Оригинальная внутренняя отделка стен из блоков Porotherm
Традиционнойя внутренней отделкой стен из блоков Porotherm считается оштукатуривание. Именно штукатурка защищает блоки от накапливания влаги и дальнейшего разрушения. Многие другие отделочные материалы не подходят для керамических поризованных блоков, например, обои.
Но что делать, если средств на приобретение штукатурки и оплату профессиональных услуг нет? Мы нашли способ сэкономить на внутренней отделке керамических блоков, при этом отказавшись от оштукатуривания.
Отделка стен металлическим профилем
Этот метод отделки идеально подходит для тонких стен, возведенных из керамических блоков толщиной 25 или 30 см. Так как обшивка профлистом создается вместе с прокладкой утеплителя.
Профлист не подвергается коррозии из-за оцинкованного покрытия, более того, металлический профиль препятствует любому проникновению жидкости на поверхность блоков.
Профлист зарекомендован, как долговечный и прочный материал. На открытом воздухе, при воздействии агрессивных атмосферных явлений металлический профиль эксплуатируется 50 лет, а внутри дома – срок службы увеличивается.
Многообразие цветовых решений просто поражает. Для внутренней отделки идеально подходит металлопрофиль в виде имитации под разные породы деревьев, кирпичную кладку и натуральный камень. Это придает помещению особенный колорит.
Кто сказал, что это не уютно…
Бытует мнение, что внутренняя сторона стен из профлиста отдает неким холодом, делая помещение неуютным. Это заблуждение зародилось у тех людей, кто наблюдал внутреннюю обшивку профлистом в нежилых зданиях – ангарах и гаражах. А жилой дом с такими внутренними стенами не только придают комнатам свежий и чистый вид, но и уют. Из уроков физики мы знаем, что металл лучше передает тепло. Однако, он не выпускает энергию наружу, так как этому препятствует слой утеплителя и поризованная стена.
Также металлический профиль внутри дома отлично подойдет для владельцев животных и счастливых родителей маленьких детей. Ведь оштукатуренные стены легко поцарапать когтями или разрисовать фломастерами. Такой урон покрытию придется закрашивать и замазывать. Что очень неудобно, если необходимо подбирать оттенок при помощи малярного колера.
Уход за оцинкованными листами намного проще: детские шалости в виде рисунков, наклеек и пластилина легко удаляются влажной губкой. А ваш верный пес не станет грызть и царапать металл.
Для обшивки внутренних стен дома выбирают стеновой профиль, так как кровельный и несущий не подходят. Стеновой профиль не испытывает больших нагрузок, поэтому ему не нужны усиленные ребра жесткости. Подходит металлопрофиль с длиной волны от 8 до 35мм.
Технология крепления профнастила
● Стены из блоков Porotherm не требуют предварительной обработки, так как имеют достаточно ровную поверхность.
● С помощью специализированных химических анкеров к стенам крепятся вертикальный металлический профиль. Это несущий каркас.
● Далее крепятся горизонтальные элементы каркаса, к которым будет фиксироваться профлист.
● На поверхность стены натягивается ветрозащитная дышащая мембрана, которая убережет керамоблок от разрушения.
● Устанавливается утеплитель. Рекомендуется использовать плотные материалы – минеральную или базальтовую вату в листах. Рулонная теплоизоляция не подходит, так как со временем она оседает и образует пустоты.
● В завершении крепится выбранный металлический лист.
Металлопрофиль в любой момент можно демонтировать, поменять или вовсе заменить на оштукатуривание. Также в каркасе для профлиста можно провести скрытые инженерные коммуникации, электропроводку и трубы. Так как металл быстро электризуется, то электропроводку следует заранее помещать в защитную гофру. Металлопрофиль – дешевый и быстрый способ внутренней отделки, который имеет эстетический вид, высокую прочность и долговечность. Причем, после демонтажа его беспрепятственно вторично используют во дворе, на даче или цокольном этаже.
Блок керамзитовый Новороссийск | Советы по выбору
В современном малоэтажном строительстве при возведении наружных и внутренних стен широко используются керамзитобетонные блоки. В силу того что они обладают высокими прочностными характеристиками, высокой тепло и звука-изоляционными свойствами. Также это экологически чистый материал который прост в монтаже. Это те не многие свойства чем керамзитные блоки отличаются от других строительных материалов. Например стены из глины которые возводились в прошлом веке сейчас многим уступает блокам сделанным из керамзита. Разумеется керамзит это та же обожжённая глина. Если сравнивать с кирпичной кладкой то и там есть плюсы и там, но в отличии от кирпича керамзитовый блок имеет неоспоримое преимущество это цена. В отличии от стен из газоблоков которые также широко применяются в строительстве. Они уступают керамзитобетонным стенам в прочности, что со временем может привести к трещинам, а также в экологичности. Так при высокой температуре они выделяют токсичные пары для человека, но по стоимости выходят дешевле. И так выделим основные преимущества керамзитобетонных стен:
- Относительно высокая прочность материала при марке от 50 кг/см2
- Высокая теплопроводность материала
- Высокое звукопоглощение материала
- Экологичность материала
- Быстрота монтажа и возведения стен
- Невысокая стоимость
Это не все плюсы, которые можно отнести к керамзитному блоку о других качествах мы расскажем ниже. Рассмотрим все характеристики керамзитобетонных блоков.
Характеристики блоков
Прочность блоков. Прочность керамзитных блоков – это те нагрузки которые могут выдержать блоки от плит перекрытия, крыши, а предметов находящихся внутри помещения. В зимний период добавляется еще снеговая нагрузка. Предел прочности тот показатель, при котором блок не начнет разрушаться от нагрузок. Обозначается буквой М и числом т.е. показателем прочности, например М50. Предел прочности измеряется в кг/см2. Это означает что площадь поверхности блока подвергается механическому давлению. В лабораторных условиях им является гидравлический пресс. Тот момент когда блок начнет разрушаться будет пределом прочности. Пример блока размером 120х390х190 и прочностью М50:
Площадь – 12 х 39 = 468 см2
Прочность – 468 х 50 = 23400 кг
Результатом испытаний будет сертификат соответствия ГОСТ выданный лицензированной лабораторией. Однако этот вид строительных материалов не подлежит обязательной сертификации, поэтому каждый производитель сам решает нужен ему или нет. Прочность блока зависит от многих факторов: марка и количество цемента, количество керамзита, уплотнение блока во время формовки а также наличие пустот.
Для того чтобы стены из керамзитобетонных блоков была прочной и не давала трещин нужно использовать правильный кладочный раствор. Марка прочности раствора не должна превышать марку прочности блока. Еще один совет для того чтобы прочность стен со временем не опускалась желательно после монтажа и некоторой усадки, произвести отделку кладки. Иначе со временем блок начнет разрушаться от внешнего воздействия (дождь, снег, перепады температуры).
Купить керамзитовый блок в Новороссийске по доступной цене можете у нас.
Виды керамзитовых блоков. По назначению блоки делятся на стеновые, перегородочные, вентиляционные и облицовочные. Большинство производимых блоков подразделяются на полнотелые и пустотелые. Полнотелые блоки не имеют пустот и основном их применяют для возведения несущих стен, на которые будет оказана большая нагрузка. В отличие от полнотелых, пустотелые блоки отличаются меньшей прочностью и меньшим весом. Их используют для возведения стен и перегородок. В конструкции таких блоков предусмотрены сквозные или частичные пустоты. Пустоты в керамзитоблоке бывают квадратные, прямоугольные и цилиндрические.
Толщина стен из керамзитных блоков зависит от региона, где проводится строительство и дальнейшего утепления стены. При кладке блока надо определиться с типом в полблока(20см) или в блок(40см) от этого будет зависеть толщина утеплителя. Например для технических помещений целесообразно использовать кладку в полблока, так как это сэкономит ваши средства. Для жилых помещений рекомендуется толщина в блок или блок шириной 30см. Для увеличения прочности кладки используют арматуру или металлическую сетку.
Не многие знают что в блоках предусмотрены щели для монтажа арматуры. Армирование кладки уменьшит усадку стены, что в дальнейшем не приведет к трещинам. Также для равномерной нагрузки на стены строения заливается бетонный армированный пояс. Это позволит распределить давление и конструкция становится очень прочной.
Теплопроводность и звукоизоляция. Содержание глины в качестве наполнителя придает материалу высокие теплоизоляционные качества. Небольшая теплопроводность одно из главных преимуществ керамзитового блока. На теплопроводность блока влияет плотность материала, которая зависит от количества содержания керамзита в блоке. Керамзитный блок хороший изолятор. Благодаря пустотам внутри, керамзитные блоки обладают неплохими звукоизоляционными свойствами. При толщине 20см шумоизоляция достигает 50 ДБ, при толщине 40см шумоизоляция равна 53 ДБ и это без оштукатуривания стен.
Огнестойкость. Изделия из керамзита имеют высокую огнестойкость, класс по пожаробезопасности А1. При воздействии огня на протяжении 7 часов блок не разрушается и не выделяет токсических веществ. Сопротивляемость горению позволяет использовать этот материал в различных сферах строительства.
Это не все положительные характеристики блоков из керамзита которые позволят возводить строения, обладающие высокими прочностными и теплоизоляционными свойствами. При покупке блоков надо уделить особое внимание на геометрию блока, на соотношение керамзита в блоке и конечно отпускной прочности партии.
Мы предлагаем широкий выбор керамзитобетонных блоков в новороссийске по доступным ценам. Осуществляем доставку, выгрузку различным автотранспортом удобным для вас!
Керамзитобетонный блок, керамзитный блок, керамзитовый блок новороссийск, керамзитовый блок геленджик, цена, купить.
Паробарьеры – Летучий бетон
На этом сайте есть масса технических отчетов по разным вопросам. Возможно, он не будет отвечать на ваши вопросы напрямую, но вы, вероятно, сможете начать собирать его по кусочкам. Чтобы выяснить, нужна ли вам пароизоляция и где, вы должны сначала узнать, какова проницаемость ваших строительных материалов, каков климат и какова внутренняя среда (т.е. сколько влаги образуется внутри здания). Влажность (пар) будет перемещаться от более высоких концентраций к более низким или от более горячих к более холодным помещениям. Поэтому важно знать, какова относительная влажность и температура между помещением и снаружи в разное время года. Имейте в виду, что погодные барьеры могут контролировать 3 разные вещи: воду, воздух, пар. Из этих трех пар может проходить через самые маленькие отверстия.
Вот краткое руководство с другого случайного сайта, в котором говорилось о паре относительно стен подвала. Я пытался найти быструю классификацию проницаемости бетона, и в этой была ссылка на ASHRAE (вы можете попробовать просмотреть веб-сайт ASHRAE напрямую), цитируя, что бетонная смесь 1: 2: 4 имеет проницаемость 3,2 пром. дюйм (который они делят на толщину … что я не совсем понимаю, но что угодно).
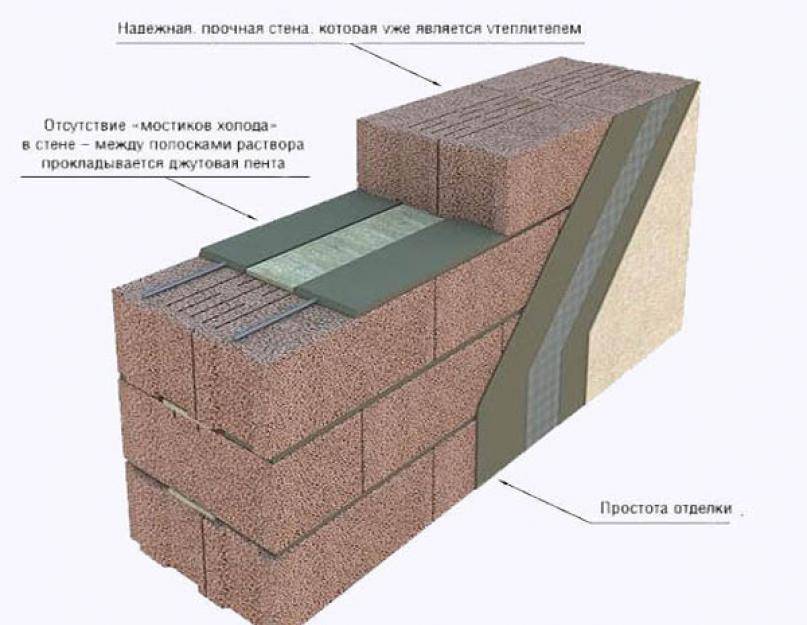
Проницаемость характеризует, насколько легко водяной пар диффундирует через материал – чем ниже, тем больше сопротивление миграции пара. Проницаемость измеряется в проницаемости (граны/час-квадратный фут-дюйм ртутного столба), т.е. скорость пропускания водяного пара (гран/час-кв.фут) на единицу перепада давления (дюйм ртутного столба).
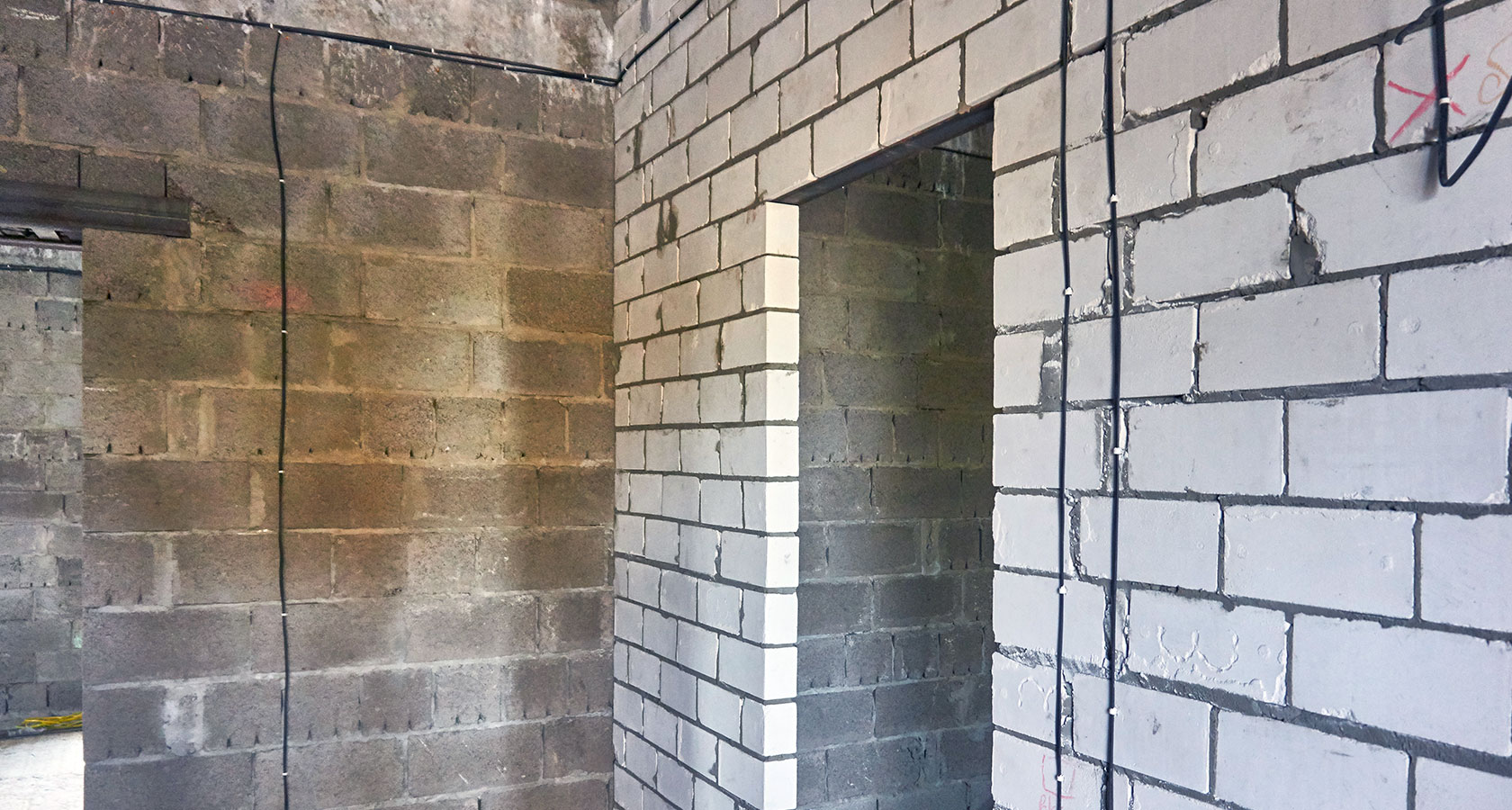
Общие классы материалов по проницаемости и примеры:
Паронепроницаемые – 0,1 проницаемость или менее
Паронепроницаемые – от 0,1 до 1,0 проницаемость: * Эластомер или битум мембраны (0,05–0,5 пром)
* Полиэтиленовая пленка (0,1 пром)
* Фольгированный утеплитель
* Керамическая плитка (но не затирка), плитка VCT, линолеум
* Эпоксидные, тяжелые уретановые или масляные краски
* Виниловые обои
Полупроницаемые для пара – Пермь от 1 до 10: * Необлицованный вспененный или экструдированный полистирол (2 или 1,2 пром/дюйм)
* Строительная бумага, пропитанная тяжелым битумом
* Слоистая изоляция из стекловолокна с бумажным или битумным покрытием
* Фанера, OSB
* Гипсокартон, окрашенный латексной краской
Паропроницаемая – более 10 пром.: * Неокрашенная штукатурка или штукатурка
* Необлицованная изоляция из стекловолокна, целлюлозная изоляция
* Цементные гидроизоляционные покрытия (20 пром. )
* Краски для внутренней гидроизоляции
* Строительная бумага, пропитанная асфальтом
* Домашняя пленка
* Неокрашенные гипсокартонные листы (50 перм.)
Избегайте скопления водяного пара, конденсата и плесени за стенами в готовых подвалах и под напольным покрытием на бетонной плите.
Для получения дополнительной информации см. www.buildingscience.com/index_html
Паропроницаемость бетона
Как насчет паропроницаемости бетона? Согласно справочнику ASHRAE, проницаемость бетона (смеси 1:2:4) составляет 3,2 проницаемости на дюйм толщины. Тогда 4-дюймовая плита будет иметь (3,2/4=) 0,8 перм. Но это только для влажного бетона «хорошего качества» с низким водоцементным отношением. Большинство подвальных плит гораздо более пористые. Хотя они могут быть почти непроницаемыми для воды, цокольные плиты полупроницаемы для водяного пара (> 1 пром.). Недавно залитые бетонные стены классифицируются как паронепроницаемые (толщина 8–10 дюймов, 3,2 / 8 = 0,4 пром.) для хорошего качества. конкретный). Однако, как только внешнее гидроизоляционное покрытие разрушается, вода начинает расширять поры в бетоне, и стены становятся проницаемыми, а позже могут даже начать просачиваться. Стены из сборных панелей имеют наименьшую проницаемость, поскольку изготавливаются из высокопрочного бетона в контролируемых заводских условиях.
Пустотелые бетонные блоки — это отдельная история. У них есть только 1 1/4-дюймовая стенка вне полых заполнителей (3,2/1,25 = 2,6 Perms). Бетон очень пористый, и полые ядра заполняются водяным паром, который затем перемещается в наиболее проницаемую область, чтобы попасть внутрь. Пористость блоков варьируется в широких пределах. Некоторые тесты хороших бетонных блоков показывают проницаемость 2,4, когда сердцевина заполнена, или проницаемость 4,8 для пустотелых блоков. Пустотелые бетонные блоки являются полупроницаемыми (скажем, 5 проницаемостей), но легкие монолитные блоки, блоки с раздельной поверхностью, блоки «попкорн» и шлакоблоки проницаемы (> 10 проницаемостей).
По возможности вместо стандартных блоков (бетонных кладочных элементов – БК) использовать для фундаментов монолитный бетон. Или хотя бы следить за тем, чтобы пустотелые сердечники были должным образом заполнены во время строительства. Нанесите паргинг снаружи и хорошее гидроизоляционное покрытие. Стены из бетонных блоков также менее способны противостоять боковому давлению воды и земли — глинистая почва или вспениваемая глина могут вызвать структурные повреждения.
При всем при этом вы можете спроектировать свой конверт таким образом, чтобы он высыхал только внутри, только снаружи или в некоторой комбинации того и другого (например, в основном внутри, но частично снаружи, или в равной степени внутри и снаружи и т. д.). Если у вас есть ситуация, при которой пар хочет идти в одном направлении летом и в другом направлении зимой, то общая рекомендация – не использовать пароизоляцию. Тем не менее, есть исключения из этого правила, например, если у вас есть каменная полая стена.
Благодаря Shelly P
Как производятся бетонные блоки?
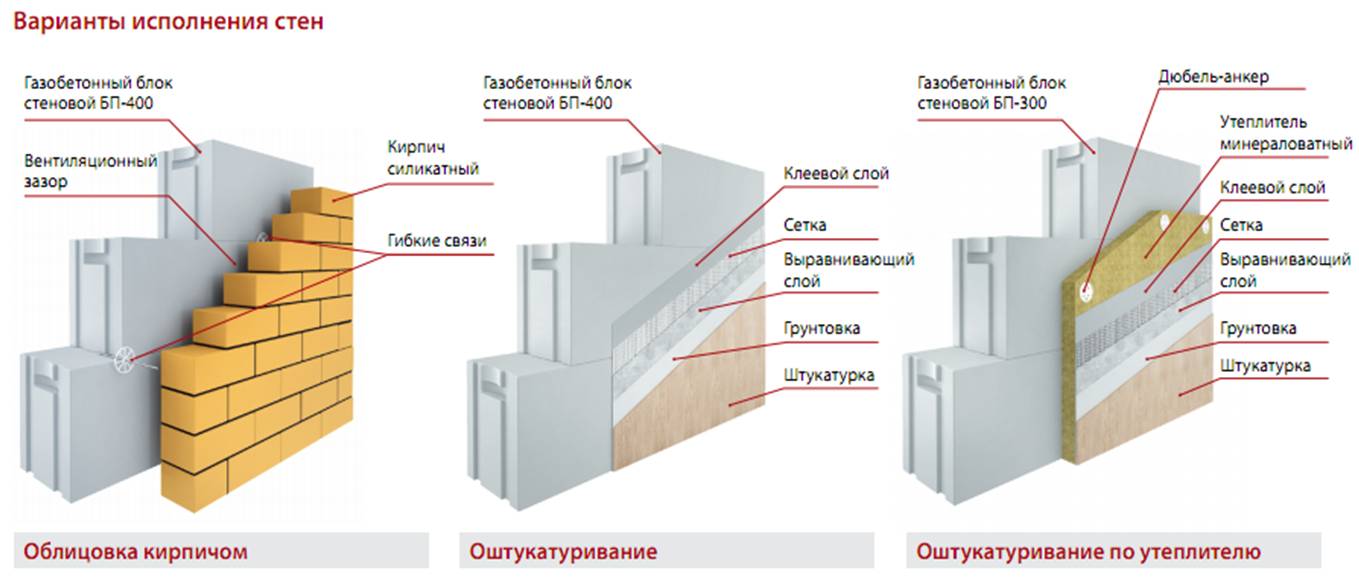
Бетонный раствор впервые использовали римляне в 200 г. до н.э. для крепления фасонного камня в здании. При римском императоре Калигуле в 37-41 гг. н.э. небольшие блоки бетона использовались в качестве строительного материала в современном Неаполе, Италия. Бетонная технология, разработанная римлянами, утрачена с падением Римской империи в пятом веке. Английский каменщик Джозеф Аспдин разработал портландцемент в 1824 году.
Первый пустотелый бетонный блок был спроектирован Хармоном С. Палмером в 1890 году в США, и после 10 лет исследований и экспериментов он запатентовал конструкцию в 1900. Блок, разработанный Палмером, имел размеры 8 x 10 x 30 дюймов и был настолько тяжелым, что для его перемещения использовался кран.
За это время один человек сделал в среднем 10 блоков и отлил их вручную. С современными машинами и передовыми технологиями это составляет 2000 блоков в час.
Какое сырье используется?Для изготовления бетонных блоков или кирпичей используется сырье, такое как смесь порошкообразного портландцемента, воды, песка и гравия. Вместе эти сырьевые материалы образуют блок светло-серого цвета с мелкой текстурой поверхности и высокой прочностью на сжатие. Вес типичного бетонного блока составляет от 38 до 43 фунтов (от 17,2 до 19 фунтов).0,5 кг). Для блоков более высокий процент песка и более низкий процент гравия и воды. Получилась очень сухая, густая смесь, сохраняющая форму при извлечении из блочной формы.
Различные виды сырья Шлакоблок изготавливается из гранулированного угля или вулканического пепла. Это темно-серый блок с текстурой поверхности от средней до грубой, обладающий хорошей прочностью и хорошими звукоизоляционными свойствами с более высокой теплоизоляцией, чем бетонный блок. Типичный шлакоблок весит около 26-33 фунтов (11,8-15,0 кг).
При наличии гранулированного угля или вулканического пепла вместо песка и гравия с керамзитом, сланцем или шифером изготавливается легкобетонный блок. Керамзит, сланец и сланец изготавливают с дроблением сырья и нагревом до 2000 o (1093 o ) . Материал раздувается или вздувается из-за быстрого образования газов, вызванного сгоранием мелких частиц органического материала внутри. Блок из легкого бетона весит около 22-28 фунтов (от 10,0 до 12,7 кг) и используется для возведения ненесущей несущей стены и других перегородок. Кроме того, для облегченных блоков используются доменный шлак и природные вулканические материалы, такие как пемза и шлак.
Наряду с основными компонентами для изготовления блоков используется бетонная смесь, содержащая химическое вещество, называемое добавкой, для изменения времени отверждения и повышения прочности на сжатие или для улучшения обрабатываемости. Пигменты добавляются в блоки для однородного цвета или делают поверхность блока однородной. Это также защищает поверхность блока от химических веществ. Глазурь на поверхности блока выполнена на термореактивной смолянистой связке, кварцевом песке и цветных пигментах.
Существуют стандартные формы и размеры стандартных бетонных блоков для строительства зданий. Обычный размер блока 8 x 8 x 16, 8 дюймов в высоту, 8 дюймов в глубину и 16 дюймов в ширину. Это измерение включает в себя валик раствора и размер блока: 7,63 дюйма (19,4 см) в высоту, 7,63 дюйма (19,4 см) в глубину и 15,63 дюйма (38,8 см) в ширину.
Многие производители блоков предлагают варианты блоков, чтобы они выглядели лучше для конкретных применений. Например, есть один производитель бетонных кирпичей или блоков, который проектирует блоки специально для обеспечения водонепроницаемости через наружные стены. Блок с раздвоенной поверхностью с шероховатой каменной текстурой на одной стороне блока, затем гладкая поверхность. Эти бетонные кирпичи придают красивый эстетический вид.
Процесс производства бетонных кирпичей состоит из четырех этапов: смешивание, формование, отверждение и формирование кубов. Есть бетонные заводы, которые производят только бетонные блоки, в то время как другие производят различные сборные изделия, такие как блоки, плоская брусчатка, декоративные элементы, такие как окантовка газона, бетонные кирпичи и т. Д. С развитием технологий некоторые заводы по производству бетонных кирпичей могут производить 2000 блоков час.
1. Смешивание Песок и гравий хранятся в силосах снаружи, а затем при необходимости передаются по ленточному конвейеру, а цемент хранится в силосах для защиты от влаги. Когда смешивание началось, песок, гравий и цемент выходят из силосов через весовой дозатор, который взвешивает каждый материал. Сухие материалы поступают в смеситель, где они смешиваются в течение нескольких минут. В основном есть два типа миксеров, в которых используется планетарный или тарельчатый миксер, также известный как неглубокий лоток с крышкой. Смесительные лопасти прикреплены к вертикальному вращающемуся валу с мешалкой. Другой тип – горизонтальный барабанный смеситель. Это кофе, перевернутый на бок, с лопастями для смешивания, прикрепленными к горизонтальному вращающемуся валу внутри миксера.
После смешивания сухих материалов в смеситель добавляется небольшое количество воды. Теперь, если завод расположен в теплых местах, вода сначала проходит через нагреватель или чиллер для поддержания температуры. В это время добавляются смешивающие химикаты и цветные пигменты, и бетон перемешивается в течение шести-восьми минут.
2. Формовка После смешивания бетон выгружается в ковшовый конвейер и транспортируется в приподнятый бункер, а цикл смешивания начинается после следующей загрузки. После этого он транспортируется в другие бункеры на блок-машине с регулируемой скоростью. Затем бетон снижают до расхода и заливают в формы. В формах есть внешняя коробка формы, в которой находятся другие вкладыши формы. Вкладыши имеют внешнюю форму блока и внутреннюю форму полостей блоков. В зависимости от мощности машины за один раз формуется от 5 до 15 блоков.
После заполнения формы бетоном гидравлический пресс прессует бетон в форму. Сжатие осуществляется воздушным или гидравлическим давлением. Многие машины для производства бетонных кирпичей и бетонных блоков используют вибрацию для завершения процесса.
После этого блоки выталкиваются из формы на плоский стальной поддон. Поддон и блоки выталкиваются из машины на цепной конвейер. Некоторые из машин имеют функцию вращающейся щетки, которая удаляет рыхлый материал с верхней части блоков.
3. Отверждение Теперь поддоны блока транспортируются к автоматизированному укладчику или загрузчику, который размещает их на стеллаже для отверждения. На каждой стойке несколько сотен блоков. После заполнения стеллажа его закатывают на рельсы, а затем перемещают в сушильную печь.
Это помещение, в котором одновременно могут разместиться несколько стоек блоков. В основном используются два типа отверждения. Во-первых, это печь низкого давления, где блоки выдерживают от одного до трех часов при комнатной температуре для медленного затвердевания. Затем вводят пар с температурой 60°F (16°C в час) для повышения температуры закалки. Блоки стандартного веса отверждаются при 150-165° F (66-74° C), а легкие блоки отверждаются при 170-185° F (77-85° C). После достижения температуры пар отключают и блоки пропитывают горячим влажным воздухом в течение 12-18 часов. Процесс отверждения занимает около 24 часов.
Другой тип печи – паровая печь высокого давления, также известная как автоклав. Температура в этой печи составляет 300-375°F (149-191°C), а давление 80-185 фунтов на квадратный дюйм, примерно от 5,5 до 12,8 бар. Блоки выдерживают от 5 до 10 часов. Давление сбрасывается, и блоки выпускают влагу внутрь. Процесс отверждения в автоклаве потребляет больше энергии и является более дорогим, но он производит больше блоков за меньшее время.
Затем стеллажи с отвержденными блоками выкатываются из печи, а поддоны блока раскладываются и размещаются на цепном конвейере. После этого блоки сталкиваются со стальных поддонов, а пустые поддоны возвращаются в блок-машину для получения новых блоков.
Если есть блок с разъемной поверхностью, он сначала отформован как два соединенных блока. После завершения отверждения двойных блоков он проходит через рассекатель, и тяжелое лезвие ударяет между двумя половинками.
Бетонные кирпичи и блоки проходят через кубер, который выравнивает каждый блок и укладывает их в куб три блока по шесть блоков в глубину и три или четыре блока в высоту. Затем кубики выносятся на улицу вилочным погрузчиком и складируются для отправки.
Качество Производство бетонных блоков и кирпичей требует постоянного контроля за получением блоков требуемых свойств.