо формулам:
Фактический расход цемента Цф = (Ц1/Vcm)*1000
Фактический расход дробленки ДсухФ= (Дсух1/Vom)*1000
Фактический расход воды Вф = (В1/Vom)*1000
Фактический расход ХД = ХДср=(ХД1/Vom)*1000
Для остальных двух составов средняя плотность и фактические расходы материалов определяются аналогично. Из подобранных смесей изготавливаются контрольные кубы размером 15x15x15 см в количестве 3 шт. для каждого состава. Укладка арболитобетонной смеси в формы производится так же, как и при определении средней плотности смеси. Отформованные кубы в течение 1-х суток твердеют в формах и еще 27 суток (при температуре 20 +/- 2С и относительной влажности воздуха 70 +/- 10%) после распалубки. После твердения на кубах определяют среднюю плотность и прочность при сжатии в Мпа.
Средний предел прочности при сжатии образцов для каждого из трех расходов цемента с оптимальным для каждого из них расходом воды наносим на график. По оси абсцисс откладываем расходы цемента на 1 м арболита, по оси ординат – предел прочности образцов арболита при сжатии в МПа. Проводим через полученные точки прямую и получаем зависимость прочности арболита при сжатии от расхода цемента. По графику определяем требуемый расход цемента для получения арболита заданного класса В2 при принятых условиях уплотнения и твердения. Расходы остальных материалов определяются по фактическим расходам трех составов арболита по интерполяции. После проверки подобранного состава в производственных условиях он рекомендуется для массового производства.
Вы также можете посмотреть следующие разделы
- Вяжущие вещества
- Заполнители
- Микрозаполнители
- Химические добавки
- Вода для бетонов
- Условия твердения строительных стеновых блоков
- Способы определения жесткости бетонной смеси
- О цементно-грунтовых строительных стеновых блоках
- Основные характеристики грунтов для производства стеновых строительных блоков
- Цементы для изготовления стеновых строительных блоков
- Подбор составов цементогрунта
- Основные требования к строительным стеновым блокам из грунтобетона
- Об арболитовых блоках
- Классификация арболитовых стеновых блоков
- Материалы для производства строительных арболитовых блоков: Органический целлюлозный заполнитель
- Материалы для производства строительных арболитовых блоков: Вяжущие вещества
- Материалы для производства строительных арболитовых блоков: Химические добавки
- Твердение и тепловая обработка стеновых арболитовых блоков
- Требования к стеновым блокам из арболита
- Арболитовые блоки и опилкобетонные блоки – отличия
- Дом из арболитовых блоков или дерева: что выбрать?
- О саманных блоках
- Основные требования к блокам из самана
- Материалы для производства саманных стеновых блоков: Вяжущее – глинистые грунты
- Материалы для производства саманных стеновых блоков: Заполнители
- Методы испытания глинистых грунтов для производства самана: Методика определения содержания глинисты
- Методы испытания глинистых грунтов для производства самана: Методика определения содержания глинисты
- Методы испытания глинистых грунтов для производства самана: Методика определения вязкости глинистого
- Подготовка грунта к производству саманных строительных блоков
- Сушка и хранение саманных строительных блоков
- Мероприятия по повышению прочности и водостойкости стеновых саманных блоков
- Особенности производства саманных строительных блоков в зимнее время
- Изготовление блоков из бесцементных бетонов
- Про шлакощелочной бетон
- Требования к материалам для изготовления шлакощелочного бетона
- Подбор состава шлакощелочного бетона
- Рекомендуемые ориентировочные составы тяжелых шлакощелочных бетонов
- Изготовление стеновых бетонных блоков из легких шлакощелочных бетонов
- Изготовление стеновых бетонных блоков из мелкозернистых шлакощелочных бетонов
- Изготовление стеновых бетонных блоков из арболита на шлакощелочном вяжущем
- Изготовление блоков с декоративным слоем
- Приготовление и нанесение декоративных растворов
- Составы декоративных растворов
состав, пропорции, технология изготовления в домашних условиях
Арболитовые блоки – это строительный материал, применяемый для возведения малоэтажных домов (не более 2 этажей), хозяйственных построек, перегородок и в качестве теплоизоляции. Для его изготовления используются такие компоненты как портландцемент, древесные отходы, добавки и вода. Пропорции зависят от требуемой марки. Он бывает теплоизоляционным и конструкционно-теплоизоляционным. В отличие от опилкобетона для арболита не нужен песок.
Компоненты и пропорции
В состав входит цемент, заполнитель, добавки и вода. Для изготовления качественных блоков рекомендуется использовать портландцемент марок М300-М500, но не ниже. Для теплоизоляционных понадобится М300, конструкционно-теплоизоляционных – от М400. Расход зависит от требуемой марки по прочности и вида наполнителя.
В качестве заполнителя используется щепа хвойных и твердолиственных пород деревьев, также может добавляться кора и хвоя, но в небольших количествах – 5-10 %. Щепки могут быть заменены на костру льна. Нельзя использовать отходы от лиственниц или только изготовленные. Щепки можно разбавлять опилками или древесной стружкой в соотношении 1:1. Перед применением свежей щепы ее оставляют на 3 месяца вне помещения, чтобы разрушились вещества, содержащие сахар, или обрабатывают известью.
Главное требование к наполнителю – это размер. Он не должен быть слишком крупным, так как при попадании на него воды он начинает разбухать. В итоге щепки разламываются. Оптимальным размером является длина до 2,5 см, ширина 1 см, толщина от 2 до 5 мм, форма игольчатая.
Если используется костра льна, то следует сначала ее подготовить, так как она содержит большое количество сахара, который ухудшает адгезионные характеристики цементного порошка. Для этого ее поливают известковым молоком в пропорции 1 часть извести к 4 частям костры. После чего оставляют на двое суток. 2 раза в день кучу перемешивают, чтобы вся костра льна равномерно пропиталась известковым молоком. Эта обработка не только улучшает адгезию наполнителя с вяжущим компонентом, но и уменьшает расход последнего.
Для достижения необходимой прочности и плотности в состав смеси из щепы и портландцемента вносятся химические добавки. Благодаря им разрушаются сахара, находящиеся в древесных отходах, и значительно ускоряется процесс схватывании раствора, улучшается показатель водонепроницаемости и увеличивается срок эксплуатации.
К добавкам относятся хлористый кальций, жидкое стекло, известь и сернокислый алюминий. Чаще всего используется хлористый кальций и сернокислый алюминий. Если добавить алюминий, то прочность блоков значительно возрастает, так как этот компонент устраняет все негативные последствия сахара.
Пропорция добавок не должна превышать 2-4% от всего объема вяжущего наполнителя. Их можно использовать как по отдельности, так и комбинировать, например, хлористый кальций с алюминием в соотношении 1:1. Перед тем как добавить в состав, их разводят водой. Расход материалов зависит от требуемой марки по прочности.
Воду для замешивания смеси можно брать практически любую, главное, чтобы она была без грязи и других подобных примесей. Температура должна быть не ниже +15°С. Иначе значительно снизится скорость процесса гидратации цемента.
Перед тем как сделать арболитовые блоки своими руками, нужно рассчитать пропорции. Для этого рекомендуется умножить число требуемой марки на 17, например, если необходим М25, то 17*25=425 кг цемента потребуется для изготовления 1 м3.
Приблизительное соотношение компонентов следующее: 1 часть древесных отходов, 1 часть вяжущего порошка и 1,5 части добавок, разведенных водой. Для замешивания смеси арболита марки М15 потребуется около 270 кг портландцемента, 280 кг щепы, примерно 12 кг добавок и 280 л воды. Для М20 – 330 кг цементного порошка, 300 кг древесных отходов, столько же химических добавок и 40 л воды.
Технология производства
Чтобы изготовить блоки в домашних условиях, потребуется самому сделать формы, причем лучше всего разборные, тогда во время вытаскивания меньше риск повредить материал. Сооружаются формы из деревянных досок или фанеры. Внутри рекомендуется отделать их линолеумом или другим подобным материалом, чтобы смесь не присохла к стенкам. Размеры могут быть любыми, в зависимости от назначения.
Формы устанавливаются на ровном месте, чтобы состав распределился равномерно. Приступают к приготовлению раствора своими руками. Древесные отходы засыпают в бетономешалку, вносят цементный порошок и воду с добавками. Все перемешивается в течение 10 мин до однородной консистенции. Химические добавки лучше всего вносить методом распыления, так они распределятся по всем щепкам равномерно.
Как только смесь готова, ее разливают по формам. Во время заливки ее нужно постоянно утрамбовывать, чтобы удалить все пустоты. Из-за оставшегося внутри блока воздуха сильно снижается прочность. Удалять пустоты лучше всего специальным оборудованием, например, вибропрокатом.
Готовые формы оставляют для затвердевания, накрыв пленкой. При температуре +15°С арболитовая смесь достигнет 50%-ной прочности за 5 суток, а при +40°С схватится полностью за 2 дня. Во время замешивания не стоит всыпать сразу всю дозировку компонентов, лучше всего делать это частями. Это поможет избежать появления комков.
Преимущества:
- низкий коэффициент теплопроводности;
- устойчивость к огню;
- невысокая стоимость;
- хороший показатель на изгиб.
При движении фундамента во время пучения грунта арболит не растрескивается, а при повышенных нагрузках лишь слегка продавливается. Различается марками по прочности. Маркируется она буквой М и числом после нее: М5, М10, М15, М25, М35 и М50. От М5 до М15 – теплоизоляционный, М25-М50 – конструкционно-теплоизоляционный.
Главный недостаток – в условиях повышенной влажности обязательно необходима пароизоляция и защита от атмосферных осадков. Снаружи блоки окрашивают, а изнутри закрывают пароизоляционной пленкой.
состав, особенности производства и характеристики
Арболит – сравнительно новый строительный материал, отличающийся впечатляющими свойствами, речь о которых пойдет ниже. Если внимательно проанализировать тематические статьи и публикации, становится очевидным, что большинство специалистов высоко оценивают арболитовые блоки, скромно умалчивая о недостатках этого материала. Впрочем, в нашем мире нет ничего идеального, особенно, если речь идет о строительной отрасли.
Для максимально эффективного применения арболита, и нивелирования его «минусов», следует внимательнее остановиться на его технических характеристиках, особенностях использования.
Особенности производства арболита
Остановимся подробнее на составе и технологических особенностях производства строительного материала. Качество выполнения ряда технологических процессов обуславливает наличие или отсутствие некоторых «минусов» арболита.
Это очень важный аспект, поскольку материал позиционируют, как подвид легких бетонных решений с крупноячеистой структурой.
Главная его особенность – в качестве наполнителя применяют древесную щепу, благодаря которой получается «монолитное цементное тесто».
Материал получил широкое распространение в современном строительстве:
- теплоизоляционные плиты;
- блоки с пустотелой структурой;
- блоки крупного формата;
- густые смеси для образования ограждающих решений, готовых конструкций.
Состав арболитовых блоков
Для производства арболитовых блоков применяют ряд ингредиентов:
- цемент;
- вода;
- химические компоненты;
- натуральная древесная щепа.
Вода. Чтобы получаемый арболит соответствовал высоким техническим характеристикам, его готовят в строгом соответствии с технологическими предписаниями, рекомендациями мастеров. Воду, в которую добавляют различные пластификаторы и минерализаторы заблаговременно. Если говорить об ингредиентах арболита, то их используют в таких пропорциях:
Что касается деревянной щепы, то ее добавляют в специальный смеситель. Пользоваться традиционными бетономешалками гравитационного типа не рекомендуется, поскольку она не в состоянии обеспечить необходимый уровень гомогенизации. Минерализатор, растворенный в воде тщательно перемешивают, а также равномерно распределяют по всей площади натуральной щепы. Продолжительность перемешивания не превышает 30 секунд. Только после этого в готовый состав вносят цемент. На перемешивание перечисленных компонентов отводится до 3-х минут.
Химические добавки. В составе древесного наполнителя присутствуют натуральные сахара, препятствующие естественной адгезии с деревянными микрочастичками. Чтобы решить столь актуальную проблему специалисты прибегают к 2-м методам:
- Обработку деревянной щепы при помощи химических соединений.
- Предварительное высушивание натурального дерева в течение 2-3-х месяцев.
- обеспечивает водонепроницаемость натурального компонента;
- увеличивает биологическую устойчивость сырья.
Натуральная древесная щепа. Прочностные характеристики рассматриваемого материала зависят от физических размеров и калибра натурального сырья. Для производства качественного арболита важно использовать только природную щепу. Размеры этого ингредиента регламентируются ГОСТ-ами. Опытные мастера рекомендуют пользоваться частичками с физическими размерами в 40х10х5 мм.
Профессионалы используют сырье со следующими размерами:
- толщина – от 3 до 6 мм;
- ширина – от 6 до 11 мм;
- длина – порядка 26 мм.
В преобладающем большинстве случаев производство арболита поставлено на поток около деревоперерабатывающих предприятий и лесопилок. Что касается вида древесины, то она никак не влияет на итоговое качество подготавливаемого сырья.
Производство арболитовых блоков
После перемешивания компонентов, описанных выше, формирование строительных блоков важно завершить в течение 15 минут. Существует несколько подходов к формированию блоков, исходя из выбранного производственного подхода:
- использование специализированной выброустановки с дополнительной нагрузкой;
- применение вибростанков;
- производство материала вручную;
- ручное изготовление без механических элементов.
Блоки, произведенные механическим способов зачастую гораздо качественнее аналогов, изготовленных вручную. Если рассматривать плотностные характеристики, геометрию и размеры изделий, то они абсолютно идентичны.
В кустарных условиях применяют специальную опалубку. В некоторых случаях ее проблематично удалить из-за жидкого раствора.
Арболитовые решения не отличаются по составу, при этом их характеристики могут существенно отличаться от партии к партии, метода уплотнения и степени сжатия. Главная задача прессования жидкого состава – повышение плотности итоговой консистенции, увеличение ее прочностных характеристик.
Методику вибрации на этапе уплотнения используют строго дозировано. Если злоупотреблять методикой, существует высокая опасность осаждения ингредиентов на дне. Форменное прессование направлено не только на то, чтобы повысить плотность готового изделия. Ключевое его предназначение – обеспечить равномерное распределение консистенции по всему объему смеси.
Что касается цементного теста, то оно действует по аналоги с клеем. Корректируется только концентрация натуральных ингредиентов, их толщина и объем.
Блоки уплотняют на протяжении того периода времени, которого будет достаточно, чтобы переориентировать направленность наполнительных зерен. Это способствует увеличению эффективной площади контакта щепок с составом. В арболите не происходит никакого деформирования или сжатия.
Усадка арболита
Многие полагают, что арболит является материалом, не подверженным какой-либо усадке. Впрочем, установлено, что в первые 3-4 месяца в этом материале все же наблюдаются минимальные усадочные реакции. Зачастую они завершаются на этапе производства арболитовых блоков. Допустимой считается усадка в пределах от 0.5 до 0.85%.
Если придавить материал другими изделиями, может фиксироваться еще незначительная корректировка по высоте блоков. Потому опытные мастера не проводят штукатурные или отделочные мероприятия в течение первых 3-4-х месяцев по завершению основного этапа работ.
Огнестойкость арболита
С точки зрения огнестойкости арболитовые материалы могут похвастаться такими параметрами и характеристиками:
- уровень воспламеняемости – В1, что соответствует материалам, которые практически не воспламеняются;
- значение горючести – Г1;
- Д1 – материал образует минимальное количество дыма при воспламенении.
Арболит своими руками в домашних условиях пропорции — из чего состоит арболитовый блок?
Монолитный арболит своими руками: как приготовить заливной арболит
Монолитный арболит своими руками приготовить не сложно. Главное удобство в том, что это делается непосредственно на стройплощадке. По составу и пропорциям, а также по своим характеристикам и свойствам он ничем не отличается от блочного.
Номенклатура монолитного арболита
Номенклатура арболита монолитного такая же, как и у блочного — существует 2 вида:
- Конструкционный. Имеет плотность от 500 до 850 кг/куб. м. Соответствует классу прочности В1, В1,5, В2, В2,5. Используют для возведения несущих стен и перегородок зданий до 2-х этажей.
- Теплоизоляционный. Его плотность от 300 до 500 кг/куб. м. Класс прочности — В0,35, В0,5, В0,75. Применяют для заливки пазух и межстеных пустот для теплоизоляции и звукоизоляции.
Прочность заливного арболита зависит от используемой марки цемента и качества уплотнения смеси. При недостаточной прочности выполняют армирование арболита.
Готовим монолитный арболит: состав и пропорции смеси
Монолитный арболит на 80-90% состоит из щепы, как заполнителя, цемента, воды и химических добавок, ускоряющих твердение раствора и для устранения влияния сахаров древесины.
Щепа для арболита по ГОСТу должна иметь определенный размер и форму. Желательно использовать хвойные породы древесины, кроме лиственницы. В лиственных породах содержится немного больше древесных ядов, их также можно использовать.
Пропорции минеральной добавки
В качестве минеральных добавок для ускорения твердения раствора, обработки щепы, увеличения подвижности раствора можно использовать различные химические компоненты описанные в статье «Химические добавки для арболита». Самые распространенные и в то же время эффективные добавки это – хлористый кальций (технический CaCl2), жидкое стекло, сернокислый алюминий, известь-пушенка.
Соответственно существует много рецептов приготовления монолитного арболита. В одних рецептах подготавливается и обрабатывается древесина, в других – добавляют химический компонент непосредственно в смесь.
По одному из рецептов щепу вымачивают в извести (80 кг извести на куб древесины), отжимают. Затем сверху посыпают порошком негашеной извести (80 кг), перемешивают, разравнивают, высушивают и добавляют в смесь. Таким образом, избавляются от древесных сахаров, влияющих на прочность монолитного арболита.
Возиться со щепой, да тем более с такими объемами для строительства – дело достаточно затратное по времени, требующее площадей для этого процесса. Поэтому быстрым вариантом приготовления монолитного арболита будет применение хлористого кальция или сульфата алюминия (сернокислого алюминия). В этом случае щепу можно не обрабатывать, но будет лучше, если она отлежится на открытом воздухе, под солнцем и дождем, пару месяцев (не в куче!). Также, если есть возможность, ее можно замочить в воде, а перед приготовлением смеси высушить. Замачивание и вылеживание – это своего рода элементарная подготовка древесины, позволяющая частично устранить сахара.
На этапе приготовления состава монолитного арболита добавляется хлористый кальций или сульфат алюминия 2-5% от массы цемента. Так какая же все-таки пропорция химической добавки для арболита, 2% или 5%? Это зависит от марки и от качества цемента. Состав одной и той же марки (например, М500) но разных производителей на самом деле может отличаться качеством. Поэтому рекомендуют сделать тестовый замес. Если при добавлении хлористого кальция 5% от массы вяжущего на отвердевшем материале появятся «высолы» (белого цвета соляные выцветы), то процент содержания химического компонента нужно уменьшать. Высолы говорят о том, что цемент хороший и 5% для состава многовато. В то же время 2% может быть мало. Пару тестовых замесов стоит сделать.
Важно знать! Конкретной пропорции химического компонента для монолитного арболита нет! Ее всегда нужно определять в зависимости от качества используемого цемента и щепы (качество, порода древесины, размеры).
Некоторые не хотят заниматься подборкой пропорции хлористого кальция. И, чтобы не образовывались соляные выцветы, добавляют в состав жидкое стекло. Например, 2% хлористого кальция и 3% жидкого стекла от массы цемента. Но жидкое стекло достаточно дорогое, поэтому для многих экономичнее сделать пару тестовых замесов и определить пропорцию хлористого кальция.
Пропорции щепы, цемента и воды на 1м3 заливного арболита
Пропорция зависит от того, какой вид монолитного арболита вы готовите: конструкционный или теплоизоляционный.
Рассмотрим пропорции состава на 1м3 заливного монолитного арболита при использовании вяжущего марки М400 и абсолютно сухой щепы хвойных пород древесины:
Конструкционный монолитный арболит
В2,5(М25) – 380 кг цемента, 250кг древесного заполнителя, 440 литров воды;
В2,0(М20) – 350 кг, 230кг, 400 литров;
В1,0(М15) – 320 кг, 210кг, 360 литров;
Теплоизоляционный монолитный арболит
В0,75(М10) – 300 кг цемента, 190кг древесного заполнителя, 430 литров воды;
В0,35(М5) – 280 кг, 170кг, 300 литров;
Корректировка состава
Если вы используете другую марку цемента, то пропорция высчитывается с применением коэффициента: для М300 коэффициент 1,05, для М500 – 0,96, для М600 – 0,93.
Пропорция щепы дана для абсолютно сухого материала. Обычно это редкость. Поэтому ее количество нужно скорректировать в зависимости от ее влажности – добавить некоторое количество. Для подсчета дополнительного количества умножаем вышеприведенную массу на коэффициент, который рассчитывается как %влажности щепы деленная на 100%.
Например, древесный заполнитель имеет влажность 20%. Получить нужно монолитный арболит класса прочности В2,0. Следовательно: 20%/100%=0,2. Умножаем коэффициент 0,2 на количество сухой щепы 230 кг для В2,0 – 0,2*230=46 кг. В состав дополнительно нужно добавить 46 кг древесного заполнителя.
Процесс замеса
Щепа и хлористый кальций (или другая хим. добавка) перемешиваются в сухом виде, потом добавляется цемент. Достигают однородности состава. Затем из лейки струей добавляется вода с постоянным перемешиванием, до тех пор, пока весь древесный заполнитель со всех сторон не будет покрыт смесью.
Смешивать удобно при помощи строительного миксера или смесителя. Обычно на это затрачивается 5 – 7 минут.
Готовая смесь монолитного арболита – это умеренно влажная масса. Если взять в руку щепу, то из нее не должна вытекать вода!
Если в состав не вводилась химическая добавка, а выполнялась предварительная обработка заполнителя в извести, то процесс перемешивания длиться минут 25, чтобы известь успела погаситься.
Так можно приготовить монолитный арболит своими руками для последующей заливки в возведенную опалубку или несъемную опалубку стен и перегородок, а также заливки полов и перекрытий.
Из чего состоят арболитовые блоки?
Арболит является одним из представителей легкого бетона и используется при строительстве зданий и сооружений любого предназначения. Возведение загородных домов, дач и надворных построек станет бюджетным мероприятием, если в качестве основного материала выбрать арболит. Его применяют в виде блоков для устройства наружных несущих стен и внутренних перегородок, а также из него изготавливают различные плиты и панели.
- Из чего состоит арболит?
- Пропорции компонентов и нюансы изготовления
- Плюсы и минусы
Технические характеристики:
Состав блоков
Арболит производят из древесного наполнителя, связующего, химических составляющих и воды. Древесный заполнитель присутствует в виде отходов деревообработки (ель, пихта, осина, сосна, береза, тополь) и растениеводства (льняная костра, рисовая солома, стебли хлопчатника). Очень крупные частицы после намокания увеличиваются в объеме, это может привести к последующему разрушению, а мелкие возьмут на себя больше цементного раствора. Оптимальный их размер – 40х10х5 мм. Его химическая активность является основным недостатком, поэтому введение древесины свежесрубленных деревьев в состав арболитовых блоков крайне не рекомендуется.
Наиболее востребованным органическим составом считается стружка древесная и щепа в пропорции 1:1 или 1:2. Помимо опилок можно брать отходы льна. Костра должна быть игольчатой формы, шириной 2-5 мм и длиной 15-25 мм. В составе сырья недопустимо присутствие инородных частиц, признаков плесени и гнили, а в зимний период – льда и снега.
Находящийся в льне сахар разрушает цемент, поэтому необходимо ввести в состав арболита химические вещества. Для улучшения качества легкого бетона, костру нужно обработать известковым молочком (2,5 кг извести растворить в 150-200 литров воды на 1 м3 наполнителя) выдержать 2 суток и перемешивать каждый день. Использование этой технологии снизит расход цемента до 100 кг на куб бетона. Еще один способ нейтрализовать сахар – это поместить костру 3-4 месяца на свежем воздухе, что придаст блокам дополнительную прочность.
Минеральным связывающим в составе смеси является портландцемент марки 400, 500 и выше. Чтобы рассчитать количество цемента на 1 куб арболита 16, нужно увеличить его значение в 17 раз. Получается: 16х17= 272 кг. Химические добавки определяют свойства арболитового блока. Независимо от климатического пояса, где будет возводиться сооружение или здание из этого строительного материала, введение их в состав обязательно. Благодаря способности нейтрализации сахара, химические вещества сделают возможным использовать древесные наполнители без ее обработки.
Такими добавками могут служить: растворимое стекло, K2SO4, гашеная известь и CaCl2. Сернокислый алюминий, соединяясь с сахарами, нейтрализует их действие увеличивая при этом прочность готового изделия. Химические вещества применяют как отдельно, так и в сочетании: Al2(SO4)3 и CaCl2 в пропорции 1:1, гашеная известь и растворимое стекло – 1:1. Перед использованием их разводят в воде, после чего соединяют с арболитовой смесью. Общая масса присадок в 1 кубометре не должно превышать 4% от всего веса цемента.
Арболит марки 30 включает добавки: Al2(SO4)3 и CaCl2 – 1:1; Na2SO4 и CaCl2 – в таком же соотношении и в количестве 4 % от всего веса цемента. Na2SO4 и AlCl3 – 1:1 в 2 % от массы связывающей части. При производстве арболита пропорции на 1 м3 замеса должны быть строго соблюдены.
Технология изготовления
Арболитовые блоки можно делать своими руками. Если нужно большое их количество, приобретают бетономешалку, трамбовку, пресс-формы и печь для сушки. Бюджетный вариант предполагает самостоятельное изготовление форм и покупку смесителя составных частей раствора. Пропорции компонентов в арболитовых блоках были рассмотрены выше, поэтому:
1. В бетономешалку постепенно насыпаем древесный наполнитель и заливаем его водой с химическими добавками, тщательно все перемешиваем.
2. Засыпаем портландцемент и, понемногу вливая воду, снова все мешаем.
3. Обрабатываем форму внутри известковым раствором.
4. Готовую смесь накладываем в формы, плотно трамбуя каждый слой. Объем заполняется до уровня 2 см от края.
5. На свободное место укладываем раствор для штукатурки. Разравниваем поверхность при помощи шпателя.
Полученный блок должен находиться в форме около 24 часов, после чего его вынимают и размещают на две недели под навес для постепенной просушки.
Как видно, технология изготовления арболитовых блоков своими руками довольно проста, а соблюдение необходимых пропорций позволит получить на выходе строительный материал, полностью соответствующий его техническим характеристикам.
Преимущества и недостатки блоков
- высокая звуко- и теплоизоляция;
- повышенная пожароустойчивость;
- устойчивость к появлению плесени и к гниению;
- обладает достаточной прочностью;
- отсутствует необходимость в мощном фундаменте;
- легкость и простота монтажа;
- экологичный, невысокая стоимость.
Обладая определенной влагопроницаемостью, конструкции из арболита могут эксплуатироваться в условиях сухого режима. Во всех остальных случаях стены должны быть защищены от влаги изоляционным материалом. При строительстве стен в подвалах и цокольных этажей применение арболитных блоков не рекомендуется. Защитой от воздействия атмосферных осадков служит их гидрофобная окраска или оштукатуривание стен с двух сторон.
Прежде чем самому приступить к изготовлению арболитовых блоков, необходимо все правильно рассчитать и обдумать. При точном соблюдении технологии производства дома из этого строительного материала получатся комфортными, теплыми и недорогими.
Состав арболитовых блоков
По мере того как технический прогресс двигается вперед, появляются все новые материалы для строительства домов своими руками. Если раньше дело ограничивалось деревом, камнем или кирпичом, то сегодня существуют различные виды бетона, которые превосходят другие материалы по характеристикам. Одним из таких материалов является арболит. Это уникальный материал, который вместил в себе преимущества как бетона, так и древесины. Его состав достаточно прост, и вы можете приготовить раствор своими руками. Примечательно, что он может использоваться как обычный бетон, путем заливки смеси в опалубку, а может быть, сделан в виде блоков, для обычной кладки. Арболитовые блоки можно купить в специализированном магазине, или приготовить раствор своими руками, сделав блоки из готовой смеси.
Все что нужно – знать точный состав арболита, пропорции для смешивания смеси и технологию его приготовления. Давайте рассмотрим все детальней.
Арболитовый блок – из чего он состоит
Арболит, из которого формируют арболитовые блоки для кладки, состоит из 3 основных компонентов:
- заполнитель;
- минеральное вяжущее;
- химические добавки и вода.
Путем соединения всех этих элементов получается арболитовый раствор, который впоследствии используется для формирования блоков. Состав достаточно простой и каждый сможет сделать материал для своих целей. Сам по себе материал легкий, поэтому блоки идеально подходят для кадки. Их достоинством, по сравнению с газоблоками и пеноблоками, является большая граница прочности. Они стойкие к трещинам и ударам.
Несмотря на то что главным компонентом является древесные опилки (щепа), арболит высоко ценится и не уступает по характеристикам традиционным материалам. Наоборот, арболитовые блоки хорошо сохраняют тепло и создают хороший микроклимат в помещении.
Органический заполнитель
Львиную долю в составе арболитных блоков занимает древесная щепа. Это основной материал, который входит в его состав. Такой органический заполнитель легко можно приобрести за небольшие деньги. Стоит обратиться в местную пилораму, где есть отходы деревообработки и договориться с работниками. Преимущественно используют хвойные породы дерева и твердолиственные. Пихта, сосна, ель, осина, бук, береза и тополь идеально подходят, чтобы сделать из них арболитовый раствор. Также можно использовать костру льна.
Чаще всего применяется древесный заполнитель: дробленка, стружка с опилками, в пропорции 1:1 или 1:2, щепа, стружка и опилки, в пропорции 1:1:1. Все пропорции измеряются в объеме. К примеру, если нужно добиться соотношения 1:2, то берется 1 ведро древесных опилок и 2 ведра стружки. Опилки легко заменяются кострой льна или конопляными стеблями, на состав это не повлияет.
Какие требования к заполнителю? Прежде всего, важно правильно подобрать их размер. Крупные опилки использовать не рекомендуется, ведь когда изделия вступят в контакт с водой, они могут увеличиться в объеме. В результате блок может разрушиться. Если же использовать слишком мелкие частицы, то увеличивается расход цементной смеси. Рекомендуемый размер частиц – 15 или 25 мм длинной и не больше 2–5 мм шириной. Сырье не должно иметь листья и другие примеси.
Предупреждение! Лиственница и свежесрубленная древесина любых пород в состав арболитовых растворов не добавляется. Это запрещено!
Костра льна
Полноценным заполнителем, добавляющимся в раствор, является костра льна. Так как в ней присутствует сахар, обязательно применяются химические добавки. Чтобы улучшить качества готовой смеси для блоков, костра заранее обрабатывается известняковым молоком, в пропорции: 200 кг костры на 50 кг извести. Затем все выдерживается несколько дней в куче, после чего все готово для производства арболита. Благодаря такой технологии расход цемента значительно уменьшается. На 1 м3 арболита требуется 50–100 кг цемента.
Важно! Если костра льна используется в обычном виде, то конопляные стебли требуют некой обработки. Их нужно предварительно измельчить.
За счет того, что в составе отходов органики есть вещества, растворимые водой, среди которых смоляные кислоты и сахар, это препятствует хорошей адгезии между частицами. Для устранения сахара, древесные щепки требуется выдержать на воздухе 3 или больше месяцев, или обработать его известняком. Во втором случае смесь выдерживается 3–4 дня. Содержимое перемешивается 2 раза на день.
Минеральное вяжущее
Вам никак не сделать раствор своими руками без вяжущего компонента. Он делает арболитовые блоки прочными и пригодными для кладки. В качестве вяжущего вещества используется портландцемент марки М400, М500 или еще выше.
Его расход зависит от вида заполнителя, крупности частиц, марки цемента, характеристик и т. д. Чтобы немного ориентироваться, можно определить расход таким образом: коэффициент 17 нужно умножить на требуемую марку арболита. К примеру, вам нужно приготовить раствор, маркой 15 (B1). В таком случае на 1 м3 арболита потребуется 255 кг цемента.
Химические добавки
Свойства, которые имеют арболитовые блоки, напрямую зависят от химических добавок. Их использование обязательно в любом случае, неважно, в каком климате выполняются работе. Благодаря добавкам, заполнитель можно использовать без выдержки, ведь они нейтрализуют сахар и другие вещества, что улучшает качество готовых блоков.
В качестве таких добавок может использоваться:
- жидкое стекло (силикат натрия). Закрывает все поры в древесине, поэтому влага не попадет внутрь. Используется после удаления сахара;
- гашеная известь. Она расщепляет сахар и убивает микроорганизмы в опилках;
- сернокислотный алюминий. Отлично расщепляет сахар. Благодаря компоненту состав быстрее набирает прочность;
- хлористый кальций. Убивает все микроорганизмы и придает древесине противогнилостных свойства.
Сернокислотный алюминий и хлористый кальций считаются лучшими добавками. Пропорции добавок – 2–4% от массы цемента, или от 6 до 12 кг на 1 м3. Добавки можно сочетать между собой.
Пропорции для арболитовых блоков
Чтобы сделать арболитовые блоки своими руками важно знать не только состав, но и пропорции. Соотношение всех компонентов между собой следующее: 4:3:3 (вода, древесная щепа, цемент). Химические добавки – 2–4% от общей массы.
Для изготовления 1 м3 арболита своими руками, из которого будут сделаны блоки для кладки, вам потребуется:
- 300 кг древесных отходов;
- 300 кг портландцемента;
- 400 л воды.
В раствор добавляется хлористый кальций или другой химикат. Это классический состав, который легко можно сделать своими руками. Все что потребуется: бетономешалка или большая емкость для размешивания, ведра, лопаты, вилы (для перемешивания вручную) и все компоненты арболита. Процесс выполнения работ следующий:
- Наполнитель (щепу) засыпают в емкость и смачивают водой. Тогда сцепление с цементом будет лучше.
- Затем, постепенно добавляется цемент с добавками. Содержимое тщательно перемешивается в бетономешалке или своими руками, при помощи вил.
- Настало время добавлять воду, в которой уже растворены химические добавки. Все снова перемешивается.
- Как цемент, так и воду требуется добавлять не сразу, а понемногу, небольшими порциями.
Так смесь будет легче перемешивать и компоненты будут лучше соединяться между собой.
- После того как сделан раствор, его нужно поместить в подготовленные формочки, чтобы они обрели вид блоков для кладки.
Это состав и пропорции смеси арболитовых блоков, которые можно сделать своими руками. Все что требуется – быть внимательным и четко придерживаться инструкций по его приготовлению. Ниже приводится таблица, которая поможет вам разобраться в том, какие есть марки арболита и каковы пропорции компонентов для его приготовления.
Какой раствор используется для кладки
Это логичный вопрос. Ведь если арболит специфический материал, то может для кладки арболитовых блоков потребуется специфический раствор? Нет. Арболитовые блоки кладутся на обычный цементный раствор, который под силу сделать любому. Он состоит из цемента, песка и воды. Соотношение компонентов – 3:1. Вода добавляется до тех пор, пока раствор не приобретет нужной консистенции. Эта смесь идеально подходит для кладки блоков своими руками.
Итак, зная состав, пропорции и технологию замешивания арболитового раствора, вы можете делать блоки для ваших целей.
- Состав и пропорции раствора для кладки кирпича
- Как сделать цветной раствор для кирпича
- Размер и вес белого силикатного кирпича
- Кирпич облицовочный силикатный
Что происходит с блоком, в составе которого есть только цементный раствор и щепа? Он крошится, подобно пенопласту, и оббивается при транспортировке и укладке. От такого «арболита» можно руками оторвать кусок.
Минерализатор – такой же ключевой компонент, как цемент и щепа.
«Русский Арболит» выбирает для минерализации сульфат алюминия, так как он полностью безопасен: его используют для очистки питьевой воды или в качестве пищевой добавки Е-520. После высыхания блока он полностью деактивируется.
При изготовлении арболита своими руками добавка иногда заменяется известью, что, во-первых, не так эффективно, во-вторых, создает проблемы при армировании конструкции (известь провоцирует корродирование металлических элементов).
Как сульфат алюминия делает блок прочнее?
При взаимодействии древесных сахаров с раствором бетона образуются «цементные яды». Для человека они не несут вреда; такое название дано им за то, что они замедляют схватывание цемента. Чтобы нейтрализовать сахара, нужны минерализаторы – соли. Самой эффективной и экономически выгодной признан сульфат алюминия.
В щепе лиственных деревьев сахаров больше, именно поэтому она не так предпочтительна, как щепа сосновых пород. Если все же приходится использовать древесину лиственных – увеличится и количество минерализатора.
Состав «древесного» бетона арболита: органическая и неорганическая части
Арболит – весьма необычный вид бетона, где основным наполнителем выступают отходы лесоперерабатывающей промышленности – стружка, хвоя и другое. Именно состав и обеспечивает необычные свойства этого строительного материала. Итак, давайте сегодня поговорим про состав для производства арболита и блоков из него по ГОСТу, пропорции, рецепт и технологию производства.
Состав
Как и всякий бетон, материал включает в себя цементирующее вещество и наполнитель – только органического происхождения, а также различные добавки. Происхождение и свойства ингредиентов влияют на качества конечного продукта.
Органические наполнители сообщают арболиту очень значительные тепло- и звукоизоляционные свойства. По прочности материал мало чем уступает бетону с такими же показателями плотности. Такое сочетание качеств возможно лишь при правильном выборе сырья.
О том, как сделать щепу для производства арболита своими руками поговорим ниже.
Более подробно о том, как подобрать состав для арболита и опилкобетонов, расскажет этот видеосюжет:
Органические компоненты
В виде древесного наполнителя применяют несколько видов материала. Далеко не всякая стружка годится в качестве сырья – не стоит путать материал с опилкобетоном. Новый ГОСТ четко регулирует размеры и геометрию добавляемых в арболит фракций.
- Щепа – получают ее методом дробления нетоварной древесины – горбыля, сучков, верхушек и тому подобного.
Для производства арболита используют щепу длиной в 15–20 мм – не превышая 40 мм, шириной в 10 мм и толщиной в 2–3 мм. В промышленных условиях дробление выполняют специальные установки. Практические исследования утверждают, что для достижения лучшего качества при изготовлении дробленая щепа для арболита должна иметь игольчатую форму и быть меньше в размерах: длина до 25 мм, ширина – 5–10 мм, толщина 3–5 мм. Дело в том, что древесина по-разному впитывает влагу вдоль и против волокна, а указанные выше размеры уравнивают эту разницу.
Годится для щепы не всякое дерево: можно использовать ель, сосну, осину, березу, бук, а вот лиственница нежелательна. Древесный материал перед использованием обязательно обрабатывают антисептическими составами, чтобы предупредить развитие плесени или грибков.
- Измельченные кора и хвоя также может применяться. Однако доля их меньше: коры должна быть не более 10% от массы продукта, а хвои – не более 5%.
- Сырьем может выступать рисовая солома, костра льна и конопли, а также стебли хлопчатника.
Материалы измельчают: длина не должна превышать 40 мм, ширина – 2–5 мм. Очесы и пакля, если они оказываются в наполнителе, не превышают 5% от массы. ГОСТ 19222-84 регламентирует размеры фракций, которые получают при измельчении того или иного сырья. И хотя в пропорции ингредиентов допускаются отклонения, отступать от стандартов сырьевых нельзя.
Лен содержит большое количество сахаров, а последние, вступая в реакцию с цементом, разрушают его. Предварительно костру льна вымачивают в известковом молоке – 1–2 дня, или выдерживают на воздухе 3–4 месяца.
Неорганические компоненты
Вяжущим в деревобетоне, а именно так называют арболит, выступают следующие вещества:
- портландцемент – традиционный материал и наиболее популярный;
- портландцемент с минеральными дополнительными компонентами – обычно, таким образом повышают морозостойкость блоков;
- сульфатостойкий цемент, за исключением пуццоланового, обеспечивает стойкость к химически агрессивным веществам.
Согласно требованиям ГОСТ использоваться может лишь материал соответствующей марки:
- не менее, чем 300 для теплоизоляционного деревобетона;
- не менее, чем 400 для конструкционного.
А теперь поговорим про пропорции химдобавки в составе арболита.
Общее количество дополнительных ингредиентов может достигать 2–4% от веса цемента. Большинство из них повышают прочность деревобетона: вещества взаимодействуют с сахарами, которые наличествуют в древесине, и образуют безвредные для цемента соединения.
Конкретное количество ингредиентов определяется маркой арболита. Например, в состав деревобетона марки 30 могут входить:
- хлорид кальция и сульфат алюминия в пропорции 1:1 – не более 4% от массы цемента;
- хлорид кальция и сульфат натрия в пропорции 1:1 – не более 4%;
- хлористый алюминий и сульфат алюминия в пропорции 1:1 – не более 2%;
- хлорид кальция и хлористый алюминий в пропорции 1:1 – не более 2%.
В тех же целях может использоваться и жидкое стекло – силикаты натрия и калия.
Вода
ГОСТ регламентирует степень чистоты воды, но на практике используют любую – центральный водопровод, колодцы, скважина. Для качества арболита принципиальным является температура воды. В состав она добавляется вместе с дополнительными ингредиентами.
Чтобы скорость гидратации цемента была достаточной, нужна вода с температурой не менее +15 С. Уже при +7–+8 С скорость схватывания цемента заметно падает.
Далее будет рассмотрен рецепт, состав пропорции смеси на куб (1м3) арболита своими руками.
Пропорции
Жестко состав арболита не регламентируется. Если требованиям ТУ материал соответствует, то этот показатель считают более важным, чем точность состава. Приблизительные пропорции таковы: 1 часть заполнителя, 1 вяжущего и 1,5 части раствора с химическими добавками.
Более точно состав вычисляется для конкретной марки, где важным является достигнуть требуемой прочности и плотности.
Например, соотношение для обычного деревобетона в расчете на получение 1 куб. м.
Марка | Цемент, кг | Органический заполнитель, кг | Присадки, кг | Вода, кг |
---|---|---|---|---|
15 | 250–280 | 240–300 | 12 | 350–400 |
25 | 300–330 | 240–300 | 12 | 350–400 |
Если древесный наполнитель неоднородный, то долю щепы и стружки в нем определяют как соотношение объемов, например, 1 ведро опилок и 1 ведро стружек. Также допускается 1 ведро опилок и 2 стружки.
- В смеси с дробленкой доли щепы и опилок будут равными – 1:1:1.
- Костра льна и стебли хлопчатника могут замещать опилки в той же пропорции.
О том, как происходит замес смеси арбалитобетона по указанным пропорциям, расскажет это видео:
ГОСТ
Состав арболита регламентирует ГОСТ 19222-84. Стандарт разрешает подбирать состав смеси в лабораторных условиях, но предъявляет жесткие требования к сырью и к параметрам конечного результата. В зависимости от прочности на сжатие и показателей по теплоизоляции выделяют 2 вида арболита:
- теплоизоляционный, то есть, разработанный для утепления стен;
- конструкционный – допускается возведение самонесущих стен.
Показатели этих материалов разные.
Вид арболита | Класс по прочности на сжатие | Марка по прочности при осевом сжатии | Средняя плотность, кг/куб. м. | |||
---|---|---|---|---|---|---|
На измельченной древесине | На костре льна или стеблях хлопчатника | На костре конопли | На рисовой соломе | |||
Теплоизоляционный | В0,35 | М5 | 400–500 | 400–450 | 400–450 | 500 |
В0,75 | М10 | 450–500 | 450–500 | 450–500 | ||
В1,0 | М15 | 500 | 500 | 500 | ||
Конструкционный | В1,5 | – | 500–650 | 500–650 | 550–650 | 600–700 |
В2,0 | М25 | 500–700 | 600–700 | 600–700 | – | |
В2,5 | М35 | 600–750 | 700–800 | – | – | |
В3,5 | М50 | 700–850 | – | – | – |
Поскольку условия эксплуатации изделий из арболита могут быть весьма разными, к ним могут предъявляться дополнительные требования, регламентируемые ГОСТ 4. 212-80.
Именуются марки арболита по ГОСТ 25192-82. Может указываться также структура материала.
Размерные отклонения в изделиях
ГОСТ регулирует возможные размерные отклонения в изделиях:
- по длине, при общей длине блока до 3,0 м – не более 5 мм;
- при длине изделия от 3 до 6 м – 7 мм;
- по высоте и толщине отклонения могут быть лишь в пределах 5 мм;
- погрешность размеров выступов, выемок, полок, ребер и так далее не превышает 5 мм.
Разрешается армирование изделий из деревобетона сетками и стальными стрежнями, регламентируемыми соответствующим ГОСТом.
Так как материал не отличается высокой влагостойкостью, наружную поверхность изделий покрывают слоем декоративного бетона или другого материала с минеральными наполнителями. Внутренний слой может отсутствовать. Допускается отделка цементом или цементно-известковым раствором.
Проверка арбалитовой смеси
Согласно ГОСТ не реже 2 раз в смену проводят проверку арбалитовой смеси:
- оценивают показатель плотности;
- удобоукладываемость;
- уровень расслаиваемости;
- оценка межзерновых пустот.
Для проверки на прочность проводят серию лабораторных исследований, для смеси спустя 7 суток затвердевания, для смеси спустя 28 суток и смеси, которая испытывалась и спустя 7 суток и через 28.
- Морозостойкость оценивают для отделочных и несущих слоев,
- Теплопроводность измеряется по образцам смеси,
- Влажность рассчитывают на пробах из готовых изделий.
Только, если смесь проходит испытания, предлагаемые ГОСТ, ее можно в полной мере считать рабочей и принимать в производство.
Арболит – пример удачного сочетания органического наполнителя и неорганического вяжущего. И как для всех видов бетона, состав в значительной мере определяет качества конечного продукта.
О том, как подобрать состав арболита и замесить ингредиенты для постройки гаража, узнаете из видео ниже:
Состав смеси и пропорции для бетонных блоков
По мере того как технический прогресс идет вперед, появляются новые материалы для строительства дома своими руками. Если раньше это ограничивалось деревом, камнем или кирпичом, то сегодня существуют разные виды бетона, которые превосходят другие материалы по характеристикам. Одним из таких материалов является арболит. Это уникальный материал, сочетающий в себе преимущества как бетона, так и дерева. Его состав довольно прост и вы можете приготовить раствор своими руками.Примечательно, что его можно использовать как обычный бетон, залив смесь в опалубку, а можно сделать в виде блоков, для обычной кладки. Арболитные блоки можно купить в специализированном магазине или приготовить раствор своими руками, сделав из блоков готовую смесь.
Все, что вам нужно знать, точный состав арболита, пропорции замеса смеси и технологию ее приготовления. Давайте подробно рассмотрим каждый.
Арболит, из которого формируются бетонные блоки для кладки, состоит из 3-х основных компонентов:
- наполнитель;
- связующее минеральное;
- химические добавки и вода.
Соединяя все эти элементы, получается бетонный раствор, который впоследствии используется для создания блоков. Композиция довольно проста, и каждый может делать что-то для своих целей. Сам материал легкий, поэтому блоки идеально подходят для ванн. Их преимущество по сравнению с газобетонными и бетонными блоками – это отличный рубеж безопасности. Они устойчивы к трещинам и ударам.
Несмотря на то, что основным ингредиентом являются опилки (щепа), арболит высоко ценится и по своим характеристикам не уступает традиционным материалам.Напротив, бетонные блоки хорошо сохраняют тепло и создают в помещении хорошую атмосферу.
Львиную долю в арболитовых блоках составляет щепа. Это основной материал, который входит в его состав. Такой органический наполнитель легко приобрести за небольшие деньги. Вам следует обратиться на местную лесопилку, где есть древесные отходы, и договориться с рабочими. В основном используются хвойные и лиственные породы. Ель, сосна, ель, осина, бук, береза и тополь идеально подходят для приготовления бетонного раствора.Также можно использовать лен.
Чаще всего используются древесные наполнители: гранулы, стружка и опилки в соотношении 1: 1 или 1: 2, щепа, стружка и опилки в соотношении 1: 1: 1. Все пропорции измерены в объеме. Например, если вам нужно получить соотношение 1: 2, потребуется 1 ведро опилок и 2 ведра щепы. Опилки легко заменяются пожарами стеблей льна или конопли, на состав это не влияет.
Какие требования к наполнителю? Во-первых, важно правильно подобрать размер.Использование крупных опилок не рекомендуется, поскольку при контакте продукта с водой они могут увеличиться в объеме. В результате агрегат может выйти из строя. Если использовать слишком мелкие частицы, это увеличивает текучесть цементной смеси. Рекомендуемый размер частиц – 15 или 25 мм в длину и не более 2-5 мм в ширину. Сырье не должно иметь листьев и других примесей.
Внимание! Лиственница и свежесрубленная древесина любых пород в состав бетонных растворов не добавляются.Запрещено!
Лен ↑
Полный наполнитель, добавляемый в раствор, – лен. Так как в нем есть сахар, обязательно применяйте химические добавки. Для повышения качества готовых смесей для блоков используйте предварительно обработанное известняковое молоко в пропорции: 200 кг костра на 50 кг извести. Затем все выдерживается несколько дней в куче, после чего все готово для производства арболита. Благодаря этой технологии значительно снижается расход цемента. На 1 м Три арболита необходимо 50-100 кг цемента.
Важно! Если лен используется в обычном виде, то стебли конопли требуют некоторой обработки. Их необходимо предварительно измельчить.
В связи с тем, что в составе отходов органических химикатов, растворимой в воде, среди которых есть смоляные кислоты и сахар, предотвращается хорошая адгезия между частицами. Чтобы исключить сахар, щепу необходимо выдерживать на воздухе 3 и более месяцев или обработать ее известняком. Во втором случае смесь выдерживается 3-4 дня. Содержимое перемешивают 2 раза в день.
Без связующего компонента раствор своими руками не приготовишь. Он делает бетонные блоки прочными и пригодными для кладки. В качестве вяжущего используется портландцемент М400, М500 или даже выше.
Его расход зависит от типа наполнителя, размера частиц, типа цемента, характеристик и т. Д., Чтобы немного сфокусироваться, вы можете определить расход следующим образом: соотношение 17 необходимо умножить на желаемую марку арболита. Например, вам нужно приготовить раствор марки 15 (В1).В этом случае на 1 м Три арболита потребуется 255 кг цемента.
Свойства, которыми обладают арболиты, напрямую зависят от химических добавок. Их использование обязательно в любом случае, в каком бы климате ни работали. Благодаря добавкам наполнители можно использовать без старения, потому что они нейтрализуют сахар и другие вещества, что улучшает качество готовых блоков.
В качестве таких добавок могут использоваться:
- стекло жидкое (силикат натрия).Закрывает все поры в древесине, чтобы влага не попадала внутрь. Используется после удаления сахара;
- Известь гашеная. Она расщепляет сахар и убивает микроорганизмы в опилках;
- серная кислота алюминий. Прекрасно расщепляет сахар. За счет составной части быстро набирает прочность;
- хлорид кальция.
Убивает все микробы и придает дереву антисептические свойства.
Сульфат алюминия и хлорид кальция – лучшие добавки. Доля добавок от 2 до 4% от массы цемента, или от 6 до 12 кг на 1 м. Три .Добавки можно комбинировать.
Для изготовления бетонных блоков своими руками важно знать не только состав, но и пропорции. Соотношение всех компонентов следующее: 4: 3: 3 (вода, щепа, цемент). Химические добавки 2-4% от общего веса.
Для изготовления 1 м Три арболита своими руками, из которых изготавливаются блоки для кладки, вам понадобятся:
- 300 кг древесных отходов;
- 300 кг портландцемента;
- 400 л воды.
В раствор был добавлен хлорид кальция или другое химическое вещество. Это классическая композиция, которую легко сделать вручную. Все, что вам нужно: миксер большой емкости или для перемешивания, ведра, лопаты, вилка (для ручного перемешивания) и все компоненты арболита. Процесс выполнения работ следующий:
- Наполнитель (щепа) насыпают в емкость и смачивают водой.
Тогда сцепление с цементом будет лучше.
- Затем постепенно добавляется цемент.Содержимое тщательно перемешивают в бетономешалке или руками, вилкой.
- Пора добавить воду, в которой растворены химические добавки. Все снова перемешалось.
- Как цемент и воду, которые нужно добавить сразу, но медленно, небольшими порциями. Таким образом, смесь легче смешивается и компоненты лучше соединяются между собой.
- После раствора укладываем его в подготовленные банки, чтобы они имели форму блоков для кладки.
Это состав и пропорции смеси бетонных блоков, которые можно сделать своими руками.Все, что требуется, – это соблюдать осторожность и строго следовать инструкции по его приготовлению. Ниже представлена таблица, которая поможет вам понять, что такое марка арболита и каковы пропорции компонентов для ее приготовления.
Это логичный вопрос. Ведь если арболит специфический материал, может ли кладка бетонных блоков потребует определенного решения? Нет. Арболитные блоки укладываются на обычный цементный раствор, из которого можно сделать любой. Он состоит из цемента, песка и воды.Соотношение смешивания – 3: 1. Воду добавляют до тех пор, пока раствор не достигнет желаемой консистенции. Эта смесь идеальна для укладки блоков своими руками.
Итак, зная состав, пропорции и технологию замешивания бетонного раствора, вы сможете изготавливать блоки под свои цели.
Связанные с контентом
Древесные отходы в бетонных блоках, изготовленных методом вибропрессования
Для изготовления образцов ПСБ использовался уплотнитель с одним цилиндром для виброуплотнения (пневмовибратор) (рис.5). Цилиндр имеет размер 100 мм в диаметре и 200 мм в высоту. Арболит вводится в цилиндры двумя одинаковыми слоями по 1,7 кг каждый.
Рис. 5Схема внутренней части камеры виброуплотнения
Продолжительность вибрации каждого слоя PSC составляла 15 с (определено серией калибровочных испытаний). Затем к образцу прикладывают желаемую силу уплотнения. Виброуплотнение выполняется с помощью вибрации в горизонтальной плоскости и увеличивающейся осевой силы по вертикали, прилагаемой с помощью поршня ко всему сечению образца.Пневматический домкрат, работающий со сжатым воздухом, может создать максимальное давление 6 бар. Требуемое давление уплотнения достигается через 2 или 3 с. Вибрация имеет частоту 250 Гц и амплитуду 2 мм. Комбинированное действие уплотнения и вибрации способствует образованию гранулированного бетона, что очень быстро приводит к хорошей плотности.
Выбор времени вибрации и силы уплотнения
Время вибрации и сила уплотнения являются основными параметрами, которые будут влиять на развитие бетона, полученного путем виброуплотнения, и его механические свойства.Оптимальное время вибрации было определено серией испытаний на компактность для 3 бетонных смесей (PSC0, PSC30 и PSC60). Плотность рассчитывалась как отношение вибрирующего объема бетона к начальному объему для одного слоя арболита (1,7 кг) в разное время вибрации. Результаты представлены на рис. 6.
Эволюция компактности PSC в зависимости от времени вибрации
На рис. 6 видно, что вибрация в течение 15 с дает оптимальную компактность для 3-х древесно-бетонных смесей.Это оптимальное время вибрации является обычным для бетонных смесей PSC.
Величина напряжения уплотнения для производства арболита была определена на основе измерений механической прочности в течение 7 дней на трех образцах Ø10×20 см в соответствии с EN 12390–3 из-за сроков поставки продукции заводом-изготовителем. Испытания на сжатие также проводились через 28 дней и показали очень низкое изменение сопротивления (менее 1 МПа для образца, изготовленного без усилия уплотнения, и менее 2 МПа для образца, изготовленного с применением усилия уплотнения), поскольку пористость образца была высокой. .Образцы были извлечены из формы и помещены в запечатанные пластиковые пакеты через 24 часа после литья до желаемого испытания в соответствии с EN 12390–2. Результаты представлены на рис. 7.
Изменение прочности на сжатие как функция напряжения уплотнения ( слева ) и образцы PSC0 и PSC30 через 7 дней ( справа )
Изготовление образцов методом виброуплотнения увеличивает механическую прочность смеси.Механическая прочность бетонных смесей PSC0, PSC30 и PSC60 увеличена до оптимальной для напряжения уплотнения 40 кПа (1,8 кН). За пределами этого напряжения механическая прочность снижалась. Поскольку устройство быстро достигает желаемого напряжения уплотнения, это снижение для PSC0, PSC30 и PSC60 можно объяснить скоростью введения высокой нагрузки, которая блокирует зернистую структуру бетона при вибрации.
Уменьшение массы блоков является важным параметром при разработке арболитов ПСБ.Масса образцов измерялась в свежем состоянии. Изменение плотности массы как функция напряжения уплотнения приведено на рис. 8. Уплотнение увеличивает плотность образцов для испытаний. При каждом напряжении уплотнения замена песка топольными опилками делает бетон более легким. Мы можем наблюдать уменьшение массы, когда напряжение увеличивается после 40 кПа, что согласуется с уменьшением прочности на сжатие бетона PSC через 7 дней после напряжения уплотнения.
Изменение массовой плотности свежего бетона PSC0, PSC30 и PSC60 в зависимости от различных напряжений уплотнения
Состав бетона PSC0 соответствует бетонным блокам, производимым компанией партнера по проекту. Эти образцы являются нашим эталонным тестом. Механическая прочность достигает 7 МПа за 7 дней без приложения напряжения уплотнения. Он может утроиться при использовании процесса виброуплотнения с напряжением уплотнения 40 кПа.Этот результат почти такой же, как у Линга (2012). В его исследованиях наблюдалось увеличение прочности на сжатие бетонного блока, изготовленного путем виброуплотнения, в 2,5 раза по сравнению с традиционным производством. Включение опилок тополя в цементный композит значительно снижает его механические характеристики (уменьшение на 50% при замене опилок на 30%; рис. 7). Приложение силы уплотнения позволяет повысить механическую прочность бетонных образцов.
Оптимизация рецептуры PSC
Для оптимизации рецептуры древесного бетона из тополя были изучены степени замещения 30, 40, 50 и 60%. Изменение прочности на сжатие через 7 дней дается как функция уплотнения (рис. 9).
Рис. 9Изменение прочности на сжатие PSC через 7 дней в зависимости от различных напряжений уплотнения
Добавление опилок тополя в бетон PSC сильно влияет на его механические характеристики.Прочность на сжатие снижается в зависимости от степени замещения в бетоне из-за ингибирования древесины на реакцию гидратации цементного композита, полученного изотермической калориметрии (рис. 4). Снижение прочности достигает 50% для PSC30, 56% для PSC40 и 64% для PSC50 без напряжения уплотнения во время изготовления образцов. Сила PSC60 составляет почти 1/3 от силы PSC0 через 7 дней. Для всех PSC изготовление бетонных смесей путем виброуплотнения увеличивает их прочность на сжатие.
Сравнение механической прочности PSC с опилками тополя и без них показывает, что наличие напряжения уплотнения значительно увеличивает прочность PSC на сжатие через 7 дней. Мы можем заметить, что скорость увеличения прочности на сжатие может быть замедлена в соответствии с коэффициентом замещения опилок. Виброуплотнение снижает ингибирующее действие древесины на реакцию гидратации цементного композита и приводит к улучшению пределов механических характеристик.Предлагаемый заменитель 50% песка тополевыми опилками в PSC, ввиду его механических свойств, может быть предложен для реализации древесного бетона в промышленных масштабах путем виброуплотнения.
(PDF) Древесные отходы в бетонных блоках, изготовленные с помощью вибропрессования
строительный материал (Удойо и др. 2006; Нгуен 2010; Чеа и Рамли 2011; Берра и др.
2015). Согласно последним исследованиям, древесные отходы добавлялись в качестве добавки к бетонной смеси или
в качестве замены обычного портландцемента в бетоне.Но замена песка в бетоне
также важна для изучения из-за истощения запасов сырья. Замена
песка древесными отходами дает преимущества легкости и снижает выбросы углекислого газа
в области строительства (Trouy and Triboulot 2012). По этой причине в данном исследовании мы
изучали замещение песка древесными отходами. В рамках исследовательского проекта ARCIR Wood
регион Нор-Па-де-Кале во Франции был заинтересован в переработке побочных продуктов древесины в инновационном производстве строительных материалов
.Изучаемая порода древесины – опилки тополя.
Это оправдано массовым производством этого вида в регионе (CRPF 2006).
В ходе первоначального исследования в нашей лаборатории мы проверили возможность использования древесины тополя на
продуктах в обычном растворе (Xing 2013). Были испытаны различные пропорции замены песка в растворе
древесными частицами тополя, поскольку их классы гранулометрии
относительно близки. Это исследование показало значительное влияние на реологические и теплофизические свойства
.Удобоукладываемость раствора улучшилась с увеличением на
коэффициента замещения песка частицами древесины до оптимального значения 30%.
Однако о проблеме ингибирования реакции гидратации свидетельствовало замедление
и уменьшение тепловыделения, что привело к значительному снижению прочности на сжатие
этих растворов.
Следуя этим результатам, наш выбор применения был ориентирован на полусухие бетонные блоки
.Этот материал не требует высокой прочности и обычно используется в строительной отрасли
. Партнер проекта, компания из региона Нор-Па-де-Кале
во Франции, производит бетонные блоки методом виброуплотнения. Высокочастотная вибрация
сочетается с уплотнением для производства полусухих бетонных блоков. Конечный продукт
имеет более высокую плотность, лучшее сопротивление и более низкую проницаемость, чем у обычного промышленного бетона
(Nguyen 2010).Концепция производства в основном основана на
комбинации очень низкого отношения вода / цемент (W / C) и высокого уплотнения (Ling 2012).
Ожидалось, что введение побочных продуктов древесины в бетонные блоки путем замены примерно
заполнителей позволит облегчить блоки и улучшить термические и
акустические свойства.
Конкретная формула нашего промышленного партнера была взята для нашего исследования в качестве образца. Критерий
, которому должен соответствовать разработанный новый продукт, – это прочность на сжатие 6 МПа в течение 7 дней,
, потому что компания (партнер по проекту) поставляет свои блоки через 7 дней после изготовления.
Испытания на сжатие также проводились через 14 и 28 дней. Они показали очень низкое повышение сопротивления
(менее 1 МПа), потому что продукт сухой; в этих закаленных блоках высокая пористость
. Полученные результаты были использованы для разработки бетонных блоков
с древесными отходами методом виброуплотнения.
В этом исследовании предлагается метод производства нового бетонного материала путем замены песка в пропорции
тополевыми опилками, которые могут использоваться в качестве строительного материала в
областях, требующих низкой прочности.В частности, исследование направлено на понимание
влияния включения побочного продукта древесины тополя на свойства полусухого бетонного блока
. Также проанализирована роль изготовления бетона методом виброуплотнения. Исследование
включает характеристику опилок тополя, влияние пропорции замены песка
в смеси опилками на теплофизические и механические свойства сухого бетона полу
, а также определение оптимального времени и оптимальное виброуплотнение
силы, обеспечивающие максимальную прочность композитного бетона на сжатие.Тесты
исследования были выполнены согласно соответствующим международным стандартам.
S224 Z. Xing et al.
Разница между цементными, шлакобетонными блоками и бетонными блоками
Бетон и шлакоблоки имеют общие общие элементы, но жизненно важный ингредиент имеет решающее значение. Иногда люди используют эти термины как синонимы, но бетон и шлакоблоки очень разныеБетон
Бетон – это предмет, сделанный из цемента и заполнителей.В тот момент, когда ингредиенты смешиваются, происходит химическая реакция, и конечным результатом является бетон.
Заполнители
Бетонные блоки
Бетонные блоки построены из чистого бетона. То есть используемые заполнители – это мелкий щебень или песок.
Шлакоблоки
Теперь о так называемых «шлакоблоках»… Я говорю «так называемые», потому что «шлакоблок» – это несколько устаревший и общий термин для типа структурных блоков, которые можно легко разобрать. много разных вещей.В те времена, когда люди сжигали уголь для обогрева своих домов, и в таких местах, как Bethlehem Steel, были большие коксовые печи, работающие круглосуточно, производилось много «золы» – общий термин для обозначения золы, которая осталась после сжигания угля или аналогичного топлива. . Как и в случае с дровяной золой сегодня, типичная зима оставит домовладельца с большим количеством мусорных баков золы; а угольные электростанции и сталелитейные заводы будут производить тонны этих отходов каждый день.
Таким образом, он использовался для изготовления «шлакоблоков». Они были – и в некоторых случаях до сих пор остаются – той же формы и размера, что и бетонные блоки, но с промышленными отходами в качестве «заполнителя» вместо песка или мелкого гравия, используемых для изготовления актуальный бетон.
Как я уже указывал ранее, разница между бетоном и цементом состоит в том, что «бетон» – это термин для конечного продукта, полученного, когда наполнитель скрепляется с цементом. Таким образом, эти большие грузовики с постоянно вращающимися цилиндрами – это, по сути, автобетононасосы, а не на самом деле «цементовозы». И хотя настоящих шлакоблоков в наши дни мало, кто-то смотрит на штабель того, что правильнее было бы назвать «каменными блоками». или «шлакоблоки» гораздо чаще называют их шлакоблоками, а не бетонными блоками. Шлакоблоки также создаются из бетона, но заполнитель включает угольные шлаки или золу. Следовательно, шлакоблоки намного легче бетонных блоков.
Шлакоблоки – это полые прямоугольные конструкции, обычно сделанные из бетона и угольных шлаков, которые находят применение на строительных площадках. С другой стороны, бетонные блоки часто представляют собой плоские конструкции из стали, дерева или цемента. Существенные различия можно проиллюстрировать в виде таблицы, показывающей различия между шлакоблоком и шлакоблоком.бетонный блок.
Шлакоблоки.
– Обычно делается из бетона, а также из угольных шлаков.
– Намного легче по сравнению с последним из-за пропорции агрегатных компонентов.
– Не очень сильный, поэтому в некоторых местах его часто избегают.
– Они более склонны к изгибу, а коробление и ремонт обычно очень дороги, поэтому их следует избегать.
– практически устарели, так как не производились серийно уже около 50 лет.
– Не обладают значительным пределом прочности на разрыв.
Прочность
Бетон и шлакоблоки производятся с открытыми ячейками, которые могут принимать металлическую арматуру или дополнительный бетон для повышения прочности. Бетонные блоки намного прочнее шлакоблоков. Некоторые строительные нормы и правила прямо запрещают использование шлакоблоков в строительных проектах.
Бетонный блок.
– Состоит из стали, дерева или цемента.
– Обычно более громоздкий, чем шлакоблок.
– Может выдерживать гораздо большие нагрузки по сравнению с шлакоблоками, поэтому во многих местах использование шлакоблоков специально запрещено.
– Более эффективен по сравнению с первым, так как выдерживает большое давление.
– Много используется из-за его неоспоримых сильных сторон и преимуществ перед первым.
– Используется одновременно в смеси с огарком по вертикали для образования прочной структуры по разумной цене из-за его значительной прочности на растяжение.
Вес и прочность.
Я поговорил с несколькими специалистами по этой сложной теме, и все согласились, что настоящие шлакоблоки намного легче по весу, чем бетонные блоки, и что настоящий бетон намного тяжелее, долговечнее и долговечнее.
Может показаться, что сегодняшним строителям нужен только бетонный блок, но это не та ситуация. Если строительные нормы и правила работы позволяют это, многие строители выбирают «шлакоблок», потому что он легче.Настоящие бетонные блоки очень тяжелые, и их подъем быстро устаревает. Так что, хотите верьте, хотите нет, но современные шлакоблоки, которые делают из вулканической пемзы, если поблизости нет угольной электростанции, могут привести к тому, что в действительности цена будет выше.
Если блок новый и тяжелый, это бетон, созданный из песка или гравия; не золы. Если он более старый и легкий, вероятно, это «шлак» – отходы от сжигания угля. Если он новый и легкий, и вы покупаете его новым, продавец должен точно сказать, что в нем: вулканическая пемза или старомодные золы.
Известняк Хьюстон Людер | Даллас / Форт-Уэрт Людер Известняк | Сан-Антонио-Людер Известняк | Остин / Центральный Техас Людерский известняк | Известняк New Braunfels Lueder | Известняк Бомонта | Killeen Limestone | Храмовый известняк
Хьюстонский каменный карьер | Каменный карьер Даллас / Форт-Уэрт | Каменный карьер Сан-Антонио | Остин / Центральный Техасский каменный карьер | Каменный карьер Нью Браунфелс | Каменный карьер Бомонта | Каменный карьер Киллин | Храмовый каменный карьер
Древесные отходы в бетонных блоках
% PDF-1.5 % 1 0 obj > / Метаданные 363 0 R / OCProperties >>>] / ON [464 0 R] / Order [] / RBGroups [] >> / OCGs [364 0 R 464 0 R] >> / Outlines 360 0 R / Pages 2 0 R / StructTreeRoot 3 0 R / Тип / Каталог >> endobj 362 0 объект > / Шрифт >>> / Поля 368 0 R >> endobj 363 0 объект > поток application / pdf
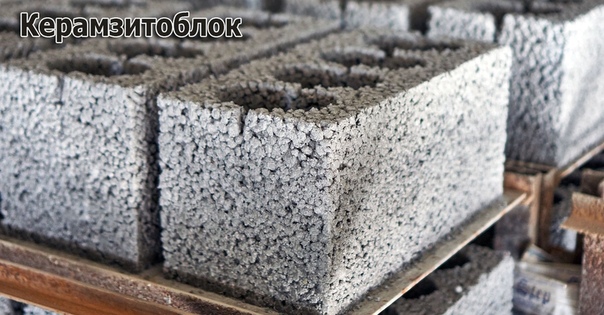

Шлакоблок Vs. Бетонный блок
В этой статье мы поговорим о шлакоблоке и бетонном блоке , которые представляют собой два разных структурных элемента, перепутанных друг с другом. Хотя их основные элементы одинаковы, эти два структурных элемента имеют очень разные свойства.
Сравнение шлакоблока и бетонного блока может быть непонятно с первого взгляда. Несмотря на то, что в их конструкции использованы одни и те же материалы, в шлакоблоке есть лишний материал.Он входит в состав для выполнения различных функций.
Прежде чем рассматривать различия, преимущества и недостатки этих двух материалов, давайте объясним шлакоблок для тех, кто его не знает.
Cinder Block Vs. Бетонный блок
Различия между шлакоблоком и бетонным блоком заключаются в следующем:
Шлакоблок | Бетонный блок | |
1 | Ясень используется в качестве заполнителя в шлакоблоке.![]() | В бетонных блоках ясень используется при строительстве стеновых блоков. |
3 | Шлакоблок изготавливается из бетона и шлакобетона. | Бетонный блок изготавливается из стали, дерева или цемента. |
4 | Шлакоблок легче бетонных блоков. | Бетонный блок тяжелее, потому что он содержит камень и песок. |
5 | Шлакоблок не имеет прочности, чтобы выдерживать высокое давление. | Бетонный блок – твердый строительный элемент с высокой прочностью. |
6 | Поскольку шлакоблок не очень гибкий, его использование вообще запрещено. | Бетонный блок можно использовать практически в любой конструкции, так как он намного прочнее. |
7 | Шлакоблок чаще используется в небольших проектах, таких как садовые стены. | Бетонный блок используется в более ответственных проектах и крупных строительных проектах.![]() |
8 | Шлакоблок – старинный строительный элемент. Серийное производство не производилось почти 50 лет. | Бетонный блок используется чаще из-за его более твердой структуры и других преимуществ. |
9 | Шлакоблок требует большого ремонта, поэтому его общая стоимость выше. | Бетонный блок дешевле, так как не требует ремонта. |
Что такое шлакоблок?
Шлакоблок также изготовлен из бетонного материала.Но внутри тоже есть шлак. Таким образом, он становится намного более легким строительным элементом.
И бетонный блок, и шлакоблок можно укрепить металлической или бетонной арматурой для повышения прочности. Для этого в них есть открытые ячейки.
Цели стен из шлакоблоков
Шлакоблок используется для следующих целей:
- В качестве барьера безопасности
- Для фиксации дверей и окон
- Для украшения стены
- Для дифференциации внешнего вида конструкций
Кроме этих целей, шлакоблок может быть использован в соответствии с потребностями конструкции. Поскольку он используется для самых разных целей, он становится подходящим выбором для строительных работ, строительства складов или ландшафтных работ.
Типы бетонных блоков
Шлакоблок против бетонного блока | Что такое шлакоблоки
Самый важный момент в этой статье
Что такое шлакоблоки?
Шлакоблоки – это полые конструкции прямоугольной формы, обычно сделанные из бетона и угольных шлаков, которые находят применение на строительных площадках.
или
Шлакоблоки похожи по форме и конструкции на бетонные блоки , за исключением того, что вместо песка или гравия большая часть заполнителя представляет собой зола, особенно угольный шлак.
Зольный компонент делает шлакоблоки намного легче, чем традиционные блоки , но они не обладают почти такой же прочностью на разрыв или несущей способностью.
Следовательно, шлакоблоки идеально подходят для таких проектов, как садовая стена или подпорная стена , но не подходят для использования в более крупных строительных проектах.
Также прочтите: Что такое структурные поселения | Причины структурного поселения | Что такое грунтовое поселение и структурное поселение фундамента
Шлакоблоки
Теперь о так называемых «шлакоблоках ». Шлакоблок – это несколько старомодный и общий термин для типа структурного блока, который можно легко изготовить из самых разных вещей.
В то время, когда люди сжигали уголь для обогрева своих домов, в таких местах, как Bethlehem Steel, были большие коксовые печи , работающие круглосуточно, было произведено много « золы » – общий термин для золы – оставленный, когда сжигают уголь или подобное топливо.
Как в золе сегодняшних дров печи , типичная зима оставила бы владельца с бесчисленным количеством мусорных баков стоимостью золы ; угольные и сталелитейные заводы будут производить тонны этих отходов каждый день.
Таким образом, он использовался для изготовления « шлакоблоков ». Они были – а в некоторых случаях до сих пор имеют – той же формы и размера, что и бетонные блоки , но с промышленными отходами, например заполнитель ‘вместо песка или гравия, используемых для превращения бетона в бетон.
Как я указывал ранее, разница между бетоном и цементом состоит в том, что « бетон » – это термин для конечного продукта, созданного, когда заполняющий компонент сохраняется вместе с цементом.
Таким образом, эти большие грузовики с цилиндрами, находящимися в постоянном вращении, по сути, представляют собой бетонные грузовики , а не « цементовозы ».
И хотя настоящие бетонные блоки сегодня в меньшинстве, тот, кто смотрит на груду того, что правильнее было бы назвать « кирпичей » или « ветрозащитными блоками », с гораздо большей вероятностью назовет их бетонными блоками, чем это бетонные блоки.
Шлакоблоки также создаются из бетона, но заполнитель включает золу или золу. Следовательно, шлакоблоки намного легче бетонных блоков .
Шлакоблоки – это полые прямоугольные конструкции, обычно из бетона и угольного шлака, которые используются на строительных площадках. С другой стороны, бетонные блоки представляют собой плоские конструкции из стали , дерева или цемента.
Также прочтите: Что такое соты в бетоне | Причина | Лечение | Тип затирки
Шлакоблоки.
- Как правило, помимо угольного шлака изготавливается из бетона.
- Намного легче по сравнению с последним из-за доли заполнителя.
- Он не очень прочен, поэтому в некоторых местах его часто избегают.
- Они более склонны к изгибу, а изгиб и ремонт часто очень дороги, поэтому их следует избегать.
- Они почти вышли из моды, так как не производились серийно около 50
- Не имеет значительного количества прочности на разрыв.
Прочность шлакоблоков
Бетон и шлакоблоки производятся с открытыми ячейками, которые могут принимать металлическую арматуру или дополнительный бетон для большей прочности.
Бетонные блоки намного прочнее шлакоблоков. Некоторые строительные нормы и правила прямо запрещают использование шлакоблоков в проектах гражданского строительства.
Также прочтите: Что такое соты в бетоне | Причина | Лечение | Тип затирки
Что такое бетонные блоки?
Бетонные блоки состоят из воды, цемента и заполнителей, таких как песок, гравий или щебень .
После смешивания и отверждения эти ингредиенты образуют твердое, прочное и долговечное вещество, идеально подходящее для использования в строительстве. Бетонные блоки имеют различную форму и могут быть сплошными или пустотелыми.
Типы бетонных блоков
1. Пустотные бетонные блоки
Полые бетонные блоки , обычно используемые в строительной отрасли, обычно производятся из легких заполнителей с определенной расчетной нагрузкой , в зависимости от характера элемента, в котором он будет использоваться.
Как правило, полые бетонные блоки имеют пустоты брутто на своей общей площади, а площадь сплошного массива не должна быть меньше половины его площади, чтобы достичь максимально допустимой нагрузки , говорится в исследовании.
Пустоты обычно заполняются раствором из легких заполнителей и .
Есть два типа пустотелых бетонных блоков; несущие пустотелые бетонные блоки и пустотные ненесущие бетонные блоки.
Доступны такие размеры, как , 100x200x400 мм, 200x200x400 мм, 150x200x400 мм, и т. Д.
Также прочтите: Что такое тест конуса спада | Принцип теста на спад | Типы оседания бетона
2. Автоклавный газобетонный блок (AAC)
Ингредиенты такие же, как кирпичи, но с другим составом , который сделал материал контейнером для снижения затрат .
Исследования показывают, что использование автоклавных газоблоков значительно снизило общий расход стали и бетона на 15% и 10% .
Очевидно, что с точки зрения рентабельности автоклавный газоблок проходит через кирпич в нескольких областях, таких как время строительства, адаптация к различным поверхностям, огнестойкость и стоимость .
Для установки блока AAC объявление метода должно быть отправлено на утверждение до начала работы.
3. Бетонные кирпичи
Бетонные кирпичи обычно представляют собой небольшие прямоугольные блоки, систематически уложенные и уложенные друг на друга для создания жесткой стены.
Эти кирпичи обычно делают из обожженной глины или бетона. Некоторые производители используют твердый бетон, в то время как другие играют со своей долей цемента и заполнителей в экономических целях.
Другие производители также создали кирпичи разных цветов по просьбе некоторых клиентов. Бетонный кирпич обычно используется для изготовления заборов, фасадов, так как он обеспечивает хороший эстетический и гладкий вид.
Также прочтите: Что такое покрытие в бетоне | Прозрачная крышка в балках, плитах, колоннах, опорах
4.Полнобетонные блоки
Путь плотнее и больше, чем бетонные кирпичи, массивные бетонные блоки сделаны прочными, тяжелыми и созданы из естественно плотных заполнителей .
Эти массивные бетонные блоки достаточно прочные, чтобы их можно было использовать в больших кирпичных блоках , которые выдерживают нагрузки по своей природе .
Полнобетонные блоки похожи на бетонные кирпичи, но они намного дороже и тяжелее и могут выдерживать большие нагрузки по сравнению с кирпичами .
5. Блоки перемычки
Эти бетонные блоки используются для изготовления перемычек. Эти блоки перемычки производятся по методу таким образом, что они служат каменной кладкой и опалубкой.
Эстетически блоки перемычки имеют глубокую канавку , в которую арматурные стержни помещаются вместе с бетоном.
То есть они служат в качестве несъемной опалубки для балки перемычки.Этот считается эффективным и полезным большинством строителей , поскольку он служит двум разным целям. Продукт два в одном – это.
Также прочтите: Что такое DLC (сухой обедненный бетон) | Преимущество DLC (сухой постный бетон)
6. Блоки для мощения
Брусчатка обычно представляет собой прямоугольную или квадратную коробку из железобетона .
Поскольку эти блоки используются для мощения и на обочинах дорог, они должны быть окрашены красками для бетона повышенной видимости , чтобы водители и водители могли сразу видеть их .
Кроме того, эти блоки должны быть достаточно жесткими, чтобы выдерживать столкновения автомобилей.
Брусчатка также используется в парках, на пешеходных дорожках, а иногда и на парковках. Обычный размер брусчатки – 60 мм.
Также прочтите: Что отслаивается в бетоне | Причины отслаивания бетона | Ремонт бетонных блоков
7. Бетонный блок растяжителя
Опять же, как и угловой блок, бетонные блоки растяжителя используются для объединения блоков каменной кладки.
По внешнему виду бетонный блок примерно такой же, как и обычный полый блок, но его грани расположены параллельно лицевой стороне стены .
Бетонный блок.
- Они состоят из стали, дерева или цемента.
- Обычно тяжелее шлакоблока.
- Он может выдержать гораздо больше, чем шлакоблоки, и во многих местах использование шлакоблоков специально запрещено.
- Очень эффективен по сравнению с предыдущим, так как выдерживает большое давление.