Соломобетонные блоки: изготовление своими руками
Глянул кадры из ESBG-2009, там парни закладывают в каркас блоки, а затем прессуют их домкратами.В связи с чем возникла идея, чтобы (при отсутствии соломы в блоках) прессовать солому прямо в каркасе. Монолитная солома :-)Можно закладывать блоки, предварительно подготовленные вручную (вернее, вножную, как на фотках выше).
По технологии возникает пара вопросов – перемещающиеся вверх по каркасу опалубка и упор для домкрата, а также перевязка. Она обязательна?
Немного поразмыслил.Упор для домкрата. Например, предварительно заготовленные бруски разной длины с шагом 50 см, упирающиеся в домкрат и горизонтальный элемент каркаса в перекрытии.Опалубка. Пара широких досок или сколоченные щиты.
Из стального прута делается две скобы, по ширине щитов, длиной – по толщине каркас+щиты, на концах скобы – петли. В петли продевается прут и таким образом фиксирует щит на другой стороне. Чтобы щиты не падали, подпирать можно чем угодно хоть палками, упертыми в кирпичи. Возможно, конструкция выходит немного неплотная, “гуляющая”, но, думается, что это не принципиально, т.
к. всё равно соломенная кладка перед отделкой постригается пилой, ножом, триммером, бензопилой.Обвязка в этом случае не принципиально. Она ведь для того, чтобы блоки не рассыпались при манипуляциях на пути от пресса до каркаса.
Ну а если принципиальна, то прошить уже запрессованую стену не проблема, веревка, прут и прошивай как угодно, можно сшить и по вертикали, и горизонтали (причем намертво к каркасу).
Опилкобетон – это одна из разновидностей легких бетонов, обладающих пониженной плотностью. Он был разработан в 60-х годах 20 века в Советском Союзе и прошел абсолютно все технические и качественные испытания, после чего был стандартизирован. Массовое применение в частном домостроении и потребительский спрос опилкобетон получил лишь в середине 90-х годов, после чего его уникальные свойства неизменно привлекают потребителей.
Главными преимущественными характеристиками этого стройматериала являются:
- экологическая безопасность;огнестойкость;прочность;массовое отношение влаги;паропроницаемость;теплотехнические показатели;морозостойкость;доступная стоимость материала.

Содержание
- 1 Область применения опилкобетона
- 2 Состав опилкобетона
- 3 Изготовление опилкобетона своими руками
- 4 Производство блоков из опилкобетона
- 5 Преимущества использования арболитовых блоков
- 6 Технология изготовления арболитовых блоков
- 7 Предъявляемые требования
Область применения опилкобетона
Этот строительный материал широко применяется при строительстве домов, дач, коттеджей и хозяйственных построек. Он также используется при работах по утеплению подвалов и реконструкции зданий. При такой реконструкции не возникает необходимости в усилении фундамента.
Для строительства здания из опилкобетона подойдет любой проект, созданный для домов из других материалов. Однако затраты на строительство будут существенно ниже.
Дом, построенный из опилкобетона, достаточно легкий: при площади в 250 м2его вес составляет около 50 тонн. Это обстоятельство позволяет не закладывать сложный фундамент. Кроме этого есть еще множество преимуществ, среди которых можно назвать хорошую звукоизоляцию, простоту сборки, экологичность, экономичность, долгий срок эксплуатации.
Состав опилкобетона
Основой этого строительного материала, как понятно из названия, являются древесные опилки. Кроме этого, в состав входят песок, вяжущие материалы (песок, известь) и вода. Благодаря санитарно-гигиеническим показателям опилкобетон является одним из оптимальных материалов для возведения стен зданий.
Плотность стройматериала зависит от соотношения песка и опилок. Соответственно, плотность тем меньше, чем меньшее количество песка пошло на изготовление опилкобетона.
В этом случае улучшаются теплотехнические свойства, но уменьшается прочность материала. С увеличением количества песка и вяжущих материалов прочность возрастает. Также улучшаются морозостойкость и водонепроницаемость, что в свою очередь препятствует воздействию коррозии на стальную арматуру.
Такая арматура применяется при укладке стен из блоков, сделанных из опилкобетона. Поэтому, прежде чем приступать к изготовлению, необходимо четко знать свойства бетонируемой конструкции. Здесь не бывает мелочей, принимается в расчет толщина стен, количество этажей, наружная, внутренняя стена это будет или несущая конструкция.
В зависимости от состава, опилкобетон подразделяется на марки. Блоки марок М5 и М10 применяются для строительства, реконструкции и утепления подвалов, поскольку им свойственны прекрасные теплоизоляционные характеристики. Марки М15 и М20 наилучшим образом подходят для возведения как внутренних, так и наружных стен домов.
Марки и пропорции опилкобетона:
М5. На 200 кг опилок берется 50 кг цемента, 50 кг песка, 200 кг извести или глины. Плотность – 500 кг/м3.М10.
На 200 кг опилок берется 100 кг цемента, 200 кг песка, 150 кг извести или глины. Плотность – 650 кг/м3.М15. На 200 кг опилок берется 150 кг цемента, 350 кг песка, 100 кг извести или глины.
Плотность – 800 кг/м3.М20. На 200 кг опилок берется 200 кг цемента, 500 кг песка, 50 кг извести или глины. Плотность – 950 кг/м3.
Изготовление опилкобетона своими руками
Заготовка необходимых материалов.Компоненты, входящие в состав опилкобетона, хороши тем, что их не нужно заготавливать заранее. Все составляющие можно купить в магазинах, торгующих стройматериалами, на рынках или складах. Благодаря этому к заготовке можно приступить практически за один день до начала изготовления.
Смешивание компонентов.
Приготовление вручную опилкобетона является очень трудоемким процессом, поэтому для смешивания компонентов по возможности желательно использовать бетономешалку или растворосмеситель. Прежде всего, высушенные опилки необходимо просеять через сито, ячейки которого должны быть по размеру 10*10 миллиметров. Затем опилки смешиваются с песком и цементом.
После этого в приготовленную смесь добавляют глиняное или известняковое тесто и тщательно перемешивают. Получившуюся смесь разводят водой, постепенно добавляя ее в малых порциях через лейку. После каждого долива смесь необходимо перемешать.
Если смесь приготовлена правильно и хорошо перемешана, то при сжатии в кулаке она образует пластичный комок, на котором видны вмятины от пальцев, при отсутствии капель воды. Это является основным признаком готовности смеси.
После этого ее можно формировать в блоки. В этом деле медлить нельзя ни в коем случае, так как по истечении 1,5-2 часов смесь начинает твердеть. Укладывая смесь в форму, ее необходимо хорошо утрамбовать, чтобы исключить наличие воздуха.
Размеры блоков.Такие размеры стандартами не установлены. Они напрямую зависят от толщины стен, ширины простенков и проемов, расстояния от проемов до углов строения, а также от способа укладки. Для наибольшего удобства при строительстве длина участков стены или ширина простенков должны быть кратными блочным размерам.
Толщина блока обычно равняется двум толщинам красного кирпича, учитывая и уложенный между ними раствор. В общем, это составляет 140 миллиметров. Учитывая то, что при кладке часто используется и красный обожженный кирпич, такой подход является очень практичным.
Большие опилкобетонные блоки сохнут достаточно долго. Для ускорения процесса высыхания в них делают 2-3 отверстия, что не только позволяет блоку быстрее высохнуть, но и улучшает теплозащитные свойства этого стройматериала.
Формы для отливки.Наиболее оптимальным вариантом является возведение стен не при помощи опалубки, а из заранее подготовленных блоков.
Они высушиваются в течение трех месяцев, после чего опилкобетон приобретает свою марочную прочность. Перед тем, как начать приготовление смеси, изготавливаются формы для отливки блоков. Форму с опилкобетонного блока снимают не сразу, а по прошествии от трех до пяти дней.
Для ускорения процесса изготовления делают 10-20 форм. Таким образом, процесс не прервется, а также не потратится время на ожидание высыхания блоков. Количество форм напрямую зависит от того количества блоков, которое вы планируете изготовить за один раз.
Формы для габаритных блоков. Для крупных блоков изготавливаются разборные одинарные или двойные формы. Они выполняются в виде сбитых из досок ящиков.
Формы являются разъемными, что позволяет очень быстро их разбирать и собирать. Делаются они из досок, толщина которых составляет 20 миллиметров. Части разъемной конструкции скрепляются при помощи стальных стержней Г-образной формы, обладающих резьбой М8, на которую накручивается барашковая гайка.Формы для небольших блоков.
Для изготовления мелкогабаритных блоков изготавливаются в собранных из 20 миллиметровых досок сотовых формах. В основном такие формы делают для производства 9 блоков из опилкобетона одновременно. По желанию количество ячеек может варьироваться.
Эти формы, состоящие из внутренних и боковых досок, так же легко и быстро собираются и разбираются. Составляющие ячейки внутренние доски крепятся между собой при помощи задвижных пазов. Торцевые же доски прикрепляются к боковым стальными Г-образными стержнями и барашковыми гайками.
Внутренние стенки форм.Чтобы доски, из которых изготавливаются формы для отливки, не впитывали влагу, внутренние стенки обивают кровельной сталью, пластиком или прокладываются полиэтиленовой пленкой. Из формы, подготовленной таким образом, блоки вынимаются очень легко и просто, не приставая к деревянным стенкам.
Учитывая то, что при высыхании происходит усушка блоков, формы делаются немного больших размеров, чем должны получиться готовые блоки. Эта разница должна составлять приблизительно 10%:
- Для цельных блоков с размерами 120*250*140 мм (ширина*длина*высота) размер ящика должен быть 132*235*154 мм.Для блоков с размерами 190*390*140 мм размер ящика составляет 209*430*154 мм.Для блоков с размерами 130*410*140 мм размер формы должен быть 143*450*154 мм.
Производство блоков из опилкобетона
Деревянные формы, перед тем как заполнить их опилкобетонной смесью, устанавливают на поддоны, изготовленные из стали или пластика, предварительно посыпанные тонким слоем опилок. В форме располагают обернутые толем деревянные пробки, необходимые для получения сквозных отверстий.
После этого подготовленную смесь плотно укладывают в форму, трамбуя при этом специально изготовленной ручной трамбовкой. После проведения этих работ формы с опилкобетоном оставляют на 3-4 дня. В течение этого времени стройматериал приобретает прочность, процентная доля которой составляет 30-40 процентов от марочной.
По истечении указанного срока вынимают пробки и толь, сами формы разбирают, а блоки оставляют на том же месте еще на 3-4 дня, чтобы их прочность еще возросла.
Теперь она составляет 60-70% от марочной прочности. После этого блоки следует перенести под навес для последующей сушки. Для достижения лучшего результата необходимо соблюдать некоторые условия:
- опилкобетонные блоки при сушке лучше всего расположить на сквозняке. Так их сушка будет более равномерно осуществляться;при укладывании блоков для сушки оставляйте между ними зазоры;если нет навеса, то блоки необходимо укрыть полиэтиленовой пленкой в случае дождливой погоды.

Для окончательной сушки из блоков сооружают столбы.
Это происходит так: на предварительно обожженные кирпичи укладывают два блока, на них располагают поперек еще два, затем поперек еще пару и так далее. Расположенные так, блоки окончательно просохнут и затвердеют. 90% прочность стройматериал приобретает уже через месяц, однако для достижения стопроцентной прочности потребуется три месяца.
Полностью готовые блоки очень прочны, тверды и не имеют трещин. Доказательством прочности стройматериала является то, что блок не разбивается при падении с высоты, достигающей 1 метра.
Арболитовые блоки — это материал, который активно используется в малоэтажном строительстве.
Если говорить о его составе, то он состоит из опилок (деревянной стружки) и цементного раствора обычно серии М-200, М-400. Говоря о истории арболитовых блоков, то их использование было реализовано еще в 1940 годах прошлого века, тогда множество заводов производили данные блоки и стоит отметить, что они пользовались большой популярностью не только для временного, но и для капитального жилья. Говоря о применении опилкобетонных блоков, то их целесообразно применять в малоэтажном строительстве или например при возведении дома на ленточном фундаменте.
Арболитовые блоки — образец
Преимущества использования арболитовых блоков
Опилкобетонные блоки обладают удивительными качествами во первых — это безусловно дешевый вид производства блоков для последующего строительства дома.
Во-вторых арболитовые блоки обладают хорошими теплоизоляционными качествами, да-да именно так, они прекрасно удерживают и аккумулируют тепло внутри дома. Третье преимущество — это легкость производства опилкобетонных блоков даже для начинающих строителей. И наконец к четвертому и пятому преимуществу можно отнести пожаробезопасность данного материла и его прочность и долговечность при соответствующем уровне соблюдения технологии.
Технология изготовления арболитовых блоков
Для, того чтобы блоки получились правильной формы и не разрушались под воздействием времени необходимо делать стружку от 3 до 15 см в длину и от 0,5 см до 2 см в ширину.
Разумеется сначала нам будет необходимо огромное количество деревянных опилок, процесс получения опилок может быть у всех разный, у кого-то они остаются после токарных работ, кто-то пропускает их через рубильную машину, кто-то заказывает опилки с лесопилок, но говоря о простом получении деревянной стружки советуем вам заехать на вашу местную лесопилку и договориться о покупке отходов (стружки) т. к обычно их все равно выкидывают или просто напросто сжигают.Вторым этапом после заготовки древесной стружки будет ее выдержка на улице — это придаст очищение стружки от сахара, который будет оказывать негативное влияние на ее состав, выдержка на уличных условиях производится около 40-80 дней при этом необходимо переворачивать и шарудить вашу кучу с опилками, чтобы воздух проникал и в нижние слои, а не задерживался на поверхности.
Кстати, чтобы был максимальный эффект кучу необходимо обильно поливать окисью кальция.После того, наш заготовочный материал отлежался на поверхности его необходимо пропустить через крупное сито — это избавит его от остатков земли и прочих органических материалов, которые будут служить разрушающим фактором при формировании блоков. Следующий шаг — это замачивание опилок водой с добавлением жидкого стекла, готовую смесь необходимо замешивать в специальной бетономешалке, но обратите внимание, что когда происходит замес он зависит от того, какую прочность арболитовым блокам вы хотите придать, в стандартном классическом применении используется пропорция — 1:2:6 то есть, на 1 мешок цемента приходится 2 мешка песка и 6 мешков опилок.Арболитовые блоки обладают малым весомОбратите внимание, что минусом строительства дома из опилкобетона является его подверженность крысиным и мышиным «атакам», но не отчаивайтесь существует несколько способов его защитить: первый это после возведения фундамента сделать бетонную заливку около — полуметра в высоту и второй способ — это залить прямо вплотную к арболитовым блокам обыкновенную сетку — рабицу, чтобы грызуны не имели доступа к нашим блокам.Процесс перемешивания раствора в бетономешалкеПосле того, как наш раствор готов, остается заключительная часть — это создание специальной формы арболитовых блоков.
Форма придается с помощью специального шаблона, который имеет форму прямоугольника. Кстати обратите внимание, что площадь внутри блока обшивается линолеумом,для того чтобы раствор не прилипал к стенкам блока.Форма для арболитовых блоковПосле того, как наш раствор залит в форму его нужно, как следует взболтать, для того чтобы участки не завоздушились по стенкам формы постепенно стучат молотком, а лучше проходят вибратором, что несомненно даст лучший эффект.
Арболитовые (опилкобетонные) блоки своими рукамиСсылка на основную публикацию
- Дата: 11-03-2015Просмотров: 326Комментариев: Рейтинг: 30
Сейчас очень многие стараются строить дома из экологически чистых материалов. Говоря о таковых, в голову сразу приходят мысли о древе. Но не стоит забывать и о той же самой глине или даже соломе.
Многие могут сказать, что солома — это прошлый век и это не надежно. Но благодаря современным технологиям такой материал приобрел не только качество, но и прочность. И если нет желания тратиться на него, то соломобетонные блоки своими руками тоже можно сделать.
Соломобетонные блоки являются дешевым, прочным и экологически чистым материалом.
Но для начала нужно разобраться, что это такое.
Такой материал выпускается в виде прямоугольных блоков. Блок имеет стандартную ширину (45 см) и высоту (35 см), а вот длина может варьироваться от 90 до 112 см. Весить такой блок может от 16 до 30 кг.
Чтобы такой материал сохранял свою форму, блоки обвязывают (а некоторые производители и прошивают) полипропиленовыми шнурами. В сельскохозяйственных сферах такие блоки собираются в единое целое при помощи проволок или натуральных волокон. Но эти крепления подходят для хранения соломы, а никак не для построек.
Ведь сама проволока железная, а железо имеет свойство ржаветь. А волокно по прошествии времени теряет свою прочность из-за гниения. Солома тоже бывает нескольких видов, поэтому для постройки лучше применять ржаную или рисовую.
Они обладают оптимальными свойствами. Если останавливать свой выбор на первом варианте, то лучше, если она будет озимая. Такая солома имеет более плотную структуру.
Предъявляемые требования
Есть определенные требования к соломенным блокам, а именно:
Схема бескаркасной стены из соломенных блоков.
Сухость.
Влага, скопленная внутри, будет провоцировать гниение. Кстати, именно сухие блоки такие легкие, и если они имеют значительный вес, то есть вероятность, что солома была не доброкачественно просушена. Если ощущается запах гнили или пальцами чувствуется влажность, то такой материал некачественный.Качество соломы.
Стебли должны быть гибкими и крепкими. Если при сгибании он не ломается, то это качественный блок. В обратном же случае такой материал быстро рассыпется.Качественный пресс.
Если соблюдалась правильная технология спрессовывания блока, то он не должен терять своей формы. Для этого можно попробовать просунуть под шнур пальцы, если больше 3х пальцев не помещается, то это качественный пресс.Одинаковые размеры.Вся партия должна быть идентичной. Если блоки разнятся по размерам между собой, то лучше отказаться от применения данного материала и найти другого производителя.
Вернуться к оглавлению
Когда вы делаете что-либо своими руками, всегда возникает огромный плюс — экономия средств. К тому же при собственноручном изготовлении всегда можно быть уверенным в качестве применяемых материалов. То же самое относится и к блокам из соломы и бетона.
Цемент компонируется соломой не только по причине придания прочности.Он помогает органическим веществам соломы преобразоваться в сахар, который легко растворяется водой. Но такие преобразования мешают соломенному блоку отвердеть. Для того чтобы устранить такой отрицательный эффект, применяются физические и химические способы.
Схема перекрытия из соломобетонных блоков.
Первое, что используют — окисление. Для этого блоки выносят на открытые солнечные лучи, под воздействием которых происходит окисление веществ, и они начинают впитываться в стенки древесных клеток.
В то же время часть других веществ при взаимодействии с бактериями преобразуется в кристаллы и в дальнейшем образует нерастворимые формы. Но для того чтоб все это произошло на надлежащем уровне, необходимо очень много времени. Второй способ — вымачивание водой.
Если блок оставить под дождем на длительное время, то практически все водорастворимые вещества выйдут из него. С этой целью используют и специальные емкости. Но опять-таки для того чтобы обработать всю партию соломенных блоков, требуется значительное время.
Самым распространенным на сегодняшний день способом является обработка растворами хлористого кальция или жидкого стекла. В среднем их надо около 9 кг на метр кубический. Эта технология популярна по ряду причин:
Благодаря жидкому компоненту стекла и хлористому кальцию изделие быстро затвердевает.
Но если сравнивать прочность готовых блоков обеих марок, вторые этот показатель имеют намного выше, чем первые. Если применять кальций, то следует знать, что лучше всего использовать выдержанную солому. А вот для применения жидкого стекла порода соломы особой роли не играет.Используя такие добавки, при условии, что средняя температура окружающей среды будет 20 градусов тепла, такие блоки уже через 24 четыре часа можно складывать, а через 7 дней применять и для строительства.
Есть рекомендуемый расход для изготовления блоков, ориентированный на объемный вес компонентов (кг/м3):
Сравнение теплопроводности соломобетонных блоков с другими материалами.
- цемента — 1700;гашеной извести — 600;песка — 1550;соломы — 80-105.
А вот на расход воды влияют несколько моментов:
- какая необходима вязкость замеса и заполнителя;марка бетонного раствора;показатель исходной влажности соломы.
Такие пропорции позволят создать блок с показателем прочности М-10.
Некоторые строители заменяют бетон на глину. Изначально они рубят солому на куски (0,5 м), после чего замачивают ее в глиняном растворе. И опять-таки полученный материал прессуется.
Сам блок формируется при помощи киповальной машины.
Ее можно соорудить и самому, а можно обратиться к профессиональным киповальщикам или взять пресс в аренду. Если же все-таки решено обращаться за помощью, следует знать, что качество соломы во многом зависит и от того, как ее собирали и хранили.
Немаловажным моментом является и ее помол, ведь если ее трубчатая структура будет нарушена, то такой материал потеряет все свои свойства. Сейчас солому чаще продают в виде рулонов, что слегка удлинит процесс. Ведь такие рулоны придется заново раскатать и перекиповать.
А это может привести к нарушению изначальной структуры соломы. Но каждый сам выбирает, как ему удобно. Нельзя забывать и том, что готовые соломенные блоки пропитываются специальными химическими составами, которые значительно влияют на их прочностные характеристики.
Вернуться к оглавлению
Стройка загородного дома — это всегда какие-то проблемы, связанные то с работой, то с финансами. Но вот применение соломенных блоков помогает решить некоторые негативные моменты в строительстве.
А все потому, что они имеют ряд своих особенностей.
Низкая себестоимость. В основном солома — это отходы в сельском хозяйстве.
Поэтому приобрести ее не составит особого труда. Единственное, на что придется потратиться, это на перевоз такого материала.
Постройки из такого материала не требуют дополнительного утепления. Нет проблем и с отделочными работами, ведь, имея шероховатую поверхность, материал отлично «цепляет» к себе любые покрытия.Но также следует отметить, что все-таки соломеннобетонные блоки имеют определенную «мягкость», поэтому на них не кладутся плиты перекрытий, так как это приводит к деформации. Это является основной причиной, почему такой материал применяется для построек только каркасных домов.
Вернуться к оглавлению
Материал имеет ряд положительных моментов, из-за которых его и применяют в современном строительстве:
Благодаря небольшому весу и крупным габаритам соломенных блоков, строительство идет очень быстро.
Дешевизна и доступность материала. В наших широтах проблем с соломой не возникает, в любом колхозе ее достаточно.Экологически чистый материал.
Если солома росла на полях не в радиационной зоне и не обрабатывалась вредными веществами, то такая постройка будет иметь благоприятное воздействие и на здоровье жильцов, и на саму окружающую среду. Легкий вес. Благодаря этой характеристике строительство идет очень быстро. В зависимости от проекта, одноэтажную постройку можно завершить в сроки от двух недель до двух месяцев.Форма материала.
Так как во время производства такого блока используется пресс, то даже несмотря на наличие соломы внутри, грызуны не обустроят себе дом в стенах. Еще одним из моментов, которые влияют на популярность такого строительства, является экономия строительных ресурсов и энергии, а также сама эксплуатация такой постройки.
Несмотря на несерьезность материала, соломенные блоки имеют долгие сроки службы. Но это при условии, что они прошли правильную техническую обработку. Только в таком случае есть гарантия, что они не рассыпятся, не деформируются и не поддадутся гниению.
Даже если такой материал сравнить с древесиной, то второй вариант уступает по параметру насыщения помещения кислородом. Трубчатая структура соломенных волокон отлично держит в себе воздух, при этом внутри комнат создается свой особый климат. Также они способствуют естественному вентилированию и даже после оштукатуривания.
Соломенные блоки имеют и высокую теплопроводность и энергоэффективность. Дом, построенный из такого материала, требует меньше чем 40 кВТ*ч/м2 в год. Что опять-таки при наличии счетчиков позволяет не беспокоиться о платежках.
Кстати, об экономии. Как уже говорилось выше, соломенный блок имеет очень легкий вес (16-30 кг), что существенно сказывается и на выборе фундамента под застройку. Такие дома не нуждаются в монолитных основаниях.
Самое интересное, что даже на уровне современного подорожания других стройматериалов такие блоки значительно в цене не прибавят. Значит, сильных финансовых утрат строительство не понесет.
И конечно же, пару слов стоит сказать о пожарной безопасности. Оштукатуренный блок имеет высокие пожароустойчивые свойства. Поэтому такие дома и не боятся огня и пожаров.
Источники:
- straw.z42.ru
- sekretystroyki.ru
- stroyvopros.
net
- ostroymaterialah.ru
Бетоны на органических заполнителях – описание материалов
В самом упрощенном представлении бетон – это затвердевшая смесь щебня и песка с цементом. Люди, которые поближе знакомы с темой строительства, знают, что вместо дробленого камня можно использовать и другие материалы. Берут, например, керамзит, шлак, перлит или бой кирпича. Это все – минеральные заполнители. Но существует особый класс бетонов, которые изготавливают на основе органических материалов.
- Бетоны на органических заполнителях
- Арболит
- Деревобетон (щепобетон)
- Костробетон
- Соломобетон
- Опилкобетон
- Полистиролбетон (ПСБ)
- Арболит и полистиролбетон: сравнительные характеристики
К нему относятся две основные разновидности:
- Арболит
- Полистиролбетон (ПСБ)
У этих материалов есть как сходства, так и различия. Но перед тем, как мы перейдем к их сравнению, давайте разберемся, что собой представляет каждый из них.
Арболит
Название этого материала происходит от французского слова «arbre» – «дерево». И действительно, функцию заполнителя в нем выполняет измельченная древесина и стебли растений. Такой материал используют в основном в частном жилищном строительстве. Из него возводят монолитные или сборные (из блоков) стены и перегородки, а также обустраивают теплоизоляцию.
Требования к качеству товарного арболита приведены в:
- ГОСТ Р 54854-2011 «Бетоны легкие на органических заполнителях растительного происхождения»
- ГОСТ 19222-2019 «Арболит и изделия из него»
Отметим, что технология получения арболита достаточно сложная. Чтобы материал отвечал всем нормативам, нужно тщательно подбирать заполнитель и использовать цемент высоких марок. Далеко не все производители этим озадачиваются. Поэтому на рынке стройматериалов много некачественного арболита. Как следствие, некоторые люди относятся к нему с предубеждением.
Чтобы не наткнуться на брак, к выбору материала нужно подходить с умом. Заказывайте арболит и блоки из него только у тех поставщиков, которые могут подтвердить качество своего товара сертификатами. По-хорошему, это касается всех строительных материалов для ответственных работ.
Арболит делится на виды в зависимости от типа заполнителя:
- Деревобетон (щепобетон)
- Костробетон
- Соломобетон
- Опилкобетон
Давайте остановимся на каждом из них подробнее.
Деревобетон (щепобетон)
Это основная разновидность арболита, которую чаще всего и имеют в виду, когда говорят об этом материале. Его делают на основе измельченной древесины – проще говоря, щепы.
Щепу получают путем дробления пней, сучьев, обрубков и других некондиционных кусков древесины. Сами деревообрабатывающие предприятия, бывает, выпускают так называемую технологическую щепу. Но для изготовления качественного арболита она не подходит.
Щепа для бетона должна отвечать таким требованиям:
- Длина – не более 30 мм
- Ширина – не более 10 мм
- Толщина – не более 5 мм
- Примеси коры – не более 10%
- Примеси хвои и листьев – не более 5%
- Содержание водорастворимых сахаров – не более 2%
- Наличие камней, мусора, земли, гнили, грибка, снега и льда – не допускается
Ответственные производители обычно сами режут древесину, а не покупают готовый материал у других предприятий. Их щепорезы специально откалиброваны так, чтобы получать заполнитель наилучшего качества.
Готовый деревобетон имеет такие свойства:
- Класс по прочности – от В0,5 до В3,5
- Марка по прочности – от М5 до М50
- Плотность – от 500 до 1000 кг/м3
- Теплопроводность – от 0,07 до 0,17 Вт/(м·°С)
Это материал с хорошими теплотехническими характеристиками, но низкой прочностью. Он подходит для строительства малоэтажных домов, но в более ответственных работах использовать его нельзя.
Костробетон
Чтобы соткать льняную или конопляную ткань, нужно сначала получить мягкое растительное волокно. Для этого стебли льна и конопли мнут и треплют. В результате такой обработки твердые одревесневшие оболочки отделяются от волокнистой сердцевины. Их-то и называют кострой.
В России костробетон распространен не так широко, как деревобетон (который обычно и имеют в виду под словом «арболит»). Объясняется это тем, что возделывание льна и технической конопли в нашей стране особо не развито. Встретить такой материал можно в Центральной и Южной России, а также в Западной Сибири и Поволжье.
К качеству костры для бетона тоже предъявляются особые требования:
- Длина – не более 40 мм
- Содержание очесов и пакли – не более 5%
- Содержание водорастворимых сахаров – не более 2%
- Наличие посторонних включений, гнили, грибка – не допускается
При этом бетон из конопляной костры получается более качественным, чем на основе льняного материала. Это связано с тем, что перед трепанием коноплю вымачивают, а затем сушат. В результате из нее уходят сахара, которые замедляют твердение цемента.
Костробетон имеет такие характеристики:
Для вашего удобства ниже мы разместили эту таблицу в виде картинки:
По прочности он уступает деревобетону и имеет более ограниченную сферу применения. В частности, из него нельзя возводить несущие стены и перегородки. В то же время костробетон выигрывает по теплоизоляционным свойствам. Он отлично подходит для утепления полов, перекрытий, стен, чердаков и фасадов.
Соломобетон
При производстве арболита также можно применять измельченные стебли растений. ГОСТ разрешает использовать для этого хлопчатник и рисовую солому.
Как и костробетон, этот материал можно найти далеко не во всех регионах. Ведь хлопок и рис – культуры очень «капризные». Их выращивают только в южных регионах России: Краснодарском крае, Ростовской и Астраханской областях, Калмыкии, на Кавказе.
Требования к качеству соломы для бетона такие же, как и для костры.
Характеристики этого материала по ГОСТу следующие:
Для вашего удобства ниже мы разместили эту таблицу в виде картинки:
Но производителей настоящего соломобетона по ГОСТу в России нет. Его замешивают в основном в домашних условиях «из того, что было» и на глаз. Точные показатели такого материала никто не измеряет и предсказать их сложно.
Идейно соломобетон схож с другим строительным материалом – саманом. Но в самане роль вяжущего играет глина, поэтому его можно использовать только в сухом климате. Соломобетон таких ограничений не имеет, потому что цементу вода не страшна.
Опилкобетон
Строго говоря, этот материал уже не является арболитом. Это один из видов самомесного бетона, который можно охарактеризовать как «дешево и сердито». Но для полноты картины мы рассмотрим и его тоже.
Опилки – это стружка, которая образуется при распиле дерева. Ее размеры никак не нормируются. Иногда в ней есть посторонние включения: кора, листья, крупные щепки, песок, камни и даже обычный мусор, который валяется на полу в мастерской. Все это отрицательно сказывается на свойствах бетона.
Стандартный «рецепт» опилкобетона включает такие компоненты:
- Опилки как основной заполнитель
- Песок для более высокой плотности и прочности
- Цемент марки М400-М500
- Гашеная известь для нейтрализации сахаров и защиты материала от гниения
Их пропорции варьируются от строителя к строителю, потому что никакой единой технологии изготовления этого материала нет. Свойства его тоже непредсказуемы. Ведь для измерения характеристик бетона нужны лабораторные испытания, которые в этом случае никто не проводит.
Это значит, что и отзывы об опилкобетоне очень противоречивые. Кто-то позиционирует его как копеечный и при этом хороший материал для постройки теплого частного дома. Другие ругают его за то, что он долго сохнет, активно всасывает воду и быстро разрушается.
Оптимальная сфера применения опилкобетона – это заливка стен хозяйственных построек и небольших домов. При этом материал должен быть как следует утрамбован и покрыт водостойкой штукатуркой с обеих сторон.
Больше узнать об арболите, его особенностях и специфике производства вы можете в нашей статье Арболит. А если вам интересно, где и как применяется такой материал, ознакомьтесь со статьей Применение арболита.
Полистиролбетон (ПСБ)
Его делают на основе вспученных гранул полистирола – тех самых, из которых состоит пенопласт. В отличие от дерева, это материал искусственного происхождения.
Классификация и технические характеристики ПСБ закреплены в ГОСТ 33929-2016.
Пенополистирольные гранулы для производства бетона имеют такие характеристики:
- Насыпная плотность – до 20 кг/м3
- Размер – до 10 мм в диаметре
- Теплопроводность – не выше 0,035 Вт/(м·°С)
- Содержание воздуха – около 90%
Это очень пористый материал с отличными теплоизоляционными свойствами. Их же «наследует» и сам полистиролбетон.
Особенность ПСБ заключается в том, что его свойства не так сильно зависят от качества наполнителя. По сути, легкие гранулы в нем выполняют роль внутренней опалубки. Они формируют пористую структуру цементного камня, который и принимает на себя всю основную нагрузку. Этим он отличается от арболита, в котором щепа (костра, солома) образует сам каркас камня.
В соответствии с ГОСТом характеристики полистиролбетона следующие:
- Класс по прочности – от В0,35 до В2,5
- Марка по прочности – от М2 до М20
- Плотность – от 150 до 600 кг/м3
- Теплопроводность – от 0,051 до 0,135 Вт/(м·°С)
Он имеет отличные теплотехнические характеристики и малый вес, но при этом очень низкую прочность.
Больше узнать об особенностях этого материала вы можете в статье Полистиролбетон.
В продолжении статьи мы подробнее поговорим о том, чем похожи и чем отличаются друг от друга эти материалы.
Арболит и полистиролбетон: сравнительные характеристики
Эти две разновидности бетона считаются конкурентами на рынке строительных материалов.
Они имеют целый ряд общих характеристик:
- Малый вес
И арболит, и полистиролбетон относятся к классу очень легких бетонов. Стены из них оказывают небольшую нагрузку на фундамент. А значит – можно немного сэкономить на обустройстве прочного основания. - Тепло- и звукоизоляционные свойства
За счет своей пористости оба материала имеют низкую теплопроводность. Это значит, что зимой они удерживают тепло в помещении, а летом – защищают его от перегрева. Кроме того, они имеют свойство поглощать и рассеивать звук благодаря своей сложной структуре и упругости. - Прочность
Как и все легкие бетоны, они не способны выдерживать высокие нагрузки на сжатие. Вместе с тем арболит и ПСБ лучше работают на изгиб и растяжение, чем хрупкие пено- и газобетон. Это значит, что колебания грунта им не так страшны. - Сфера применения
Арболит и полистиролбетон применяют в малоэтажном жилищном строительстве для заливки монолитных стен и перегородок, производства стеновых блоков и панелей, а также для утепления полов, перекрытий, стен, чердаков, подвалов и фасадов. - Горючесть
Как известно, органика горит, и это свойство передается и бетонам на ее основе. Этим арболит и ПСБ отличаются от обычного бетона на щебне и песке, который относится к негорючим стройматериалам. - Стоимость
Цены на арболит и ПСБ варьируются от производителя к производителю, но находятся примерно в одной ценовой категории. Эти материалы нельзя назвать бюджетными: зачастую они стоят дороже газо- и пеноблоков, не говоря уже о шлакоблоках и керамзитобетоне.
Эти сходства приводят к тому, что перед заказчиками часто встает дилемма: какому материалу отдать предпочтение? Чтобы сделать правильный выбор, нужно посмотреть на различия между ними.
В таблице ниже мы привели сравнение арболита и полистиролбетона по их основным характеристикам:
Для вашего удобства ниже мы разместили эту таблицу в виде картинки:
О том, как учитывается паропроницаемость при строительстве дома, вы можете прочитать в статье Паропроницаемость бетона.
Какие выводы можно сделать из таблицы?
Арболит – материал более плотный и прочный. Кроме того, его пожаро-технические характеристики чуть повыше, чем у полистиролбетона. Он имеет низкую морозостойкость, но эту проблему можно решить при помощи хорошей цементной штукатурки.
У полистиролбетона запас прочности поменьше, но зато лучше теплоизоляционные свойства. Кроме того, он имеет высокую (для легкого бетона) морозостойкость.
Можно вывести ряд рекомендаций:
- Если планируется дом в 2-3 этажа и выше, то строить лучше из арболита – он более прочный
- Минимальные расходы на отопление будут в доме из полистиролбетона
- В условиях влажного климата предпочтение лучше отдать полистиролбетону, поскольку он меньше впитывает влагу и лучше переносит перепады температуры
- Ни один из этих материалов нельзя использовать в помещениях с высокой пожарной опасностью без слоя огнестойкой штукатурки (например, цементной)
Не последнюю роль здесь играет и вопрос стоимости. Если характеристики обоих материалов подходят под вашу задачу, то целесообразно будет взять тот, который обойдется дешевле.
Давайте еще раз подведем итог всему сказанному выше.
К бетонам на органических заполнителях относятся арболит и полистиролбетон (ПСБ). Первый производится на основе измельченной древесины, костры или соломы; а второй – на основе гранул пенополистирола. Эти материалы отличаются малым весом, высокой пористостью, прочностью на растяжение и изгиб, а также хорошими тепло- и звукоизоляционными свойствами. К их минусам можно отнести низкую прочность на сжатие, горючесть и высокую стоимость. Оба эти материала пользуются спросом при строительстве частных малоэтажных домов. Из них возводят стены и обустраивают теплоизоляцию.
- Арболит
- Полистиролбетон
Инновации в строительстве: Зеленые технологии – 1389 слов
Общие тенденции
- Строительство зеленых зданий является эффективным инструментом повышения устойчивости среды обитания.
- Зеленое строительство развивается во многих направлениях.
- Инновационные решения для зданий с низким энергопотреблением активно разрабатываются и внедряются в современную практику. Элементы «зеленых» зданий – зеленые крыши и зеленые фасады – постоянно совершенствуются.
Определение «зеленое строительство» не просто характеризует тот или иной тип сооружения или использование определенного комплекса архитектурных приемов при его возведении – это понятие подразумевает сложную систему специально разработанных принципов, на основе которых как ведутся строительство и эксплуатация здания (Yilmaz and Bakis, 2015).
Зеленые материалы и технологии
- К «зеленым» технологиям, применяемым в строительстве, можно отнести любые меры, направленные на сохранение окружающей среды.
Однако главное и самое важное – это снижение энергопотребления с целью экономии природных ресурсов и минимизации количества вредных веществ, воздействующих на окружающую среду, при сохранении тепла и уюта в доме (Дыкстра, 2016).
- Фраза «зеленые» строительные материалы имеет несколько значений.
- Их условно можно разделить на две большие подгруппы: органические и энергоэффективные.
- К «зеленым» органическим материалам предъявляются два основных требования. Во-первых, это должны быть переработанные и многоразовые материалы.
- Второй параметр – экологичность.
- «Зеленый» кирпич:
- Сегодня использование зеленого кирпича стало настолько популярной строительной технологией, что он практически полностью заменил традиционные материалы.
- Сырой кирпич изготавливается из переработанных материалов, он очень легкий и обладает улучшенными изоляционными свойствами.
Инновационные материалы и технологии – важнейшая основа зеленого строительства. Изменения в разработке и производстве строительных материалов уже сегодня коренным образом меняют строительную отрасль. Современные материалы и решения позволяют достичь высокого уровня энергосбережения, помогают снизить стоимость жизненного цикла объекта и в целом обеспечивают более комфортную и здоровую окружающую среду.
В штаб-квартире LEED пол сделан из дробленого бетона, похожего на мраморную крошку, и дерева, которое лежало на дне реки более 100 лет. Его собирали, сушили и использовали для украшения (Dhir et al., 2019).
Многие производители под понятие «зеленый» подпадают все материалы, изготовленные из натурального, «экологически чистого» сырья. Но в классическом понимании «зеленые» строительные материалы — это материалы, изготовленные из возобновляемого природного (то есть органического) сырья и с «нулевыми» или минимальными выбросами углекислого газа при их производстве (Kibert, 2016; Magwood, 2017). .
Самым популярным материалом, отвечающим этим критериям, является дерево, спектр его применения достаточно широк. То же самое относится и к другим популярным «зеленым» материалам — соломе и камышу, пеньке, целлюлозе и хлопковому утеплителю.
Проблема органических материалов в том, что они пожароопасны, а это значит, что в процессе строительства их необходимо обрабатывать химическими средствами, что нейтрализует экологичность. Например, добавление цемента в древесину снижает экологические свойства конечного материала, но при этом повышает огнестойкость.
Арболит в зеленом строительстве
Очень перспективным новым материалом в этом отношении является арболит – конструкционные блоки из опилок и цемента. Применение цемента значительно повысило пожарную безопасность материала и расширило возможности его применения в гражданском массовом строительстве.
Древесный блок, вернее, арболитовый блок содержит до 85-90 процентов древесных отходов. Так же зависит от марки. Благодаря этому такие блоки по праву считаются одним из самых экологически чистых строительных материалов. По сути, это дерево в бетоне. Сочетание этих ингредиентов дает сильный эффект. По тепло- и звукоизоляции арболитовые блоки превосходят кирпич почти в 4-5 раз, а керамзитобетонные – в 2-3 раза.
Свойства арболита
Арболит очень теплоемкий – при нагревании он поглощает тепло, а при охлаждении отдает. Благодаря этому свойству микроклимат в помещении относительно стабилен днем и ночью.
В арболитовом помещении при нагреве сначала будет прогреваться окружающий воздух, а потом только стены. Теплоемкость арболитовых панелей и блоков составляет около 2,3 кДж/кгК. Это выше, чем воздушный индекс (Dhir et al., 2019).
Размеры стандартного блока 500 х 250 х 300 миллиметров. Вес 1 кв. м арболитовой стены не превышает 200 кг при толщине стены всего 30 см (Subramaniam, Subasinghe, Fonseka, 2015).
Благодаря этой массе фундамент можно сделать облегченным. При этом важными являются такие характеристики, как достаточно высокий предел прочности – ее предел прочности при изгибе и повышенная устойчивость к ударным нагрузкам, морозостойкость (F25 – F50), неподверженность влиянию гнилей, бактерий, грызунов (Han, Чжан и Оу, 2017 г.).
Благодаря этим характеристикам арболит нашел широкое применение в строительстве в северных регионах.
Деревобетонные дома практически никогда не бывают сырыми. Стены «дышат», воздухообмен с окружающей средой не нарушается. Пожароопасность таких построек очень низкая, даже несмотря на высокое содержание органических компонентов. 0,8 – 1,5 часа – это показатель огнестойкости арболитовых зданий (De Luca, Carbone, and Nagy, 2017).
Применение в строительстве:
Арболитобетон марок: 5, 10, 15, 25, 35 и 50. Теплоизоляционный (до 500 кг на 1 м3), конструкционный (500 – 850 кг на 1 м3) (Аруова, 2018).
Блоки и стеновые панели являются основными конструкционными элементами, изготавливаемыми из арболита. Размеры блоков обычно составляют 500 х 200 х 300 миллиметров (для возведения наружных стен) и 500 х 200 х 200 миллиметров (для возведения перегородок внутри). Панели более массивные – 2300 х 1200 миллиметров, и толщиной 200 – 280 миллиметров. Обычно они используются для теплоизоляции (Dhir, et al., 2019).). Вышеуказанные размеры для панелей и блоков не являются стандартными. Заказчик сам может выбрать нужные ему размеры.
Арболит Общие преимущества
Стоимость стены из арболита дешевле керамзитобетонной плиты и кирпича, утепленного минеральной ватой, более чем в 2 раза.
Кроме того, значительно снижаются затраты на строительство фундамента, так как вес арболита намного меньше кирпичной кладки. Стоимость дома почти в 2-3 раза ниже, чем кирпичного (Сабнис, 2015).
Интерес к арболиту особенно возрос за последние пять лет (Subramaniam, Subasinghe, and Fonseka, 2015). Этому способствуют возрастающие требования к жилью с точки зрения экологии, энергоэффективности и пожарной безопасности. Что касается экологичности, то в арболитовых домах легко дышится, а паропроницаемость такова, что воздух в помещении постоянно обновляется.
Заключение
- Блоки арболитовые применяются как в промышленном, так и в гражданском строительстве для:
- укрепление стен.
- возведение несущих конструкций.
- теплоизоляция зданий и сооружений.
- При использовании арболита вы получите следующие неоспоримые преимущества:
- Сокращение затрат на строительство дома за счет оптимизации финансовых и энергетических затрат.
- Значительно сократить время строительства здания.
- Уменьшить общую массу здания.
- Улучшите качество жизни с помощью экологичных строительных материалов.
- Сокращение затрат на строительство дома за счет оптимизации финансовых и энергетических затрат.
Таким образом, использование арболита обеспечивает значительные экономические, экологические и социальные преимущества.
Любой отделочный материал легко ложится на арболит. Все эти свойства арболита делают его одним из самых популярных строительных материалов.
Здания из арболита возводились даже в крайне суровых условиях Антарктиды.
В многоэтажных домах арболит может применяться в качестве заполнения проемов, при монолитном железобетонном каркасе здания.
Ссылки
Аруова, Л. (2018) «Производство арболитных строительных изделий с использованием солнечной энергии», Журнал исследований и разработок в области машиностроения , 41(2), стр. 49-55.
Де Лука, П., Карбон, И., и Надь, Дж. (2017) «Зеленые строительные материалы: обзор современных исследований инновационных материалов», Journal of Green Building , 12(4) , стр. 141-161.
Дхир, Р. К. и др. (2019) Устойчивые строительные материалы: переработанные заполнители . Кембридж: Издательство Вудхед.
Дайкстра, А. (2016) Зеленое строительство: введение в меняющуюся отрасль . Лондон: Книги Киршнера.
Хань Б., Чжан Л. и Оу Дж. (2017) Светоизлучающий бетон. Умный и многофункциональный бетон на пути к устойчивой инфраструктуре . Нью-Йорк: Спрингер.
Киберт, К. (2016) Экологически безопасное строительство: проектирование и поставка экологичных зданий . Хобокен: Уайли.
Мэгвуд, К. (2017) Основной экологически безопасный дизайн дома: полное руководство по целям, вариантам и процессу проектирования . Остров Габриола: Издательство Нового Общества.
Сабнис, Г. (2015) Зеленое строительство из бетона: устойчивое проектирование и строительство . Бока-Ратон: CRC Press.
Субраманиам П., Субасингхе К. и Фонсека К. (2015). «Древесная зола как эффективное сырье для бетонных блоков», International Journal of Research in Engineering and Technology , 04(02), стр. 228-233.
Йилмаз, М. и Бакис, А. (2015) «Устойчивое развитие в строительном секторе», Procedia – Социальные и поведенческие науки, 195, стр. 2253-2262.
Zwicky, D. (2015) Механические свойства древесно-цементных смесей . Конференция: 10-я конференция по передовым строительным покрытиям. Берн, Швейцария.
сколько блоков в кубе, технология производства, из чего делают
Главная » Стройматериалы
Арболит – уникальный материал, который используется для строительства домов за рубежом уже более 100 лет. Его характеристики и свойства вызывают множество противоречивых мнений о качестве и надежности этого материала.
Содержание
- Технология, состав, характеристики
- Расчет количества арболита
- Процесс возведения стен
Технология, состав, характеристики
Застройщики стараются использовать качественные, проверенные строительные материалы, максимально практичный использовать и дешевле в цене. Большую популярность приобрел арболит благодаря своим техническим характеристикам и эксплуатационным свойствам.
Древесный бетон содержит:
- бетон М400 или М500;
- химическая добавка ;
- органический наполнитель .
Бетон должен быть высокой прочности. Используется в качестве химической добавки сульфат алюминия, хлорид кальция или жидкое стекло … К органическим наполнителям относятся древесина, измельченные стебли хлопка, рисовая солома и т.д.
В зависимости от технологии производства и удельного веса компонентов в состав, блоки могут иметь разную плотность:
- менее 500 кг/м³ применяется в качестве теплоизоляционного материала, а также для устройства межкомнатных перегородок;
- более 500 кг/м³ применяются для возведения несущих конструкций.
Технология производства арболита включает несколько этапов:
- приготовление необходимого количества органического наполнителя ;
- пропитка древесины хлористым кальцием;
- дозировка всех составляющих в правильной пропорции;
- Изготовление блоков.
Ключевыми характеристиками арболита , отличающими его от других строительных материалов , считаются теплопроводность и влагопоглощение .
Теплопроводность арболита напрямую зависит от его плотности. Рекомендуемая толщина стены из арболита – 38 см … А чаще стены жилого дома строят из блоков размером 500х300х200 мм в один ряд … С учетом внутренней и внешней отделки стен дома такой толщины достаточно для обеспечения комфортного температурного режима внутри помещения комната.
Сравнение теплопроводности строительных материаловВлагопоглощение арболитовых блоков до 85% для внутренних стен и до 75% для несущих стен … Материал должен быть тщательно гидроизолирован, чтобы он не потерял свои свойства. свойства в течение длительного времени.
Простота
Простота использования
Простота внешней отделки
Крепость
Звукоизоляция
Низкая теплопроводность
Долгий срок службы
Склонен к процессы распада
Низкая прочность
Воздухопроницаемость стен
Некрасивый вид
Вкл.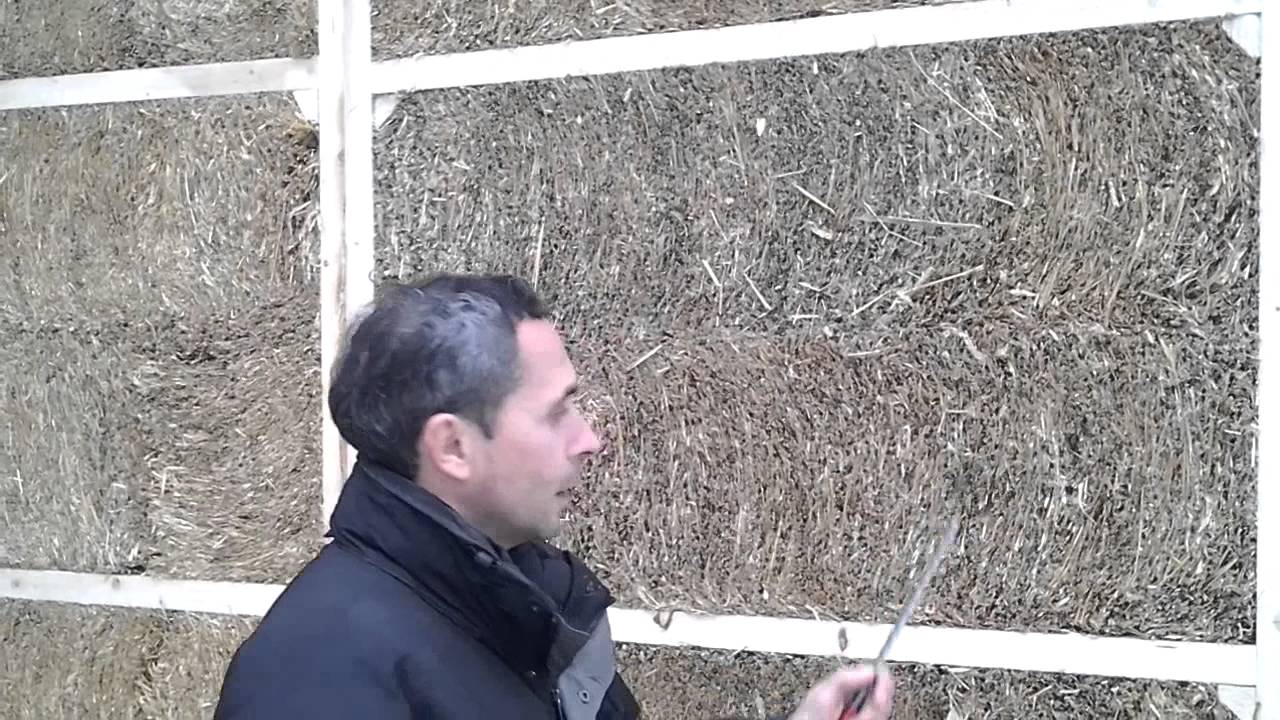
Арболит сочетает в себе положительных характеристик дерева и камня.
- Вес одного куба составляет около 650 кг (для сравнения, кирпичный куб весит около 2 тонн). Малый вес стен позволяет сэкономить на фундаменте дома.
- Арболит легко режется, пилится и крепится … Блоки можно распиливать ножовкой по дереву, в них можно вкручивать саморезы, вбивать гвозди. Легко подходят под кладку, технологичны отверстия.
- Арболит – пористый материал , благодаря которому штукатурка, проникая в блок, образует с ним монолит. Однако если блоки обработаны машинным маслом, без фасадной штукатурной сетки не обойтись.
- Материал обладает уникальной прочностью на изгиб … От механического удара по блоку остается лишь небольшая вмятина. Однако не рекомендуется строить здание выше 2-3 этажного дома, и обязательно для более равномерной нагрузки на все стены по периметру здания монтировать монолитный армопояс.
- Обладает самым высоким коэффициентом звукопоглощения из мягких ячеистых материалов для строительства.
- Низкая теплопроводность 0,12-0,19Вт/(м°С) позволяет строить дома из арболита и в средней полосе России.
- При соблюдении технологии строительства и использовании качественных блоков дома прослужат очень долго .
недостатки арболитовые конструкции:
- На арболитовых блоках может появиться плесень , как и на любом другом материале, при создании соответствующих условий для ее образования. При строительстве важно соблюдать правила гидроизоляции и вентиляции.
- На силу влияет множество факторов. Важно, что арболит марки изготавливался из цемента марки и обладал нормативной прочностью М25 .
- Сильные порывы ветра ощущаются сквозь деревобетонные стены. Воздухопроницаемость – это одно из ценных качеств этого материала.
Проблема решается качественной паропроницаемой штукатуркой.
- Стены из арболита требуют внутренней и внешней отделки … Вы можете выбрать любую отделку на свой вкус. В продаже имеются готовые арболитовые блоки с внешней облицовкой.
Теплопроводность
5
Прочность
2
Простота использования
5
Водопоглощение
2,5
Всего
3,6
Арболит подходит для легких зданий, стены которых не подвергается механическим воздействиям. Блоки необходимо тщательно гидроизолировать.
Расчет количества арболита
Формулы расчета площади стен и фронтоновДля оценки стоимости материала и объема работ при строительстве дома из арболитовых блоков необходимо рассчитать необходимое количество для строительства. Необходимо знать длину и толщину всех несущих стен, межкомнатных перегородок, высоту каждого этажа, квадратуру оконных и дверных проемов.
Для расчета можно использовать следующий метод:
- Определить периметр дома – сумма длин всех стен.
- Определить общую высоту дома .
- Умножить общую длину на общую высоту .
- Вычтите общие площади оконных и дверных проемов .
- Результат умножить на количество блоков для кладки 1 м² стен.
- Добавляется 1% сток .
Для дальнейшего расчета необходимо знать количество арболитовых блоков в кубе. Стандарт для несущих стен 1 м³ требуется 33,3 арболитовых блока размерами 500х300х200 мм … Для возведения межкомнатных перегородок чаще применяют блоки размером 500х150х200 мм – в 1 66,6 штук м³ … При использовании арболита размером 400х200х200 мм в 1 м³ будет 62 блока .
Процесс возведения стен
При возведении стен из арболита может применяться штабелирование в один или два блока . .. В качестве связующего используется стандартное связующее. Цементно-песчаный раствор с добавлением перлита для повышения теплоизоляции швов. Часто застройщики выбирают для соединения арболитовых блоков газобетонный клей .
Валера
Голос строительного гуру
Задать вопрос
При укладке арболита необходимо смачивать водой, так как из-за своей пористой структуры он вытягивает влагу из раствора. При укладке можно использовать специальную влагоудерживающую смесь.
Перед укладкой первого ряда блоков необходимо провести гидроизоляцию в тех местах, где блоки будут примыкать к фундаменту. Армировать каждые 3-5 рядов блоков обычной сеткой.
Сетка армирующаяДля устройства оконных и дверных проемов можно использовать сборный брус, железобетон, монолитные перемычки, стальные уголки, швеллеры и другие профили.
При кладке блоков следует использовать раствор прочностью М50 – М100.